薄壁筒体精密控形设备的制作方法



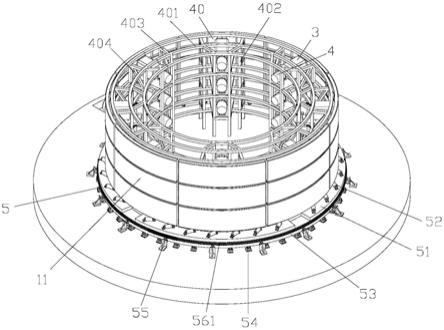
[0001]
本实用新型涉及一种薄壁筒体控形设备,特别是超大直径薄壁筒体的精密控形设备。
背景技术:
[0002]
超大直径薄壁筒形件广泛应用于石油石化、海洋装备等领域,其加工方式可采用环轧与热处理的方式进行。筒件在环轧和热处理后的冷却过程中会出现不规则变形,导致工件尺寸无法满足使用要求。对薄壁筒体常用的矫形方法有压力机点压校形、四辊矫圆机校形和涨形校形等方式。
[0003]
上述校形方法均为机械校形方法,对于结构尺寸较小、变形程度小、整体精度要求不高的工件基本能够满足要求。但对于超大直径薄壁筒形件,由于存在着不规则变形难以矫正、造成筒体壁厚减薄、应力过大造成新的变形等原理性缺陷及难以制造相应的加工装备,使用上述方法均难以实现筒体的精密控形,无法满足产品的尺寸与性能需求。
技术实现要素:
[0004]
有鉴于此,本实用新型的主要目的在于提供一种用于对超大直径薄壁筒体精密控形设备,控形精度高,壁厚不减薄,精密控形后残余应力小的显著优点,能够简化后续工序。同时内胎模锥度可调,可适应于锥筒等工件的精密控形。
[0005]
为达到上述目的,本实用新型是通过如下技术方案来实现的:一种薄壁筒体精密控形设备,包括:
[0006]
旋转支撑台,用于校形过程中工件的支撑和冷却收缩过程中工件的旋转;
[0007]
精密控形内胎模,绕所述旋转支撑台圆心均匀分布,用以提供控形时所需的圆弧面和工作时校形力传导;
[0008]
液压推缸,与所述精密控形内胎模连接,用于精确精密控形内胎模微距移动;
[0009]
导向装置,安装在所述液压推缸的活塞杆上,用于液压推缸轴向移动的导向及导向方向的定位;
[0010]
支架,以所述旋转支撑台圆心为中心,呈圆环状安装在地面,用于固定液压推缸和导向装置。
[0011]
由上,通过液压推缸精确精密控形内胎模微距移动,利用高温工件冷却过程中的收缩效应,采用可调式圆周内胎模,通过控制特定弧度的精密控形内胎模位置限制薄壁筒形件的收缩范围,具有控形精度高,壁厚不减薄,精密控形后残余应力小的显著优点,能够简化后续工序。同时精密控形内胎模锥度可调(上下内胎模推出距离不同,实现垂直方向上为筒形面或锥度面),可适应于锥筒等工件的精密控形。
[0012]
可选的,所述支架采用桁架结构,其上具有多个用于安装导向装置和液压推缸的网格,该网格沿所述旋转支撑台轴向分布有多层,每层网格沿所述旋转支撑台径向间隔均匀的排布。
[0013]
由上,采用桁架结构,将推缸支撑架连接成整体,安装过程中保证导向装置和液压推缸安装和使用精度;轴向分布的多层网格,可以方便地根据工件的高度调整导向装置和液压推缸安装层数,用于满足对不同高度工件的控形。
[0014]
进一步地,所述支架包括同一水平方向沿所述旋转支撑台径向从内到外设置的三根圆形的横梁,竖直设置在地面的多根立柱分别与这些横梁相接,通过相接的横梁与立柱形成所述网格。
[0015]
由上,采用横梁和立柱形成的网格,在满足安装导向装置和液压推缸需求下,减轻整个支架的重量,结构简单,也便于导向装置和液压推缸的安装。
[0016]
更进一步地,位于外侧的两根圆形的横梁与立柱之间设置有水平梁,在上下相邻的两根水平梁之间设置有加强筋。
[0017]
由上,加强筋能进一步提高支架的整体稳定性,保证导向装置和液压推缸安装和使用精度。
[0018]
可选的,所述精密控形内胎模由多组高刚度内胎模组成,所述内胎模胎膜面弧度与所加工工件内径相匹配,通过内胎模胎膜面位置限制薄壁筒形件的收缩范围。
[0019]
由上,将整个圆周切分为多个单元,对每个单元分别布置内胎模,每单元高度随工件高度调整,必要时可多层布置通过控制特定弧度的内胎模胎膜面位置限制薄壁筒形件的收缩范围,使其符合工件尺寸要求。
[0020]
可选的,所述旋转支撑台包括:环状的转台骨架、支撑座、工件支撑滚轮、支撑轮以及定心轮,
[0021]
所述支撑轮以转台骨架圆心为中心均匀安装在地面、并与所述转台骨架底部具有的轨道啮合;
[0022]
所述转台骨架上端面固定有环状的支撑座,所述工件支撑滚轮绕所述转台骨架圆心斜向均匀布置在支撑座上;
[0023]
所述定心轮绕转台骨架圆心均匀安装在地面上,与所述转台骨架外圆周相抵接,用于保证整个设备在工作时的旋转始终围绕旋转支撑台中心运行;
[0024]
还包括用于使转台骨架沿支撑轮旋转的传动系统。
[0025]
由上,支撑轮支撑在旋转支撑台的中心位置,设计多组支撑轮提供旋转支撑台和工件的承重,在保证为滚动摩擦的同时,平台为一个平面,满足整个装置的平稳支撑。定心轮固定在地面上,其中心为旋转支撑台中心,保证整个设备在工作时的旋转始终围绕旋转支撑台中心运行。
[0026]
进一步地,所述传动系统包括安装在转台骨架外侧的链条、与链条啮合的链轮以及用于驱动链轮旋转的减速电机,通过链传动实现工件旋转支撑台的旋转,用于检测过程中为旋转支撑台旋转提供动力。
[0027]
由上,在检测过程中为旋转支撑台旋转提供动力,方便尺寸检测装置检测工件圆度及尺寸,保证工件校形尺寸。
[0028]
可选的,所述导向装置还包括用于将其安装在所述支架上的推缸支撑架,所述推缸支撑架由高强度结构钢采用分体式结构组成,所述液压推缸卡扣在推缸支撑架上。
[0029]
由上,推缸支撑架是校形设备中内胎模、导向装置和液压推缸的支撑部分,内胎模及导向装置固定在推缸支撑架上,实现导向位置及导向方向的定位和工作时校形力传导。
附图说明
[0030]
图1为本实用新型薄壁筒体精密控形设备的结构示意图;
[0031]
图2为本实用新型图1的俯视图;
[0032]
图3为本实用新型图1的侧视图;
[0033]
图4为本实用新型图3的a-a视图;
[0034]
图5为本实用新型图1中旋转支撑台的结构示意图;
[0035]
图6为本实用新型图1中内胎膜、液压推缸、导向装置以及推缸支撑架的连接结构示意图。
具体实施方式
[0036]
下面参照附图1-6对本实用新型所述的薄壁筒体精密控形设备的具体实施方式进行详细的说明。
[0037]
实施例1。本实用新型优选实施例提供的薄壁筒体精密控形设备,包括精密控形内胎模1、液压推缸2、导向装置3、支架4、旋转支撑台5及控制系统,控制系统主要通过传感器监测液压位置与动作,通过pic实现动作控制。
[0038]
由图1、图3所示,精密控形内胎模1由多组高刚度内胎模11组成,其作用是利用高温工件冷却过程中的收缩效应,通过控制特定弧度的内胎模11胎膜面位置限制薄壁筒形件的收缩范围,使其符合工件尺寸要求。本实施例中胎膜面由8组24个((也可以调整为36个(12组)))高刚度内胎模11组成,其弧度与所加工工件内径相匹配,可以是筒型件也可以是锥度面,内胎模11采用铸锻后机加工件,保证其整体刚度好。内胎模机加工工序中,应对内胎模11直径误差、外壁粗糙度等提出要求使筒体在定型控形时,在保确工件形状准确下,能自由收缩而不损伤筒体内壁。内胎模11及导向装置3部分是控形设备的主要工作部分,提供控形时所需的圆弧面。设计在将整个圆周切分为多个单元,对每个单元分别布置内胎模11,每单元高度随工件高度调整,必要时可多层布置。内胎模11设计时考虑热膨胀与内胎模动作等情况给予内胎模之间足够的余量。内胎模11及导向装置3作为整体安装在支架4上。安装时,导向装置3从支架4后侧安装,内胎模11从支架4前侧安装,方便设备各个部分的维护。
[0039]
由图1、图6所示,液压推缸2为数字伺服液压推缸,液压推缸2卡扣在推缸支撑架31上,推缸支撑架31为导向装置3一部分,导向装置3可使用螺栓连接或焊接方式固定推缸支撑架31上,具体包括多套数字伺服液压油缸,分别安装在精密控形内胎模1后方,用于精确精密控形内胎模1微距移动,同时通过液压控制实现位置锁定。
[0040]
由图6所示,推缸支撑架3由高强度结构钢采用分体式结构组成。推缸支撑架3是校形设备中内胎模11、导向装置3和液压推缸2的支撑部分,导向装置3为较厚的耐热钢制成的导向钢套,防止液压推缸因安装、磨损、热膨胀等因素发生偏转导致圆弧面偏移。内胎模11及导向装置3固定在推缸支撑架3上,实现导向位置及导向方向的定位和工作时校形力传导。
[0041]
由图1所示,支架4为型钢焊接而成。推缸支撑架3可采用螺栓连接或焊接方式固定在支架4上,支架4采用桁架结构,将推缸支撑架31连接成整体,安装过程中需保证其安装和使用精度。本实施例中,支架4上具有多个用于安装导向装置3和液压推缸2的网格40,该网格40沿旋转支撑台5轴向分布有多层,每层网格40沿旋转支撑台5径向间隔均匀的排布。更
为具体地,支架4包括同一水平方向沿旋转支撑台5径向从内到外设置的三根圆形的横梁401,竖直设置在地面的多根立柱402分别与这些横梁401相接,通过相接的横梁401与立柱402形成所述网格40。并且,位于外侧的两根圆形的横梁401与立柱402之间设置有水平梁403,在上下相邻的两根水平梁403之间设置有加强筋404,采用横梁401和立柱402形成的网格40,在满足安装导向装置3和液压推缸2需求下,减轻整个支架4的重量,结构简单,也便于导向装置3和液压推缸2的安装。加强筋404能进一步提高支架4的整体稳定性,保证导向装置3和液压推缸2安装和使用精度。
[0042]
由图3、图4、图5所示,旋转支撑台5是工件的支承结构,由支撑座51、工件支撑滚轮52、环状的转台骨架53、支撑轮54、定心轮55和传动系统56组成。旋转支撑台5满足校形过程中工件的支撑和冷却收缩过程中工件的旋转,保证工件校形后的尺寸。其中,支撑轮54以转台骨架53圆心为中心均匀安装在地面、并与转台骨架53底部具有的轨道啮合,多个轮组可以满足工件承重;转台骨架53上端面固定有环状的支撑座51,工件支撑滚轮52绕转台骨架53圆心斜向均匀布置在支撑座51上;定心轮55绕转台骨架53圆心均匀安装在地面上,与转台骨架53外圆周相抵接,用于保证整个设备在工作时的旋转始终围绕旋转支撑台中心运行;传动系统56用于使转台骨架53沿支撑轮54旋转,包括安装在转台骨架53外侧的链条561、与链条561啮合的链轮562以及用于驱动链轮562旋转的减速电机563,通过链传动实现工件旋转支撑台的旋转,用于检测过程中为旋转支撑台5旋转提供动力。传动系统在检测过程中为旋转支撑台5旋转提供动力,方便尺寸检测装置检测工件圆度及尺寸,保证工件校形尺寸。
[0043]
其中,工件通过吊装放置在沿旋转支撑台5圆心斜向均匀布置的工件支撑滚轮52上,工件支撑滚轮52通过螺栓连接固定在支撑座51上,支撑座51及转台骨架53焊接为一个整体,由使用螺栓固定在地面上的支撑轮54支撑,转台骨架53底部具有轨道,旋转支撑台5可以沿轨道移动,多个轮组可以满足工件承重。工件冷却收缩的过程中,工件底部向心收缩,放置在旋转支撑台5上的工件与旋转支撑台5作为整体在沿轨道进行向心滑动,将滑动摩擦转变为滚动摩擦,减小摩擦力对工件底部收缩的影响,保证工件上部和底部最大限度地均匀收缩。
[0044]
更为具体地,转台骨架53采用矩形方管焊接而成,四周为钢制旋转支撑台外壳,保证旋转支撑台形成一个整体,校形设备工作时,工件及支撑座51的重量均施加在转台骨架53上。支撑轮54支撑在旋转支撑台5的中心位置,设计多组支撑轮54提供旋转支撑台5和工件的承重,在保证为滚动摩擦的同时,平台为一个平面,满足整个装置的平稳支撑。定心轮55固定在地面上,其中心为旋转支撑台中心,保证整个设备在工作时的旋转始终围绕旋转支撑台中心运行。
[0045]
该设备还需配备用于检测工件位置、圆度、平整度等参数的尺寸检测装置,尺寸检测装置(图中未示出)位于精密控形内胎模外侧,绕旋转支撑台5圆心均匀设置。在旋转支撑台旋转时,对旋转的工件进行位置、圆度、平整度等参数测量,与精密控形内胎模校形形成闭环控制,提高控形精度,防止产品出现缺陷。
[0046]
实施例2。通过内胎模的前后移动用于实现控制超大型薄壁筒形件形状。
[0047]
规格:筒体内直径12000~12500mm,筒体壁厚70~80mm,筒体高度4000mm。
[0048]
精整精度:筒体圆度不大于
±
2.5mm。
[0049]
校形过程:
[0050]
通过控制液压推缸2将内胎模11移动至以旋转支撑台5中心为圆心,直径为工件尺寸圆弧位置,旋转旋转支撑台5,使用尺寸检测装置检测内胎模11位置,使其圆度误差不大于
±
1.0mm。
[0051]
采用专用吊具,将环轧后红热筒形工件吊运至薄壁筒体精密控形设备上,使用尺寸检测装置对筒形件进行圆度测量,保证其中心与旋转支撑台5中心重合。
[0052]
移动内胎模11,使其处于以旋转支撑台5中心为圆心,直径为工件尺寸圆弧位置。
[0053]
筒形件自然空冷至室温,在热胀冷缩的作用下,工件自然收缩,利用内胎模11约束筒体在冷却时的径向收缩,使筒体的径向收缩力变为法向力,在法向力作用下,筒体沿周向收缩变形,在筒体冷却到室温时,筒体的内表面与内胎模11外表面自然贴合,筒体即可达到初定型的尺寸与圆度要求。
[0054]
内胎模11向内收回,方便吊具将工件转移。
[0055]
以上所述,仅为本实用新型较佳的具体实施方式,但本实用新型的保护范围并不局限于此,任何熟悉本技术领域的技术人员在本实用新型披露的技术分范围内,可轻易想到的变化或者替换,都应涵盖在范明的保护范围之内。因此,本实用新型的保护范围应该以权利要求的范围为准。
起点商标作为专业知识产权交易平台,可以帮助大家解决很多问题,如果大家想要了解更多知产交易信息请点击 【在线咨询】或添加微信 【19522093243】与客服一对一沟通,为大家解决相关问题。
此文章来源于网络,如有侵权,请联系删除
相关标签: 液压支架



tips