一种腔体支撑架结构轮胎的制作方法



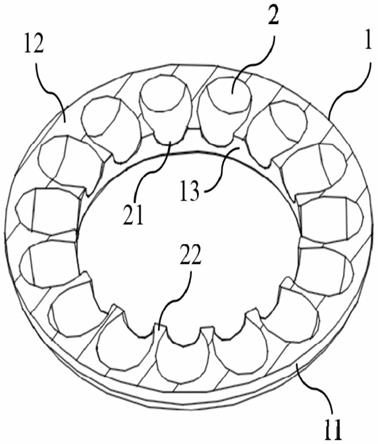
[0001]
本实用新型涉及轮胎技术领域,更具体地说是一种腔体支撑架结构轮胎。
背景技术:
[0002]
自橡胶出现以来,橡胶轮胎经历实心轮胎—充气轮胎—免充气轮胎与充气轮胎并行的进程。而自2014年兴起——2016年混战——2017年洗牌的共享单车因解决近距离打车快和走路远、传统车桩自行车存取不方便、gps定位且扫码取车方便等用户痛点而得到爆发式增长;继共享单车、共享汽车后,共享运营的时代也催化了另外一种交通工具——共享电动车,其历经2016年试水校园、景区等,于2017年正式投放,于2018年政府监管发展过程,其发展过程中陆续出现了电动车超标超速、停靠车位紧张、电池与骑行管理困难等等问题而严重制约了其发展速度,未来将依托互联网+电动车智能管理系统等设施,加大推动共享电动车的推广与应用。同时传统充气轮胎应用于共享单车、共享电动车等造成其维护十分困难,而新型出现的免充气轮胎恰好解决这一缺陷而被得到广泛的应用,极大推动免充气轮胎的发展。
[0003]
免充气轮胎采用结构减震设计,一般的是横向蜂窝穿孔或纵向多空的结构,其制作工艺都是整个轮胎都是一种材料、一次成型。而不像汽车轮胎一样,为多层设计,每一层材料偏重有所不同。一般的免充气轮胎考虑到轮胎的各个方面的指标,如抗压、耐磨、耐热、防滑、耐热等各个方面指标达到要求,就会把轮胎做的相对比较硬,这样就会大大的牺牲轮胎的舒适性,特别是和充气轮胎相比,差距很大,这样用户的使用体验感较差,就不会选择免充气轮胎,这也就是免充气轮胎无法大规模推广和应用的主要原因。如果想改善舒适度的问题,一般会把免充气轮胎做的比较软,这样又会造成负重降低,耐磨较差,容易开裂,使用寿命降低,同时一般免充气轮胎的重量较重,会增加整车的重量,从而增加了车辆的能耗,降低车辆的续航里程。
[0004]
经检索,中国专利公布号为:cn105599214a,公开日为:2016年5月25日,实用新型名称:一种免充气轮胎整体成型的压注方法,包括以下步骤:1)把配置好的免充气轮胎制造原料放入存料箱,并搅拌均匀;2)预热压注机至180℃-190℃;3)提升压注机压力至50pa-60pa;4)调整进料速度为10m/s-20m/s;5)调整保压时间至2min-3min;6)把步骤1)中的免充气轮胎制造原料注射入压注机,根据预设模式启动作业;7)依次经过合模、注射、热熔、冷却、开模后,获取免充气轮胎。该工艺简单,无需多次加工,操作便利,成本低;所获得的免充气轮胎结构均匀合理,没有内外胎之分,消除了内外胎之间的摩擦力和阻力。但该实用新型应用的材料tpe的耐热性不如橡胶,随着温度上升而物性下降幅度较大,因而适用范围受到限制。同时,压缩变形、弹性回复、耐久性等同橡胶相比较差,价格也高于同类橡胶。
技术实现要素:
[0005]
1.实用新型要解决的技术问题
[0006]
针对现有技术中免充气轮胎的强度性能与舒适性不能兼顾等问题,本实用新型提
出一种腔体支撑架结构轮胎,所述轮胎胎体内部沿径向开设有囊腔,各个囊腔在轮胎胎体内部形成腔体支撑架结构,以提高缓冲能力、增强骑行舒适性,并能够保证轮胎结构强度,兼顾轮胎骑行中的承载能力,节省骑行电耗。
[0007]
2.技术方案
[0008]
为达到上述目的,本实用新型提供的技术方案为:
[0009]
一种腔体支撑架结构轮胎,包括轮胎胎体,所述轮胎胎体包括胎体外周面和胎体内周面,所述胎体内周面沿其周向等间距的径向开设有模芯伸缩通孔;对应每个所述模芯伸缩通孔位置在所述轮胎胎体内部沿径向开设有囊腔,所述囊腔在所述轮胎胎体内部形成腔体支撑架结构,从而降低轮胎重量、节省材料,提高减震缓冲能力,增强骑行舒适性。
[0010]
进一步的技术方案,所述腔体支撑架结构水平面进一步的技术方案,所述轮胎胎体内部开设的相邻各个囊腔之间相离或相切或相交;相邻各个囊腔之间相离时,所述囊腔在所述轮胎胎体内部形成周期规律性间式相对独立腔体支撑架结构,常态下囊腔之间相互独立,互动较小,骑行时囊腔之间相互互动较小,从而降低轮胎重量、节省材料,一定程度提高轮胎骑行舒适性;相邻各个囊腔之间相切时,所述囊腔在所述轮胎胎体内部形成周期规律性点接触式腔体支撑架结构,常态下,各囊腔之间相互独立,骑行时囊腔之间相互互动明确,不仅能降低轮胎重量,还能够均分各囊腔受到的应力,从而增大轮胎胎体的强度,增强轮胎骑行负载能力;相邻各个囊腔之间相交时,所述囊腔在所述轮胎胎体内部形成相互联通式腔体支撑架结构,常态下囊腔之间相互联通,骑行时囊腔之间贯通一体形成一个整体,从而起到支撑轮胎胎体内部的作用,以保证轮胎结构强度更高。
[0011]
进一步的技术方案,所述腔体支撑架结构垂直投影为囊腔相连的弹簧环结构,各相邻囊腔相互联通,各弹簧环结构环形连接,形成类似于弹簧状的腔体支撑架结构,呈现囊腔单独受力支撑缓冲与腔体整体受力支撑缓冲相结合状态,因此,不仅能够起到加强轮胎结构强度的作用,还能够提高轮胎胎体的缓冲能力,增强骑行舒适性,同时轮胎缓冲性能、骑行舒适性大大提高,胎体质量大大减轻,腔体内部散热性大大增强。
[0012]
进一步的技术方案,所述轮胎胎体内部的各囊腔之间为胎体填充部,相邻两所述囊腔之间的胎体填充部形成弹性支撑构件,以支撑各囊腔之间间隙部分,以保证在提高轮胎结构强度的同时分散各囊腔之间的应力。
[0013]
进一步的技术方案,由于轮胎成型模具的出模通孔和中模模芯构件均属于刚性金属材料,当所述模芯伸缩通孔外径小于所述囊腔最大外径时,也就意味着轮胎成型模具的出模通孔外径小于中模模芯构件的最大外径,此时中模模芯构件无法从轮胎成型模具的出模通孔中插入,因此要求所述模芯伸缩通孔外径大于或等于所述囊腔最大外径,使得所述中模模芯构件头端易于从模芯伸缩通孔中拔出。
[0014]
一种腔体支撑架结构轮胎的加工方法,包括如下步骤:
[0015]
步骤一、合模:将轮胎成型模具的上模和下模合模,以形成上模腔和下模腔合并后的模腔;所述上模和下模合并后其二者内侧壁周向预留等间距分布的出模通孔;
[0016]
步骤二、安装模芯:将模芯提前放入成型模具的内环中部,模芯内的中模模芯构件呈周向分布,伸出中模模芯构件,使得中模模芯构件尾端对齐上、下模内侧壁上预留的出模通孔;
[0017]
步骤三、注射:将注射管一端插入轮胎成型模具的模腔内,然后注射橡胶材料,保
持恒定压力维持5~60s,以保证充满、充实;
[0018]
步骤四、插入模芯:当接收到橡胶填充完毕的信号后,翻转中模模芯构件,所述中模模芯构件头端伸出并穿过出模通孔,然后沿着垂直于所述胎体内周面方向插入轮胎胎体内部,使得所述轮胎胎体内部的胎体填充部受到中模模芯构件的挤压,进而形成囊腔;
[0019]
步骤五、硫化成型:对成型模具内部的轮胎胎体进行硫化处理,硫化处理过程中中模模芯构件仍置于轮胎胎体内部,从而降低开模取放模芯所产生的能耗,并避免硫化反应时囊腔精度出现尺寸公差;所述模芯沿轮胎胎体周向等间距分布,所述模芯外端置于所述胎体内周面的外侧,从而方便后续的取出工序;
[0020]
步骤六、取出模芯:所述中模模芯构件与胎体内周面接触部分形成模芯伸缩通孔,收缩模芯,所述中模模芯构件头端沿着所述模芯伸缩通孔轴线方向收缩回模芯内,由于所述轮胎胎体为具有弹性橡胶材质,从而易于从模芯伸缩通孔中拔出;
[0021]
步骤七、出模:打开上模腔和下模腔,拆除上模和下模,取出轮胎。
[0022]
进一步的技术方案,步骤四中,所述中模模芯构件头端从靠近轮胎成型模具的注射管的一端,依次插入至轮胎胎体内部,从而在一定程度上改善注射橡胶材料时产生的模腔内存在压力不均的问题;且能够保证各囊腔相互联通,以形成一个整体。
[0023]
进一步的技术方案,单个所述中模模芯构件水平面投影形状为u形,从而能够形成u形相连的弹簧环结构,从而起到加强轮胎结构强度的作用。
[0024]
3.有益效果
[0025]
采用本实用新型提供的技术方案,与现有技术相比,具有如下有益效果:
[0026]
(1)本实用新型的一种腔体支撑架结构轮胎,能够在一个模具中完成注射、硫化以及成型过程,成型过程中,所述中模模芯构件能够通过不开模方式进、出轮胎胎体内部,从而降低开模取出模芯所产生的能耗,并避免硫化反应时囊腔精度出现尺寸公差,大大简化生产工序,提高生产效率及成品率;
[0027]
(2)本实用新型的一种腔体支撑架结构轮胎,所述轮胎胎体内部开设的相邻各个囊腔之间相离或相切或相交;相邻各个囊腔之间相离时,所述囊腔在所述轮胎胎体内部形成周期规律性间式相对独立腔体支撑架结构,常态下囊腔之间相互独立,互动较小,骑行时囊腔之间相互互动较小,从而降低轮胎重量、节省材料,在一定程度上提高了轮胎骑行舒适性;相邻各个囊腔之间相切时,所述囊腔在所述轮胎胎体内部形成周期规律性点接触式腔体支撑架结构,常态下囊腔之间相互独立,骑行时囊腔之间相互互动明确,不仅能降低轮胎重量,还能够均分各囊腔受到的应力,从而增大轮胎胎体的强度,增强轮胎骑行负载能力;相邻各个囊腔之间相交时,所述囊腔在所述轮胎胎体内部形成相互联通式腔体支撑架结构,常态下囊腔之间相互联通,骑行时囊腔之间贯通一体形成一个整体,从而起到支撑轮胎胎体内部的作用,以保证轮胎结构强度更高;
[0028]
(3)本实用新型的一种腔体支撑架结构轮胎,所述囊腔相互联通形成支撑架结构,从而降低重量节省材料,提高缓冲能力,增强骑行舒适性;并能够起到支撑轮胎胎体内部的作用,以保证轮胎结构强度;
[0029]
(4)本实用新型的一种腔体支撑架结构轮胎,所述腔体支撑架结构垂直投影为囊腔相连的弹簧环结构,各相邻囊腔相互联通,各弹簧环结构环形连接,形成类似于弹簧状的支撑架结构,因此,不仅能够起到加强轮胎结构强度的作用,还能够提高轮胎胎体的缓冲能
力,增强骑行舒适性;
[0030]
(5)本实用新型的一种腔体支撑架结构轮胎,相邻两所述囊腔之间的胎体填充部形成弹性支撑构件,以支撑各囊腔之间间隙部分,以保证在提高轮胎结构强度的同时分散各囊腔之间的应力;
[0031]
(6)本实用新型的一种腔体支撑架结构轮胎,所制得的联通式囊腔结构轮胎不仅能够起到加强轮胎结构强度的作用,还能够提高轮胎胎体的缓冲能力,增强骑行舒适性,从而平衡了免充气轮胎的强度性能与舒适性等问题;
[0032]
(7)本实用新型的一种腔体支撑架结构轮胎,所述模芯伸缩通孔外径大于或等于所述囊腔最大外径,以保证中模模芯构件头端插入轮胎胎体内部形成囊腔后,所述中模模芯构件头端易于从模芯伸缩通孔中拔出;
[0033]
(8)本实用新型的一种腔体支撑架结构轮胎,合模后模芯提前放入成型模具的内环中部,使模芯内呈周向分布的成型段的前端对齐上、下模内侧壁上预留的出模通孔,再向轮胎成型模具的模腔内注射橡胶材料,注射完毕后模芯启动,所述中模模芯构件的前端伸出并穿过出模通孔,然后沿着垂直于所述胎体内周面方向,依次插入至轮胎胎体内部,由于所述中模模芯构件头端从靠近轮胎成型模具的注射管的一端依次插入至轮胎胎体内部,从而改善注射橡胶材料时产生的模腔内压力不均;且能够保证各囊腔相互联通,以形成一个整体,此种成型方式结构简单、且操作方便,从而有效提高了生产效率、降低能耗。
附图说明
[0034]
图1为本实用新型的轮胎结构示意图;
[0035]
图2为本实用新型的轮胎囊腔分离状态横向剖切结构示意图;
[0036]
图3为图2的俯视图;
[0037]
图4为本实用新型的轮胎囊腔联通状态横向剖切结构示意图;
[0038]
图5为图4的俯视图;
[0039]
图6为本实用新型的轮胎成型模具结构示意图;
[0040]
图7为本实用新型的轮胎成型模具的上、下模腔结构示意图;
[0041]
图8为本实用新型的中模模芯构件结构示意图。
[0042]
图中:1-轮胎胎体;2-囊腔;3-轮胎成型模具;4-注射管;5-中模模芯构件;11-胎体外周面;12-胎体填充部;13-胎体内周面;21-模芯伸缩通孔;22-弹性支撑构件;23-弹簧环结构;31-上模;32-下模;33-上模腔;34-下模腔;35-出模通孔;51-中模模芯构件头端;52-中模模芯构件尾端。
具体实施方式
[0043]
为进一步了解本实用新型的内容,结合附图对实用新型作详细描述。
[0044]
实施例1
[0045]
本实施例的一种腔体支撑架结构轮胎,如图1所示,包括轮胎胎体1,所述轮胎胎体1包括胎体外周面11和胎体内周面13,所述胎体内周面13沿其周向等间距的径向开设有模芯伸缩通孔21;如图2所示,对应每个所述模芯伸缩通孔21位置在所述轮胎胎体1内部沿径向开设有囊腔2,从而降低重量节省材料,提高缓冲能力,增强骑行舒适性;所述囊腔2在所
述轮胎胎体1内部形成腔体支撑架结构,从而起到支撑轮胎胎体1内部的作用,以保证轮胎结构强度。
[0046]
实施例2
[0047]
本实施例的一种腔体支撑架结构轮胎,基本结构同实施例1,不同和改进之处在于:如图2~5所示,所述轮胎胎体1内部开设的相邻各个囊腔2之间相离或相切或相交;相邻各个囊腔2之间相离时,所述囊腔2在所述轮胎胎体1内部形成周期规律性间式相对独立腔体支撑架结构,常态下,各囊腔2之间相互独立,互动较小,骑行时各囊腔2之间相互互动较小,从而降低轮胎重量、节省材料,一定程度提高轮胎骑行舒适性;相邻各个囊腔2之间相切时,所述囊腔2在所述轮胎胎体1内部形成周期规律性点接触式腔体支撑架结构,常态下,囊腔2之间相互独立,骑行时,囊腔2之间相互互动明确,不仅能降低轮胎重量,还能够均分各囊腔2受到的应力,从而增大轮胎胎体1的强度,增强轮胎骑行负载能力;相邻各个囊腔2之间相交时,所述囊腔2在所述轮胎胎体1内部形成相互联通式腔体支撑架结构,常态下,各囊腔2之间相互联通,骑行时,囊腔2之间贯通一体形成一个整体,从而起到支撑轮胎胎体1内部的作用,以保证轮胎结构强度更高;
[0048]
本实施中,所述囊腔2成型用的模芯与胎体内周面13接触部分形成模芯伸缩通孔21,沿着所述模芯伸缩通孔21能够将模芯取出,由于所述轮胎胎体1为具有弹性橡胶材质,因此模芯易于从模芯伸缩通孔21中拔出;所制得的联通式囊腔结构轮胎不仅能够起到加强轮胎结构强度的作用,还能够提高轮胎胎体的缓冲能力,增强骑行舒适性,从而平衡了免充气轮胎的强度性能与舒适性等问题。
[0049]
实施例3
[0050]
本实施例的一种腔体支撑架结构轮胎,基本结构同实施例2,不同和改进之处在于:如图2~3所示,所述腔体支撑架结构垂直投影为囊腔2相连的弹簧环结构23,各相邻囊腔2相互联通,各弹簧环结构23环形连接,形成类似于弹簧状的腔体支撑架结构,呈现囊腔2单独受力支撑缓冲与腔体整体受力支撑缓冲相结合状态,因此,不仅能够起到加强轮胎结构强度的作用,还能够提高轮胎胎体1的缓冲能力,增强骑行舒适性,同时轮胎缓冲性能、骑行舒适性也大大提高,胎体质量大大减轻,腔体内部散热性大大增强;所述囊腔2的腔体结构保持圆滑状,最大程度上消除了应力集中点;因此,不仅能够起到加强轮胎结构强度的作用,还能够提高轮胎胎体1的缓冲能力,增强骑行舒适性。
[0051]
实施例4
[0052]
本实施例的一种腔体支撑架结构轮胎,基本结构同实施例3,不同和改进之处在于:如图2所示,所述轮胎胎体1内部的各囊腔2之间为胎体填充部12,相邻两所述囊腔2之间的胎体填充部12形成弹性支撑构件22,以支撑各囊腔2之间间隙部分,以保证在提高轮胎结构强度的同时分散各囊腔2之间的应力,并尽可能在扩大囊腔2尺寸的情况下,加强轮胎结构强度,从而提高轮胎胎体1的缓冲能力。
[0053]
实施例5
[0054]
本实施例的一种腔体支撑架结构轮胎,基本结构同实施例4,不同和改进之处在于:对于小型轮胎(尺寸:6~9寸),如平衡车轮胎、滑板车轮胎,所述轮胎胎体1内部开设的囊腔2数目为15~18个;对于中型轮胎(尺寸:9~16寸),如自行车、电动车轮胎,所述轮胎胎体1内部开设的囊腔2数目为22~26个;对于大型轮胎(尺寸:16~22寸),如机动车轮胎,所
述轮胎胎体1内部开设的囊腔2数目为28~32个;以保证各囊腔2相互联通,以形成一个整体,进而加强轮胎结构强度;所述轮胎胎体1为橡胶材质,本身具有弹性,使得所述中模模芯构件头端51能够沿着轮胎成型模具3的内侧壁周向预留等间距分布的出模通孔35,同轴插入轮胎胎体1内部,从而在轮胎胎体内周面13上形成模芯伸缩通孔21,并在轮胎胎体1内部形成囊腔2;由于轮胎成型模具3的出模通孔35和中模模芯构件5均属于刚性金属材料,当所述模芯伸缩通孔21外径小于所述囊腔2最大外径时,也就意味着轮胎成型模具3的出模通孔35外径小于中模模芯构件5的最大外径,此时无法将中模模芯构件5插入轮胎成型模具3的出模通孔35中,因此要求所述模芯伸缩通孔21外径大于或等于所述囊腔2的最大外径,使得所述中模模芯构件头端51易于从模芯伸缩通孔21中拔出。
[0055]
实施例6
[0056]
本实施例的一种腔体支撑架结构轮胎,基本结构同实施例5,不同和改进之处在于:包括如下步骤:
[0057]
步骤一、合模:将轮胎成型模具3的上模31和下模32合模,以形成上模腔33和下模腔34合并后的模腔;所述上模31和下模32合并后其二者内侧壁周向预留等间距分布的出模通孔35;
[0058]
步骤二、安装模芯:将模芯提前放入轮胎成型模具3的内环中部,模芯内的中模模芯构件5呈周向分布,伸出中模模芯构件5,使得中模模芯构件尾端52对齐上、下模内侧壁上预留的出模通孔35;
[0059]
步骤三、注射:将注射管4一端插入轮胎成型模具3的模腔内,然后注射橡胶材料,保持恒定压力维持5~60s,以保证充满、充实;
[0060]
步骤四、插入模芯:当接收到橡胶填充完毕的信号后,翻转中模模芯构件5,所述中模模芯构件头端51伸出并穿过出模通孔35,然后沿着垂直于所述胎体内周面13方向插入轮胎胎体1内部,使得所述轮胎胎体1内部的胎体填充部12受到中模模芯构件5的挤压,进而形成囊腔2;
[0061]
步骤五、硫化成型:对成型模具内部的轮胎胎体1进行硫化处理,硫化处理过程中中模模芯构件仍置于轮胎胎体1内部,从而降低开模取放模芯所产生的能耗,并避免硫化反应时囊腔2精度出现尺寸公差;所述模芯沿轮胎胎体1周向等间距分布,所述模芯外端置于所述胎体内周面13的外侧,从而方便后续的取出工序;
[0062]
步骤六、取出模芯:所述中模模芯构件5与胎体内周面13接触部分形成模芯伸缩通孔21,沿着所述模芯伸缩通孔21轴线方向取出所述中模模芯构件5,由于所述轮胎胎体1为具有弹性橡胶材质,从而易于从模芯伸缩通孔21中拔出;
[0063]
步骤七、出模:打开上模腔33和下模腔34,拆除上模31和下模32,完成轮胎成型工序。
[0064]
本实施例中,所述中模模芯构件头端51插入轮胎胎体1内部,插入轮胎胎体1内部的相邻的中模模芯构件5相互独立,以形成等间距周向分布的若干个囊腔2;如图8所示,单个所述中模模芯构件5水平面投影形状为u形,各相邻囊腔2相互独立,相邻两所述囊腔2之间形成弹性支撑构件22,从而从轮胎胎体1内部起到加强轮胎结构强度的作用,以解决由于轮胎胎体1内部开设囊腔2造成的强度下降等问题。
[0065]
实施例7
[0066]
本实施例的一种腔体支撑架结构轮胎,基本结构同实施例6,不同和改进之处在于:包括如下步骤:
[0067]
步骤一、合模:将轮胎成型模具3的上模31和下模32合模,以形成上模腔33和下模腔34合并后的模腔;所述上模31和下模32合并后其二者内侧壁周向预留等间距分布的出模通孔35;
[0068]
步骤二、安装模芯:将模芯提前放入轮胎成型模具3的内环中部,模芯内的中模模芯构件5呈周向分布,伸出中模模芯构件5,使得中模模芯构件尾端52对齐上、下模内侧壁上预留的出模通孔35;
[0069]
步骤三、注射:将注射管4一端插入轮胎成型模具3的模腔内,然后注射橡胶材料,保持恒定压力维持5~60s,以保证充满、充实;
[0070]
步骤四、插入模芯:当接收到橡胶填充完毕的信号后,翻转中模模芯构件5,所述中模模芯构件头端51伸出并穿过出模通孔35,然后沿着垂直于所述胎体内周面13方向插入轮胎胎体1内部,使得所述轮胎胎体1内部的胎体填充部12受到中模模芯构件5的挤压,进而形成囊腔2;
[0071]
步骤五、硫化成型:对轮胎成型模具3内部的轮胎胎体1进行硫化处理,硫化处理过程中中模模芯构件5仍置于轮胎胎体1内部,从而降低开模取放模芯所产生的能耗,并避免硫化反应时囊腔2精度出现尺寸公差;所述模芯沿轮胎胎体1周向等间距分布,所述模芯外端置于所述胎体内周面13的外侧,从而方便后续的取出工序;
[0072]
步骤六、取出模芯:所述中模模芯构件5与胎体内周面13接触部分形成模芯伸缩通孔21,沿着所述模芯伸缩通孔21轴线方向取出所述中模模芯构件5,由于所述轮胎胎体1为具有弹性橡胶材质,从而易于从模芯伸缩通孔21中拔出;
[0073]
步骤七、出模:打开上模腔33和下模腔(34),拆除上模31和下模32,取出轮胎,完成轮胎成型工序。
[0074]
本实施例中,如图6~7所示,合模后模芯提前放入轮胎成型模具3的内环中部,使模芯内呈周向分布的中模模芯构件尾端52对齐上、下模内壁上预留的出模通孔35,将注射管4一端插入轮胎成型模具3的上模腔33和下模腔34之间,然后注射橡胶材料,注射完毕后启动模芯,翻转中模模芯构件5,使得所述中模模芯构件头端51伸出并穿过出模通孔35,然后沿着垂直于所述胎体内周面13方向,从靠近轮胎成型模具3的注射管4的一端,依次插入至轮胎胎体1内部,从而能够在一定程度上改善注射橡胶材料时产生的模腔内压力不均的问题;且能够保证各囊腔2相互联通,以形成一个整体;通过先注射后插模的方式,从而保证轮胎胎体1内部橡胶材料的均匀性,且能够保证所形成的囊腔2外围更加圆滑;通过不开模即可收缩模芯,从而避免开合模具造成的能耗,并且能够避免成型过程中囊腔2精度出现尺寸公差;此种成型方式结构简单、且操作方便,从而有效提高了生产效率、降低能耗;如图2~3所示,单个所述中模模芯构件5相互接触,以保证各囊腔2相互联通,以形成一个整体;单个所述中模模芯构件5水平面投影形状为u形,从而能够形成u形相连的弹簧环结构23,各相邻囊腔2相互联通,各弹簧环结构23环形连接,形成类似于弹簧状的支撑架结构,所述囊腔2相交形成腔体支撑架结构,所述腔体支撑架结构水平面投影为u形相连的弹簧环结构23,相互贯通形成一个整体,以起到兼具加强轮胎结构强度和提高轮胎胎体的缓冲能力的作用,进一步增强骑行舒适性,节省骑行电耗。
[0075]
以上示意性的对本实用新型及其实施方式进行了描述,该描述没有限制性,附图中所示的也只是本实用新型的实施方式之一,实际的结构并不局限于此。所以,如果本领域的普通技术人员受其启示,在不脱离本实用新型创造宗旨的情况下,不经创造性的设计出与该技术方案相似的结构方式及实施例,均应属于本实用新型的保护范围。
起点商标作为专业知识产权交易平台,可以帮助大家解决很多问题,如果大家想要了解更多知产交易信息请点击 【在线咨询】或添加微信 【19522093243】与客服一对一沟通,为大家解决相关问题。
此文章来源于网络,如有侵权,请联系删除



tips