煤专用船或矿/煤兼用船的船舱用耐蚀钢及船舱的制作方法



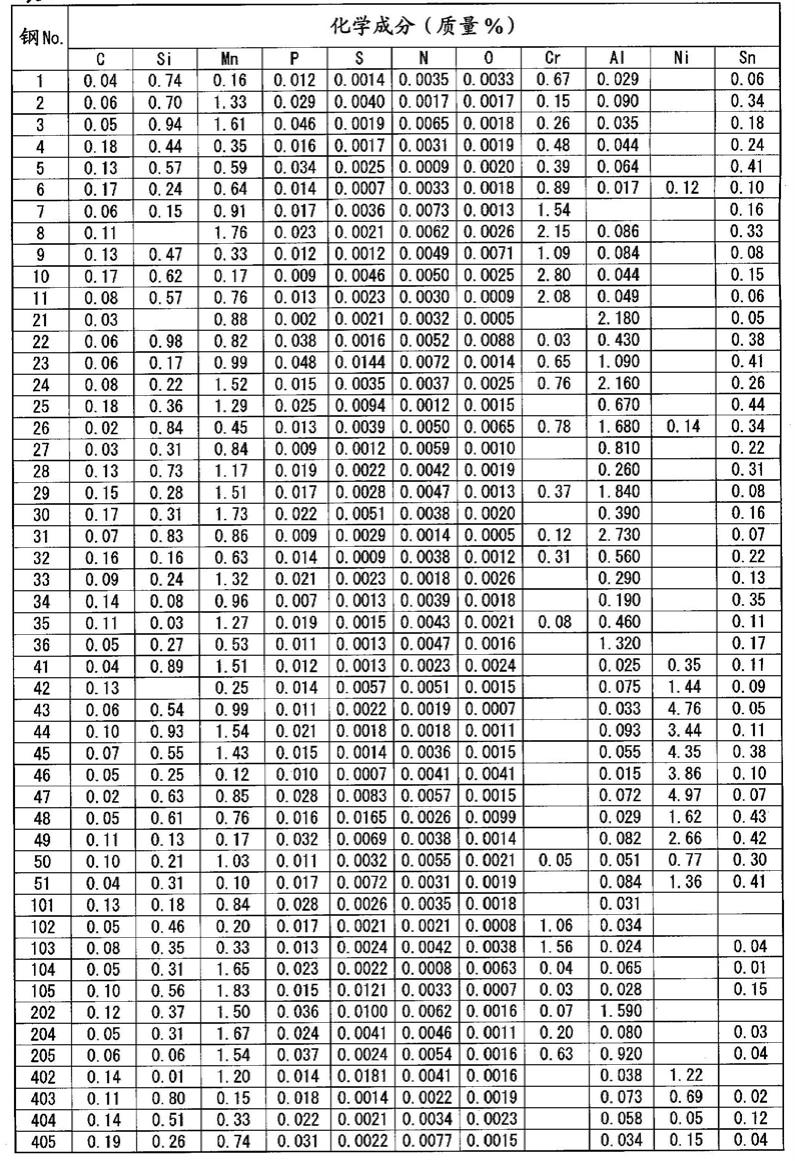
[0001]
本发明涉及煤专用船或矿/煤兼用船的船舱用耐蚀钢及船舱。本申请基于在2018年10月31日向日本申请的专利申请2018-204699号、专利申请2018-204700号、专利申请2018-204701号要求优先权,将其内容援引于此。
背景技术:
[0002]
近年来,运输煤的煤专用船或运输铁矿石及煤的矿/煤兼用船的船舱内(以下有时称为货舱内)的腐蚀被视为问题。以往就曾对装载煤的货舱内实施了涂装,但由于由煤引起的机械损伤、由卸货时的重型设备引起的伤痕
·
磨损而导致涂装层剥落的情况较多,产生的伤痕部暴露于腐蚀环境中,不能得到充分的防蚀效果。
[0003]
为了维持由涂膜形成带来的防蚀效果,需要定期的再涂装及修补,但要进行再涂装、修补的话非常花费成本。因而,需求即使是涂装层剥落了的部分也具有优异的耐蚀性(无涂装耐蚀性)的钢板。对于这样的要求,例如,在专利文献1~3中提出了一种通过合金元素的微量添加而提高了耐蚀性的耐蚀钢。
[0004]
这些专利文献所记载的技术是含有sb、cu等的抑制由酸引起的腐蚀的合金元素(耐酸元素)且以提高低ph环境下的耐蚀性为目标的耐蚀钢。
[0005]
在先技术文献
[0006]
专利文献
[0007]
专利文献1:日本国特开2012-177190号公报
[0008]
专利文献2:日本国特开2013-227610号公报
[0009]
专利文献3:日本国特开2016-027198号公报
技术实现要素:
[0010]
以往认为:在船舱内,煤中包含的硫向在船舱的侧壁部产生的结露水中溶出,因温度的上升而生成硫酸,成为低ph环境,因而进行腐蚀。然而,本发明人分析了在船舱内腐蚀了的钢材的结果,从腐蚀生成物与钢基体的界面确认到了氯离子(cl-),但是没有确认到硫酸根离子(so
42-)。因此,认为船舱内的主要腐蚀因子不是硫酸根离子(so
42-)而是氯离子(cl-)。
[0011]
以往,认为在船舱内钢材的腐蚀因硫酸而进行,所以在船舱所使用的钢材中添加耐酸元素,避开了cr之类的促进由酸引起的腐蚀的合金元素的添加。然而,本发明人研究的结果判明:在船舱内,氯离子(cl-)是腐蚀因子,腐蚀因干湿反复而进行。因此,对于煤专用船或矿/煤兼用船的船舱用耐蚀钢的成分设计,需要与以往不同的思想。
[0012]
即,通过本发明人的研究而知晓:需要不是考虑硫酸根离子影响的腐蚀形态而是考虑氯离子影响的腐蚀形态来进行船舱用耐蚀钢的成分设计。
[0013]
本发明的课题是提供与含有sb、cu等耐酸元素的基于以往技术的耐蚀钢的成分设计相比更适合于船舱内(货舱内)的氯离子影响的腐蚀环境且能够进一步抑制腐蚀的煤专
用船或矿/煤兼用船的船舱用耐蚀钢。
[0014]
本发明人通过研究而发现:在船舱内的钢板表面生成的锈层中包含β-feooh。因此,本发明人认为:在船舱内,不是以往所认为的硫酸根离子(so
42-)而是氯离子(cl-)成为腐蚀的原因,成为了中性氯化物环境和ph下降了的高浓度的氯化物环境(低ph高浓度氯化物环境)反复的腐蚀环境。具体而言,认为:煤装载于船舱中的状态(称为载货状态)的钢材与煤的界面的腐蚀环境是中性氯化物环境,另一方面,煤被从船舱卸货了的状态(称为空载状态)的钢材的表面的腐蚀环境是低ph高浓度氯化物环境。
[0015]
在载货、运输中,煤互相摩擦,生成煤的微粉末。可设想为在该环境中尤其影响到腐蚀的不是煤的大的块而是该微粉末。微粉末覆盖货舱底部的钢材,起到保持水分的作用。
[0016]
因而,推定为:在载货状态下,通过在港湾保管的煤中包含的氯离子、来源于海水的氯化钠、氯化钙及氯化镁等海盐以及雨、冷却水等水分,而成为在煤与钢材的表面之间总是存在包含氯离子的中性的溶液的中性氯化物环境。
[0017]
另一方面,推定为:在空载状态下,通过残留于船舱内的煤的微粉末与氯化物的混合物吸湿等而在钢材的表面形成氯离子浓化了的薄的水膜,伴随着腐蚀的进行,ph下降,钢材的表面成为低ph高浓度氯化物环境。
[0018]
因此,认为:将煤作为装载的货物的煤专用船或矿/煤兼用船的船舱内的腐蚀环境,与单纯的海水环境、仅将硬而几乎不生成微粉末的铁矿石作为装载的货物的情况不同。
[0019]
本发明人基于将煤作为装载的货物的船舱内成为了如上所述的中性氯化物环境和低ph高浓度氯化物环境反复的腐蚀环境这一推定,进行了抑制钢材的腐蚀的合金元素的研究。而且,本发明人发现:通过同时含有抑制中性氯化物环境中的腐蚀的cr、al或不论在中性氯化物环境、低ph高浓度氯化物环境的哪种环境下都抑制钢的腐蚀的ni与抑制低ph高浓度氯化物环境中的腐蚀的sn,能够显著地抑制腐蚀。
[0020]
本发明是基于这样的见解而完成的,其主旨如下。
[0021]
(1)本发明的一方案涉及的煤专用船或矿/煤兼用船的船舱用耐蚀钢,化学组成以质量%计含有c:0.01~0.20%、mn:0.10~2.00%、sn:0.05~0.50%、cr:0~5.00%、al:0~3.000%、ni:0~5.00%、sb:0~0.50%、cu:0~0.50%、mo:0~1.00%、w:0~1.00%、ti:0~0.100%、zr:0~0.200%、ca:0~0.0500%、mg:0~0.0500%、rem:0~0.0500%、nb:0~0.100%、v:0~0.100%、b:0~0.0100%、si:1.00%以下、p:0.050%以下、s:0.0300%以下、n:0.0080%以下、o:0.0100%以下,余量为fe及杂质,在所述化学组成中,满足下述式1~式3之中的至少一个。
[0022]
0.10≤[cr]≤5.00
ꢀꢀꢀꢀ…
式1
[0023]
0.100<[al]≤3.000
ꢀꢀ…
式2
[0024]
0.30≤[ni]≤5.00
ꢀꢀꢀꢀ…
式3
[0025]
在所述式1~式3中,[x]表示元素x的含量,其单位为质量%。
[0026]
(2)上述(1)所述的煤专用船或矿/煤兼用船的船舱用耐蚀钢,也可以以质量%计含有选自sb:0.01~0.50%、cu:0.01~0.50%、mo:0.05~1.00%和w:0.05~1.00%之中的1种或2种以上。
[0027]
(3)上述(1)或(2)所述的煤专用船或矿/煤兼用船的船舱用耐蚀钢,也可以以质量%计含有选自ti:0.005~0.100%、zr:0.005~0.200%、ca:0.0010~0.0500%、mg:
0.0010~0.0500%和rem:0.0010~0.0500%之中的1种或2种以上。
[0028]
(4)上述(1)~(3)的任一项所述的煤专用船或矿/煤兼用船的船舱用耐蚀钢,也可以以质量%计含有选自nb:0.005~0.100%、v:0.005~0.100%和b:0.0003~0.0100%之中的1种或2种以上。
[0029]
(5)本发明的另一方案涉及的煤专用船或矿/煤兼用船的船舱,采用上述(1)~(4)的任一项所述的船舱用耐蚀钢来制成。
[0030]
根据本发明的上述方案,能够提供在将煤作为装载的货物的船舱内的腐蚀环境下耐蚀性优异的煤专用船或矿/煤兼用船的船舱用耐蚀钢及船舱。而且,根据使用这样的煤专用船或矿/煤兼用船的船舱用耐蚀钢制造出的船舱,能够大幅降低由船舱内的腐蚀所引起的构件更换、再涂装所导致的维护成本。因此,本发明的产业上的贡献极其显著。
具体实施方式
[0031]
以下,对本发明的一实施方式涉及的煤专用船或矿/煤兼用船的船舱用耐蚀钢(以下,有时称为本实施方式涉及的船舱用耐蚀钢)进行详细说明。
[0032]
首先,对本实施方式涉及的船舱用耐蚀钢的化学组成进行叙述。表示化学组成中的各元素的含量的“%”意味着质量%。另外,在化学组成中的数值范围中,使用“~”表示的数值范围只要没有特别指定就意味着将在“~”的前后记载的数值作为下限值及上限值而包含的范围。由此,例如,0.01~0.20%意味着0.01%以上且0.20%以下的范围。另一方面,关于超过或小于,意味着不包含该值。
[0033]
(c:0.01~0.20%)
[0034]
c(碳)是使钢的强度增加的元素。为了充分得到该效果,将c含量设为0.01%以上。优选将c含量设为0.03%以上。
[0035]
另一方面,若c含量变得过量,则因渗碳体的生成而导致耐蚀性下降。因而,将c含量设为0.20%以下。优选将c含量设为0.15%以下。
[0036]
(mn:0.10~2.00%)
[0037]
mn(锰)是使钢的强度和韧性提高的元素。为了得到该效果,将mn含量设为0.10%以上。优选将mn含量设为0.20%以上,更优选设为0.50%以上。
[0038]
另一方面,mn是形成成为腐蚀的起点的mns的元素。为了避免钢材的耐蚀性的劣化,将mn含量设为2.00%以下。优选将mn含量设为1.50%以下,更优选设为1.20%以下。
[0039]
(sn:0.05~0.50%)
[0040]
sn(锡)是在低ph高浓度氯化物环境下降低钢的阳极溶解速度,另外抑制阴极反应的重要的元素。为了使空载状态的船舱内的耐蚀性提高,将sn含量设为0.05%以上。优选将sn含量设为0.07%以上,更优选设为0.10%以上。
[0041]
另一方面,若过量地含有sn,则会损害制造性。因而,将sn含量设为0.50%以下。优选将sn含量设为0.35%以下。
[0042]
(cr:0~5.00%)
[0043]
cr(铬)是在中性氯化物环境下大幅降低钢的阳极溶解速度的重要的元素。在利用cr来使载货状态的船舱内的耐蚀性提高的情况下,将cr含量设为0.10%以上。优选将cr含量设为0.20%以上,更优选设为0.30%以上。在利用al和/或ni来使载货状态的船舱内的耐
蚀性提高的情况下,cr含量也可以为0%,但cr与al、ni相比提高耐蚀性的效果大,因此优选含有cr。
[0044]
另一方面,若过量地含有cr,则焊接性下降。因而,将cr含量设为5.00%以下。优选将cr含量设为3.00%以下,更优选设为2.50%以下,进一步优选设为2.00%以下或0.80%以下、0.60%以下、0.50%以下。
[0045]
虽然一般认为cr使低ph高浓度氯化物环境下的耐蚀性下降,但是,通过与规定量的sn同时地含有,这样的不良影响消失。
[0046]
(al:0~3.000%)
[0047]
al(铝)是在中性氯化物环境下降低钢的阳极溶解速度的重要的元素。在利用al来使载货状态的船舱内的耐蚀性提高的情况下,将al的含量设为超过0.100%。但是,在利用cr和/或ni来使载货状态的船舱内的耐蚀性提高的情况下,al含量也可以为0.100%以下,也可以为0%。
[0048]
另一方面,若过量地含有al,则焊接性下降。因而,将al含量设为3.000%以下。优选将al含量设为2.500%以下,更优选设为2.000%以下。
[0049]
另外,al也是对钢的脱氧有效的元素。脱氧也能够采用al以外的元素来实现,al含量也可以为0%,但为了得到由al带来的脱氧效果,优选将al含量设为0.001%以上,更优选将al含量设为0.005%以上,进一步优选将al含量设为0.010%以上。
[0050]
(ni:0~5.00%)
[0051]
ni是使载货状态及空载状态的船舱内的耐蚀性提高的元素。在利用ni来使载货状态的船舱内的耐蚀性提高的情况下,将ni含量设为0.01%以上。更优选将ni含量设为0.05%以上。ni对于在热轧含有cu的钢时产生的表面瑕疵的抑制也是有效的。在利用cr和/或al来使船舱内的耐蚀性提高的情况下,ni含量也可以为0%。
[0052]
另一方面,ni含量的上限从成本的观点来看设为5.00%以下。优选将ni含量设为小于0.30%,更优选将ni含量设为0.20%以下。
[0053]
另一方面,为了在船舱内的腐蚀环境下进一步提高尤其是空载状态下的钢材的耐蚀性,也可以除了上述的成分以外还含有sb、cu、mo、w之中的1种或2种以上。
[0054]
另外,也可以以使耐蚀性下降的mns的生成的抑制、形态的控制为目的,除了上述的成分以外还含有ti、zr、ca、mg、rem之中的1种或2种以上。
[0055]
另外,为了提高钢材的强度,也可以除了上述的成分以外还含有nb、v、b之中的1种或2种以上。
[0056]
这些元素都未必需要含有,因此含量的下限为0%。
[0057]
(sb:0~0.50%)
[0058]
sb(锑)与sn同样是使空载状态下的耐蚀性提高的元素。在要获得该效果的情况下,优选将sb含量设为0.01%以上。更优选将sb含量设为0.05%以上。
[0059]
另一方面,若过量地含有sb,则会损害制造性。因而,即使在含有的情况下,也将sb含量设为0.50%以下。优选将sb含量设为0.35%以下。
[0060]
(cu:0~0.50%)
[0061]
cu(铜)与sn、sb同样是使空载状态下的耐蚀性提高的元素。在要获得该效果的情况下,优选将cu含量设为0.01%以上。更优选将cu含量设为0.05%以上。另外,若使cu和sn
共存,则船舱内的耐蚀性显著提高,因此优选共存。
[0062]
另一方面,若过量地含有cu,则会损害制造性。因而,即使在含有的情况下,也将cu含量设为0.50%以下。优选将cu含量设为0.35%以下。
[0063]
(mo:0~1.00%)
[0064]
mo(钼)是形成含氧酸根离子moo
42-而在酸性溶液中作为抑制剂发挥作用,来抑制钢的阳极溶解的元素。为了使空载状态下的耐蚀性提高,优选将mo含量设为0.05%以上。更优选将mo含量设为0.10%以上。另一方面,mo含量即使超过1.00%,其效果也饱和。因而,即使在含有的情况下,也将mo含量设为1.00%以下。优选将mo含量设为0.50%以下。
[0065]
(w:0~1.00%)
[0066]
w(钨)与mo同样是形成含氧酸根离子wo
4-而在酸性溶液中作为抑制剂发挥作用,来抑制钢的阳极溶解的元素。为了使空载状态下的耐蚀性提高,优选将w含量设为0.05%以上。更优选将w含量设为0.10%以上。
[0067]
另一方面,w含量即使超过1.00%,其效果也饱和。因而,即使在含有的情况下,也将w含量设为1.00%以下。优选将w含量设为0.50%以下。
[0068]
(ti:0~0.100%)
[0069]
ti(钛)是与s结合而形成硫化物、碳硫化物的元素,是具有抑制成为腐蚀的起点而使耐蚀性劣化的mns的生成的效果的元素。在要获得该效果的情况下,优选将ti含量设为0.005%以上。更优选将ti含量设为0.010%以上。
[0070]
另一方面,若过量地含有ti,则有时韧性劣化。因而,即使在含有的情况下,ti含量也设为0.100%以下。优选将ti含量设为0.050%以下。
[0071]
(zr:0~0.200%)
[0072]
zr(锆)是与s结合而形成硫化物的元素,是具有抑制成为腐蚀的起点而使耐蚀性劣化的mns的生成的效果的元素。在要获得该效果的情况下,优选将zr含量设为0.005%以上。更优选将zr含量设为0.010%以上。
[0073]
另一方面,若过量地含有zr,则有时韧性劣化。因而,即使在含有的情况下,zr含量也设为0.200%以下。优选将zr含量设为0.100%以下,更优选设为0.050%以下。
[0074]
(ca:0~0.0500%)
[0075]
(mg:0~0.0500%)
[0076]
(rem:0~0.0500%)
[0077]
ca、mg、rem是与s结合而形成硫化物、碳硫化物的元素,是具有抑制成为腐蚀的起点而使耐蚀性劣化的mns的生成的效果的元素。因而,在本实施方式涉及的船舱用耐蚀钢中,也可以含有从这些元素中选择的1种或2种以上。在要抑制成为腐蚀的起点而使耐蚀性劣化的mns的生成的情况下,优选将ca、mg、rem之中的任意的元素的含量设为0.0010%以上。另外,它们的硫化物在腐蚀反应时溶于水而成为碱,具有抑制钢材界面的ph下降的作用。因而,更优选将任意的元素的含量设为0.0030%以上,进一步优选设为0.0050%以上。
[0078]
另一方面,ca、mg、rem即使过量地含有,其效果也饱和。因而,即使在含有的情况下,ca、mg、rem的含量也分别设为0.0500%以下。优选设为0.0300%以下,更优选设为0.0100%以下。
[0079]
rem是稀土金属元素、即sc、y、la、ce、pr、nd、pm、sm、eu、gd、tb、dy、ho、er、tm、yb和
lu的总称。rem含量意指这些元素的合计含量。
[0080]
(nb:0~0.100%)
[0081]
(v:0~0.100%)
[0082]
nb、v是形成碳化物、氮化物而提高钢的强度的元素。在要获得该效果的情况下,优选将至少任一元素含有0.005%以上。更优选将nb、v之中的任意的元素的含量设为0.010%以上。
[0083]
另一方面,若过量地含有nb、v,则钢材的韧性下降。因而,即使在含有的情况下,nb、v的含量也分别设为0.100%以下。优选设为0.050%以下。
[0084]
(b:0~0.0100%)
[0085]
b是提高钢的淬火性而使强度提高的元素。在要获得该效果的情况下,优选将b含量设为0.0003%以上。更优选将b含量设为0.0005%以上,进一步优选设为0.0010%以上。
[0086]
另一方面,若过量地含有b,则有时会损害钢材的机械特性。因而,即使在含有的情况下,b含量也设为0.0100%以下。优选将b含量设为0.0050%以下,更优选设为0.0030%以下。
[0087]
(si:1.00%以下)
[0088]
si(硅)是作为脱氧剂有用并且使钢的强度增加的元素。脱氧也能够采用si以外的元素来实现,si含量也可以为0%,但在要获得脱氧的效果的情况下,优选将si含量设为0.01%以上。更优选将si含量设为0.02%以上,进一步优选设为0.05%以上。
[0089]
另一方面,若si含量超过1.00%,则会损害母材及焊接接头部的韧性。因而,将si含量设为1.00%以下。优选将si含量设为0.50%以下,更优选设为0.30%以下。
[0090]
(p:0.050%以下)
[0091]
p(磷)是一般作为杂质而含有的元素,是使钢材的机械特性、焊接性劣化的元素。因而,将p含量设为0.050%以下。优选为0.025%以下。p含量也可以为0%,但从制造成本的观点来看,也可以含有0.0001%以上的p。另外,p是使氯化物环境下的钢的耐蚀性提高的元素,也可以以获得该效果为目的而将p含量设为0.001%以上。
[0092]
(s:0.0300%以下)
[0093]
s(硫)是杂质,是形成促进腐蚀的mns的元素。因而,将s含量限制为0.0300%以下。s含量优选为0.0050%以下,更优选为0.0030%以下。s含量也可以为0%,但从制造成本的观点来看,也可以将s含量设为0.0001%以上。
[0094]
(n:0.0080%以下)
[0095]
n(氮)是杂质,是形成使钢材的韧性下降的粗大的氮化物的元素。为了抑制粗大的氮化物的形成,将n含量设为0.0080%以下。优选将n含量设为0.0060%以下。n含量的下限也可以为0%,但从制造成本的观点来看,也可以为0.0010%以上。
[0096]
(o:0.0100%以下)
[0097]
o(氧)是杂质,是形成使钢材的韧性下降的粗大的氧化物的元素。为了抑制粗大的氧化物的形成,将o含量设为0.0100%以下。优选将o含量设为0.0060%以下,更优选设为0.0040%以下。o含量的下限也可以为0%,但从制造成本的观点来看,也可以为0.0001%以上。
[0098]
本实施方式涉及的船舱用耐蚀钢的上述各成分以外的成分基本上是fe及杂质。在
此,所谓杂质,是在工业性制造钢板时以矿石、废料等之类的原料为首而由于制造工序的各种因素而混入的成分,且意指在不对本实施方式涉及的船舱用耐蚀钢的特性造成不良影响的范围内容许的成分。
[0099]
(满足0.10≤[cr]≤5.00
…
式1、0.100<[al]≤3.000
…
式2、0.30≤[ni]≤5.00
…
式3之中的至少一个)
[0100]
如上所述,为了在以煤为装载的货物的船舱内,使中性氯化物环境下的耐蚀性提高,需要含有0.10%以上的cr、超过0.100%的al、0.30%以上的ni之中的至少一者以上。即,在本实施方式涉及的船舱用耐蚀钢中,需要在将各元素的含量设为上述的范围的基础上满足以下的式1~式3之中的至少1个。
[0101]
0.10≤[cr]≤5.00
···
式1
[0102]
0.100<[al]≤3.000
···
式2
[0103]
0.30≤[ni]≤5.00
···
式3
[0104]
在所述式1~式3中,[x]表示元素x的含量,其单位为质量%。
[0105]
cr含量也可以设为以下的式1
’
的范围。
[0106]
0.10≤[cr]≤3.00
···
式1
’
[0107]
在本实施方式中,船舱用耐蚀钢的形状没有特别的限定,只要是钢板、钢带、型钢、钢管、棒钢、钢线等即可。钢板、钢带、型钢、钢管等钢材的厚度没有特别的限定,但通常为3~50mm。优选的下限为6mm,更优选的下限为10mm。另外,厚度的优选的上限为40mm,更优选的上限为30mm。
[0108]
另外,在本实施方式涉及的船舱用耐蚀钢中,关于金属组织没有限定。金属组织只要根据所要求的强度等机械特性来适当选择铁素体-珠光体、贝氏体或马氏体等即可。
[0109]
接着,对本发明的一实施方式涉及的煤专用船或矿/煤兼用船的船舱(本实施方式涉及的船舱)进行说明。
[0110]
本实施方式涉及的船舱,通过将上述的本实施方式涉及的船舱用耐蚀钢作为材料,将它们根据需要进行加工,并采用焊接等来组合从而制造。关于本实施方式涉及的船舱用耐蚀钢具有的化学组成,在钢板成为船舱的过程中不变化。因此,关于本实施方式涉及的船舱的化学组成的范围及限定理由,与上述的本实施方式涉及的船舱用耐蚀钢实质上相同。
[0111]
即,可以说本实施方式涉及的船舱具备本实施方式涉及的船舱用耐蚀钢。
[0112]
接着,对本实施方式涉及的船舱用耐蚀钢及本实施方式涉及的船舱的制造方法进行说明。在本实施方式涉及的船舱用耐蚀钢中,包括实施热轧、进而根据需要实施冷轧从而制造的钢板、型钢、钢管等。
[0113]
本实施方式涉及的船舱用耐蚀钢,通过利用常规方法熔炼钢,将成分调整为上述的范围后,进行铸造而得到钢坯,将所述钢坯热轧,进而根据需要实施冷轧来制造。在热轧后,也可以原样地水冷或空冷后,再加热而进行淬火、回火。在热轧后,也可以卷取成卷状。也可以在热轧后,进行冷轧,进而实施热处理。
[0114]
在本实施方式中,在制造钢管的情况下,可以将钢板成形为管状并焊接,能够制成为uo钢管、电焊钢管、锻接钢管、螺旋钢管等。
[0115]
对钢坯实施热挤压、穿孔轧制而制造的无缝钢管也包括在本实施方式的船舱用耐
蚀钢中。
[0116]
本实施方式涉及的船舱,只要将这样得到的本实施方式涉及的船舱用耐蚀钢作为材料,采用公知的方法来制造即可。
[0117]
实施例
[0118]
以下,关于本发明的煤专用船或矿/煤兼用船的船舱用耐蚀钢示出实施例。但是,以下记载的实施例是沿着具体的例子来进行说明的,并不限定本发明的权利要求的内容。
[0119]
从后述的表1、表2中所示的化学组成(余量为fe及杂质)的钢坯制作(制取)了长度100mm、宽度60mm、厚度5mm的试样。对试样的表面实施了喷砂处理以使得粗糙度成为sa2.5(iso8501-1)以上。使用这些试样进行了模拟煤成为装载的货物的船舱内的环境的腐蚀试验。
[0120]
腐蚀试验在将温度保持为40℃且将相对湿度保持为98%的试验槽内进行。将“在使含有人造海水的粉状的煤装载于试样上的状态下在试验槽内保持1星期来再现载货状态,接着,在将附着于试样的表面的煤利用刮刀轻轻除去的状态下在试验槽内保持1星期来再现空载状态”的工序设为1循环。将该循环进行了6循环后,利用刮刀除去试样表面的锈,利用柠檬酸铵溶液除去锈。
[0121]
然后,测定试样的重量,并从试验前的试样的重量减去,从而求出腐蚀减量,根据6循环(12星期)的腐蚀减量算出腐蚀速度[mm/y]。y意指年。
[0122]
后述的表1、表2中所示的钢no.101是不含有sn且cr、al、ni的含量不满足式1~式3之中的任何一个的以往钢。可知:钢no.101的腐蚀速度与暴露于实际的船舱内的钢材的腐蚀速度同等,通过上述的腐蚀试验成功模拟了船舱内的环境。因而,各钢的耐蚀性,采用表1、表2中的各钢的腐蚀速度相对于钢no.101的腐蚀速度之比即腐蚀速度比(%)来进行评价。
[0123]
将化学组成和前述的试验的结果示于表1、表2。
[0124]
表1
[0125][0126]
表2
[0127][0128]
如表1、表2所示,钢no.1~11、21~36、41~51,相对于钢no.101,腐蚀速度被抑制到70.0%以下,耐蚀性良好。
[0129]
另一方面,含有cr且al含量少且不含ni及sn的钢no.102、和sn含量不足的钢no.103,耐蚀性的改善效果不充分。
[0130]
另外,cr含量、al含量、ni含量、sn含量全部不足的钢no.104,与钢no.101相比,腐蚀减量变多。认为这是因为:没有得到充分的耐蚀性提高效果,而且,在酸性环境中,微量地含有的cr反而造成不良影响。
[0131]
充分含有sn但cr含量、al含量、ni含量不足的钢no.105,在中性氯化物环境中的腐蚀抑制效果变小,没有看到充分的耐蚀性提高。
[0132]
含有超过0.100%的al但不含sn的钢no.202,耐蚀性的改善效果不充分。充分含有al、cr但sn含量不足的no.204、钢no.205,在低ph高浓度氯化物环境中的腐蚀抑制效果变小,没有看到充分的耐蚀性提高效果。
[0133]
含有0.30%以上的ni且不含sn的钢no.402、和含有ni和sn但sn含量不足的钢no.403,耐蚀性的改善效果不充分。
[0134]
另外,充分含有sn但cr含量、al含量、ni含量均不满足式1~式3的钢no.404,在中性氯化物环境中的腐蚀抑制效果变小,没有看到充分的耐蚀性提高。
[0135]
cr含量、al含量、ni含量均不满足式1~式3且sn含量也不足的钢no.405,不论在酸性环境和酸性氯化物环境的哪个环境中都腐蚀抑制效果小,耐蚀性没有提高。
[0136]
产业上的可利用性
[0137]
根据本发明,能够大幅降低由船舱内的腐蚀引起的构件更换、再涂装所导致的维护成本,因此产业上的贡献极大。
起点商标作为专业知识产权交易平台,可以帮助大家解决很多问题,如果大家想要了解更多知产交易信息请点击 【在线咨询】或添加微信 【19522093243】与客服一对一沟通,为大家解决相关问题。
此文章来源于网络,如有侵权,请联系删除



tips