车身构造的制作方法



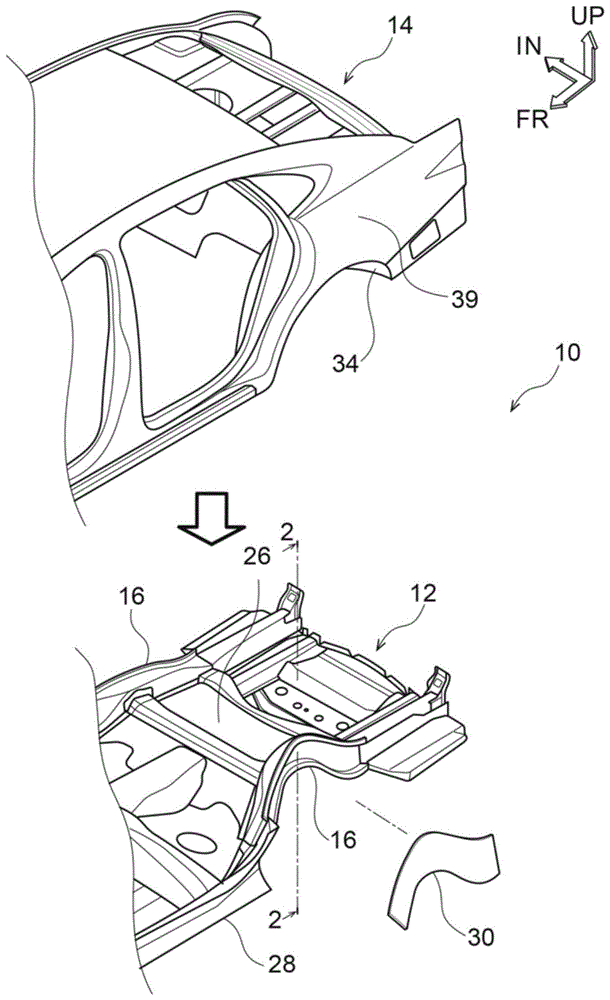
本发明涉及一种车身构造。
背景技术:
在日本专利5606539中,公开了具有单体壳构造的车辆的后部车身构造。若简单地进行说明,则后部车身构造具备:轮罩,配置于车辆宽度方向侧方;以及纵梁,配置于轮罩的车辆宽度方向内侧,在车辆前后方向延伸。此外,从车辆轻量化的观点,纵梁被设为铝压铸件制。
另外,在轮罩为铁制的情况下,难以通过焊接来将铝制的纵梁与铁制的轮罩接合,因此考虑使用铆钉机械性地进行接合。但是,在将组装于上部车身的轮罩与组装于下部车身的纵梁直接地接合的情况下,需要大型的接合机。因此,可以想到:必须以不与接合机干扰的方式来设计车身,会产生外观设计的制约。
技术实现要素:
本发明是考虑上述事实而完成的,其目的在于得到一种在将铝制的纵梁与铁制的轮罩接合的构成中能提高外观设计的自由度的车身构造。
根据方案1所述的本发明的车身构造,具备:铝制的纵梁,配置于车身的前部和后部中的至少一方的车辆宽度方向外侧,并在车辆前后方向延伸;铁制的轮罩,配置于比所述纵梁靠车辆宽度方向外侧的位置,该轮罩的内侧供车轮配置,并且在车辆宽度方向内侧部具有沿车辆上下方向延伸设置的纵壁部;以及铁制的接合构件,在车辆宽度方向配置于所述纵梁与所述轮罩之间,并被配置为包括:第一接合部,与所述纵梁接合;以及第二接合部,配置于从车辆宽度方向观察时不与该第一接合部和所述纵梁重叠的位置,并与所述轮罩的所述纵壁部接合。
在方案1所述的本发明的车身构造中,铝制的纵梁与铁制的轮罩经由夹置于两者之间的铁制的接合构件进行接合。在此,纵梁与接合构件通过第一接合部进行接合,轮罩与接合构件通过第二接合部进行接合。此外,第二接合部配置于从车辆宽度方向观察时不与第一接合部和纵梁重叠的位置。因此,例如,能通过以下工序来制造车身,即在形成下部车身时预先使用铆钉等将彼此为异种金属的接合构件与纵梁机械性地接合,然后使接合构件与上部车身侧的轮罩接合。而且,在该工序中,接合构件和轮罩均为铁制,因此能通过点焊等冶金接合方法来接合。其结果是,在使上部车身接合于车身的下部车身的工序中,不需要大型的接合机,为了避免接合机与零件的干扰而对车身带来的外观设计的制约减少。
对于方案2所述的本发明的车身构造而言,在方案1所述的构成中,所述纵梁形成为向车辆宽度方向外侧开口的截面帽形形状,所述接合构件配置为从车辆宽度方向外侧覆盖所述纵梁,并被设为与所述纵梁一起沿车辆前后方向形成闭合截面的板状的加强件。
在方案2所述的本发明的车身构造中,加强件从车辆宽度方向外侧覆盖截面帽形形状的纵梁的开口部,因此沿车辆前后方向形成闭合截面。由此,对纵梁进行加强。而且,能通过根据需要变更加强件的板厚、材质来提高纵梁的强度和刚性。
此外,与使轮罩的纵壁部向车辆下方侧延伸出而与纵梁直接接合的构成不同,上述构成中接合于纵梁的加强件和轮罩被设为分体。因此,相对于前者为了提高纵梁的强度以及刚性而需要变更轮罩整体的板厚、材质,本发明能仅通过变更加强件来提高纵梁的强度和刚性。由此,抑制车身的重量增加。
对于方案3所述的本发明的车身构造而言,在方案1或方案2所述的构成中,所述接合构件具备:延伸设置部,比所述纵梁的上端部向车辆上方侧延伸设置;以及覆盖部,从该延伸设置部向车辆下方侧延伸设置并从车辆宽度方向外侧覆盖所述纵梁,所述第一接合部形成于所述覆盖部,所述第二接合部形成于所述延伸设置部。
在方案3所述的本发明的车身构造中,使轮罩与接合构件接合的第二接合部在接合构件中利用比纵梁的上端部向车辆上方侧延伸设置的延伸设置部来形成。这样一来,在第一接合部的车辆上方侧形成第二接合部,第二接合部形成于从车辆宽度方向观察时不与第一接合部和纵梁重叠的位置。因此,易于在接合构件组装于下部车身后确保接合构件与轮罩的重叠余量,接合点的定位变得容易。其结果是,成为生产性优异的构造。
对于方案4所述的本发明的车身构造而言,在方案1或方案2所述的构成中,所述纵梁在该纵梁的上端部形成有多个凸片部,所述凸片部在车辆前后方向隔开规定的间隔地进行配置,并且向车辆上方侧突出,所述第一接合部至少将该凸片部与所述接合构件接合,所述第二接合部配置于相邻配置的一对该凸片部之间,将所述轮罩的所述纵壁部与所述接合构件接合。
在方案4所述的本发明的车身构造中,第一接合部沿形成于纵梁的上端部并向车辆上方侧突出的多个凸片部进行配置。此外,在相邻配置的一对凸片部之间,配置有将轮罩与接合构件接合的第二接合部。这样一来,第一接合部和第二接合部沿车辆前后方向进行配置,第二接合部配置于从车辆宽度方向观察时不与第一接合部和纵梁重叠的位置。由此,能抑制形成于接合构件间的接合点的车辆上下方向的分布。其结果是,能提高纵梁与轮罩间的载荷传递效率。
这是因为,在本发明中,纵梁与轮罩经由接合构件进行接合。因此,第一接合部的接合点和第二接合部的接合点的分布越在车辆上下方向扩大,纵梁与轮罩之间的载荷传递路径越长,使载荷传递效率降低。
因此,在本发明中,通过上述构成来抑制形成于接合构件的接合点的车辆上下方向的分布。由此,载荷传递路径变短,能提高纵梁与轮罩间的载荷传递效率。
如以上说明的那样,方案1的车身构造具有在将铝制的纵梁与铁制的轮罩接合的构成中能提高外观设计的自由度的优异效果。
方案2的车身构造具有能抑制车身的重量增加并且提高纵梁的强度和刚性的优异效果。
方案3的车身构造具有能提高车身的生产性的优异效果。
方案4的车身构造具有能提高纵梁与轮罩间的载荷传递效率的优异效果。
附图说明
以下,参照附图对本发明的示例性实施例的特征、优点以及技术和工业意义进行说明,其中,相同的附图标记表示相同的元件,其中:
图1是分解表示应用了第一实施方式的车身构造的车辆后部构造的分解立体图。
图2是沿图1的2-2线剖切的放大剖视图。
图3是用于说明图2所示的车身构造的接合工序的、对应于图2的剖视图。
图4的(a)是表示第二实施方式的车身构造的主要部分的立体图,图4的(b)是从车辆宽度方向观察图4的(a)所示的主要部分的侧视图。
图5是用于说明比较例的车身构造的接合工序的、对应于图3的剖视图。
具体实施方式
<第一实施方式>以下,基于图1~图3对第一实施方式的车身构造进行说明。需要说明的是,在各图中适当地表示的箭头fr表示车辆前方侧,箭头up表示车辆上方侧,箭头in表示车辆宽度方向内侧。此外,在以下的说明中没有特别说明地使用前后、上下、左右的方向的情况下,设为表示车辆前后方向的前后、车辆上下方向的上下、朝向行进方向的情况下的左右。
(整体构成)如图1所示,车身10的骨架被设为将底盘框架(chassisframe)和车身(body)一体地制造的所谓单体壳框架(monocoqueframe)。该单体壳框架在制造工序中被设为上下二分割构造,通过将构成车身的下部的下部车身(underbody)12与构成车身的上部的上部车身(upperbody)14接合而形成。
构成车身10的下部的骨架的下部车身12配置为包括在车辆前后方向的后部在车辆宽度方向分离并且分别在车辆前后方向延伸的左右一对后纵梁16。而且,下部车身12配置为包括配置于比后纵梁16靠车辆宽度方向外侧的位置并接合于该后纵梁16的纵梁加强件(以下,称为“纵梁r/f”。)30。另一方面,构成车身10的上部的骨架的上部车身14在车辆前后方向的后部具有车身10的容纳后轮(未图示)的一对轮罩34。以下,以这些构件为中心进行说明。需要说明的是,在以下的说明中,“铝制”不仅包括铝单体,还包括铝合金。此外,“铁制”不仅包括铁单体,还包括铁合金。
(后纵梁16)如图1和图2所示,作为纵梁的后纵梁16是分别配置于左右一对后轮(未图示)的车辆宽度方向内侧并在车辆前后方向延伸的骨架构件。该后纵梁16被设为铝制,更具体而言被设为铝压铸件制。后纵梁16形成为沿车辆宽度方向的截面形状呈大致帽形。
该帽形截面由向车辆宽度方向外侧开口的开放截面形状的开放截面部18、设于开放截面部18的上端部的上凸缘部20以及设于开放截面部18的下端部的下凸缘部22构成。开放截面部18具备在车辆上下方向延伸的内侧面18a、从内侧面18a的上端部向车辆宽度方向外侧延伸的上侧面18b以及从内侧面18a的下端部向车辆宽度方向外侧延伸的下侧面18c。
而且,在内侧面18a一体地形成有从车辆上下方向的中间部向车辆内侧延伸的内侧凸缘24。在该内侧凸缘24的上方侧配置有构成车身10的未图示的行李舱的底板面的中央地板面板26。中央地板面板26形成为俯视观察时呈大致矩形的板状,并配置于一对后纵梁16的内侧。并且,中央地板面板26的车辆宽度方向的右侧端部和左侧端部接合于内侧凸缘24。该接合部被设为机械接合构造,更具体而言,使用自刺穿铆钉(spr)32。
需要说明的是,一对后纵梁16的前端部在下部车身12的车辆前后方向的中央部分别连接于配置在车辆宽度方向的右侧部和左侧部的一对下边梁(rocker)28。
(纵梁加强件30)如图1和图2所示,作为接合构件的纵梁r/f30形成为以车辆前后方向为长尺寸方向且以车辆宽度方向作为板厚方向的板状,配置于上述的后纵梁16的车辆宽度方向外侧。纵梁r/f30被设为铁制,更具体而言,使用钢板。
纵梁r/f30在构造上具备延伸设置部30a和覆盖部30b。延伸设置部30a是比后纵梁16的上凸缘部20的上端部20a向车辆上方侧延伸设置并且接合于后述的轮罩34的部位。此外,覆盖部30b是从延伸设置部30a向车辆下方侧延伸设置并且从车辆宽度方向外侧覆盖后纵梁16的部位。
覆盖部30b通过第一接合部40接合于后纵梁16的上凸缘部20和下凸缘部22。第一接合部40被设为机械接合构造,更具体而言,使用自刺穿铆钉32。
通过上述接合构造,后纵梁16的开放截面部18的开口部被纵梁r/f30覆盖,由后纵梁16和纵梁r/f30形成矩形的闭合截面。这样一来,后纵梁16被纵梁r/f30加强。
(轮罩34)如图2所示,轮罩34是分隔车厢和后轮的构件,配置为包括配置于车宽度方向内侧的轮罩内侧件36和配置于车宽度方向外侧的轮罩外侧件38。此外,轮罩内侧件36和轮罩外侧件38被设为铁制,更具体而言,使用钢板。
轮罩内侧件36具备:周面部36a,沿车辆宽度方向的截面形成为倒l字形,沿未图示的后轮的周面进行配置;以及纵壁部36b,从周面部36a的车辆宽度方向内侧向车辆下方侧延伸。此外,在周面部36a的车辆宽度方向外端部设有沿后轮的径向朝外侧延伸设置的外周凸缘36c。在轮罩内侧件36的车辆上方侧一体地形成有未图示的悬架塔,该悬架塔从轮罩内侧件36的上端部朝向车辆上方侧立起设置。并且,悬架塔对配置于其内侧的未图示的减振器(absober)的上端部进行支承。
另一方面,轮罩外侧件38形成为与轮罩内侧件36大致左右对称,沿车辆宽度方向的截面被设为倒l字形。具体而言,轮罩外侧件38具备沿后轮的周面配置的周面部38a和从周面部38a的车辆宽度方向外侧向车辆下方侧延伸的纵壁部38b。此外,在周面部38a的车辆宽度方向内端部设有沿后轮的径向朝外侧延伸设置的外周凸缘38c。
需要说明的是,在轮罩外侧件38的车辆宽度方向外侧配置有构成车身10的后部的外侧面的侧外面板(sidememberouter)39。侧外面板39的沿轮罩外侧件38的形状而形成的下端部通过卷边加工而接合于纵壁部38b的下端部。
关于上述构成的轮罩34,上述的轮罩内侧件36和轮罩外侧件38的外周凸缘36c、38c之间通过点焊42接合,从车辆宽度方向观察时形成为半圆形的拱形。
在此,轮罩内侧件36的纵壁部36b比轮罩外侧件38的纵壁部38b向车辆下方侧延伸设置得长。此外,成为纵壁部36b的下端部从车辆宽度方向观察时与纵梁r/f30的延伸设置部30a重叠的构成。并且,该延伸设置部30a与纵壁部36b通过第二接合部44接合。纵梁r/f30的延伸设置部30a比配置有第一接合部40的覆盖部30b向车辆上方侧延伸设置,因此从车辆宽度方向观察时第二接合部44相对于第一接合部40在车辆上下方向分离。此外,第二接合部44配置于从车辆宽度方向观察时不与后纵梁16重叠(与后纵梁16分离)的位置。需要说明的是,第二接合部44被设为冶金接合构造,更具体而言,使用点焊42。
(关于后纵梁16与轮罩34的接合工序)接着,使用图3,对后纵梁16与轮罩34的接合工序进行详细说明。
如图3所示,铝压铸件制的后纵梁16在车身10的下部车身12的生产线上进行组装。此外,钢板制的纵梁r/f30也同样地在该下部车身12的生产线上使用铆钉接合机预先接合于后纵梁16。
另一方面,钢板制的轮罩34与侧外面板39一起在车身10的上部车身14的生产线上完成组装。
然后,在进行下部车身12与上部车身14的接合的主车身的生产线上,将下部车身12侧的纵梁r/f30与上部车身侧的轮罩内侧件36接合。具体而言,使纵梁r/f30的延伸设置部30a与轮罩内侧件36的纵壁部36b在车辆宽度方向重叠并通过点焊42接合。由此,后纵梁16与轮罩34的接合工序完成。
(作用以及效果)接着,对本实施方式的作用以及效果进行说明。
在本实施方式中,铝压铸件制的后纵梁16与钢板制的轮罩34隔着夹置于两者之间的钢板制的纵梁r/f30进行接合。在此,后纵梁16与纵梁r/f30通过第一接合部40进行接合,轮罩34与纵梁r/f30通过第二接合部44进行接合。此外,第二接合部44配置于从车辆宽度方向观察时不与第一接合部40和后纵梁16重叠的位置。
根据上述接合构造,能减少为了避免在车身的生产线上接合机与车身侧的零件的干扰而对车身10带来的外观设计的制约。
即,如图5所示的比较例那样,在将铝压铸件制的后纵梁50与铁制的轮罩52直接地接合的情况下,将轮罩内侧件54的纵壁部54a向车辆下方侧延伸设置。并且,纵壁部54a在与后纵梁50在车辆宽度方向上重叠的位置处使用自刺穿铆钉32(参照图2)进行接合。在此,后纵梁50和轮罩52分别组装于下部车身12和上部车身14,因此这些接合需要在使下部车身12和上部车身14接合的主车身的生产线上进行。因此,在通过比较大型的铆钉接合机进行接合的情况下,接合机容易与上下车身侧的零件产生干扰,为了避免该干扰而对车身10的外观设计的制约增加。
相对于此,在本实施方式中,能在形成下部车身12时预先将彼此为异种金属的纵梁r/f30与后纵梁16进行铆钉接合,然后,通过点焊来使彼此为同种金属的纵梁r/f30与上部车身侧的轮罩34接合。因此,在主车身的生产线上,不需要大型的铆钉接合机,使用比较小型的点焊机即可。由此,易于避免接合机与车身侧的零件的干扰,作为结果,能使对车身10带来的外观设计的制约减少。
而且,在本实施方式中,在比后纵梁16的上端部(上端部20a)向车辆上方侧延伸设置的延伸设置部30a形成第二接合部44,由此,第二接合部44配置于第一接合部40的车辆上方侧。因此,易于在纵梁r/f30组装于下部车身12后确保纵梁r/f30与轮罩34的重叠余量,接合点的定位变得容易。其结果是,成为车辆制造时的施工性也优异的构造。
需要说明的是,对于在主车身的生产线上避免接合机与车身侧的零件的干扰这一点,也可以采用将轮罩的接合工序加入主车身的生产线这样的方法。就是说,若基于图5所示的比较例的构造进行说明,则为如下工序:在主车身的生产线上,通过自刺穿铆钉32将轮罩内侧件54接合于下部车身的后纵梁50,接着,通过点焊将轮罩外侧件56接合于轮罩内侧件54,最后,将包括侧外面板58的上部车身接合于轮罩外侧件56。在此,在该工序中,在铆钉接合时轮罩内侧件54未组装于上部车身,因此具有易于避免接合机与车身零件的干扰的优点。另一方面,具有与在主车身的生产线上所处理的工序增加相应地导致整体的生产效率的下降的缺点。
鉴于这一点,对于上述的本实施方式的车身构造,主车身的生产线上的处理工序不会增加。由此,能提高车辆的外观设计的自由度,并且提高生产性。
此外,在本实施方式中,纵梁r/f30从车辆宽度方向外侧覆盖截面帽形形状的后纵梁16的开口部,因此沿车辆前后方向形成闭合截面。由此,能加强后纵梁16。并且,能通过根据需要变更纵梁r/f30的板厚、材质来提高后纵梁16的强度。
此外,在本实施方式中,与图5所示的比较例的构造不同,接合于后纵梁16的纵梁r/f30和轮罩34被设为分体。因此,相对于在比较例的构造的情况下为了提高后纵梁50的强度而需要变更轮罩52整体(至少轮罩内侧件54)的板厚、材质,本发明能仅通过纵梁r/f30的变更来提高后纵梁16的强度。由此,能抑制车身10的重量增加。
而且,由于能无需变更后纵梁16的截面地调整骨架强度,因此,即使在多个车型中共用后纵梁16的情况下,也能容易地确保骨架强度。
<第二实施方式>接着,使用图4对第二实施方式的车身构造进行说明。需要说明的是,对于与前述的第一实施方式相同的构成部分标注相同的附图标记并省略其说明。在该第二实施方式的车身构造中,特征在于后纵梁16的上凸缘部20的形状以及第一接合部40和第二接合部44的形成位置。需要说明的是,在图4的(a)中,通过立体图概略地示出了从车辆宽度方向观察配置于车辆宽度方向右侧部的后纵梁16的状态。
如图4的(a)、(b)所示,后纵梁16的上凸缘部20的形状形成为波浪形状。由此,在后纵梁16的上端部形成有多个凸片部46,所述凸片部46在车辆前后方向隔开规定的间隔地进行配置,并且向车辆上方侧突出。此外,该凸片部46与纵梁r/f30通过第一接合部40进行接合。
另一方面,轮罩内侧件36的纵壁部36b在配置于纵梁r/f30的车辆宽度方向外侧的状态下,其下端部36b1配置于与后纵梁16的上凸缘部20在车辆宽度方向重叠的位置。并且,在相邻配置的一对凸片部46之间配置有第二接合部44。由此,在纵梁r/f30,第一接合部40和第二接合部44沿后纵梁16的延伸方向配置为大致直线状,并交替地配置。此外,第二接合部44配置于从车辆宽度方向观察时不与第一接合部40和后纵梁16(凸片部46)重叠的位置。
根据上述构成,在后纵梁16的上端部与轮罩内侧件36的接合构造中,第一接合部40和第二接合部44的高度位置被设定为大致相同。因此,抑制了第一接合部40的接合点和第二接合部44的接合点的分布在车辆上下方向扩大。具体而言,能抑制在后纵梁16的上凸缘部20与轮罩内侧件36的纵壁部36b之间产生的空隙区间d扩大。需要说明的是,在图4的(b)中由斜线所图示的带状的区域为空隙区间d。
空隙区间d是在纵梁r/f30中与上凸缘部20接合的第一接合部40的接合点和与纵壁部36b接合的第二接合部44的接合点之间产生的在车辆上下方向分布的区间。该空隙区间d越扩大,后纵梁16与轮罩内侧件36间的载荷传递路径越长。由此,从提高载荷传递路径的观点来看,理想的是减小空隙区间d的上下方向的宽度。
(作用以及效果)上述构成的车身构造基本上沿袭了第一实施方式的车身构造,因此能得到同样的作用以及效果。
此外,在本实施方式中,第一接合部40沿形成于后纵梁16的上端部的多个凸片部46进行配置。此外,在邻接的凸片部46之间配置有第二接合部44。由此,能抑制沿纵梁r/f30的延伸方向配置的接合点向车辆上下方向的分布。其结果是,能提高后纵梁16与轮罩34间的载荷传递效率。
如上所述,在经由纵梁r/f30将后纵梁16与轮罩内侧件36接合的构造中,第一接合部40的接合点和第二接合部44的接合点的分布在车辆上下方向越扩大,后纵梁16与轮罩34之间的载荷传递路径越长,使载荷传递效率越下降。
因此,在本实施方式中,第一接合部40和第二接合部44沿车辆前后方向形成在大致直线上,抑制了沿纵梁r/f30的延伸方向配置的接合点向车辆上下方向的分布。由此,载荷传递路径变短,能提高后纵梁16与轮罩34间的载荷传递效率。
此外,能省略相当于上述第一实施方式的延伸设置部30a的部分而使纵梁r/f30小型化,因此,能进一步减少车身10的重量增加。
[补充说明]在上述各实施方式中,对经由纵梁r/f30将后纵梁16与车身10的容纳后轮的轮罩34接合的车身构造进行了说明,但本发明并不限定于此。例如,也可以是经由纵梁r/f将前纵梁与容纳车辆的前轮的轮罩接合的构造。
此外,在上述的各实施方式中,通过自刺穿铆钉32将后纵梁16与纵梁r/f30接合,但并不限定于此,也可以应用其他的机械接合构造。此外,在上述的各实施方式中,通过点焊42将纵梁r/f30与轮罩34接合,但并不限定于此,也可以应用其他的冶金接合构造。
起点商标作为专业知识产权交易平台,可以帮助大家解决很多问题,如果大家想要了解更多知产交易信息请点击 【在线咨询】或添加微信 【19522093243】与客服一对一沟通,为大家解决相关问题。
此文章来源于网络,如有侵权,请联系删除


