一种风力松散除杂机及方法与流程



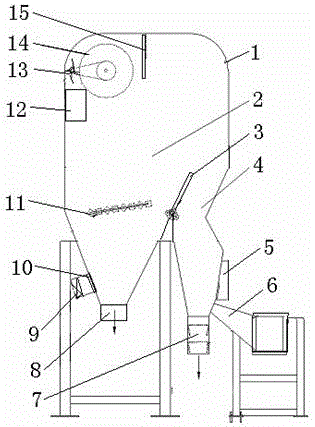
本发明涉及一种风力松散除杂机及方法,特别涉及一种在打叶复烤生产线上,为实现光电自动选叶而先要完成烟叶松散的设备及方法,属于烟草加工技术领域。
背景技术:
在烟叶打叶复烤生产中,通常都使用滚筒式润叶机对烟叶进行加温、加湿,使烟叶柔软、松散。由于烟叶受压且长期存放等原因,致使部分烟叶因粘连严重而出现结饼或结块现象,这样在使用上述滚筒式润叶机进行处理时,难于将结饼或结块的烟叶分开,当送入打叶复烤生产线上后,因要使用光电自动选叶设备对充分松散,并舒展的烟叶进行选别,而结饼或结块的烟叶因尚未分开,更谈不上松散、舒展,因而很难将其中的杂质或废、次烟叶剔除,这样必然会因烟叶中夹带杂质、废烟叶、次烟叶而影响烟叶质量。因此,有必要对现有技术加以改进。不仅要解决粘连结饼或结块的烟叶无法进行松散的问题,还要解决如何将松散的烟叶进行舒展的问题,使烟叶在进入打叶复烤生产线上后,能够通过光电装置自动对充分松散并舒展的烟叶进行精准选别。
技术实现要素:
本发明正是为解决现有技术存在的上述不足,提供一种风力松散除杂机及方法。
本发明利用风力输送、机械抛翻和加温去湿等方式对湿度为13-18%的烟叶进行松散、舒展、适当干燥处理,并去除其中所含的石块、金属等重质量杂质,以及粘接结块的烟叶和轻质量的麻丝、灰尘等杂质,以满足打叶复烤生产线使用光电自动选叶设备对松散、舒展的烟叶进行选叶、分级的工艺要求。
本发明通过下列技术方案完成:一种风力松散除杂机,包括其内带空腔的壳体,其特征在于空腔顶部相互连通、底部通过隔板分为松散烟叶空腔、舒展烟叶空腔,松散烟叶空腔底部设有重质量杂质和结块烟叶排出口、侧部设有进料口和进风口,舒展烟叶空腔底部设有烟叶排出口、中部设有烟叶舒展辊组、顶部设有挡板和排风口,以便烟叶自进料口进入松散烟叶空腔后,通过进风口送入的风力将烟叶向上托起、分散的同时,使重质量杂质和结块烟叶在自重作用下落入下方的排出口排出,托起、分散的烟叶随风进入上部空腔后,在挡板作用及自重作用下落入舒展烟叶空腔中部的烟叶舒展辊组上,经烟叶舒展辊组的反复抛起、翻动而完成烟叶舒展后,落入下方的排出口排出,从而完成烟叶松散、舒展、除杂。
所述隔板设为竖直板,隔板的下端通过水平铰轴铰接在壳体上,水平铰轴两端分别通过轴承固定在壳体壁上,水平铰轴的其中一端向外延伸后与手柄相连,通过手柄调节隔板的倾斜角底;或者水平铰轴的其中一端向外延伸后与动力机相连,通过动力机调节隔板的倾斜角底;使松散烟叶空腔形成异形烟叶通道,并通过隔板倾斜角度的调整,实现内速调整,完成烟叶的松散。
所述挡板设为竖直板,挡板的上端固定在壳体顶壁上、下端悬空,以便进入松散烟叶空腔顶部的烟叶在挡板的阻挡作用下失速、改向后,在自身重力作用下顺利进入舒展烟叶空腔中,再在自重作用下落入烟叶舒展辊组上,进行烟叶舒展。
所述舒展烟叶空腔一侧设有通孔,通孔上设置干燥器,所述干燥器包括固定在通孔上的电加热元件,固定在通孔外侧的风管,风管外端与鼓风机相连,以便通过鼓风机送风至电加热元件加热成热风后送入舒展烟叶空腔中,用于对烟叶进行干燥,降低烟叶中的水份。
所述排风口内侧设有其上带网孔的滚筒,滚筒一侧设有毛刷辊,毛刷辊下方设有收集槽,滚筒的筒轴一端连接有转动轮,该转动轮通过传动带与电机主轴上的主动轮相连,以便在电机带动下通过主动轮、传动带、转动轮使滚筒转动,从而使随风带入的麻丝等轻质杂物被网孔挂住后,经毛刷辊带离滚筒的网孔进入下部的收集槽中。
所述排风口外侧连接有回风管,该回风管外端与风机入风口相连,风机出风口通过短管或直接与松散烟叶空腔上的进风口相连,以形成循环供风。
所述壳体上位于松散烟叶空腔侧部的进风口设于进料口下方,以便将进入的烟叶通过风力向上托起、吹散。
所述烟叶舒展辊组包括断面呈矩形的、间隔且交错设置的若干水平辊,若干水平辊的两端分别通过对应的轴承固定在壳体壁上,形成无动力辊组而自行转动;或者若干水平辊的其中一端向外延伸后通过传动件与动力机相连,以便在动力机带动下通过传动件使若干水平辊转动;进而使烟叶被反复抛起、翻动而完成再次松散、舒展。
本发明提供的一种基于所述风力除杂机对烟叶进行松散、舒展的方法,其特征在于包括下列步骤:
1)一次松散烟叶,以4-9m/s的风速,向松散烟叶空腔中供风,用该风力使进入松散烟叶空腔中的含水量为13-18%的烟叶,在下部的异形通道中自下而上被托起、被旋转、与壳体内壁发生碰撞,使粘连成块的烟叶被打开、松散,同时质量大的结块物料和非烟杂质在自重作用下,沉落至该空腔底部的排出口排出,完成一次松散和除杂;
2)随风向上进入上部的烟叶,在挡板作用下进入舒展烟叶空腔中部,再在自身重力作用下落入烟叶舒展辊组上;
3)二次松散并舒展烟叶,落入烟叶舒展辊组上的烟叶,经烟叶舒展辊组的反复抛起、翻动完成二次松散的同时,完成烟叶舒展后,落入下方的排出口排出;
4)麻丝除去,风从舒展烟叶空腔顶部排风口排出的同时,随风带入的麻丝等轻质杂物被其上带网孔的滚筒阻隔在网孔上,经毛刷辊带离滚筒的网孔并进入下部的收集槽中,完成麻丝的去除;
5)风经回风管、风机进入松散烟叶空腔,形成循环供风。
还包括对舒展、摊平后的烟叶进行干燥的步骤,通过舒展烟叶空腔一侧的干燥器,对进入舒展烟叶空腔内的烟叶进行干燥,降低烟叶中的水份至8-12%。
本发明具有下列优点和效果:采用上述方案,可方便地利用风力在密闭环境中对粘连结块的烟叶进行充分打开、松散、舒展并去除重质物及轻质麻丝等杂物,风力输送使本发明具有较大的处理能力,机械抛翻进一步使烟叶充分松散、舒展,通过干燥器,对烟叶进行除湿,有效地控制烟叶的水分,使烟叶既有一定的舒展度,又保持一定的韧性,降低烟叶的造碎率,同时保证烟叶的平展度,为后续打叶复烤生产线中,利用光电设备自动、有效分选出不同的等级烟叶提供有效、可靠的技术支持,最终获得物理状态好的烟叶。
附图说明
图1为本发明结构示意图;
图2为图1的俯视图。
具体实施方式
下面结合附图对本发明做进一步描述。
如图1、图2,本发明提供的风力松散除杂机,包括其内带空腔的壳体1,其中,空腔顶部相互连通、底部通过隔板3分为松散烟叶空腔4、舒展烟叶空腔2,松散烟叶空腔4底部设有重质量杂质和结块烟叶排出口7、侧部设有进料口5和进风口6,舒展烟叶空腔2底部设有烟叶排出口8、中部设有烟叶舒展辊组11、顶部设有挡板15和排风口16;所述隔板3设为竖直板,隔板3的下端通过水平铰轴铰接在壳体1上,水平铰轴两端分别通过轴承固定在壳体1壁上,水平铰轴的其中一端向外延伸后与手柄相连,通过手柄调节隔板3的倾斜角底;或者水平铰轴的其中一端向外延伸后与动力机相连,通过动力机调节隔板3的倾斜角底;使松散烟叶空腔4形成异形烟叶通道,并通过隔板3倾斜角度的调整,实现内速调整,完成烟叶的松散;所述挡板15设为竖直板,挡板15的上端固定在壳体1顶壁上、下端悬空,以便进入松散烟叶空腔2顶部的烟叶在挡板15的阻挡作用下失速、改向后,再在自身重力作用下顺利落入舒展烟叶空腔2中的烟叶舒展辊组11上,进行烟叶舒展;所述舒展烟叶空腔2一侧设有通孔,通孔上设置干燥器,所述干燥器包括固定在通孔上的电加热元件10,固定在通孔外侧的风管9,风管9外端与鼓风机相连,以便通过鼓风机送风至电加热元件10加热成热风后送入舒展烟叶空腔2中,用于对烟叶进行干燥,降低烟叶中的水份;所述排风口16内侧设有其上带网孔的滚筒14,滚筒14一侧设有毛刷辊13,毛刷辊13下方设有收集槽12,滚筒14的筒轴一端连接有转动轮,该转动轮通过传动带与电机主轴上的主动轮相连,以便在电机带动下通过主动轮、传动带、转动轮使滚筒14转动,从而使随风带入的麻丝等轻质杂物被网孔挂住后,经毛刷辊13带离滚筒14的网孔进入下部的收集槽12中;所述排风口16外侧连接有回风管17,该回风管17外端与风机18入风口相连,风机18出风口直接与松散烟叶空腔4上的进风口6相连,以形成循环供风;所述壳体1上位于松散烟叶空腔4侧部的进风口6设于进料口5下方,以便将进入的烟叶通过风力向上托起、吹散;所述烟叶舒展辊组11包括断面呈矩形的、间隔且交错设置的若干水平辊,若干水平辊的两端分别通过对应的轴承固定在壳体壁上,若干水平辊的其中一端向外延伸后通过传动件与动力机相连,以便在动力机带动下通过传动件使若干水平辊转动;进而使烟叶被反复抛起、翻动而完成再次松散、舒展。
本发明提供的一种基于所述风力除杂机对烟叶进行松散、舒展的方法,其特征在于包括下列步骤:
1)一次松散烟叶,以4-9m/s的风速,通过进风口6向松散烟叶空腔4中供风,用该风力使进入松散烟叶空腔4中的含水量为13-18%的烟叶,在下部的异形通道中自下而上被托起、被旋转,并且与壳体1内壁发生碰撞,使粘连成块的烟叶被打开、松散,同时质量大的结块物料和非烟杂质在自重作用下,沉落至该空腔底部的排出口7排出,完成一次松散和除杂;
2)随风向上进入上部的烟叶,在挡板15作用下,失速、改向进入舒展烟叶空腔2中部,再在自身重力作用下落入烟叶舒展辊组11上;
3)二次松散并舒展烟叶,落入烟叶舒展辊组11上的烟叶,经烟叶舒展辊组11的反复抛起、翻动完成二次松散的同时,完成烟叶舒展后,并在下落过程中,通过舒展烟叶空腔2一侧的干燥器9、10,对进入舒展烟叶空腔2内的烟叶进行干燥,降低烟叶中的水份至8-12%,经排出口8排出;
4)麻丝除去,风从舒展烟叶空腔2顶部排风口16排出的同时,随风带入的麻丝等轻质杂物被其上带网孔的滚筒14阻隔在网孔上,经毛刷辊13带离滚筒14的网孔并进入下部的收集槽12中,完成麻丝的去除;
5)风经回风管17、风机18再进入松散烟叶空腔2,形成循环供风。
起点商标作为专业知识产权交易平台,可以帮助大家解决很多问题,如果大家想要了解更多知产交易信息请点击 【在线咨询】或添加微信 【19522093243】与客服一对一沟通,为大家解决相关问题。
此文章来源于网络,如有侵权,请联系删除


