一种常压下催化合成氨的方法与流程



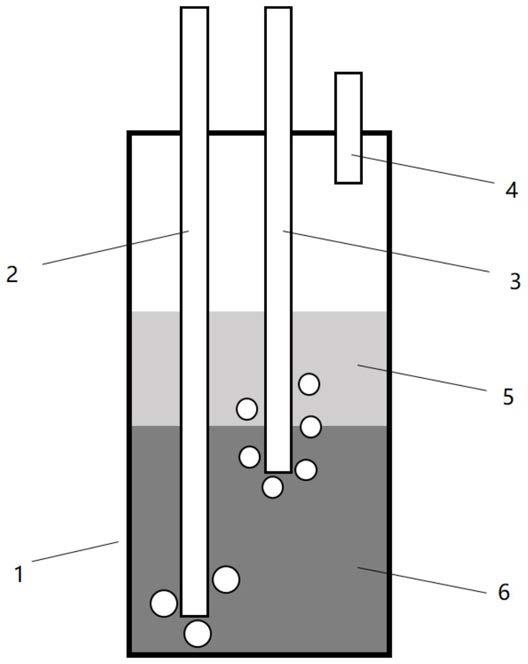
[0001]
本发明涉及一种合成氨的方法,具体涉及一种常压下催化合成氨的方法。
背景技术:
[0002]
氨(nh3)是一种重要的化工原料,在国民经济中占有重要地位,其中约有80%的氨用来生产化学肥料,20%为其它化工产品的原料。氨主要用于制备氮肥、铵盐、硝酸、氰化物等。另外,氨也是一种重要的储氢材料。氨的含氢量的质量分数不仅高达18%,而且在室温条件(300k,27℃)下,氨的饱和蒸汽压低,仅为10个大气压左右,所以,氨比氢更易于液化存储和运输。因此,氨有潜力成为一种重要的能源存储和应用的物质,在未来全球可持续能源的布局中发挥重要作用(macfarlane,d.r.,et al.,a roadmap to the ammonia economy,joule,volume 4,pages 1186-1205,2020)。
[0003]
目前,工业上使用哈伯法大规模合成氨。哈伯法合成氨是以氢气和氮气为原料,在高温(400~500℃)和高压(100~500atm)条件下,使氮气和氢气在铁催化剂作用下反应制备氨。然而,由于哈伯法所需的高温高压条件,合成氨工业总体消耗的能量巨大,同时也带来了严重的环境问题(international energy agency,world energy outlook,2007)。
[0004]
专利cn109803923提供了一种以碱金属为催化剂合成氨的方法,但按照专利方法操作合成氨的含量非常低,而且合成速率也非常低,不容易实现大规模化合成氨。
技术实现要素:
[0005]
鉴于以上所述现有技术的缺点,本发明的目的在于提供一种催化合成氨的方法,其能够在常压下(一个大气压)以液态合金为催化剂催化氢气和氮气合成氨。
[0006]
为了实现上述目的及其他相关目的,本发明是通过包括采用如下技术方案获得。
[0007]
本发明的目的在于提供一种常压下催化合成氨的方法,在反应器中,氢气和氮气以液态合金为催化剂常压下反应合成氨,反应中采用熔融盐,所述熔融盐的密度小于液态合金的密度,所述熔融盐用于提供反应界面并用于隔离液态合金避免引入反应环境中杂质。
[0008]
本发明中,浮在液态合金上方的熔融盐起到了三方面的作用,1)合金和氮气反应生成的金属氮化物在熔融盐中有一定的溶解度,其中金属氮化物中的氮通常以氮离子的形式溶于熔融盐中,因此熔融盐可以为金属氮化物与氢气反应提供新的反应界面;2)反应器内可能有来自外界大气的氧气和水蒸汽,熔融盐可以避免液态合金与外界大气的氧气和水蒸汽接触,从而避免液态合金被氧化,延长液态合金的使用寿命;3)原料气体氮气和氢气可能含有少量杂质气体(如水蒸汽和氧气),这些杂质气体可与液态合金中的活泼金属反应生成金属氧化物。金属氧化物比液态合金的密度小,而且在液态合金的溶解度低。在气泡的作用下,金属氧化物会上浮到熔融盐中进行溶解,可去除氢气和氮气中的杂质,使反应高效进行。
[0009]
优选地,所述熔融盐选自licl、nacl、kcl、mgcl2、cacl2、srcl2、bacl2、zncl2、alcl3、
libr、nabr、kbr、lii、nai、ki的一种或多种盐的熔融体。
[0010]
更优选地,所述熔融盐为licl和kcl的熔融盐。
[0011]
进一步优选地,所述licl和kcl的摩尔比为(55~60):(35~45)。更具体地,所述licl和kcl的摩尔比可以是(55~57):(35~42),也可以是(55~57):(38~45),也可以是(56~60):(35~42),也可以是(56~60):(38~45)。所述熔融盐是将一种及以上熔融盐装入塑料瓶子中,在混料机上进行混料;混料完成后,装入氧化铝坩埚中,在氩气保护以及400℃下,用机械真空泵抽真空,干燥;冷却后即可得到熔融盐。
[0012]
优选地,所述熔融盐与液态合金的质量比为(0.02~0.9):(0.1~0.98)。所述熔融盐与液态合金的质量比可以是(0.02~0.3):(0.14~0.32),也可以是(0.25~0.6):(0.23~0.61),也可以是(0.52~0.9):(0.50~0.98)。
[0013]
优选地,所述液态合金包括第一金属,所述第一金属的熔点为27~180.54℃。本发明中第一金属为活性金属,可以和氮气反应生成金属氮化物。
[0014]
更优选地,所述第一金属为碱金属,所述碱金属选自li、na、k、rb、cs、fr的一种或多种。进一步优选地,所述第一金属为li。
[0015]
优选地,所述液态合金还包括第二金属,所述第二金属的熔点为29.77~630℃。本发明中第二金属可以降低第一金属的活度,一方面可以避免第一金属腐蚀反应器,另一方面可以驱动反应过程中所形成的第一金属氢化物的分解。
[0016]
更优选地,所述第二金属为两性金属,所述两性金属选自zn、sn、bi、ga、in、pb、sb的一种或多种。
[0017]
进一步优选地,所述第二金属为sn。
[0018]
更优选地,所述第一金属和第二金属的摩尔比为(0.2~0.7):(0.3~0.8)。
[0019]
进一步优选地,所述第一金属和第二金属的摩尔比为(0.4~0.6):(0.4~0.7)。本发明的合金优选第一金属和第二金属形成的液态合金。
[0020]
本发明中常压下催化合成氨的方法,所述合成氨包括两步:
[0021]
1)第一步是氮的固定。氮气与第一金属反应生成金属氮化物,以li为例,反应为:6li+n2=2li3n。金属氮化物通常比液态合金的密度小,而且在液态合金中的溶解度低,所以在气体气泡的作用下,金属氮化物通常会上浮。
[0022]
2)第二步是氨的合成。氢气与金属氮化物反应生成氨和金属,以li为例,反应为2li3n+3h2=2nh3+6li。产物氨(nh3)以气体形式离开反应器,然后被分离和收集。此外,氢气与金属氮化物反应也会生成氨和金属氢化物,以li为例,反应为li3n+6h2=nh3+3lih。但由于第二金属降低了第一金属的活度,因此将促进金属氢化物分解,以li为例,反应为2lih=2li+h2。释放出的第一金属可以继续参与和氮气的反应生成金属氮化物,然后金属氮化物再和氢气反应生成氨。通过上述反应过程,这样就建立了一个持续进行的闭合化学链,在常压下,不间断地有效合成氨。
[0023]
本发明中形成液态合金的方法是现有技术,可以是将第一金属或/或第一金属与第二金属的混合物在反应器中直接加热熔融制得液态合金,也可以是将第一金属或第一金属与第二金属熔融后呈液态合金装入反应器中。也可以采取原位电解的方法把第一金属引入第二金属,具体为选用液态的第二金属为阴极,施加电压电解第一金属的氧化物或盐,在第二金属阴极表面原位生成第一金属,并通过扩散与第二金属形成液态合金。
[0024]
在本发明一个更优选的技术方案中,不仅采用熔融盐,还采用了由第一金属和第二金属形成的液态合金,因为单纯使用第一金属,第一金属的密度低,第一金属会随着气泡的产生会上浮,导致氨的合成速率低和产量低,缩短第一金属的使用寿命,甚至会导致反应器破裂。而第二金属与第一金属形成液态合金可以有效地提高密度,此外,不仅可以避免第一金属腐蚀陶瓷反应器,还可以驱动反应过程中所形成的第一金属氢化物的分解。
[0025]
优选地,所述合成氨过程中反应的温度为300~600℃。更优选地,所述温度为400~500℃。根据热力学分析,过高的温度不利于氨的合成和收集。此外,根据动力学分析,过低的温度又使合成氨反应的速率降低,因此应选择合适的反应温度范围。
[0026]
优选地,所述催化反应中还采用有第三金属,所述第三金属熔点比第一金属的熔点高,并且以固态形式存在于液态合金中,用于活化反应气体;所述第三金属为过渡金属。本发明中第三金属具有较高的比表面积(6500~8000cm2/g),第三金属可以促进氮气分子和氢气分子的活性,对氨的合成具有催化活性。具体地,所述第三金属可以采用泡沫镍,固定在氮气和氢气的出气部;也可以以铁丝网的形式放置在液体合金中;也可以是第三金属与第一金属和第二金属直接混合。
[0027]
更优选地,所述第三金属选自ni、fe、mo、co、ru、re和pt中的一种或多种。
[0028]
更优选地,所述第三金属和液态合金的质量比为(0.1~10):(90~99.9)。进一步优选地,所述第三金属和液态合金的质量比为(0.3~7):(94~96)。
[0029]
优选地,所述氮气和所述氢气加入的流速比例为(1~99):(1~99)。
[0030]
更优选地,所述氮气和氢气的流速比1:(2~50)。
[0031]
优选地,所述氮气和氢气通入液态合金的方式至少有两种:
[0032]
一种是,所述氮气和氢气分别经不同的通气管通入液态合金中,所述氮气通入液态合金的底部,所述氢气通入液态合金或熔融盐的上部。
[0033]
另外一种是,所述氮气和氢气先混合,然后经通气管通入液态合金中。
[0034]
优选地,所述氮气的流速为5~100cm3/min,氢气的流速为5~100cm3/min。
[0035]
优选地,所述反应在保护气体下进行,所述保护气体用于防止氨的分解。所述保护气体选自氮气、氢气和惰性气体中的一种。所述气体的流速为60~100cm3/min。本发明可以通过保护气体的吹扫,使已生成的氨气快速离开反应器的高温区域,可以有效防止催化反应生成氨的分解。
[0036]
本发明提供了一种常压下催化合成氨的方法的反应器,包括反应器、用于提供热源的加热机构,氢气源和氮气源。
[0037]
优选地,所述反应器包括反应器本体、氮气通气管和氢气通气管,所述氮气通气管和所述氢气通气管贯穿进入所述的反应器本体且延伸至所述的反应器本体内。
[0038]
更优选地,所述反应器本体的上部设有产物气体出口。进一步优选地,所述产物气体出口连通有氨气收集机构,用于避免氨气排出对环境的污染以及引发的不安全因素。更具体地,氨气收集机构为盛装有酸水溶液的收集槽。
[0039]
优选地,所述反应器还设有保护气体通气管,所述保护气体通气管的进气管与保护气体源连通,所述保护气体通气管的出气端贯穿所述反应器本体进入所述反应器本体内。
[0040]
本发明的反应过程中为了确保反应温度为300~600℃,可以将反应器转移至加热
机构如管式炉中进行加热。
[0041]
与现有技术相比,本发明具有以下有益效果:
[0042]
1)本发明催化剂使用活性高的碱金属,与氮气较易反应生成碱金属氮化物,并能在常压下合成氨,而且相比于贵金属催化剂,碱金属通常来源更广泛,成本更低。
[0043]
2)本发明中的第二金属能降低第一金属的活度,一方面可以避免第一金属腐蚀反应器,另一方面可以驱动反应过程中所形成的第一金属氮化物的分解。
[0044]
3)本发明催化反应中,熔融盐能为金属氮化物与氢气反应合成氨提供新的反应界面,使金属氮化物不断生成氨,有效提高了反应的速率和氨的合成量,此外,熔融盐可以避免液态合金与外界大气的氧气和水蒸汽接触,从而避免液态合金被氧化,从而延长液态合金的使用寿命。
[0045]
4)本发明催化反应中,固氮反应生成的第一金属氮化物密度较小而且溶解度低,所以第一金属氮化物将随着气泡上浮,生成的第一金属氮化物再与氢气反应合成氨,第一金属氮化物在第二金属的促进下分解为第一金属和氢气,实现了持续进行的闭合化学链,可在常压下不间断地有效合成氨。
[0046]
5)本发明合成氨反应的工艺和设计简单,反应条件相对温和,易于实现大规模化合成氨。
附图说明
[0047]
图1显示为本发明的反应器的结构示意图。
[0048]
图1中附图标记如下:1为反应器,2为氮气通气管,3为氢气通气管,4为产物气体出口,5为熔融盐,6为液态合金。
具体实施方式
[0049]
以下由特定的具体实施例说明本发明的实施方式,熟悉此技术的人士可由本说明书所揭露的内容轻易地了解本发明的其他优点及功效。
[0050]
在进一步描述本发明具体实施方式之前,应理解,本发明的保护范围不局限于下述特定的具体实施方案;还应当理解,本发明实施例中使用的术语是为了描述特定的具体实施方案,而不是为了限制本发明的保护范围。下列实施例中未注明具体条件的试验方法,通常按照常规条件,或者按照各制造商所建议的条件。
[0051]
当实施例给出数值范围时,应理解,除非本发明另有说明,每个数值范围的两个端点以及两个端点之间任何一个数值均可选用。除非另外定义,本发明中使用的所有技术和科学术语与本技术领域技术人员通常理解的意义相同。除实施例中使用的具体方法、设备、材料外,根据本技术领域的技术人员对现有技术的掌握及本发明的记载,还可以使用与本发明实施例中所述的方法、设备、材料相似或等同的现有技术的任何方法、设备和材料来实现本发明。
[0052]
本申请实施例中,所述合金为预制li-sn合金,具体为:1)在氩气手套箱中,将6.87gli和78.32gsn混合放置在坩埚中;2)把1.52g licl和1.86g kcl混合覆盖在表面,用于使金属与气氛隔离;3)将坩埚整体转移至管式炉中,在氩气保护气下,加热至500℃,保温12h后,冷却至室温,将licl和kcl去除,从而获得预制li-sn合金,其中li和sn的摩尔比为
60:40。
[0053]
本申请实施例中,所述熔融盐为预制licl-kcl熔融盐:称取100g无水licl和122g无水kcl装入塑料瓶子中,在混料机上进行混料24小时;混料完成后,将盐装入氧化铝坩埚中,在氩气保护以及400℃下,用机械真空泵抽真空,干燥24h;冷却后的样品转移进入手套箱中即得,其中licl-kcl熔融盐中licl和kcl的摩尔比为59:41。但是,从实现本申请中发明目的来说,只要熔融盐的密度小于液态合金的密度,能够起到提供反应界面并隔离液态合金从而避免引入反应环境中杂质的效果均可以达到采用本申请实施例中这种具体的licl-kcl熔融盐的技术效果。
[0054]
实施例1
[0055]
本实施例中公开了一种具体的常压下催化合成氨的装置,其包括反应器、用于提供热源的加热机构,氢气源和氮气源。
[0056]
图1为本发明的反应器的结构示意图,所述反应器包括反应器本体1、氮气通气管2、氢气通气管3;所述的反应本体器1的上部设有产物气体出口4,所述氮气通气管2和所述氢气通气管3贯穿进入所述的反应器本体1且延伸至所述的反应器本体1内。
[0057]
为了避免氨气排出对环境的污染以及引发的不安全因素,所述产物气体出口4连通有氨气收集机构,如盛装有酸水溶液的收集槽。
[0058]
为了使得这一反应器能够用于本申请中合成过程,所述反应器均采用氧化铝制成。
[0059]
为了使得用于作为催化剂的合金在反应器本体1内形成加热熔融成液态合金,并排除这一过程中反应器本体1内的空气对液态合金的氧化作用等的影响,所述反应器还可以包括保护气体通气管,所述保护气体通气管的进气管与保护气体源连通,所述保护气体通气管的出气端贯穿所述反应器本体1进入所述反应器本体1内。所述保护气体通气管可以为氩气、氮气、氢气或惰性气体。同样地,所述保护气体通气管的材质为氧化铝材质。
[0060]
在一个具体在使用上述装置进行常压下合成氨时,
[0061]
将作为催化剂的固态合金放入反应器本体1中,并在合金表面覆盖熔融盐5,然后在氩气保护下加热使得固态合金形成液态合金,氮气通气管2的进气端与氮气源连通,氮气通气管2的出气端位于液态合金6中,氢气通气管3的进气端与氢气源连通,氢气通气管3的出气端位于液态合金6中或者也可以位于熔融盐5中,反应产生的氨气通过产物气体出口4进行收集。
[0062]
在反应过程中为了确保反应温度为300~600℃,可以将反应器转移至加热机构如管式炉中进行加热。
[0063]
本申请中实施例2~4以及对比例1~2均采用反应器1进行催化反应,但是注意的是,从实现本申请中发明目的来说,不限于本发明所举列的反应器,只要能满足在常压下氮气和氢气通入,在液态合金的催化下合成氨的反应器或装置或设备都可以。
[0064]
实施例2
[0065]
本实施例中,以li-sn液态合金为催化剂,添加licl-kcl的熔融盐,常压合成氨。
[0066]
本实施例中常压下催化合成氨的方法,催化反应步骤如下:
[0067]
1)在氩气手套箱中,称取21.3g预制li-sn合金和8.46g预制licl-kcl熔融盐,并先后装入反应器中。
[0068]
2)将反应器整体转移至管式炉中。反应器通入氩气,氩气的流速为5cm3/min,并以4℃/min的速率升温至500℃,使预制li-sn合金成为li-sn液态合金,然后停止通氩气。将氮气经过氮气通气管通入li-sn液态合金的底部,氮气的流速为5cm3/min;将氢气经过氢气通气管通入li-sn液态合金的上部,氢气的流速为15cm3/min。反应在500℃和常压条件下进行24小时。将产物氨气经产物气体出口通入稀硫酸水溶液,对氨进行收集。稀硫酸水溶液的浓度为0.1mol/l,体积为20ml。
[0069]
实施结果:用离子色谱仪测定稀硫酸水溶液中氨根离子的含量为182.22mg/l。氨的合成速率可以计算为143.41μg/h,这说明了在添加熔融盐下,以液态合金为催化剂,可在常压下高效催化合成氨。
[0070]
相比于专利cn109803923提供的仅使用液态纯钠在500℃和常压下合成氨的方法,本实施例的氨的合成速率提高了5倍。
[0071]
实施例3
[0072]
本实施例中,以li-sn液态合金为催化剂,添加licl-kcl的熔融盐,常压合成氨。
[0073]
本实施例中常压下催化合成氨的方法,催化反应步骤如下:
[0074]
1)在氩气手套箱中,称取11.76g预制li-sn合金,再称取26.97g sn混合,使li和sn的摩尔比为30:70,再称取3.38g预制licl-kcl熔融盐,并先后装入反应器中。
[0075]
2)将反应器整体转移至管式炉中。反应器通入氩气,氩气的流速为5cm3/min,并以4℃/min的速率升温至400℃,使预制li-sn合金成为li-sn液态合金,然后停止通氩气。将氮气经过氮气通气管通入li-sn液态合金的底部,氮气的流速为5cm3/min;将氢气经过氢气通气管通入熔融盐中,氢气的流速为15cm3/min。反应在400℃和常压条件下进行24小时。将产物氨气经产物气体出口通入稀硫酸水溶液,对氨进行收集。稀硫酸水溶液的浓度为0.1mol/l,体积为20ml。
[0076]
实施结果:用离子色谱仪测定稀硫酸水溶液中氨根离子的含量为3.9mg/l。氨的合成速率可以计算为2.66μg/h,这说明在添加熔融盐下,以液态合金为催化剂,可在常压下高效催化合成氨。这个结果小于实施例2的氨合成速率,主要归因于反应的温度相对较低,使得反应速率较低。此外,熔融盐添加少以及液态合金中锂含量少也会降低催化合成氨的速率和氨的含量。
[0077]
实施例4
[0078]
本实施例中催化反应步骤和条件同实施例2。但在氢气通气管和氮气通气管的出气端分别用镍丝固定了0.126g的泡沫镍。作为第三金属,泡沫镍用于活化反应气体。
[0079]
实施结果:用离子色谱仪测定稀硫酸水溶液中氨根离子的含量为189.47mg/l。氨的合成速率可以计算为149.12μg/h。与未引入第三金属的实施例2相比,氨的含量和氨的合成速率都有提高。这说明在反应中引入第三金属泡沫镍进一步促进合成氨反应。
[0080]
对比例1
[0081]
对比例1中,以li-sn液态合金为催化剂,常压下合成氨。
[0082]
合成氨的催化反应步骤如下:
[0083]
1)在氩气手套箱中,将21.3g预制li-sn合金装入反应器中。
[0084]
2)将反应器整体转移至管式炉中。反应器通氩气,氩气的流速为5cm3/min,并以4℃/min的速率升温至500℃,使预制li-sn合金成为li-sn液态合金,然后停止通氩气。将氮
气经过氮气通气管通入li-sn液态合金的底部,氮气的流速为5cm3/min;将氢气经过氢气通气管通入li-sn液态合金中,氢气的流速为15cm3/min。反应在500℃和常压条件下进行24小时,将产物氨气经产物气体出口通入稀硫酸水溶液,对氨进行收集。稀硫酸水溶液的浓度为0.1mol/l,体积为20ml。
[0085]
实验结果:用离子色谱仪测定稀硫酸水溶液中氨根离子的含量为4.22mg/l。氨的合成速率可以计算为3.32μg/h。这个结果远远小于实施例2的氨合成速率,说明了熔融盐对于在常压下催化合成氨反应起到重要的作用。熔融盐在氨合成中的作用有三方面的,1)氮化锂在熔融盐中有一定的溶解度,其中氮化锂中的氮通常以氮离子的形式溶于熔融盐中,因此熔融盐可以为氮化锂与氢气反应提供新的反应界面;2)反应器内可能有来自外界大气的氧气和水蒸汽,熔融盐可以避免液态合金与外界大气的氧气和水蒸汽接触,从而避免液态合金被氧化,延长液态合金的使用寿命;3)原料气体氮气和氢气可能含有少量杂质气体(如水蒸汽和氧气),这些杂质气体可与液态合金中的活泼金属反应生成金属氧化物。金属氧化物比液态合金的密度小,而且在液态合金的溶解度低。在气泡的作用下,金属氧化物会上浮到熔融盐中进行溶解,可去除氢气和氮气中的杂质,使反应高效进行。
[0086]
与没有添加熔融盐的对比例1相比,实施例2中氨的含量提高了43倍,氨的合成速率提高了43倍。
[0087]
对比例2
[0088]
对比例2中,以sn液态合金为催化剂,添加licl-kcl熔融盐,常压下合成氨。
[0089]
合成氨的催化反应步骤如下:
[0090]
1)在氩气手套箱中,称取45.87g sn和3.38g预制licl-kcl熔融盐,并先后装入反应器中。
[0091]
2)将反应器整体转移至管式炉中。反应器通氩气,氩气的流速为5cm3/min,并以4℃/min的速率升温至400℃,然后停止通氩气。将氮气经过氮气通气管通入sn液态合金的底部,氮气的流速为5cm3/min;将氢气经过氢气通气管通入熔融盐中,氢气的流速为15cm3/min。反应在400℃和常压条件下进行24小时。将产物氨气经产物气体出口通入稀硫酸水溶液,对氨进行收集。稀硫酸水溶液的浓度为0.1mol/l,体积为20ml。
[0092]
实验结果:用离子色谱仪测定稀硫酸水溶液中氨根离子的含量为1.77mg/l。氨的合成速率计算为1.40μg/h。这个结果小于实施例2的氨合成速率,说明了第一金属锂和熔融盐在催化过程中相互协作,对于在常压下催化合成氨反应起到重要的作用。
[0093]
上述实施例仅例示性说明本发明的原理及其功效,而非用于限制本发明。任何熟悉此技术的人士皆可在不违背本发明的精神及范畴下,对上述实施例进行修饰或改变。因此,举凡所属技术领域中具有通常知识者在未脱离本发明所揭示的精神与技术思想下所完成的一切等效修饰或改变,仍应由本发明的权利要求所涵盖。
起点商标作为专业知识产权交易平台,可以帮助大家解决很多问题,如果大家想要了解更多知产交易信息请点击 【在线咨询】或添加微信 【19522093243】与客服一对一沟通,为大家解决相关问题。
此文章来源于网络,如有侵权,请联系删除



tips