一种新型轴类铸件铸造方法与流程



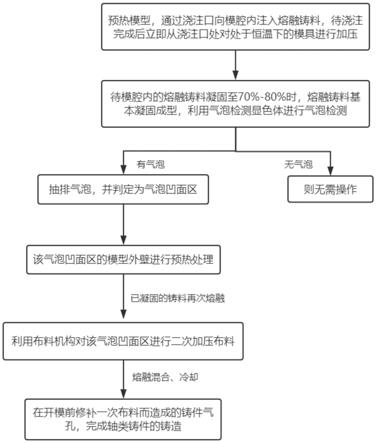
[0001]
本发明涉及轴类铸件铸造技术领域,更具体地说,涉及一种新型轴类铸件铸造方法。
背景技术:
[0002]
在砂型铸造过程中,必须充分考虑砂芯出气,确保芯子排出的气体完全按照设计的通道排出,这样才能确保生产出来的铸件尺寸符合相关质量要求。
[0003]
对于一些特殊结构的砂芯,砂芯的完全出气往往成为铸造的最大难点。比较典型的是机体类产品中的轴类结构,轴类零件是五金配件中经常遇到的典型零件之一,它主要用来支承传动零部件,传递扭矩和承受载荷。轴用轴承支承,与轴承配合的轴段称为轴颈。轴颈是轴的装配基准,指轴上同一直径的一段轴或直径不等但形成的外圆表面是均匀连续的圆柱面,外圆表面必须是均匀连续的,不能有轴肩或凹槽断开,它们的精度和表面质量一般要求较高。
[0004]
其主要特征是轴颈为细长结构,其表面积大,铸件存在气孔类缺陷是致命的,气孔类缺陷问题是由于气体排除不完全,造成铸件端面的凹凸不平或形成气孔,铸件光滑度降低,当铸件外端面出现气孔或存在凹凸不平的现象时便达不到质量要求,故而需要后期进行大量的打磨处理,操作较为繁琐,所导致的气孔以及凹凸不平面难以避免,且难以发现并补救,降低了轴类铸件的铸造精度。
[0005]
为此,我们提出一种新型轴类铸件铸造方法来有效解决现有技术中所存在的一些问题。
技术实现要素:
[0006]
1.要解决的技术问题
[0007]
针对现有技术中存在的问题,本发明的目的在于提供一种新型轴类铸件铸造方法,通过在模型的外端壁设置多个与其内部相连通的气泡检测显色体,气泡检测显色体用于对模型内壁的不同位置进行气体抽取显色检测,以此判定铸件与模腔内壁的什么位置存有空隙,即判定铸件外端壁的什么位置上存有气孔或形成的凹面,利用显色现象标记该存有气孔、凹面的区域为气泡凹面区,并对该气泡凹面区进行热熔融,再利用布料机构对该气泡凹面区进行二次布料,以实现在铸件开模前修补铸件端面上的气孔或凹面问题,发现问题并解决问题,在一定程度上提高了铸件端面的光滑度,有效减少铸件因气孔缺陷而需要进行打磨的情况。
[0008]
2.技术方案
[0009]
为解决上述问题,本发明采用如下的技术方案。
[0010]
一种新型轴类铸件铸造方法,具体铸造方法步骤如下:
[0011]
s1、清洁模具上的模型,模型内部开设有模腔,预热模型,通过浇注口向模腔内注入熔融铸料,待浇注完成后立即从浇注口处对处于恒温下的模具进行加压;
[0012]
s2、待模腔内的熔融铸料凝固至70%-80%时,熔融铸料基本凝固成型,利用分布于模型上的多个气泡检测显色体检测模腔内壁处是否存在气泡,抽排气泡,有气泡的区域即判定为气泡凹面区;
[0013]
s3、标记气泡凹面区,并对该气泡凹面区的模型外壁进行预热处理,使得该区域以凝固的铸料再次熔融;
[0014]
s4、利用布料机构对该气泡凹面区进行二次加压布料,经过熔融混合、冷却,在开模前修补一次布料而造成的铸件气孔,完成轴类铸件的铸造。
[0015]
进一步的,所述s1中的所加压力为0.025~0.03mpa,加压时间为0.3~0.6h。
[0016]
进一步的,所述模具包括上下匹配设置的上模和下模,所述模型设于下模上,所述模型的顶端固定连接有内卡圈,所述上模的底端固定连接有与内卡圈相匹配的外卡圈,内卡圈与外卡圈的密封嵌设衔接,实现模型内部的模腔为一个密封铸造空间。
[0017]
进一步的,所述内卡圈和外卡圈的内壁上均分别开设有相互连通的内排气孔和外排气孔,所述内卡圈的内壁上包覆有耐高温透气膜层,内排气孔与外排气孔的连通结构,有效实现在铸料浇注时进行排气处理。
[0018]
进一步的,所述气泡检测显色体设置有多个,且多个气泡检测显色体环形均匀分布于模型的外侧壁上,所述气泡检测显色体包括贯穿设置于模型上的气体检测杆,所述气体检测杆的内端与模型的内壁相匹配衔接,所述气体检测杆的内端开设有多个透气孔,所述气体检测杆的外端部安装有抽吸机构,所述气体检测杆位于模型外端部的一端侧壁上设有气泡显色囊,待模腔内的熔融铸料凝固至%-%时,熔融铸料基本凝固成型,当模腔内壁与凝固的铸料之间存有空隙时则会形成铸料端面的气泡,该孔隙必然存在气体,利用分布于模型外壁的多个抽吸机构向外抽气,若气泡显色囊显色后,则判定该处的铸件端面存在气孔。
[0019]
进一步的,所述抽吸机构包括活动衔接于气体检测杆内部的活塞,所述活塞的外端固定连接有活塞杆,所述气体检测杆的顶端嵌设安装有与活塞杆相对应的微型电动滑轨,所述微型电动滑轨通过密封滑动块与活塞杆的顶端相衔接,且微型电动滑轨位于气泡显色囊的外侧,默认初始状态下活塞相抵于气体检测杆的最内端,在进行检测时,微型电动滑轨带动活塞杆向外侧运动,当气体检测杆内端存在气体时,则会在气体检测杆内部形成负压的情况下将气体抽出。
[0020]
进一步的,所述气泡显色囊包括连接于气体检测杆上且与其内部相连通的弹性透明扩张囊,所述弹性透明扩张囊内部固定连接有显色球,所述显色球上包覆有无水硫酸铜粉末分布层,气体通过透气孔向气体检测杆外部抽出时导入至弹性透明扩张囊内部,无水硫酸铜粉末分布层接触到空气后变成蓝色,显色后以此表面该处的铸件端面存在气孔。
[0021]
进一步的,所述无水硫酸铜粉末分布层包括包覆于显色球上的透明显色套,所述透明显色套上开设有多个分布孔,所述分布孔内填充有无水硫酸铜粉末。
[0022]
进一步的,所述布料机构包括设置于下模上的二次补料筒,所述二次补料筒位于左右两组气泡检测显色体的外侧方,所述二次补料筒上连接有上料管,所述上料管的两侧侧壁上从上之下分布有多个与气泡检测显色体位置对应的浇注管,所述浇注管远离上料管的一端通过浇注嘴与气体检测杆的内部相连接,且浇注嘴设置于气泡显色囊的内侧处,每个浇注管上均安装有电磁阀,根据显色情况标记气泡凹面区,并利用二次补料筒、上料管以
及浇注管、浇注嘴的配合向标记气泡凹面区的气体检测杆进行注料,并在注料前需要对该标记气泡凹面区进行预热处理,使得以凝固的铸料再次部分熔融并与二次布料的铸料混合,实现在开模前的铸造修补。
[0023]
进一步的,所述模型的外端壁上嵌设安装有多个与气泡检测显色体位置对应的加热模块,所述加热模块内安装有加热块。
[0024]
3.有益效果
[0025]
相比于现有技术,本发明的优点在于:
[0026]
(1)本方案通过在模型的外端壁设置多个与其内部相连通的气泡检测显色体,气泡检测显色体用于对模型内壁的不同位置进行气体抽取显色检测,以此判定铸件与模腔内壁的什么位置存有空隙,即判定铸件外端壁的什么位置上存有气孔或形成的凹面,利用显色现象标记该存有气孔、凹面的区域为气泡凹面区,并对该气泡凹面区进行热熔融,再利用布料机构对该气泡凹面区进行二次布料,以实现在铸件开模前修补铸件端面上的气孔或凹面问题,发现问题并解决问题,在一定程度上提高了铸件端面的光滑度,有效减少铸件因气孔缺陷而需要进行打磨的情况。
[0027]
(2)模具包括上下匹配设置的上模和下模,模型设于下模上,模型的顶端固定连接有内卡圈,上模的底端固定连接有与内卡圈相匹配的外卡圈,内卡圈与外卡圈的密封嵌设衔接,实现模型内部的模腔为一个密封铸造空间,内卡圈和外卡圈的内壁上均分别开设有相互连通的内排气孔和外排气孔,内卡圈的内壁上包覆有耐高温透气膜层,内排气孔与外排气孔的连通结构,有效实现在铸料浇注时进行排气处理。
[0028]
(3)气泡检测显色体设置有多个,且多个气泡检测显色体环形均匀分布于模型的外侧壁上,气泡检测显色体包括贯穿设置于模型上的气体检测杆,气体检测杆的内端与模型的内壁相匹配衔接,气体检测杆的内端开设有多个透气孔,气体检测杆的外端部安装有抽吸机构,气体检测杆位于模型外端部的一端侧壁上设有气泡显色囊,待模腔内的熔融铸料凝固至%-%时,熔融铸料基本凝固成型,当模腔内壁与凝固的铸料之间存有空隙时则会形成铸料端面的气泡,该孔隙必然存在气体,利用分布于模型外壁的多个抽吸机构向外抽气,若气泡显色囊显色后,则判定该处的铸件端面存在气孔。
[0029]
(4)抽吸机构包括活动衔接于气体检测杆内部的活塞,活塞的外端固定连接有活塞杆,气体检测杆的顶端嵌设安装有与活塞杆相对应的微型电动滑轨,微型电动滑轨通过密封滑动块与活塞杆的顶端相衔接,且微型电动滑轨位于气泡显色囊的外侧,默认初始状态下活塞相抵于气体检测杆的最内端,在进行检测时,微型电动滑轨带动活塞杆向外侧运动,当气体检测杆内端存在气体时,则会在气体检测杆内部形成负压的情况下将气体抽出。
[0030]
(5)气泡显色囊包括连接于气体检测杆上且与其内部相连通的弹性透明扩张囊,弹性透明扩张囊内部固定连接有显色球,显色球上包覆有无水硫酸铜粉末分布层,无水硫酸铜粉末分布层包括包覆于显色球上的透明显色套,透明显色套上开设有多个分布孔,分布孔内填充有无水硫酸铜粉末,气体通过透气孔向气体检测杆外部抽出时导入至弹性透明扩张囊内部,无水硫酸铜粉末分布层接触到空气后变成蓝色,显色后以此表面该处的铸件端面存在气孔。
[0031]
(6)布料机构包括设置于下模上的二次补料筒,二次补料筒位于左右两组气泡检测显色体的外侧方,二次补料筒上连接有上料管,上料管的两侧侧壁上从上之下分布有多
个与气泡检测显色体位置对应的浇注管,浇注管远离上料管的一端通过浇注嘴与气体检测杆的内部相连接,且浇注嘴设置于气泡显色囊的内侧处,每个浇注管上均安装有电磁阀,根据显色情况标记气泡凹面区,并利用二次补料筒、上料管以及浇注管、浇注嘴的配合向标记气泡凹面区的气体检测杆进行注料,并在注料前需要对该标记气泡凹面区进行预热处理,使得以凝固的铸料再次部分熔融并与二次布料的铸料混合,实现在开模前的铸造修补。
附图说明
[0032]
图1为本发明的流程图;
[0033]
图2为本发明的上模、下模以及模型结合处的立体图一;
[0034]
图3为为本发明的上模、下模以及模型结合处的立体图二;
[0035]
图4为本发明的布料机构与气泡检测显色体结合处的部分立体图;
[0036]
图5为本发明的气泡检测显色体处的内部剖视图图;
[0037]
图6为本发明的气泡显色囊的内部剖视图。
[0038]
图中标号说明:
[0039]
1模型、2内卡圈、201内排气孔、3外卡圈、301外排气孔、4气泡检测显色体、401气体检测杆、402微型电动滑轨、403活塞杆、404气泡显色囊、4041弹性透明扩张囊、4041显色球、4043无水硫酸铜粉末分布层、40活塞、5二次补料筒、6上料管、7浇注管、701浇注嘴、8加热模块。
具体实施方式
[0040]
下面将结合本发明实施例中的附图;对本发明实施例中的技术方案进行清楚、完整地描述;显然;所描述的实施例仅仅是本发明一部分实施例;而不是全部的实施例,基于本发明中的实施例;本领域普通技术人员在没有做出创造性劳动前提下所获得的所有其他实施例;都属于本发明保护的范围。
[0041]
在本发明的描述中,需要说明的是,术语“上”、“下”、“内”、“外”、“顶/底端”等指示的方位或位置关系为基于附图所示的方位或位置关系,仅是为了便于描述本发明和简化描述,而不是指示或暗示所指的装置或元件必须具有特定的方位、以特定的方位构造和操作,因此不能理解为对本发明的限制。此外,术语“第一”、“第二”仅用于描述目的,而不能理解为指示或暗示相对重要性。
[0042]
在本发明的描述中,需要说明的是,除非另有明确的规定和限定,术语“安装”、“设置有”、“套设/接”、“连接”等,应做广义理解,例如“连接”,可以是固定连接,也可以是可拆卸连接,或一体地连接;可以是机械连接,也可以是电连接;可以是直接相连,也可以通过中间媒介间接相连,可以是两个元件内部的连通。对于本领域的普通技术人员而言,可以具体情况理解上述术语在本发明中的具体含义。
[0043]
实施例1:
[0044]
请参阅图1-3,一种新型轴类铸件铸造方法,具体铸造方法步骤如下:
[0045]
s1、清洁模具上的模型1,模型1内部开设有模腔,预热模型1,通过浇注口向模腔内注入熔融铸料,待浇注完成后立即从浇注口处对处于恒温下的模具进行加压,所加压力为0.025~0.03mpa,加压时间为0.3~0.6h;
[0046]
s2、待模腔内的熔融铸料凝固至70%-80%时,熔融铸料基本凝固成型,利用分布于模型1上的多个气泡检测显色体4检测模腔内壁处是否存在气泡,抽排气泡,有气泡的区域即判定为气泡凹面区;
[0047]
s3、标记气泡凹面区,并对该气泡凹面区的模型1外壁进行预热处理,模型1的外端壁上嵌设安装有多个与气泡检测显色体4位置对应的加热模块8,加热模块8内安装有加热块,使得该区域以凝固的铸料再次熔融;
[0048]
s4、利用布料机构对该气泡凹面区进行二次加压布料,经过熔融混合、冷却,在开模前修补一次布料而造成的铸件气孔,完成轴类铸件的铸造。
[0049]
请参阅图2-3,模具包括上下匹配设置的上模和下模,模型1设于下模上,模型1的顶端固定连接有内卡圈2,上模的底端固定连接有与内卡圈2相匹配的外卡圈3,内卡圈2与外卡圈3的密封嵌设衔接,实现模型1内部的模腔为一个密封铸造空间,内卡圈2和外卡圈3的内壁上均分别开设有相互连通的内排气孔201和外排气孔301,内卡圈2的内壁上包覆有耐高温透气膜层,内排气孔201与外排气孔301的连通结构,有效实现在铸料浇注时进行排气处理。
[0050]
请参阅图3-5,气泡检测显色体4设置有多个,且多个气泡检测显色体4环形均匀分布于模型1的外侧壁上,气泡检测显色体4包括贯穿设置于模型1上的气体检测杆401,气体检测杆401的内端与模型1的内壁相匹配衔接,气体检测杆401的内端开设有多个透气孔,气体检测杆401的外端部安装有抽吸机构,气体检测杆401位于模型1外端部的一端侧壁上设有气泡显色囊404,抽吸机构包括活动衔接于气体检测杆401内部的活塞405,活塞405的外端固定连接有活塞杆403,气体检测杆401的顶端嵌设安装有与活塞杆403相对应的微型电动滑轨402,微型电动滑轨402通过密封滑动块与活塞杆403的顶端相衔接,且微型电动滑轨402位于气泡显色囊404的外侧,默认初始状态下活塞405相抵于气体检测杆401的最内端,待模腔内的熔融铸料凝固至70%-80%时,熔融铸料基本凝固成型,当模腔内壁与凝固的铸料之间存有空隙时则会形成铸料端面的气泡,该孔隙必然存在气体,在进行检测时,利用微型电动滑轨402带动活塞杆403向外侧运动,当气体检测杆401内端存在气体时,则会在气体检测杆401内部形成负压的情况下将气体抽出,若气泡显色囊404显色后,则判定该处的铸件端面存在气孔,
[0051]
请参阅图6,具体的,气泡显色囊404包括连接于气体检测杆401上且与其内部相连通的弹性透明扩张囊4041,弹性透明扩张囊4041内部固定连接有显色球4042,显色球4042上包覆有无水硫酸铜粉末分布层4043,无水硫酸铜粉末分布层4043包括包覆于显色球4042上的透明显色套,透明显色套上开设有多个分布孔,分布孔内填充有无水硫酸铜粉末,无水硫酸铜粉末可替换成其它遇空气而反应变色的物质,气体通过透气孔向气体检测杆401外部抽出时导入至弹性透明扩张囊4041内部,无水硫酸铜粉末分布层4043接触到空气后变成蓝色,显色后以此表面该处的铸件端面存在气孔。
[0052]
请参阅图3-5,在检测到有气孔后,标记该区域为气泡凹面区,利用布料机构对该气泡凹面区进行二次布料,具体的,布料机构包括设置于下模上的二次补料筒5,二次补料筒5位于左右两组气泡检测显色体4的外侧方,二次补料筒5上连接有上料管6,上料管6的两侧侧壁上从上之下分布有多个与气泡检测显色体4位置对应的浇注管7,浇注管7远离上料管6的一端通过浇注嘴701与气体检测杆401的内部相连接,且浇注嘴701设置于气泡显色囊
404的内侧处,每个浇注管7上均安装有电磁阀,根据显色情况标记气泡凹面区,并利用二次补料筒5、上料管6以及浇注管7、浇注嘴701的配合向标记气泡凹面区的气体检测杆401进行注料,并在注料前需要对该标记气泡凹面区进行预热处理,使得以凝固的铸料再次部分熔融并与二次布料的铸料混合,实现在开模前的铸造修补。
[0053]
本发明通过在模型1的外端壁设置多个与其内部相连通的气泡检测显色体4,气泡检测显色体4用于对模型1内壁的不同位置进行气体抽取显色检测,以此判定铸料与模腔内壁的什么位置存有空隙,即判定铸件外端壁的什么位置上存有气孔,利用显色现象标记该存有气孔的区域为气泡凹面区,对该气泡凹面区进行热熔融,再利用布料机构对该气泡凹面区进行二次布料,以实现在铸件开模前修补铸件端面上的气孔问题,在一定程度上提高了铸件端面的光滑度,有效减少铸件因气孔缺陷而需要进行打磨的情况。
[0054]
本发明中的所采用的部件均为通用标准件或本领域技术人员知晓的部件,其结构和原理都为本技术人员均可通过技术手册得知或通过常规实验方法获知。
[0055]
以上所述;仅为本发明较佳的具体实施方式;但本发明的保护范围并不局限于此;任何熟悉本技术领域的技术人员在本发明揭露的技术范围内;根据本发明的技术方案及其改进构思加以等同替换或改变;都应涵盖在本发明的保护范围内。
起点商标作为专业知识产权交易平台,可以帮助大家解决很多问题,如果大家想要了解更多知产交易信息请点击 【在线咨询】或添加微信 【19522093243】与客服一对一沟通,为大家解决相关问题。
此文章来源于网络,如有侵权,请联系删除
相关标签: 活塞杆



tips