一种防弹车身及车辆的制作方法



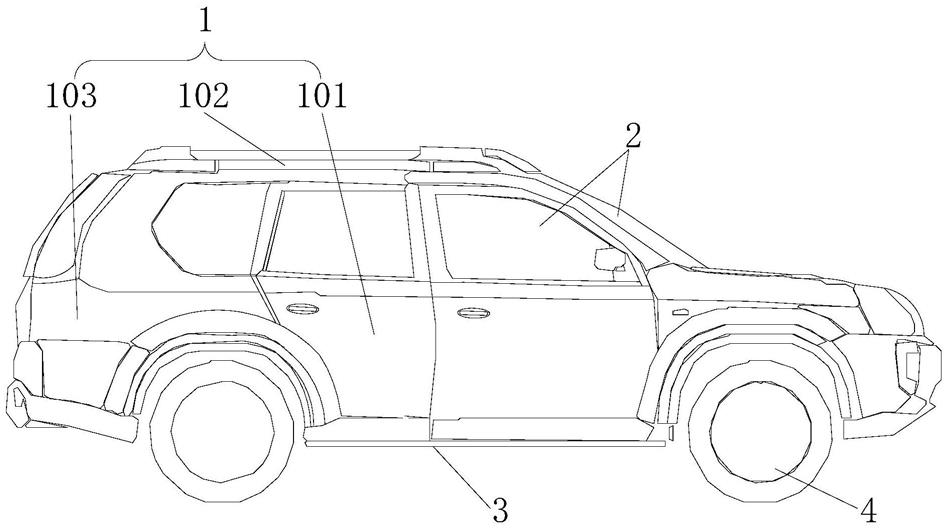
[0001]
本实用新型涉及技术领域,特别涉及一种防弹车身。本实用新型还涉及一种车辆。
背景技术:
[0002]
在现有的社会生活中,一些高端和有特殊安保需求的汽车经常需要有防弹性能方面的需求。现有汽车车辆的防弹车身,其技术方案约可分为两大类。第一大类为硬式防弹结构方案,即车身壳体为高强度防弹厚钢板结构,车窗为厚的防弹安全玻璃结构。其优点是这项技术较比成熟,实施起来并不十分艰难。其缺点是车身笨重,驱动功率过大,加工较难,设备投资较大等。第二大类为半硬式防弹结构方案,即车身壳体是由金属薄板与防弹复合材料,或由高分子复合材料与防弹材料相固化模压为一整体的结构件,其中防弹材料层已处于半硬半软的固化状态。
[0003]
对于第二大类的防弹车身,金属薄板随形设置在车身壳体的多曲面结构以内,金属薄板仍需要较大厚度,再配合防弹复合材料才能满足所需的抗弹击性能要求,对于车辆壳体的厚度和重量仍是不小的负担,尤其对于轿车类的小型车辆而言,防弹车身的壳体重量和厚度与防弹性能之间的矛盾尤为显著。
技术实现要素:
[0004]
有鉴于此,本实用新型旨在提出一种防弹车身,以为防弹车身的壳体厚度和重量等规格的改善提供有利条件。
[0005]
为达到上述目的,本实用新型的技术方案是这样实现的:
[0006]
一种防弹车身,应用于车辆上,所述防弹车身包括由防弹玻璃构成的车窗和壳体,所述壳体包括外板、内板、以及衬设于所述内板内侧的装饰板,于所述外板和所述内板之间夹设有防弹隔板;由所述车辆的外部向着所述车辆的内部方向,所述防弹隔板顺次设置有合金层和缓冲层两层;所述合金层的至少部分由多个合金片单元拼接而成,而形成所述合金层于所述缓冲层的多曲面外壁上的随形贴覆。
[0007]
进一步的,所述合金层采用稀土合金板或稀土钛合金板。
[0008]
进一步的,所述稀土钛合金板采用抗拉强度在tc4钛合金板以上的产品。
[0009]
进一步的,所述稀土钛合金板的厚度在0.3-15mm之间。
[0010]
进一步的,所述合金层的至少部分由呈正多边形的所述合金片单元密铺拼接。
[0011]
进一步的,所述合金片单元采用正六边形。
[0012]
进一步的,所述合金层的平面部分由大块合金片单元构成,所述大块合金片单元与所述合金片单元共同拼接而形成所述合金层。
[0013]
进一步的,所述缓冲层采用芳纶纤维。
[0014]
进一步的,于所述缓冲层的边缘部位嵌装有紧固螺母,于所述内板上构造有紧固座,所述防弹隔板由穿设于所述紧固座中并螺接于所述紧固螺母内的紧固螺栓固装于所述内板上。
[0015]
相对于现有技术,本实用新型具有以下优势:
[0016]
(1)本实用新型所述的防弹车身,通过在防弹车身的壳体的外板和内板之间加设具有合金层的防弹隔板,且合金层至少部分采用多个合金片单元拼接的方式,不仅降低了合金板在缓冲层上的多曲面随形贴覆难度,而且可提升防弹隔板的抗弹击性能,并有助于降低防弹隔板的厚度和重量规格,从而利于改善防弹车身的壳体厚度和重量。
[0017]
(2)采用稀土钛合金板作为合金层,使合金层的重力更轻,且抗拉强度、屈服强度、伸长率等各项性能优异,并具备良好的燃烧阻挡效果;可很好满足合金层在防弹隔板中的性能要求。
[0018]
(3)使用tc4以上级别的稀土钛合金板,性能更为可靠,且可根据抗弹击防护的规格要求,适当减薄合金层的厚度。
[0019]
(4)采用0.3-15mm厚的稀土钛合金板,匹配适当厚度的缓冲层,两者可满足多种抗弹击性能的指标要求,并可将整个防弹隔板的厚度和重量控制一个较为优异的范围内。
[0020]
(5)采用正六边形的合金片单元,剪切加工更为规范,便于拼接的规范操作,可提升拼接效率;且多种合金材料,如钛合金中的钛的同质异晶体在882℃以下为密排六方结构α钛,正六边形的裁切,和钛合金板的金属结构相适应,可使整个合金层受力性能更为稳定,弹击的冲击力在合金层上的分解效果良好,不易发生合金片单元因弹击而错位偏移的情况。
[0021]
(6)由于高强度合金板材一般具有较强的弹性变形和形状记忆恢复性能,对其的多曲面随形加工极为困难,采用多个小块的合金片单元拼接构成合金层的形式,可以很好客服这一工艺难题。而在缓冲层的平面部分,无需考虑随形困难的问题,在平面部分使用大块合金片单元,可提升拼接的效率。
[0022]
(7)采用芳纶纤维等防弹材料,例如凯夫拉材料,缓冲性能优良,技术成熟可靠。
[0023]
本实用新型的另一个目的在于提出一种车辆,包括底板和车轮,所述车辆采用本实用新型所述的防弹车身。
[0024]
相对于现有技术,本实用新型提出的车辆具有本实用新型的防弹车身所具备的技术优点。
附图说明
[0025]
构成本实用新型的一部分的附图,是用来提供对本实用新型的进一步理解,本实用新型的示意性实施例及其说明是用于解释本实用新型,其中涉及到的前后、上下等方位词语仅用于表示相对的位置关系,均不构成对本实用新型的不当限定。在附图中:
[0026]
图1为本实用新型实施例所述的车辆的总体结构示意图;
[0027]
图2为本实用新型实施例所述壳体的结构示意图;
[0028]
图3为图2中a所示部位的局部放大图;
[0029]
图4为本实用新型实施例所述防弹隔板的立体结构示意图;
[0030]
图5为图4中b所示部位的局部放大图;
[0031]
图6为本实用新型实施例所述的另一种拼接形式的防弹隔板的立体结构示意图;
[0032]
附图标记说明:
[0033]
1-壳体,101-车门,102-车顶,103-尾部壳体,2-车窗,3-底板,4-车轮;
[0034]
5-外板,501-包边,6-内板,601-装饰板固定座,602-紧固座,603-紧固螺栓,604-紧固螺母;
[0035]
7-防弹隔板,70-大块合金片单元,700-合金片单元,701-合金层,702-缓冲层。
具体实施方式
[0036]
需要说明的是,在不冲突的情况下,本实用新型中的实施例及实施例中的特征可以相互组合。
[0037]
此外,在本实用新型的描述中,涉及到的左、右、上、下等方位名词,是为了描述方便而基于图示状态下的用语,不应理解为构成对本实用新型结构的限定。
[0038]
本实施例涉及一种防弹车身,可以为防弹车身的壳体厚度和重量等规格的改善提供有利条件。该防弹车身应用于车辆上,所述防弹车身包括由防弹玻璃构成的车窗和壳体,所述壳体包括外板、内板、以及衬设于所述内板内侧的装饰板,于所述外板和所述内板之间夹设有防弹隔板;由所述车辆的外部向着所述车辆的内部方向,所述防弹隔板顺次设置有合金层和缓冲层两层;所述合金层的至少部分由多个合金片单元拼接而成,而形成所述合金层于所述缓冲层的多曲面外壁上的随形贴覆。
[0039]
基于上述的总体结构原则,下面将参考附图并结合实施例来详细说明本实用新型。应用有本实施例防弹车身车辆的一种示例性结构如图1所示,其主要包括壳体1、车窗2、底板3和车轮4。其中,壳体1包括车门101、车顶102、尾部壳体103等车身部位,这些部位的壳体1均需具备防弹功能,壳体1连同采用防弹玻璃的车窗2共同构成车辆的防弹车身。
[0040]
在本实施例中,如图2并图3所示,壳体1包括外板5、内板6、以及衬设于内板6内侧的装饰板于外板5和内板6之间夹设有防弹隔板7;由车辆的外部向着车辆的内部方向,防弹隔板7顺次设置有合金层701和缓冲层702两层;合金层701的至少部分由多个合金片单元700拼接而成,而形成合金层701于缓冲层702的多曲面外壁上的随形贴覆。由于高强度合金板材一般具有较强的弹性变形和形状记忆恢复性能,对其的多曲面随形加工极为困难,采用多个小块的合金片单元700拼接构成合金层701,可以很好客服这一工艺难题。
[0041]
其中,外板5的边缘具有包边501,包边501将内板6的边缘包裹,从而将外板5和内板6嵌装为一体的层叠结构板材。在车辆内部装设的装饰板固装于内板6的内侧,为了适配装饰板的非规则造型及其安装,在内板6上构造有用于随形或安装固定装饰板的装饰板固定座601。
[0042]
如图3所示,起到防弹作用的防弹隔板7夹设在由内板6和外板5围构的夹层内,包括合金层701和缓冲层702,为在控制一定重量和厚度的前提下达到预定的防弹性能要求,合金层701采用高强度、韧性及弹性形变性能的合金板材。例如,可采用钛合金板、稀土合金板中的重稀土系列合金板;优选地,合金层701采用稀土钛合金板。采用稀土钛合金板作为合金层701,使合金层701的重力更轻,且抗拉强度、屈服强度、伸长率等各项性能优异,并具备良好的燃烧阻挡效果;可很好满足合金层701在防弹隔板7中的性能要求。
[0043]
为使防弹性能更为可靠,上述的稀土钛合金板优选采用抗拉强度在tc4钛合金板以上的产品。这样,可根据抗弹击防护的规格要求,适当减薄合金层701的厚度。
[0044]
稀土钛合金板的厚度可根据防弹隔板7的抗弹击性能要求和厚度重量要求相应匹配,当减薄合金层701的厚度时,在确定的抗弹击性能要求下,就需要增加缓冲层702的厚
度。在测试实验中,稀土钛合金板的厚度在0.3-15mm之间,缓冲层702的厚度在4-20mm之间,可满足多种规范要去的抗弹击效果。例如,稀土钛合金板的厚度为0.4mm,缓冲层702厚度为12mm,可满足常规的车辆防弹要求。合金层701和缓冲层702厚度的配合调整,可使防弹隔板7满足多种抗弹击性能的指标要求,并可将整个壳体1的厚度和重量控制一个较为优异的范围内。
[0045]
对于合金层701的拼接形式、以及合金片单元700的形状可灵活适配,优选地,如图4和图5所示,合金层701的至少部分由呈正多边形的合金片单元700密铺拼接。采用正六边形的合金片单元700,剪切加工更为规范,便于拼接的规范操作,可提升拼接效率;且多种合金材料,如钛合金中的钛的同质异晶体在882℃以下为密排六方结构α钛,正六边形的裁切,和钛合金板的金属结构相适应,可使整个合金层701受力性能更为稳定,弹击的冲击力在合金层701上的分解效果良好,不易发生合金片单元700因弹击而错位偏移的情况。
[0046]
由于高强度合金板材一般具有较强的弹性变形和形状记忆恢复性能,对其的多曲面随形加工极为困难,采用多个小块的合金片单元700拼接构成合金层701的形式,即解决了这一工艺难题。如图6所示,由于壳体1往往在其中部存在一定面积的平面形状,相应地,随形于壳体1形状的防弹隔板7同样具有部分的平面形状,在防弹隔板7的缓冲层702的平面部分,无需考虑随形困难的问题;因此,可在该平面部分使用大块合金片单元70,可提升拼接的效率。这样,合金层701的平面部分就由大块合金片单元70构成,大块合金片单元70与合金片单元700共同拼接而形成合金层701。
[0047]
关于缓冲层702的材料,有很多成熟防弹材料可选,在本实施例中,缓冲层702采用芳纶纤维。采用芳纶纤维等防弹材料,例如凯夫拉材料,缓冲性能优良,技术成熟可靠。
[0048]
此外,为良好固定防弹隔板7,在缓冲层702的边缘部位嵌装有紧固螺母604,于内板6上构造有紧固座602,防弹隔板7由穿设于紧固座602中并螺接于紧固螺母604内的紧固螺栓603固装于内板6上。这样可使防弹隔板7的固定更为稳定,防弹隔板7在壳体1内的组配更佳方便。实际组配时,先将防弹隔板7安装在内板6上,再将内板6和外板5嵌装为一体即可。
[0049]
本实施例所述的防弹车身及其车辆,通过在防弹车身的壳体1的外板5和内板6之间加设具有合金层701的防弹隔板7,且合金层701至少部分采用多个合金片单元700拼接的方式,不仅降低了合金板在缓冲层702上的多曲面随形贴覆难度,而且可提升防弹隔板7的抗弹击性能,并有助于降低防弹隔板7的厚度和重量规格,从而利于改善防弹车身的壳体1厚度和重量。
[0050]
以上所述仅为本实用新型的较佳实施例而已,并不用以限制本实用新型,凡在本实用新型的精神和原则之内,所作的任何修改、等同替换、改进等,均应包含在本实用新型的保护范围之内。
起点商标作为专业知识产权交易平台,可以帮助大家解决很多问题,如果大家想要了解更多知产交易信息请点击 【在线咨询】或添加微信 【19522093243】与客服一对一沟通,为大家解决相关问题。
此文章来源于网络,如有侵权,请联系删除
相关标签:



tips