一种机舱棚总段建造方法与流程



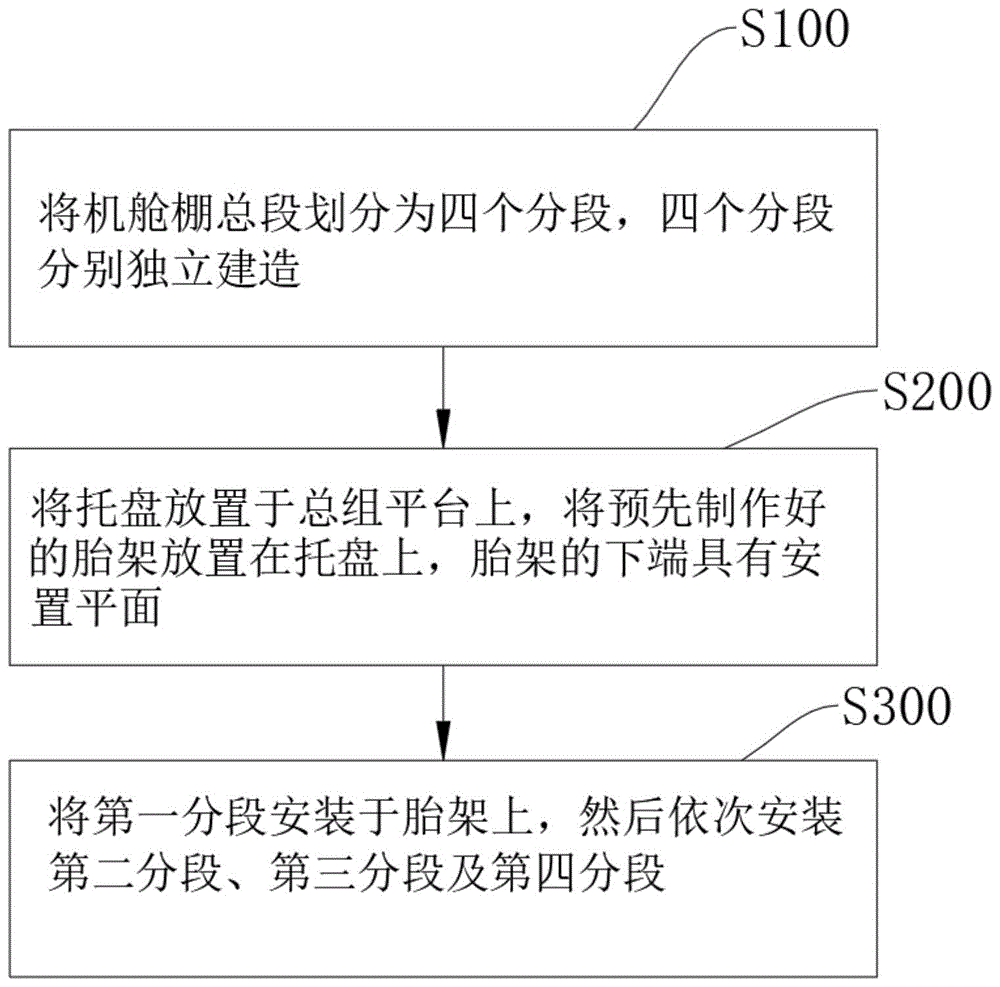
本发明涉及船舶建造技术领域,尤其涉及一种机舱棚总段建造方法。
背景技术:
机舱棚位于机舱口上方,机舱口四周有围蔽直通至露天甲板,其上设置有机舱顶盖。机舱棚的作用是给机舱采光和自然通风。机舱棚顶应高出露天甲板以防风暴天气是波浪海水的侵入。
对于大型机舱棚总段和超大型机舱棚总段的体积较大,按照传统的舾装方式将机舱棚的各个零部件装配于船舶的其他构件,不利于保证舾装的完整性。
技术实现要素:
本发明要解决的技术问题是为了克服现有技术中的上述缺陷,提供一种机舱棚总段建造方法。
本发明是通过下述技术方案来解决上述技术问题的:
一种机舱棚总段建造方法,包括如下步骤:
s100、将机舱棚总段划分为四个分段,四个分段分别独立建造,四个分段从下到上依次为第一分段、第二分段、第三分段及第四分段;
s200、将托盘放置于总组平台上,将预先制作好的胎架放置在托盘上,胎架的下端具有安置面,安置面贴合在托盘上;
s300、将第一分段安装于胎架上,然后依次安装第二分段、第三分段及第四分段。
优选地,步骤s300具体包括如下步骤:
s31、将第一分段正态吊装至胎架上,第一分段的下口抵接于胎架上;
s32、校准第一分段,然后固定第一分段和胎架,并固定胎架和托盘。
优选地,步骤s32具体包括如下步骤:
s321、控制第一分段的分段中心线与总组平台上预设的船体中心线对齐;
s322、控制第一分段的水平度满足精度要求;
s323、校核第一分段的分段中心线与总组平台的船体中心线是否对齐,若是则执行步骤s324,否则返回步骤s322;
s324、焊接第一分段和胎架,焊接胎架和托盘。
优选地,步骤s300还包括位于步骤s32之后的如下步骤:
s33、将第二分段正态吊装至第一分段上;
s34、校准第二分段,然后固定第二分段和第一分段。
优选地,步骤s34具体包括如下步骤:
s341、控制第二分段的分段中心线与第一分段的分段中心线对齐;
s342、控制第二分段的水平度和高度满足精度要求;
s343、焊接第一分段和第二分段。
优选地,步骤s300还包括位于步骤s34之后的如下步骤:
s35、将第三分段正态吊装至第二分段上;
s36、校准第三分段,然后固定第三分段和第二分段。
优选地,步骤s36具体包括如下步骤:
s361、控制第三分段的分段中心线与第二分段的分段中心线对齐;
s362、控制第三分段的水平度和高度满足精度要求;
s363、焊接第二分段和第三分段。
优选地,步骤s300还包括位于步骤s36之后的如下步骤:
s37、将第四分段正态吊装至第三分段上;
s38、校准第四分段,然后固定第四分段和第三分段。
优选地,步骤s38具体包括如下步骤:
s381、控制第四分段的分段中心线与第三分段的分段中心线对齐;
s382、控制第四分段的水平度满足精度要求;
s383、控制第四分段的高度满足精度要求;
s384、焊接第三分段和第四分段。
优选地,机舱棚总段建造方法还包括位于步骤s300之后的如下步骤:
s400、将机舱棚总段放置于驳船上;
步骤s400具体通过如下步骤实现:
s40、在总组平台以外的区域布置左舷动力头、左运输模块、右舷动力头及右运输模块,其中,左舷动力为左运输模块提供行走的动力,右舷动力头为右运输模块提供行走的动力;在左运输模块和右运输模块上铺设垫木;
s41、控制左运输模块和右运输模块位于托盘下方,控制左舷动力头和右舷动力头伸出机舱棚总段;
s42、在左舷动力头和托盘之间铺设垫木,在右舷动力头和托盘之间铺设垫木;
s43、控制左运输模块和右运输模块将机舱棚总段移动至码头;
s44、割除胎架和托盘之间的连接,保持胎架与第一分段的连接;
s45、将机舱棚总段和胎架一通调运至驳船。
在符合本领域常识的基础上,上述各优选条件,可任意组合,即得本发明各较佳实例。
本发明的积极进步效果在于:
本发明中,通过将机舱棚总段划分成四个分段,将四个分段独立建造后装配在一起,降低了机舱棚总段的建造难度,提高了可操作性,对大型和超大型机舱棚建造具有更好的效果。
附图说明
图1为本发明一实施例的机舱棚总段建造方法流程图;
图2为本发明一实施例的机舱棚总段的分段划分示意图;
图3为本发明一实施例的托盘放置于总组平台的示意图;
图4为本发明一实施例的胎架的结构示意图;
图5为本发明一实施例的机舱棚总段的示意图;
图6为本发明一实施例的运输模块的布置图;
图7为图6的截面视图。
附图标记说明:
第一分段1
第二分段2
第三分段3
第四分段4
机舱棚总段5
托盘6
胎架7
安置面71
船体中心线8
第一分段的分段中心线9
左舷动力头11
右舷动力头12
左运输模块13
右运输模块14
坞墩15
垫木16
具体实施方式
下面通过实施例的方式进一步说明本发明,但并不因此将本发明限制在下述的实施例范围之中。
请参阅图1-4进行理解。本发明实施例提供一种机舱棚总段建造方法,预先将机舱棚总段5装配成一个整体,然后将机舱棚总段5整体装配在船舶的其他构件上。
本实施例的机舱棚总段建造方法包括如下步骤:
s100、将机舱棚总段5划分为四个分段,四个分段分别独立建造,四个分段从下到上依次为第一分段1、第二分段2、第三分段3及第四分段4。
其中,机舱棚总段5可以理解为能够在船舶上正常运转的完整的机舱棚成品,也可以理解为具有机舱棚成品绝大多数零(部)件的机舱棚半成品,例如机舱棚总段5不包含用于连接两个或两个以上的分段的构件。
四个分段可结合机舱棚总段5的重量、体积以及施工因素进行划分。各分段的制造过程相对独立。图2示意了四个分段在机舱棚总段5中对应的位置,诚然,在其他的实施例中,四个分段可具有不同于此的划分方式。
各分段相对于机舱棚总段5在体积和质量上均小很多,相应地,各分段相对于机舱棚总段5的施工难度和复杂程度均降低许多,各分段的可操作性提高,且便于控制精度。
s200、将托盘6放置于总组平台上,将预先制作好的胎架7放置在托盘6上,胎架7的下端具有安置面71,胎架7的安装面贴合在托架上。
其中,总组平台为装配机舱棚总段5提供场地,可在总组平台上设置若干用于承载作用力的支撑件,各支撑件间隔设置,胎架7搭置在支撑件上。进一步来说,支撑件可采用坞墩15。
托盘6用作承重件。托盘6以框架的形式体现,可采用若干型钢交叉设置并焊接而成。图3中示意了托盘6放置于总组平台的俯视状态,其中,为直观体现托盘6而隐去了支撑件。
胎架7可在步骤s100中制作完成。胎架7可按照第一分段1的下口的形状制作。胎架7的下端具有安置面71,安置面71贴合在托盘6上,从而第一分段1的下口通过胎架7的安置面71与托盘6面接触,提高了第一分段1的稳定性,降低了装配过程中第一分段1下口的变形。胎架7可以框架的形式体现,可用若干槽钢和/或工字钢焊接而成。图4示意了一种胎架7结构,诚然,在其他的实施例中,根据第一分段1的下口的形状的不同,胎架7可具有不同于图4的形状。
s300、将第一分段1安装于胎架7上,然后依次安装第二分段2、第三分段3及第四分段4。
其中,先将第一分段1放置并定位于胎架7上,其次,将第二分段2放置并定位于第一分段1上,再次,将第三分段3放置并定位于第二分段2上,最后,将第四分段4放置并定位于第三分段3上,形成机舱棚总段5。
另外,实施例中,四个分段可采用点焊的方式装配在一起,在步骤s300之后,再进一步对四个分段的连接位置进行连续焊接以达到对机舱棚成品的安装要求。
从上述可知,本实施例通过将机舱棚总段5划分成四个分段,将四个分段独立建造后装配在一起,降低了机舱棚总段5的建造难度,提高了可操作性,对大型和超大型机舱棚建造具有更好的效果。
本发明实施例中,步骤s300具体包括如下步骤:
s31、将第一分段1正态吊装至胎架7上,第一分段1的下口完全位于胎架7上。其中,正态相对于倒置、侧放等状态而言,其为第一分段1在成品船舶上正常运转时所呈现的状态。第一分段1作为一个整体吊装到胎架7上,框架形式的胎架7限定了第一分段1的下口可放置的空间,从而在放置第一分段1的时候便能够较为准确地确定第一分段1的位置,提高了机舱棚总段5的装配效率。
s32、校准第一分段1,然后固定第一分段1和胎架7,并固定胎架7和托盘6。其中,校准操作可包括控制第一分段1的水平度和高度在装配精度要求的范围之内,还可包括控制第一分段1与胎架7的相对位置关系在预先设定的精度要求的范围之内。第一分段1和胎架7可焊接固定,具体可点焊固定。胎架7和托盘6也可采用点焊固定。固定第一分段1和胎架7能够防止装配过程中第一分段1出现晃动、位移或其他不稳定的情况,还能够使得第一分段1的受力分散到胎架7上,并通过胎架7的安置面71传递到托盘6上,从而降低了第一分段1的下口的应力集中,减缓了第一分段1的下口的变形量。固定胎架7和托盘6提高了胎架7和第一分段1的稳定性,相应地,也提高了装配过程中第一分段1的稳定性,从而有利于保证机舱棚的装配精度。
本实施例在校准第一分段1后将第一分段1和胎架7固定,并将胎架7和托盘6固定,有效提高了装配过程中第一分段1的稳定性,降低了第一分段1的变形量,保证了机舱棚的装配精度。另外,本实施例在通过在总组平台上设置船体中心线8,用作机舱棚总段5装配过程中的定位基准线,能够有效提高装配效率,并有利于保证装配精度。
请参阅图3和图5进行理解。本发明实施例中,步骤s32具体包括如下步骤:
s321、控制第一分段的分段中心线9与总组平台上预设的船体中心线8对齐。其中,船体中心线8预先在总组平台上划好,船体中心线8可以作为机舱棚总段5装配过程中的定位基准线。图3中以单点划线的形式体现了总组平台的船体中心线8。
各个分段的建造过程中均划有各自的分段中心线。校准第一分段1的过程中,控制第一分段的分段中心线9与船体中心线8对齐。图5以单点划线的形式体现了第一分段的分段中心线9。
需要说明的是,船体中心线8和分段中心线可以是基于船舶的全船基准线施工规范进行设定和施工,因此不仅在建造机舱棚总段5过程中被用到,还在将机舱棚总段5装配于船舶的其他构件的过程中被用到。在其他实施例中,船体中心线8和分段中心线也可以进作为机舱棚总段5建造的基准,而不作为机舱棚总段5装配于其他船舶其他构件的过程中的基准使用。
另外,可在托盘6和胎架7上设置与船体中心线8相对应的参照线,步骤s200中放置托盘6和胎架7时可将参照线与船体中心线8对齐,从而可提高定位第一分段1和校准第一分段1的效率。
s322、控制第一分段1的水平度满足精度要求。具体来说,通过调整第一分段1的四个角水平进行调整水平度,水平度的范围在-4mm到+4mm之间。
s323、校核第一分段的分段中心线9与总组平台的船体中心线8是否对齐,若是则执行步骤s324,否则返回步骤s322。复核第一分段的分段中心线9和船体中心线8,并根据复核结果执行相应的操作,保证第一分段1的定位准确无误,从而提高机舱棚总段5的装配精度。
步骤s323中还可复核第一分段1的轮廓,判断第一分段1的下口是否都完全落在了胎架7上,如果复核结果为否,则返回步骤s31中,否则执行步骤s324。
s324、焊接第一分段1和胎架7,焊接胎架7和托盘6。
本实施例中,通过控制第一分段的分段中心线9与船体中心线8对齐和控制第一分段1的水平度满足精度要求,实现对第一分段1的准确定位,从而提高机舱棚总段5的装配精度。
本发明实施例中,步骤s300还包括位于步骤s32之后的如下步骤:
s33、将第二分段2正态吊装至第一分段1上。其中,建造过程中可将第二分段2以倒置的状态进行建造,本步骤中则将第二分段2翻身至正态,然后将其吊装到第一分段1的上端,使第二分段2坐在第一分段1上。
s34、校准第二分段2,然后固定第二分段2和第一分段1。其中,校准操作可包括控制第二分段2的水平度和高度在装配精度要求的范围之内,还可包括控制第二分段2与第一分段1的相对位置关系在预先设定的精度要求的范围之内。第二分段2和第一分段1可焊接固定,具体可采用点焊固定。固定第二分段2和第一分段1能够防止装配过程中这两个分段出现晃动、位移或其他不稳定的情况,还能够使得第二分段2的受力较好地分散到第一分段1上。
本实施例在校准第二分段2后将其与第一分段1固定,有效提高了第二分段2和第一分段1的稳定性。
本发明实施例中,步骤s34具体包括如下步骤:
s341、控制第二分段2的分段中心线与第一分段的分段中心线9对齐。其中,
s342、控制第二分段2的水平度和高度满足精度要求,还可进一步控制第一分段1的外围壁和第二分段2的外围壁相对应位置的平面度满足精度要求。其中,通过控制第二分段2的四个角水平使第二分段2的水平度在-4mm到+4mm之间。本步骤中,调控水平度、高度以及平面度的操作的先后顺序可以任意调整。
s343、焊接第一分段1和第二分段2。本步骤中,第一分段1和第二分段2可以采用点焊。
本实施例通过控制第二分段2的分段中心线和第一分段的分段中心线9对齐,和控制第二分段2的水平度、高度以及外围壁满足精度要求,实现对第二分段2的准确定位,从而提高机舱棚总段5的装配精度。
本发明实施例中,步骤s300还包括位于步骤s34之后的如下步骤:
s35、将第三分段3正态吊装至第二分段2上,使第三分段3坐在第二分段2的上端。
s36、校准第三分段3,然后固定第三分段3和第二分段2。其中,校准操作可包括控制第三分段3的水平度和高度在装配精度要求的范围之内,还可包括控制第三分段3与第二分段2的相对位置关系在预先设定的精度要求的范围之内。第三分段3和第二分段2可焊接固定,具体可点焊固定。固定第三分段3和第二分段2能够防止装配第四分段4的过程中第三分段3出现晃动、位移或其他不稳定的情况,还能够使得第三分段3的受力较好地分散到第二分段2和第一分段1上。
本发明实施例中,步骤s36具体包括如下步骤:
s361、控制第三分段3的分段中心线与第二分段2的分段中心线对齐。
s362、控制第三分段3的水平度和高度满足精度要求;其中,对调控水平度和高度的操作不分先后顺序。
s363、在第二分段2和第三分段3的外围壁上将两者点焊在一起。
本发明实施例中,步骤s300还包括位于步骤s36之后的如下步骤:
s37、将第四分段4正态吊装至第三分段3上,
s38、校准第四分段4,然后固定第四分段4和第三分段3。
本发明实施例中,步骤s38具体包括如下步骤:
s381、控制第四分段4的分段中心线与第三分段3的分段中心线对齐;
s382、控制第四分段4的水平度和高度满足精度要求。其中,通过调节第四分段4的四个角实现对水平度的控制。另外,调控水平度的操作和调控高度的操作的顺序不限定。
s383、通过点焊的方式将第三分段3和第四分段4焊接在一起。
本发明实施例中,机舱棚总段建造方法还包括位于步骤s300之后步骤s400:将机舱棚总段5放置于驳船,驳船将机舱棚总段5运送至船舶建造的其他装配平台。
步骤s400具体包括如下步骤:
s40、在总组平台以外的区域布置左舷动力头11、左运输模块13、右舷动力头12及右运输模块14,其中,左运输模块13和右运输模块14均为可行走的部件。连接左舷动力头11和左运输模块13,左舷动力头11为左运输模块13提供行走的动力,连接右舷动力头12和右运输模块14,右舷动力头12为右运输模块14提供行走的动力。在左运输模块13和右运输模块14上铺设垫木16,以将两个运输模块和托盘6隔开,减少机械损伤。
s41、控制左运输模块13和右运输模块14位于托盘6下方,控制左舷动力头11和右舷动力头12伸出机舱棚总段5。其中,左舷动力头11驱动左运输模块13运动至托盘6的下方,右舷动力头12驱动右运输模块14运动至托盘6的下方。托盘6上可设置加强结构,左运输模块13和右运输模块14可均位于托盘6的加强结构的下方,以提升运输效果。图6以俯视的角度示意了本步骤中两个运输模块和两个动力头相对于托盘6和胎架7的位置关系。图7以剖视图和局部放大的形式体现了坞墩15、托盘6、两个运输模块的位置关系。
s42、在左舷动力头11和托盘6之间铺设垫木,在右舷动力头12和托盘6之间铺设垫木,以将托盘6和两个动力头隔开,减少机械损伤。
s43、控制左运输模块13和右运输模块14将机舱棚总段5移动至码头。其中,左舷动力头11和右舷动力头12顶升起托盘6,左舷动力头11和右舷动力头12同步运动,驱动两个动力模块同步运行。另外,运输过程中,可在运输路径上铺设钢板,做运输模块和右运输模块14行走在钢板上,从而提高了运输的平稳性。
s44、割除胎架7和托盘6之间的连接,保持胎架7与第一分段1的连接,以便于在后续的操作中机舱棚总段5能够通过胎架7的安置面71放置在地面或其他的平台上,从而减缓机舱棚总段5的下口(即第一分段1的下口)的变形。
s45、将机舱棚总段5和胎架7一通调运至驳船,安置面71贴合在驳船上。
虽然以上描述了本发明的具体实施方式,但是本领域的技术人员应当理解,这仅是举例说明,本发明的保护范围是由所附权利要求书限定的。本领域的技术人员在不背离本发明的原理和实质的前提下,可以对这些实施方式做出多种变更或修改,但这些变更和修改均落入本发明的保护范围内。
起点商标作为专业知识产权交易平台,可以帮助大家解决很多问题,如果大家想要了解更多知产交易信息请点击 【在线咨询】或添加微信 【19522093243】与客服一对一沟通,为大家解决相关问题。
此文章来源于网络,如有侵权,请联系删除


