一种热泵蒸汽机及用于热泵蒸汽机的相变套管式换热器的制作方法



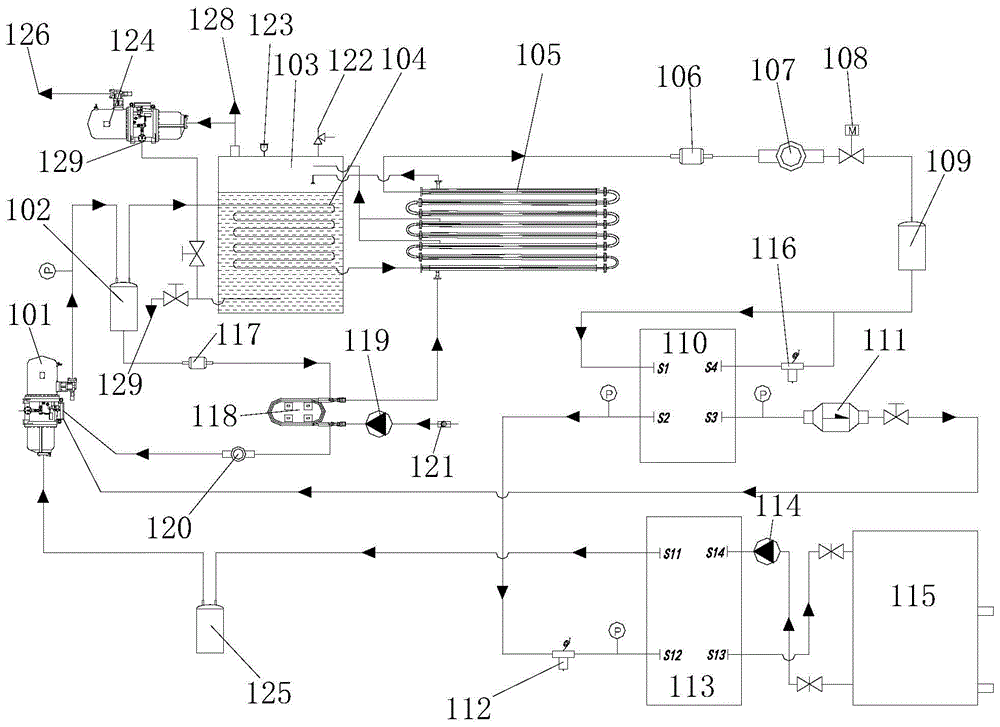
本发明涉及热泵蒸汽机技术领域,尤其涉及一种热泵蒸汽机及用于热泵蒸汽机的相变套管式换热器,能够实现电力驱动制取饱和蒸汽,符合电能替代发展战略。
背景技术:
随着国家能源消费改革、大气污染防治及节能减排低碳发展战略的推进,以电能为驱动力的产品在能源消费市场占据比例会有大幅度提升。目前,工业园区管网蒸汽供应普遍采用燃气锅炉,一次能源转化率低,排放大量co2和nox,并且初装成本高。与之对应,以电驱动的先进高温蒸汽热泵技术具有明显的节能性,其相比燃气锅炉,节能率可达50%-60%,相比电锅炉,能效系数更是2-3倍。因此,有必要研究电驱动高温蒸汽热泵技术。
目前国际上采用高温热泵生产高温高压热水,再利用高压热水降压闪蒸的方式制取蒸汽,由于降压过程伴随温度下降,造成
技术实现要素:
本发明的目的是克服上述现有技术的不足,提供一种热泵蒸汽机及用于热泵蒸汽机的相变套管式换热器。
本发明是通过以下技术方案来实现的:一种热泵蒸汽机,包括冷媒压缩机、蒸汽压缩机、一级冷凝器、二级冷凝器、经济器、蒸发器、油冷器、气液分离器、油分离器、进水泵、循环水泵、热源水箱和承压水箱、单向阀、第一过滤器、第二过滤器、第一视液镜、第二视液镜及相关连接管道、阀门;所述一级冷凝器浸泡在所述承压水箱内,所述冷媒压缩机依次连接所述油分离器、一级冷凝器、二级冷凝器、第一过滤器、第一视液镜、储液罐、经济器;所述经济器一出口通过所述单向阀与所述冷媒压缩机相接,所述经济器另一出口与所述蒸发器相接,所述蒸发器与所述热源水箱相连,所述蒸发器一出口依次连接所述气液分离罐、冷媒压缩机;所述油分离器依次连接所述第二过滤器、油冷器、第二视液镜后与所述冷媒压缩机相接;所述油冷器一端连接有所述进水泵,其另一端依次连接所述二级冷凝器、承压水箱;所述承压水箱顶部设有低温蒸汽出口管,其下部设有高温热水出口管,所述蒸气压缩机的进口与所述低温蒸汽出口管相接,所述蒸气压缩机的喷液口通过支路与所述承压水箱下部相接。
原水经油冷器、二级冷凝器部分蒸发,蒸发的气体经排气管进入承压水箱上部,未蒸发的液体及未排出的蒸汽经二级冷凝器管程出口进入承压水箱,在有高温热水需求时,由承压水箱底部高温热水出口管供应高温热水,在蒸汽需求时,承压水箱内液态水被一级冷凝器内高温高压工质煮沸产生蒸汽,与二级冷凝器内产生的蒸汽混合经蒸汽排出管口进入蒸汽压缩机,以高温蒸汽的形式排出系统;高温热水出口管设置一支路,用于满足双螺杆水润滑蒸汽压缩机的喷液需求;本系统提供一种高温热水、低温蒸汽、高温蒸汽的热泵蒸汽机组,采用二级冷凝器直接相变换热、采用冷媒压缩和蒸汽压缩,吸收余热热源的能量,制取饱和蒸汽。所述一级冷凝器采用盘管换热器,所述一级冷凝器放置在液位以下,并通过支撑件固定在所述承压水箱内;所述一级冷凝器管内流经高温高压冷媒;二级冷凝器的设置,大幅降低一级冷凝器的换热面积,实现热泵蒸汽机的直接换热蒸发制取蒸汽。
所述承压水箱的压力设为0.2mpa,所述承压水箱上部设有卸压阀、安全阀。卸压阀、安全阀的设置,可在承压水箱内压力超过卸压阀设定压力时自动开启卸压,保证承压水箱的压力安全,防止发生意外。
所述冷媒压缩机采用双螺杆压缩机,所述蒸汽压缩机采用双螺杆无油水润滑压缩机。冷媒压缩机采用双螺杆压缩机,可耐高温,外置油冷却器可带走机身热量;蒸汽压缩机采用双螺杆无油水润滑压缩机,采用喷水工艺消除机身过热,避免高温热泵蒸汽机的局部过热现象。
一种用于热泵蒸汽机的相变套管式换热器,所述二级冷凝器为相变套管式换热器,所述相变套管式换热器包括壳程管道、内置于壳程管道内的管程管道、水侧连通器;所述壳程管道由上而下通过支持件固定而设有若干层,所述管程管道两端分别设有法兰,所述管程管道一端的法兰通过连接弯管与上层所述管程管道同一端的法兰相接,所述管程管道另一端的法兰通过连接弯管与下层所述管程管道同一端的法兰相接,两端的连接弯管交替分布;所述壳程管道一端通过所述水侧连通器与上层所述壳程管道同一端部相连,所述壳程管道另一端通过所述水侧连通器与下层所述壳程管道同一端部相连,两端的水侧连通器交替分布;最下层所述管程管道一端设有与所述一级冷凝器相连的冷媒入口管,最上层所述管程管道一端设有与所述第一过滤器相连的冷媒出口管;最下层所述壳程管道底部设有与所述油冷器连通的水侧入口管,最上层所述壳程管道顶部设有与所述承压水箱连通的水侧出口管;所述管程管道采用变径管,所述管程管道外部通过三角支撑板固定在所述壳程管道内;冷媒流经所述管程管道内,水侧流经所述管程管道外部与所述壳程管道内部之间的空间;所述壳程管道开设有与所述承压水箱相连的排气管。壳程管道由上而下设有多层,并在两端通过通过法兰、连接弯管交替设置,可实现增长冷媒与水的循环路径,增大换热面积;管程管道采用变径管,输送可靠性高,可保证流速及换热效果;蒸发过程产生的蒸汽由排气管快速进入承压水箱。
连通所述油冷器的水侧连通器与所述冷媒入口管位于同一端,连通所述承压水箱的水侧连通器与所述冷媒出口管位于同一端;所述管程管道同一截面的外部设有三块所述三角支撑板,三块所述三角支撑板以该截面中心为基准,两两之间互成120度夹角;所述三角支撑板采用锯齿形结构。三块锯齿形结构的三角支撑板的设置,既可将管程管道稳定固定在壳程管道内,又可将流动过程中的气泡破碎和快速分离。
沿管道长度方向,所述管程管道外部设置有若干块所述三角支撑板。
与现有技术对比,本发明的优点在于:本发明采用两级冷凝器,降低承压水箱内换热盘管的换热面积,二级冷凝器采用相变式套管换热器,套管换热器内完成部分蒸发过程,产生的蒸汽经排气管和管程出口进入承压水箱;一级冷凝器固定在承压水箱内,由支撑件固定,放置在液位以下位置,利用高温高压冷媒冷凝放热原理,直接换热制取蒸汽;热泵蒸汽机组是完全以电力驱动,采用高温工质循环吸收余热热源热量,制取低温蒸汽,再辅助无油水润滑的蒸汽压缩机,制取高温蒸汽。
附图说明
图1为本发明实施例热泵蒸汽机的流程示意图;
图2为本发明实施例二级冷凝器的结构示意图;
图3为本发明实施例壳程管道与管程管道的结构示意图;
图4为本发明实施例壳程管道与管程管道的侧视图。
图中附图标记含义:1、壳程管道;2、管程管道;3、支持件;4、水侧出口管;5、水侧连通器;6、水侧入口管;7、排气管;8、冷媒入口管;9、冷媒出口管;10、法兰;11、三角支撑板;101、冷媒压缩机;102、油分离器;103、承压水箱;104、一级冷凝器;105、二级冷凝器;106、第一过滤器;107、第一视液镜;108、第一电磁阀;109、储液罐;110、经济器;111、单向阀;112、第三电磁阀;113、蒸发器;114、循环水泵;115、热源水箱;116、第二电磁阀;117、第二过滤器;118、油冷器;119、进水泵;120、第二视液镜;121、流量计;122、安全阀;123、卸压阀;124、蒸汽压缩机;125、气液分离罐;126、高温蒸汽出口管;127、高温热水出口管;128、低温蒸汽出口管;129、喷液口。
具体实施方式
下面结合附图和具体实施方式对本发明的内容做进一步详细说明。
实施例
参阅图1至图4,为一种热泵蒸汽机,包括冷媒压缩机101、蒸汽压缩机124、一级冷凝器104、二级冷凝器105、经济器110、蒸发器113、油冷器118、气液分离器、油分离器102、进水泵119、循环水泵114、热源水箱115和承压水箱103、单向阀111、第一过滤器106、第二过滤器117、第一视液镜107、第二视液镜120及相关连接管道、阀门;一级冷凝器104浸泡在承压水箱103内,冷媒压缩机101依次连接油分离器102、一级冷凝器104、二级冷凝器105、第一过滤器106、第一视液镜107、储液罐109、经济器110;经济器110一出口通过单向阀111与冷媒压缩机101相接,经济器110另一出口与蒸发器113相接,蒸发器113与热源水箱115相连,蒸发器113一出口依次连接气液分离罐125、冷媒压缩机101;油分离器102依次连接第二过滤器117、油冷器118、第二视液镜120后与冷媒压缩机101相接;油冷器118一端连接有进水泵119,其另一端依次连接二级冷凝器105、承压水箱103;承压水箱103顶部设有低温蒸汽出口管128,其下部设有高温热水出口管127,蒸气压缩机的进口与低温蒸汽出口管128相接,蒸气压缩机的喷液口129通过支路与承压水箱103下部相接。
原水经油冷器118、二级冷凝器105部分蒸发,蒸发的气体经排气管7进入承压水箱103上部,未蒸发的液体及未排出的蒸汽经二级冷凝器105管程出口进入承压水箱103,由承压水箱103设有的喷淋口进入承压水箱103内,在有高温热水需求时,由承压水箱103底部高温热水出口管127供应高温热水,在蒸汽需求时,承压水箱103内液态水被一级冷凝器104内高温高压工质煮沸产生蒸汽,与二级冷凝器105内产生的蒸汽混合经蒸汽排出管口进入蒸汽压缩机124,以高温蒸汽的形式从蒸气压缩机的高温蒸汽出口管126排出系统;高温热水出口管127设置一支路,用于满足双螺杆水润滑蒸汽压缩机124的喷液需求;本系统提供一种高温热水、低温蒸汽、高温蒸汽的热泵蒸汽机组,采用二级冷凝器105直接相变换热、采用冷媒压缩和蒸汽压缩,吸收余热热源的能量,制取饱和蒸汽。一级冷凝器104采用盘管换热器,一级冷凝器104放置在液位以下,并通过支撑件固定在承压水箱103内;一级冷凝器104管内流经高温高压冷媒;二级冷凝器105的设置,大幅降低一级冷凝器104的换热面积,实现热泵蒸汽机的直接换热蒸发制取蒸汽。
本实施例中,经济器110是个换热器,通过制冷剂自身节流蒸发吸收热量从而使另一部分制冷剂得到过冷,是现有技术设备,因此不展开分析。阀门包括若干电磁阀(电子膨胀阀),如第一电磁阀108、第二电磁阀116、第三电磁阀112。由进水泵119、循环水泵114、热源水箱115和承压水箱103、一级冷凝器104、二级冷凝器105,以及阀门、流量计121等组成本实施例的水循环回路;由二级冷凝器105、承压水箱103、蒸汽压缩机124及管道、阀门等组成本实施例的蒸汽循环回路。第一视液镜107与储液罐109之间连接有第一电磁阀108;经济器110设有四个进出口,分别为第一进口s1、第一出口s2、第二出口s3、第二进口s4,储液罐109的出口分两个支路,一个支路与经济器110的第一进口s1相接,另一个支路通过第二电磁阀116与第二进口s4相接;储液罐109的第二出口s3通过单向阀111与冷媒压缩机101相接。蒸发器113设有四个进出口,分别为第三出口s11、第三进口s12、第四出口s13、第四进口s14;储液罐109的第一出口s2通过第三电磁阀112与蒸发器113的第三进口s12相接,蒸发器113的第四出口s13与热源水箱115的进口相接,热源水箱115的出口通过循环水泵114与蒸发器113的第四进口s14相接,蒸发器113的第三出口s11与气液分离罐125的进口相接。在实际应用中根据需求在连接管路上加入流量计121或压力计p,本实施例中,流量计121设置在进水泵119之前。
承压水箱103的压力设为0.2mpa,承压水箱103上部设有卸压阀123、安全阀122。卸压阀123、安全阀122的设置,可在承压水箱103内压力超过卸压阀123设定压力时自动开启卸压,保证承压水箱103的压力安全,防止发生意外。
热源水箱115利用工厂余热废水,一般在50-70℃之间,承压水箱103的高温热水出口温度在120℃左右,低温蒸汽出口为0.2mpa蒸汽,高温蒸汽出口为0.7mpa蒸汽。高温循环工质采用r245fa,冷凝压力为130℃。
冷媒压缩机101采用双螺杆压缩机,蒸汽压缩机124采用双螺杆无油水润滑压缩机。冷媒压缩机101采用双螺杆压缩机,可耐高温,外置油冷却器可带走机身热量;蒸汽压缩机124采用双螺杆无油水润滑压缩机,采用喷水工艺消除机身过热,避免高温热泵蒸汽机的局部过热现象。
参阅图3及图4,为一种用于热泵蒸汽机的相变套管式换热器,二级冷凝器105为相变套管式换热器,相变套管式换热器包括壳程管道1、内置于壳程管道1内的管程管道2、水侧连通器5;壳程管道1由上而下通过支持件3固定而设有若干层,管程管道2两端分别设有法兰10,管程管道2一端的法兰10通过连接弯管与上层管程管道2同一端的法兰10相接,管程管道2另一端的法兰10通过连接弯管与下层管程管道2同一端的法兰10相接,两端的连接弯管交替分布;壳程管道1一端通过水侧连通器5与上层壳程管道1同一端部相连,壳程管道1另一端通过水侧连通器5与下层壳程管道1同一端部相连,两端的水侧连通器5交替分布;最下层管程管道2一端设有与一级冷凝器104相连的冷媒入口管8,最上层管程管道2一端设有与第一过滤器106相连的冷媒出口管9;最下层壳程管道1底部设有与油冷器118连通的水侧入口管6,最上层壳程管道1顶部设有与承压水箱103连通的水侧出口管4;管程管道2采用变径管,管程管道2外部通过三角支撑板11固定在壳程管道1内;冷媒流经管程管道2内,水侧流经管程管道2外部与壳程管道1内部之间的空间;壳程管道1开设有与承压水箱103相连的排气管7。壳程管道1由上而下设有多层,并在两端通过通过法兰10、连接弯管交替设置,可实现增长冷媒与水的循环路径,增大换热面积;管程管道2采用变径管,输送可靠性高,可保证流速及换热效果;蒸发过程产生的蒸汽由排气管7快速进入承压水箱103。
连通油冷器118的水侧连通器5与冷媒入口管8位于同一端,连通承压水箱103的水侧连通器5与冷媒出口管9位于同一端;管程管道2同一截面的外部设有三块三角支撑板11,三块三角支撑板11以该截面中心为基准,两两之间互成120度夹角;三角支撑板11采用锯齿形结构。三块锯齿形结构的三角支撑板11的设置,既可将管程管道2稳定固定在壳程管道1内,又可将流动过程中的气泡破碎和快速分离。
沿管道长度方向,管程管道2外部设置有若干块三角支撑板11。
上列详细说明是针对本发明可行实施例的具体说明,该实施例并非用以限制本发明的专利范围,凡未脱离本发明所为的等效实施或变更,均应包含于本案的专利范围中。
起点商标作为专业知识产权交易平台,可以帮助大家解决很多问题,如果大家想要了解更多知产交易信息请点击 【在线咨询】或添加微信 【19522093243】与客服一对一沟通,为大家解决相关问题。
此文章来源于网络,如有侵权,请联系删除


