改进的膜片高压成型模具的制作方法



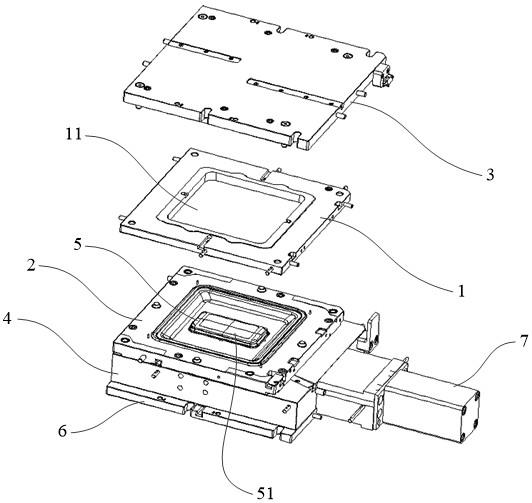
[0001]
本实用新型涉及一种膜片成型模具,更具体的说,本实用新型主要涉及一种改进的膜片高压成型模具。
背景技术:
[0002]
在iml、imd、imt、imf等行业中,目前所使用的高压成型模具大多采用机台模座发热管加热再传导至模具;膜片通过外陶瓷发热砖或ir灯辐射烤盘加热,或者采用模内陶瓷发热砖或ir灯辐射加热,通过前述方式瞬间对膜片加热至200℃-300℃;合模后由上模吹入高压空气作用于膜片表面使膜片依附于下模,从而以下模型状为型进行拉伸付型,最终得到具备一定形状的膜片制品。但前述方式只能做简单部件的成型且成型应力无法释放,更是难以实现反包、高拉伸及同一产品存在多种几何形状的情况成型。模板及烤盘辐射大至使车间运行能耗高;产品成型残留应力太大、拉伸不均、翘曲变形、困气造成突包、r角龟裂、橘皮现象等已成为现有传统高压成型的瓶颈。因而有必要针对此类模具的结构做进一步的研究和改进。
技术实现要素:
[0003]
本实用新型的目的之一在于针对上述不足,提供一种改进的膜片高压成型模具,以期望解决现有技术中同类模具在膜片成型出现残留应力,拉伸不均,翘曲变形、困气造成突包等技术问题。
[0004]
为解决上述的技术问题,本实用新型采用以下技术方案:
[0005]
本实用新型所提供的一种改进的膜片高压成型模具,所述成型模具包括压板与下模板,所述压板置于下模板的上部,且所述下模板具有成型腔,所述压板具有与所述成型腔对应的通槽;所述压板的上部还设有面板,用于由压板的上部、下部分别与面板、下模板紧密接触形成密闭空间;所述面板上还设有高压气孔;所述下模板的下部还设有下模垫板,所述下模垫板与下模板均设有相互对应的座槽,所述座槽内安装有模芯,所述模芯的上部具有平置的模芯排气面,所述模芯排气面上设有多个排气孔;所述下模垫板的一侧设有液压缸动力系统,用于使模芯上下运动。
[0006]
作为优选,进一步的技术方案是:所述下模板与下模垫板上的座槽均置于中部,且所述下模板的座槽四周形成型腔。
[0007]
更进一步的技术方案是:所述面板、压板与下模板通过机台锁模力压合固定为一体。
[0008]
更进一步的技术方案是:所述模芯的模芯排气面的高度,高于所述成型腔的最底部。
[0009]
更进一步的技术方案是:所述下模垫板置于底板上。
[0010]
更进一步的技术方案是:所述面板、压板、下模板、下模垫板、底板与模芯中的任意一个或多个内置加热器件,加热器件的电极接入电源。
[0011]
与现有技术相比,本实用新型的有益效果之一是:通过将模具的成型部分设计为面板、压板、下模板、模芯以及及模芯排气面件组合的结构形式,使得膜片在成型过程中,模具中的各个成型部分位置可调,可使产品几何形状在不同的模芯动作下进行拆解,从而完成产品几何拆解成型,并且模芯上的平置模芯排气面也便于排气,避免出现困气现象;通过模具中的各个器件自发热,使得模具可通过局部加热使温度精确可控,改善同类模具在加热烤盘撤走后膜片温度急速下降的问题,并且模具自发热的方式也更利于膜片付型,在付型完成后通过高压空气持续给压定型,配合模具本身的温度完成应力释放,同时本实用新型所提供的一种改进的膜片高压成型模具结构简单,采用不同类型的成型结构可加工各类规格的膜片材,应用范围广阔。
附图说明
[0012]
图1为用于说明本实用新型一个实施例的结构示意图;
[0013]
图中,1为压板、11为通槽、2为下模板、3为面板、4为下模垫板、5为模芯、51为模芯排气面、6为底板、7为液压缸动力系统。
具体实施方式
[0014]
下面结合附图对本实用新型作进一步阐述。
[0015]
参考图1所示,本实用新型的一个实施例是一种改进的膜片高压成型模具,该成型模具包括压板1与下模板2,压板1置于下模板2的上部,且下模板2具有成型腔,通过该成性腔可对膜片进行付型,而压板1可将膜片的边缘压住,压板1具有与成型腔对应的通槽11,以避免影响膜片成型;更为重要的是,在前述压板1的上部还设有一块面板3,用于由压板1的上部、下部分别与面板3、下模板2紧密接触形成密闭空间,使膜片可在该密闭空间中进行成型及定型;因此前述面板3上还需设置高压气孔,该高压气孔可与外部的高压气源相连通;同时为便于前述的下模板2安装,还可在下模板2的下部还设计一个下模垫板4,该下模垫板4与下模板2上均设有相互对应的座槽,然后在座槽内安装有模芯5,为便于高压排气,可在模芯5的上部设计平置的模芯排气面51,在模芯排气面51上需要设置多个排气孔,膜片成型过程中膜片下部的残留气体可由排气孔排出,使膜片可继续处于该密闭腔中进行定型;优选的是,前述模芯5的模芯排气面51的高度,高于成型腔的最底部,以避免前述模芯排气面51影响膜片成型,亦避免模芯排气面51影响密闭空间中气压对膜片所施加的力,正如图1所示出的,前述下模垫板4的一侧还有液压缸动力系统7,该液压缸动力系统7用于带动模芯5上下运动
[0016]
作为本实用新型的另一大改进,为进一步降低付型完成后膜片的内应力,即需避免膜片升温后急速降温,因此可根据不同的情况,在面板3、压板1、下模板2、下模垫板4、底板6与模芯5中的任意一个或多个内置加热器件,并且加热器件均接入电源,可由控制模块控制各个加热器件的启停以及运行的功率。
[0017]
在本实施例中,通过将模具的成型部分设计为面板3、压板1、下模板2及模芯5及模芯排气面51组合的结构形式,使得膜片在成型过程中,模具中的各个成型部分位置可调,可使产品几何形状在不同的模芯动作下进行拆解,从而完成产品几何拆解成型,并且模芯上的平置模芯排气面也便于排气,避免出现困气现象;通过模具中的各个器件自发热,使得模
具可通过局部加热使温度精确可控,改善同类模具在加热烤盘撤走后膜片温度急速下降的问题,并且模具自发热的方式也更利于膜片付型,在付型完成后通过高压空气持续给压定型,配合模具本身的温度完成应力释放。
[0018]
基于上述的实施例,发明人还对上述膜片高压成型模具的结构进行了优化,具体为将下模板2与下模垫板4上的座槽均设计在中部,并使下模板2的座槽四周形成上述的型腔,从而进一步提升膜片成型的精度。同时为便于拆卸,亦可再将上述面板3、压板1与下模板2通过机台锁模力压合固定为一体,使三者通过机台锁模力压合形成密闭的空间。
[0019]
参考图1所示,本实用新型上述优选的一个实施例在实际使用中,打开模具,将待成型的膜片放置在下模板2上,然后用压板1压在膜片的边缘,再放上面板3并锁紧,形成密闭空间;同时利用模具中的加热器件对膜片进行加热,当膜片温度到达一定的温度后,由面板3上的高压气孔通入高压空气,在密闭的空间中形成气压,使得膜片在气压作用下被压入下模板2的成型腔中成型,成型完毕后持续给压定型,亦可通过模芯5上的模芯排气面51排除膜片下部的残留气体,此时由于模芯排气面51的高度高于成型腔的最底部,因此排气不会对付型完成后的膜片造成影响。通过模具本身的温度使付型后的膜片完成应力释放。
[0020]
即在本实用新型中,改变传统加热方式中烤盘撤走后片材温度急速下降的问题,模具采用自身局部加热,精确部位温度可控;在成型过程中利用模具本身热能使膜片更利于付型,付型完成持续给压定型;在付型及定型过程中由于利用模具本身温度同时也是一个应力释放过程。成型主体部分模芯活动在成型过程中做到位置可调:利用专用设计的动力系统使模具模芯按预设位置运动,使产品几何形状在不同的模芯动作下进行拆解,完成产品几何拆解成型。同时将3d打印排气镶件、排气钢等技术引入高压成型模具领域,解决高压排气困难,局部细微结构难于成型或尺寸形状与模型差异的问题。
[0021]
除上述以外,还需要说明的是在本说明书中所谈到的“一个实施例”、“另一个实施例”、“实施例”等,指的是结合该实施例描述的具体特征、结构或者特点包括在本申请概括性描述的至少一个实施例中。在说明书中多个地方出现同种表述不是一定指的是同一个实施例。进一步来说,结合任一实施例描述一个具体特征、结构或者特点时,所要主张的是结合其他实施例来实现这种特征、结构或者特点也落在本实用新型的范围内。
[0022]
尽管这里参照本实用新型的多个解释性实施例对本实用新型进行了描述,但是,应该理解,本领域技术人员可以设计出很多其他的修改和实施方式,这些修改和实施方式将落在本申请公开的原则范围和精神之内。更具体地说,在本申请公开、附图和权利要求的范围内,可以对主题组合布局的组成部件或布局进行多种变型和改进。除了对组成部件或布局进行的变型和改进外,对于本领域技术人员来说,其他的用途也将是明显的。
起点商标作为专业知识产权交易平台,可以帮助大家解决很多问题,如果大家想要了解更多知产交易信息请点击 【在线咨询】或添加微信 【19522093243】与客服一对一沟通,为大家解决相关问题。
此文章来源于网络,如有侵权,请联系删除
相关标签: 压板



tips