一种汽车顶棚用仿麂皮面料的制备方法与流程



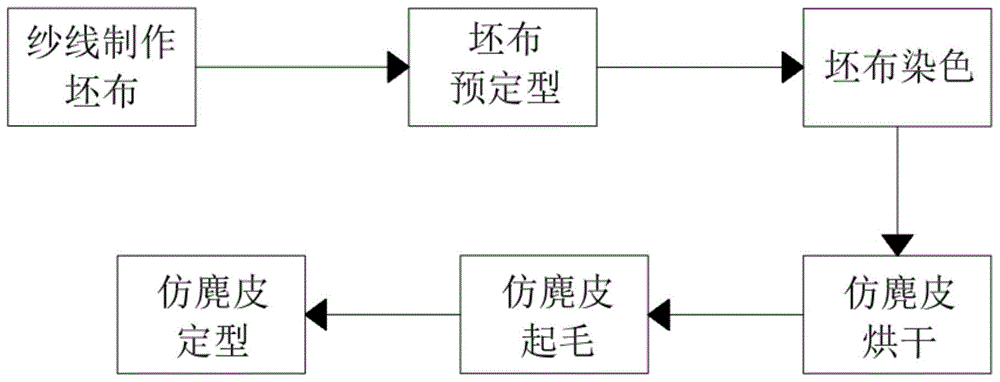
本发明涉及汽车内饰顶棚材料制作
技术领域:
,特别涉及一种汽车顶棚用仿麂皮面料的制备方法。
背景技术:
:仿麂皮绒面料是一种类似麂皮的人工面料,仿麂皮(英文名suedette)在纺织行业中把仿制麂皮毛风格的面料叫仿麂皮或者仿麂皮绒,但是在纺织行业中,一般都习惯把仿麂皮或仿麂皮绒直接叫麂皮绒。麂皮绒有针织和梭织之分,针织麂皮绒又分经编麂皮绒(比较常见)和纬编麂皮绒,梭织麂皮绒又分经向麂皮绒和纬向麂皮绒。仿麂皮绒的手感和外观都颇似天然麂皮,它的表面纹路结构也近似天然麂皮,经过特殊的后整理后,细密平整,柔软丰满,比天然的麂皮更耐用,也更易保养;被广泛应用于服装,家纺,箱包材料,灯饰材料等领域仿麂皮绒面料是使用特殊的纺织原料,并配合特殊的染整加工工艺加工而成的具有特殊风格的纺织面料,是目前国内市场较为流行的高档面料之一。由于对高档仿麂皮面料的需求,海岛丝仿麂皮面料应运而生,海岛丝是近年来开发的新型复合纤维,纤维内部岛的部分由超细聚酯组成,外部海水溶性聚酯纤维包裹,染整时通过减量开纤将海的布分溶解露出岛的部分也就是超细涤纶纤维。在汽车装饰领域,仿麂皮面料因其华丽的外观,滑糯的风格,高雅舒适的手感,近期被进一步开发作为高档材料应用于汽车内饰中。但是汽车内饰材料对阻燃性、拉伸强度、耐磨耗性、耐光色牢度等特别物性要求非常高。同时,一般仿麂皮织物面料会处于一种高密度或高收缩的紧密状态,这会使绝大多数仿麂皮面料都有一种厚重感,在汽车内饰领域中只适用于座椅,门板,方向盘等部位为此,无法满足汽车顶棚部位的高拉伸性和轻便感的要求。因此,本发明提供一种汽车顶棚用仿麂皮面料的制备方法,以提供一款新型的轻量化仿麂皮面料。技术实现要素:本发明的目的在于克服现有技术的缺陷,提供一种汽车顶棚用仿麂皮面料的制备方法,直接采用单丝常规纱线进行圆编方式编织坯布,坯布再经过预定型、染色、起毛和定型等处理而制备出一种能应用于汽车顶棚用的轻量化仿麂皮面料。为了实现上述目的,本发明提供一种汽车顶棚用仿麂皮面料的制备方法,该制备方法包括以下步骤:s1纱线制作坯布,纱线坯布采用两层涤纶纱线制作;第一层经线和第一层纬线的涤纶纱线均为单丝0.18dtex~0.22dtex的dty涤纶纱线制作;将所述第一层经线和第一层纬线安装于纬编圆机上进行编织,得到面料层;第二层经线和第二层纬线的涤纶纱线使用单丝为2dtex~3dtex的dty涤纶纱线制作;第二层经线为一股,纬线为两股,将所述第二层经线和第二层纬线安装于纬编圆机上进行编织,得到支撑层;s2坯布预定型,将步骤s1所述第一层面料层和第二层支撑层在预定型机上熔接预定型,所述预定型温度为150℃~170℃,所述预定型速度为20m/min~30m/min,得到预定型坯布;s3坯布染色,对步骤s2中得到的预定型坯布放入高温高压溢流染色机的染缸中浸润一段时间后;再向所述染缸中加入高耐光染料、分散剂、表面活性剂和阻燃剂,并把所述染缸升温到120℃~140℃,恒温进行反应20min~40min,反应完成后进行降温至50℃~60℃后溢流,溢流3次后水洗15min~20min后出缸,得到颜色一致,耐光和阻燃性好的仿麂皮坯料;所述仿麂皮坯料厚度为1.0mm~1.5mm;s4仿麂皮烘干,对步骤s3中得到的所述仿麂皮坯料进行高温烘干第一次定型,所述高温烘干温度在130℃~150℃,所述高温烘干速度15m/min~20m/min,得到幅宽为150cm~160cm,厚度为0.9mm~1.1mm的仿麂皮粗料;s5仿麂皮起毛,采用起毛机对所述步骤s4中得到的所述仿麂皮粗料的面料层进行起毛处理,起毛速度为13m/min~15m/min,起毛张力控制在6kg/c㎡~8kg/c㎡,起毛回数为3~5回,起毛后得到幅宽为122cm~128cm,厚度为1.7mm~1.8mm的仿麂皮细料;s6仿麂皮定型,对步骤s5中得到的所述仿麂皮细料进行高温第二次定型,所述高温定型温度130℃~150℃,定型速度13m/min~17m/min,得到成品幅宽在145cm~155cm,厚度为1.45mm~1.55mm的轻量化仿麂皮面料,其重量为190g/㎡~225g/㎡。优选的,所述步骤s2预定型处理还包括,在步骤s1所述面料层表面均匀涂覆季铵盐型阳离子柔软剂,然后放置于150℃~170℃的烘箱中进行烘干。优选的,将步骤s3中的染缸中浸润一段时间是指,在所述染缸中加入弱碱性溶液,然后升温到70℃~80℃,在该温度下进行反应5min~8min,反应完成后进行降温至50℃~60℃后溢流结束后;再加入弱酸溶液,再升温到50℃~60℃,恒温下进行中和反应,反应完成后开始降温,当降到室温时开始批次溢流,溢流结束后水洗一段时间后出缸进行染色。优选的,将步骤s3中所述阻燃剂为磷酸酯阻燃剂,耐光剂为纳米二氧化钛和纳米氧化银的混合氧化物,分散剂为亚甲基双萘磺酸钠,表面活性剂为聚氧乙烯脂肪醇醚。优选的,所述步骤s5仿麂皮起毛处理是指:通过起毛工序对烘干定型后得的所述仿麂皮粗料的面料层进行打毛,然后采用四道砂磨辊进行磨毛,前两道砂磨辊采用200目~220目砂磨辊,用于割断面料层的编织涤纶纱线;后两道砂磨辊采用550目~600目砂磨辊,用于磨削割断的编织涤纶纱线,得到短而密的绒毛,通过剪毛工艺使绒毛高度为0.2mm~0.4mm范围内,从而得到绒毛短而密、高度均匀的仿麂皮面料。相比于现有技术,本发明具有如下有益效果:1、本发明的轻量化仿麂皮面料,包括面料层和支撑层,通过采用单丝常规纱线进行圆编方式编织坯布,坯布再经过预定型、染色、仿麂皮烘干、起毛和仿麂皮定型步骤的处理而制备出一种能应用于汽车顶棚用的轻量化仿麂皮面料,其重量为190g/㎡~225g/㎡;且支撑层纱线作为成品面料的主体来支撑整个面料,从而保证强度;该轻量化仿麂皮面料在染色时加入分散剂、表面活性剂和阻燃剂,还具有较好的阻燃性、较高拉伸强度和收缩弹性、耐磨耗性和耐光色牢度强的优点。2、另外,通过专门的制备方法,使其面层能增强表面成膜及耐磨耗性能,改善产品的柔韧性,形成稳定的仿麂皮面料层;特别是步骤s5的仿麂皮起毛处理,通过剪毛工艺使绒毛高度为0.2mm~0.4mm范围内,从而得到绒毛短而密、高度均匀的仿麂皮面料。3、本发明的轻量化仿麂皮面料,直接使用常规涤纶纱线制作,在染色过程中,不需要强碱强酸溶液处理,减少了生产工艺的难度,降低对环境的污染;且单丝涤纶纱线比碱处理过的纱线略粗,但是整体手感相差不大,减少处理加工步骤。附图说明图1是本发明一种汽车顶棚用仿麂皮面料的制备方法工艺流程图。具体实施方式为了使本发明的目的、技术方案及优点更加清楚明白,以下结合实施例,对本发明作进一步的详细说明,以使本领域技术人员能够充分理解本发明的技术内容。应当说明的是,此处所描述的具体实施例仅用以解释本发明,并不用于限定本发明。实施例中未注明具体条件者,按照常规条件或制造商建议的条件进行。所用试剂或仪器未注明生产厂商者,均为可以通过市售购买获得的常规产品。本发明提供一种汽车顶棚用仿麂皮面料的制备方法,该制备方法包括以下步骤:s1纱线制作坯布,纱线坯布采用两层涤纶纱线制作;第一层经线和第一层纬线的涤纶纱线均为单丝0.18dtex~0.22dtex的dty涤纶纱线制作;将第一层经线和第一层纬线安装于纬编圆机上进行编织,得到面料层;第二层经线和第二层纬线的涤纶纱线使用单丝为2dtex~3dtex的dty涤纶纱线制作;第二层经线为一股,纬线为两股,将第二层经线和第二层纬线安装于纬编圆机上进行编织,得到支撑层;s2坯布预定型,将步骤s1第一层面料层和第二层支撑层在预定型机上熔接预定型,在面料层表面均匀涂覆季铵盐型阳离子柔软剂,预定型温度为150℃~170℃,预定型速度为20m/min~30m/min,得到预定型坯布;s3坯布染色,对步骤s2中得到的预定型坯布放入高温高压溢流染色机的染缸中浸润一段时间后;再向染缸中加入高耐光染料、分散剂、表面活性剂和阻燃剂,并把染缸升温到120℃~140℃,恒温进行反应20min~40min,反应完成后进行降温至50℃~60℃后溢流,溢流3次后水洗15min~20min后出缸,得到颜色一致,耐光和阻燃性好的仿麂皮坯料;仿麂皮坯料厚度为1.0mm~1.5mm;其染缸中浸润一段时间是指,在染缸中加入弱碱性溶液,然后升温到70℃~80℃,在该温度下进行反应5min~8min,反应完成后进行降温至50℃~60℃后溢流结束后;再加入弱酸溶液,再升温到50℃~60℃,恒温下进行中和反应,反应完成后开始降温,当降到室温时开始批次溢流,溢流结束后水洗一段时间后出缸进行染色;s4仿麂皮烘干,对步骤s3中得到的仿麂皮坯料进行高温烘干第一次定型,高温烘干温度在130℃~150℃,高温烘干速度15m/min~20m/min,得到幅宽为150cm~160cm,厚度为0.9mm~1.1mm的仿麂皮粗料;s5仿麂皮起毛,采用起毛机对步骤s4中得到的仿麂皮粗料的面料层进行起毛处理,起毛速度为13m/min~15m/min,起毛张力控制在6kg/c㎡~8kg/c㎡,起毛回数为3~5回,起毛后得到幅宽为122cm~128cm,厚度为1.7mm~1.8mm的仿麂皮细料;其仿麂皮起毛处理是指:通过起毛工序对烘干定型后得的仿麂皮粗料的面料层进行打毛,然后采用四道砂磨辊进行磨毛,前两道砂磨辊采用200目~220目砂磨辊,用于割断面料层的编织涤纶纱线;后两道砂磨辊采用550目~600目砂磨辊,用于磨削割断的编织涤纶纱线,得到短而密的绒毛,通过剪毛工艺使绒毛高度为0.2mm~0.4mm范围内,从而得到绒毛短而密、高度均匀的仿麂皮面料;s6仿麂皮定型,对步骤s5中得到的仿麂皮细料进行高温第二次定型,高温定型温度130℃~150℃,定型速度13m/min~17m/min,得到成品幅宽在145cm~155cm,厚度为1.45mm~1.55mm的轻量化仿麂皮面料,其重量为190g/㎡~225g/㎡。实施例1:本实施例提供的一种汽车顶棚用仿麂皮面料的制备方法,该制备方法包括以下步骤,一次制备四块仿麂皮面料:s1纱线制作坯布,纱线坯布采用两层涤纶纱线制作;第一层经线和第一层纬线的涤纶纱线均为单丝0.2dtex的dty涤纶纱线制作;将第一层经线和第一层纬线安装于纬编圆机上进行编织,得到面料层;第二层经线和第二层纬线的涤纶纱线使用单丝为2.5dtex的dty涤纶纱线制作;第二层经线为一股,纬线为两股,将第二层经线和第二层纬线安装于纬编圆机上进行编织,得到支撑层;s2坯布预定型,将步骤s1第一层面料层和第二层支撑层在预定型机上熔接预定型,在面料层表面均匀涂覆季铵盐型阳离子柔软剂,预定型温度为150℃~170℃,预定型速度为25m/min,得到预定型坯布;s3坯布染色,对步骤s2中得到的预定型坯布放入高温高压溢流染色机的染缸中浸润一段时间后;再向染缸中加入高耐光染料、分散剂、表面活性剂和阻燃剂,并把染缸升温到120℃~140℃,恒温进行反应20min~40min,反应完成后进行降温至50℃~60℃后溢流,溢流3次后水洗15min~20min后出缸,得到颜色一致,耐光和阻燃性好的仿麂皮坯料;仿麂皮坯料厚度为1.2mm;其染缸中浸润一段时间是指,在染缸中加入弱碱性溶液,然后升温到70℃~80℃,在该温度下进行反应5min~8min,反应完成后进行降温至50℃~60℃后溢流结束后;再加入弱酸溶液,再升温到50℃~60℃,恒温下进行中和反应,反应完成后开始降温,当降到室温时开始批次溢流,溢流结束后水洗一段时间后出缸进行染色;s4仿麂皮烘干,对步骤s3中得到的仿麂皮坯料进行高温烘干第一次定型,高温烘干温度在130℃~150℃,高温烘干速度15m/min,得到幅宽为155cm,厚度为1.0mm的仿麂皮粗料;s5仿麂皮起毛,采用起毛机对步骤s4中得到的仿麂皮粗料的面料层进行起毛处理,起毛速度为15m/min,起毛张力控制在7kg/c㎡,起毛回数为3~5回,起毛后得到幅宽为125cm,厚度为1.75mm的仿麂皮细料;其仿麂皮起毛处理是指:通过起毛工序对烘干定型后得的仿麂皮粗料的面料层进行打毛,然后采用四道砂磨辊进行磨毛,前两道砂磨辊采用200目~220目砂磨辊,用于割断面料层的编织涤纶纱线;后两道砂磨辊采用550目~600目砂磨辊,用于磨削割断的编织涤纶纱线,得到短而密的绒毛,通过剪毛工艺使绒毛高度为0.2mm~0.4mm范围内,从而得到绒毛短而密、高度均匀的仿麂皮面料;s6仿麂皮定型,对步骤s5中得到的仿麂皮细料进行高温第二次定型,高温定型温度130℃~150℃,定型速度15m/min,得到成品幅宽在150cm,厚度为1.5mm的轻量化仿麂皮面料。按照上述方法制备的轻量化仿麂皮面料重量检测结果参见表1。从表1中的测量数据可以看出,轻量化仿麂皮面料在190g/㎡~225g/㎡范围内(测定方法依据gb/t4669-2008纺织品机织物单位长度质量和单位面积质量的测定)。实施例2:与实施例1相比区别在于,该制备方法包括以下步骤,一次制备四块仿麂皮面料:s1纱线制作坯布,第一层其涤纶纱线均为单丝0.19dtex的dty涤纶纱线制作;第二层其涤纶纱线均为单丝为2.8dtex的dty涤纶纱线制作;s2坯布预定型,预定型温度为150℃~170℃,预定型速度为20m/min,得到预定型坯布;s3坯布染色,仿麂皮坯料厚度为1.1mm;s4仿麂皮烘干,对步骤s3中得到的仿麂皮坯料进行高温烘干第一次定型,高温烘干温度在130℃~150℃,高温烘干速度20m/min,得到幅宽为150cm,厚度为0.95mm的仿麂皮粗料;s5仿麂皮起毛,采用起毛机对步骤s4中得到的仿麂皮粗料的面料层进行起毛处理,起毛速度为14m/min,起毛张力控制在7.8kg/c㎡,起毛回数为3~5回,起毛后得到幅宽为123cm,厚度为1.78mm的仿麂皮细料;s6仿麂皮定型,对步骤s5中得到的仿麂皮细料进行高温第二次定型,高温定型温度130℃~150℃,定型速度16m/min,得到成品幅宽在149cm,厚度为1.55mm的轻量化仿麂皮面料。按照上述方法制备的轻量化仿麂皮面料重量检测结果参见表1。从表1中的测量数据可以看出,轻量化仿麂皮面料在190g/㎡~225g/㎡范围内(测定方法依据gb/t4669-2008纺织品机织物单位长度质量和单位面积质量的测定)。实施例3:与实施例1相比区别在于,该制备方法包括以下步骤,一次制备四块仿麂皮面料:s1纱线制作坯布,第一层其涤纶纱线均为单丝0.21dtex的dty涤纶纱线制作;第二层其涤纶纱线均为单丝为2.1dtex的dty涤纶纱线制作;s2坯布预定型,预定型温度为150℃~170℃,预定型速度为30m/min,得到预定型坯布;s3坯布染色,仿麂皮坯料厚度为1.45mm;s4仿麂皮烘干,对步骤s3中得到的仿麂皮坯料进行高温烘干第一次定型,高温烘干温度在130℃~150℃,高温烘干速度17m/min,得到幅宽为158cm,厚度为1.05mm的仿麂皮粗料;s5仿麂皮起毛,采用起毛机对步骤s4中得到的仿麂皮粗料的面料层进行起毛处理,起毛速度为14.5m/min,起毛张力控制在6.8kg/c㎡,起毛回数为3~5回,起毛后得到幅宽为127cm,厚度为1.72mm的仿麂皮细料;s6仿麂皮定型,对步骤s5中得到的仿麂皮细料进行高温第二次定型,高温定型温度130℃~150℃,定型速度14m/min,得到成品幅宽在154cm,厚度为1.42mm的轻量化仿麂皮面料。按照上述方法制备的轻量化仿麂皮面料重量检测结果参见表1。从表1中的测量数据可以看出,轻量化仿麂皮面料在190g/㎡~225g/㎡范围内(测定方法依据gb/t4669-2008纺织品机织物单位长度质量和单位面积质量的测定)。表1为该方法制备的轻量化仿麂皮面料重量检测结果。科目实施例1实施例2实施例3第一块(单位g/㎡)191.616191.776191.824第二块(单位g/㎡)220.624220.8220.128第三块(单位g/㎡)201.504203.104201.824第四块(单位g/㎡)206.832207.152206.144通过上述实施例,我们可知,该轻量化仿麂皮面料其重量为190g/㎡~225g/㎡;且支撑层纱线作为成品面料的主体来支撑整个面料,从而保证强度;该轻量化仿麂皮面料在染色时加入分散剂、表面活性剂和阻燃剂,还具有较好的阻燃性、较高拉伸强度和收缩弹性、耐磨耗性和耐光色牢度强的优点,具有广阔的应用前景。需要指出的是,上述较佳实施例仅为说明本发明的技术构思及特点,其目的在于让熟悉此项技术的人士能够了解本发明的内容并据以实施,并不能以此限制本发明的保护范围。凡根据本发明精神实质所作的等效变化或修饰,都应涵盖在本发明的保护范围之内。当前第1页1 2 3 
起点商标作为专业知识产权交易平台,可以帮助大家解决很多问题,如果大家想要了解更多知产交易信息请点击 【在线咨询】或添加微信 【19522093243】与客服一对一沟通,为大家解决相关问题。
此文章来源于网络,如有侵权,请联系删除
相关标签: 涤纶面料



tips