一种根据加热功率智能控制的蒸汽发生系统的制作方法



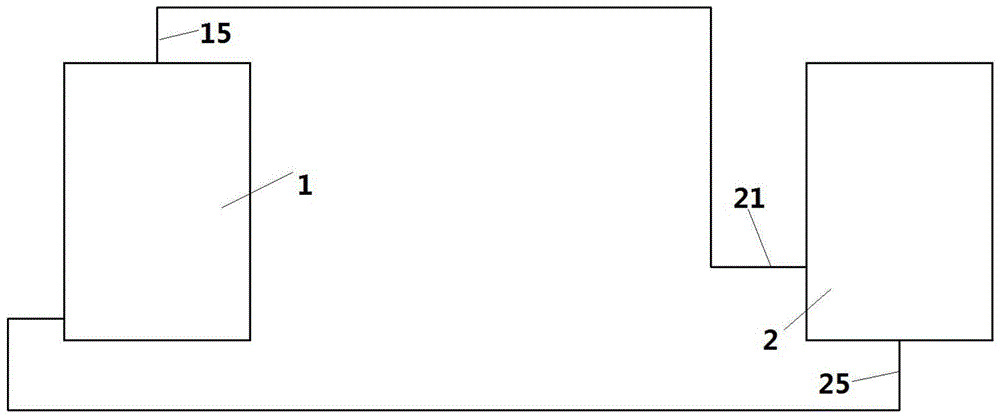
本发明涉及锅炉技术领域,尤其涉及一种智能控制的蒸发器。
背景技术:
蒸发器是利用燃料或其他能源的热能把水加热成为蒸汽的机械设备。蒸发器应用领域广泛,广泛适用于制衣厂,干洗店,饭店,馍店,食堂,餐厅,厂矿,豆制品厂等场所。蒸汽发生系统包括蒸发器,蒸发器产生的蒸汽一般应用于蒸汽利用装置,但是蒸汽利用装置和蒸发器之间缺少相应的智能控制调节,例如根据蒸汽利用设备的条件来控制蒸发器的蒸汽产生。因此本发明主要针对蒸汽发生系统的进行智能控制方面的改进。
此外,蒸汽利用设备中一般的管道存在汽水混合物。换热管在蒸发过程中,不可避免的会携带液体到蒸汽管内,同时因为冷凝端的放热冷凝,从而使得冷凝端中存在液体,液体也不可避免的进入蒸汽管,从而使得换热管内的流体是汽液混合物,汽液混合物存在导致汽体混成一团,与液体之间换热能力下降,大大的影响了换热的效率。
技术实现要素:
本发明针对现有技术中的不足,提供一种智能控制的蒸发器,同时也提供了一种新式结构的蒸发器利用设备,而且该蒸发器具有加热迅速、温度分布均匀、功率自动控制、安全可靠的功能,提高了加热效率。
为实现上述目的,本发明采用如下技术方案:
一种蒸发器系统,包括蒸发器和蒸汽利用设备,蒸发器中加热产生的蒸汽通过蒸汽入口管进入蒸汽利用设备,在蒸汽利用设备中充分换热利用后再循环混到蒸发器中进行加热;
所述蒸发器包括蒸汽室,所述蒸汽室内设置电加热装置;
所述的蒸汽室内设置水位传感器,所述水位传感器、电加热器与控制器数据连接,所述控制器根据测量的蒸汽室内的水位自动控制电加热器的加热功率。
作为优选,如果水位过低,控制器则通过控制降低电加热器的功率或者直接关闭电加热器的加热,从而避免因为加热功率过高造成的蒸汽产出过大,造成水位的进一步降低,如果水位过高,则通过增加电加热器的加热功率,提高蒸汽产出,从而降低水位。
作为优选,当测量的水位低于第一水位时,控制器控制电加热装置以第一功率进行加热;当测量的水位低于比第一水位低的第二水位时,控制器控制电加热装置以低于第一功率的第二功率进行加热;当测量的水位低于比第二水位低的第三水位时,控制器控制电加热装置以低于第二功率的第三功率进行加热;当测量的水位低于比第三水位低的第四水位时,控制器控制电加热装置以低于第三功率的第四功率进行加热;当测量的水位低于比第四水位低的第五水位时,控制器控制电加热装置以低于第四功率的第五功率进行加热;当测量的水位低于比第五水位低的第六水位时,控制器控制电加热装置停止加热。
作为优选,第一水位是第二水位的1.1-1.15倍,第二水位是第三水位的1.15-1.2倍,第三水位是第四水位的1.2-1.25倍,第四水位是第五水位的1.25-1.3倍。
作为优选,第一功率是第二功率的1.6-1.7倍,第二功率是第三功率的1.5-1.6倍,第三功率是第四功率的1.4-1.5倍,第四功率是第五功率的1.3-1.4倍
作为优选,蒸汽利用设备包括集箱和蒸汽管,所述蒸汽管从集箱向上延伸。
作为优选,所述蒸汽管内设置稳流装置,所述稳流装置是片状结构,所述片状结构在蒸汽管的横截面上设置;所述稳流装置为正方形通孔和正八边形通孔组成,所述正方形通孔的边长等于正八边形通孔的边长,所述正方形通孔的四个边分别是四个不同的正八边形通孔的边,正八边形通孔的四个互相间隔的边分别是四个不同的正方形通孔的边。
作为优选,蒸汽管的横截面是正方形。
作为优选,蒸汽管内设置多个稳流装置,相邻稳流装置之间的距离为m1,正方形通孔的边长为b1,蒸汽管的边长为b2,满足如下要求:
m1/b2=a*ln(b1/b2)+b
其中a,b是参数,其中1.725<a<1.733,4.99<b<5.01;
11<b2<46mm;
1.9<b1<3.2mm;
18<m1<27mm。
进一步优选,随着b1/b2的增加,a越来越小,b越来越大。
作为优选,a=1.728,b=4.997;
作为优选,所述稳流装置包括下面两种类型中的至少一种,第一种类型是正方形中心稳流装置,正方形通孔位于蒸汽管的中心,第二种类型是正八边形中心稳流装置,正八边形通孔位于蒸汽管的中心。
作为优选,相邻设置的稳流装置类型不同。
作为优选,蒸汽管内设置多个稳流装置,距离蒸汽管入口的距离为h,相邻稳流装置之间的间距为s,s=f1(h),满足如下要求:
s’<0,s”>0。
作为优选,蒸汽管内设置多个稳流装置,距离蒸汽管入口的距离为h,稳流装置的正方形通孔的边长为d,d=f3(h),满足如下要求:
d’<0,d”>0。
作为优选,所述蒸汽管内壁设置凹槽,所述稳流装置的外壳设置在凹槽内,所述外壳的内壁与蒸汽管的内壁对齐。
本发明具有如下优点:
1)本发明通过上述的设置,一方面避免了水位过低造成电加热装置的干烧,造成电加热装置的损坏以及产生安全事故,另一方面,避免了因为水位过高而造成的蒸汽室内的水量过大,从而造成蒸汽产出率过低。
2)本发明提供一种新式结构的蒸汽利用装置,通过设置蒸汽管以及连接片,可以实现扩大蒸汽管换热面积,而且还可以起到强化传热的目的。
3)本发明提供了一种新式正方形通孔和正八边形通孔相结合的新式结构的稳流装置,通过正方形和正八边形,使得形成的正方形孔和正八边形孔的边形成的夹角都是大于等于90度,从而使得流体能够充分流过每个孔的每个位置,避免或者减少流体流动的短路。本发明通过新式结构的稳流装置将两相流体分离成液相和气相,将液相分割成小液团,将气相分割成小气泡,抑制液相的回流,促使气相顺畅流动,起到稳定流量的作用,具有减振降噪的效果,提高换热效果。相对于现有技术中的稳流装置,进一步提高稳流效果,强化传热,而且制造简单。
4)本发明通过合理的布局,使得正方形和正八边形通孔分布均匀,从而使得整体上的横街面上的流体分割均匀,避免了现有技术中的环形结构沿着周向的分割不均匀问题。
5)本发明通过正方形孔和正八边形孔的间隔均匀分布,从而使得大孔和小孔在整体横截面上分布均匀,而且通过相邻的稳流装置的大孔和小孔的位置变化,使得分隔效果更好。
6)本发明通过设置稳流装置为片状结构,使得稳流装置结构简单,成本降低。
7)本发明通过在吸热管高度方向上设置相邻稳流装置之间的距离、稳流装置的孔的边长、吸热管的管径、管间距等参数大小的规律变化,研究了上述参数的最佳的关系尺寸,从而进一步达到稳流效果,降低噪音,提高换热效果。
8)本发明通过对稳流装置各个参数的变化导致的换热规律进行了广泛的研究,在满足流动阻力情况下,实现换热效果的最佳关系式。
附图说明:
图1为本发明蒸发器系统的结构示意图。
图2是本发明蒸发器结构示意图。
图3为图2蒸发器的控制结构示意图。
图4是本发明的蒸汽换热器正面切面示意图。
图5是本发明的蒸汽换热器侧面切面示意图。
图6是本发明蒸汽换热器的另一具体结构示意图。
图7是本发明蒸汽换热器的连通管和连接板结构示意图。
图8本发明稳流装置横截面结构示意图;
图9本发明稳流装置另一个横截面结构示意图;
图10是本发明稳流装置在蒸汽管内布置示意图;
图11是本发明稳流装置在蒸汽管内布置横截面示意图
图12是图4上部观察示意图。
图13是图6上部观察示意图。
图中:1、蒸发器,11、蒸汽室,12、补水箱,13、电加热装置,14水入口管路,15蒸汽出口管路,16水泵,2蒸汽利用设备,21蒸汽入口管,22蒸汽管,23连接板,24集箱,25水出口管,3连通管,4稳流装置,41正方形通孔,42正八边形通孔,43边,5控制器
具体实施方式
一种蒸发器系统,包括蒸发器1和蒸汽利用设备2。蒸发器1中加热产生的蒸汽通过蒸汽入口管21进入蒸汽利用设备2,在蒸汽利用设备中充分换热利用后再循环到蒸发器1中进行加热。
所述蒸发器结构如图1所示,包括蒸汽室11、补水箱12、水泵16,所述补水箱12通过管路连接水泵16,所述水泵16通过管路连接蒸汽室11,所述蒸汽室11内设置电加热装置13,所述蒸汽室11上部设置蒸汽出口管路15,所述蒸汽室11设置水入口管路14。
所述的水从补水箱12通过水泵16进入蒸汽室11中,在蒸汽室11中通过电加热装置13加热,产生的蒸汽通过蒸汽出口管路15排出。
作为优选,蒸汽出口管路15排出的蒸汽进行利用后,通过水入口管路14进入蒸汽室11中,以达到循环利用的目的。
作为优选,所述补水箱12设置入口管路,所述入口管路连接自来水管,通过自来水管补充水。作为优选,自来水管和补水箱12之间设置净化装置,对自来水进行净化,避免补水箱内电加热装置的结垢,影响加热的效果。
作为优选,所述蒸汽室11的横截面为圆形结构。
作为优选,所述电加热装置13为多个。所述电加热装置是电加热管。所述电热加装置13从蒸汽室11底部壁面向上竖直设置,如图1所示。
本发明可以实现如下控制:
(一)温度控制
作为优选,所述蒸汽入口管21中设置温度传感器,用于测量蒸汽入口管21中蒸汽的温度。所述温度传感器、电加热装置13与控制器5数据连接,所述控制器5根据温度传感器测量的温度来自动控制电加热装置13的加热功率。
作为优选,如果温度传感器测量的温度低于一定的温度,则控制器控制电加热装置增加加热功率。如果温度传感器测量的温度高于一定的温度,则为了避免热量浪费,控制器控制电加热装置降低加热功率。
通过控制加热功率,保证入口温度满足要求,避免入口温度过高,造成热量损失,入口温度过低,造成热量不满足实际要求。
作为优选,如果检测温度数据低于第一数值,则控制器5自动提高电加热装置13的加热功率,如果测量的温度数据高于第二数值,则控制器5自动降低电加热装置13的加热功率,所述第二数值大于第一数值。
作为优选,当测量的温度低于第一温度时,电加热装置13以第一功率进行加热;当测量的温度低于比第一温度低的第二温度时,电加热装置13以高于第一功率的第二功率进行加热;当测量的温度低于比第二温度低的第三温度时,电加热装置13以高于第二功率的第三功率进行加热;当测量的温度低于比第三温度低的第四温度时,电加热装置13以高于第三功率的第四功率进行加热;当测量的温度低于比第四温度低的第五温度时,电加热装置13以高于第四功率的第五功率进行加热。
作为优选,第一温度大于第二温度2-3摄氏度,第二温度大于第三温度2-3摄氏度,第三温度大于第四温度2-3摄氏度,第四温度大于第五温度2-3摄氏度。
进一步优选,第一温度大于第二温度5.5-6摄氏度,第二温度大于第三温度2.5摄氏度,第三温度大于第四温度2.5摄氏度,第四温度大于第五温度2.5摄氏度。
作为优选,第五功率是第四功率的1.08-1.18倍,第四功率是第三功率的1.08-1.18倍,第三功率是第二功率的1.08-1.18倍,第二功率是第一功率的1.08-1.18倍。
作为优选,第五功率是第四功率的1.14倍,第四功率是第三功率的1.14倍,第三功率是第二功率的1.14倍,第二功率是第一功率的1.14倍。
通过上述温度和功率的优选,尤其是通过差别化的加热功率和温差的设定,可以进一步提高加热效率,节省时间。通过实验发现,能够提高10-15%左右的加热效率。
作为优选,所述温度传感器为多个,所述控制器依据的温度数据是多个温度传感器测量的温度,来控制蒸发器的运行。
(二)水位控制
作为优选,所述的蒸汽室11内设置水位传感器,所述水位传感器、电加热器13、水泵16与控制器5数据连接,所述控制器5根据测量的蒸汽室11内的水位自动控制水泵16的功率。
作为优选,如果水位下降,控制器则通过控制提高水泵16的功率来增加进入蒸汽室11的水的流量,如果水位过高,则通过降低水泵16的功率或者关闭水泵16来减少进入蒸汽室11内水流量或者停止向蒸汽室11内补水。
通过上述的设置,一方面避免了水位过低造成的蒸汽产出率过低以及电加热装置的干烧,造成电加热装置的损坏以及产生安全事故,另一方面,避免了因为水位过高而造成的水量过大,从而造成蒸汽产出率过低。
作为优选,当测量的水位低于第一水位时,控制器5控制水泵16以第一功率进行补水;当测量的水位低于比第一水位低的第二水位时,控制器5控制水泵16以高于第一功率的第二功率进行补水;当测量的水位低于比第二水位低的第三水位时,控制器5控制水泵16以高于第二功率的第三功率进行补水;当测量的水位低于比第三水位低的第四水位时,控制器5控制水泵16以高于第三功率的第四功率进行补水;当测量的水位低于比第四水位低的第五水位时,控制器5控制水泵16以高于第四功率的第五功率进行补水。
作为优选,第一水位是第二水位的1.08-1.18倍,第二水位是第三水位的1.08-1.18倍,第三水位是第四水位的1.08-1.18倍,第四水位是第五水位的1.08-1.18倍。
作为优选,第一水位是第二水位的1.1-1.15倍,第二水位是第三水位的1.15-1.2倍,第三水位是第四水位的1.2-1.25倍,第四水位是第五水位的1.25-1.3倍。
作为优选,第五功率是第四功率的1.7-1.9倍,第四功率是第三功率的1.6-1.8倍,第三功率是第二功率的1.5-1.7倍,第二功率是第一功率的1.3-1.5倍。
通过上述水位和水泵功率的优选,尤其是通过差别化的水位和水泵功率的设定,可以快速的实现水位的恒定,提高蒸汽产出率,节省时间。通过实验发现,能够提高12-16%左右的蒸汽产出。
(三)根据水位对加热功率的控制
作为优选,所述的蒸汽室11内设置水位传感器,所述水位传感器、电加热器6与控制器5数据连接,所述控制器5根据测量的蒸汽室11内的水位自动控制电加热器的加热功率。
作为优选,如果水位过低,控制器则通过控制降低电加热器6的功率或者直接关闭电加热器6的加热,从而避免因为加热功率过高造成的蒸汽产出过大,造成水位的进一步降低,如果水位过高,则通过增加电加热器6的加热功率,提高蒸汽产出,从而降低水位。
通过上述的设置,一方面避免了水位过低造成电加热装置的干烧,造成电加热装置的损坏以及产生安全事故,另一方面,避免了因为水位过高而造成的蒸汽室内的水量过大,从而造成蒸汽产出率过低。
作为优选,当测量的水位低于第一水位时,控制器5控制电加热装置13以第一功率进行加热;当测量的水位低于比第一水位低的第二水位时,控制器5控制电加热装置13以低于第一功率的第二功率进行加热;当测量的水位低于比第二水位低的第三水位时,控制器5控制电加热装置13以低于第二功率的第三功率进行加热;当测量的水位低于比第三水位低的第四水位时,控制器5控制电加热装置13以低于第三功率的第四功率进行加热;当测量的水位低于比第四水位低的第五水位时,控制器5控制电加热装置以低于第四功率的第五功率进行加热;当测量的水位低于比第五水位低的第六水位时,控制器5控制电加热装置停止加热。
作为优选,第一水位是第二水位的1.08-1.18倍,第二水位是第三水位的1.08-1.18倍,第三水位是第四水位的1.08-1.18倍,第四水位是第五水位的1.08-1.18倍。
作为优选,第一水位是第二水位的1.1-1.15倍,第二水位是第三水位的1.15-1.2倍,第三水位是第四水位的1.2-1.25倍,第四水位是第五水位的1.25-1.3倍。
作为优选,第一功率是第二功率的1.6-1.7倍,第二功率是第三功率的1.5-1.6倍,第三功率是第四功率的1.4-1.5倍,第四功率是第五功率的1.3-1.4倍。
通过上述水位和电加热装置的功率的优选,尤其是通过差别化的水位和电加热装置的功率的设定,可以快速的实现水位的在预定的安全位置,而且水位过高的时候能够保证蒸汽产出率,节省时间。
(四)压力控制
作为优选,所述蒸汽利用设备的蒸汽入口管21上设置压力传感器,用于测量蒸汽入口管21中压力。所述压力传感器、电加热装置13与控制器5数据连接,所述控制器5根据压力传感器测量的压力来自动控制电加热装置13的加热功率。
作为优选,如果压力传感器测量的压力低于一定的压力,则控制器5控制电加热装置13启动加热。如果压力传感器测量的温度高于上限压力,则为了避免压力过大产生危险,控制器控制电加热装置13停止加热。
通过如此设置,可以根据蒸汽入口管21的压力来调节加热功率,从而保证蒸汽利用设备的换热量达到要求,同时在最大化蒸汽产出的情况下,保证蒸发器的安全。
作为优选,如果压力传感器测量的压力低于某一数值,则控制器5控制电加热装置13提高加热功率。如果压力传感器测量的温度高于一定数值,则为了避免压力过大产生危险,控制器控制电加热装置13降低加热功率。
作为优选,当测量的压力高于第一压力时,控制器5控制电加热装置13的加热功率降低到第一功率进行加热;当测量的压力高于比第一压力高的第二压力时,控制器5控制电加热装置13的加热功率降低至比第一功率低的第二功率进行加热;当测量的压力高于比第二压力高的第三压力时,控制器5控制电加热装置13的加热功率降低至比第二功率低的第三功率进行加热;当测量的压力高于比第三压力高的第四压力时,控制器5控制电加热装置13的加热功率降低至比第三功率高的第四功率进行加热;当测量的压力高于比第四压力高的第五压力时,控制器5停止电加热装置13的加热。
作为优选,第四功率是第三功率的0.4-0.6倍,第三功率是第二功率的0.6-0.8倍,第二功率是第一功率的0.7-0.9倍。
进一步优选,作为优选,第四功率是第三功率的0.5倍,第三功率是第二功率的0.7倍,第二功率是第一功率的0.8倍。
所述第五压力就是上限压力。
作为优选,所述压力传感器为多个,所述控制器依据的压力数据是多个压力传感器测量的压力,来控制蒸发器的运行。
(五)蒸汽流量控制
作为优选,所述蒸汽利用设备的蒸汽入口管21上设置流量传感器,用于测量单位时间进入蒸汽利用设备的蒸汽流量,所述流量传感器、电加热器6与控制器5数据连接。所述控制器5根据测量的蒸汽流量自动控制电加热器的功率。
作为优选,如果测量的蒸汽流量低于一定的数值,则控制器5控制电加热装置13增加加热功率。如果压力传感器测量的温度高于一定的数值,控制器控制电加热装置13降低加热功率。
通过如此设置,可以根据进入的蒸汽数量来调节加热功率,保证进入的蒸汽数量的恒定,避免数量过大或者过小,造成蒸汽数量不足或者浪费。
作为优选,当测量的流量高于第一流量时,控制器5控制电加热装置13的加热功率降低到第一功率进行加热;当测量的流量高于比第一流量高的第二流量时,控制器5控制电加热装置13的加热功率降低至比第一功率低的第二功率进行加热;当测量的流量高于比第二流量高的第三流量时,控制器5控制电加热装置13的加热功率降低至比第二功率低的第三功率进行加热;当测量的流量高于比第三流量高的第四流量时,控制器5控制电加热装置13的加热功率降低至比第三功率高的第四功率进行加热;当测量的流量高于比第四流量高的第五流量时,控制器5停止电加热装置13的加热。
作为优选,第四功率是第三功率的0.4-0.6倍,第三功率是第二功率的0.6-0.8倍,第二功率是第一功率的0.7-0.9倍。
进一步优选,作为优选,第四功率是第三功率的0.5倍,第三功率是第二功率的0.7倍,第二功率是第一功率的0.8倍。
进一步优选,第五流量是第四流量的1.1-1.2倍,第四流量是第三流量的1.2-1.3倍,第三流量是第二流量的1.3-1.4倍,第二流量是第一流量的1.4-1.5倍。
通过上述流量和电加热装置的功率的优选,尤其是通过差别化的流量和电加热装置的功率的设定,可以快速的实现流量的恒定,节省时间。
(六)水出口管路温度控制
作为优选,所述蒸汽利用设备的水出口管路21上设置温度传感器,用于测量换热后的水的温度,所述温度传感器、电加热器6与控制器5数据连接。所述控制器5根据温度传感器测量的温度来自动控制电加热器的加热功率。通过控制加热功率,保证换热后的温度满足要求,避免水温过高,造成热量损失,水温过低,造成热量不满足实际要求。
作为优选,如果温度传感器测量的温度低于一定的温度,则控制器控制电加热装置增加加热功率。如果温度传感器测量的温度高于一定的温度,例如造成热量浪费,则为了避免热量浪费,控制器控制电加热装置降低加热。通过降低加热功率,使得蒸汽输出量少,从而使得避免浪费。
作为优选,如果检测温度数据低于第一数值,则控制器5自动提高电加热装置13的加热功率,如果测量的温度数据高于第二数值,则控制器5自动降低电加热装置13的加热功率,所述第二数值大于第一数值。
作为优选,当测量的温度低于第一温度时,电加热装置13以第一功率进行加热;当测量的温度低于比第一温度低的第二温度时,电加热装置13以高于第一功率的第二功率进行加热;当测量的温度低于比第二温度低的第三温度时,电加热装置13以高于第二功率的第三功率进行加热;当测量的温度低于比第三温度低的第四温度时,电加热装置13以高于第三功率的第四功率进行加热;当测量的温度低于比第四温度低的第五温度时,电加热装置13以高于第四功率的第五功率进行加热。
作为优选,第一温度大于第二温度2-3摄氏度,第二温度大于第三温度2-3摄氏度,第三温度大于第四温度2-3摄氏度,第四温度大于第五温度2-3摄氏度。
进一步优选,第一温度大于第二温度2.5摄氏度,第二温度大于第三温度2.5摄氏度,第三温度大于第四温度2.5摄氏度,第四温度大于第五温度2.5摄氏度。
作为优选,第五功率是第四功率的1.08-1.18倍,第四功率是第三功率的1.08-1.18倍,第三功率是第二功率的1.08-1.18倍,第二功率是第一功率的1.08-1.18倍。
作为优选,第五功率是第四功率的1.14倍,第四功率是第三功率的1.14倍,第三功率是第二功率的1.14倍,第二功率是第一功率的1.14倍。
通过上述温度和功率的优选,尤其是通过差别化的加热功率和温差的设定,可以进一步提高加热效率,节省时间。通过实验发现,能够提高10-15%左右的加热效率。
作为优选,所述温度传感器为多个,所述控制器依据的温度数据是多个温度传感器12测量的温度,来控制系统的运行。
(七)蒸汽室温度控制
作为优选,所述蒸汽室中设置温度传感器,用于测量蒸汽室内中蒸汽的温度。所述温度传感器、电加热装置13与控制器5数据连接,所述控制器5根据温度传感器测量的温度来自动控制电加热装置13的加热功率。
作为优选,如果温度传感器测量的温度低于一定的温度,则控制器控制电加热装置增加加热功率。如果温度传感器测量的温度高于一定的温度,例如高于危险的临界温度,则为了避免过热,控制器控制电加热装置停止加热。
作为优选,如果检测温度数据低于第一数值,则控制器5自动提高电加热装置13的加热功率,如果测量的温度数据高于第二数值,则控制器5自动降低电加热装置13的加热功率,所述第二数值大于第一数值。
作为优选,当测量的温度低于第一温度时,电加热装置13以第一功率进行加热;当测量的温度低于比第一温度低的第二温度时,电加热装置13以高于第一功率的第二功率进行加热;当测量的温度低于比第二温度低的第三温度时,电加热装置13以高于第二功率的第三功率进行加热;当测量的温度低于比第三温度低的第四温度时,电加热装置13以高于第三功率的第四功率进行加热;当测量的温度低于比第四温度低的第五温度时,电加热装置13以高于第四功率的第五功率进行加热。
作为优选,第一温度大于第二温度2-3摄氏度,第二温度大于第三温度2-3摄氏度,第三温度大于第四温度2-3摄氏度,第四温度大于第五温度2-3摄氏度。
进一步优选,第一温度大于第二温度2.5摄氏度,第二温度大于第三温度2.5摄氏度,第三温度大于第四温度2.5摄氏度,第四温度大于第五温度2.5摄氏度。
作为优选,第五功率是第四功率的1.08-1.18倍,第四功率是第三功率的1.08-1.18倍,第三功率是第二功率的1.08-1.18倍,第二功率是第一功率的1.08-1.18倍。
作为优选,第五功率是第四功率的1.14倍,第四功率是第三功率的1.14倍,第三功率是第二功率的1.14倍,第二功率是第一功率的1.14倍。
通过上述温度和功率的优选,尤其是通过差别化的加热功率和温差的设定,可以进一步提高加热效率,节省时间。通过实验发现,能够提高10-15%左右的加热效率。
作为优选,所述温度传感器设置在蒸汽室的底壁上。
作为优选,所述温度传感器为多个,所述控制器依据的温度数据是多个温度传感器12测量的温度,来控制蒸发器的运行。
作为优选,所述蒸汽利用装置2是蒸汽换热器。所述蒸汽换热器包括集箱24和蒸汽管22,所述蒸汽管22从集箱向上延伸。如图5、6所示,所述蒸汽管22为多根,所述多根蒸汽管22按照矩阵方式排列,具有平行的多行和多列,所述多根蒸汽管之间设置连接板23,通过连接板23将多行和多列的蒸汽管连接在一起。所述蒸发器1产生的蒸汽进入集箱24,然后从集箱24中向上流动进入蒸汽管22。蒸汽管22与外部进行热交换后形成冷凝水,然后在重力的作用下返回集箱24,然后从集箱24下部的回水口返回到蒸发器1中。
作为优选,蒸汽入口管21设置在集箱24的一端或者两端。
通过设置连接板23,使得拓展换热面积,起到类似翅片的作用。
作为优选,沿着蒸汽管22的高度方向,所述的连接板23设置多层。沿着蒸汽管22的高度方向,所述连接板23在高度方向上的距离越来越小。主要是因为在研究中发现,热蒸汽都向上部走,因此随着高度的不断增加,换热能力越来越强。通过连接板23在高度方向上的距离的变化,使得整体换热均匀,避免局部温度过高或者过低。
作为优选,沿着蒸汽管22的高度方向,所述连接板23在高度方向上的距离越来越小的幅度不断增加。上述的规律变化是通过大量的实验和研究的出来的结论,通过上述幅度的变化,使得整体换热更加均匀,进一步避免局部温度过高或者过低。
作为另一种选择,如图6、13所示,所述蒸汽管之间设置连通管3。至少两个相邻的蒸汽管22之间设置连通管3。在研究中发现,在蒸发管放热的过程中,会出现不同位置的放热管的放热量不同,导致蒸汽管22之间的压力或者温度不同,这样会导致部分蒸汽管22温度过高,造成寿命缩短,一旦一个蒸汽管22出现问题,可能导致整个热管出现无法使用的问题。本发明通过大量的研究,在相邻的蒸汽管设置连通管3,可以在蒸汽管受热不同而导致压力不同的情况下,可以使得压力大的蒸汽管22内的流体快速的流向压力小的蒸汽管22,从而保持整体压力均衡,避免局部过热或者过冷。
图13展示了只是横排设置连通管,但是本申请不限于横排,可以仅仅是竖排或合横排竖排都设置。
作为优选,从蒸汽管22下部向蒸汽管22上部,相邻的蒸汽管22之间设置多个连通管3。通过设置多个连通管,能够使得流体在吸热蒸发过程中不断的均衡压力,保证整个蒸汽管内的压力均衡。
作为优选,从蒸汽管22下部向蒸汽管22上部,相邻连通管3之间的距离不断减小。此目的是为了设置更多的连通管,因为随着流体的向上流动,流体不断的放热,随着流体不断的放热,不同集热管内的放热越来越不均匀,因此通过上述设置,能够保证在流体流动过程中尽快的达到压力均衡。
作为优选,从蒸汽管22下部向蒸汽管22上部,相邻连通管之间的距离不断减小的幅度越来越大。通过实验发现,上述设置,能够保证在流体流动过程中更优更快的达到压力均衡。这也是通过大量的研究压力分布变化规律而得来的最佳的连通方式。
作为优选,从蒸汽管22下部向蒸汽管22上部,连通管3的直径不断增加。此目的是为了设置保证更大的连通面积,因为随着流体的向上流动,流体不断的放热,随着蒸汽不断的放热,不同集热管内的温度压力越来越不均匀,因此通过上述设置,能够保证在流体流动过程中尽快的达到压力均衡。
作为优选,从蒸汽管22下部向蒸汽管22上部,连通管3的直径不断增加的幅度越来越大。通过实验发现,上述设置,能够保证在流体流动过程中更优更快的达到压力均衡。这也是通过大量的研究压力分布变化规律而得来的最佳的连通方式。
作为优选,如图13所示,所述连接板23连接相邻的连通管3。
作为优选,所述的换热器是药材干燥器,所述药材设置在连接板23上,从而形成多层的药材干燥板。
作为优选,所述换热器是药液换热器,蒸汽管伸入在箱体的药液中,用于加热药液。
作为优选,所述换热器是保健品换热器,蒸汽管伸入在箱体的保健品中,用于加热保健品。
蒸汽管中因为蒸汽的换热,使得蒸汽管出现汽液两相流,一方面,蒸汽管在蒸发过程中,不可避免的会携带液体到蒸汽管内,同时因为冷凝端的放热冷凝,从而使得冷凝端中存在液体,液体也不可避免的进入蒸汽管,从而使得蒸汽管内的流体是汽液混合物,同时蒸汽管在运行过程中会因为老化产生的不凝气体,不凝气体一般上升到蒸汽管上部的冷凝端,不凝气体的的存在导致蒸汽管冷凝端内的压力增加,压力使得液体向蒸汽管内流动。大大的影响了换热的效率。因此本发明采取了新的结构,来分割汽相和液相,使得换热加强。
蒸汽管内设置稳流装置4,所述稳流装置4的结构如图8、9所示。所述稳流装置4是片状结构,所述片状结构在蒸汽管3的横截面上设置;所述稳流装置4为正方形和正八边形结构组成,从而形成正方形通孔41和正八边形通孔42。如图1所述正方形通孔41的边长等于正八边形通孔42的边长,所述正方形通孔的四个边43分别是四个不同的正八边形通孔的边43,正八变形通孔的四个互相间隔的边43分别是四个不同的正方形通孔的边43。
本发明采用新式结构的稳流装置,具有如下优点:
1)本发明提供了一种新式正方形通孔和正八边形通孔相结合的新式结构的稳流装置,通过正方形和正八边形,使得形成的正方形孔和正八边形孔的边形成的夹角都是大于等于90度,从而使得流体能够充分流过每个孔的每个位置,避免或者减少流体流动的短路。本发明通过新式结构的稳流装置将两相流体分离成液相和气相,将液相分割成小液团,将气相分割成小气泡,抑制液相的回流,促使气相顺畅流动,起到稳定流量的作用,具有减振降噪的效果,提高换热效果。相对于现有技术中的稳流装置,进一步提高稳流效果,强化传热,而且制造简单。
2)本发明通过合理的布局,使得正方形和正八边形通孔分布均匀,从而使得整体上的横街面上的流体分割均匀,避免了现有技术中的环形结构沿着周向的分割不均匀问题。
3)本发明通过正方形孔和正八边形通孔的间隔均匀分布,从而使得大孔和小孔在整体横截面上分布均匀,而且通过相邻的稳流装置的大孔和小孔的位置变化,使得分隔效果更好。
4)本发明通过设置稳流装置为片状结构,使得稳流装置结构简单,成本降低。
本发明通过设置环形稳流装置,相当于在换蒸汽管内增加了内换热面积,强化了换热,提高了换热效果。
本发明因为将气液两相在所有换蒸汽管的所有横截面位置进行了分割,从而在整个换蒸汽管截面上实现气液界面以及气相边界层的分割与冷却壁面的接触面积并增强扰动,大大的降低了噪音和震动,强化了传热。
作为优选,所述稳流装置包括两种类型,如图8,9所示,第一种类型是正方形中心稳流装置,正方形位于蒸汽管或者冷凝管的中心,如图9所示。第二种是正八边形中心稳流装置,正八边形位于蒸汽管或者冷凝管的中心,如图8所示。作为一个优选,上述两种类型的稳流装置相邻设置,即相邻设置的稳流装置类型不同。即与正方形中心稳流装置相邻的是正八边形中心稳流装置,与正八边形中心稳流装置相邻的是正方形中心稳流装置。本发明通过正方形孔和正八边形孔的间隔均匀分布,从而使得大孔和小孔在整体横截面上分布均匀,而且通过相邻的稳流装置的大孔和小孔的位置变化,使得通过大孔的流体接下来通过小孔,通过小孔的流体接下来通过大孔,进一步进行分隔,促进汽液的混合,使得分隔和换热效果更好。
作为优选,所述蒸汽管3的横截面是正方形。
作为优选,沿着流体流动的方向,蒸汽管3的管径不断的降低。主要原因如下:通过增降低蒸汽管的管径,可以增加流动的阻力,使得蒸汽管内蒸发的汽体减少的向着管径增加的方向运动,从而进一步促进整体的蒸汽管的换热均匀,避免热量都集中在蒸汽管上部进行换热。
作为优选,沿着流体流动的方向,蒸汽管3的管径不断的增加的幅度越来越大。上述管径的幅度变化是本申请人通过大量的实验和数值模拟得到的结果,通过上述的设置,能够进一步的促进环路蒸汽管的循环流动,达到换热整体均匀。
作为优选,蒸汽管内设置多个稳流装置,从蒸汽管3的入口向上延伸的方向(即图4从下部向上部方向),稳流装置之间的间距不断变小。设距离蒸汽管入口的距离为h,相邻稳流装置之间的间距为s,s=f1(h),即s是以高度h为变量的函数,s’是s的一次导数,满足如下要求:
s’<0;
主要原因是因为蒸汽管内的汽体在上升过程中会携带者液体,在上升过程中,蒸汽不断的越来越向上部集中,导致气液两相流中的汽体越来越多,因为汽液两相流中的汽相越来越多,蒸汽管内的换热能力会随着汽相增多而相对减弱,震动及其噪音也会随着汽相增加而不断的增加。因此需要设置的相邻稳流装置之间的距离越来越短。
通过实验发现,通过上述的设置,既可以最大程度上减少震动和噪音,同时可以提高换热效果。
进一步优选,从蒸汽管3的入口向上延伸的方向(即图4从下部向上部方向)相邻稳流装置之间的距离越来越短的幅度不断增加。即s”是s的二次导数,满足如下要求:
s”>0;
通过实验发现,通过如此设置,能够进一步降低7%左右的震动和噪音,同时提高8%左右的换热效果。
作为优选,蒸汽管内设置多个稳流装置,从蒸汽管3的入口向上延伸的方向(即图4从下部向上部方向),正方形的边长越来越小。距离蒸汽管入口的距离为h,正方形的边长为c,c=f2(h),c’是c的一次导数,满足如下要求:
c’<0;
进一步优选,从蒸汽管3的入口向上延伸的方向(即图4从下部向上部方向),正方形的边长越来越小的幅度不断的增加。c”是c的二次导数,满足如下要求:
c”>0。
具体理由参见前面稳流装置间距变化。
作为优选,相邻稳流装置之间的距离保持不变。
作为优选,所述蒸汽管内壁设置缝隙,所述稳流装置的外端设置在缝隙内。
作为优选,蒸汽管为多段结构焊接而成,多段结构的连接处设置稳流装置。
通过分析以及实验得知,稳流装置之间的间距不能过大,过大的话导致减震降噪以及分隔的效果不好,同时也不能过小,过小的话导致阻力过大,同理,正方形的边长也不能过大或者过小,也会导致减震降噪的效果不好或者阻力过大,因此本发明通过大量的实验,在优先满足正常的流动阻力(总承压为2.5mpa以下,或者单根蒸汽管的沿程阻力小于等于5pa/m)的情况下,使得减震降噪达到最优化,整理了各个参数最佳的关系。
作为优选,相邻稳流装置之间的距离为m1,正方形通孔的边长为b1,上升管为正方形截面,上升管正方形截面的边长为b2,满足如下要求:
m1/b2=a*ln(b1/b2)+b
其中a,b是参数,其中1.725<a<1.733,4.99<b<5.01;
11<b2<46mm;
1.9<b1<3.2mm;
18<m1<27mm。
进一步优选,随着b1/b2的增加,a越来越小,b越来越大。
作为优选,a=1.728,b=4.997;
作为优选,正方形通孔的边长b1是正方形通孔内边长和外边长的平均值,上升管正方形截面的边长b2是上升管内边长和外边长的平均值。
作为优选,正方形通孔的外边长等于上升管正方形截面的内边长。
作为优选,随着b2的增加,b1也不断增加。但是随着b2的增加,b1不断增加的幅度越来越小。此规律变化是通过大量的数值模拟和实验得到的,通过上述规律的变化,能够进一步提高换热效果,降低噪音。
作为优选,随着b2的增加,m1不断减小。但是随着b2的增加,m1不断减小的幅度越来越小。此规律变化是通过大量的数值模拟和实验得到的,通过上述规律的变化,能够进一步提高换热效果,降低噪音。
通过分析以及实验得知,上升管的间距也要满足一定要求,例如不能过大或者过小,无论过大或者过小都会导致换热效果不好,而且因为本申请上升管内设置了稳流装置,因此稳流装置也对上升管间距有一定要求。因此本发明通过大量的实验,在优先满足正常的流动阻力(总承压为2.5mpa以下,或者单根上升管的沿程阻力小于等于5pa/m)的情况下,使得减震降噪达到最优化,整理了各个参数最佳的关系。
相邻稳流装置之间的距离为m1,正方形的边长为b1,上升管为正方形截面,上升管的边长为b2,相邻上升管中心之间的间距为m2满足如下要求:
m2/b2=d*(m1/b2)2+e+f*(m1/b2)3-h*(m1/b2);
其中d,e,f,h是参数,
1.239<d<1.240,1.544<e<1.545,0.37<f<0.38,0.991<h<0.992;
11<b2<46mm;
1.9<b1<3.2mm;
18<m1<27mm。
16<m2<76mm。
相邻上升管中心之间的间距为m2是指上升管中心线之间的距离。
进一步优选,d=1.2393,e=1.5445,f=0.3722,h=0.9912;
作为优选,随着m1/b2的增加,d,e,f越来越大,h越来越小。
作为优选,随着b2的增加,m2不断增加,但是随着b2的增加,m2不断增加的幅度越来越小。此规律变化是通过大量的数值模拟和实验得到的,通过上述规律的变化,能够进一步提高换热效果。
作为优选,蒸汽管长度l为2000-2500mm之间。进一步优选,2200-2300mm之间。
通过上述公式的最佳的几何尺度的优选,能够实现满足正常的流动阻力条件下,减震降噪达到最佳效果。
对于其他的参数,例如管壁、壳体壁厚等参数按照正常的标准设置即可。
作为优选,所述蒸汽管的管径大于回流管的管径。主要是增加回流管的阻力,降低蒸汽管的阻力,使得蒸汽从蒸发部流动更容易,环路蒸汽管更好的形成循环。
虽然本发明已以较佳实施例披露如上,但本发明并非限定于此。任何本领域技术人员,在不脱离本发明的精神和范围内,均可作各种更动与修改,因此本发明的保护范围应当以权利要求所限定的范围为准。
起点商标作为专业知识产权交易平台,可以帮助大家解决很多问题,如果大家想要了解更多知产交易信息请点击 【在线咨询】或添加微信 【19522093243】与客服一对一沟通,为大家解决相关问题。
此文章来源于网络,如有侵权,请联系删除


