一种钻孔灌注桩无沉渣施工装置的制作方法



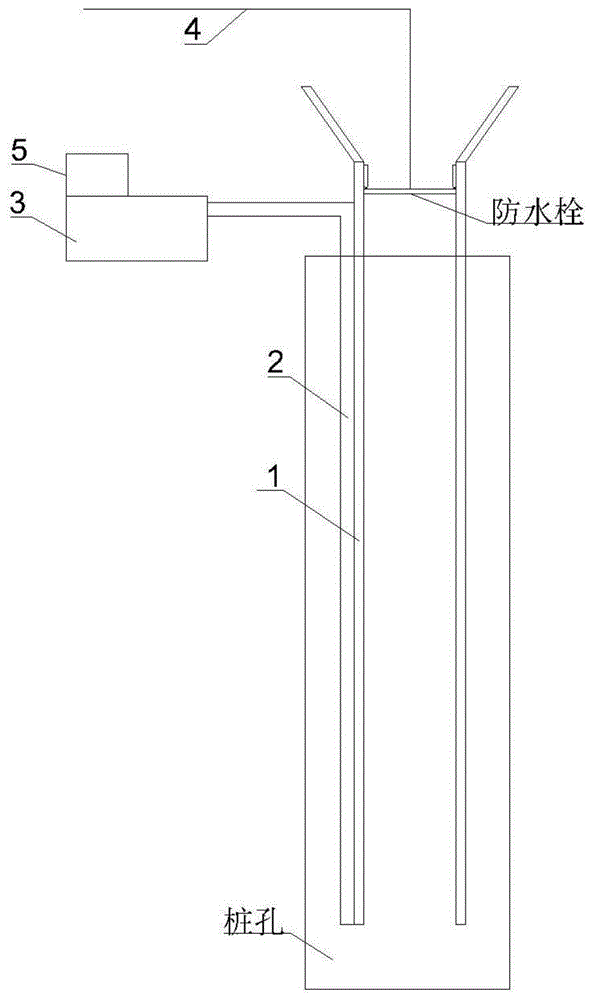
本实用新型涉及一种建筑工程用施工装置,具体为一种钻孔灌注桩的施工装置。
背景技术:
传统钻孔灌注桩的桩底沉渣控制原理是,在砼浇注前控制沉渣厚度,利用初方量在导管下落过程的冲击力,泛起桩底小量沉渣,使比重较大的砼浆沉入桩底,并使导管底口埋入砼面一下,沉渣浮在砼面以上,最后依靠导管内混凝土强大的压力逐渐把沉渣和浮渣推向桩顶。
然而上述现有技术中仍存在一定的问题,处方量的在冲击桩底沉渣时无法完全将浮渣充起,导致桩底沉渣过厚,并且为了满足混凝土能够顺利由灌注桩流出一般将灌注桩底端与桩底保持一定的距离,这就导致混凝土冲出灌注桩后会与存在的浮渣产生较大的冲击,从而存在二者混合的现象,影响了桩底的强度,存在较大的隐患。
技术实现要素:
本实用新型的目的在于克服现有技术的不足,提供了一种钻孔灌注桩无沉渣施工装置,以解决现有技术中桩底浮渣影响桩体质量的技术问题。
本实用新型是通过以下技术方案实现的:
本实用新型提供了一种钻孔灌注桩无沉渣施工装置,包括顶部联通有灌注斗的灌注桩,所述灌注桩的外壁上设置有高压管,所述高压管的顶端连接有气泵,所述灌注桩内设置有可在其内上下滑行的防水栓,所述防水栓通过吊装结构吊设在灌注桩内腔顶部,所述气泵与控制器信号连接,所述防水栓具体由底座和外径与灌注桩内径相同的圆柱形围板构成,所述圆柱形围板具体由多个弧形围板构成,每个弧形围板的底端中心处与底座铰接。
进一步,所述底座具体由底板和固定安装在其顶部的圆柱形挡板构成。
进一步,所述底板具体为倒锥形结构。
进一步,所述灌注桩底端通过复位装置与套设在其外壁的导流围板连接,且复位装置的触发装置设置在灌注桩内,底板自上而下冲击触发装置后,导流围板在复位装置的作用下上行至其底部与灌注桩底部持平,且常态下导流围板的顶端套设在灌注桩的底端外部。
进一步,所述复位装置具体由腰型孔、导向柱、限位件、复位弹簧、限位槽、卡扣和连接件构成,所述灌注桩底端侧壁上均匀的开设有贯穿其本体且在竖直方向上延伸的腰型孔,每个腰型孔内均固定安装有竖直方向上的导向柱每个导向柱上自上而下的套设有限位件和复位弹簧,每个限位件的外端分别与导流围板的内壁固定连接,所述导向柱上开设有限位槽,每个限位槽内嵌置有对应的卡扣,且卡扣卡设在限位槽内时对应的复位弹簧被限位件压缩在极限位置,每个卡扣朝向灌注桩中心处的端部之间通过连接件构成,外力触动连接件时可将卡扣由对应的限位槽内拉出令导流围板被复位弹簧经限位件推动上行。
进一步,所述腰型孔至少为两个。
进一步,所述连接件具体为连接绳。
进一步,所述吊装结构具体为吊装锁链,且其底端与底座中心处连接顶端与外部支撑结构连接将底座吊设在灌注桩顶端内部。
进一步,所述高压管的底端转动套设有导流盖,所述导流盖的侧壁上均匀的开设有贯穿其侧壁且与其径向不同的导流孔,所述导流孔背离导流盖的端部倾斜向下或水平设置。
进一步,所述导流盖的底部也绕其中心处均匀的开设有喷孔。
本实用新型相比现有技术具有以下优点:本实用新型提供了一种钻孔灌注桩无沉渣施工装置,通过设置防水栓,使得混凝土下行过程中形态保持稳定同时防水栓可压缩灌注桩内的空气,从而带动压缩空气吹动桩底沉渣使得其扰动从而避免沉渣过厚的弊端;同时本申请通过设置导流围板使得灌注桩底端得以延伸,进而灌注桩底与桩底的距离有效缩短,一方面压缩空气对桩底的扰动效果可有效提升,另一方面底板在混凝土方和重力的作用下触发连接件令导流围板上行复位的过程中,混凝土会冲击限位件使得导流围板上行速度减缓,从而处于底板上的混凝土可在导流围板内继续下行一段时间,进而有效延长了底座处于被限位导向的时长(由原来的仅灌注桩导向和限位,变为灌注桩和导流围板对其导向和限位),缩短了冲击距离,降低了初始冲出灌注桩的混凝土与桩底浮渣的混合程度,进而提高了桩基质量,且伴随着混凝土的下行导流围板最终也可在复位弹簧的作用下完全复位,不会影响灌注速度;通过设置高压管和气泵使得在灌注前浮渣保持扰动浑浊状态,避免了其沉积带来的弊端,同时当底座触发复位装置时气泵停止工作可避免气流扰动混凝土使二者混合程度增加的现象,进一步提高了桩基质量了;通过设置导流孔是的压入桩底的气流无法稳定,进一步增加了其扰动效果提高了桩基质量。
附图说明
图1是实施例一提供的一种钻孔灌注桩无沉渣施工装置的结构示意图;
图2是实施例一中防水栓结构示意图;
图3是实施例二提供的防水栓的剖视图;
图4是实施例三提供的防水栓的剖视图;
图5是实施例四提供的圆柱形挡板与灌注桩连接的剖视图;
图6是实施例五提供的导流盖的结构示意图。
图中:1、灌注桩;2、高压管;3、气泵;4、吊装结构;5、控制器;6、底座;7、弧形围板;8、底板;9、圆柱形挡板;10、导流围板;11、腰型孔;12、导向柱;13、限位件;14、复位弹簧;15、限位槽;16、卡扣;17、连接件;18、导流盖;19、导流孔。
具体实施方式
下面将结合本实用新型实施例中的附图,对本实用新型实施例中的技术方案进行清楚、完整地描述,显然,所描述的实施例仅仅是本实用新型一部分实施例,而不是全部的实施例。基于本实用新型中的实施例,本领域普通技术人员在没有做出创造性劳动前提下所获得的所有其他实施例,都属于本实用新型保护的范围。
结合图1和图2,在本实施例提供一种钻孔灌注桩无沉渣施工装置,包括顶部联通有灌注斗的灌注桩1(灌注斗可为用于对灌注入灌注桩1内的混凝土进行预存储),灌注桩1的外壁上设置有高压管2(高压管2的底端与灌注桩1的底端持平),高压管2的顶端连接有气泵3(通过气泵3将气流导入高压管2内并将气流输送到高压管2的底部),灌注桩1内设置有可在其内上下滑行的防水栓(防水栓可有效阻止灌注斗内混凝土自主下滑,且其下滑过程中可有效的对灌注桩1内空气进行压缩,避免因混凝土本身处于流体状态经高压空气冲击时高压空气冲入混凝土内),防水栓通过吊装结构4吊设在灌注桩1内腔顶部(初始状态时防水栓可稳定的设置在灌注桩1的内腔的顶部,吊装结构4可以为锁链等或由电磁阀等构成的可自动控制的设备,只需达到其能够在需要时与防水栓有效脱离便可,当期为自动化设备时其可与控制器5信号连接,控制器5控制吊装结构4与防水栓的脱离),气泵3与控制器5信号连接(用于控制气泵3的启停),为了便于防水栓顶部的混凝土在落至桩底时能够顺利坍塌以填充桩底,在本实施例中防水栓具体由底座6和外径与灌注桩1内径相同的圆柱形围板构成,圆柱形围板具体由多个弧形围板7构成,每个弧形围板7的底端中心处与底座6铰接,所有的弧形围板7在竖直设置时构成圆柱形围板,相互作用下,每个弧形围板7无法向底座6中处倾斜进而构成一个稳定的圆柱形围板,且每个弧形围板7与底座6铰接,其在脱离灌注桩1内壁的束缚下其受到内部混凝土的压力可向外部转动形成花瓣状四散,从而当防水栓由灌注桩1内脱离后在混凝土的压力下每个弧形围板7可向外散开,便于其内的混凝土坍塌。
工作原理:
将高压管2固定安装在灌注桩1的外壁上,将灌注桩1竖直固定打好的桩孔内,二者同轴分布,且灌注桩1的底端距桩底一定的距离,以便于后期混凝土流出,通过控制器5开启气泵3将高压气流导入桩底,气流扰动桩底沉渣使其处于悬浮扰动的状态;
将防水栓通过吊装结构4稳定吊设在灌注桩1顶端内腔内,然后将混凝土灌入灌注斗内,灌满后截断吊装结构4与底座6的连接,防水栓在重力和混凝土压力的双重作用下在灌注桩1内向下滑行,且在此过程中,一方面由多个弧形围板7构成的稳定的圆柱形围板可有效的在灌注桩1内壁的限位下对底座6进行导向使其始终保持水平状态向下滑动,另一方面,底座6保持水平状态时可有效的对其下方的空气进行压缩并通过灌注桩1底端排出,压缩空气由灌注桩1底端排出时可进一步增加浮渣的扰动程度,避免浮渣沉积,当底座6要冲出灌注桩1底部时通过控制器5关闭气泵3,扰动桩底浮渣的气流仅为底座6下部的气流,可将处于其下方的部分浮渣浑浊液排开其它部分的浮渣浑浊液无气流作用逐渐稳定,底座6冲出后弧形围板7在其内和上部混凝土的作用下外转呈四散状,同时可将部分浮渣浑浊液向外排挤降低浑浊液与其上混凝土的混合程度,底座6最终在重力加速度的作用下砸入桩底且弧形围板7呈四散状,跟随而下的混凝土在底座6冲击桩底后受力也四散开来排开浑浊液逐渐充满桩底,混凝土和浑浊液在密度不同的条件下浮渣浑浊液在混凝土不断落入的过程中逐渐上浮,并最终完成桩体的灌注。
实施例2
参考图3,在本实施例1中防水栓具体由底座6和多个弧形围板7构成,但是在其存在当防水栓稳定设置于灌注桩1内时其上部混凝土内的水分极易通过弧形围板7与底座6连接处渗出,不利于保持灌注斗内混凝土的水料配比,影响了混凝土的质量,因此为了克服上述缺陷,在本实施例中提供一种钻孔灌注桩无沉渣施工装置,设备结构与实施例1基本相同,主要的区别在于防水栓的不同。
本实施例中,防水栓的底座6具体由底板8和固定安装在其顶部的圆柱形挡板9构成,弧形围板7与圆柱形围板9的顶部转动连接,如图3。
通过上述设置圆柱形挡板9(其外径与灌注桩1内径相同)可有效的将经弧形围板7与其连接处渗出的水分堵住,使得水分存留在灌注斗内,避免了上述缺陷。
本实施例可有效的保持混凝土的质量。
实施例3
结合图4,在实施例2中底板8的底部为水平面,使得其落出灌注桩1底端与沉渣浑浊液接触时冲击力过大,不利与其顺利落水,浑浊液易与混凝土混合,降低了桩底混凝土的质量,因此为了克服上述缺陷,在本实施例中提供一种钻孔灌注桩无沉渣施工装置,该装置与实施例2设备结构基本相同,区别在于本实施例中底板8具体为倒锥形结构。
通过上述设置,底板8冲击浑浊液时浑浊液可被底板8底部尖端导流,降低了二者之间的冲击力,使得初始时流出灌注桩1的混凝土受到浑浊液的冲击力有效降低,可保持一定的初始状态,并伴随底板8一起冲击桩底,从而可进一步降低初始混凝土与浑浊液的混合程度,实现提高桩基质量的目的。
实施例4
在实施例1-3中灌注桩1的底端始终与桩底保持一定的位置,目的是为了后期混凝土能够有效流出进而充填桩孔内,实现灌注成桩的目的,但是这种设置也是的冲出灌注桩1底端的混凝土始终与桩底有一定的距离,进而使得混凝土必然存在与浮渣浑浊液冲击混合的可能性,二者混合后必然影响成桩的桩底的质量,因此,为了进一步提高成桩的质量,本实施例提供一种钻孔灌注桩无沉渣施工装置,其设备结构与实施例3基本相同,主要的区别在于本实施例中:
结合图5,灌注桩1底端通过复位装置与套设在其外壁的导流围板10连接,且复位装置的触发装置设置在灌注桩1内,底板8自上而下冲击触发装置后,导流围板10在复位装置的作用下上行至其底部与灌注桩1底部持平,且常态下导流围板10的顶端套设在灌注桩1的底端外部。
通过上述设置,底板8在冲出灌注桩1底端后仍可在导流围板10内继续下落一段时间,且导流围板10在后期可在复位装置的作用下上行至与灌注桩1的底端齐平达到设置的混凝土落出距离,从而不会影响后期混凝土的有效流出。
特别的,在本实施例中,复位装置具体由腰型孔11、导向柱12、限位件13、复位弹簧14、限位槽15、卡扣16和连接件17构成,灌注桩1底端侧壁上均匀的开设有贯穿其本体且在竖直方向上延伸的腰型孔11,每个腰型孔11内均固定安装有竖直方向上的导向柱12每个导向柱12上自上而下的套设有限位件13和复位弹簧14,每个限位件13的外端分别与导流围板10的内壁固定连接,导向柱12上开设有限位槽15,每个限位槽15内嵌置有对应的卡扣16,且卡扣16卡设在限位槽15内时对应的复位弹簧14被限位件13压缩在极限位置,每个卡扣16朝向灌注桩1中心处的端部之间通过连接件17构成,外力触动连接件17时可将卡扣16由对应的限位槽15内拉出令导流围板10被复位弹簧14经限位件13推动上行。
上述设置中,腰型孔11为导向柱12提供设置空间,导向柱12上套设的复位弹簧14可为限位件13提供复位力,导向柱12和复位弹簧14的外径均小于灌注桩1的壁厚,使得导向柱12和复位弹簧14可藏在灌注桩1的内壁,不会影响底板8的滑行,同时限位件13朝向灌注桩1中心的端部也处于灌注桩1侧壁内,从而也不会影响底板8的滑行,并且卡扣16卡设在对应的限位槽15内后,其朝向灌注桩1内的端部也设置在灌注桩1侧壁内,可避免其对底板8滑行的影响,且当底板8冲击连接件17后,连接件17拉动卡扣16朝向灌注桩1中心处移动时,当卡扣16脱离限位槽15时其仍在灌注桩1的侧壁即腰型孔11内,使得其不会影响底板8的移动。
特别的,为了实现受力平衡,在本实施例中,腰型孔11至少为两个。
特别的,在本实施例中连接件17具体为连接绳。
通过上述设置,当底板8滑行至冲击连接件17,连接件17拖动其两端的卡扣16朝向灌注桩1中心处移动并最终脱离对应的限位槽15,复位弹簧14从而推动限位件13带动导流围板10上行,在此过程中,底板8继续下行,其顶部的混凝土伴随而下,部分混凝土会冲入腰型孔11内从而可为限位件13提供一定的上行阻力,降低其上行趋势;
在本实施例中设备的工作原理为:气泵3持续为高压管2导入高压气流扰动桩孔底部浮渣使其呈悬浊液状态,当底板8冲击连接件17后冲至灌注桩1底端时停止气泵3,浮渣浑浊液停止扰动,但此时圆柱形围板10存在完全复位和未完全复位的两种情况:
当其处于完全复位时,因前一时间段圆柱形围板1处于浮渣悬浮液内,处于其内的悬浮液背其保护可不受经高压管2导入的气流扰动,其内的浮渣逐渐下沉至底部且圆柱形围板10的底部也不与桩孔底接触,因此受气流扰动沉积到圆柱形围板10底部的浮渣可被气流扰动吹走,则其内悬浊液内的浮渣密度远小于外部的悬浊液,且即便没有被扰动气流吹走,也会被经底板8压缩的气流吹走,因此,当圆柱形围板10完全复位且底板8冲出灌注桩1底端后气泵3停止,悬浊液扰动停止,灌注桩1底端下方的悬浊液内的浮渣浓度远小于其它部分(且伴随压缩气流的影响使得其正下方悬浊液内浮渣浓度被有效降低,即被挤压至其它部分处),底板8冲击其正下方悬浊液后,其下方浮渣浓度也低于其它部分浓度,混凝土伴随底板8下行至与浑浊液接触后,因混凝土浓度大于浮渣悬浮液,被排挤的浮渣会继续被混凝土排挤,进而可有效的提高形成的桩基底部的强度;
当其未完全复位时,圆柱形围板10相当于作为灌注桩1延长部分,底板8可在内进行一端时间下滑,在此过程中,圆柱形围板10对其内的悬浮液围挡,在压缩气流的作用下圆柱形围板10内的悬浊液可被排出其内,即此部分处于短时间的中空状态,进而可有效避免在该段时间内底板8与浑浊液的冲击,缩短底板8初始冲击悬浮液与直至冲击桩底之间的距离,进而可进一步降低初始混凝土与浑浊液冲击后二者混合的程度,从而可有效的提高形成桩基底座的质量;同时圆柱形围板10也缓慢的上行且混凝土逐渐流出,在此过程中圆柱形围板10仍为可混凝土提供一定的防护避免其内的混凝土过快的与浑浊液接触,从而可提高桩基底座的质量;
同时存在底板8冲击桩底后圆柱形围板10才开始复位(受到后继混凝土的影响,复位过程缓慢,但是在复位弹簧14的作用下仍缓慢复位,在本实施例中复位弹簧14提供的复位力大于混凝土下流时对其的冲击力,同时在本实施例中灌注桩1安装完成后,复位弹簧14被压缩在极限位置,圆柱形围板10的底端处于桩孔底部的上方很小距离出,根据实际情况可设定为10-20cm等,目的是为了尽量减小其底端与桩底的距离同时又不影响压缩空气的正常排出),此种情况下初始混凝土由圆柱形围板10冲出后其与桩孔底部的距离处于极限小的位置,进而极大的降低了初始混凝土与浑浊液的混合程度,极大的提供桩基底部的质量,且后继混凝土在圆柱形围板10的保护下其进一步避免与浑浊液过早接触,在初始混凝土不断自圆柱形围板10底端流出后其内(在底板8和弧形围板7的共同作用下浑浊液在初始时刻被排挤至外部)初始混凝土可迅速充填桩孔底部空间并将浮渣浑浊液逐渐上挤,后继混凝土在圆柱形围板10不断上升过程中排出逐渐充满桩底,圆柱形围板10完全复位后,后继混凝土可有效流出,进行桩孔的灌注;
整个过程中可极大的提高桩基灌注后的质量。
特别的,在本实施例中,吊装结构4具体为吊装锁链,且其底端与底座6中心处连接顶端与外部支撑结构连接将底座6吊设在灌注桩1顶端内部;
吊装锁链可有效为底板8提供吊装力,在灌注开始是外力控制吊装锁链断开使底板8有效在重力和混凝土的作用下下滑;可有效保障设备的稳定。
实施例5
结合图6,在前述实施例中高压管2导出的高压气流至桩孔内后,其气流排出的方向多为自高压管2底部直接向上涌动(因为缺少有效的导向)进而桩底浮渣的扰动程度可能达不到理想效果,因此在本实施例中提供一种钻孔灌注桩无沉渣施工装置,设备结构与实施例4基本一样,主要的区别在于,高压管2的底端转动套设有导流盖18,导流盖18的侧壁上均匀的开设有贯穿其侧壁且与其径向不同的导流孔19,导流孔19背离导流盖18的端部倾斜向下或水平设置。
通过上述设置,高压气流被导向并且倾斜的导流孔19可在分为多个方向对浮渣进行扰动,气流的推动下导流盖18也可被有效推动进行转动从而可进一步增加扰动效果;
特别的,为了进一步增加扰动效果,导流盖18的底部也绕其中心处均匀的开设有导流孔19。
通过上述设置,可有效的提高浮渣的扰动效果,避免其沉积在桩孔底部。
对于本领域技术人员而言,显然本实用新型不限于上述示范性实施例的细节,而且在不背离本实用新型的精神或基本特征的情况下,能够以其他的具体形式实现本实用新型。因此,无论从哪一点来看,均应将实施例看作是示范性的,而且是非限制性的,本实用新型的范围由所附权利要求而不是上述说明限定,因此旨在将落在权利要求的等同要件的含义和范围内的所有变化囊括在本实用新型内。
此外,应当理解,虽然本说明书按照实施方式加以描述,但并非每个实施方式仅包含一个独立的技术方案,说明书的这种叙述方式仅仅是为清楚起见,本领域技术人员应当将说明书作为一个整体,各实施例中的技术方案也可以经适当组合,形成本领域技术人员可以理解的其他实施方式。
本实用新型不限于以上对实施例的描述,本领域技术人员根据本实用新型揭示的内容,在本实用新型基础上不必经过创造性劳动所进行的改进和修改,都应该在本实用新型的保护范围之内。
起点商标作为专业知识产权交易平台,可以帮助大家解决很多问题,如果大家想要了解更多知产交易信息请点击 【在线咨询】或添加微信 【19522093243】与客服一对一沟通,为大家解决相关问题。
此文章来源于网络,如有侵权,请联系删除


