一种装配式混凝土梁柱可滑动自复位节点连接结构的制作方法



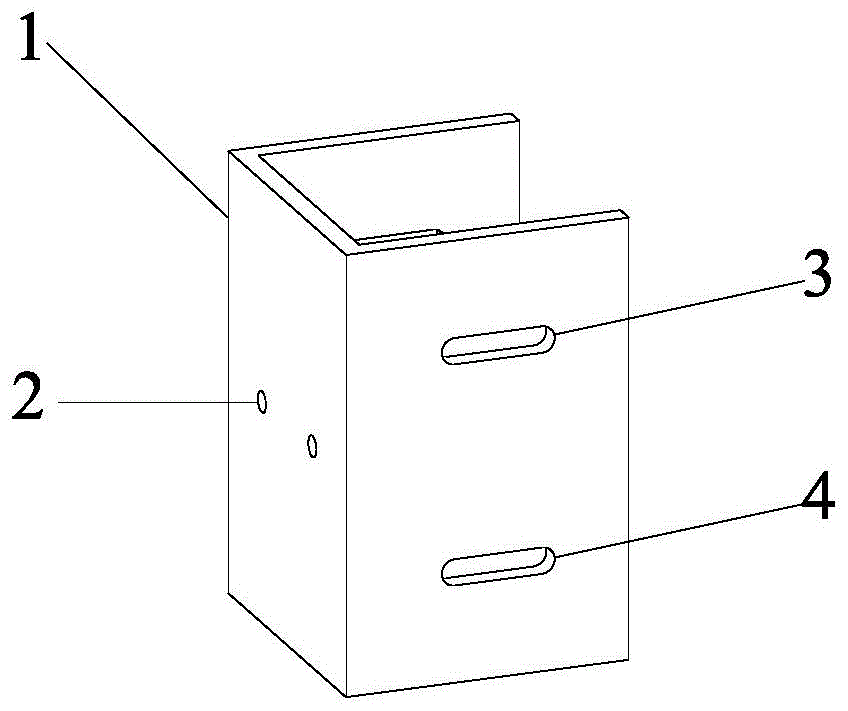
本实用新型涉及一种装配式混凝土梁柱可滑动自复位节点连接结构,属于装配式混凝土建筑技术领域。
背景技术:
装配式混凝土结构具有提高生产效率,节能环保,施工方便快捷等优点,是我国建筑结构发展的重要方向之一。目前,在这一研究领域,学界和工程界重点关注的问题即如何安全、高效、可靠的提高装配式结构节点连接部位的抗震性能,避免不必要的结构损伤和破坏。
传统的装配式混凝土结构,为达到结构整体“等同现浇”的目的,常规做法是梁柱预制,节点现浇。采用现浇做法的节点,结构整体的力学性能与全预制结构基本相近,但施工现场仍需要大量的混凝土湿作业,无法满足装配式建筑绿色环保,高效节能的发展理念。近年来,以套筒灌浆连接、约束浆锚连接和后浇带连接等方式为代表的干式连接技术逐渐兴起。试验研究表明,此类连接方式能够保证节点连接区域的刚度和承载力,受力可靠,但耗能较差,在反复地震荷载作用下灌浆处容易发生脆性破坏。因此,如何有效提高节点的耗能能力,最大限度的降低结构在地震作用下的损伤和破坏,对于加快装配式建筑在我国的推广,推动装配式建筑工业化和产业化发展都具有重要意义。
技术实现要素:
本实用新型为了解决上述背景技术中提到的技术问题,提出一种新型的装配式混凝土梁柱可滑动自复位节点连接结构,实现预制钢筋混凝土梁和预制钢筋混凝土柱间的连接,以满足实际设计与施工中的需要。
本实用新型提出一种装配式混凝土梁柱可滑动自复位节点连接结构,包括u型钢板预埋件、预制钢筋混凝土柱、预制钢筋混凝土梁、山字型钢板预埋件、滑动定位螺栓组、若干预应力筋和若干预应力筋锚具,所述预制钢筋混凝土柱上定位安装有u型钢板预埋件,所述预制钢筋混凝土梁上定位安装有山字型钢板预埋件,所述预制钢筋混凝土梁和预制钢筋混凝土柱通过u型钢板预埋件与山字型钢板预埋件垂直连接,所述u型钢板预埋件与山字型钢板预埋件相对设置且通过滑动定位螺栓组配合连接,能够实现相对滑动,若干预应力筋依次横穿预制钢筋混凝土梁、u型钢板预埋件和山字型钢板预埋件,最后从预制钢筋混凝土柱穿出,每个预应力筋锚具对应旋在预应力筋的伸出端进行固定。
优选地,所述u型钢板预埋件包括u型钢板、两个预应力筋孔ⅰ、两个螺栓滑动槽ⅰ和螺栓滑动槽ⅱ,所述u型钢板的u型底面与预制钢筋混凝土柱连接,其上设置有两个预应力筋孔ⅰ,所述u型钢板的左右两翼板壁的上部位置设置有相对的螺栓滑动槽ⅰ,下部位置设置有相对的螺栓滑动槽ⅱ。
优选地,所述螺栓滑动槽ⅰ和螺栓滑动槽ⅱ呈矩形,角点处进行圆弧倒角处理;所述螺栓滑动槽ⅰ和螺栓滑动槽ⅱ的左右宽度不超过u型钢板侧板壁宽度的三分之一,以保证u型钢板预埋件具有足够的抗弯刚度。
优选地,所述预制钢筋混凝土柱包括若干柱纵向受力钢筋、柱箍筋、定位钢筋ⅰ和金属波纹管ⅰ,若干柱纵向受力钢筋与柱箍筋相互垂直焊接为纵向的钢筋骨架,所述钢筋骨架外浇筑混凝土预制成柱体,所述钢筋骨架的前后面安装有若干定位钢筋ⅰ,若干金属波纹管ⅰ顺着预应力筋的方向安装在定位钢筋ⅰ上,所述金属波纹管ⅰ的内部空心区域作为预应力筋孔道ⅰ,用以穿过预应力筋,根据金属波纹管ⅰ的位置,u型钢板预埋件的连接面与钢筋骨架间进行焊接连接,在焊接过程中,保证预应力筋孔ⅰ与预应力筋孔道ⅰ对齐。
优选地,所述山字型连接钢板键包括山字型钢板、两个预应力筋孔ⅱ、螺栓孔i和螺栓孔ⅱ,所述山字型连接钢板键的山字型底面与预制钢筋混凝土梁定位连接,其上设置有两个预应力筋孔ⅱ,所述山字型钢板的左右两翼板壁的上部位置设置有相对的螺栓孔i,下部位置设置有相对的螺栓孔ⅱ,所述山字型钢板的左右两翼板壁插入u型钢板内。
优选地,所述山字型钢板的两翼外侧板壁外间距等于u型钢板1的两翼内侧板壁内间距,高度和u型钢板的高度相同,以保证山字型钢板预埋件能够平行插入到u型钢板预埋件内。
优选地,所述预制钢筋混凝土梁包括若干梁负弯矩筋、梁正弯矩筋、梁箍筋、定位钢筋ⅱ和金属波纹管ⅱ,若干梁负弯矩筋、梁正弯矩筋、梁箍筋相互垂直焊接为横向的钢筋骨架,所述钢筋骨架外浇筑混凝土预制成梁,所述钢筋骨架的前后安装有定位钢筋ⅱ,若干金属波纹管ⅱ顺着预应力筋的方向安装在定位钢筋ⅱ上,所述金属波纹管ⅱ的内部空心区域作为预应力筋孔道ⅱ,用以穿过预应力筋,根据金属波纹管ⅱ的位置,u型钢板预埋件的连接面与钢筋骨架间进行焊接连接,在焊接过程中,应保证预应力筋孔ⅱ与预应力筋孔道ⅱ对齐。
优选地,所述滑动定位螺栓组包括两个高强螺栓、四个螺母和两个矩形摩擦垫片,其中一个高强螺栓穿过重合的螺栓孔i与螺栓滑动槽ⅰ沿上述槽左右滑动,另一个高强螺栓穿过重合的螺栓孔ⅱ和螺栓滑动槽ⅱ且沿上述槽左右滑动,两个高强螺栓分别通过四个螺母进行固定,四个螺母与u型钢板预埋件的左右两翼外侧板壁间设置有矩形摩擦垫片,所述矩形摩擦垫片上下设置有两个螺纹孔。
优选地,所述矩形摩擦垫片为铜制材料,其与u型钢板预埋件接触的一侧进行粗糙处理以增加摩擦阻力。
本实用新型所述的一种装配式混凝土梁柱可滑动自复位节点连接结构的有益效果为:
1、本实用新型通过对高强螺栓施加预紧力,能够有效保证u型钢板预埋件和山字形钢板预埋件间的紧密连接,使结构整体保持较大的抗侧刚度,承担预制构件间传递的弯矩和剪力。
2、本实用新型采用的山字型钢板预埋件,在中等地震作用下能够沿u型钢板预埋件内预设的螺栓滑动槽左右滑动,根据所受荷载的大小和方向不同,使预制钢筋混凝土梁在一定范围内上下滑动。在此过程中,矩形摩擦垫片和u型钢板预埋件两翼板壁间发生摩擦并耗散能量,可防止结构变形过于集中,避免结构构件发生损伤破坏。此外,高强螺栓和矩形摩擦垫片可根据实际需求进行更换,操作简单方便。
3、本实用新型预制构件间传递的弯矩由无粘结预应力筋承担。在强震作用下,当预制钢筋混凝土梁相对于预制钢筋混凝土柱达到可控的最大滑动位置时,由于无粘结预应力筋始终保持弹性状态,此时开始发挥自复位作用,使预制梁柱在震后恢复到原来的初始状态。
4、本实用新型制作要求较高的部分,包括预制钢筋混凝土柱、预制钢筋混凝土梁、u型钢板预埋件以及山字型钢板预埋件的制作,均可在工厂完成,运输到现场后按顺序拼装,安装步骤简单,安装过程安全可靠,且施工现场无混凝土湿作业,符合装配式建筑绿色环保,高效节能的发展理念。
附图说明
构成本申请的一部分的附图用来提供对本实用新型的进一步理解,本实用新型的示意性实施例及其说明用于解释本实用新型,并不构成对本实用新型的不当限定。
在附图中:
图1是本实用新型所述的u型钢板预埋件的三维图;
图2是本实用新型所述的预制钢筋混凝土柱内的钢筋布置三维图;
图3是本实用新型所述的将u型钢板预埋件与预制钢筋混凝土柱内钢筋焊接完毕的三维图;
图4是本实用新型所述的预制钢筋混凝土柱的三维图;
图5是本实用新型所述的山字型钢板预埋件的三维图;
图6是本实用新型所述的预制钢筋混凝土梁内的钢筋布置三维图;
图7是本实用新型所述的将山字型钢板预埋件与预制钢筋混凝土梁内钢筋焊接完毕的三维图;
图8是本实用新型所述的预制钢筋混凝土梁的三维图;
图9是本实用新型所述的高强螺栓的三维图;
图10是本实用新型所述的螺母的三维图;
图11是本实用新型所述的矩形摩擦垫片的三维图;
图12是本实用新型所述的预应力筋的三维图;
图13是本实用新型所述的预应力筋锚具的三维图;
图14是本实用新型所述的预制钢筋混凝土柱和预制钢筋混凝土梁吊装完毕,将山字型钢板预埋件插入到u型钢板预埋件内的三维图;
图15是本实用新型所述的无粘结预应力筋穿过全部预制构件后的三维图;
图16是本实用新型所述的将无粘结预应力筋张拉完毕,用预应力筋锚具固定后的三维图;
图17是本实用新型所述的将高强螺栓与u型钢板预埋件、山字型钢板预埋件间固定并拧紧后的三维图;
图18是本实用新型所述的地震作用下预制钢筋混凝土梁向上方滑动的状态三维图;
图19是本实用新型所述的地震作用下预制钢筋混凝土梁向下方滑动的状态三维图;
图中所示:1-u型钢板;2-预应力筋孔ⅰ;3-螺栓滑动槽ⅰ;4-螺栓滑动槽ⅱ;5-柱纵向受力钢筋;6-柱箍筋;7-定位钢筋ⅰ;8-金属波纹管ⅰ;9-预应力筋孔道ⅰ;10-山字形钢板;11-预应力筋孔ⅱ;12-螺栓孔ⅰ;13-螺栓孔ⅱ;14-梁负弯矩筋;15-梁正弯矩筋;16-梁箍筋;17-定位钢筋ⅱ;18-金属波纹管ⅱ;19-预应力筋孔道ⅱ;20-高强螺栓;21-螺母;22-螺母孔;23-矩形摩擦垫片;24-螺栓孔;25-无粘结预应力筋;26-预应力筋锚具。
具体实施方式
以下结合附图对本实用新型的具体实施方式作进一步详细的说明:
具体实施方式一:参见图1-图19说明本实施方式。本实施方式所述的装配式混凝土梁柱可滑动自复位节点连接结构,包括u型钢板预埋件、预制钢筋混凝土柱、预制钢筋混凝土梁、山字型钢板预埋件、滑动定位螺栓组、若干预应力筋25和若干预应力筋锚具26,所述预制钢筋混凝土柱上定位安装有u型钢板预埋件,所述预制钢筋混凝土梁上定位安装有山字型钢板预埋件,所述预制钢筋混凝土梁和预制钢筋混凝土柱通过u型钢板预埋件与山字型钢板预埋件垂直连接,所述u型钢板预埋件与山字型钢板预埋件相对设置且通过滑动定位螺栓组配合连接,能够实现相对滑动,若干预应力筋25依次横穿预制钢筋混凝土梁、u型钢板预埋件和山字型钢板预埋件,最后从预制钢筋混凝土柱穿出,每个预应力筋锚具26对应旋在预应力筋25的伸出端进行固定。
所述u型钢板预埋件包括u型钢板1、两个预应力筋孔ⅰ2、两个螺栓滑动槽ⅰ3和螺栓滑动槽ⅱ4,所述u型钢板1的u型底面与预制钢筋混凝土柱连接,其上设置有两个预应力筋孔ⅰ2,所述u型钢板1的左右两翼板壁的上部位置设置有相对的螺栓滑动槽ⅰ3,下部位置设置有相对的螺栓滑动槽ⅱ4。
所述预制钢筋混凝土柱包括若干柱纵向受力钢筋5、柱箍筋6、定位钢筋ⅰ7和金属波纹管ⅰ8,若干柱纵向受力钢筋5与柱箍筋6相互垂直焊接为纵向的钢筋骨架,所述钢筋骨架外浇筑混凝土预制成柱体,所述钢筋骨架的前后面安装有若干定位钢筋ⅰ7,若干金属波纹管ⅰ8顺着预应力筋25的方向安装在定位钢筋ⅰ7上,所述金属波纹管ⅰ8的内部空心区域作为预应力筋孔道ⅰ9,用以穿过预应力筋25,根据金属波纹管ⅰ8的位置,u型钢板预埋件的连接面与钢筋骨架间进行焊接连接,在焊接过程中,保证预应力筋孔ⅰ2与预应力筋孔道ⅰ9对齐。
所述山字型连接钢板键包括山字型钢板10、两个预应力筋孔ⅱ11、螺栓孔i12和螺栓孔ⅱ13,所述山字型连接钢板键的山字型底面与预制钢筋混凝土梁定位连接,其上设置有两个预应力筋孔ⅱ11,所述山字型钢板10的左右两翼板壁的上部位置设置有相对的螺栓孔i12,下部位置设置有相对的螺栓孔ⅱ13,所述山字型钢板10的左右两翼板壁插入u型钢板1内。
所述预制钢筋混凝土梁包括若干梁负弯矩筋14、梁正弯矩筋15、梁箍筋16、定位钢筋ⅱ17和金属波纹管ⅱ18,若干梁负弯矩筋14、梁正弯矩筋15、梁箍筋16相互垂直焊接为横向的钢筋骨架,所述钢筋骨架外浇筑混凝土预制成梁,所述钢筋骨架的前后安装有定位钢筋ⅱ17,若干金属波纹管ⅱ18顺着预应力筋25的方向安装在定位钢筋ⅱ17上,所述金属波纹管ⅱ18的内部空心区域作为预应力筋孔道ⅱ19,用以穿过预应力筋25,根据金属波纹管ⅱ18的位置,u型钢板预埋件的连接面与钢筋骨架间进行焊接连接,在焊接过程中,应保证预应力筋孔ⅱ11与预应力筋孔道ⅱ19对齐。
所述滑动定位螺栓组包括两个高强螺栓20、四个螺母21和两个矩形摩擦垫片23,其中一个高强螺栓20穿过重合的螺栓孔i12与螺栓滑动槽ⅰ3沿上述槽左右滑动,另一个高强螺栓20穿过重合的螺栓孔ⅱ13和螺栓滑动槽ⅱ4且沿上述槽左右滑动,两个高强螺栓20分别通过四个螺母21进行固定,四个螺母21与u型钢板预埋件的左右两翼外侧板壁间设置有矩形摩擦垫片23,所述矩形摩擦垫片23上下设置有两个螺纹孔24。
(1)如图1所示,u型钢板预埋件的具体结构及制作过程如下:
u型钢板预埋件(图1)由u型钢板1、预应力筋孔ⅰ2、螺栓滑动槽ⅰ3和螺栓滑动槽ⅰ4组成。u型钢板1和预制构件连接的前板壁侧面通过双面贯通钻孔的方式设置预应力筋孔ⅰ2,预应力筋孔ⅰ2的位置、个数和尺寸由穿过孔内的无粘结预应力筋25的位置、根数和尺寸确定。
u型钢板1的左右两翼板壁侧面,上方和下方区域均采用车槽或铣床加工的方式设置螺栓滑动槽ⅰ3和螺栓滑动槽ⅱ4,螺栓滑动槽ⅰ3和螺栓滑动槽ⅱ4呈矩形,角点处进行圆弧倒角处理。螺栓滑动槽ⅰ3和螺栓滑动槽ⅱ4的中心位置根据设计需求确定,上下高度等于穿过槽内的高强螺栓20的螺杆外径,左右宽度不超过板壁宽度的三分之一,以保证u型钢板预埋件(图1)具有足够的抗弯刚度。
u型钢板1的前板壁厚度应大于等于其所连接的预制构件的混凝土保护层厚度,以保证山字型钢板预埋件(图5)和u型钢板预埋件(图1)间预留一定的空隙进行相对滑动。
u型钢板1的其余尺寸由预制构件间传递的弯矩和剪力计算确定。
(2)如图2-图4所示,预制钢筋混凝土柱的具体结构和制作过程如下:
所述预制钢筋混凝土柱内的钢筋由柱纵向受力钢筋5、柱箍筋6和定位钢筋ⅰ7组成。定位钢筋ⅰ7的作用在于固定金属波纹管ⅰ8,其位置可灵活调整。钢筋绑扎完毕后,根据设计需求,在钢筋骨架的中部区域绑扎若干根金属波纹管ⅰ8(图2),金属波纹管ⅰ8的内部空心区域作为预应力筋孔道ⅰ9,用以穿过无粘结预应力筋25。
根据金属波纹管ⅰ8的位置,u型钢板预埋件(图1)远离两翼的板壁一侧,与钢筋骨架间进行焊接连接(图3)。在焊接过程中,应保证预应力筋孔ⅰ2与预应力筋孔道ⅰ9对齐,孔间接触位置处无相对错动。
在柱内的钢筋骨架外支撑模板,浇筑混凝土,混凝土在模板内的保护层浇筑厚度不超过u型钢板预埋件(图1)的内壁表面,混凝土凝固后拆除模板,完成预制钢筋混凝土柱(图4)的制作。
(3)如图5所示,山字型钢板预埋件的具体结构及制作过程如下:
山字型钢板预埋件(图5)由山字形钢板10、预应力筋孔ⅱ11、螺栓孔i12和螺栓孔ⅱ13组成。山字型钢板10和预制构件连接的的板壁侧面通过双面贯通钻孔的方式设置预应力筋孔ⅱ11,预应力筋孔ⅱ11的位置、个数和尺寸由穿过孔内的无粘结预应力筋25的位置、根数和尺寸确定。
山字型钢板10的左右两翼和中翼板壁侧面,上方和下方区域均通过双面贯通钻孔的方式设置螺栓孔i12和螺栓孔ⅱ13,螺栓孔i12和螺栓孔ⅱ13的尺寸由穿过孔内的高强螺栓20的尺寸确定,位置则根据设计需求,由u型钢板1内螺栓滑动槽ⅰ3和螺栓滑动槽ⅱ4的中心位置以及山字型钢板预埋件(图5)与u型钢板预埋件(图1)间预留的相对滑动空隙大小确定。
山字形钢板10的前板壁厚度应大于等于其所连接的预制构件的混凝土保护层厚度,以保证山字型钢板预埋件(图5)和u型钢板预埋件(图1)间预留一定的空隙进行相对滑动。
山字形钢板10的两翼外侧板壁净间距等于u型钢板1的两翼内侧板壁净间距,高度和u型钢板1的高度相同,以保证山字型钢板预埋件(图5)能够平行插入到u型钢板预埋件(图1)内。
(4)如图6-图8所示,预制钢筋混凝土梁的具体结构和制作过程如下:
梁内的钢筋由梁负弯矩筋14、梁正弯矩筋15、梁箍筋16和定位钢筋ⅱ17组成。定位钢筋ⅱ17的作用在于固定金属波纹管ⅱ18,其位置可灵活调整。钢筋绑扎完毕后,根据预制钢筋混凝土柱(图4)内金属波纹管ⅰ8的位置和根数,在钢筋骨架内绑扎相同数量的金属波纹管ⅱ18。金属波纹管ⅱ18的内部空心区域作为预应力筋孔道ⅱ19,用以穿过无粘结预应力筋25。
根据金属波纹管ⅱ18的位置,山字型钢板预埋件(图5)远离两翼和中翼的板壁一侧,与钢筋骨架间进行焊接连接(图7)。在焊接过程中,应保证预应力筋孔ⅱ11与预应力筋孔道ⅱ19对齐,孔间接触位置处无相对错动。
在梁内的钢筋骨架外支撑模板,浇筑混凝土,混凝土在模板内的保护层浇筑厚度不超过山字型钢板预埋件(图5)的内壁表面,混凝土凝固后拆除模板,完成预制钢筋混凝土梁(图8)的制作。
(5)如图9-图11所示,高强螺栓、螺母和矩形摩擦垫片的具体结构及制作过程如下:
高强螺栓20的螺杆长度不小于u型钢板预埋件(图1)的左右两翼外侧板壁净间距和和螺母21的厚度之和。
高强螺栓20的螺杆外径由预制构件间传递的剪力计算确定。螺母孔22的尺寸由高强螺栓20的螺杆外径确定。
矩形摩擦垫片23优选铜制材料,与u型钢板预埋件(图1)接触的一侧可进行粗糙处理以增加摩擦阻力。螺栓孔24的尺寸由高强螺栓20的螺杆外径确定。
(6)如图12-图13所示,无粘结预应力筋与锚头的具体结构及制作过程如下:
无粘结预应力筋25的材质、根数和尺寸可根据实际设计需求确定。
预应力筋锚具26可结合实际情况,选用夹片式锚具、支承式锚具或锥塞式锚具。
上述构件均可在工厂内预制完成或采购,然后运输到施工现场组装,具体组装过程如下:
(1)如图14所示,将预制钢筋混凝土柱(图4)和预制钢筋混凝土梁(图8)吊装至预定位置,缓慢移动预制钢筋混凝土梁(图8),使山字型钢板预埋件(图5)的两翼板壁外侧平行插入到u型钢板预埋件(图1)的两翼板壁内侧,直至螺栓孔ⅰ12和螺栓孔ⅱ13分别与螺栓滑动槽ⅰ3和螺栓滑动槽ⅱ4的中心边界对齐,此时山字型钢板预埋件(图5)未完全插入到u型钢板预埋件(图1)内,二者间预留了一定的空隙用以相对滑动。
(2)如图15-图16所示,引导无粘结预应力筋25穿过全部预制构件(图15),然后在预制钢筋混凝土梁(图8)的一侧对无粘结预应力筋25进行张拉,同时在预制钢筋混凝土柱(图4)的一侧采用预应力筋锚具26固定无粘结预应力筋25(图16)。
(3)如图17所示,待无粘结预应力筋25张拉并锚固完毕后,在u型钢板预埋件(图1)的两翼外侧放置矩形摩擦垫片23,使螺栓孔24与螺栓滑动槽ⅰ3和螺栓滑动槽ⅱ4的中心边界对齐,然后将高强螺栓穿过螺栓孔24,并用扭矩扳手拧紧螺母21,扭矩扳手施加的预紧力由预制构件间传递的剪力计算确定。
本实施例中,u型钢板预埋件(图1)和山字型钢板预埋件(图5)间通过高强螺栓20连接,对高强螺栓20施加的预紧力可以使结构整体保持较大的抗侧刚度,承担预制构件间传递的弯矩和剪力。
在中等地震作用下,如图18-图19所示,山字型钢板预埋件(图5)能够沿螺栓滑动槽ⅰ3和螺栓滑动槽ⅱ4左右滑动,根据所受荷载的大小和方向不同,预制钢筋混凝土梁(图8)相对于预制钢筋混凝土柱(图4)会向上方或向下方滑动。在此过程中,矩形摩擦垫片23和u型钢板预埋件(图1)两翼板壁间发生摩擦并耗散能量,可防止结构变形过于集中,避免结构构件发生损伤破坏。
预制构件间传递的弯矩由无粘结预应力筋25承担。通过对无粘结预应力筋25施加预应力,将全部预制构件连接起来并产生预压力。在强震作用下,当预制钢筋混凝土梁(图8)达到可控的最大滑动位置时,由于无粘结预应力筋25始终保持弹性状态,此时开始发挥自复位作用,使预制梁柱在震后恢复到原来的初始状态。
以上所述的具体实施例,对本实用新型的目的、技术方案和有益效果进行了进一步详细说明。所应理解的是,以上所述仅为本实用新型的具体实施例而已,并不用于限制本实用新型,还可以是上述各个实施方式记载的特征的合理组合,凡在本实用新型精神和原则之内,所做的任何修改、等同替换、改进等,均应包含在本实用新型的保护范围之内。
起点商标作为专业知识产权交易平台,可以帮助大家解决很多问题,如果大家想要了解更多知产交易信息请点击 【在线咨询】或添加微信 【19522093243】与客服一对一沟通,为大家解决相关问题。
此文章来源于网络,如有侵权,请联系删除


