一种大型设备油缸修复加工及再制造技术的制作方法



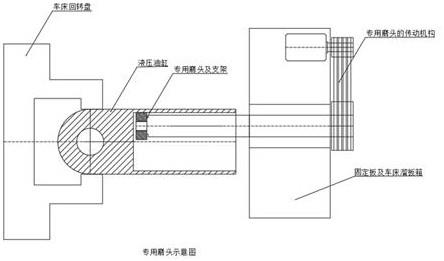
[0001]
本发明涉及油缸技术领域,具体是一种大型设备油缸修复加工及再制造技术。
背景技术:
[0002]
液压油缸是工程机械中的重要部件,承担传递动力、完成作业动作、提高作业效率等功能。因此液压油缸的质量直接决定工程机械的整体质量,所以必须确保液压油缸质量良好。
[0003]
液压油缸是一个耐用部件,它的制造较为复杂。同时液压油缸制造消耗大量钢材,所以大部分企业均希望对液压油缸进行多次修复利用。由于修复油缸较制造油缸难度加大,而企业重视不够导致修复油缸的寿命出力等都较新件差距很大。
[0004]
下面以大型矿车用的前后悬挂为例介绍液压油缸的修复工艺。
[0005]
全国有大型矿车约1.2万台,每台车每年平均消耗悬挂约1个,每个悬挂约3吨,若全部换新光钢材消耗就是3.6万吨,若50%~70%能修旧如新再使用,每年节约钢材1.8~2.5万吨,悬挂修复意义重大。悬挂是长时间往复运动的特殊液压油缸,其制造难度很大,质量稍有瑕疵其寿命性能都不能满足设备要求。正常情况下悬挂失效主要表现为各个往复部件的磨损及橡胶密封件密封失效;造成悬挂泄漏,承载能力下降,必须更换;换下来的悬挂大部分企业是对悬挂换一下密封件后继续使用,结果很不理想,多少使用很短时间就会再次泄漏,又被迫换下。为此我们跟踪研究了多年,探索出了一套行之有效的修复工艺;因此,本发明提供了一种大型设备油缸修复加工及再制造技术,以解决上述提出的问题。
技术实现要素:
[0006]
本发明的目的在于提供一种大型设备油缸修复加工及再制造技术,以解决上述背景技术中提出的问题。
[0007]
为实现上述目的,本发明提供如下技术方案:一种大型设备油缸修复加工及再制造技术,包括油缸修复加工和再制造技术,所述油缸修复加工的具体步骤如下:第一步:缸筒的修复,采用镗、磨、滚压一体化工艺进行,先确定镗孔尺寸,将原有的硬化层除去即可;第二步:再对缸筒内壁进行磨削加工提高表面光洁度;第三步:最后进行滚压加工恢复缸筒内壁原来的表面硬度;第四步:活塞杆修复,首先对活塞杆进行去铬处理,去铬不能在电镀槽里去铬,而是在磨床是进行磨削加工,磨削加工时的磨削速度较正常磨削速度要快15%-25%,磨削进给量小40%-50%,将镀铬层全部磨削去掉;第五步:再进行镀铬处理,镀铬层厚为原设计的110%-130%,镀铬完成后再次进行磨削加工,完成活塞杆的加工;所述油缸再制造技术的具体步骤如下:
第一步:缸筒、活塞杆经过上述处理后较原设计尺寸有所变化,缸筒内径要大于活塞杆的直径,因此原设计选用的密封件不能直接套用,必须调整密封件的压缩量,对此有两种方法,一、优先采用的,选用原设计密封件,在密封件沟槽里增加辅助密封,这种方法适用于缸筒内经、活塞杆直径增大或缩小在1毫米以内的使用,且可以多次维修,费用较低,二、定制特殊的密封件,当缸筒内径和活塞杆直径尺寸变化较大:1~2毫米时,要进行配置定做的密封件,这种方法修理费用较高,尽量不要采用;第二步:整个液压油缸修复后,经现场使用考核,寿命为原件的120%,出力性能、运动轨迹等与原件一致,满足整体设备的性能要求;第三步:液压油缸不是使用一次就废弃的易耗品,而是一个可以反复修理的耐用品,但同时要对液压油缸的修理次数进行严格合理的规定,因为钢材的疲劳损坏是不能修复的,液压油缸在高压油的作用下,实际就是压力容器,所以缸筒、活塞杆都会发生疲劳损坏,在实践中我们发现大负荷,重负载的工程机械液压油缸的修理次数4次最为合理,其他小负荷的机械液压油缸修理次数可以8-10次。
[0008]
作为本发明进一步的方案:所述油缸修复加工的第一步中,镗孔的加工量为0.1~0.2毫米。
[0009]
作为本发明再进一步的方案:所述油缸修复加工的第四步中,磨削加工时的磨削速度较正常磨削速度要快20%。
[0010]
作为本发明再进一步的方案:所述油缸修复加工的第四步中,磨削进给量小50%。
[0011]
作为本发明再进一步的方案:所述油缸修复加工的第五步中,镀铬层厚为原设计的120%。
[0012]
与现有技术相比,本发明的有益效果是:本发明设计的液压油缸的修理是很有意义的,重点是要有一个好的修理工艺,不仅能为企业节约费用,满足生产急需,降低生产成本,本发明还能节约钢材的使用,降低能源消耗,正真节能降耗。
附图说明
[0013]
图1为一种大型设备油缸修复加工及再制造技术的专用磨头的结构示意图。
[0014]
图2为一种大型设备油缸修复加工及再制造技术的专用滚压头的结构示意图。
具体实施方式
[0015]
下面将结合本发明实施例中的附图,对本发明实施例中的技术方案进行清楚、完整地描述,显然,所描述的实施例仅仅是本发明一部分实施例,而不是全部的实施例。基于本发明中的实施例,本领域普通技术人员在没有做出创造性劳动前提下所获得的所有其他实施例,都属于本发明保护的范围。
[0016]
请参阅图1~2,本发明实施例中,一种大型设备油缸修复加工及再制造技术,1、缸筒的修复:采用镗、磨、滚压一体化工艺进行。
[0017]
根据缸筒内径磨损情况,确定镗孔尺寸,一般镗孔的加工量很小约0.1~0.2毫米,将原有的硬化层除去即可。
[0018]
再对缸筒内壁进行磨削加工提高表面光洁度,一般缸筒内圆都是用内圆磨或绗磨机进行磨削加工,但已成型的油缸缸筒用上述方法很难保证加工完整及加工精度,为此我
们改变了传统的磨削方式利用普通车床配合专门设计的磨头进行磨削加工,缸筒有车床带动高速旋转,专用磨头安装在车床的跟刀架上并能按要求调整磨削量,调整磨头转速,此方法磨削缸筒内径又快又好(见图1)。
[0019]
最后进行滚压加工恢复缸筒内壁原来的表面硬度,传统的滚压加工是用滚压头,只适用于通孔的缸筒加工,而一边封闭了的缸筒无法滚压,我们同样利用普通车床,配合专门设计的滚压轮进行滚压加工,滚压质量高于传统滚压头滚压的质量,表面硬度均达到设计要求(见图2)。
[0020]
滚压加工是对金属表面进行硬化的过程,传统的滚压头上有多个滚子随工件转动对表面进行滚压,滚压轨迹有重合和间断现象,重合部分会使金属表面过度硬化压,间断部分会使表面没有硬化层,因此,传统滚压加工的表面质量不均匀,直接影响缸筒寿命。滚轮滚压加工的滚压轨迹连续稳定无重合现象,所以表面硬化质量均匀,缸筒寿命长。缸筒经过上述工序的加工基本恢复到新件一样的质量水平,做到了修旧如新。
[0021]
2、活塞杆修复:首先对活塞杆进行去铬处理,去铬不能在电镀槽里去铬,而是在磨床是进行磨削加工,磨削加工时的磨削速度较正常磨削速度要快20%,磨削进给量小50%。直到将镀铬层全部磨削去掉。再进行镀铬处理,镀铬层厚为原设计的120%。镀铬完成后再次进行磨削加工,直到活塞杆表面达到设计要求。
[0022]
3、缸筒、活塞杆经过上述处理后较原设计尺寸有所变化,缸筒内径要大一些,活塞杆直径要小一些。因此原设计选用的密封件不能直接套用,必须调整密封件的压缩量。对此有两种方法,一、优先采用的,选用原设计密封件,在密封件沟槽里增加辅助密封,这种方法适用于缸筒内经、活塞杆直径增大或缩小在1毫米以内的使用,且可以多次维修,费用较低。二、定制特殊的密封件,当缸筒内径和活塞杆直径尺寸变化较大:1~2毫米时,要进行配置定做的密封件,这种方法修理费用较高,尽量不要采用。
[0023]
4、整个液压油缸修复后,经现场使用考核,寿命为原件的120%,出力性能、运动轨迹等与原件一致,满足整体设备的性能要求。
[0024]
5、液压油缸不是使用一次就废弃的易耗品,而是一个可以反复修理的耐用品。但同时要对液压油缸的修理次数进行严格合理的规定,因为钢材的疲劳损坏是不能修复的,液压油缸在高压油的作用下,实际就是压力容器,所以缸筒、活塞杆都会发生疲劳损坏。在实践中我们发现大负荷,重负载的工程机械液压油缸的修理次数4次最为合理,其他小负荷的机械液压油缸修理次数可以8次甚至更多。
[0025]
本发明的工作原理是:本发明设计的液压油缸的修理是很有意义的,重点是要有一个好的修理工艺,不仅能为企业节约费用,满足生产急需,降低生产成本,本发明还能节约钢材的使用,降低能源消耗,正真节能降耗。
[0026]
以上所述,仅为本发明较佳的具体实施方式,但本发明的保护范围并不局限于此,任何熟悉本技术领域的技术人员在本发明揭露的技术范围内,根据本发明的技术方案及其发明构思加以等同替换或改变,都应涵盖在本发明的保护范围之内。
起点商标作为专业知识产权交易平台,可以帮助大家解决很多问题,如果大家想要了解更多知产交易信息请点击 【在线咨询】或添加微信 【19522093243】与客服一对一沟通,为大家解决相关问题。
此文章来源于网络,如有侵权,请联系删除



tips