一种平台化前副车架的制作方法



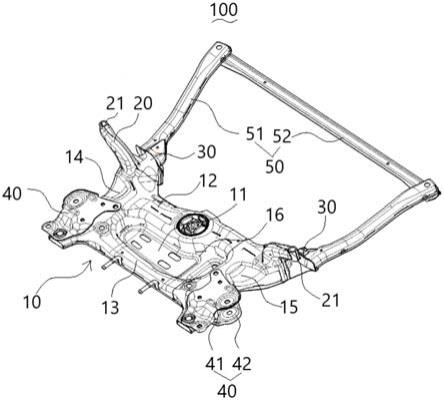
[0001]
本实用新型涉及汽车底盘技术领域,尤其是涉及一种平台化前副车架。
背景技术:
[0002]
随着国内汽车品牌的竞争日趋激烈,顾客对于汽车质量的要求也越来越高。如何能够在有限的研发经费中,提供更多更高质量的车型,是汽车研发人员急需解决的问题。在汽车研发过程中,每一款新的车型都需要重新研发一套新的底盘结构,其中前副车架就是底盘零部件系统中的重要组成部分。其主要连接车身、发动机悬置以及悬架等零件,可以减少路面的振动以及噪音等激励向车身传递,同时还可以提高悬架的刚度,使得车身可以获得更好的舒适性和稳定性。因此,在一款新的车型的研发过程中,前副车架结构的研发设计需要耗费较多的研发经费和研发周期。
[0003]
在中国专利文献公开号为cn201820377604.1中提供了一种前副车架总成。该前副车架总成存在以下缺陷:第一,前副车架主体的上下板为整块钣金冲压成型,其羊角处和车身安装点套管直径较大,不利于布置稳定杆,并且该前副车架主体仅适用于一种转向机类型,不利于平台化车型的升级和衍生,若该前副车架总成的周边边界条件发生变化,该前副车架的整体结构就需要重新研发,重新开发模具、检具和焊接工装,所需投入的研发成本较高;第二,该前副车架的前侧无防撞梁吸能结构,不能很好的吸收汽车冲击过程中由于碰撞所产生的能量,在日趋严格的汽车安全法规的碰撞要求中无法满足碰撞要求为汽车乘员舱提供有效地保护;第三,该前副车架上的后侧安装点加强板、稳定杆安装支架等部件分别用不同钣金散件焊接在前副车架主体上,在焊接过程中容易在前副车架主体处出现裂缝,并且焊接的精度差,成本高。
[0004]
综上所述,现有的前副车架总成的设计大多仅能适用于一款转向机等配套的设备,无法满足平台化升级和衍生的需求,并且前副车架的吸能结构不足,也无法满足碰撞安全性能的要求,同时,前副车架上多个连接点通过焊接固定时的焊接精度低、成本高且容易在前副车架主体上产生裂缝的问题。
技术实现要素:
[0005]
本实用新型的目的在于解决现有前副车架总成无法平台化升级和衍生,碰撞性能差、多个部件之间焊接容易在主体上出现裂缝且焊接精度低、成本高的缺点,提供一种平台化前副车架。
[0006]
本实用新型解决其技术问题采用的技术方案是:一种平台化前副车架,包括前副车架本体,所述前副车架本体包括底板、前上板、后上板、左上板和右上板,所述前上板与所述底板焊接形成前横梁,所述后上板与所述底板焊接形成后横梁,所述左上板与所述底板焊接形成左纵梁,所述右上板与所述底板焊接形成右纵梁,所述前上板、所述后上板、所述左上板和所述右上板在所述底板的中心处围合形成容纳转向机放置的凹槽。
[0007]
进一步地,还包括一对固定于所述底板上、分别位于所述前上板前侧两端的羊角
安装支架,所述羊角安装支架的底部焊接于所述底板上,顶部焊接有羊角安装套管。
[0008]
具体地,所述羊角安装套管在远离所述羊角安装支架的一侧设置有由上至下贯穿所述羊角安装套管的缺口。
[0009]
进一步地,还包括一对设置于所述前副车架本体前方的摆臂前安装支架和一对设置于所述前副车架本体后方的摆臂后安装支架组。
[0010]
进一步地,还包括固定于所述前副车架本体前方的前防撞梁,所述前防撞梁包括一对分别由所述左上板和所述右上板的前端向前方延伸的小纵梁以及连接两个所述小纵梁的前加强横梁。
[0011]
具体地,所述小纵梁包括相互拼接的小纵梁上板和小纵梁下板,所述小纵梁上板的末端焊接于所述摆臂前安装支架上,所述小纵梁下板的末端焊接于所述底板上所述前加强横梁的两端分别搭接于一对所述小纵梁下板的前端。
[0012]
具体地,所述摆臂后安装支架组包括设置于所述左上板或所述右上板上的摆臂后安装支架上板和固定于所述底板上的摆臂后安装支架下板。
[0013]
具体地,所述摆臂后安装支架上板和所述摆臂后安装支架下板在远离所述前防撞梁的一侧相互焊接固定。
[0014]
具体地,所述摆臂后安装支架上板和所述摆臂后安装支架下板上均设置有可供前下摆臂后侧衬套固定的摆臂后衬套安装位。
[0015]
具体地,所述摆臂后安装支架上板上还设置有用于固定稳定杆的稳定杆安装位和用于固定所述转向机的转向机安装位。
[0016]
本实用新型所提供的一种平台化前副车架的有益效果在于:该前副车架本体是由一块底板和四块上板焊接而成,并且四块上板在底板的中心处围合形成了容纳转向机放置的凹槽,相较于传统结构通过钣金件拔模成型的设计方式,可以在有限的空间范围内形成最大的空间避让用于放置转向机,并且底板与四块上板焊接的方式也更加有利于底盘和前机舱各个零件的布置,仅需修改四块上板与底板的尺寸即可实现车型之间的升级和衍生,节约新车型的研发时间和成本。
附图说明
[0017]
图1是本实用新型提供的一种平台化前副车架的第一视角的立体结构示意图;
[0018]
图2是本实用新型提供的一种平台化前副车架的第二视角的立体结构示意图;
[0019]
图3是本实用新型提供的一种平台化前副车架的第三视角的立体结构示意图;
[0020]
图4是本实用新型提供的一种平台化前副车架的羊角安装套管处的局部放大图;
[0021]
图5是本实用新型提供的一种平台化前副车架的摆臂前安装支架处的立体结构示意图;
[0022]
图6是本实用新型提供的一种平台化前副车架的摆臂后安装支架处的立体结构示意图。
[0023]
图中:100-平台化前副车架、10-前副车架本体、11-底板、12-前上板、13-后上板、14-左上板、15-右上板、16-凹槽、20-羊角安装支架、21-羊角安装套管、22-缺口、30-摆臂前安装支架、40-摆臂后安装支架、41-摆臂后安装支架上板、411-稳定杆安装位、412-转向机安装位、42-摆臂后安装支架下板、43-焊接位、44-摆臂后衬套安装位、50-前防撞梁、51-小
纵梁、511-小纵梁上板、512-小纵梁下板、52-前加强横梁。
具体实施方式
[0024]
为了使本实用新型的目的、技术方案及优点更加清楚明白,以下结合附图及实施例,对本实用新型进行进一步详细说明。应当理解,此处所描述的具体实施例仅仅用以解释本实用新型,并不用于限定本实用新型。
[0025]
参见图1-图6,为本实用新型所提供的一种平台化前副车架100。该平台化前副车架100中的多个部件可以随着不同车型中的悬架总成的配置不同而进行适应性调整,从而满足相同车型中不同配置的升级需求或者是不同车型的衍生需求。
[0026]
具体地,如图1所示,本实用新型所提供的一种平台化前副车架100,包括前副车架本体10,前副车架本体10包括底板11、前上板12、后上板13、左上板14和右上板15。该底板11呈蝶状结构,采用整体钣金件成型加工,设置于整个平台化前副车架100的底部用于承托和固定前上板12、后上板13、左上板14和右上板15。而位于底板11上的前上板12、后上板13、左上板14和右上板15均为截面呈n字形结构,具有两个相互平行的竖直面,通过竖直面底部的翻边与底板11焊接固定。其中,前上板12与底板11焊接形成前横梁,后上板13与底板11焊接形成后横梁,左上板14与底板11焊接形成左纵梁,右上板15与底板11焊接形成右纵梁。该前上板12和后上板13均位于左上板14和右上板15之间,即前上板12和后上板13的左右两端部分别与左上板14和右上板15焊接固定,整个前副车架本体10的连接结构可以提升前副车架100的车架强度和刚度。同时,该前上板12、后上板13、左上板14和右上板15在底板11的中心处围合形成容纳转向机放置的凹槽16。该凹槽16形成于底板11的中央处,用于容纳前悬架总成中的转向机放置。
[0027]
具体地,如图2所示,在本实用新型所提供的一种平台化前副车架100中,该前副车架本体10中的前上板12与底板11之间相互焊接固定。并且在前上板12的中心处设置有可与后悬置总成中的拉杆固定连接的安装部121,该安装部121包括设置于前上板12的前侧中央的安装孔122以及设置于前上板12与底板11之间的两个橡胶衬套123。后悬置总成中的拉杆可以的一端由该安装孔122伸入前上板12内部并最终固定于两个橡胶衬套123中。在前上板12与底板11之间设置的两个橡胶衬套123可以增加整个前副车架本体10的强度和刚度,设置在上方的橡胶衬套123的内管设置为螺纹管,设置于下方的橡胶衬套123的内管设置为通孔。在前上板12上设置用于固定拉杆的安装部121可以为后悬置总成的设置避让出更多x向空间,使得使用该平台化后副车架100的后悬置的布置更加紧凑。同时,本实用新型所提供的前副车架本体10的底板11和四个上板的结构中,还可以在前上板12和右上板15之间增设第二拉杆支架,通过第二拉杆支架用于增加后悬置安装点,无需重新开模即可实现单拉杆和双拉杆之间的相关切换,可以为前副车架100提供较大的扭矩,解决单个后悬置拉杆动刚度不足的问题,提升整车的nvh性能。
[0028]
本实用新型所提供的一种平台化前副车架100中的前副车架本体10的整体呈蝶状设计,并且前副车架本体10是由一块底板11和四块上板(前上板12、后上板13、左上板14和右上板15)相互焊接而成,使得前副车架本体10具有较强的抗扭转、动刚度、高强度和安全性能。并且四块上板在底板11的中心处围合形成了容纳转向机放置的凹槽16,本实用新型所提供的这种由底板11与四块上板相互焊接形成的前横梁、后横梁、左纵梁和右纵梁结构,
相较于传统的通过钣金件拔模成型结构,可以在有限的车身底盘空间范围内形成最大的空间避让用于放置转向机。这种设计结构能够最大限度的满足使用平台车型中转向机不同供应商电机所需边界的需求,还可以降低样件在冲压成型中的减薄率。并且底板11与四块上板焊接的方式也更加有利于底盘和前机舱各个零件的布置。本实用新型所提供的前副车架本体10的底板11与四块上板焊接成型的结构,也更加利于前副车架100的升级与衍生,对于该前副车架100用于匹配不同型号和尺寸的其他前悬置总成配件时,仅需对底板11的尺寸以及对应的四个上板的尺寸进行适应性调整,即可衍生出不同的车型所需的前副车架本体10结构。在新车型的研发时,仅需修改底板11与四块上板的尺寸即可实现车型之间的升级和衍生,节约新车型的研发时间和成本。同时,对于前悬置总成上其他配件与前副车架本体10之间的连接也仅需调整安装支架的尺寸和结构即可灵活混合取舍以适用于不同平台需求。
[0029]
进一步地,如图1所示,本实用新型所提供的一种平台化前副车架总成100中还包括一对固定于底板11上、分别位于前上板12前侧两端的羊角安装支架20。该羊角安装支架20设置于整个前副车架本体10的前端两侧,并由前端向两侧延伸。羊角安装支架20的底部焊接于底板11上,顶部焊接有羊角安装套管21。该羊角安装支架20包括相互焊接的前板和后板,该前板和后板的底部均与前副车架本体10的底板11焊接固定,顶部焊接有羊角安装套管21。该羊角安装支架20通过其顶部所设置的羊角安装套管21与车身连接。
[0030]
具体地,如图4所示,本实用新型所提供的羊角安装套管21在远离羊角安装支架20的一侧设置有由上至下贯穿羊角安装套管21的缺口22。该缺口22设置于整个前副车架100的外侧,可以在碰撞过程中结合前副车架100的其他部件传力路径到羊角安装套管21处,通过该缺口22诱导进行快速脱落,从而解决短前悬情况下在碰撞后利用有限的空间范围吸能,适应更加严格的汽车安全法规。该缺口22的设置配合该羊角安装套管21的壁厚设计,可以在车辆发生偏置碰撞的时候,诱导车身由羊角安装套管21的缺口22处快速脱落,也可以为稳定杆和驱动轴布置避让更大的空间。该缺口22的宽度与羊角安装套管21的壁厚相关。在本实施例中,羊角安装套管21的壁厚为4.5mm,能够为平台车型前横向稳定杆和驱动轴的x向更大空间,能适应平台不同车型周边零件的衍生。同时,设置与羊角安装套管21上的缺口22的宽度为1mm-2.5mm。该缺口22设计在该宽度范围内,能够保证羊角安装套管21在预紧力矩时不会发生屈服,并且在整车的耐久试验后也不会发生力矩衰减的问题。作为优选的,该角安装套管21的壁厚为4.5mm时,缺口22的宽度为1.5mm。
[0031]
进一步地,如图3所示,本实用新型所提供的一种平台化前副车架100还包括一对设置于前副车架本体10前方的摆臂前安装支架30和一对设置于前副车架本体10后方的摆臂后安装支架组40。该摆臂前安装支架30和摆臂后安装支架组40用于将前副车架本体10与前悬置总成中的前下摆臂固定连接。其中位于前副车架本体10后侧的摆臂后安装支架组40采用上下夹持的方式安装和固定前下摆臂,从而可以适用于使用橡胶衬套或者液压衬套的前下摆臂使用,利于前副车架100的平台化设计需求。而摆臂前安装支架30设置于前副车架本体10的前侧,位于前上板12的前侧的两端。在前副车架本体10的底板11上设置有用于固定前下摆臂前端衬套的安装位,并且在摆臂前安装支架30上设置有可供前下摆臂的前端插入底板11与摆臂前安装支架30之间的工艺安装孔。
[0032]
进一步地,如图2所示,本实用新型所提供的一种平台化前副车架100中还包括固
定于前副车架本体10前方的前防撞梁50,前防撞梁50包括一对分别由左上板14和右上板15的前端向前方延伸的小纵梁51以及连接两个小纵梁51的前加强横梁52。在本实用新型所提供的一种平台化前副车架100中,该摆臂前安装支架30还同时兼顾连接前副车架本体10与前防撞梁50的作用。该前防撞梁50的小纵梁51的末端上部分与摆臂前安装支架30焊接固定,末端的下部分与前副车架本体10的底板11固定连接。在底板11的前端设置有与前防撞梁50连接的接口。
[0033]
具体地,如图5所示,为本实用新型的前防撞梁50与前副车架本体10连接处的局部放大图。在本实施例中,该小纵梁51包括相互拼接的小纵梁上板511和小纵梁下板512,小纵梁上板511的末端焊接于摆臂前安装支架30上。在小纵梁上板511与摆臂前安装支架30的连接处,还设置有加强板(图中未示出),该加强板设置于小纵梁上板511与摆臂前安装支架30之间,不仅能够降低小纵梁51整体钣金件冲压工艺的难度,还可以大大提升钣金材料的利用率,前下摆臂前点动刚度、强度以及安全性能。如图3所示,小纵梁下板512的末端焊接于底板11上,前加强横梁52的两端分别搭接于一对小纵梁下板512的前端。小纵梁上板511的末端焊接于摆臂前安装支架30上,通过摆臂前安装支架30实现与前副车架本体10的左上板14或右上板15之间的固定连接。小纵梁下板512的底部直接焊接到底板11上实现与前副车架本体10的固定连接。其中,前防撞梁50的一对小纵梁51的末端均与前副车架本体10固定连接,前端通过前加强横梁52固定连接。该前加强横梁52为横向设置的钣金件,用于连接和固定一对小纵梁51的前端。该前防撞梁50在一对小纵梁51的前端还设置有与车身连接的连接固定位513,位于前防撞梁50上的一对连接固定位513与位于前副车架本体10上的其余6个固定位配合实现与车身之间的固定连接。
[0034]
具体地,如图1和如图6所示,本实用新型所提供的一种平台化前副车架100中,该摆臂后安装支架组40包括设置于左上板14或右上板15上的摆臂后安装支架上板41和固定于底板11上的摆臂后安装支架下板42。摆臂后安装支架上板41和摆臂后安装支架下板42均是有前副车架本体10的侧面后方向着两侧延伸的钣金件。通过摆臂后安装支架上板41和摆臂后安装支架下板42由上下两侧夹紧前下摆臂的后安装点。该摆臂后安装支架组40的设置为整个平台化前副车架100周边零件布置提供了空间和轻量化的结构设计方案。
[0035]
具体地,在本实施例中,应用于前副车架本体10上的前下摆臂上设置的衬套为橡胶衬套,因此在摆臂后安装支架上板41和摆臂后安装支架下板42上均设置有可供前下摆臂后侧衬套固定的摆臂后衬套安装位44。该摆臂后衬套安装位44由上下两侧将橡胶衬套上下夹紧固定。若该前下摆臂上设置的衬套为液压衬套,仅需将摆臂后安装支架上板41和摆臂后安装支架下板42进行适应性调整为适合液压衬套放置的凹槽即可,通过上下夹持的方式固定。本实用新型所提供的平台化前副车架100中的摆臂后安装支架组40可以适用于不同前下摆臂的衬套结构相互切换,而前副车架本体10部分无需重新开模设计,更加利于前副车架100的平台化需求,加速整车研发的速度,降低研发成本和丰富产品的配置,降低研发过程中的风险。
[0036]
具体地,如图3所示,本实用新型所提供的摆臂后安装支架组40中的摆臂后安装支架上板41和摆臂后安装支架下板42在远离前防撞梁50的一侧相互焊接固定。即在摆臂后安装支架上板41和摆臂后安装支架下板42的后侧具有相互连接的焊接位。该摆臂后安装支架下板42的后侧具有向上延伸至摆臂后安装支架上板41处的翻边43。通过设置于摆臂后安装
支架下板42上的翻边43实现摆臂后安装支架上板41和摆臂后安装支架下板42在前副车架本体10后侧相互固定连接,两者相互焊接固定之后,使得整个摆臂后安装支架组40的结构更牢固,能提升前下摆臂后安装点动刚度,同时也能预防前悬架总成过减速带产生的异响。
[0037]
具体地,如图6所示,本实用新型所提供的摆臂后安装支架组40中摆臂后安装支架上板41上还设置有用于固定稳定杆的稳定杆安装位411和用于固定转向机的转向机安装位412。后悬置总成中的稳定杆通过稳定杆固定夹利用紧固件固定于该稳定杆安装位411上,实现稳定杆与前副车架100的固定连接。该稳定杆安装位411和转向机安装位412均设置于摆臂后安装支架上板41,位于同一平面上,可以无需另外增加安装点支架或者凸台的设计即可完成稳定杆和转向机的安装与固定。并且在转向机安装位412的周边无需焊接工艺,更加有利于减少由于焊缝引起热影响区域导致开裂的问题。同时,在转向机安装于转向机安装位412时,还可以利用转向机安装力矩预紧时所产生的预紧力自动压紧摆臂后安装支架上板41,更加有利于前下摆臂后安装点的夹持固定,还可以有利于增加前下摆臂安装点z向动刚度。
[0038]
具体地,如图6所示,本实用新型所提供的摆臂后安装支架组40中摆臂后安装支架上板41上还设置有两个与车身连接的连接固定位413,位于摆臂后安装支架上板41上的四个连接固定位413位于整个平台化前副车架100的后侧。该四个连接固定位413与位于前防撞梁50上的一对连接固定位513以及位于羊角安装支架20上的羊角安装套管21组成了整个前副车架100上的八个与车身连接的固定位,八个固定位分别位于整个前副车架100的前中后三段,使得前副车架100与车身的连接更加可靠,可以提升整车的nvh性能。
[0039]
以上仅为本实用新型的较佳实施例而已,并不用以限制本实用新型,凡在本实用新型的精神和原则之内所作的任何修改、等同替换和改进等,均应包含在本实用新型的保护范围之内。
起点商标作为专业知识产权交易平台,可以帮助大家解决很多问题,如果大家想要了解更多知产交易信息请点击 【在线咨询】或添加微信 【19522093243】与客服一对一沟通,为大家解决相关问题。
此文章来源于网络,如有侵权,请联系删除



tips