多级提氦装置及氦气分离系统的制作方法



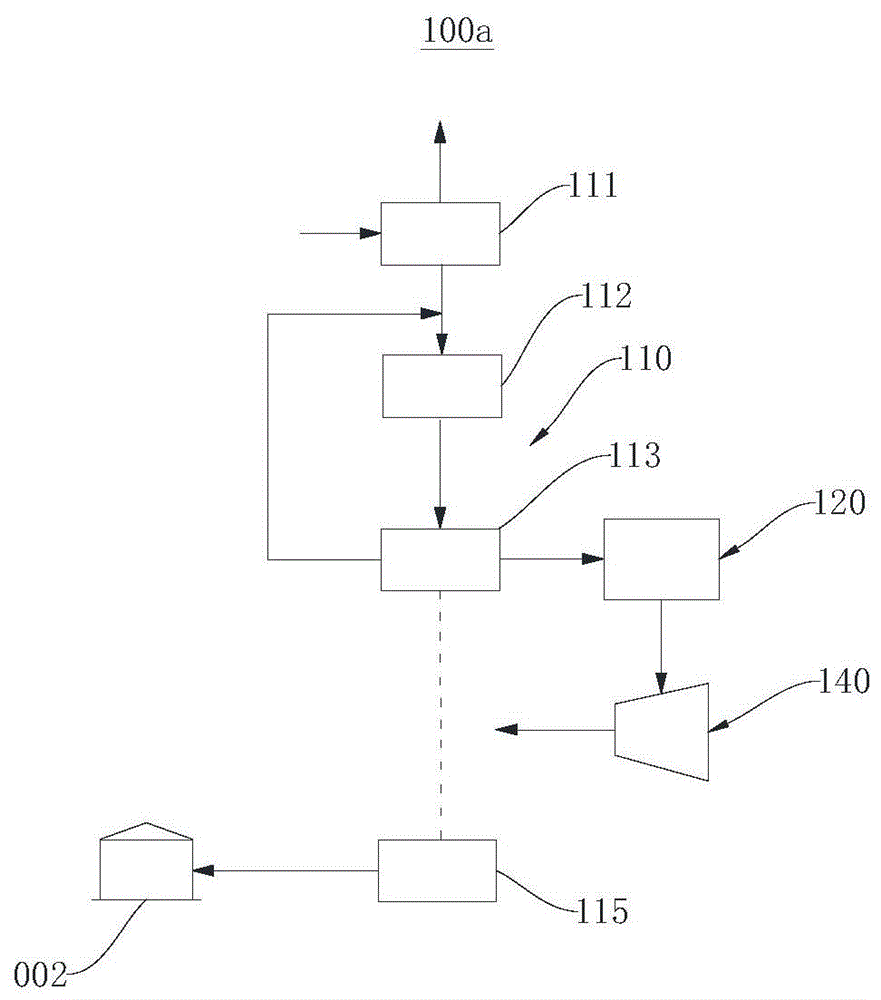
本实用新型涉及气体分离技术领域,具体而言,涉及多级提氦装置及氦气分离系统。
背景技术:
氦气是重要的战略资源,被广泛用于军工、医疗、半导体、低温超导、核磁共振及气体检漏等领域。氦气在空气中的含量比较低,在地层中的含量明显高于空气。随着我国石油天然气勘探的快速发展,我国天然气及页岩气加工及处理得到了快速发展,国内天然气消费市场规模不断扩大,天然气中含有大量的氦气且浓度较高,油田伴生天然气及天然气处理工厂中大量放空气通常通过工厂锅炉燃烧或者火炬燃烧,造成了天然气中大量氦气被浪费,因此能够亟需研发一种投资成本较低、能耗较低的氦气回收装置,对天然气中的较高浓度的氦气进行回收,能够有效避免氦气的浪费,增加国内的氦气储存。
现有的提纯氦气的方法普遍采用深冷分离或者变压吸附装置,深冷分离氦气装置设备具有投资较大、启动时间较长、能耗较高、产品纯度低等缺点;变压吸附装置具有设备体积大、噪音大、氦气收率较低等缺点。
技术实现要素:
本实用新型的目的在于提供一种多级提氦装置,旨在降低提氦过程的能耗,同时保证产品的纯度和收率。
本实用新型的另一目的在于提供一种氦气分离系统,旨在提升产品纯度的前提下,降低工艺的能耗。
本实用新型是这样实现的:
本实用新型提供一种多级提氦装置,用于从天然气中提取氦气,包括多级膜分离单元和除氢单元,多级膜分离单元包括至少三级膜分离组,分别为第一级膜分离组至第n级膜分离组,每一级膜分离组的渗透气出口与下一级膜分离组的进气口连通,除氢单元设置于任意相邻的两级膜分离组之间,第一级膜分离组的非渗透气出口与提氦尾气排气口连通,第n级膜分离组的渗透气出口与氦气产品收集口连通。
进一步地,在本实用新型较佳的实施例中,多级膜分离单元包括至少四级膜分离组,多级提氦装置还包括第一增压单元,第一增压单元的进气口与天然气供气管路连通,第一增压单元的出气口与第一级膜分离组的进气口连通。
进一步地,在本实用新型较佳的实施例中,在第一级膜分离组至第n级膜分离组的任一相邻的两个膜分离组之间设置第二增压单元。
进一步地,在本实用新型较佳的实施例中,在第一级膜分离组至第n级膜分离组的任一相邻的两个膜分离组之间均设置有增压单元。
进一步地,在本实用新型较佳的实施例中,第二级膜分离组的非渗透气出口与第一增压单元中压缩机的进气口连通,从第三级膜分离组至第n级膜分离组的非渗透气出口均与前端压缩机的进气口连通。
进一步地,在本实用新型较佳的实施例中,第一增压单元包括依次设置的压缩机、冷却器和分离罐,压缩机的进气口与天然气供气管路连通,分离罐的气体出口与第一级膜分离组的进气口连通。
进一步地,在本实用新型较佳的实施例中,除氢单元包括依次设置的脱氢塔、脱氧塔和脱水塔,脱氢塔的进气口分别与膜分离组的渗透气出口和供氧管路连通,脱水塔的出气口与另一组膜分离组的进气口连通。
进一步地,在本实用新型较佳的实施例中,在脱氧塔和脱水塔之间设置冷却分离装置;其中,冷却分离装置包括用于对塔式设备处理后的物料进行冷却的冷却器和用于对冷却后的物料进行气液分离的分离罐。
进一步地,在本实用新型较佳的实施例中,脱水塔和对应的膜分离组之间的还包括过滤器,过滤器的出气口与膜分离组的进气口连通。
本实用新型还提供一种氦气分离系统,其包括上述多级提氦装置。
本实用新型的有益效果是:本实用新型通过上述设计得到的多级提氦装置,其通过采用至少三级膜分离组对氦气进行逐级提浓,后面级的膜分离组的非渗透气返回前面压缩机入口增压,提氦尾气从第一级膜分离组的非渗透气出口排出,氦气产品从第n级膜分离组的渗透气出口排出。通过将后面级膜分离组的非渗透气循环至前面级膜分离组的入口,实现对各级非渗透气中的氦气成分的进一步提取,有效提高了提氦装置的产品收率。
此外,从第一级至第n级膜分离组的处理气量依次减小,氦气浓度依次升高,有效减少了压缩机的压缩做功,降低了装置能耗。此外,将包含脱氢塔、脱氧塔、脱水塔的除氢单元设置于相邻的两级膜分离组之间,实现了氦气与氢气的有效分离,避免了深冷分离氦气和氢气造成的能耗较高的缺点。同时,无需设置变压吸附装置,在保证产品纯度和收率的基础上,有效降低了装置的投资和操作难度。
特别说明的是,本实用新型中多级提氦装置的后面级膜分离组的非渗透气出口根据气体组分相近的原则,选择与前端某一增压单元的压缩机入口连通,避免了不同纯度的气体返混造成的分离做功。
特别说明的是,本实用新型中除氢单元的设置位置较为关键,通过将除氢单元设置在相邻的两级膜分离组之间,既避免了在低浓度下进行除氢反应需要处理大量原料气而存在的能耗高、处理精度低等缺点,也避免了在过高浓度下进行除氢反应(放热反应)而存在的设备超温风险。
本实用新型所提供的一种氦气分离系统,其包括上述多级提氦装置,通过多级膜分离组和位于相邻的两级膜分离组之间的除氢单元进行分离,避免了采用深冷分离或者变压吸附所带来的能耗高、启动时间长等问题。
附图说明
为了更清楚地说明本实用新型实施方式的技术方案,下面将对实施方式中所需要使用的附图作简单地介绍,应当理解,以下附图仅示出了本实用新型的某些实施例,因此不应被看作是对范围的限定,对于本领域普通技术人员来讲,在不付出创造性劳动的前提下,还可以根据这些附图获得其他相关的附图。
图1是本实用新型实施例提供的多级提氦装置的第一结构示意图;
图2是本实用新型实施例提供的多级提氦装置的第二结构示意图;
图3是本实用新型实施例提供的多级提氦装置的第三结构示意图;
图4是图3中除氢单元的结构示意图;
图5是本实用新型较佳的实施例中的流程图。
图标:100a-多级提氦装置;100b-多级提氦装置;100c-多级提氦装置;001-lng储罐;002-氦气收集罐;110-多级膜分离单元;111-第一级膜分离组;112-第二级膜分离组;113-第三级膜分离组;114-第四级膜分离组;115-第n级膜分离组;120-除氢单元;121-脱氢塔;122-脱氧塔;123-脱水塔;124-冷却分离装置;1241-冷却器;1242-分离罐;1243-过滤器;130-第一增压单元;131-压缩机;132-冷却器;133-分离罐;140-第三增压单元;150-第二增压单元。
具体实施方式
为使本实用新型实施方式的目的、技术方案和优点更加清楚,下面将结合本实用新型实施方式中的附图,对本实用新型实施方式中的技术方案进行清楚、完整地描述,显然,所描述的实施方式是本实用新型一部分实施方式,而不是全部的实施方式。基于本实用新型中的实施方式,本领域普通技术人员在没有作出创造性劳动前提下所获得的所有其他实施方式,都属于本实用新型保护的范围。因此,以下对在附图中提供的本实用新型的实施方式的详细描述并非旨在限制要求保护的本实用新型的范围,而是仅仅表示本实用新型的选定实施方式。基于本实用新型中的实施方式,本领域普通技术人员在没有作出创造性劳动前提下所获得的所有其他实施方式,都属于本实用新型保护的范围。
此外,术语“第一”、“第二”仅用于描述目的,而不能理解为指示或暗示相对重要性或者隐含指明所指示的技术特征的数量。由此,限定有“第一”、“第二”的特征可以明示或者隐含地包括一个或者更多个该特征。在本实用新型的描述中,“多个”的含义是两个或两个以上,除非另有明确具体的限定。
在本实用新型中,除非另有明确的规定和限定,术语“安装”、“相连”、“连接”、“固定”等术语应做广义理解,例如,可以是固定连接,也可以是可拆卸连接,或成一体;可以是机械连接,也可以是电连接;可以是直接相连,也可以通过中间媒介间接相连,可以是两个元件内部的连通或两个元件的相互作用关系。对于本领域的普通技术人员而言,可以根据具体情况理解上述术语在本实用新型中的具体含义。
请参照图1,本实用新型实施例提供一种多级提氦装置100a,用于从天然气中提取氦气,包括多级膜分离单元110和除氢单元120,除氢单元120用于去除混合气体中的氢气,起到进一步提纯氦气的目的。
具体地,多级膜分离单元110包括至少三级膜分离组,分别为第一级膜分离组111至第n级膜分离组115,每一级膜分离组的渗透气出口与下一级膜分离组的进气口连通,除氢单元120设置于任意相邻的两级膜分离组之间。如图1中,第一级膜分离组111、第二级膜分离组112、第三级膜分离组113、第n级膜分离组115;图2中多级提氦装置100b示出了最具有应用价值的四级膜分离组,即第一级膜分离组111至第四级膜分离组114。在图2中,多级膜分离单元110为四级膜分离组,除氢单元120的处理气进口与第三级膜分离组113的渗透气出口连通,除氢单元120的处理气出口与第四级膜分离组114的进气口连通。本申请实施例中的n是指四或四以上的整数。
需要说明的是,膜分离组不能直接将氢气和氦气进行有效分离,本申请设置了除氢单元120,采用氢气和氧气在催化剂作用下发生氧化反应生成水的原理去除氢气,再进行氧气和水的脱除。本申请通过将除氢单元120根据各级膜分离组渗透气出口的氢气浓度,设置于适宜的相邻两级膜分离组之间,既避免了在低浓度下进行除氢反应需要处理大量原料气而存在的能耗高、处理精度低等缺点,也避免了在过高浓度下进行除氢反应而存在的超温风险。除氢单元的设置显著提升了氢气和氦气分离效果,保证了最终氦气的纯度,且避免了深冷分离或变压吸附(或低温吸附)过程所带来的高能耗、启动时间长、产品收率低等缺点。
在本实用新型较佳的实施例中,用于提氦分离的天然气原料为液化天然气的闪蒸气(bog),bog来自于lng储罐001。
在一些实施例中,请结合图3-4,多级提氦装置100c还包括第一增压单元130,第一增压单元130的进气口与bog供气管路连通,第一增压单元130的出气口与第一级膜分离组111的进气口连通。通过第一增压单元130将气体增压,以使气体在进行膜分离之前具备较大的压力,在膜分离过程中渗透气的压力损失较大,如不进行增压,各级膜分离组的进口压力会逐渐降低。因此,可以根据需要在第二级膜分离组112至第n级膜分离组115的任一相邻的两个膜分离组之间设置第二增压单元(图未示),既确保了膜分离组件间所需要的压差,又实现了不同压力的相近氦气浓度的气体汇合。
请结合图5,在本实用新型较佳的实施例中,第二级膜分离组112的非渗透气出口与第一增压单元130中压缩机的进气口连通,第三级膜分离组113的非渗透气出口与第一增压单元130中压缩机的进气口连通,第四级膜分离组114的非渗透气出口与第二增压单元150中压缩机进气口连通。
在本实用新型较佳的实施例中,从第三级膜分离组113至第n级膜分离组115的非渗透气出口均通过压缩机与前端相近氦气浓度的膜分离组的进气口连通,使后端的非渗透气返回前端氦气浓度相近的膜分离组件入口(后端的非渗透气返回前端压缩机入口,以通过压缩机返回前端膜分离组件入口),实现了相近浓度气体的汇合,节省了压缩机功耗,提高了氦气总收率。需要指出的是,压缩机的个数可以为一台或多台,可以在每一级膜分离之间都可以设置压缩机,这种情况下可以使每一级的非渗透气出口均与对应的上一级膜分离组的进气口连通,都返回上一级。
进一步地,第一增压单元130包括依次设置的压缩机131、冷却器132和分离罐133,压缩机131的进气口与天然气供气管路连通,分离罐133的气体出口与第一级膜分离组111的进气口连通。利用压缩机131对气体加压,通过冷却器132降温之后通过分离罐133进行气液分离,防止带入液体至膜分离阶段。
经提氦处理后的尾气从第一级膜分离组的非渗透气出口排出,氦气产品从第n级膜分离组的渗透气出口排出。当然,在多级膜分离单元中的相邻两个膜分离单元之间均设置有氦气产品出口,可在各级出口分别获得不同纯度的氦气产品。
在一些实施例中,设置氦气收集罐002,用于收集第n级膜分离组115的渗透气,可以通过氦气收集罐002前端增设氦气分析仪,得到不同浓度的氦气进行回收。
进一步地,请参照图3和图4,除氢单元120包括依次设置的脱氢塔121、脱氧塔122和脱水塔123,脱氢塔121的进气口分别与膜分离组的渗透气出口和供氧管路连通,脱水塔123的出气口与另一组膜分离组的进气口连通。具体地,供氧管路用于输送氧气或空气,脱氢塔121采用氢气和氧气反应的原理去除氢气,脱氧塔122和脱水塔123分别进行氧气和水的去除。脱氢塔121、脱氧塔122和脱水塔123的个数不限,可以为1-3个。其中,脱水塔123也称为干燥塔,利用干燥剂去除水分,可以采用分子筛脱水的方式进行干燥。
在一些实施例中,可以通过氧气分析仪检测脱氢塔121和脱氧塔122之间的分离罐1242分离的气相氧气浓度,间接分析脱氢是否完全,并指导调整输入脱氢塔121的氧气或空气的流量。
在本实用新型较佳的实施例中,在脱氧塔122和脱水塔123之间设置冷却分离装置124;其中,冷却分离装置124包括用于对塔式设备处理后的物料进行冷却的冷却器1241和用于对冷却后的物料进行气液分离的分离罐1242。经过塔式设备反应之后往往伴随放热的发生,通过冷却器1241冷却之后经过分离罐1242进行气液分离,防止液体的产生带入下一工序。
在本实用新型较佳的实施例中,脱水塔123和对应的膜分离组之间还包括过滤器1243,过滤器1243的进气口与脱水塔123的气体出口连通,过滤器1243的出气口与膜分离组的进气口连通。通过过滤器1243针对粉尘等杂质进行过滤,以保护后端膜分离组不受杂质破坏。
在本实用新型较佳的实施例中,在膜分离组和除氢单元之间设置第三增压单元140,第三增压单元140可以根据需要进行设置,以防止除氢单元120后压力过低不利除氢分离过程。
本实用新型实施例还提供一种氦气分离系统,其包括上述多级提氦装置,通过多级膜分离单元110和除氢单元120进行提纯,并改进除氢单元120的位置使提纯效果得到进一步提升。
采用图3中的装置进行多级提氦,lng储罐001的bog经过第一增压单元压缩机增压至3mpa-10mpa后经冷却器、分离后进入第一级膜分离组件,第一膜分离组件非渗透气作为提氦尾气(主要成分为甲烷、氮气)返回工厂,第一级膜分离组件渗透气进入第二级膜分离组件;第二级膜分离组件的非渗透气返回第一增压单元压缩机入口,渗透气经第二增压单元压缩机增压至3-6mpa后进入除氢单元,经脱氢、脱氧、脱水处理后,进入第三级膜分离组件。第三级膜分离组件的非渗透气返回第一增压单元压缩机入口,渗透气进入第四级膜分离组件。第四级膜分离组件的非渗透气返回第二增压单元压缩机入口,渗透气作为产品氦气进入氦气收集装置。
在图3的具体的实例中,原料气组分为:ch472.16%,n222.31%,he4.31%,h21.22%,流量为1000m3/h。经四级提氦分离后的尾气流量为945.71m3/h,组分为:ch476.30%,n223.59%,he0.07%,h20.04%,氦气产品纯度为99.999%,流量为42.45m3/h,产品收率为98.49%,产品纯度高,收率高。
综上,本实用新型提供了一种多级提氦装置,其通过采用至少三级膜分离组进行多级膜分离,并将除氢单元设置于相邻的两级膜分离组之间,避免了深冷分离或者变压吸附所造成的能耗高、产品收率低、产品纯度低等缺点,并有效缩短了装置启动时间。
本实用新型还提供了一种氦气分离系统,其包括上述多级提氦装置,通过多级膜分离组和位于相邻的两级膜分离组之间的除氢单元进行分离,避免了采用深冷分离或者变压吸附所带来的能耗高、启动时间长等问题。
以上仅为本实用新型的优选实施方式而已,并不用于限制本实用新型,对于本领域的技术人员来说,本实用新型可以有各种更改和变化。凡在本实用新型的精神和原则之内,所作的任何修改、等同替换、改进等,均应包含在本实用新型的保护范围之内。
起点商标作为专业知识产权交易平台,可以帮助大家解决很多问题,如果大家想要了解更多知产交易信息请点击 【在线咨询】或添加微信 【19522093243】与客服一对一沟通,为大家解决相关问题。
此文章来源于网络,如有侵权,请联系删除


