无光干粒釉、无光干粒釉面效果的瓷砖及其制备方法与流程



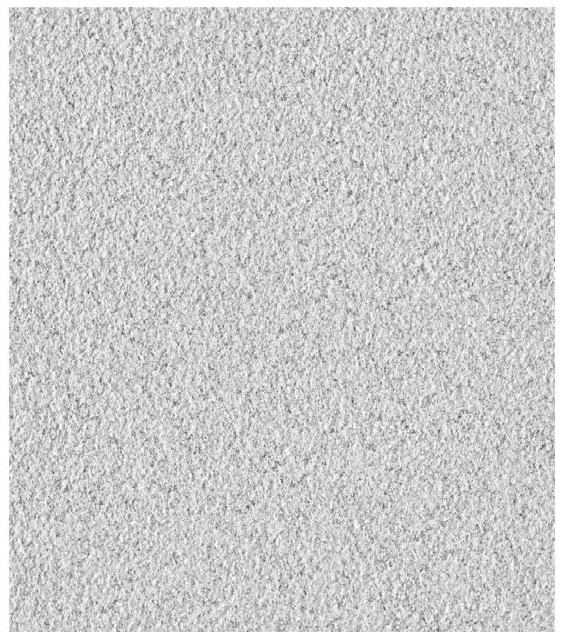
本发明属于陶瓷建材领域,具体涉及一种无光干粒釉、无光干粒釉面效果的瓷砖及其制备方法。
背景技术:
:目前市场上的干粒釉基本以哑光、亮光为主,而无光干粒釉极少研究。无光干粒釉光泽度低于2.5°,其表面基本没有光泽,从而产生出低调沉稳的视觉效果。无光干粒釉目前的主要技术难题是釉层透感和防污性能差。干粒釉光泽度越低则越容易析晶,析晶产生的大量晶相容易导致釉面乳浊透感差。另外干粒釉的光泽度低代表干粒釉的始融温度高,熔融性能差,这使得干粒釉表面毛孔多而且容易藏污。技术实现要素:针对上述存在的问题,本发明目的在于提供一种无光干粒釉、无光干粒釉面效果的瓷砖及其制备方法。本发明的无光干粒釉将无光泽、良好透感、耐磨、防滑、耐污染有效结合在一起,提升了产品的综合性能,满足市场对无光干粒釉产品多元化的需求。第一方面,本发明提供一种无光干粒釉。所述无光干粒釉以重量份数计,包括高温干粒25~35份、哑光干粒5份以下和保护釉40~45份;其中,所述高温干粒占无光干粒釉的质量百分比为35~47%;高温干粒的始融温度为1175~1195℃。较佳地,所述高温干粒的化学组成包括:按质量百分比计,sio2:48~52%;al2o3:22.0~26.0%;碱土金属氧化物:12.0~17.6%;碱金属氧化物:7.3~9.8%;优选地,所述高温干粒的硅铝摩尔比为(3.1~4.1):1。较佳地,所述哑光干粒的化学组成包括:按质量百分比计,sio2:49~54%;al2o3:16.0~22.0%;碱土金属氧化物:14.8~19.1%;碱金属氧化物:9.2~11.7%;zno:4.8~6.2%;优选地,所述哑光干粒的硅铝摩尔比为(3.7~5.1):1。较佳地,所述保护釉的化学组成包括:按质量百分比计,sio2:42~48%;al2o3:16.0~19.0%;碱土金属氧化物:17.1~22%;碱金属氧化物:7.4~10.7%;zno:5.8~7.6%。较佳地,所述高温干粒的颗粒级配包括:以质量百分比计,120目~150目:10~25%,150目~250目:40~65%,250目以下:10~25%。较佳地,所述哑光干粒的颗粒级配包括:以质量百分比计,100目~150目:10~28%,150目~250目:45~65%,250目以下:10~20%。较佳地,所述无光干粒釉的光泽度低于2.5°。本发明所述无光干粒釉将无光泽、透明度、耐磨防滑、耐污染性能有效结合在一起,适合运用各种场合。相对普通的干粒釉,本发明的无光干粒釉具有如下特点:表面光泽度低于2.5°,在侧灯光下基本没有光泽感,正面俯视无光泽,透感发色良好,耐污染性能5级,耐磨性能5级。第二方面,本发明提供一种无光干粒釉面效果的瓷砖的制备方法,包括:在坯体上施上述任一项所述的无光干粒釉,然后烧成获得无光干粒釉面效果的瓷砖;所述无光干粒釉的施加方式为喷釉,比重为1.2~1.4g/cm3,施釉量为250~275g/m2。较佳地,施无光干粒釉之前,在坯体上施析晶型面釉并喷墨打印图案;所述析晶型面釉的化学组成为:sio2:52~56%;al2o3:26~32%;碱土金属氧化物:9.7~14.3%;碱金属氧化物:4.7~6.6%;zno:2~3.0%;zro2:8~12%。较佳地,所述析晶型面釉的施加方式为喷釉,比重为1.4~1.5g/cm3,施釉量为515~545g/m2。第三方面,本发明还提供上述任一项所述的制备方法获得的无光干粒釉面效果的瓷砖。附图说明图1是本发明无光干粒釉应用于花岗岩图案瓷砖上的米色砖面效果图。图2是本发明无光干粒釉应用于花岗岩图案瓷砖上的棕色砖面效果图。图3是本发明无光干粒釉应用于花岗岩图案瓷砖上的灰色砖面效果图。具体实施方式通过下述实施方式进一步说明本发明,应理解,下述实施方式仅用于说明本发明,而非限制本发明。在没有特殊说明的情况下,各百分含量指质量百分含量。在本发明未作具体说明的情况下,“无光干粒釉”也可以称为“干粒釉”。制备无光干粒釉。无光干粒釉可包括三个部分:高温干粒、哑光干粒和保护釉。一些实施方式中,所述无光干粒釉以重量份数计,包括:高温干粒25~35份、哑光干粒0~5份和保护釉40~45份。通过将高温干粒、哑光干粒和保护釉三者的特性结合在一起解决了因光泽度极低导致透感差、耐污染性能差的问题。高温干粒为无光干粒釉提供较高的铝,熔剂含量相对较低,主要起到降低干粒釉光泽度和提高干粒釉耐磨性能的作用;保护釉的铝要相对低,而且保护釉和哑光干粒中熔剂的含量尤其是碱土金属氧化物的含量相对较高,同时含有高含量的zno,这有利于提高干粒釉的透感和耐污染性能。高温干粒主要作用在于降低干粒釉的光泽度和提高干粒釉的耐磨性能以及止滑性能,其化学组成包括:按质量百分比计,sio2:48~52%;al2o3:22.0~26.0%;cao:6.1~8.2%;mgo:2.5~4.6%;k2o:4.6~6.2%;na2o:2.7~3.6%;zno:3.2~4.6%;bao:3.6~4.8%。该高温干粒硅铝含量高,有助于提高干粒釉的耐磨和止滑性能。所述高温干粒的硅铝摩尔比可为(3.1~4.1):1,该合适的硅铝比使得高温干粒虽然无光泽但透感良好。一些实施方式中,所述高温干粒的始融温度为1175~1195℃。所述高温干粒的原料组成可包括:以重量份数计,钾长石:44~56份,钠长石4~14份,霞石:5~15份,高岭土:5~9份,煅烧氧化铝9.5~10.5份,方解石4~9份,白云石:6~15份,烧滑石:0~6份,煅烧氧化锌3~6份,碳酸钡:4~7份。上述所述的高温干粒制备方法包括:将上述重量份数的高温干粒原料以及添加剂0.5~0.8份混合,加入40~50份的蒸馏水,再进行球磨。将球磨好的物料烘干磨成粉末并煅烧。煅烧温度可为1380~1400℃。煅烧结束后水淬,破碎至合适的粒径,沥干。本发明的技术方案中,精选高温干粒的粒径在120目~250目,使之烧成后的无光干粒釉面耐污染性能良好,又能很好的满足生产问题。如果高温干粒的粒度过大,大颗粒容易沉淀,会发生赌喷枪、干粒喷不出的生产问题。同时高温干粒粒径过小,在烧成过程中与面釉粘结性能不好,干粒之间也不能紧密结合,容易产生表面粗糙、吸污的现象。作为示例,高温干粒的颗粒级配包括:以质量百分比计,120目~150目:10~25%,150目~250目:40~65%,250目以下:10~25%。哑光干粒主要作用在于提高干粒釉的耐污染性能,其化学组成包括:按质量百分比计,sio2:49~54%;al2o3:16.0~22.0%;cao:5.6~7.4%;mgo:3.6~4.8%;k2o:5.6~6.8%;na2o:3.6~4.9%;zno:4.8~6.2%;bao:5.6~6.9%。哑光干粒化学组成中硅铝较高,同时锌钡含量也较高,可以提高干粒釉的耐污染性能。优选地,所述哑光干粒的硅铝摩尔比为(3.7~5.1):1。所述哑光干粒的原料组成包括:以重量份数计,钾长石:53~60份,钠长石0~7份,霞石:10~25份,高岭土:0~5份,煅烧氧化铝3~5份,白云石:15~19份,烧滑石:1~2份,煅烧氧化锌4~7份,碳酸钡:7~9份。上述哑光干粒制备方法包括:将上述重量份数的哑光干粒原料以及添加剂0.5~0.8份混合,加入40~50份的蒸馏水,再进行球磨。将球磨好的物料烘干磨成粉末并煅烧。煅烧温度可为1320~1340℃。煅烧结束后水淬,破碎至合适的粒径,沥干。上述哑光干粒的始融温度为1160~1175℃。作为所述高温干粒的始融温度为1175~1195℃。高温干粒的始融温度优选高于哑光干粒35℃,更优选25~35℃。作为示例,所述哑光干粒的颗粒级配包括:以质量百分比计,100目~150目:10~28%,150目~250目:45~65%,250目以下:10~20%。上述哑光干粒和颗粒级配控制原则与高温干粒基本相同。保护釉主要作用在于提高干粒釉的耐污染性和釉面透感,其化学组成包括:按质量百分比计,烧失:5.6~7.8%;sio2:42~48%;al2o3:16.0~19.0%;cao:2.8~4.5%;mgo:4.6~5.9%;k2o:4.2~5.8%;na2o:3.2~4.9%;zno:5.8~7.6%;bao:8.5~10.2%;sro:1.2~1.4%。该保护釉具有较高的zno和bao含量,一方面有助于提高保护釉的防污性能,另一方面可以增强保护釉的发色。所述无光干粒釉的原料组成还可以包括100份胶水。胶水主要作用在于提高干粒釉的悬浮性,使得干粒釉能够均匀分布于瓷砖表面,烧成后干粒与干粒紧密结合,有助于生产的稳定性和干粒釉的耐污染性能。本发明还提供上述无光干粒釉的制备方法。按质量份记,将高温干粒25~35份、哑光干粒0~5份、保护釉浆40~45份、胶水100份加入到搅拌机进行搅拌、过筛及陈腐,即得到无光干粒釉浆。一些实施方式中,所述无光干粒釉的化学组成包括,按质量百分比计,sio2:46~50%;al2o3:20~24%;cao:3.5~5.5%;mgo:3.7~5.2%;k2o:4.3~5.5%;na2o:3.5~4.8%;zno:4.5~6.5%;bao:7.5~9.5%;sro:0.5~0.7%。所述无光干粒釉的硅铝摩尔比可为3.25~4.24。所述无光干粒釉的始融温度为1165~1175℃。以下示例性说明无光干粒釉的应用。在坯体上施析晶型面釉。所述析晶型面釉的化学组成包括,按质量百分比计,烧失:4.2~6.4%;sio2:52~56%;al2o3:26~32%;cao:3.3~4.5%;mgo:3.2~4.8%;k2o:4.3~5.8%;na2o:0.4~0.8%;bao:3.2~5%;zno:2~3.0%;zro2:8~12%。析晶型面釉优选熔融性能好的釉料,始融温度可为980~1050℃。作为优选,所述析晶型面釉的始融温度低于无光干粒釉115~195℃。如此可以使釉面光滑平整,改善无光干粒釉的手感和防污性能。可采用喷釉工艺施析晶型面釉。一些实施方式中,所述析晶型面釉的比重1.4~1.5g/cm3,施加量515~545g/m2。在施析晶型面釉的坯体上喷墨打印花岗岩设计图案。将无光干粒釉施于喷墨打印后的坯体上。在无光干粒釉施用过程中优选使用比重为1.2~1.4g/cm3的釉浆。此外,无光干粒釉的施釉量优选为250~275g/m2。无光干粒釉的施釉量不能过多,因为施釉量过多容易析晶,导致釉面细毛孔多容易藏污,影响干粒釉防污性能,但是施釉量也不能过少,这对使得无法遮盖面釉从而影响干粒釉的耐磨性能。所述无光干粒釉的釉层厚度可为0.08~0.12mm。将施无光干粒釉后的坯体烧成、磨边即得到无光干粒釉面效果的瓷砖。最高烧成温度可为1210~1220℃,烧成时间可为65~75分钟。烧成后的干粒釉层中锌钡含量较高,容易在硅酸盐中析出细腻柔和的晶体,从而利于提高干粒釉的耐污染性能。本发明的无光干粒釉与析晶型面釉和坯体紧密结合,烧成后的瓷砖釉层表面几乎无光泽,釉面透感良好。一些实施方式中,无光干粒釉面效果的瓷砖耐污染性能达到5级,耐磨性能达到5级。使用本发明提供的方法制备得到的高防污性能的花岗岩瓷砖,除了防污性能好、装饰效果佳之外,结构强度很高,还能给消费者带来低调沉稳的视觉效果,以及舒适、踏实、温暖、放松的仿古效果。下面进一步例举实施例以详细说明本发明。同样应理解,以下实施例只用于对本发明进行进一步说明,不能理解为对本发明保护范围的限制,本领域的技术人员根据本发明的上述内容作出的一些非本质的改进和调整均属于本发明的保护范围。下述示例具体的工艺参数等也仅是合适范围中的一个示例,即本领域技术人员可以通过本文的说明做合适的范围内选择,而并非要限定于下文示例的具体数值。实施例1无光干粒釉面效果的瓷砖的制备方法如下:(1)在坯体上采用喷釉工艺施析晶型面釉,面釉的比重为1.45g/cm3,施加量为530g/m2;(2)在施析晶型面釉的坯体上喷墨打印,(3)制备无光干粒釉;将高温干粒30份、哑光干粒3份、保护釉40份、胶水100份加入到搅拌机进行搅拌、过筛及陈腐,即得到无光干粒釉;高温干粒的化学组成包括:按质量百分比计,sio2:49%;al2o3:23%;cao:7.5%;mgo:3.5%;k2o:5.4%;na2o:3.5%;zno:3.5%;bao:4.6%;哑光干粒的化学组成包括:按质量百分比计,sio2:49%;al2o3:18%;cao:6.5%;mgo:4%;k2o:6.4%;na2o:4.6%;zno:5.5%;bao:6%;保护釉的化学组成包括:按质量百分比计,sio2:46%;al2o3:18%;cao:3.2%;mgo:5.8%;k2o:4.8%;na2o:4.2%;zno:7.4%;bao:9.8%;sro:0.8%;(4)将步骤(3)得到的无光干粒釉采用喷釉工艺施于喷墨打印后的坯体上,无光干粒釉的比重为1.32g/cm3,施加量为265g/m2;(5)将步骤(4)所得坯体烧成、磨边,获得无光干粒釉面效果的瓷砖。实施例2无光干粒釉面效果的瓷砖的制备方法如下:(1)在坯体上采用喷釉工艺施析晶型面釉,面釉的比重为1.42g/cm3,施加量为545g/m2;(2)在施析晶型面釉的坯体上喷墨打印,(3)制备无光干粒釉;将高温干粒35份、哑光干粒5份、保护釉45份、胶水100份加入到搅拌机进行搅拌、过筛及陈腐,即得到无光干粒釉;高温干粒的化学组成包括:按质量百分比计,sio2:49%;al2o3:26%;cao:6.5%;mgo:2.5%;k2o:5.4%;na2o:3.5%;zno:3.5%;bao:4.6%;哑光干粒的化学组成包括:按质量百分比计,sio2:49%;al2o3:16%;cao:7.5%;mgo:4%;k2o:6.4%;na2o:4.6%;zno:6.0%;bao:6.5%;保护釉的化学组成包括:按质量百分比计,sio2:46%;al2o3:18%;cao:3.2%;mgo:5.8%;k2o:4.8%;na2o:4.2%;zno:7.4%;bao:9.8%;sro:0.8%;(4)将步骤(3)得到的无光干粒釉采用喷釉工艺施于喷墨打印后的坯体上,无光干粒釉的比重为1.30g/cm3,施加量为275g/m2;(5)将步骤(4)所得坯体烧成、磨边,获得无光干粒釉面效果的瓷砖。实施例3无光干粒釉面效果的瓷砖的制备方法如下:(1)在坯体上采用喷釉工艺施析晶型面釉,面釉的比重为1.44g/cm3,施加量为540g/m2;(2)在施析晶型面釉的坯体上喷墨打印,(3)制备无光干粒釉;将高温干粒33份、哑光干粒4份、保护釉43份、胶水100份加入到搅拌机进行搅拌、过筛及陈腐,即得到无光干粒釉;高温干粒的化学组成包括:按质量百分比计,sio2:49%;al2o3:23%;cao:7.5%;mgo:3.5%;k2o:5.4%;na2o:3.5%;zno:3.5%;bao:4.6%;哑光干粒的化学组成包括:按质量百分比计,sio2:49%;al2o3:18%;cao:6.5%;mgo:4%;k2o:6.4%;na2o:4.6%;zno:5.5%;bao:6%;保护釉的化学组成包括:按质量百分比计,sio2:46%;al2o3:17%;cao:3.2%;mgo:5.8%;k2o:4.8%;na2o:4.2%;zno:7.4%;bao:10.8%;sro:0.8%;(4)将步骤(3)得到的无光干粒釉采用喷釉工艺施于喷墨打印后的坯体上,无光干粒釉的比重为1.32g/cm3,施加量为268g/m2;(5)将步骤(4)所得坯体烧成、磨边,获得无光干粒釉面效果的瓷砖。实施例4无光干粒釉面效果的瓷砖的制备方法如下:(1)在坯体上采用喷釉工艺施析晶型面釉,面釉的比重为1.41g/cm3,施加量为545g/m2;(2)在施析晶型面釉的坯体上喷墨打印,(3)制备无光干粒釉;将高温干粒28份、哑光干粒0份、保护釉42份、胶水100份加入到搅拌机进行搅拌、过筛及陈腐,即得到无光干粒釉;高温干粒的化学组成包括:按质量百分比计,sio2:50%;al2o3:26%;cao:6.5%;mgo:2.5%;k2o:5.4%;na2o:3.5%;zno:2.5%;bao:3.6%;哑光干粒的化学组成包括:按质量百分比计,sio2:49%;al2o3:18%;cao:6.5%;mgo:4%;k2o:6.4%;na2o:4.6%;zno:5.5%;bao:6%;保护釉的化学组成包括:按质量百分比计,sio2:46%;al2o3:16%;cao:3.2%;mgo:5.8%;k2o:4.8%;na2o:4.2%;zno:8.4%;bao:10.8%;sro:0.8%;(4)将步骤(3)得到的无光干粒釉采用喷釉工艺施于喷墨打印后的坯体上,无光干粒釉的比重为1.32g/cm3,施加量为275g/m2;(5)将步骤(4)所得坯体烧成、磨边,获得无光干粒釉面效果的瓷砖。比较例1与实施例1相比,区别仅在于:无光干粒釉中保护釉为36份。通过减少保护釉的量,瓷砖的耐污染性能减弱,这是因为保护釉起到助融作用,提高干粒釉的熔融性能,增加干粒釉的液相,从而利于提高干粒釉的防污性能。因此当无光干粒釉中保护釉的含量较小时无法实现良好的耐污染效果。比较例2与实施例2相比,区别仅在于:无光干粒釉中高温干粒为39份。可以发现,当高温干粒的用量过多时,瓷砖的耐污染性能减弱,这是因为高温干粒中铝含量很高,铝含量过高容易析晶,导致釉面毛细孔多,降低干粒釉的防污性能。比较例3与实施例3相比,区别仅在于:无光干粒釉中保护釉浆为48份。当保护釉浆的含量过多时,瓷砖的光泽度较高,无法达到良好的无光效果,这是因为过量的保护釉助融效果增强,干粒釉中液相含量增加导致光泽度提高,从而使得无光效果变差。比较例4与实施例5相比,区别仅在于:所述高温干粒的颗粒级配包括:以质量百分比计,120目~150目:35%,150目~250目:50%,250目以下:15%;所述哑光干粒的颗粒级配包括:以质量百分比计,100目~150目:30%,150目~250目:55%,250目以下:15%。本对比例中瓷砖的耐污染性能减弱,这是因为干粒粒径过大,在烧成过程中与面釉粘结性能不好,干粒之间也不能紧密结合,容易产生表面粗糙、吸污的现象。分别取实施例1~5和对比例1-5的瓷砖成品,按照gb/t3810-2006,gb/t4100-2006规定的方法测其表面耐磨性、耐污染性、光泽度,结果如下表示。表1性能检测表检测项目耐磨性光泽度耐污染性实施例152.05实施例252.55实施例352.05实施例452.54比较例151.54比较例252.04比较例3534比较例451.54表1可以看出本发明无光干粒釉将特定组成和颗粒级配的高温干粒、保护釉和哑光干粒和结合,高温干粒可以降低干粒釉的光泽,同时也会影响干粒釉的耐污染性能,保护釉和哑光干粒可以提高干粒釉的耐污染性,从而实现低光泽的同时,获得优异的耐磨性和耐污染性。当无光干粒釉中不包含哑光干粒时,瓷砖的耐污染无法达到最优效果。当前第1页1 2 3 
起点商标作为专业知识产权交易平台,可以帮助大家解决很多问题,如果大家想要了解更多知产交易信息请点击 【在线咨询】或添加微信 【19522093243】与客服一对一沟通,为大家解决相关问题。
此文章来源于网络,如有侵权,请联系删除



tips