一种适用于大跨径悬臂浇筑高强高韧性砼拱桥的主拱构造的制作方法



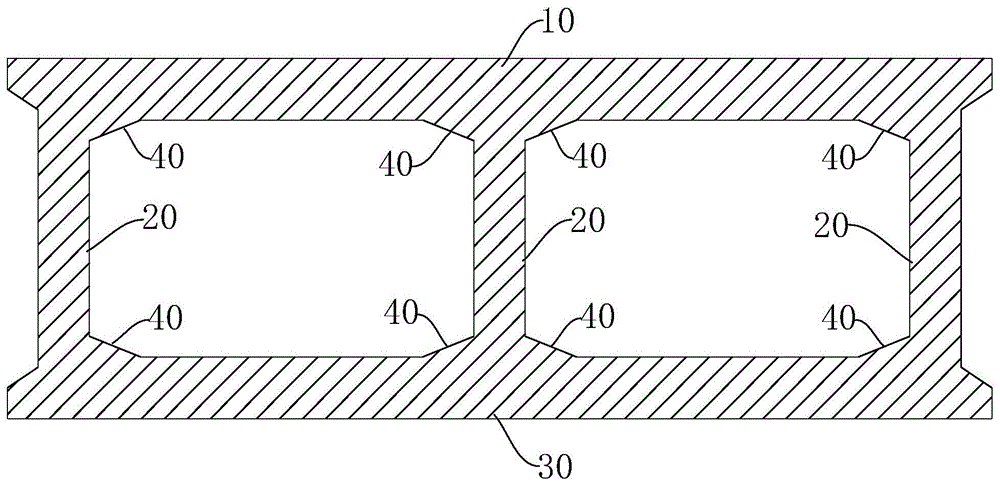
本实用新型涉及钢筋砼拱桥领域,特别是一种适用于大跨径悬臂浇筑高强高韧性砼拱桥的主拱构造。
背景技术:
目前国内已建成的悬臂浇筑砼拱桥的跨径大都在200米左右、拱圈高度在3.5m左右。由于悬臂浇筑砼拱桥自身承重等因素,拱桥跨径难以进一步取得较大突破。现有拱桥主拱圈多由一条独立闭合截面的拱肋形成,拱圈或拱肋截面型式多采用单箱双室截面,即一个箱梁里设有两个空腔,如图1;拱肋包括均由混凝土浇筑形成的顶板10、底板30和腹板20,空腔呈矩形,夹角处一般设有20cm(高)×50cm(宽)的小倒角40。在施工制作单箱双室截面拱肋时,单个拱肋需要两套内模以形成两个腔室然后浇筑混凝土成型。该种主拱结构横截面尺寸大、自重大,在吊装合龙施工过程斜拉体系受力大,施工难度也较大。
技术实现要素:
本实用新型的目的在于:针对现有技术悬臂浇筑砼拱桥跨径受自重的影响大,难以取得更大跨径拱桥的施工成果的问题,提供一种适用于大跨径悬臂浇筑高强高韧性砼拱桥的主拱构造,将主拱构造轻型化,保证主拱承载能力的同时减轻拱肋自重,提高更大跨径的跨越能力。
为了实现上述目的,本实用新型采用的技术方案为:
一种适用于大跨径悬臂浇筑高强高韧性砼拱桥的主拱构造,包括两条单箱形拱肋,两条拱肋之间分布有若干个肋间横隔板,每个肋间横隔板横向连接两条拱肋。
本实用新型主拱构造采用双箱单室结构,即拱圈有两条拱肋,每条拱肋设有一个腔室,只需要采用一套内模,简化了模板工艺;两条拱肋之间通过设置若干肋间横隔板,将肋间横隔板与两侧拱肋结构相连成整体,保证拱圈的横向稳定性。相比传统的单箱双室结构,本实用新型可将主拱圈中的两条单箱拱肋进行独立浇筑,不仅受力稳定性好,还减小了主拱截面尺寸,大大减少悬臂浇筑混凝土重量,减小斜拉扣挂体系施工受力,从而减轻自重、实现轻型化,提高了跨越能力,尤其适用于300米以上跨径的主拱。
作为本实用新型的优选方案,拱肋为八边形结构。在传统箱式矩形截面的基础上设置大倒角,可有效降低倒角处局部应力,简化模板构造并减轻自重;同时对于山区桥梁在峡谷风较大的环境,有利于提高主拱圈抗风性能,同时多边形外观较常规拱肋断面优美。其中,倒角尺寸范围可参考取值:宽度45cm-55cm,高度95cm-105cm。
作为本实用新型的优选方案,拱肋包括腹板、顶板和底板,腹板的厚度至少为30cm,顶板、底板的厚度至少为40cm;即在减少悬臂浇筑混凝土重量的同时,为了保证主拱抗剪、抗压及抗弯能力及施工可行性,根据受力需要,除拱脚段落的拱肋适当加厚外,拱肋其余段落的腹板的最小厚度可取至30cm,顶板、底板的最小厚度可取至40cm,以实现主拱结构轻型化。
作为本实用新型的优选方案,当主拱跨径大于300m、拱肋截面高度大于6m时,拱圈高度与腹板厚度的高厚比大于20,使主拱结构轻型化的同时合理受力,能够适用于大跨径的桥梁。
作为本实用新型的优选方案,肋间横隔板与相邻两条拱肋为一体成型结构。将肋间横隔板骨架与拱肋骨架相连接,在悬臂浇筑施工过程中进行同步浇筑,利于结构稳定,方便施工。
作为本实用新型的优选方案,肋间横隔板为i型梁,厚度至少为30cm,利于提高抗扭能力,加强整体性能。
作为本实用新型的优选方案,拱肋内部设有若干个箱内横隔板,所有箱内横隔板横向设置并沿拱肋延伸方向分布。箱内横隔板有利于提高结构强度,改善抗压性能,提高结构的稳定性,加强整体性。
作为本实用新型的优选方案,箱内横隔板与拱肋一体成型,受力性能好、便于立模浇筑,施工方便。
作为本实用新型的优选方案,箱内横隔板与拱肋内部周边轮廓连接,箱内横隔板包括成型为一圈的闭口横隔板和成型为半圈的断口横隔板,其中闭口横隔板位于拱肋与立柱的连接处,其余截面则采取断口横隔板,以减轻拱圈自重。
作为本实用新型的优选方案,主拱构造为c80钢纤维混凝土结构。采用高强高性能混凝土,并掺入钢纤维提高混凝土的韧性和抗拉强度,可有效减轻拱圈自重,提高主拱承载能力,从而使拱肋截面尺寸减小实现轻型化。
综上所述,由于采用了上述技术方案,本实用新型的有益效果是:
1、本实用新型拱肋采用八边形双箱单室钢筋砼箱型结构,具有单条拱肋自重轻、模板构造简单、施工方便、缩短工期等优点,减轻了悬臂节段浇筑重量,降低斜拉扣挂体系受力,进而大大减少了工程措施费用。
2、本实用新型双箱单室结构设有大倒角,相比一般施工工程的小倒角,更利于抗风,简化模板构造,外观优美。
3、本实用新型结合轻型截面拱肋结构,采用了高强高性能混凝土,增大主拱圈承载能力,以减小主拱圈截面尺寸,从而减轻拱桥上部结构自重,提高跨越能力,使跨径可达350m以上,取得较大跨径突破。
附图说明
图1是现有拱肋单箱双室截面的结构示意图。
图标:10-顶板;20-腹板;30-底板;40-倒角。
图2是1/2拱桥立面布置示意图。
图3是拱桥部分平面布置示意图。
图4是图2中a部放大图。
图5是图3中b部放大图。
图6是图4中i部截面图。
图7是图4中ii部截面图。
图8是图4中iii部截面图。
图9是图8中iv部截面图。
图2-9中标记:1-拱肋;11-顶板;12-腹板;13-底板;14-倒角;2-肋间横隔板;3-箱内横隔板;31-闭口横隔板;32-断口横隔板。
具体实施方式
下面结合附图,对本实用新型作详细的说明。
为了使本实用新型的目的、技术方案及优点更加清楚明白,以下结合附图及实施例,对本实用新型进行进一步详细说明。应当理解,此处所描述的具体实施例仅用以解释本实用新型,并不用于限定本实用新型。
实施例1
一种适用于大跨径悬臂浇筑高强高韧性砼拱桥的主拱构造,如图2-图9所示,包括两条单箱形拱肋1,两条拱肋1之间分布有若干个肋间横隔板2,每个肋间横隔板2横向连接两条拱肋1。
该主拱构造采用双箱单室结构,即拱圈有两条拱肋1,每条拱肋1设有一个腔室、只需要采用一套内模,简化了模板工艺;两条拱肋1之间通过设置若干肋间横隔板2,将肋间横隔板2与两侧拱肋1结构相连成整体,保证拱圈的横向稳定性。相比传统的单箱双室结构使用斜拉扣挂体系进行整体浇筑施工,本实施例中的主拱构造可将两条单箱拱肋1分别独立浇筑,同时将若干分布的肋间横隔板2与拱肋1结构横向稳定连接,不仅受力稳定性好,还减小了主拱截面尺寸,大大减少悬臂浇筑混凝土重量,减小斜拉扣挂体系施工受力,从而减轻自重、实现轻型化,提高了跨越能力,尤其适用于300米以上跨径的主拱。
具体地,如图6-图8,拱肋1为八边形结构,即主拱采用八边形双箱单室钢筋砼箱型结构。在传统箱式矩形截面的基础上设置100cm(高)×50cm(宽)的大倒角14以呈现八边形形状,可有效降低倒角处局部应力,大倒角的设置也简化了外模板构造并减轻自重;同时对于山区桥梁在峡谷风较大的环境,根据风载体型系数设置箱型截面倒角尺寸,有利于提高主拱圈抗风性能,同时多边形外观较常规拱肋断面优美。
如图6,拱肋1包括腹板12、顶板11和底板13。根据受力需要,除拱脚段落的拱肋1适当加厚外,拱肋1其余段落的腹板12的最小厚度可取至30cm;当主拱跨径大于300m、截面高度大于6m时,拱圈高度与腹板12厚度的高厚比大于20,使主拱结构轻型化的同时合理受力,适用于大跨径的桥梁。此外,考虑抗压及抗弯性能,除拱脚段的其余拱肋段落,腹板12、顶板11及底板13厚度最小可取40cm。
如图5、8、9,肋间横隔板2为薄壁结构,内部设置劲性骨架,将肋间横隔板2骨架与拱肋1骨架相连接,肋间横隔板2的高度与拱肋1的高度一致,在悬臂浇筑施工过程中同步浇筑,与相邻两条拱肋1成为整体,利于结构稳定,方便施工。考虑抗扭能力及整体性能,肋间横隔板2选取i型梁,厚度最小可取30cm。
如图2-图5、图7-图8所示,拱肋1内部设有若干个箱内横隔板3,箱内横隔板3横向设置并沿拱肋1延伸方向分布。箱内横隔板3与拱肋1内部周边轮廓连接,立模浇筑一体成型。箱内横隔板3有利于提高结构强度,改善抗压性能,提高结构的稳定性,加强整体性。箱内横隔板3除立柱位置采用成型为一圈的闭口横隔板31外,其余截面采取大开口半断面薄壁的断口横隔板32(最小间距可取25cm),以减轻拱圈自重。
进一步地,在主拱结构截面尺寸轻型优化的基础上,主拱还采用了高强高性能混凝土使结构更轻型化。拱圈拱肋在砼骨架搭建完成进行混凝土浇筑作业时,掺入了钢纤维以提高混凝土的韧性和抗拉强度,可有效减轻拱圈自重,提高主拱承载能力,从而使拱肋截面尺寸轻型化。主拱泵送c80钢纤维混凝土配合比如下表。
主拱泵送c80钢纤维混凝土配合比
实验表明,主拱采用c80混凝土浇筑上述截面结构,其坍落度≥255mm,扩展度≥650mm,含气量约为1.8%,28d抗压强度≥92mpa、28d抗折强度≥6.5mpa,弹性模量为4.0×104mpa,断裂韧性是c60普通泵送混凝土的2.1倍,收缩徐变是普通泵送混凝土的0.6倍。
采用本结构,主拱结构跨径可达350m以上,主跨350m的拱桥主拱重量与c60的主跨180m的主拱重量相当,轻型化结构的设计使得拱桥领域取得较大跨径突破,具有十分显著的意义。
以上所述仅为本实用新型的较佳实施例而已,并不用以限制本实用新型,凡在本实用新型的精神和原则之内所作的任何修改、等同替换和改进等,均应包含在本实用新型的保护范围之内。
起点商标作为专业知识产权交易平台,可以帮助大家解决很多问题,如果大家想要了解更多知产交易信息请点击 【在线咨询】或添加微信 【19522093243】与客服一对一沟通,为大家解决相关问题。
此文章来源于网络,如有侵权,请联系删除


