悬挂式单轨系统的制作方法



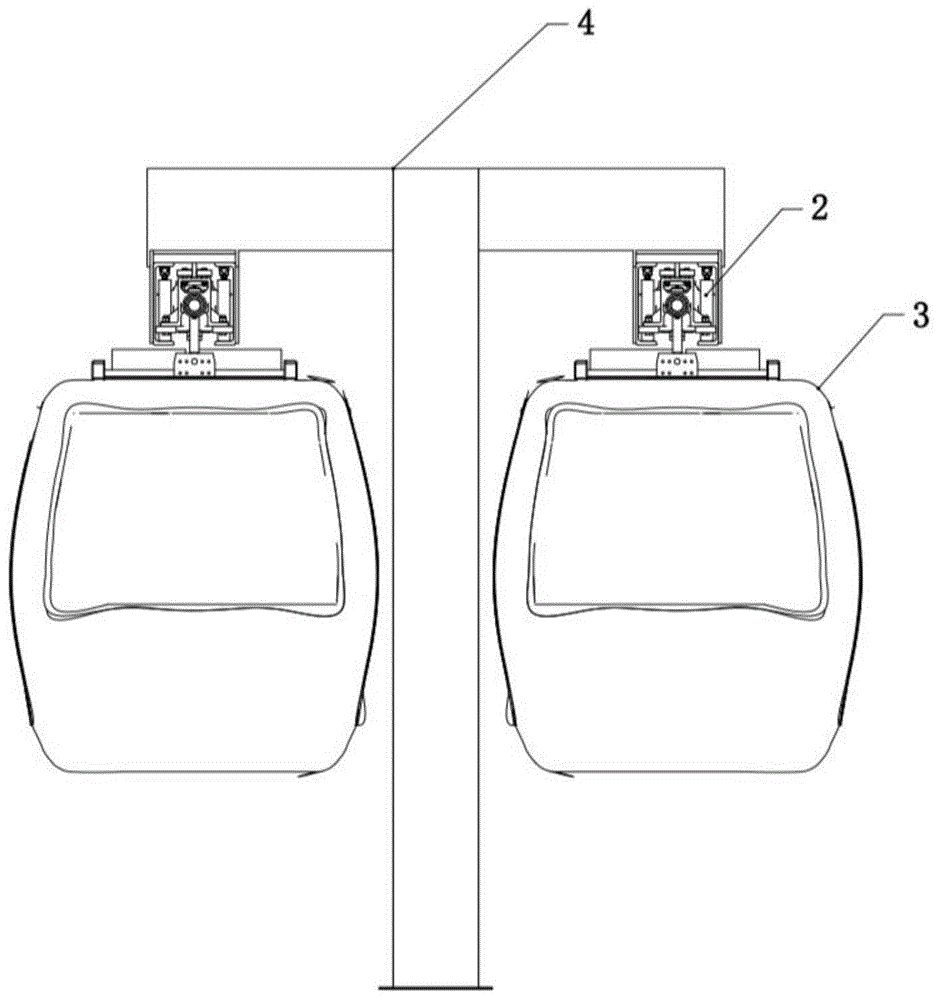
本申请涉及悬挂式轨道运输领域,具体涉及悬挂式单轨系统。
背景技术:
悬挂式单轨系统指的是载具悬挂在轨道下方运行的铁路轨道系统,由于轨道主体结构和动车整体走行空间均在一定高度的空中,该轨道系统整体所需的占地面积很小,因此可以一定程度上缓解城市紧张的土地资源问题;另外,动车在轨道下方运行,动车内的乘客可以获得更广阔的视野,得益于此,悬挂式单轨不仅可以作为交通工具缓解城市交通问题,而且还可以作为观光车使用,为旅客提供更好的观光体验。除此之外,悬挂式单轨的造价相比地铁要低得多,并且工程速度更快。
现有的悬挂式单轨系统的动车在转向时一般是依靠动车自带的转向轮或者说导向轮与轨道梁的导向面或导向板配合完成,其中,导向面或导向板一般设置于轨道梁内部两侧边,而转向轮设置于走行轮外侧并与导向面或导向板接触。动车转弯时,导向面或导向板压迫转向轮使动车完成转向。这样的设置导致动车转向架的宽度增大,并且对轨道梁内部宽度的一致性要求较高,即要求很小范围的宽度误差,从而增加了施工难度,提升了工程造价;另外,在动车转弯时,因为是单侧转向轮受力,在轨道梁内部宽度与设计必然存在误差的情况下,其转向稳定性难以保证,即动车转弯时的稳定性还有待加强以提升乘坐舒适性和安全性。
技术实现要素:
出于提升动力车架运行稳定性、降低整体工程成本等目的,本申请提供了一种悬挂式单轨系统,所述悬挂式单轨系统包括轨道梁和匹配的支撑装置、若干动力车架和匹配的载具;所述轨道梁下部中间开口,内部贯通形成动力车架的走行空间;所述动力车架沿走行空间行走,所述动力车架的下方吊挂有载具;所述支撑装置支撑轨道梁,所述载具悬挂于轨道梁下方;
所述轨道梁的内部两侧底面形成走行面,所述动力车架的两侧设置走行轮,所述走行轮沿走行面行走;所述轨道梁的内部上方、并且两侧走行轮之间中部固定设置导向板,所述动力车架的上部左右两侧向内分别设置导向轮,两侧导向轮接触或邻近导向板并沿导向板行走;
所述轨道梁的宽度小于载具的宽度。
可选的,两侧导向轮接触导向板;所述动力车架设有夹紧装置;所述夹紧装置驱使两侧导向轮夹紧导向板;所述夹紧装置为液压装置、弹力装置或电磁装置,导向轮带驱动装置或不带驱动装置。
可选的,所述动力车架两侧导向轮未夹紧导向板,且两侧相邻外沿之间的间距大于导向板横向宽度的预设差值d在1~30mm之内。
可选的,所述动力车架下部两侧、走行轮沿走行方向的前侧或/和后侧向外设有稳定轮,所述稳定轮与轨道梁两侧内壁下部邻近或接触,任一侧稳定轮外沿与轨道梁内壁之间的预设间距大于两侧导向轮相邻外沿之间的间距大于导向板横向宽度的预设差值d的一半,稳定轮在动力车架下部处于侧向突出部位。
可选的,所述轨道梁的上部、导向轮和轨道梁内壁之间设置导电轨,导电轨通过动力车架上的受流器与动力系统连接。
可选的,所述动力车架上部设置用于钳制导向板的驻车装置。
可选的,所述轨道梁为箱式结构、型钢组合结构或桁架组合结构的一种,所述走行轮是胶轮。
可选的,所述轨道梁是型钢组合结构,由左右型钢主梁、上横梁及中部导向板组成;左右型钢主梁上下均有开口,上开口由上横梁连接左右型钢主梁后成为梁上断续开口;在梁上断续开口上设置防护盖,防护盖左右侧设有通风口及溢水槽。
可选的,所述动力车架在走行轮沿走行方向的前或/和后位置安装与载具顶部的承载装置衔接的弹性承载体。
可选的,所述动力车架的弹性承载体为倒t型结构,倒t型结构的下承载梁两端与载具的承载装置的两承载边梁分别弹性连接,同时相对滑动。
可选的,承载所述载具的动力车架由两个轮对整体联结组成单个转向架、或两个双轴的转向架、或两个单轴独立轮对转向架构成;轮对由轴旁电机或轴电机驱动,电机驱动控制分别采用架控、轴控、轮控方式或其中的组合方式进行。
可选的,承载所述载具的动力车架由两个单轴独立轮对转向架分别构成;在两个独立轮对的中心设有转轴,两个转轴由纵梁铰链,纵梁上设置电控箱;独立轮对前后分别设置的两个弹性承载体下部连接有稳固梁,所述稳固梁的两承载销的轴心连线中心与载具的承载装置的承载横梁中心铰链连接,所述承载横梁向下对应转轴。
本申请提供了一种悬挂式单轨系统。所述单轨系统包括轨道梁、动力车架、载具和支撑装置等结构,所述支撑装置支撑轨道梁,所述轨道梁下部开口,动力车架位于轨道梁内。所述轨道梁在其内部的上部设有导向板,所述动力车架在上部的两侧边分别设有与导向板相匹配的两组导向轮,所述导向轮与导向板贴紧接触或相邻,在动力车架转弯时,通过导向板和导向轮的作用为动力车架提供向心力并使动力车架保持高稳定性。相比现有单轨系统,本申请所述单轨系统整体结构更加紧凑,单位长度的轨道梁重量下降;另外,得益于动力车架运行的高稳定性和导向作用方式,本系统对轨道梁的精度要求大幅降低,因此,相比于常规悬挂式单轨系统,本申请所述悬挂式单轨系统的动力车架运行更加平稳,并且可以在提升运行稳定性的同时大幅降低该悬挂式单轨系统的总体工程成本,具备很好的推广价值。
附图说明
图1为所述悬挂式单轨系统垂直走行方向的截面结构示意图;
图2为所述轨道梁的一种截面结构示意图;
图3为所述动力车架在轨道梁内平行走行方向视角的结构示意图;
图4为所述动力车架与载具垂的立体结构示意图;
图5为图4中a处放大图;
图6为所述动力车架的部分透视结构示意图;
图7为带有稳定轮的动力车架示意图;
图8为另一种悬挂式单轨系统的部分结构示意图;
图9为图8中b处的放大图;
图10为设有防护盖的轨道梁结构示意图;
图11为所述防护盖的立体结构示意图;
图12为所述防护盖的截面结构示意图;
图13为所述弹性挂载装置的立体结构示意图;
图14为所述转向架的部分结构示意图;
图15为所述载具的承载装置示意图;
图16为所述动力车架与载具弹性连接的立体结构示意图;
图17为图16中c处放大图;
图18为转向架部分结构的底部视角结构示意图;
图19为载具的另一种载具承载装置的结构示意图;
图20为所述稳固梁、传动销与承载横梁的结构示意图;
图21为实施例7中动力车架与载具弹性连接的立体结构示意图;
图22为图21中d处放大图;
图23为动力车架中前后两独立轮对转向架的底部视角示意图;
图24为所述防撞装置垂直走行方向的结构示意图;
图25为所述防撞装置的立体结构示意图;
图26为图25中e处放大图。
图中标号说明:
1-轨道梁、11-主梁、11a-型钢主梁、111-走行面、112-内壁、12-横梁、12a-上横梁、121-梁上断续开口、13-导向板、13a-中部导向板、14-导电轨、15-防护盖、151-通风口、152溢水槽、2-动力车架、21-承载箱、211-轴电机、212-弹簧安装结构、213-转轴、214-纵梁、22-走行轮、23-导向轮、24-受流器、25-稳定轮、26-挂载装置、27-夹紧装置、28-前端防撞缓冲装置、29-后端防撞缓冲装置、261-弹簧、262-承载销、263-下承载梁、264-稳固梁、265-传动销、27-夹紧装置、3-载具、31-车厢、32-承载装置、321-承载边梁、322-承载横梁、33-电控箱、4-支撑装置。
具体实施方式
下面结合附图与具体实施方式对本方案进行阐述。
本申请提供了一种悬挂式单轨系统,所述悬挂式单轨系统包括轨道梁1和动力车架2,还包括与之匹配的载具3和支撑装置4,所述动力车架2和载具3可以设置多个。其中,所述载具3指的是与动力车架2匹配的运载装置,可以是类似于轿厢、货厢或者托架的结构设置,其中,轿厢和货厢分别供人乘坐和运载货物,托架则可以用于直接吊挂集装箱。总的来说,所述载具3应当具备车厢31和用于连接动力车架2的承载装置32,相应的,所述动力车架2底部设有挂载装置26。所述支撑装置4为轨道梁1的支撑结构设置,比如墩柱或其他类似结构,所述支撑装置4支撑轨道梁1。显然,由于本申请讨论的主体是悬挂式单轨系统,在上述设置下,所述载具3设置吊挂于动力车架2的下方,并且载具3整体悬挂于轨道梁1的下方。本申请中,所述支撑装置4为现有技术的常规设置,本领域普通技术人员可以结合本领域公知常识并参照本申请其他内容对其进行任意设置,此处不再赘述。
所述轨道梁1至少下部开口,其内部为贯通的通道,该通道即构成动力车架2的走行空间,所述动力车架2沿着该走行空间行走。所述轨道梁1为箱式结构、型钢组合结构或桁架组合结构,总的来说,所述轨道梁1至少应当具备主梁11和横梁12,所述横梁12至少构成轨道梁1的顶部,所述主梁11至少构成轨道梁1的两侧和底部,所述轨道梁1的内部两侧底面构成走行面111,即主梁11的内部两侧底面构成所述走行面111,所述走行面111为动力车架2提供支撑并供动力车架2的走行轮22行走。
所述动力车架2至少包括承载箱21、走行轮22和挂载装置26;所述承载箱21为动力车架2的主体结构,所述承载箱21为其他结构提供连接支撑;所述走行轮22设置于走行面111上,并且沿走行面111行走,同时,通过该方式,动力车架2获得轨道梁1的支撑。所述挂载装置26吊挂载具3。另外,出于单轨系统轨道梁的特性,所述轨道梁1的宽度小于载具3的宽度。
特别的,在本申请所述的悬挂式单轨系统中,所述轨道梁1的内部上方,且两侧走行轮22之间设有导向板13,即所述导向板13设于横梁12的底面,所述导向板13可以是钢材或其它材料,其应当具备可以承受动力车架2转弯离心力的强度。所述动力车架2的上部左右两侧设有导向轮23,在上述设置下,两侧导向轮23设于导向板13的左右两侧,并且,两侧导向轮23接触或邻近导向板13并沿导向板13行走。也就是说两侧导向轮23可以直接夹持住导向板13,也可以是与导向板13保持一个较近的距离,虽然此处并未说明该距离的具体数值,但是应当容易理解的是,根据不同规格的轨道梁1和动力车架2的实际应用场景,本领域普通技术人员在理解本申请所述悬挂式单轨系统的宗旨后,容易想到该距离的适宜应用范围。一种优选的实施方式是,两侧导向轮23与导向板13直接接触,为了在动力车架运行时进一步保持该种状态,所述动力车架2设置有夹紧装置27,在夹紧装置27作用下,导向轮23向导向板13施以正压力,即两侧导向轮23对导向板13形成夹持效果,所述夹紧装置27可以是液压装置、弹性装置或电磁装置等现有装置。该种实施方式可以使导向轮23牢牢贴紧导向板13,使动力车架2运行更加稳定,但是其结构要稍显复杂,成本更高,本领域普通技术人员可以根据实际应用场景自主选择导向轮23与导向板13的设置方式。另外,我们还可以设置导向轮23带驱动装置或不带驱动装置,在带驱动装置的情况下,导向轮23可以驱动动力车架2行走,特别是在爬坡路段,可以辅助提升动力车架2的爬坡力,该技术手段会增加动力车架2的结构复杂性和成本,因此,应当在爬坡线路较多的悬挂式单轨系统中优选设置
通过上述方式,导向轮23无需伸出在走行轮22的两侧,因此,动力车架2的整体宽度得以减小,结构更加紧凑,作为匹配的,所述轨道梁1的宽度得以减小,在单轨系统具备一定规模的情况下,轨道梁1宽度的减小可以明显降低轨道梁1整体的材料成本。
需要说明的是,在未另有说明的情况下,本申请中,诸如“两侧”、“左右”等描述,其是以动力车架2面向或背向走行方向时作为参考,比如,两侧指的是动力车架2行走时,面向行车方向的两侧,或者说人员面对行车方向的左右两侧。
为便于本领域普通技术人员理解,下面通过具体实施例进一步说明本申请所述悬挂式单轨系统的几种具体实施方式及技术效果。
实施例1
如图1-图6所示,本实施例所述悬挂式单轨系统包括轨道梁1、动力车架2、载具3和支撑装置4,其中,支撑装置4为现有技术的常规设置,本实施例中对其不做具体说明。
所述轨道梁1为箱式结构,具体由主梁11、横梁12、导向板13和导电轨14组成,所述主梁11组成轨道梁1的侧面和底部,所述横梁12组成轨道梁1的顶部,所述轨道梁1整体为下部开口的箱式结构。两侧主梁11内部底面构成供动力车架2行走的走行面111,所述轨道梁1的内部为贯通的通道,所述动力车架2在该通道内行走。
所述轨道梁1底部开口,供动力车架2穿过并吊挂载具3。所述轨道梁1的内部上方、并且在动力车架2的两侧走行轮22之间固定设置设有导向板13,为保证强度,所述导向板13与横梁12为相同材料,并且,所述导向板13焊接于横梁12底面的中部。
所述动力车架2包括承载箱21、走行轮22、导向轮23、受流器24和挂载装置26。所述承载箱21为动力车架的主体结构,其在走行轮22之间设有轴电机211,所述轴电机211轴向驱动走行轮22行走,所述走行轮22为胶轮并设于承载箱21的两侧,两走行轮22构成轮对,两侧走行轮22分别与同侧走行面111接触,所述动力车架2在走行面111上行走并获得支撑。所述导向轮23设于承载箱21上方的两侧位置,并且,两侧导向轮23整体位于两侧走行轮22之间,因此,导向轮23的设置不会影响动力车架2的整体宽度。所述挂载装置26为动力车架的底部结构,用于连接并吊挂载具3;本实施例中,所述挂载装置26为现有常规的挂载结构设置。所述承载箱21、走行轮22或者说轮对、导向轮23等结构构成了动力车架2的转向架。所述动力车架2可以是:由两个轮对整体联结组成单个转向架、两个双轴的转向架、两个单轴独立轮对转向架构成;轮对由轴旁电机或轴电机驱动,电机驱动控制分别采用架控、轴控、轮控方式或其中的组合方式进行。本实施例中,所述走行轮22为独立轮对,并且设有前后两组,相应的转向架设有两组,本实施例所述动力车架2由两个单轴独立轮对转向架分别构成。
所述导电轨14分别设于轨道梁1的上部两侧、且两侧导向轮23与轨道梁1的内壁112之间,在竖直方向上,所述导电轨14位于两侧走行轮22的外沿之间。作为匹配的,所述动力车架2两侧设有受流器24,两侧导电轨14分别与同侧受流器24连接。所述导电轨14通过受流器24与动力车架2连接并对其供电。
本实施例中,所述导向板13位于动力车架2的两侧导向轮23之间并同时与两侧导向轮23接触。所述动力车架2设有夹紧装置27,所述夹紧装置27驱使两侧导向轮23向内侧夹紧导向板13。在所述夹紧装置27的作用下,在动力车架2直线运行和转弯时,两侧导向轮23都可以紧紧地贴紧于导向板13两侧,因此,动力车架2整体运行稳定,不会出现左右晃动的情况。本实施例中,所述夹紧装置27为液压装置。
通过上述设置,本实施例中,所述动力车架2转向时,由转弯内侧向的导向轮23进一步压迫导向板13为动力车架2提供向心力,如前所述,由于两侧导向轮23与导向板13在垂直走行方向上保持相对静止,因此可以显著提升动力车架2过弯的稳定性。
本实施例所述悬挂式单轨系统的轨道梁1内部上方设置导向板13,并在动力车架2对应设置有导向轮23,通过该种设置,动力车架2可以沿导向板13始终保持横向稳定。相比之下,现有常规悬挂式单轨系统将导向轮设置于依赖于轨道梁两侧的导向板或导向面进行转向,因此,不可避免的是,为了避免动力车架在运行和转弯时左右晃动,轨道梁两侧导向板或导向面的间距必须控制在一个适宜的范围中,也就是说,该种设置下,其必须要求轨道梁的内部两侧宽度控制在一个较小的误差范围内,显然,这将明显提升轨道梁的施工难度,进而显著提高工程造价;另外重要的一点是,该种常规设置下,导向轮两侧必须相对走行轮向两侧突出,显然,该种结构一定程度上增加了轨道梁的宽度,即增加了轨道线路单位长度的轨道梁重量,大幅提高工程成本,并对支撑装置提出更高的要求。
总的来说,本实施例所述悬挂式单轨系统中,动力车架2转弯更加平稳,对于轨道梁1两侧宽度的误差容忍度更高,并且轨道梁1宽度可以做得更窄,整体结构更加紧凑,且施工难度降低,可以显著降低该悬挂式单轨系统的整体造价。
实施例2
在实施例1的基础上,作为区别的,本实施例所述悬挂式单轨系统中,所述动力车架未设置有夹紧装置27,因此动力车架两侧的导向轮23不能主动夹紧中间的导向板13。
上述设置下,本实施例所述动力车架2两侧导向轮23之间的间距略大于导向板13的横向宽度;并且,考虑到动力车架2转弯时的稳定性,我们要求两者之差应尽可能小;另外,综合考虑到导向板13的横向宽度误差和两侧导向轮23的间距误差,本实施例中,我们设定所述动力车架2两侧导向轮23相邻外沿的间距大于导向板13的横向宽度的预设差值d在1-30mm之内。
通过上述设置,本实施例所述导向轮23之间的间距以及导向板13横向宽度的总体误差在易于实现的范围内,便于实际施工。并且,可以预见的是,本实施例所述悬挂式单轨系统在运行和转弯时,其左右晃动的幅度控制在最大30mm以内,其左右晃动程度属于不易感的程度。实际上,在具体设计该差值时,应当综合考虑到该线路的具体工况与用途,比如,对于载人线路,尤其是观光线路来说,所述预设差值d可以预设控制在1-5mm之内,该设置虽然相对提高了工程成本,但是考虑到乘员感受与安全性,其仍然是一种较为优选的设置,本领域普通技术人员可以根据实际情况对其进行灵活设置,此处不再赘述。
相比实施例1所述悬挂式单轨系统,本实施例所述悬挂式单轨系统的动力车架2的结构相对更加简单,可靠度较高,但是其动力车架2运行的稳定性有所下降,不过仍处于较高水平。
本实施例中,其他未特殊说明的部分皆与实施例1相同。
实施例3
如图7所示,在实施例2的基础上,作为区别的,本实施例所述悬挂式单轨系统中,所述动力车架2的下部两侧、且走行轮22沿走行方向的前侧和后侧设有稳定轮25,所述稳定轮25与轨道梁23两侧内壁112的下部邻近,其中,我们设置任一侧稳定轮25与内壁112之间的预设间距不小于前述预设差值d的一半。实际上,由于不可避免的误差,我们应主动设置任一侧稳定轮25与轨道梁1的内壁112之间的预设间距大于预设差值d的一半,但是该差值也须尽可能的小。
通过上述设置,本实施例所述悬挂式单轨系统的稳定性较实施例2所述悬挂式单轨系统得到进一步提升。具体的,本实施例中,当动力车架2转弯或行进时,当动力车架2向一侧轻微滑移,此时,由于导向轮23与导向板13之间的间距小于预设间距d,所述导向轮23预先接触到同侧的导向板13并通过压迫导向板13使动力车架2获得足够的转向向心力,之后,在惯性作用下,动力车架2的下部将会产生微小的摆动,使稳定轮25与同侧轨道梁1内壁112接触获得支撑,此时,动力车架2趋于稳定,易于想到的,动力车架2从导向轮23接触导向板13到动力车架2完全稳定的摆动幅度和摆动时间与该侧稳定轮25与轨道梁1内壁112之间的预设间距大于预设差值d一半的差值x正相关,因此,考虑到动力车架2运行的稳定性和施工难度,我们应将该差值x控制在一个易于达成且较小的范围,比如5-10mm。
通过上述稳定轮25以及相应设置,本实施例所述悬挂式单轨系统在实施例2的基础上进一步增加了动力车架2运行的稳定性,并且其结构较为简单,实施较为容易,额外设置成本较低。另外,考虑到实施例1中,导向轮23夹紧导向板13后,动力车架2也仍然会不可避免地存在绕导向轮23与导向板13的夹紧点轻微摆动的问题,因此,本实施例所述稳定轮25的设置同样适用于实施例1所述悬挂式单轨系统。
本实施例中,其他未特殊说明的部分皆与实施例2相同。
实施例4
在实施例3的基础上,作为区别的,本实施例所述动力车架的上部设置有驻车装置,所述驻车装置同样为夹持结构,我们设置所述驻车装置可以钳制或松开导向板13,在动力车架2驻车时,可以通过该驻车装置钳制夹紧导向板13以充当手刹的结构。并且,一种更加优选的方式是,所述驻车装置采用与导向轮23同样的夹紧装置27,即本实施例中,所述夹紧装置27同时驱动导向轮23和驻车装置夹紧导向板13,其仅有区别在于:驻车装置为制动性夹紧,并且,所述驻车装置设置为驻车时夹紧,在行车时不产生钳制效果。
本实施例中将动力车架的驻车装置与导向轮23、导向板13结合,进一步简化了动力车架2的结构,可以一定程度上降低生产制造成本,并使动力车架的结构2更加紧凑。
本实施例中,其他未特殊说明的部分皆与实施例1相同。
实施例5
如图8、图9所示,在实施例1的基础上,作为区别的,本实施例中,所述轨道梁为型钢组合结构,具体由左右型钢主梁11a、上横梁12a、中部导向板13a以及导电轨14组成。其中,所述左右型钢主梁11a构成轨道梁1的主体结构,其作为轨道梁的侧面、顶部和部分顶部;所述上横梁12a为非连续梁,即所述上横梁12a为若干条形型钢组成,所述上横梁12a连接左右型钢主梁11a,所述上横梁12a组成轨道梁1的部分顶部。所述左右型钢主梁11a内部左右两侧底面构成了供动力车架行走的走行面111,所述轨道梁1的内部为贯通的通道,所述动力车架2在该通道内行走。
本实施例中,所述中部导向板13a设于上横梁12a的底部,其形状伸入到走行空间内。
通过上述设置,本实施例所述悬挂式单轨系统中,轨道线路单位长度的轨道梁1钢材用量显著下降,可以显著降低生产制造成本。
如图8-图12所示,作为进一步优化的,本实施例所述悬挂式单轨系统在轨道梁上方还设有防护盖15。
具体的,所述左右型钢主梁11a上部开口且通过上横梁12a连接,因此,左右型钢主梁11a的上部与上横梁12a形成若干梁上断续开口121;在下雨时,雨水将会进入到轨道梁1内部,对轨道梁1和动力车架2造成锈蚀,尤其在雨水充足的南方,容易造成轨道梁1或动力车架2的锈蚀损坏。为解决上述问题,本实施例中在所述梁上断续开口121上方设有防护盖15,所述防护盖15对轨道梁1内部和动力车架2形成保护。显然,所述防护盖15可以采用价格更低的塑料制品,因此整体上仍然可以降低所述悬挂式单轨系统的工程成本。另外,所述防护盖15左右侧还设置通风口151及溢水槽152。
本实施例中,其他未特殊说明的部分皆与实施例1相同。
实施例6
如图13-图17所示,在实施例3的基础上,作为区别的,本实施例所述动力车架2的挂载装置26为弹性承载体,所述弹性承载体设于动力车架2的走行轮22沿走行方向的前侧和后侧位置。作为匹配的,所述载具3的顶部设有承载装置32,所述弹性承载体与承载装置32衔接。
其中,所述弹性承载体为倒t型结构,包括弹簧261、承载销262和下承载梁263,所述弹簧261和下承载梁263分设于承载销262的上端和下端;作为匹配的,所述转向架上设有弹簧安装结构212,所述弹簧261通过弹簧安装结构212与转向架弹性连接。另外,所述承载装置32设有平行走行方向的两侧承载边梁321,所述下承载梁263的两端与两承载边梁321分别弹性邻接,并且可以产生适宜的相对滑动,即下承载梁263与承载边梁321的连接位置处设有弹性件,在垂直运行方向的水平方向上可以产生相对轻微的滑动。
本实施例中,动力车架2的弹性承载体和载具3顶部的承载装置32的设置可以进一步缓冲动力车架2的晃动对载具3的影响,具体的,在转弯或直行时,动力车架2产生侧向的滑动,此时,由于动力车架2与载具3之间的弹性承载体与承载装置32的弹性和滑动连接方式,传导到载具3的侧向摆动的动能得以部分吸收并缓慢释放,因此可以一定程度上提升载具3的运行稳定性,并且其结构与常规动力车架2与载具3连接结构的复杂性相当,不会造成成本的提升。
本实施例中,其他未特殊说明的部分皆与实施例3相同。
实施例7
如图18-图23所示,在实施例6的基础上,作为进一步优化的,本实施例中,所述动力车架2前后独立轮对中心位置分别设有转轴213。动力车架2中,前后独立轮对的转轴213由纵梁214连接,考虑到前后转向架转动时的延迟性,所述转轴213与纵梁214的连接方式为铰接式连接,纵梁214可以绕转轴213做一定程度的旋转。所述纵梁214将动力车架2的前后两组独立轮对转向架连接为一体,显著提升了动力车架2的整体结构强度和稳定性,并且不会对前后独立轮对的运动造成影响。本实施例中,所述电控箱33设于纵梁214上,最大化空间利用。
另外,本实施例所述动力车架的同一独立轮对转向架中,独立轮对前后两个弹性承载体下部连接有稳固梁264,所述稳固梁的两承载销262的轴心连线中心与载具3的承载装置32的承载横梁322中心铰链连接,所述承载横梁322向下对应转轴213。通过该设置,所述转向架或者说动力车架2的整体强度得到明显增强,可以避免长时间运行下,同一转向架前后弹性承载体产生位移造成运行不稳定,甚至影响后续挂装载具3。
本实施例通过稳固梁264、纵梁214等设置显著增强了动力车架2的整体结构强度和刚度,有利于动力车架2在长期运行下保持结构稳定,并且,其结构较为简单,对于成本的影响较小。
本实施例中,其他未特殊说明的部分皆与实施例6相同。
实施例8
如图24-图26所示,在实施例7的基础上,作为区别的,本实施例中,所述动力车架2中,在其运行方向的前端设有前端防撞缓冲装置28,在其后端设有后端防撞缓冲装置29,所述前端防撞缓冲装置28和后端防撞缓冲装置29在竖直方向上突出于载具3之外,因此,当载有载具3的动力车架2相碰时,在上述设置下,总是预先由前端防撞缓冲装置28与另一动力车架2的后端防撞缓冲装置29接触碰撞,因此在机械结构上实现绝对的防撞或者缓冲作用。
本实施例中,其他未特殊说明的部分皆与实施例7相同。
实施例9
在实施例8的基础上,作为进一步优化的,所述前端防撞缓冲装置28和后端防撞缓冲装置29还设有活动连接结构,所述活动连接结构为球形连接结构,可以满足前后两动力车架2处于不同的运动状态。该设置下,所述动力车架2可以通过前端防撞缓冲装置28和后端防撞缓冲装置29进行连接,并且可以相对运动。也就是说,本实施例中,将前后动力车架2的防撞装置和连接装置结合为一体,可以一定程度上简化动力车架的整体结构,降低生产成本。
本实施例中,其他未特殊说明的部分皆与实施例8相同。
需要说明的是,本申请所述悬挂式单轨系统的各实施例中,若包括电控箱33等常规设置未有具体说明,即代表该部分结构为现有技术中的常规设置,本领域普通技术人员参考上述内容并结合本领域公知常识容易想到其实施方式,因此,出于简明扼要的目的,本申请对该部分未做具体说明,但是其仍然可以构成一个清楚完整的技术方案,本领域普通技术人员在不做出创造性劳动的情况下仍然可以对其进行实施。
本申请说明书中各个实施例之间相同相似的部分互相参见即可。尤其,对于系统及实施例而言,由于其中的方法基本相似于方法的实施例,所以描述得比较简单,相关之处参见方法实施例中的说明即可。
需要说明的是,在本文中,诸如术语“包括”、“包含”或者其任何其他变体意在涵盖非排他性的包含,从而使得包括一系列要素的过程、方法、物品或者设备不仅包括那些要素,而且还包括没有明确列出的其他要素,或者是还包括为这种过程、方法、物品或者设备所固有的要素。在没有更多限制的情况下,由语句“包括一个......”限定的要素,并不排除在包括所述要素的过程、方法、物品或者设备中还存在另外的相同要素。
当然,上述说明也并不仅限于上述举例,本申请未经描述的技术特征可以通过或采用现有技术实现,在此不再赘述;以上实施例及附图仅用于说明本申请的技术方案并非是对本申请的限制,如来替代,本申请仅结合并参照优选的实施方式进行了详细说明,本领域的普通技术人员应当理解,本技术领域的普通技术人员在本申请的实质范围内所做出的变化、改型、添加或替换都不脱离本申请的宗旨,也应属于本申请的权利要求保护范围。
起点商标作为专业知识产权交易平台,可以帮助大家解决很多问题,如果大家想要了解更多知产交易信息请点击 【在线咨询】或添加微信 【19522093243】与客服一对一沟通,为大家解决相关问题。
此文章来源于网络,如有侵权,请联系删除


