玻璃基板的薄化方法及显示面板的制作方法与流程



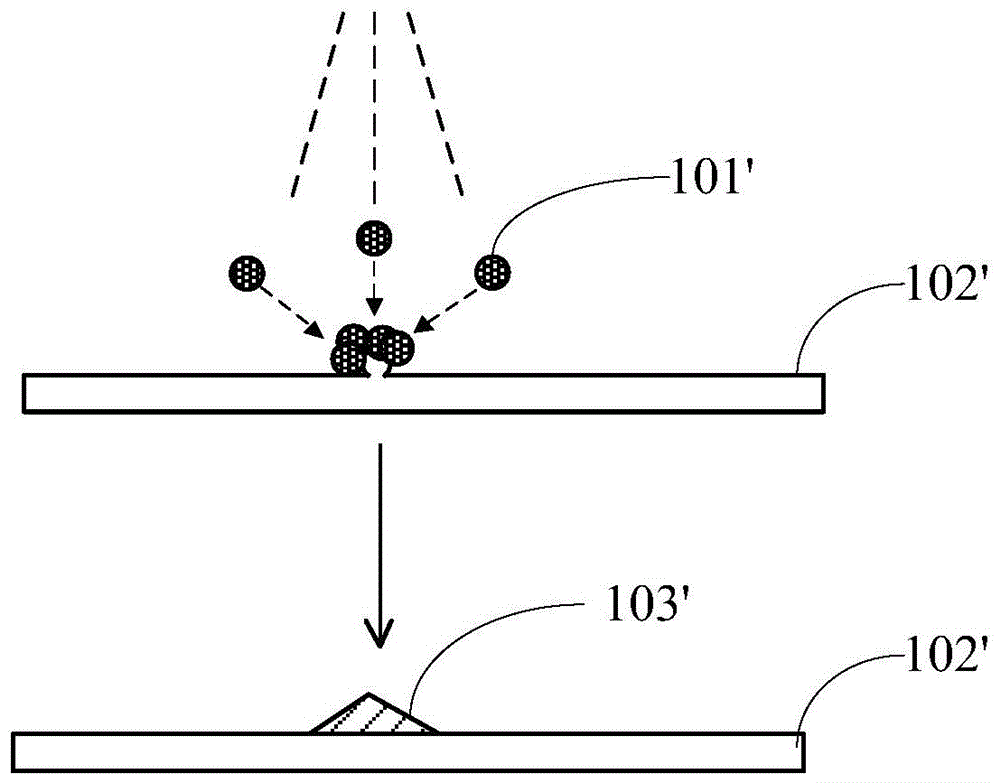
本发明涉及薄化技术领域,更具体地,涉及一种玻璃基板的薄化方法及显示面板的制作方法。
背景技术:
随着显示技术的日益成熟,显示装置的轻薄化成为了当今的主流发展趋势,其中一个方向就是使用超薄玻璃基板作为显示面板的衬底基板。因此,玻璃基板的薄化制程是实现显示装置薄型化的重要环节。
目前,化学刻蚀减薄是玻璃基板的主要减薄方法,通过刻蚀酸液与玻璃成分的化学反应,使玻璃基板减薄至工艺要求的厚度。但是,用于减薄的刻蚀酸液与玻璃反应后会产生玻璃粉,随着减薄过程的进行,玻璃粉也会不断增加,进而导致玻璃粉在玻璃基板表面聚集形成玻璃渣,玻璃渣附着在异物处产生凸点,严重影响了玻璃基板的减薄效率和品质。
技术实现要素:
本申请提供了一种玻璃基板的薄化方法及显示面板的制作方法,能够避免玻璃基板的表面在薄化过程中产生凸起不良,从而保证产品良率。
第一方面,本申请提供一种玻璃基板的薄化方法,包括刻蚀系统,所述刻蚀系统包括刻蚀线体、第一储液罐、第二储液罐以及连接所述第一储液罐和所述第二储液罐的旁通管道;
所述玻璃基板的薄化方法包括:
提供一玻璃基板;
获取所述第一储液罐中的第一刻蚀酸液,并利用所述旁通管道将所述第一刻蚀酸液注入所述第二储液罐;其中,所述第一刻蚀酸液中包含刻蚀残渣;
获取第二刻蚀酸液,并将所述第二刻蚀酸液注入所述第二储液罐;
将所述第二储液罐中的所述第一刻蚀酸液和所述第二刻蚀酸液注入所述刻蚀线体,使所述第一刻蚀酸液与所述第二刻蚀酸液混合,并利用混合得到的刻蚀酸液对所述玻璃基板的待薄化表面进行薄化处理。
第二方面,本申请还提供一种显示面板的制作方法,包括:
提供第一母板和第二母板;
在所述第一母板或所述第二母板上滴注液晶,并对盒所述第一母板及所述第二母板;
对所述第一母板远离所述第二母板的一侧表面进行薄化处理,并对所述第二母板远离所述第一母板的一侧表面进行薄化处理;
切割薄化后的第一母板和第二母板,得到多个显示面板;
其中,采用本申请所提供的玻璃基板的薄化方法对所述第一母板和所述第二母板进行薄化处理。
与现有技术相比,本申请提供的玻璃基板的薄化方法及显示面板的制作方法,至少实现了如下的有益效果:
本申请所提供的玻璃基板的薄化方法包括刻蚀系统,刻蚀系统包括刻蚀线体、第一储液罐、第二储液罐以及连接第一储液罐和第二储液罐的旁通管道;其中,第一储液罐中存储有第一刻蚀酸液,将含有刻蚀残渣的第一刻蚀酸液与不含有刻蚀残渣的第二刻蚀酸液混合后,得到的刻蚀酸液中也含有一定浓度的刻蚀残渣。利用混合后的刻蚀酸液对玻璃基板进行薄化处理时,能够使刻蚀酸液快速度过成核期、达到稳定的离子增长期,从而避免刻蚀残渣在薄化制程前期因镁离子浓度上升而结合形成玻璃渣,解决了玻璃表面的凸起不良问题。另外,采用上述薄化方法制作而成的显示面板不仅具有良好的薄化品质,也更加满足用户的轻薄化需求。
当然,实施本发明的任一产品必不特定需要同时达到以上所述的所有技术效果。
通过以下参照附图对本发明的示例性实施例的详细描述,本发明的其它特征及其优点将会变得清楚。
附图说明
被结合在说明书中并构成说明书的一部分的附图示出了本发明的实施例,并且连同其说明一起用于解释本发明的原理。
图1所示为相关技术中玻璃基板的薄化方法的一种示意图;
图2所示为本申请实施例所提供的玻璃基板的薄化方法的一种流程图;
图3所示为本申请实施例所提供的刻蚀系统的一种示意图;
图4所示为本申请实施例所提供的镁离子浓度随薄化数量的变化示意图;
图5所示为本申请实施例所提供的玻璃基板的薄化方法的一种示意图;
图6所示为本申请实施例所提供的刻蚀系统的另一种示意图;
图7所示为本申请实施例所提供的玻璃基板的薄化方法的另一种示意图;
图8所示为本申请实施例所提供的显示面板的制作方法的一种流程图。
具体实施方式
现在将参照附图来详细描述本发明的各种示例性实施例。应注意到:除非另外具体说明,否则在这些实施例中阐述的部件和步骤的相对布置、数字表达式和数值不限制本发明的范围。
以下对至少一个示例性实施例的描述实际上仅仅是说明性的,决不作为对本发明及其应用或使用的任何限制。
对于相关领域普通技术人员已知的技术、方法和设备可能不作详细讨论,但在适当情况下,所述技术、方法和设备应当被视为说明书的一部分。
在这里示出和讨论的所有例子中,任何具体值应被解释为仅仅是示例性的,而不是作为限制。因此,示例性实施例的其它例子可以具有不同的值。
应注意到:相似的标号和字母在下面的附图中表示类似项,因此,一旦某一项在一个附图中被定义,则在随后的附图中不需要对其进行进一步讨论。
目前,显示装置正在向着薄型化发展,所以在显示面板的生产过程中会有一道减薄玻璃基板的工序,而化学刻蚀是玻璃基板的常用减薄方法。图1所示为相关技术中玻璃基板的薄化方法的一种示意图。可以理解的是,采用化学刻蚀的方法对玻璃基板进行薄化制程时,可以将刻蚀酸液喷淋在玻璃基板的表面,或者直接将玻璃基板浸泡于刻蚀酸液中,通过刻蚀酸液与玻璃之间发生的化学反应来达到减薄玻璃厚度的目的。请参见图1,由于刻蚀酸液101'与玻璃基板102'反应后会产生刻蚀残渣103',且刻蚀时间越久,产生的刻蚀残渣103'就越多,当刻蚀残渣103'在玻璃基板102'的异物处发生聚集时,不仅会出现凸点或刻蚀不均的现象,同时也降低了玻璃的刻蚀速率。
有鉴于此,本申请提供了一种玻璃基板的薄化方法及显示面板的制作方法,能够避免玻璃基板的表面在薄化过程中产生凸起不良,从而保证产品良率。
图2所示为本申请实施例所提供的玻璃基板的薄化方法的一种流程图,图3所示为图1实施例所提供的刻蚀系统的一种示意图。请参见图2和图3,本申请提供一种玻璃基板的薄化方法,包括刻蚀系统,该刻蚀系统包括刻蚀线体、第一储液罐、第二储液罐以及连接第一储液罐和第二储液罐的旁通管道;
玻璃基板的薄化方法包括:
步骤s1、提供一玻璃基板;
步骤s2、获取第一储液罐中的第一刻蚀酸液,并利用旁通管道将第一刻蚀酸液注入第二储液罐;其中,第一刻蚀酸液中包含刻蚀残渣;
步骤s3、获取第二刻蚀酸液,并将第二刻蚀酸液注入第二储液罐;
步骤s4、将第二储液罐中的第一刻蚀酸液和第二刻蚀酸液注入刻蚀线体,使第一刻蚀酸液与第二刻蚀酸液混合,并利用混合得到的刻蚀酸液对玻璃基板的待薄化表面进行薄化处理。
本实施例中,刻蚀系统包括刻蚀线体、第一储液罐、第二储液罐和旁通管道。在玻璃基板的薄化制程中,第一储液罐用于盛装第一刻蚀酸液,第二储液罐用于盛装经旁通管道流入的第一刻蚀酸液和新加入的第二刻蚀酸液,刻蚀线体包括减薄玻璃基板的多种薄化设备,用于将第一刻蚀酸液与第二刻蚀酸液混合后进行玻璃基板的薄化处理。
应当理解,采用刻蚀酸液进行玻璃基板减薄的主要原理是:刻蚀酸液与玻璃中的sio2、mgo等成分发生反应并使玻璃表层剥离,从而达到减薄玻璃厚度的目的。但是,上述反应过程中会生成刻蚀残渣,刻蚀残渣中的四氟化硅与镁离子结合后形成难溶于水的白色沉淀物,玻璃减薄行业中通常称其为玻璃渣。图4所示为相关技术中镁离子浓度随薄化数量的变化示意图,其中,横轴表示减薄玻璃基板的数量,纵轴表示刻蚀酸液中镁离子的浓度。显然,在减薄过程中,随着处理玻璃基板数量的增加,刻蚀酸液中镁离子的浓度变化呈现出三个阶段:
第一阶段为未成核期,在薄化第0~t1张玻璃基板的过程中,刻蚀酸液中镁离子的浓度会随着减薄数量的增加而快速升高,并逐渐超过其饱和溶解度值,当刻蚀酸液中刻蚀残渣的浓度达到c2时,镁离子进入饱和态。
第二阶段为成核期,也称为晶核生成期;在薄化第t1~t2张玻璃基板时,刻蚀酸液中镁离子的浓度仍持续增长并进入过饱和态,镁离子从刻蚀酸液中析出并聚集。
第三阶段为离子增长期,当薄化至第t2~t3张玻璃基板时,镁离子的浓度虽然仍保持在大于饱和溶解度的范围内,但不再析出。
上述过程中,t1、t2、t3为已经完成减薄的玻璃基板的数量,且t1<t2<t3,可选地,t1=60、t2=90、t3=120;也就是说,薄化前60片玻璃基板时,镁离子处于未成核期,薄化第60~90片玻璃基板时,镁离子处于成核期,薄化第90~120片玻璃基板时,镁离子处于离子增长期。进一步地,c1=0.0005%,c2=0.005%,即镁离子的饱和溶解度c1可以为0.0005%,成核浓度c2可以为0.005%。
在本实施例所提供的玻璃基板的薄化方法中,由于第一刻蚀酸液中含有刻蚀残渣,那么通过上述步骤s2和步骤s3将二者混合后,得到的刻蚀酸液中也必然含有一定浓度的刻蚀残渣。在减薄过程中,随着刻蚀酸液与玻璃发生反应,刻蚀残渣的浓度会在原有浓度的基础上迅速上升,而镁离子浓度则会快速度过成核期、进入离子增长期,也就是说镁离子不再析出,避免了刻蚀残渣在成核期内于待薄化表面发生聚集并附着,从而解决了玻璃基板表面的凸起不良问题,有效保证玻璃基板的薄化品质。
可选地,第一刻蚀酸液为每一生产周期结束时所预留的预设体积的剩余刻蚀酸液,第二刻蚀酸液不含有刻蚀残渣;其中,每一生产周期包括30~120张玻璃基板的薄化过程。
由图3可知,本实施例中刻蚀线体与第一储液罐连接,刻蚀线体对每一片玻璃基板薄化后的剩余刻蚀酸液均会流入第一储液罐。可以理解的是,混合后的刻蚀酸液与玻璃发生反应所产生的刻蚀残渣能够在剩余刻蚀酸液流走时被一同带走,因此第一储液罐内盛装的剩余刻蚀酸液中含有大量薄化过程中产生的刻蚀残渣。一方面,在刻蚀酸液中加入适量的刻蚀残渣有利于在薄化制程中使镁离子浓度快速跃过成核期、到达稳定的离子增长期,进而避免刻蚀残渣在待薄化表面聚集,解决了玻璃基板表面的凸起不良问题;另一方面,薄化过程中产生的刻蚀残渣为危险废弃物,进行无害化处理的成本很高,本实施例通过对废弃的刻蚀残渣进行回收利用,不仅有利于节约生产成本,也更加环保。
本实施例中,每一生产周期可以包括30~120张玻璃基板的薄化过程,当然,每个生产周期中薄化玻璃基板的数量应当根据实际生产需求来确定,本实施例对此不做限定。
在本发明的一种可选实施例中,上述步骤s4中,混合得到的刻蚀酸液包括氢氟酸。
具体而言,减薄过程中氢氟酸与玻璃中的sio2发生如下化学反应:
4hf+sio2→sif4+2h2o;
4hf+2sio2→h4sio4+sif4;
其中,反应物sif4即为刻蚀残渣的主要成分之一,混合后的刻蚀酸液与待薄化表面发生如上化学反应后,待薄化表面的表层剥离,从而使玻璃基板的厚度减薄至工艺要求。显然,与物理减薄方法相比,利用氢氟酸进行刻蚀的减薄方法不仅更加高效,也有利于满足大批量生产的需要。
另外,混合后的刻蚀酸液中不仅包括氢氟酸,还可以包括其他强酸,如硫酸、盐酸或硝酸,各个成分的配比需要根据实际的薄化需求而确定,本实施例对此不做限定。
在本发明的一种可选实施例中,刻蚀残渣包括四氟化硅和镁离子。
可以理解的是,刻蚀残渣的主要成分包括四氟化硅和镁离子,四氟化硅与成核期析出的镁离子结合后,会聚集于玻璃基板的待薄化表面并形成难溶于水的白色沉淀物,也就是玻璃渣,由于玻璃渣很难被剩余刻蚀酸液冲走,因而会附着在待薄化表面形成凸点。显然,为了使混合后的刻蚀酸液尽快度过成核期,需要增大刻蚀残渣(镁离子)的浓度。因此,本实施例预先在刻蚀酸液中加入刻蚀残渣,相当于在未开始玻璃的减薄处理之前,刻蚀酸液中已经含有一定浓度的镁离子,在此基础上,随着薄化前期镁离子浓度的迅速上升,混合后的刻蚀酸液能够在短时间内达到离子稳定期,进而避免了玻璃渣的产生和聚集,使玻璃基板的薄化效果得以保证。
可选地,第一刻蚀酸液中刻蚀残渣的第一浓度为13%-25%。
应当理解,用于减薄的刻蚀酸液由第一刻蚀酸液和第二刻蚀酸液混合而成,其中,第一刻蚀酸液中含有刻蚀残渣,第二刻蚀酸液中则不含有刻蚀残渣,因此,为了使混合后的刻蚀酸液能够在减薄过程中快速度过成核期,本实施例设置第一刻蚀酸液中刻蚀残渣的第一浓度为13%-25%,此种设计方式能够确保混合后的镁离子浓度接近或到达如图4所示的a点,从而在每个生产周期的前期即可进入离子增长期,有利于避免玻璃渣聚集在待薄化表面。另外,若第一浓度小于13%,则两种刻蚀酸液混合后的刻蚀残渣浓度偏小,无法在薄化过程中迅速到达离子增长期,反之若第一浓度大于25%,则会造成原料的浪费。因此,将第一浓度设置为在13%-25%的范围内,能够在兼顾生产成本的同时,保证玻璃基板的薄化品质。
进一步地,混合得到的刻蚀酸液中刻蚀残渣的第二浓度为2.3%-4%。
本实施例中,第一刻蚀酸液与第二刻蚀酸液混合后,第二残渣的浓度应在2.3%-4%,如此能够保证在每个生产周期的前期即可进入离子增长期,有利于避免析出的刻蚀残渣与镁离子结合后聚集在待薄化表面而无法被剩余刻蚀酸液带走,从而提高了产品良率。
可选地,第一刻蚀酸液的体积为v1,第二刻蚀酸液的体积为v2,其中,1/8≤v1/v2≤1/5。
本实施例中,用于混合的第一刻蚀酸液的体积v1与第二刻蚀酸液的体积v2之比为[1/8,1/5],例如,可以在每一生产周期结束时预留的3m3的剩余刻蚀酸液作为第一刻蚀酸液,然后将3m3的第一刻蚀酸液与20m3的第二刻蚀酸液注入第二储液罐中,并在刻蚀线体内循环30分钟,以确保第一刻蚀酸液与第二刻蚀酸液混合均匀,避免不同玻璃基板的薄化品质出现差异。可以理解的是,若v1/v2<1/8,则表示第二刻蚀酸液的体积较大,那么混合后刻蚀残渣的浓度将偏小,不利于在薄化制程中快速越过成核期;若v1/v2>1/5,则表示加入的第一刻蚀酸液过多,容易造成原材料的浪费。因此,本实施例设置1/8≤v1/v2≤1/5,能够在降低生产成本的同时,解决薄化后玻璃表面存在凸点的问题。
需要说明的是,第一刻蚀酸液的体积v1和第二刻蚀酸液的体积v2取决于实际生产中待薄化的玻璃基板的数量,并且二者混合后的刻蚀酸液越多,循环的时间也应当越长,本申请不对第一刻蚀酸液的体积v1、第二刻蚀酸液的体积v2以及二者的循环时间作出限定。
可选地,在上述步骤s4中,利用混合得到的刻蚀酸液对玻璃基板的待薄化表面进行薄化处理的步骤,包括:
将玻璃基板固定于承载台;
利用喷嘴将混合得到的刻蚀酸液喷淋至玻璃基板的待薄化表面,将玻璃基板减薄至第一厚度。
图5所示为图2实施例所提供的玻璃基板的薄化方法的一种示意图。具体地,如图5所示,利用混合得到的刻蚀酸液对待薄化表面进行减薄处理时,首先将玻璃基板10固定于承载台,可选地,承载台包括滚轮20,位于承载台上方的喷嘴30可将混合后的刻蚀酸液均匀地喷淋在玻璃基板10的待薄化表面,该过程中产生的刻蚀残渣能够跟随剩余刻蚀酸液一同流入第一储液罐。当一片玻璃基板完成薄化后,持续滚动的滚轮可以将下一片玻璃基板传送至喷嘴下方,此种设计方式极大地提高了生产效率,因而本实施例所提供的玻璃基板的薄化方法能够满足批量生产的需求。
图6所示为本申请实施例所提供的刻蚀系统的另一种示意图。如图6所示,刻蚀系统还包括压滤机,压滤机分别与第一储液罐和第二储液罐连接;
利用喷嘴将混合得到的刻蚀酸液喷淋至玻璃基板的待薄化表面,将玻璃基板减薄至第一厚度的步骤,包括:
薄化处理过程中,喷淋后的剩余刻蚀酸液流入所述第一储液罐,监测第一储液罐内剩余刻蚀酸液中刻蚀残渣的第三浓度;
若第三浓度大于等于4%且小于13%,则开启压滤机,对第一储液罐内剩余刻蚀酸液中的至少部分刻蚀残渣进行过滤,并利用空气泵40将过滤后的剩余刻蚀酸液抽至第二储液罐;
若第三浓度小于4%,则利用空气泵40将第一储液罐内的剩余刻蚀酸液抽至第二储液罐;
若第三浓度大于等于13%,则预留出预设体积的剩余刻蚀酸液,作为新的生产周期使用的第一刻蚀酸液。
由于一个生产周期可以包括30~120张玻璃基板的薄化过程,一个生产周期中,每个玻璃基板完成薄化后的剩余刻蚀酸液都会经刻蚀线体流入第一储液罐,并在薄化其他玻璃基板时循环使用。但是,刻蚀残渣的浓度会随着减薄过程的进行不断变化,而刻蚀残渣的浓度又直接影响着玻璃基板的刻蚀速率及刻蚀品质,因此,本实施例可以对第一储液罐内剩余刻蚀酸液中刻蚀残渣的第三浓度进行监测。
具体而言,若第三浓度小于4%,则此时的刻蚀残渣浓度能够使镁离子浓度快速跃过成核期,因而可以利用空气泵40将第一储液罐内的剩余刻蚀酸液直接抽至第二储液罐进行循环使用;若第三浓度大于等于4%且小于13%,则表示剩余刻蚀酸液中的刻蚀残渣浓度偏高,此时需开启压滤机,对第一储液罐内刻蚀酸液中的至少部分刻蚀残渣进行过滤,使刻蚀残渣的浓度降至4%以下,再利用空气泵40将过滤后的刻蚀酸液抽至第二储液罐以进行循环使用;若第三浓度大于等于13%,那么利用压滤机过滤大量刻蚀残渣后,其过滤效果也会下降,无法再使刻蚀残渣浓度降至4%以下,因此,可以预留出预设体积的剩余刻蚀酸液,作为第一刻蚀酸液,并更换新的刻蚀酸液。
可见,本实施例通过监测第一储液罐内剩余刻蚀酸液中刻蚀残渣的第三浓度,能够将第三浓度控制在2.3%-4%的范围内,有效保证了当前生产周期内每一片玻璃基板的薄化品质;另一方面,由于相关技术中,通常在薄化完每一片玻璃基板之后都对剩余刻蚀酸液中的刻蚀残渣加以过滤,而本实施例则仅在第三浓度超过13%才开启压滤机,因此提高了生产效率。
可选地,利用混合得到的刻蚀酸液对玻璃基板的待薄化表面进行薄化处理的步骤之后,还包括:
将玻璃基板放置在碱液中浸泡,并对浸泡后的玻璃基板进行清洗。
应当理解,待薄化表面可以为玻璃基板的一个表面,也可以为玻璃基板的上下两个表面。图7所示为本申请实施例所提供的玻璃基板的薄化方法的另一种示意图,如图7所示,若对两个表面进行减薄处理,则可以同时开启玻璃基板10上下两个表面的喷嘴30;请继续参见图5,若仅对玻璃基板10的一个表面进行减薄处理,则可以在不需要薄化的另一表面贴附抗酸化薄膜,避免刻蚀酸液对其造成酸蚀。
本实施例中,完成对玻璃基板的薄化后,待薄化表面还会留有刻蚀酸液,因此可以先将玻璃基板浸泡于碱液中,利用酸碱中和去除玻璃表面的酸液,再进一步用水清洗,并用吸附垫擦拭干净,以避免残留的刻蚀酸液影响玻璃基板的薄化品质,从而有利于提升玻璃基板的薄化品质。
图8所示为本申请实施例所提供的显示面板的制作方法的一种流程图。请参见图8,本实施例提供一种显示面板的制作方法,包括:
步骤1、提供第一母板和第二母板;
步骤2、在第一母板或第二母板上滴注液晶,并对盒第一母板及所述第二母板;
步骤3、分别对第一母板的待薄化表面及第二母板的待薄化表面进行减薄处理;
步骤4、切割薄化后的第一母板和第二母板,得到多个显示面板;
其中,采用上述玻璃基板的薄化方法对第一母板和第二母板进行薄化处理。
在液晶显示面板的生产制造中,为了降低成本并进行批量化生产,通常是在一张较大的显示面板母板上制作多个显示面板,然后通过切割工序,将较大的显示面板母板切割为若干个显示面板的单体。
具体而言,第一母板可以为阵列母板/彩膜母板,第二母板可以为彩膜母板/阵列母板,采用液晶真空灌注技术在第一母板或第二母板上滴注液晶后,将第一母板与第二母板对盒并封口,完成成盒工艺,形成显示面板母板;最后,再经切割工艺,将显示面板母板切割为多个液晶显示面板。
其中,第一母板及第二母板的制作材料通常为玻璃,为了使显示面板更加轻薄,可以采用本申请所提供的玻璃基板的薄化方法对第一母板、第二母板的厚度分别进行减薄。
进一步地,由于第一母板和第二母板完成成盒工艺后才进行减薄,为了防止混合后的刻蚀酸液流入两个基板之间造成污染,可以先将uv胶均匀涂抹在显示面板母板的边缘缝隙处,此种设计方式能够有效避免刻蚀酸液进入显示面板内部,从而保证了显示面板的生产质量及性能。
需要说明的是,第一母板与第二母板的初始厚度可以相同或不同,并且二者所减薄的厚度亦可以相同或不同。例如,在显示面板轻薄化的需求下,分别将第一母板和第二母板由0.5mm(或以上)薄化至0.4mm、0.3mm、0.2mm甚至0.1mm。当然,第一母板和第二母板具体的减薄厚度应当根据工艺要求确定,本实施例对此不作限定。
显然,通过对显示面板的玻璃基板进行薄化处理,可以使玻璃基板的表面更加平整、光亮,有利于获得更加清晰的画质,随着玻璃基板的厚度减小,其占用的空间也会减小,进而节省出更多空间置放其他组件,如可以增加电池容量;玻璃基板薄化后,显示面板的重量有较大的下降空间,组装成的显示装置也会更加便携;与此同时,薄化后的玻璃基板还具备一定的柔性,也可以用于柔性显示面板的制作。
通过以上各实施例可知,本申请提供的玻璃基板的薄化方法及显示面板的制作方法,至少实现了如下的有益效果:
本申请所提供的玻璃基板的薄化方法包括刻蚀系统,刻蚀系统包括刻蚀线体、第一储液罐、第二储液罐以及连接第一储液罐和第二储液罐的旁通管道;其中,第一储液罐中存储有第一刻蚀酸液,将含有刻蚀残渣的第一刻蚀酸液与不含有刻蚀残渣的第二刻蚀酸液混合后,得到的刻蚀酸液中也含有一定浓度的刻蚀残渣。利用混合后的刻蚀酸液对玻璃基板进行薄化处理时,能够使刻蚀酸液快速度过成核期、达到稳定的离子增长期,从而避免刻蚀残渣在薄化制程前期因镁离子浓度上升而结合形成玻璃渣,解决了玻璃表面的凸起不良问题。另外,采用上述薄化方法制作而成的显示面板不仅具有良好的薄化品质,也更加满足用户的轻薄化需求。
虽然已经通过例子对本发明的一些特定实施例进行了详细说明,但是本领域的技术人员应该理解,以上例子仅是为了进行说明,而不是为了限制本发明的范围。本领域的技术人员应该理解,可在不脱离本发明的范围和精神的情况下,对以上实施例进行修改。本发明的范围由所附权利要求来限定。
起点商标作为专业知识产权交易平台,可以帮助大家解决很多问题,如果大家想要了解更多知产交易信息请点击 【在线咨询】或添加微信 【19522093243】与客服一对一沟通,为大家解决相关问题。
此文章来源于网络,如有侵权,请联系删除


