一种石材反打预制外墙及其生产方法与流程



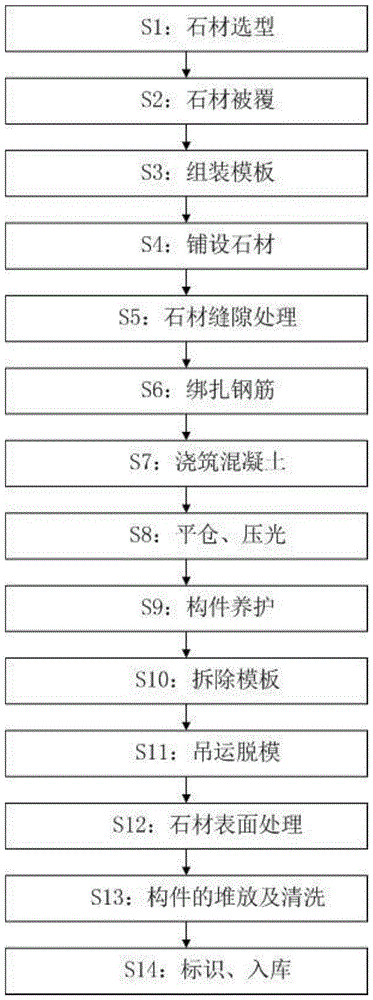
本发明涉及装配式建筑的的技术领域,尤其涉及一种石材反打预制外墙及其生产方法。
背景技术:
随着现代工业技术的发展,建造房屋可以像机器生产那样,成批成套地制造,只要把预制好的房屋构件,运到工地装配起来就完成了。由预制部件在工地装配而成的建筑,称为装配式建筑,按预制构件的形式和生产方法分为砌块建筑、板材建筑、盒式建筑、骨架板材建筑及升板升层建筑等五种类型。目前,在装配式建筑的设计和施工中,为使建筑的表面美观,一般要在其表面进行装修饰面。饰面装修一般由基层和面层组成,基层即支托饰面层的结构构件或骨架,其表面应平整,具有一定的强度和刚度,饰面层附着于基层表面起美观和保护作用,它应与基层牢固结合,且表面需平整均匀,通常将饰面层最外面的材料,作为饰面装修构造类型的命名,常见的饰面装修可分为抹灰类、贴面类、涂料类、裱糊类和铺钉类等。
涂刷外墙涂料、铺贴瓷砖和干挂石材是现有建筑外墙饰面的常见装饰品。外墙涂料,一般抗紫外线性能差,长期日照容易褪色,并且易出现雨痕、开裂、起皮等现象,影响美观;铺贴瓷砖,墙体混凝土和瓷砖粘结材料线膨胀系数不一致,易出现脱落现象,铺贴时高空作业也有一定的危险性;干挂石材,美观大方,很受青睐,但由于石材较重,使用时受到限制,存在极大的安全隐患。
技术实现要素:
针对上诉问题,本发明的目的其中一个目的在于提出一种饰面石材定位精准,表面规整,附着牢固,可大大提升预制外墙的整体装配速度,显著提高施工效率的石材反打的生产方法,本发明的另一个目的在于提供一种基于前述生产方法生产的预制外墙,旨在解决背景技术所阐述的技术问题。
为了实现上述目的,本发明提供了一种石材反打预制外墙的生产方法,其关键在于,包括以下步骤:
s1:石材选型;
s2:石材被覆处理;
s3:组装模板;
s4:将按步骤s2处理后的多块石材的正面朝下铺设在按步骤s3组装的模板中;
s5:对石材之间的缝隙进行密封处理;
s6:在石材背面上布设钢筋;
s7:浇筑混凝土;
s8:平仓、压光;
s9:预制外墙蒸汽养护;
s10:拆除模板;
s11:预制外墙吊运;
s12:针对石材外表面的缺陷部位进行修补处理;
其中,s2的具体实施步骤包括:
s201:以瓦斯或喷灯烘干石材表面水分;
s202:在石材背面划出锚固件定位线,并根据锚固件的实际尺寸及预埋深度确定锚孔位置;
s203:根据锚孔位置进行钻孔作业;
s204:使用毛刷和高压气枪清除石材表面及锚孔内的粉尘;
s205:在每块石材背面的四周边缘粘贴遮护胶带;
s206:将背覆胶均匀涂抹于石材的背面,并保证锚孔充分填实,再使用刮刀刮平;
s207:在锚孔中设置锚固件,将锚孔内溢出的背覆胶重新集中在锚孔周围,确保填满锚孔孔壁与锚固件之间的空隙;
s208:在背覆胶干燥前铺洒硅砂,硅砂用量为0.7~0.8kg/㎡。;
s209:撕去遮护胶带,静置养护。
更进一步地,所述遮护胶带的宽度为3~6mm。
更进一步地,步骤s206中背覆胶的涂抹量为0.5kg/m2。
更进一步地,在步骤s207中,所述锚固件包括抓钩,所述抓钩钩入所述锚孔的深度不低于20mm。
更进一步地,步骤s4还包括:将pe膜铺设在组装的模板底面,将多块石材正面朝下铺设在pe膜上。
更进一步地,步骤s5包括:
s501:使用亚克力条调整石材位置及缝宽;
s502:在石材缝隙中填充密封材料,并在填缝处打胶。
更进一步地,所述密封材料为pe泡棉条。
基于上述生产方法,本发明还公开了一种预制外墙,所述预制外墙包括饰面外墙及混凝土内墙,所述饰面外墙与所述混凝土内墙间通过预埋的锚固件连接固定,其中:所述饰面外墙包括饰面石材,所述饰面石材的内侧涂覆有背覆胶层,所述背覆胶层的内侧粘接有硅砂层。
与现有技术相比,本发明的显著效果为:
1、本发明通过将饰面石材在工厂加工过程中事先打到混凝土里,形成一体的建筑预制构件,通过本方法预制的预制外墙,其石材位置精准、表面规整、附着牢固;同时,使用本方法形成的建筑预制构件具有施工快、周期短等优势,且提高了抗震性能,节省了大量的人力和物力,具有显著的社会效益和经济效益;
2、通过密封材料对饰面石材间的缝隙进行填充,能够阻塞介质透过渗漏通道,起到水密性、气密性作用;
3、通过涂抹被覆胶和铺洒硅砂的方式,形成用于饰面石材背面界面处理的双组分界面材料,增强构件整体的抗碱、不透水功能性能;
4、锚固件与锚孔中填充的被覆胶形成连接强度更高的化学锚栓,增加预制外墙整体的稳定性;
5、在石材四周粘贴遮护胶可以防止涂抹在石材背面的背覆胶垂流;
6、在底模上铺设衬垫材料便于后期进行脱模处理。
附图说明
图1为实施例一生产方法的整体流程示意图;
图2为实施例一生产方法中s2的具体流程示意图;
图3为实施例一生产方法生产的预制外墙结构示意图;
图4为实施例二生产方法中s2的具体流程示意图;
图5为实施例二生产方法生产的预制外墙结构示意图;
图6为实施例二中锚固件的结构示意图。
图7为实施例三的整体结构示意图;
图8为实施例三的立体图;
实施例一:a-饰面外墙、b-混凝土内墙、c-锚固件、d-饰面石材、e-背覆胶层、f-硅砂层。
实施例二:1、饰面外墙、2-混凝土内墙、3-保温板、4-锚固件、5-容纳槽、6-爪钩、7-背栓、8-饰面石材、9-背覆胶层、10-硅砂层、11-外螺纹、12-承拉盘。
实施例三:1-支撑台’、2-模台’、3-矩形模框’、4-涂胶隔离网’、5-网格’、6-吊架’、7-吊装设备’、8-密封垫’、9-安装槽’、10-微振动设备’、11-模板’、12-压接台’、13-凸耳’、14-吊环’、15-转轴’、16-地锚件’。
具体实施方式
下面详细描述本发明的实施例,所述实施例的示例在附图中示出,其中自始至终相同或类似的标号表示相同或类似的元件或具有相同或类似功能的元件。下面通过参考附图描述的实施例是示例性的,旨在用于解释本发明,而不能理解为对本发明的限制。
在本发明的描述中,需要理解的是,术语“长度”、“宽度”、“上”、“下”、“前”、“后”、“左”、“右”、“竖直”、“水平”、“顶”、“底”“内”、“外”等指示的方位或位置关系为基于附图所示的方位或位置关系,仅是为了便于描述本发明和简化描述,而不是指示或暗示所指的装置或元件必须具有特定的方位、以特定的方位构造和操作,因此不能理解为对本发明的限制。此外,在本发明的描述中,“多个”的含义是两个或两个以上,除非另有明确具体的限定。
图1和图2示出了本发明的第一种实施例,具体为:一种石材反打的生产方法,其关键在于,包括以下步骤:
s1:石材选型;
s2:石材被覆处理;
s3:组装模板;
s4:将按步骤s2处理后的多块石材的正面朝下铺设在按步骤s3组装的模板中;
s5:对石材之间的缝隙进行密封处理;
s6:在石材背面上布设钢筋;
s7:浇筑混凝土;
s8:平仓、压光;
s9:预制外墙蒸汽养护;
s10:拆除模板;
s11:预制外墙吊运;
s12:针对石材外表面的缺陷部位进行修补处理;
其中,s2的具体实施步骤包括:
s201:以瓦斯或喷灯烘干石材表面水分;
s202:在石材背面划出锚固件定位线,并根据锚固件的实际尺寸及预埋深度确定锚孔位置;
s203:根据锚孔位置进行钻孔作业;
s204:使用毛刷和高压气枪清除石材表面及锚孔内的粉尘;
s205:在每块石材背面的四周边缘粘贴遮护胶带;
s206:将背覆胶均匀涂抹于石材的背面,并保证锚孔充分填实,再使用刮刀刮平;
s207:在锚孔中设置锚固件,将锚孔内溢出的背覆胶重新集中在锚孔周围,确保填满锚孔孔壁与锚固件之间的空隙;
s208:在背覆胶干燥前铺洒硅砂,硅砂用量为0.7~0.8kg/㎡。;
s209:撕去遮护胶带,静置养护。
具体地,所述遮护胶带的宽度为3~6mm。
具体地,步骤s206中背覆胶的涂抹量为0.5kg/m2。
具体地,在步骤s207中,所述锚固件包括抓钩,所述抓钩钩入所述锚孔的深度不低于20mm。
具体地,在步骤s207中,所述锚固件包括抓钩,所述抓钩钩入所述锚孔的深度不低于20mm。
具体地,步骤s4还包括:将pe膜铺设在组装的模板底面,将多块石材正面朝下铺设在pe膜上。
具体地,步骤s5包括:
s501:使用亚克力条调整石材位置及缝宽;
s502:在石材缝隙中填充密封材料,并在填缝处打胶。
具体地,所述密封材料为pe泡棉条。
具体地,在步骤s8中,混凝土浇筑完成后,用铝合金刮尺初步刮平表面并打平压实,漏浆部位在平仓时应及时进行清理,以降低后期拆模难度,混凝土压光操作在混凝土初凝后进行首次压光,初凝后用钢抹子进行压光作业,压光作业时从一侧开始,从前往后倒退作业,一次压光作业完成待混凝土终凝后对构件表面进行二次压光,操作顺序同首次压光。
具体地,在步骤s9中,构件在拆模过程中必须使用专用拆模工具,在混凝土强度达到设计强度的75%才可以拆模,保证预制外墙在拆模过程中不被损坏。
具体地,在步骤s208中,硅砂用量为0.7~0.8kg/㎡。
具体地,在步骤s3中,用螺丝将底模与模台固定,然后用螺丝将各个模板连接,归方校正后,紧固螺丝,并用磁盒固定侧模板及顶模,要求两个磁盒间距不大于1000mm,模板组装完成后,在底模铺设衬垫材料。
具体地,在步骤s6中,吊点位置设置补强钢筋。
具体地,在步骤s7中,混凝土布料时应均匀布料,布料完成后,人工进行混凝土的基本平整,再将混凝土基本平整完成后进行混凝土的振捣,振动棒操作时要做到“快插慢拔”,振动棒振捣时间控制在每一点20~30秒,以混凝土表面不再显著下沉、不再出现气泡、表面泛出灰浆为准。
具体地,在步骤s11中,使用构件专用吊装夹具分别夹住构件两肋根部,选取夹取位置时应两端对称,距端长度一致,避免起吊时因夹取位置不对称造成板体歪斜而损伤。夹具安装到位后,手动旋紧夹具螺帽,确认个夹具螺帽旋紧后,方可进行试吊;构件起吊前,应确认行车吊钩与构件中心是否在同一垂线上,避免起吊时,由于受力不均造成缺边、缺角;先以慢速试吊,观察夹具受力状态,操作人员保持5m以上安全距离,保持板体慢速状态致板体脱离模台。若无法一次性吊离模台,则放下吊物,再重复试吊,直至板体整体脱离模台;板体整体脱离模台后,应检查板底表观质量,若有明显麻面、不密实等现象需进行修补,则放置于待修补区。表观质量合格品放置于厂区内临时成品堆放区。
具体地,在步骤s12中,如果构件出现破损,且可在不翻转的情况下进行修补,则吊至修补架上进行修补(架高以1000mm~1300mm为宜,方便人员修补打磨作业);构件如需翻转修补,则在地面上放置与构件长度相匹配的垫木,放置在构件的两端及中部(板中位置必须设置垫木,以防止翻板时缺边),采用45×45mm垫木与橡胶块组合使用,再将构件小心翻转并放下,板材构件表面破损修补方法参见下表:
构件缺陷类型及修补方法对照表
基于实施例一的生产方法得到的预制外墙如图3所示,所述预制外墙包括饰面外墙a及混凝土内墙b,所述饰面外墙a与所述混凝土内墙b间通过预埋的锚固件c连接固定,其中:所述饰面外墙a包括饰面石材d,所述饰面石材d的内侧涂覆有背覆胶层e,所述背覆胶层e的内侧粘接有硅砂层f。
图4示出了本发明的第二种实施例,其与实施例1的主要区别在于,步骤s2还包括保温板安装方法,该步骤在s209完成后实施,具体为:
s210:在石材8的背面安装与石材大小相同的保温板3,在安装前,生产人员对应锚固件抓钩6位置在保温板3的外侧开设容纳槽5,并对应锚固件背栓7的位置在保温板3的内侧开设与容纳槽相通的通孔,在安装保温板3时,使背栓7穿过通孔,并保证抓钩6容纳在容纳槽5内。
基于实施例二中公开的生产方法得到的预制外墙如图5所示,包括饰面外墙1、混凝土内墙2以及夹设在所述饰面外墙1与所述混凝土内墙2之间的保温板3,所述饰面外墙1、混凝土内墙2以及保温板3间通过预埋的锚固件4连接固定,其中:所述保温板3的外、内两侧分别开设有容纳槽5以及与所述容纳槽5相通的通孔,所述锚固件4包括设置在所述容纳槽5内的爪钩,所述爪钩一端嵌设于所述饰面外墙1中,另一端连接有背栓7,所述背栓7的末端穿过所述通孔延伸至所述混凝土内墙2中。优选地,大理岩、花岗岩或洞岩中的一种。所述保温板3为岩棉板或玻纤板。
具体地,所述饰面外墙1包括饰面石材8,所述饰面石材8的内侧涂覆有背覆胶层9,所述背覆胶层9的内侧粘接有硅砂层10。通过涂抹被覆胶和铺洒硅砂的方式,形成用于饰面石材8背面界面处理的双组分界面材料,增强构件整体的抗碱、不透水功能性能。
具体地,所述通孔的孔径大于所述背栓7的孔径,在浇筑混凝土内墙2时,所述通孔的孔壁与所述背栓7的侧壁间形成供混凝土通过的环形间隙。通过环形间隙的混凝土可填充于容纳槽5中,作为饰面外墙1和保温板3,以及混凝土内墙2与保温板3之间的化学锚栓,增加了预制外墙的整体稳定性。
如图6所示,为了进一步增加锚固件4的锚固效果,沿所述背栓7的长度方向开设有外螺纹11。所述背栓7上通过所述外螺纹11套接有承拉盘12。
在实施列二中,通过上述生产方法生产的预制外墙采用三层构造,集保温节能装饰于一体,构造简单,集成度高,有利于后期快速施工。通过在保温板3开设容纳槽5和通孔,配合特制的锚固件4结构,既减轻了预制外墙的整体重量,又提升了饰面外墙1、混凝土内墙2及保温板3之间的连接强度,且方便后续施工对预制外墙的吊装。利用开槽和开孔方式,能够更好的适应锚固件4结构,降低了预制外墙的整体厚度,扩大了室内利用空间。饰面外墙1采用爪钩和背栓7与混凝土内墙2连接,受力满足要求,方便了保温板3的安装,受力、抗震性能更优异,极大地提高了安全性。
在本发明的第三种实施例中,可将步骤s2、s3、s4的替换为:
s2’:组装模板形成加工模具;
s3’:将石材的正面朝下铺设在步骤s2’组装的加工模具中;
s4’:对步骤s3’铺设的石材进行被覆处理;
具体地,步骤s2’组装形成的加工模具如图7和图8所示,步骤s4’的具体实施步骤为:
s401’:以瓦斯或喷灯烘干铺设石材的背面水分;
s402’:在石材背面划出锚固件定位线,并根据锚固件的实际尺寸及预埋深度确定锚孔位置;
s403’:根据锚孔位置进行钻孔作业;
s404’:使用负压吸尘装置清除石材表面、矩形模框3’及锚孔内的粉尘;
s405’:通过吊架6’和吊装设备7’将涂胶隔离网4’吊装在步骤s3’铺设的石材背面;
s406’:调整涂胶隔离网4’上的网格5’与对应的石材对齐,保证网格围合每块石材的边缘;
s407’:在每个网格分别进行背覆胶涂抹作业,并保证锚孔充分填实,再使用刮刀刮平;
s408’:在锚孔中设置锚固件,将锚孔内溢出的背覆胶重新集中在锚孔周围,确保填满锚孔孔壁与锚固件之间的空隙;
s409’:在背覆胶干燥前铺洒硅砂,硅砂用量为0.7~0.8kg/㎡。;
s410’:通过吊架6’和吊装设备7’将涂胶隔离网4’从模框中吊出,静置养护。
请参阅图7和图8,步骤s2’的具体结构为:包括支撑台1’,设置在所述支撑台1’上的模台2’,以及设置在所述模台2’上的矩形模框3’,所述矩形模框3’的上方设置有与其形状匹配的涂胶隔离网4’,所述涂胶隔离网4’中的网格5’尺寸与所述模框中铺设的每块石材的尺寸相适应,且在所述涂胶隔离网4’的上端设置有吊架6’。为了防止背覆胶从涂胶隔离网4’底部渗漏,所述涂胶隔离网4’的底面设置有与其形状适应的密封垫8’。所述模台2’的侧壁开设有条形的安装槽9’,所述安装槽9’内安装有微振动设备10’。所矩形模框3’由至少四块模板11’围合而成,所述模板11’的下端通过紧固螺栓与所述模台2’可拆卸连接,相邻两个模板11’之间也通过紧固螺栓可拆卸连接。为了避免铺设石材边缘翘曲,使石材在模台2’上铺设得更加平整,每块所述模板11’的内侧均设置有压接台12’,所述压接台12’相对于所述模台2’的高度与铺设石材的厚度相适应。所述支撑台1’的左右两端分别设置有凸耳13’和吊环14’,所述凸耳13’通过转轴15’与锚接在地面的地锚件16’转动连接。所述模框3’内铺设有衬垫材料。
上述加工模具通过吊装设备7’将涂胶隔离网4’扣合在铺设石材的背面,利用涂胶隔离网4’上的网格5’将石材的边缘围合,从而在涂刷背覆胶时,防止背覆胶从石材的边缘垂流,避免背覆胶流至模台2’造成污染和脱模困难,同时保证预制外墙的成品质量。通过在模台2’侧壁安装微振动设备10’,可以在混凝土浇筑后快速对模框3’内的混凝土进行密实振捣,振捣的范围遍布整个模台2’,使得混凝土均匀受力,进一步提高预制墙板的成品质量;同时,由于无需生产人员使用振动棒多点振捣,因此提升了使用的便捷性,降低了生产人员的工作负担。支撑台1’在吊环14’和转轴15’的作用下,可与地面形成一定角度,便于成型预制外墙与模台2’的快速分离。在底模上铺设衬垫材料便于后期进行脱模处理,同时能有效防止成型预制墙板在脱模中损坏。
综上所述,本发明通过将饰面石材在工厂加工过程中事先打到混凝土里,形成一体的建筑预制构件,通过本方法预制的预制外墙,其石材位置精准、表面规整、附着牢固;同时,使用本方法形成的建筑预制构件具有施工快、周期短等优势,且提高了抗震性能,节省了大量的人力和物力,具有显著的社会效益和经济效益;通过密封材料对饰面石材间的缝隙进行填充,能够阻塞介质透过渗漏通道,起到水密性、气密性作用;通过涂抹被覆胶和铺洒硅砂的方式,形成用于饰面石材背面界面处理的双组分界面材料,增强构件整体的抗碱、不透水功能性能;锚固件与锚孔中填充的被覆胶形成连接强度更高的化学锚栓,增加预制外墙整体的稳定性;在石材四周粘贴遮护胶可以防止涂抹在石材背面的背覆胶垂流;在底模上铺设衬垫材料便于后期进行脱模处理。
最后需要说明的是,上述说明并非是对本发明的限制,本发明也并不仅限于上述举例,本技术领域的普通技术人员在本发明的实质范围内所做出的变化、改性、添加或替换,也应属于本发明的保护范围。
起点商标作为专业知识产权交易平台,可以帮助大家解决很多问题,如果大家想要了解更多知产交易信息请点击 【在线咨询】或添加微信 【19522093243】与客服一对一沟通,为大家解决相关问题。
此文章来源于网络,如有侵权,请联系删除


