一种多流单秤的连铸铸坯定重切割控制系统及控制方法与流程



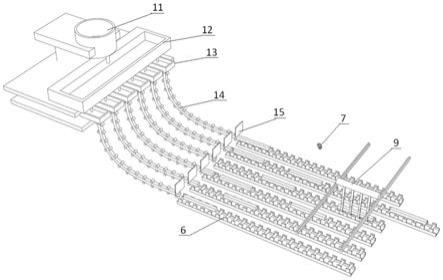
[0001]
本发明为一种多流单秤的连铸铸坯定重切割控制系统及控制方法,属于冶金连铸生产技术领域,为一切割控制系统,通过传感及输出切割控制指令,将连铸坯切割至固定重量。
背景技术:
[0002]
在钢铁连铸生产过程中,尤其是生产螺纹钢、棒材的生产线中,需要将连铸坯切割为固定重量。如果重量过重,则后续轧制工艺产生浪费,如果重量过轻,则会造成后续工序产生次品。典型的重量控制精度要求为重2.4吨的铸坯,重量偏差在
±
5kg之内。
[0003]
铸坯切割系统的输入参数只能为长度参数。而随温度、拉速等生产条件的变化,铸坯密度、界面等会发生微小的变化。同样长度的铸坯重量并不相同,差别可能在几十kg,远远超过
±
5kg的范围。使用秤做反馈,每次秤取切割后的铸坯重量,在生产条件发生变化时,及时修正每根铸坯切割长度,使其不断接近重量目标值是可行的方式。
[0004]
申请公开号cn106077553a的发明专利申请当中,公开了一种连铸钢坯重量智能控制切割系统及连铸钢坯切割定重方法,使用称重作为反馈信号,同时结合冷却水量水温等参数变化,实时调整下次切割铸坯设定长度,达到定重称重的目标。
[0005]
申请公开号cn104325105a的发明专利申请当中,使用称重重量反馈,同时使用热跟踪模型,进行下次铸坯切割长度设定调整,使得切割重量接近定重目标。
[0006]
以上两个发明申请均是可行的定重切割控制方法,均依赖于称重系统数据,但未说明称重数据如何获取。
[0007]
因为连铸生产均为多流生产,极少有单流生产的情况。每一流生产状况不同,切割长度设定量也不同。使用称重反馈做切割控制,一种做法是在连铸每流辊道上安装秤,对切割后的铸坯进行称重,然后进行称重反馈,从而进行切割定重控制。这种方法的缺点为:
[0008]
1)秤安装困难:受连铸辊道设计影响,多数连铸系统在设计之初并为称重系统预留安装空间,使得安装困难。
[0009]
2)秤成本高、维护复杂:每流有秤的情况带来秤本身的成本及安装成本较高。同时铸坯温度在600-900℃,称重设备包含传感器、通信等需要做冷却防护,润滑需要做防高温处理,给安装带来众多问题。
[0010]
3)秤的维护、校准成本高。拆卸、安装浪费时间较多,侵占大量工作时间。
技术实现要素:
[0011]
本发明的目的是提供一种多流单秤的连铸铸坯定重切割控制系统及控制方法,以克服现有技术设备复杂庞大、检测量大的问题。
[0012]
一种多流单秤的连铸铸坯定重切割控制系统,包括切割设备、连铸机的多流辊道、切割装置和通信与计算设备,其特征在于,在多流末端连接有单秤,单秤连接在多流辊道中的一个流辊道的末端,在多流末端前的上方设有铸坯移动装置,并设有视觉跟踪装置,视觉
跟踪装置的摄像头安装在多流辊道上方、铸坯移动装置前面。
[0013]
所述的铸坯移动装置是钩机搬运机构。
[0014]
所述的铸坯移动装置也可以是推拉搬运机构。
[0015]
如权利要求1所述的一种多流单秤的连铸铸坯定重切割控制系统的控制方法,其特征在于,包括下列步骤,
[0016]
步骤一、在连铸机的多流中,选择一流的末端连接一单秤;
[0017]
步骤二、安装设有视觉跟踪装置,视觉跟踪装置的摄像头安装在多流上方、铸坯移动装置前面,使摄像头能全部摄入识别区的视图;
[0018]
步骤三、工作时,视觉跟踪装置的摄像头录入多流辊道上识别区的视图,识别区域亮度超过识别亮度阈值,各流上移动的切割好的铸坯被识别;视觉追踪装置对铸坯被搬运装置搬运的过程进行追踪,以判断称重铸坯的流号来源;
[0019]
步骤四、铸坯移动装置将被识别的铸坯依次移动到末端连接一单秤的一流,将所有的识别的铸坯移动到单秤后一一称重;
[0020]
步骤五、将某一识别的铸坯的重量信息输送到通信与计算设备,通信与计算设备将切割时的长度信息与重量信息进行关联,得出切割长度修正的信息,将长度修正的信息输入对该流的切割信息进行修正;通信与计算设备将修正的切割信息输入到切割设备中;
[0021]
步骤六、切割装置用通信与计算设备修正后切割信息切割下一个流铸坯。
附图说明
[0022]
图1、本发明系统结构示意图;
[0023]
其中,11为钢包,12为中间包,13为结晶器,14为连铸扇形段,15为切割机,6为6流辊道,7为视觉追踪摄像装置,9为钩机搬运机构;
[0024]
图2、本发明视觉追踪摄像装置在系统中的位置示意图;
[0025]
1为第1流辊道,2为第2流辊道,3为第3流辊道,4为第4流辊道,5为第5流辊道,6为第6流辊道,7为视觉追踪摄像装置,8为铸坯,9为钩机搬运机构,10为第5流至称重系统辊道;
[0026]
图3、本发明方法示意框图;
[0027]
图4、本发明工作原理示意图;
[0028]
图5、本发明定重切割控制流程;
[0029]
图6、本发明视觉追踪系统对铸坯移动特征检测的视图示意图;
[0030]
图7、本发明视觉追踪系统铸坯移动追踪流程示意图;
[0031]
图8、本发明视觉追踪系统对连接称重称的流上的铸坯移动追踪流程示意图;
[0032]
图9、本发明通信与计算设备用户端显示的视觉追踪系统铸坯移动追踪视图的示意图;
[0033]
图10、本发明发明通信与计算设备提供用户界面,显示视觉追踪,定重控制决策信息的示意图。
[0034]
有益效果:
[0035]
1.建立了完整的闭环控制系统,使得重量接近。使用铸坯定重切割控制系统后,铸坯重量一致性提高,重量分布标准差明显下降。利用多流单秤的设计,大大减少称重系统硬
件成本及安装、维护成本。系统能够完全自动运行,极少人工干预。
[0036]
2.在本发明的一个实例中,由于该现场场地空间有限,只能安装一个秤,在未实施该发明之前,由于钩机完全由人工操作,铸坯搬运过程无法做到自动追踪,系统不能做到自动采集各流称重数据做到全自动运行。实施后利用视觉追踪,完成称重数据闭环,系统可全自动在线运行。全自动运行后,切割重量控制标准差为2.3
‰
,高于生产要求3
‰
的目标。
具体实施方式
[0037]
实施例一:
[0038]
一种多流单秤的连铸铸坯定重切割控制系统,包括切割设备、连铸机的6个流辊道、切割装置和通信与计算设备,其特征在于,在6个流辊道末端连接有单秤,单秤连接在6个流辊道中的第5流辊道的末端,在6个流辊道末端前的上方设有钩机搬运机构,并在设有视觉跟踪装置,视觉跟踪装置的摄像头安装在6个流辊道上方、铸坯移动装置前面的侧面。
[0039]
一种多流单秤的连铸铸坯定重切割控制系统的控制方法,其特征在于,包括下列步骤,
[0040]
步骤一、在连铸机的6个流辊道中,选择第5流辊道的末端连接一单秤;
[0041]
步骤二、安装设有视觉跟踪装置,视觉跟踪装置的摄像头安装在6流上方的侧面、铸坯移动装置前面,使摄像头能全部摄入识别区的视图;
[0042]
步骤三、工作时,视觉跟踪装置的摄像头录入6个流辊道上识别区的视图,识别区域亮度超过识别亮度阈值,各流上移动的切割好的铸坯被识别;视觉追踪装置对铸坯被搬运装置搬运的过程进行追踪,以判断称重铸坯的流号来源;
[0043]
步骤四、铸坯移动装置将被识别的铸坯依次移动到第5流,将所有的识别的铸坯移动到单秤后一一称重;
[0044]
步骤五、将某一识别的铸坯的重量信息输送到通信与计算设备,通信与计算设备将切割时的长度信息与重量信息进行关联,得出切割长度修正的信息,将长度修正的信息输入对该流的切割信息进行修正;通信与计算设备将修正的切割信息输入到切割设备中;
[0045]
步骤六、切割装置用通信与计算设备修正后切割信息切割下一个流铸坯。
[0046]
铸坯视觉追踪系统,利用摄像装置,拍摄铸坯从多个流生产完毕,汇聚至称重处的图像。以上视频图像可发送至图像图像处理单元,利用图像处理算法追踪铸坯整个运动过程,可回溯当前称重铸坯来自于哪一流。在本发明的一个实现中,铸机生产有六个流,没流均会产生铸坯。在第5个流的辊道上安装有秤,及称重系统,摄像装置拍摄铸坯被钩机吊起,移动至第5流辊道,放下的动作序列,追踪铸坯搬运的过程,来判断铸坯来源自哪个流辊道。
[0047]
定重切割反馈决策系统,包含计算及通信硬件,决策软件。系统接收到各流称重反馈信息,根据上次及历史切割信息,做下次的切割调整。系统同时也可以利用连铸生产温度信息,冷却水量等前馈信息,进行调整,如申请号cn106077553a、cn104325105a的申请所公开的方法进行调整。在本发明的一个实施实施实例中为进一步消除单个秤称重延迟带来的震荡,同时使用拟合、滤波等方法改进定重切割精度。
[0048]
以上的定重控制系统还包含一用户界面,显示铸坯追踪的过程信息,以及定重决策输入输出信息。
[0049]
实施例二
[0050]
本发明在连铸生产、称重的系统布局如下。连铸生产为6流铸机,每流铸机对应一个辊道进行切割完的连铸坯的输送。第1、2、3、4、6流辊道上的铸坯通过钩机,将辊道上的铸坯勾起,放至第5流辊道上。第5流辊道继续将铸坯输送至称重系统。6流辊道共用一个秤。在本发明实施之前,现场系统不能自动获取当前称重的铸坯来源自那一流的辊道,从而无法做到根据重量反馈自动调整切割长度。
[0051]
铸坏视觉追踪系统
[0052]
在本实施实例中,铸坯视觉追踪系统持续检测钩机动作,做铸坯提升,平移,放下等动作判断,由此进行称重铸坯来源的跟踪,方法如图6,
[0053]
本实施方式视觉追踪摄像装置采用工业用监控用摄像机,分辨率为480*372像素,可以覆盖铸坯移动区域。
[0054]
在摄像装置拍摄的视频图像中,铸坯尾部设置铸坯识别区,如上图所示,彩色线段围成的区域就是铸坯识别区。当铸坯到位或者下落后,该区域被高亮度像素占满,当铸坯向上提起后,该区域被清空。铸坯在提起横移过程中不占用其它流次的识别区域。通过对铸坯识别区域内像素的动态分析,能够识别铸坯进入和离开以及提升和下落的移动过程,然后移动过程和铸坯状态进行逻辑判断,实现铸坯移动追踪。
[0055]
如图7所示,除5流外的其它流次铸坯移动追踪流程相同,以3流为例说明如下:
[0056]
a)3流的铸坯进入勾机区域,识别区域亮度超过识别亮度阈值,3流铸坯被识别。
[0057]
b)铸坯被勾机勾起,向上提升离开识别区域,当识别区域占比低于识别亮度阈值,且亮度质心向上移动,判断铸坯被勾机提起,画面左上角标识变为3u,即3流铸坯被提起。
[0058]
c)勾机移动到5流上方,准备下降放置铸坯。
[0059]
d)铸坯下降,识别区域从上至下被占满,当识别区域占比超过识别阈值,判断铸坯被放下,且子区域亮度质心向下移动,系统将画面左上角3u标识进行临时存储后,将标识更改为5d,表示铸坯被放置到5流道次上。
[0060]
e)铸坯前进,离开识别区域,识别区域清空后,将临时存储的流号标识3u中的流号数显示在画面右上角,画面左上角的标识不变化,追踪流程结束。如右上角数字显示为3,则标识3流铸坯去称重。
[0061]
第5流铸坯移动追踪与其它流次稍有区别,5流铸坯不需要勾机,因此只有三个追踪流程。如图8所示,说明如下:
[0062]
a)5流铸坯将要进入5流道次,其它流次铸坯等待。
[0063]
b)铸坯进入识别区域,识别区域占比超过识别阈值,且亮度质心向左前移动,5流铸坯被识别,画面左上角标识变为5e。
[0064]
c)铸坯前进,离开识别区域,识别区域清空后,且亮度质心向左前方移动,将流号数5显示在画面右上角,即5流铸坯去称重。
[0065]
定重切割反馈决策系统
[0066]
定重决策系统硬件,系统使用工控机,实现对图像的采集处理,以及存储。运行系统为windows 7,硬件配置为cpu i7,内存8g,硬盘256g存储空间。
[0067]
在本发明的一个实例中,使用如下算法处理由于铸坯称重延时带来的不确定性。以及进行长度的调整。
[0068]
1)通过在线称重系统进行铸坯称重,对称重数据进行诊断,去除无效数据。
[0069]
2)通过最优化自回归数据处理算法获取对重量的正确估计,消除对延时带
[0070]
来的误差的影响。其模型为:
[0071]
w
k,esp
=w
k
+λ*(l
k-1-l
k-2
)*ρ*s
[0072]
其中,ρ(铸坯密度),s为铸坯界面。w
k
为当前该流的称重值,λ*(l
k-1-l
k-2
)*ρ*s为根据长度变化值,对重量修订值进行修正项。w
k,esp
为当前实际重量的估计值。其意义为,如果发现长度设定值变大,而实际称重量未发生变化,则增加一个正的修正值。如长度设定变小,则往称重重量上加一个付的修正量。系数λ可根据历史数据进行最小二乘拟合得到,得到最优的修正系数。由w
k,esp
与目标重量的偏差,可获取重量偏差δw。
[0073]
3)结合铸坯目标重量,计算出重量偏差,根据公式:δl(调整长度)=δw(重量偏差)/s(铸坯截面积)*ρ(铸坯密度)计算出铸坯长度调整量。
[0074]
4)对铸坯长度调整量进行限幅处理,防止长度过度调整。
[0075]
将处理后的长度调整量与铸坯切割长度设定值之和,作为新的铸坯定尺切割长度目标值,通过铸机数据发送给铸坯定尺切割系统。
[0076]
决策控制系统同时提供用户界面,显示视觉追踪,定重控制决策信息,内容如图9。
[0077]
系统界面包括通讯连接状态,称重信息,总量统计,视觉铸坯追踪,功能操作,流次数据及操作,消息框部分组成。
[0078]
1)通讯连接状态:定尺切割系统、数据库和拉速的连接状态指示为绿色表示通讯连接正常。
[0079]
2)称重信息:称重铸坯的流号,目标重量,实际重量和重量偏差信息。
[0080]
3)总量统计:当前所有铸坯的数量,总定重率和总标准差。总定重率≤60%,背景色为红色;总定重率在60%-80%之间,背景色为黄色;总定重率≥80%,背景色为绿色。
[0081]
4)视觉铸坯追踪:视觉追踪图像,图像上包含铸坯识别区域,过程识别和追踪识别号;原系统追踪、视觉识别追踪和手动确认三种追踪方式的选择;追踪数据栈的操作,数据栈可以存储2个追踪流号,流号下进上出,称重结束后,上流号跟随称重结果出栈,下流号递进,通过区域内按钮可以对数据栈内数据进行清空、增加和修改操作。
[0082]
5)功能操作:全流控制启动和停止,全流数据清空,查看统计表,查看数据曲线。
[0083]
6)流次数据及操作:每流次的系统运行(绿色)/停止(灰色)状态指示;系统正常(绿色)/报警(红色)/故障(红色)指示;铸坯数据,包括铸坯的称重时间,实际重量,重量偏差,定尺切割长度,长度调整量,调整后定尺切割长度给定值;铸坯的数量、定重率和标准差;定重控制启动/停止操作和数据曲线。
[0084]
7)消息框:启动/停止记录,状态信息记录,过程信息提示和记录。消息结构为时间+信息。
[0085]
实施例控制效果
[0086]
系统控制精度以标准差来衡量,如上界面所示,6030根六流铸坯切割,标准差为5.72kg,目标重量为2405kg,控制标准差为2.3
‰
,高于生产要求3
‰
的目标。
[0087]
本发明涉及冶金连铸领域,为一多流单秤的定重切割控制系统。该控制系统利用视觉追踪系统,追踪称重铸坯的来源,将各流切割重量与当前各流切割设定长度对应,根据各流历史重量与切割长度,计算下次切割设定长度。通过不断反馈调整,使得各流铸坯接近重量设定目标。该发明通过各流共享秤等称重设备,可有效减少称重设备安装,节省称重系
统投入,为一经济有效的连铸坯定重切割控制系统方案。
[0088]
1.一种多流单秤的连铸铸坯定重切割控制系统,其特征在于:连铸生产有多个流,要生产固定重量的铸坯,目标重量值通过系统设定。系统只需要安装1个,或少于相应流数的称重设备,即不能保证各流都安装称重设备。
[0089]
2.根据权利要求1所属系统,其特征在于,系统同时包含视觉追踪系统,可对铸坯来源进行跟踪,即通过视觉分析记录,确定当前称重铸坯来自于哪一流,将铸坯称重值与来源流号相关联。
[0090]
3.根据权利要求1所属系统,其特征在于,系统还包括定重切割决策系统,可从追踪系统接收来自称重系统各流的信息,同时接收历史切割长度设定值,根据历史设定值与历史称重值,计算下次切割铸坯长度设定值,切割控制系统根据切割长度设定值进行切割,切割出的铸坯重量与目标重量接近。
起点商标作为专业知识产权交易平台,可以帮助大家解决很多问题,如果大家想要了解更多知产交易信息请点击 【在线咨询】或添加微信 【19522093243】与客服一对一沟通,为大家解决相关问题。
此文章来源于网络,如有侵权,请联系删除



tips