一种耐老化弹性面料及其制备方法与流程



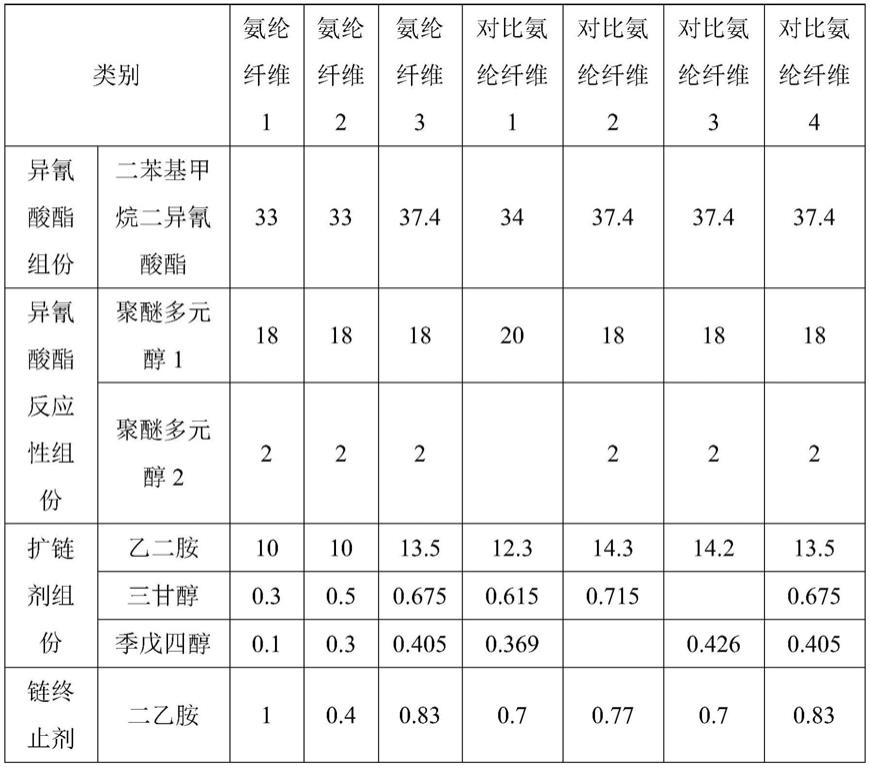
[0001]
本发明属于纺织面料领域,更具体地涉及一种耐老化弹性面料,以及所述面料的制备方法。
背景技术:
[0002]
纺织产品大部分是纤维织物,广泛应用于服装、医疗、航空航天、机械制造等领域。氨纶及其合成纤维因其高强度、低模量、高回弹、高断裂伸长率等特点逐渐占领了纺织产品市场,特别是在紧身衣、游泳衣、内衣等行业。但是,氨纶在其应用过程中会受到内外因素的影响,例如氧化、光辐射、化学试剂影响等,其优异的力学性能会出现逐渐下降的现象从而使其丧失应用价值。因此,纺织面料的耐老化性能是影响其使用的关键因素,特别是提高氨纶的抗老化性能和使用寿命,能够决定弹性纺织面料的综合性能。
[0003]
目前,现有技术中对于耐老化弹性面料的研究依然不能满足社会发展的需求,需要提供一种弹性优异且耐老化性能较好的面料。
技术实现要素:
[0004]
本发明提供了一种耐老化弹性面料,面料所用的氨纶纤维采用特制的聚醚多元醇组合、搭配乙二胺、三甘醇、季戊四醇作为复合扩链剂,能够使得氨纶纤维在具有优异弹性的同时还具有较高的耐老化性能,从而提高最终面料的性能。本发明还提供了所述面料的制备方法。
[0005]
一种耐老化弹性面料,由氨纶纤维和涤纶纤维纺织得到;其中所述氨纶纤维的制备方法为:
[0006]
步骤一,将异氰酸酯组份和异氰酸酯反应性组份混合进行反应,反应结束后得到预聚物,其中所述异氰酸酯反应性组份包括聚四亚甲基醚二醇和由季戊四醇起始的聚醚多元醇;
[0007]
步骤二,继续在所述预聚物中加入n,n-二甲基甲酰胺,搅拌均匀后加入乙二胺进行反应,反应1~3小时后加入三甘醇和季戊四醇进行反应,反应1~3小时后加入链终止剂,搅拌均匀后得到纺丝原液;其中所述乙二胺、三甘醇和季戊四醇为扩链剂组份;
[0008]
步骤三,将纺丝原液通过干法纺丝工艺制备成所述氨纶纤维。
[0009]
本发明采用特制的氨纶纤维,其中引入了由季戊四醇起始的聚醚多元醇,扩链步骤中添加了季戊四醇,对于最终制备的氨纶纤维中分子的交联程度有一定提升,分子结构更稳定,对于氨纶纤维的耐老化性能有一定提升;此外,制备工艺中引入三甘醇,结合制备方法中的其他原料和工艺,在保证氨纶纤维耐老化性能的同时确保氨纶纤维具有优异的弹性。由此使得最终制备的面料具有优异的耐老化性能和弹性。
[0010]
所述异氰酸酯组份可以选择本领域常用的异氰酸酯,优选二异氰酸酯,特别是二苯基甲烷二异氰酸酯。
[0011]
优选地,所述聚四亚甲基醚二醇的数均分子量为2000,所述由季戊四醇起始的聚
醚多元醇的数均分子量为2000,由环氧乙烷均聚得到。
[0012]
优选地,所述异氰酸酯组份中的异氰酸酯基团与所述异氰酸酯反应性组份中的羟基的摩尔比为1.5~1.7:1。更优选地,所述聚四亚甲基醚二醇和由季戊四醇起始的聚醚多元醇的摩尔比为9:1。
[0013]
控制聚四亚甲基醚二醇和由季戊四醇起始的聚醚多元醇的用量,可以控制最终形成氨纶分子的交联程度不至于过大,否则会影响氨纶的弹性。
[0014]
优选地,所述预聚物中的异氰酸酯基团与所述扩链剂组份中羟基基团的摩尔比为1.01~1.05:1;更优选地,所述乙二胺、三甘醇、季戊四醇之间的摩尔比为1:(0.03~0.05):(0.01~0.03)。
[0015]
控制三甘醇和季戊四醇在扩链剂组份中的比例,并且与所述制备方法中的其他组份和工艺进行配合,其目的一方面是控制氨纶分子的交联程度不至于过大,另一方面控制醚键的含量并综合上述因素能够使最终制备的氨纶纤维弹性适合且耐老化性能优异。
[0016]
所述链终止剂可以选择本领域常用的链终止剂,优选为二乙胺;所述二乙胺的用量以将反应体系中剩余异氰酸酯基团全部反应为准。
[0017]
所述n,n-二甲基甲酰胺的用量可以参考本领域常用的用量,优选地,所述n,n-二甲基甲酰胺的用量以将纺丝原液的固含量控制在35~40%的范围为准。
[0018]
需要说明的是,本发明对于所述各组份的用量或比例的限定,均是在理论计算的基础上,结合发明人大量的实验结果修正后得出的限定范围;本发明技术方案在应用于实施例的过程中,实际以质量为单位进行称量,组份质量的确定是按照本发明所限定的比例或用量通过理论公式换算得到,属于本发明的限定范围。
[0019]
所述氨纶纤维由所述纺丝原液通过干法纺丝工艺制备得到,所述干法纺丝工艺是本领域熟知的工艺,具体制备步骤可以参考现有技术中公开的内容,不影响本发明的实施。优选地,所述氨纶纤维的线密度控制在150~155dtex。
[0020]
所述涤纶纤维可以选择本领域常用的涤纶纤维,优选规格为22dtex/6f的涤纶纤维。
[0021]
所述面料的氨纶纤维含量为25~28%,以所述氨纶纤维和涤纶纤维的总质量为基准。
[0022]
一种所述面料的制备方法,步骤包括:以所述氨纶纤维和涤纶纤维为原料,经过纺织得到所述面料。
[0023]
所述制备方法未做说明的部分,可以采用本领域常用的工艺、参数、方法等进行,不影响本发明的实施。
[0024]
在一个优选实例中,氨纶纤维的整经速度为400m/min,预牵伸率为120%,全牵伸率为60%。
[0025]
本发明具有以下有益效果:采用由季戊四醇起始的聚醚多元醇、三甘醇、季戊四醇,与其他组份相互配合,控制氨纶分子的交联程度,在保证最终制备面料具有优异弹性的情况下,进一步增强了面料的耐老化性能。
具体实施方式
[0026]
以下结合具体实施例来进一步说明本发明。除非特别说明,本发明采用的试剂、方
法和设备为本技术领域常规试剂、方法和设备。除非特别说明,以下实施例所用试剂和材料均为市购。
[0027]
二苯基甲烷二异氰酸酯,巴斯夫公司生产;
[0028]
聚醚多元醇1,聚四亚甲基醚二醇,数均分子量为2000,巴斯夫公司生产;
[0029]
聚醚多元醇2,起始剂为季戊四醇,通过环氧乙烷聚合得到,数均分子量为2000,巴斯夫公司生产;
[0030]
涤纶纤维,规格为22dtex/6f。
[0031]
氨纶纤维1~3、对比氨纶纤维1的制备方法为:
[0032]
步骤一,将异氰酸酯组份和异氰酸酯反应性组份加入反应器,控制反应器温度为45℃,开启搅拌反应4小时,反应结束后得到预聚物;
[0033]
步骤二,继续在预聚物中加入n,n-二甲基甲酰胺,搅拌均匀后加入乙二胺进行反应,反应1小时后加入三甘醇和季戊四醇进行反应,反应3小时后加入链终止剂,搅拌均匀后进行脱泡处理,脱泡结束后得到固含量为35%的纺丝原液;其中,n,n-二甲基甲酰胺的加入量以纺丝原液固含量35%为基准;
[0034]
步骤三,将纺丝原液通过干法纺丝工艺制备成氨纶纤维,控制氨纶纤维的线密度为154dtex。
[0035]
对比氨纶纤维2的制备方法为:
[0036]
步骤一,将异氰酸酯组份和异氰酸酯反应性组份加入反应器,控制反应器温度为45℃,开启搅拌反应4小时,反应结束后得到预聚物;
[0037]
步骤二,继续在预聚物中加入n,n-二甲基甲酰胺,搅拌均匀后加入乙二胺进行反应,反应1小时后加入三甘醇进行反应,反应3小时后加入链终止剂,搅拌均匀后进行脱泡处理,脱泡结束后得到固含量为35%的纺丝原液;其中,n,n-二甲基甲酰胺的加入量以纺丝原液固含量35%为基准;
[0038]
步骤三,将纺丝原液通过干法纺丝工艺制备成氨纶纤维,控制氨纶纤维的线密度为154dtex。
[0039]
对比氨纶纤维3的制备方法为:
[0040]
步骤一,将异氰酸酯组份和异氰酸酯反应性组份加入反应器,控制反应器温度为45℃,开启搅拌反应4小时,反应结束后得到预聚物;
[0041]
步骤二,继续在预聚物中加入n,n-二甲基甲酰胺,搅拌均匀后加入乙二胺进行反应,反应1小时后加入季戊四醇进行反应,反应3小时后加入链终止剂,搅拌均匀后进行脱泡处理,脱泡结束后得到固含量为35%的纺丝原液;其中,n,n-二甲基甲酰胺的加入量以纺丝原液固含量35%为基准;
[0042]
步骤三,将纺丝原液通过干法纺丝工艺制备成氨纶纤维,控制氨纶纤维的线密度为154dtex。
[0043]
对比氨纶纤维4的制备方法为:
[0044]
步骤一,将异氰酸酯组份和异氰酸酯反应性组份加入反应器,控制反应器温度为45℃,开启搅拌反应4小时,反应结束后得到预聚物;
[0045]
步骤二,继续在预聚物中加入n,n-二甲基甲酰胺,搅拌均匀后同时加入乙二胺、三甘醇和季戊四醇进行反应,反应4小时后入链终止剂,搅拌均匀后进行脱泡处理,脱泡结束
后得到固含量为35%的纺丝原液;其中,n,n-二甲基甲酰胺的加入量以纺丝原液固含量35%为基准;
[0046]
步骤三,将纺丝原液通过干法纺丝工艺制备成氨纶纤维,控制氨纶纤维的线密度为154dtex。
[0047]
所述氨纶纤维制备方法中各原料的用量分别列于表1,以摩尔份数计算,所述摩尔份数指的是特定的制备步骤中各原料相互之间的相对摩尔比例。
[0048]
表1氨纶纤维制备步骤中各原料的用量(摩尔份数)
[0049][0050]
实施例和对比例的面料制备方法为:按照26.5%的氨纶纤维含量,将氨纶纤维与涤纶纤维纺织得到面料;其中,经编机为拉舍尔经编机,工艺参数为成品横密为19cm,成品纵密为126cm,机号为36,牵拉密度为50cm,涤纶纤维的送经量为642mm/rack,氨纶纤维的送经量为64mm/rack,面密度为85g/m2。
[0051]
由氨纶纤维1~3、对比氨纶纤维1~4经纺织,分别得到实施例1~3、对比例1~4的面料试样。
[0052]
将实施例和对比例试样按照fz/t70006-2004针织物拉伸弹性回复率试验方法的标准进行测试,测试结果列于表2。
[0053]
表2实施例和对比例面料的弹性测试结果
[0054][0055]
耐老化性能测试方法为:取实施例和对比例的面料试样分别置于恒温恒湿箱体内,箱内温度控制为60℃,湿度为20%,空气气氛,采用氙灯直照试样;试样分别在箱体内放置36小时、72小时、144小时后取出,测试试样的断裂强力,以断裂强力保持率作为试样耐老化性能的评价标准。
[0056]
所述断裂强力保持率=老化测试后的断裂强力值/断裂强力初始值*100%。其中,断裂强力初始值采用表2所列试样断裂强力的测试结果。
[0057]
实施例和对比例试样的耐老化测试结果列于表3。
[0058]
表3实施例和对比例的断裂强力保持率
[0059][0060][0061]
上述实施例为本发明较佳的实施方式,但本发明的实施方式并不受上述实施例的限制,其他的任何未背离本发明的精神实质与原理下所作的改变、修饰、替代、组合、简化,均应为等效的置换方式,都包含在本发明的保护范围之内。
起点商标作为专业知识产权交易平台,可以帮助大家解决很多问题,如果大家想要了解更多知产交易信息请点击 【在线咨询】或添加微信 【19522093243】与客服一对一沟通,为大家解决相关问题。
此文章来源于网络,如有侵权,请联系删除



tips