天然纤维及其制品的一种超临界混合流体闪爆处理方法与流程



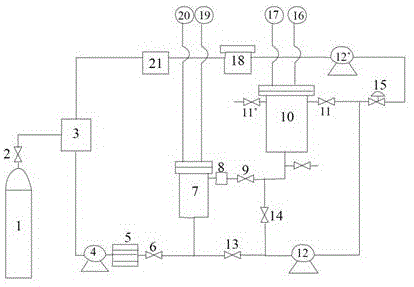
本发明涉及纺织染整加工技术领域技术领域,更具体地说,特别涉及天然纤维及其制品的一种超临界混合流体闪爆处理方法。
背景技术:
目前,我国经济社会发展与资源环境约束的矛盾日益突出,环境保护面临严峻的挑战。越来越多的传统印染行业,因为其大量的排放和污染,印染后的废水不易处理,面临着被竞争淘汰、被市场抛弃的危机。所以,寻找一种绿色、安全、环境友好型的染色方法迫在眉睫。
二氧化碳在自然状态下是一种无色、无臭、易制得的惰性气体,其分子为直线型,两个氧原子对称分布在碳原子两边,属于极性分子。且因为其临界温度和临界压力较为温和,为31.1℃和7.38mpa,成为了超临界流体染色中最为广泛的染色介质;超临界co2流体染色技术使用co2流体作为染色介质,可完全的代替水,并且工艺短、操作方便不产生工业上的废水污染,彻底的解决了因纺织品加工所带来的环境污染所造成的问题。
到目前为止,超临界co2流体染色技术在合成纤维如聚酯、聚酰胺使用分散染料已经到达了商业化的生产需求。然而,由于传统用于染色天然纤维都含有羟基、氨基基团,极性较大,所以染色过程中一般都使用直接染料、活性染料、酸性染料等极性大的染料进行染色。但由于超临界co2是非极性的,对这些极性染料的溶解度较低或不溶解,所以染色时,超临界co2流体携带的染料量低,染色后色深值极低,没有商用价值。并且溶解于超临界co2流体的分散染料由于分子量小,分子结构简单,缺少活性官能团,使分散染料对天然纤维的亲和力较小,从而也无法真正实现对天然纤维的染色。所以,天然纤维染色一直是超临界co2流体染色中的一大难点。
技术实现要素:
本发明提供了天然纤维及其制品的一种超临界混合流体闪爆处理方法,有效实现对天然纤维或其制品的改性处理,提高其在超临界co2流体的染色性能,解决了传统水浴染色中高能耗、高污染、高排放,染料难回收、难处理等问题。
根据本发明的一个方面,提供了天然纤维及其制品的一种超临界混合流体闪爆处理方法,包含有以下步骤:
将天然纤维或天然纤维制品按照预定形式装填在闪爆处理单元内,将闪爆处理单元转入闪爆处理装置内;
将闪爆处理装置连接非co2介质装置,在标准大气压下,向闪爆处理装置内部通入非co2介质,结束后断开与非co2介质装置的连接;
将闪爆处理装置连接co2介质装置,向闪爆处理装置内部充入co2介质,同时进行加热升温;当闪爆处理装置内部的混合流体的改性处理温度和改性处理压力达到预设值后,按照流体循环、流体静止的处理顺序依次处理预定的改性处理时间,使流体均匀、充分进入并分布于纤维内相;
控制分离回收单元的压力和/或温度,进行不同温差和/或不同压差的闪爆处理;
将闪爆处理装置在闪爆时间内快速泄压或瞬间泄压,对天然纤维或天然纤维制品进行闪爆处理;
开启分离回收单元的气体回收泵,对不同的介质进行分离回收,并使闪爆系统内压力降低至大气压,然后取出处理样品,完成对干态天然纤维或天然纤维制品的闪爆处理。
进一步的,所述的天然纤维为棉、麻、真丝、羊毛中的一种或几种,但不限于。
进一步的,所述的天然纤维制品为纤维、纱线、织物中的一种或几种,但不限于。
进一步的,当样品为纤维时,利用机械外力作用对蓬松的纤维进行整齐、均匀的逐层挤压加工,使其能按照一定紧密度进行平整装填在闪爆处理单元内;
当样品为纱线时,利用机械外力对纱线进行加工,使其整齐、均匀的以一定间隔的卷绕加工,使其能够均匀、平整的卷绕在闪爆处理单元内;
当样品为织物时,利用机械外力对平整的织物进行整齐、均匀卷绕加工,使其能够均匀、平整的卷绕在闪爆处理单元内。
进一步的,所述闪爆处理单元采用外覆非导致制热性表面材料制作而成,所述闪爆处理单元四周及中心空管上分布有若干镂空小孔。
进一步的,所述的闪爆处理单元采用聚四氟乙烯材料制作而成。
进一步的,所述非co2介质为饱和水蒸汽、过热水蒸汽、甲醇、乙醇、丙酮、酸、碱中的一种或多种。
进一步的,所述改性处理压力为0-30mpa。
进一步的,所述改性处理温度为90-180℃。
进一步的,所述改性处理时间为0-60min。
进一步的,所述流体循环与静止状态的时间比为1:5-10:1。
进一步的,所述闪爆时间为0-40s。
进一步的,根据所需要进行的闪爆次数,对天然纤维或天然纤维制品进行多次重复操作。
进一步的,所述的分离回收单元的温度为0-180℃,压力为0~28mpa。
在本发明中,天然纤维或天然纤维制品经过机械压紧的方式在特制的闪爆处理单位中以层状紧密装填,使得天然纤维或天然纤维制品在装置内分布均匀;通过一定的非co2介质如饱和蒸汽的处理,和临界态的co2流体共同作用下;处理一段时间后,进行快速泄压,瞬间造成的压差使得天然纤维内部孔径涨大、纤维分子间氢键断裂、纤维大分子自由度增加、纤维的无定形区增加,染料分子更容易进入纤维分子的内部,改善天然纤维或其制品在超临界co2流体内的染色性能。并且,本方法操作方便、工艺简单、工艺流程短、无废水污染、处理效率高。
通过本发明提供的天然纤维及其制品的超临界混合流体闪爆处理方法,可有效实现对天然纤维或其制品的改性处理,提高其在超临界co2流体的染色性能,解决了传统水浴染色中高能耗、高污染、高排放,染料难回收、难处理等问题。同时,本发明操作简单、方便,可有效的实现对天然纤维加工处理,不改变天然纤维的优良性能的同时,改良其染色性能。
附图说明
附图用来提供对本发明的进一步理解,并且构成说明书的一部分,与本发明的实施例一起用于解释本发明,并不构成对本发明的限制。在附图中:
图1是天然纤维及其制品的超临界混合流体闪爆处理方法的原理图;
图2是闪爆处理单元的剖面图。
图中:1、co2储罐;2、第一截止阀;3、冷凝器;4、加压泵;5、预热器;6、第二截止阀;7、染料溶解单元;8、过滤器;9、第三截止阀;10、闪爆处理单元;11、第四截止阀;11’、第五截止阀;12、循环泵;12’、气体回收泵;13、第六截止阀;14、第七截止阀;15、微调阀;16、温度计;17、压力表;18、分离釜;19、染料温度计;20、染料压力表;21、净化器;22、co2流体和染料入口;23、非co2介质出入口截止阀;24、流体出口;25、快开结构;26、闪爆处理单元密封盖;27、非co2介质入口。
具体实施方式
下面将结合本发明实施例中的附图,对本发明实施例中的技术方案进行清楚、完整地描述,显然,所描述的实施例仅仅是本发明一部分实施例,而不是全部的实施例。基于本发明中的实施例,本领域普通技术人员在没有做出创造性劳动前提下所获得的所有其他实施例,都属于本发明保护的范围。
本发明实施例所采用的纤维为棉纤维,染色前未经过处理的干态纤维;所用染料为超临界co2专用活性分散黄scf-ay02,该染料为发明人实验室制品。
参见附图1、图2所示,本发明实施例中所采用的天然纤维及其制品的超临界混合流体闪爆处理方法,在闪爆处理装置中进行闪爆处理。
闪爆处理单元10底部设置有co2流体和染料入口22,顶部设置有闪爆处理单元密封盖26,闪爆处理单元密封盖26顶部还连接有温度计16和压力表17,分别用于测量闪爆处理装置内的温度和压力值;闪爆处理单元密封盖26的两侧设置有两个快开结构25,用于快速泄压。闪爆处理单元10顶部设置有非co2介质入口27和流体出口24,底部设置有非co2介质出入口截止阀23,将干态的棉纤维采用机械压紧的方式,在闪爆处理单元10内进行一定紧密度装填,然后将闪爆处理单元采用闪爆处理单元密封盖26进行密闭,关闭闪爆处理单元密封盖26。关闭整个闪爆处理装置中的第三截止阀9、第七截止阀14,打开非co2介质出入口截止阀23,向闪爆处理单元内通入一定量的非co2介质,可以为饱和蒸汽、过热蒸汽、甲醇、乙醇、丙酮等有机溶剂、酸、碱中的一种或多种,并调节第五截止阀11’的开合度,向闪爆处理装置内部冲入co2;保持闪爆处理装置内的一定压力为0-10mpa,对纤维进行处理0-30min;控制分离回收单元的系统参数如温度和压力到预定值分别为0-180℃、0~28mpa。然后快速开启介质出口截止阀泄压,并保证泄压的时间为0-40s。开启分离回收系统的气体回收泵,对不同处理介质进行分离回收,并使闪爆系统内压力降低至大气压,然后取出样品,完成对干态天然纤维或天然纤维制品的闪爆处理。
处理结束后,关闭非co2介质和co2介质的入口截止阀,关闭第四截止阀11、第五截止阀11’,打开染料溶解单元的第三截止阀9,将闪爆处理单元10作为染色单元,在闪爆处理单元10内进行染色,向闪爆处理单元10内部通入溶解染料和co2流体,并根据预定的染色工艺流程及参数,启动由co2储罐1、冷凝器3、加压泵4、预热器5在内的加压系统对染色循环系统增压和流体预热和升温,开启第一截止阀2、第二截止阀6,并使染料溶解单元7内的染料充分溶解;染料溶解单元7连接有染料温度计19和染料压力表20。当染色循环系统温度达到预定温度如130℃、压力达到预设值如20mpa后,加压泵4停泵,并关闭第二截止阀6,开启染色循环回路中循环泵12,开启第六截止阀13,使溶解染料经过滤器8过滤后随流体循环,并与待染样品充分上染。染料上染过程中流体循环时间与流体静态时间比为10:1。在静态及循环条件下溶解染料通过自身的分子热运动及流体传质与染色单元中的纯棉短纤维充分接触,并完成吸附上染、扩散及固着过程。
保温保压染色完成后,开启微调阀15对系统泄压,利用由气体回收泵12’、分离釜18、净化器21、冷凝器3等组成的分离回收系统对染色循环系统中的染料及流体进行分离和回收。
流体分离回收结束后,再次重复上述操作对纤维进行在线清洗,温度为30-100℃,压力为8-35mpa、流体的动静循环时间比为1:5-10:1,清洗时间为10-120min。清洗结束后,再利用泄压系统对气体、染料进行分离回收,并使染色单元中压力达到大气压。最后开启流体闪爆处理单元10,将染色纤维从装置里取出。
参照上述处理步骤及工艺,用活性分散染料对棉纤维进行染色,其分析测试及其结果如下:
1.纤维表面色深值的测定
利用hunterlabultrascanpro型分光测色仪对超临界co2流体闪爆处理纤维样品进行表面色深值的测定。测试时,选择d65光源,10°视角,纤维均匀混合制样,每个样品随机测试8个点,最后计算算术平均值。
其中,i代表第i个测试点(i=1,2,3,…,n;此处n=8);
2.纤维保水率的测定
根据纺织行业标准fz/t50040—2018。对短棉纤维进行保水率的测试,测试其处理后的亲水性能是否发生改变。具体步骤为:
(1)将流体闪爆后的棉纤维进行开松,使纤维卷曲束打开,整体处于蓬松状态,待用。
(2)然后将不同条件的闪爆处理纤维分别取2g,进行开松,然后放在同一个环境下平衡24小时后,确保纤维回潮率一致,达到调湿平衡。
(3)将经过调湿平衡后的纤维准确称量m0(2.00±0.01)g,记作纤维质量m0;并将纤维放入已经制好的金属圆筒中,圆筒规格为高度(80±1)mm,直径(50±1)mm,一端封口。
(4)取2000ml烧杯,将蒸馏水加至刻度,测量水温,并保证水温恒定,保持在(20±2)℃。
(5)将金属圆筒及其中的纤维浸润在烧杯蒸馏水中,待试样完全浸没,开始计时。10min后将浸没的试样用不锈钢镊子夹起,注意在取出试样时,不要过度挤压纤维团。
(6)将取出的式样置于沥干装置上,在恒温恒压环境中将过量液体沥干,沥干时间为(30±1)min。将沥干完成后的纤维置于玻璃皿中,用电子天平将沥干后的纤维称重,记作m1,精确至0.001g。操作尽可能的轻柔仔细,防止不必要的水分损失。
(7)每次试验完成后,用滴管将烧杯中蒸馏水重新加满至刻度线,保持每次浸润纤维水的体积以及温度都保持一致。重复上述步骤,将每个试样都进行测量,并记录准确结果。
(8)将上述实验步骤中所得到的纤维浸润前的质量m0和纤维浸润和沥干后的质量m1代入到计算公式(3-1)中,可得到保水率。
实施例1:
对一定量纯棉纤维进行改性处理,通入1g/l的饱和水蒸汽在流体闪爆处理单元,密闭系统。启动增压泵充入定量co2,使压力达到5mpa。同时将闪爆处理装置内部加热升温至预定温度为130℃。当温度和压力到达设置值时,以流体循环、流体静止处理时间比为5:1的循环比开启循环泵,处理10min。按闪爆工艺或要求分别控制分离回收单元的系统参数如温度和压力分别为20℃、0.1mpa。然后打开泄压阀,快速泄压,泄压时间即闪爆时间为8s,整个闪爆过程处理一次。
处理完成后,取2g流体闪爆的棉纤维在超临界co2流体内进行染色,染色工艺为:染色压力为20mpa,染色温度为120℃,染色时间为60min,浴比为1:1000。染色结束后,在线清洗温度为80℃,压力为20mpa,总清洗时间为30min。清洗完成后,取出样品用分光测色仪测量表面色深值。再取2g处理后的棉纤维,放置于保水率装置内,根据保水率测定步骤使纤维润湿,然后测其润湿并沥干后质量m1,再根据公式(2)算得其保水率值。
经测试,实施例1通过流体闪爆改性处理的棉纤维,其染色的表面色深值(k/s)为1.04,其处理样的保水率为79.0%。
表1-1实施例1中闪爆改性处理后棉纤维染色的参数表
对比例1:
本对比例提供了一个空白对比例,采用未处理的棉纤维在超临界co2流体内进行染色,染色工艺同实施例1。再取2g染色处理后的纤维,放置于保水率装置内,根据保水率测定步骤使纤维润湿,然后测其润湿并沥干后质量m1,再根据公式(2)算得其保水率值。染色的表面色深值(k/s)为0.75,其处理样的保水率为49.2%。
表1-2对比例1中未闪爆改性处理后棉纤维染色的参数表
由于在混合流体闪爆处理的过程中,对棉纤维施加了饱和水蒸汽,这对纤维会产生一定程度的溶胀作用,有利于水蒸汽渗入到纤维内部,在瞬间泄压过程中,高温高压的水蒸汽和co2形成的混合流体在纤维内部的空隙瞬间释放出来,纤维内部以及热蒸汽的高速流动,使得纤维内发生一定程度的机械爆裂,破坏分子内氢键,使分子间作用力减弱,同时使纤维内空隙增多,孔径增大。使得水分子更易渗透进入纤维的内部,增加纤维的吸水性能,所以在进行保水率测量后,经过混合流体闪爆处理后的棉纤维其保水率明显提升,保水率从49.2%升高至79%。
棉纤维在混合流体闪爆膨化处理过程中,水蒸汽和co2流体在纤维内部流动,在棉纤维分子内晶胞之间产生摩擦,使得分子内结晶区分裂变小,使得纤维内氢键减弱,无定形区大分子链段发生重排,纤维可及度增加;高压高热的水蒸汽和co2形成的混合流体渗入到纤维内部后,在泄压的同时从封闭的孔隙瞬间释放出来,使得棉纤维内部紧密堆砌的结构得到有效疏松,纤维内部孔径增大;同时,混合流体闪爆处理产生的大量能量也极大破坏分子内氢键,改变纤维内大分子链段的排列。所以,经过混合流体闪爆处理后,无定形区域增多、氢键的断裂,使得染料在超临界co2流体内更易扩散至纤维内部。所以,经过混合流体闪爆处理后,纤维的表面色深值从0.75升高至1.04。
实施例2:
本实施例提供了一种超临界混合流体闪爆处理方法,其步骤与实施例1基本相同,区别在于:改性处理温度为70℃。
利用实施例2中的工艺处理棉纤维,经处理后染色的表面色深值(k/s)为0.64,其处理样的保水率为60.0%。
表2实施例2中闪爆改性处理后棉纤维染色的参数表
实施例3:
本实施例提供了一种超临界混合流体闪爆处理方法,其步骤与实施例1基本相同,区别在于:改性处理温度为110℃。
利用实施例3中的工艺处理棉纤维,经处理后染色的表面色深值(k/s)为0.93,其处理样的保水率为70.9%。
表3实施例3中闪爆改性处理后棉纤维染色的参数表
从实施例1、实施例2和实施例3可知,在改性处理温度70℃到130℃区间,随着温度的升高,保水率逐渐上升。由于温度的升高使得水分子更易渗透进入纤维的内部,增加纤维的吸水性能,所以在进行保水率测量后,经过混合流体闪爆处理后的纤维其保水率明显提升。
因此,随着改性处理温度升高,纤维的吸水保水能力增强,从而导致闪爆处理后纤维的保水率提高,在70℃处理温度保水率为60.0%,升高至110℃以达到70.9%,升高至130℃可以达到79.0%。
当处理温度从70℃到130℃时,随着处理温度升高,混合流体闪爆的棉纤维表面色深值增加明显。随着温度越高,分子动能越大,混合流体在棉纤维分子晶胞之间产生摩擦越频繁,同时闪爆所释放的能量越大,纤维经过混合流体闪爆处理后无定形区域增多、大分子链段排列越明显。
因此,经过混合流体闪爆棉纤维在超临界co2流体内染色,随着改性处理温度升高,其纤维表面色深值越高。在70℃时,纤维的表面色深值为0.64,上升至110℃纤维的表面色深值0.93,上升至130℃纤维的表面色深值为1.04。
实施例4:
本实施例提供了一种超临界混合流体闪爆处理方法,其步骤与实施例1基本相同,区别在于:改性处理压力为8mpa。
利用实施例4中的工艺处理棉纤维,经处理后染色的表面色深值(k/s)为0.93,其处理样的保水率为80.6%。
表4实施例4中闪爆改性处理后棉纤维染色的参数表
实施例5:
本实施例提供了一种超临界混合流体闪爆处理方法,其步骤与实施例1基本相同,区别在于:改性处理压力为12mpa。
利用实施例5中的工艺处理棉纤维,经处理后染色的表面色深值(k/s)为0.97,其处理样的保水率为87.6%。
表5实施例5中闪爆改性处理后棉纤维染色的参数表
实施例6:
本实施例提供了一种超临界混合流体闪爆处理方法,其步骤与实施例1基本相同,区别在于:改性处理压力为16mpa。
利用实施例6中的工艺处理棉纤维,经处理后染色的表面色深值(k/s)为0.92,其处理样的保水率为76.3%。
表6实施例6中闪爆改性处理后棉纤维染色的参数表
实施例7:
本实施例提供了一种超临界混合流体闪爆处理方法,其步骤与实施例1基本相同,区别在于:改性处理压力为20mpa。
实施例7工艺处理棉纤维,经处理后染色的表面色深值(k/s)为1.03,其处理样的保水率为77.4%。
表7实施例7中闪爆改性处理后棉纤维染色的参数表
从实施例1、实施例4、实施例5、实施例6、实施例7可知,处理压力从5mpa到20mpa区间,混合流体闪爆棉纤维保水率变化幅度较小,基本都在75%到80%之间。
在本方法中,低于5mpa的co2在分离的过程中,以亚临界流体状态的co2和水蒸汽在快速泄压的过程中迅速转换为气体。这种转变使得原有在纤维内部的co2流体和水蒸汽在纤维内部释放巨大能量,同时分布在空隙内的流体瞬间冲出,使得纤维的孔径增大,增大了纤维中的各微隙孔径,水分子更易渗入纤维内部。使得纤维的亲水性能提升,混合流体闪爆棉纤维的保水性能提升。而高于5mpa的co2与水蒸汽通过系统内部的循环分离回收至系统的分离釜内,这一过程减压速率缓慢,时间较长,纤维的膨化作用较小。因此,当处理压力从5mpa到20mpa,混合流体闪爆纤维的保水率变化幅度不大。
处理压力从5mpa到20mpa区间,染色后纤维的表面色深值变化幅度较小。在本实验中,低于5mpa的co2在分离的过程中,混合流体闪爆使得纤维产生机械膨化,纤维分子间氢键减弱或断裂,增大了纤维中的各微隙孔径,同时增加纤维的无定形区比例,从而使得染料分子更容易进入纤维内部,促进染料上染纤维,使得活性分散黄scf-ay02染料在超临界co2流体更易上染。而高于5mpa的co2与水蒸汽由于泄压速率缓慢,时间较长,对纤维的膨化作用较小。因此,当处理压力从5mpa到20mpa,混合流体闪爆纤维的表面色深值变化幅度不大。
实施例8:
本实施例提供了一种超临界混合流体闪爆处理方法,其步骤与实施例1基本相同,区别在于:改性处理时间为5min。
利用实施例8中的工艺处理棉纤维,经处理后染色的表面色深值(k/s)为0.73,其处理样的保水率为64.6%。
表8实施例8中闪爆改性处理后棉纤维染色的参数表
实施例9:
本实施例提供了一种超临界混合流体闪爆处理方法,其步骤与实施例1基本相同,区别在于:改性处理时间为30min。
利用实施例9中的工艺处理棉纤维,经处理后染色的表面色深值(k/s)为0.75,其处理样的保水率为53.2%。
表9实施例9中闪爆改性处理后棉纤维染色的参数表
从实施例1、实施例8和实施例9可知,随着处理时间的延长,有更多水分留在纤维空隙内部,经过闪爆处理的过程中,混合流体闪爆使得棉纤维的孔径增大,空隙增多,水分子更易渗入到棉纤维内部纤维亲水性能更好。当处理时间为5min时,棉纤维的保水率为64.6。当处理时间为10min时,棉纤维的保水率为79.0%。而当处理时间继续延长,纤维内的水蒸汽不断进入流体介质中而流失越多,使得预期的效果反而变差,当处理时间为30min时,纤维的保水率为53.2。
当处理时间从5min到10min时,染色纤维的表面色深值有明显提升。在混合流体的高压高温处理过程中,随着时间的适当延长,棉纤维含有的水蒸汽可进一步充分渗透、扩散进入到纤维内部,并对纤维进行充分膨化。同时,在纤维内部空隙中形成的co2流体和水蒸汽混合流体,在闪爆过程中瞬间释放出来,由此产生的剧烈膨胀使得纤维产生机械膨化,破坏或减弱棉纤维大分子体系中的氢键,增大了纤维中的各微隙孔径。从而增大了纤维的可及度及可染性,使得活性分散黄scf-ay02染料在超临界co2内更易上染纤维,所以其表面色深值提升。
当继续延长处理时间时,水蒸汽从纤维空隙中流失过多,使得混合流体闪爆纤维的表面色深值下降,使得预期结果反而下降。当处理时间为30min时,纤维的表面色深值为0.75。
实施例10:
本实施例提供了一种超临界混合流体闪爆处理方法,其步骤与实施例1基本相同,区别在于:闪爆时间为12s。
利用实施例10中的工艺处理棉纤维,经处理后染色的表面色深值(k/s)为1.01,其处理样的保水率为65.6%。
表10实施例10中闪爆改性处理后棉纤维染色的参数表
实施例11:
本实施例提供了一种超临界混合流体闪爆处理方法,其步骤与实施例1基本相同,区别在于:闪爆时间为16s。
利用实施例11中的工艺处理棉纤维,经处理后染色的表面色深值(k/s)为0.97,其处理样的保水率为47.6%。
表11实施例11中闪爆改性处理后棉纤维染色的参数表
从实施例10-11可知,随着闪爆时间的延长,混合流体闪爆棉纤维的保水率逐渐降低。在混合流体闪爆处理过程中,延长闪爆时间会导致纤维内形成的混合流体缓慢释放,其对纤维膨化效果变差,故纤维内部的空隙数量和纤维内部空隙孔径会越小,纤维的亲水性能下降。
因此,闪爆时间的延长,纤维的保水率下降。当闪爆时间为8s时,纤维的保水率为79.0%;当闪爆时间为12s时,纤维的保水率为65.6%;当闪爆时间为16s时,纤维的保水率为47.6%。
同时,随着闪爆时间的延长,染色纤维的表面色深值降低。在混合流体闪爆处理的过程中,混合流体在放气的过程中对纤维瞬间挤压力越大,释放的能量越大,使得纤维分子间氢键断裂或减弱,纤维大分子自由度增加,纤维孔径变大,同时增加纤维的无定形区比例。而延长闪爆时间,导致纤维内的混合流体在闪爆过程中释放缓慢,使得混合流体闪爆对分子间氢键的作用变小、大分子自由度降低、纤维的内部空隙孔径变小,同时无定形区的比例下降,不利于染料进入到纤维内部,混合流体闪爆的表面色深值下降。当闪爆时间为8s时,纤维的表面色深值为1.04;当闪爆时间为12s时,纤维的表面色深值为1.01;当闪爆时间为16s时,纤维的表面色深值为0.97。
实施例12:
本实施例提供了一种超临界混合流体闪爆处理方法,其步骤与实施例1基本相同,区别在于:将此改性处理按照实例1工艺处理2次。
利用实施例12中的工艺处理棉纤维,经处理后染色的表面色深值(k/s)为1.08,其处理样的保水率为246.3%。
表12实施例12中闪爆改性处理后棉纤维染色的参数表
实施例13:
本实施例提供了一种超临界混合流体闪爆处理方法,其步骤与实施例1基本相同,区别在于:将此改性处理按照实例1工艺处理3次。
利用实施例13中的工艺处理棉纤维,经处理后染色的表面色深值(k/s)为1.19,其处理样的保水率为334.8%。
表13实施例13中闪爆改性处理后棉纤维染色的参数表
实施例14:
本实施例提供了一种超临界混合流体闪爆处理方法,其步骤与实施例1基本相同,区别在于:将此改性处理按照实例1工艺处理4次。
利用实施例14中的工艺处理棉纤维,经处理后染色的表面色深值(k/s)为1.29,其处理样的保水率为541.3%。
表14实施例14中闪爆改性处理后棉纤维染色的参数表
从实施例1、实施例12、实施例14可知,随着纤维闪爆次数的增多,纤维的保水率增大。特别是随着闪爆次数增加到1次以上时,可以看到纤维保水率急剧上升,甚至在第四次处理时可以达到541.3%。可能是由于经过多次混合流体闪爆后,纤维分子间部分氢键彻底断裂,纤维中的各微隙孔径经过多次闪爆后,空隙孔径继续增大,使得水分子更易渗入到纤维内部。所以,闪爆次数的增多,纤维的保水率增大。
闪爆次数的增加,混合流体闪爆纤维的表面色深值增加。纤维经过混合流体闪爆处理后,纤维分子间氢键断裂或减弱,纤维大分子自由度增加,纤维孔径变大,同时增加纤维的无定形区比例,使得活性分散黄scf-ay02染料在超临界co2内更易上染纤维,所以其表面色深值增加。经过一次处理后的纤维相较于未处理的纤维,其纤维的表面色深值有明显提升。而随着闪爆次数增加,混合流体闪爆处理的过程再发生一次,维分子间氢键断裂或减弱程度增大,纤维大分子自由度继续增加,纤维内部空隙孔径继续增大,同时无定形区域比例继续增加,使得染料更易上染纤维,纤维表面上色深值增加。同时,经过多次闪爆处理后,纤维的保水率也增加显著。
经上述实施例可得出,天然纤维或天然纤维制品经过机械压紧的方式在特制的闪爆处理单位中以层状紧密装填,使得天然纤维或天然纤维制品在装置内分布均匀;通过一定的非co2介质如饱和蒸汽的处理,和临界态的co2流体共同作用下;处理一段时间后,进行快速泄压,瞬间造成的压差使得天然纤维内部孔径涨大、纤维分子间氢键断裂、纤维大分子自由度增加、纤维的无定形区增加,染料分子更容易进入纤维分子的内部,改善天然纤维或其制品在超临界co2流体内的染色性能。并且,本方法操作方便、工艺简单、工艺流程短、无废水污染、处理效率高。
本方法还可适用于毛条、纱线、梭织物、针织物、无纺布等材料。并且,纤维、纱线或织物可以同时进行处理,以充分利用闪爆处理单元空间。
通过本天然纤维及其制品的超临界混合流体闪爆处理方法,可有效实现对天然纤维或其制品的改性处理,提高其在超临界co2流体的染色性能,解决了传统水浴染色中高能耗、高污染、高排放,染料难回收、难处理等问题。同时,本发明操作简单、方便,可有效的实现对天然纤维加工处理,不改变天然纤维的优良性能的同时,改良其染色性能。
最后应说明的是:以上所述仅为本发明的优选实施例而已,并不用于限制本发明,尽管参照前述实施例对本发明进行了详细的说明,对于本领域的技术人员来说,其依然可以对前述各实施例所记载的技术方案进行修改,或者对其中部分技术特征进行等同替换。凡在本发明的精神和原则之内,所作的任何修改、等同替换、改进等,均应包含在本发明的保护范围之内。
起点商标作为专业知识产权交易平台,可以帮助大家解决很多问题,如果大家想要了解更多知产交易信息请点击 【在线咨询】或添加微信 【19522093243】与客服一对一沟通,为大家解决相关问题。
此文章来源于网络,如有侵权,请联系删除


