一种抗扎防爆车轮的制作方法



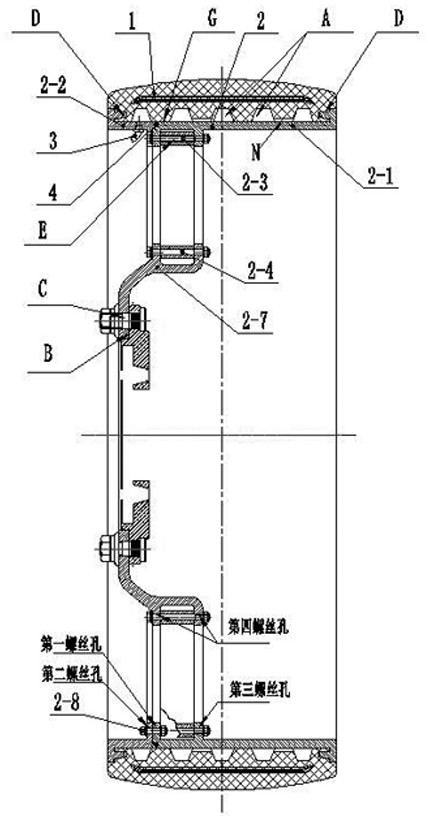
本实用新型属于车辆车轮领域,涉及一种抗扎防爆车轮,是采用轮辋板弹簧减震与气压减震相结合的技术构思。
背景技术:
目前,汽车用轮胎大都是充气轮胎,易被扎胎漏气,容易造车翻车;针对此,也出现了非充气防爆轮胎,在橡胶轮胎中夹钢丝,二者结合在一起,依靠钢丝变形减振,再由轮辋辐条活动式随钢丝变形而变形解决轮胎减振问题,轮胎较厚、不易散热,因此在试车中发现它由于发热过快,一个轮子只有几千公里的使用寿命,这种轮胎损坏后不能更换。
公开号为cn107599737a的实用新型专利申请,公开了非充气轮胎轮辋浮动减振车轮,由浮动式减振轮辋、非充气轮胎组成,浮动式减振轮辋设置侧向及径向复合支撑单元的结构(径向弹性支撑和侧向缓冲支撑);侧向缓冲支撑由对称设置在径向弹性支撑两侧的侧向缓冲支撑单元组成,径向弹性支撑的是采用有径向压簧、拉簧的结合,非充气轮胎套装在浮动式减振轮辋的外圆上结合在一起。本实用新型通过浮动式减振轮辋设置,提供好的减振效果,散热性好,轮胎使用寿命长;当轮胎磨损后,能单独拆卸并换装。
上述非充气轮胎轮辋浮动减振车轮的侧向及径向复合支撑单元结构复杂,涉及的零件多,布局复杂,制造成本高。
技术实现要素:
为了使车轮造价降低和轮胎散热性更好,轮胎一旦扎胎漏气仍能保证车轮外径不变汽车正常行驶,保证良好的减振效果,并能避免车轮在驱动做功时由于轮辐外环转速与轮辐内环转速之间的角速度相同产生前后磋移,和驱动效率损失。保证轮胎的使用寿命长,轮胎可更换,本实用新型提出一种抗扎防爆车轮。
为此,本实用新型的技术方案为:一种抗扎防爆车轮,由轮胎、轮辋组成,其特征在于:轮辋包括轮辐右外环、轮辐左外环、轮辐内环、多个八字形减振支撑单元;
轮辋中的轮辐右外环、轮辐左外环二者固定在一起形成轮辐外环,轮辐右外环、轮辐左外环的接合面处设有密封环;
多个八字形减振支撑单元沿圆周方向均布设置在轮辐内环与轮辐右外环之间,每个八字形减振支撑单元由2个对称设置的弓形板弹簧支撑组合体组成;
轮辐左外环的外圆面是轮胎左边内表面支撑面,轮辐左外环的外圆面外侧设有外法兰,外法兰的内侧面上沿圆周方向设有多个锥钉;轮辐左外环的内圆面内侧设有内法兰,内法兰设有多个第一螺栓孔;轮辐右外环的外圆面是轮胎右边内表面支撑面,轮辐右外环的外圆面外侧设有外法兰,外法兰的内侧面上沿圆周方向设有多个锥钉;轮辐右外环与轮辐左外环对接处的内圆上设有法兰盘,在法兰盘上开有安装槽,安装槽的槽口两侧壁上沿圆周方向设有与第一螺栓孔对接的第二螺栓安装孔和连接弓形板弹簧支撑组合体的第三螺栓孔;轮辐右外环、轮辐左外环二者对接,通过第一螺栓紧配装穿过第一螺栓孔、第二螺栓安装孔,把轮辐右外环、轮辐左外环紧固连接一刚体成为轮辐外环,它的外表面形成轮胎支撑面;轮辐内环的外圆面上设有安装槽,安装槽的槽口两侧壁上沿圆周方向设有连接弓形板弹簧支撑组合体的第四螺栓孔;
所述弓形板弹簧支撑组合体包括第一弓形板弹簧、第二弓形板弹簧,第一弓形板弹簧及第二弓形板弹簧的两头分别设有捲耳,第一弓形板弹簧、第二弓形板弹簧对称设置,并保证第一弓形板弹簧的内表面与第二弓形板弹簧的内表面相对;第一弓形板弹簧及第二弓形板弹簧的一头捲耳装入轮辐右外环的法兰盘的安装槽内由第三螺栓穿过第三螺栓孔和一头捲耳的圆孔无间隙能转动地定位连接,第一弓形板弹簧及第二弓形板弹簧的另一头捲耳装入轮辐内环的安装槽内由第四螺栓无间隙转动穿过第四螺栓孔定位连接,第一弓形板弹簧、第二弓形板弹簧相对设置形成弓形板弹簧支撑组合体,第一弓形板弹簧、第二弓形板弹簧相对设置形成椭缺形状(一个椭圆形两头缺陷,本实用新型称之为椭缺形);由两个组合体对称设置呈八字形构成减振支撑单元;
在轮胎的内壁上环向布有多个凹形充气环槽,在多个充气环槽之间的凸起环壁上设有多个横向小气槽,使多个凹形充气环槽连通;轮胎的内壁凸起环壁与轮辐支撑面紧贴在一起,并通过轮辐左外环及轮辐右外环的多个销钉插入轮胎两侧周向多个定位孔中,使轮胎固定在轮辐外环上;一个充气咀设置在轮辐左外环的内圆面上,充气咀与一个凹形充气环槽连通。
对本实用新型的进一步限定:所述八字形减振支撑单元有多个,均布设置在轮辐右外环与轮辐内环之间;这种结构易于加工,结构简单,便于装配。
对本实用新型的进一步限定:轮胎设有多个凹形环向充气槽是为了达到在凹形槽底部轮胎断面厚度可以做到常规充气轮胎的厚度相同,散热性好,能保持常用的轮胎使用寿命,轮胎的内表面凸起的部分,完成扎胎无气压时,车轮外径尺寸保持不变,可正常行驶;多个凸起环壁上的横向小气槽是交错设置的,这种结构不破坏凸起环壁及轮胎的强度,又能达到连通的目的。
对本实用新型的进一步限定:所述的轮胎采用超薄设置,它的断面厚度在40-50mm范围。
本实用新型的有益效果是:本实用新型中轮胎多个充气凹环槽的设置结构,轮胎一旦扎胎漏气,由充气环槽之间的凸起环壁支撑,车轮外径尺寸保持不变仍能保证汽车正常行驶,达到抗扎防爆防弹的目的;通过在轮辐外环与轮辐内环之间设置八字形板弹簧支撑单元,提供好的减振效果,车轮在旋转时受到地面阻力和反阻力时,由八字形支撑方式来阻止轮胎前后磋移,保证主动转速与被动转速的角转速相同,轮胎无移位磨损,无轮辐内环的转速与轮辐外环转速之间的角转速差,使得角转速相同。保证驱动效率不受损失和轮胎的使用寿命长,满足行车安全性。
附图说明
图1是本实用新型的主视图。
图2是本实用新型的左视图。
图3是本实用新型中轮胎的内壁上充气环槽及横向小气槽的结构示意图。
图4是本实用新型中轮胎、轮辐内环、轮辐外环之间的安装放大示意图。
图5是本实用新型中八字形板弹簧支撑单元(第一弓形板弹簧及第二弓形板弹簧)的弹性变形与轮辐内环、轮辐外环(轮辐右外环)之间的位移及受力分析图。
图6是设定第一弓形板弹簧、第二弓形板弹簧上、下连接点构成矩形的位移及受力分析图。
具体实施方式
结合图1、图2、图3及图4所示,本实用新型抗扎防爆车轮,包括轮胎1、轮辋总成2组成,轮辋包括密封环4、轮辐右外环2-1、轮辐左外环2-2、第三螺栓2-3、第四螺栓2-4、第一弓形板弹簧2-5、第二弓形板弹簧2-6、轮辐内环2-7,轮辐内环2-7的内孔腔设有内法兰,在内法兰周向设有与车桥对接的连接孔,见图1中标记b、c所示,轮辐右外环2-1、轮辐左外环2-2二者固定在一起形成轮辐外环,轮辐右外环2-2、轮辐左外环2-3的接合面处设有密封环2-1;轮辐左外环2-3的外圆面是轮胎左边内表面支撑面,轮辐左外环的外圆面外侧设有外法兰,外法兰上沿圆周方向设有多个锥钉,见图1中(左边)标记d所示;轮辐左外环的内圆面内侧设有内法兰,内法兰设有多个第一螺栓孔;轮辐右外环2-1的外圆面是轮胎右边内表面支撑面,轮辐右外环2-1的外圆面外侧设有外法兰,外法兰上沿圆周方向设有多个锥钉,见图1中(右边)标记d所示;轮辐右外环的内圆环面内侧设有法兰盘,在法兰盘上开有安装槽,槽口的两侧壁上沿圆周方向设有第二螺栓安装孔和第三螺栓安装孔;轮辐右外环2-1、轮辐左外环2-2二者对接,通过第一螺栓2-8紧压无间隙穿过第一螺栓孔、第二螺栓安装孔把轮辐右外环2-1、轮辐左外环2-2固定成一刚体为轮辐外环,它的外表面形成轮胎支撑面;在轮辐内环2-7与轮辐右外环2-1之间沿圆周方向均布设置有多个弓形板弹簧支撑组合体,所述弓形板弹簧支撑组合体包括第一弓形板弹簧2-5、第二弓形板弹簧2-6,它们的各自两头为捲耳圆孔;第一弓形板弹簧2-5、第二弓形板弹簧2-6对称设置,并保证第一弓形板弹簧的内表面与第二弓形板弹簧的内表面相对;第一弓形板弹簧2-5及第二弓形板弹簧2-6的一头捲耳圆孔装进轮辐右外环2-1的法兰盘的安装槽(深宽槽)内由第三螺栓与其无间隙能转动地定位连接,第一弓形板弹簧2-5及第二弓形板弹簧2-6的另一头捲耳圆孔装进轮辐内环安装槽内由第四螺栓2-4无间隙能转动地定位连接,形成一个弓形板弹簧支撑组合体;由两个弓形板弹簧支撑组合体对称设置呈八字形减震支撑单元;多个八字形减振支撑单元沿圆周方向均布设置在轮辐内环与轮辐右外环之间;
所述的轮胎1采用超薄设置,它的断面厚度在40-50mm范围,在轮胎的内壁上环向布有多个凹形充气槽,见图1中标记a所示,在多个充气凹形环槽之间的凸起环壁上设有横向多个交错布置小气槽,见图1中标记n所示,使多个环向凹形充气槽连通;轮胎的凸起环壁与轮辐外表面紧贴在一起,轮胎1的凸起环壁见图1中标记g示,并通过轮辐左外环2-2及轮辐右外环2-1的多个销钉插入轮胎两侧周向多个定位孔中,见图1中标记d所示,使轮胎1固定在轮辐外环上;一个充气咀3设置在轮辐左外环的内圆面上,充气咀3与其中一个充气环槽连通。
如图1、图2所示,弓形板弹簧支撑组合体中,第一弓形板弹簧2-5及第二弓形板弹簧2-6的一头捲耳装入轮辐右外环2-1的法兰盘安装槽内由第三螺栓2-3无间隙能转动地定位连接,第一弓形板弹簧2-5及第二弓形板弹簧2-6的另一头捲耳圆孔装入轮辐内环2-7的外环形安装槽内,由第四螺栓2-4无间隙能转动地定位连接,具体是通过下面的结构体现的:轮辐右外环2-1的内法兰盘安装槽(深宽槽)的壁面上圆周方向设有弓形板弹簧组合体的第三螺栓安装孔,第四螺栓安装孔设置在轮辐内环2-7外表面法兰盘安装槽(深宽槽)的槽壁上,将第一、第二弓形板弹簧2-5、2-6的两头捲耳分别装入轮辐右外环2-1和内环2-7的安装槽(深宽槽)内,分别将第三螺栓2-3和第四螺栓2-4将其无间隙能转动地定位连接;由两个弓形板弹簧支撑组合体对称布置呈八字形定位设置,完成轮辐内、外环2-1、2-2、2-7在受外力作用时,它们完成两者间的角转速保持相等、定位和支撑传力功能;两个弓形板弹簧支撑组合体对称布置成八字形减振支撑单元,联合完成支撑、减震、定位传力的单元;由多个八字形减震支撑传力单元,均布在轮辐右外环2-1,与轮辐内环2-7之间,构成了基于多个第一、第二弓形板弹簧2-5、2-6的减震定位传递扭矩的轮辋总成;所述的八字形减振支撑单元的数量为多个,这种结构易于加工,结构简单,便于装配。
本实用新型中,“第一弓形板弹簧2-5及第二弓形板弹簧2-6的一头与轮辐右外环2-1的法兰盘安装槽内两侧内壁由第三螺栓2-4能转动地连接在一起;第一弓形板弹簧2-5及第二弓形板弹簧2-6的另一头与轮辐内环2-7安装槽两侧内壁由第四螺栓2-3能转动地连接”也可以采用现有技术中其它公知的结构来实施。
如图3所示,可见在充气环槽之间的凸起环壁上有横向小气槽(见图1中标记n所示),多个环向凸起环壁(见图1中标记g所示)上的横向小气槽是交错设置的,这种结构不破坏凸起环壁及轮胎1的强度,又能达到连通的目的。
由图5对于板弹簧支撑组合体的第一弓形板弹簧2-5、第二弓形板弹簧2-6的弹性变形和轮辐内环2-7与轮辐右外环2-1三者之间由坐标z、x位移量直观分析,下面简称:第一弓形板弹簧2-5为板簧2-5,第二弓形板弹簧2-6为板簧2-6;板簧2-5、2-6的一头分别安装在轮辐内环2-7的o1点、o2点和角度ɑ1、ɑ2的位置上,板簧2-5、2-6的的另一头分别安装在轮辐右外环2-1的o点o0点和角度ɑ2、ɑ3的位置上,见图5中的z、x坐标,左侧的板簧2-5、2-6两头安装位置与右侧的板簧2-5、2-6相同且对称,即ɑ1=ɑ1'、ɑ2=ɑ2'、ɑ3=ɑ3'呈现一个八字形单元。
假设ɑ1=ɑ2=ɑ3=0,见图6示,板簧2-5、板簧2-6的上、下连接点构成矩形,分析车轮行走减震位移,当车轮工作时,v1为主动转速,它带动被动转速v2,转速v2轮胎受地面阻力fx影响,当压力p和支撑力fz互相作用下使得轮辐右外环2-1上升,这时板簧2-5、2-6产生两个变形,一个是加弹性大弯曲变形,板簧2-5的曲率从ρ4变为ρ3,板簧2-6的曲率从ρ1变为ρ2,在轮辐右外环上的组合体安装点由点分别上升到∆h,使轮胎弹性减震;另一个变形是位移,这个位移的产生是板簧2-5、2-6的四个装配点呈矩形的不稳定特性所致,这个位移的产生是,当动力转速v1由z、x坐标的-x向x方向旋转迫使轮胎向x方向旋转,由于地面阻力fx和动力推力f5作用下迫使轮辐右外环2-1、轮胎1向后平移一个∆x,此位移量∆x会改变主动转速v1与被动转速v2之间的角转速ω的不同,v2转速滞后,一是会产生轮胎在地面前后磋移,二是会使被动转速v2滞后与主动转速v1不匹配产生驱动下降,当轮辐右外环2-1,第一弓形板弹簧2-5,第二弓形板弹簧2-6、轮辐内环2-7三者之间的四个安装点o、o0、o1、o2呈矩形的不稳定特性会产生自由摆动,由原0点变为03点,00变为04点,位移∆x距离,当它们摆动到由构架关系相互制约时,板簧2-5、2-6开始产生弹性变形减震,由原安装点上升一个∆h量和后移量∆x,这个位移量车轮在实际行走中必然存在。
结合图5所示,本实用新型抗扎防爆车由轮辐右外环2-1、轮辐内环2-7、板簧2-5、2-6的结合形成一个组合体,而由两个组合体对称安装位置呈现八字形的自然稳定性,即ɑ1<ɑ2<ɑ3,ɑ1=ɑ1'、ɑ2=ɑ2'、ɑ3=ɑ3'与坐标z、x对称布置形成八字形,使得车轮在旋转时受到地面阻力fx时由八字形支撑方式来完成阻止轮胎转速滞后,保证主动转速v1与被动转速v2的角转速ω基本相同,轮胎转速无滞后,驱动效率无损失,轮胎无后移位磨损。满足行车安全性。
本实用新型中技术条件的作用:轮辐内环2-7的工作任务是完成扭矩传递给第一弓形板弹簧2-5、第二弓形板弹簧2-6,并保证它们之间位置,第一弓形板弹簧2-5、第二弓形板弹簧2-6承担车轮弹性减震并支撑载重,它另一方面承担汽车动力传递给轮辐右外环2-1和确保汽车的横向稳定性;轮辐左外环2-2的任务是完成与轮辐右外环2-1夹紧和定位轮胎1,右外环2-1的工作任务是完成接受扭力并传递给轮胎1、保证汽车行驶横向稳定性和安全性;它们的工作顺序:轮辐内环2-7——第四螺栓2-3——第一弓形板弹簧2-5、第二弓形板弹簧2-6——轮辐右外环2-1——第三螺栓2-4——轮胎1——密封环4——轮辐左外环2-2——第一螺栓2-8。
起点商标作为专业知识产权交易平台,可以帮助大家解决很多问题,如果大家想要了解更多知产交易信息请点击 【在线咨询】或添加微信 【19522093243】与客服一对一沟通,为大家解决相关问题。
此文章来源于网络,如有侵权,请联系删除


