氢气制储系统及方法与流程



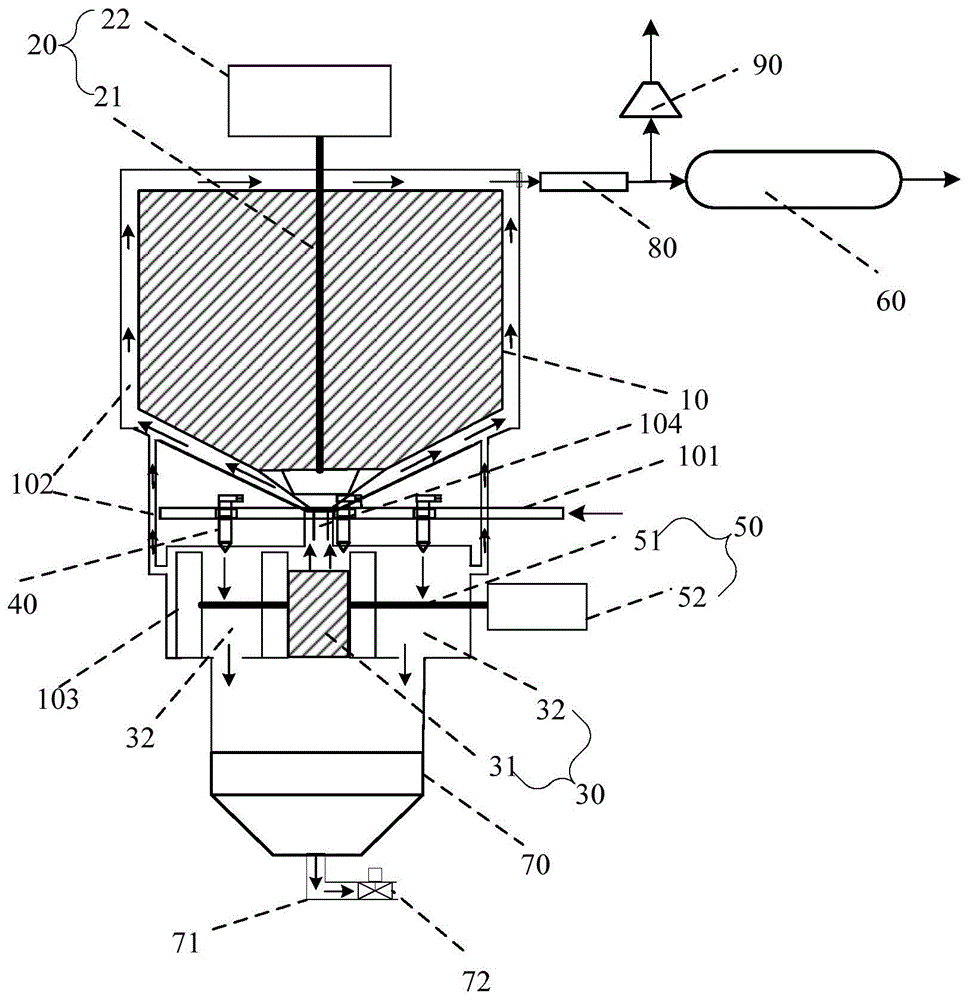
本申请涉及制氢技术领域,特别是涉及一种氢气制储系统及方法。
背景技术:
车载储氢技术是决定燃料电池应用的瓶颈所在,不管是采用气态高压储氢还是液态储氢都存在着成本高、安全性低等限制。近年来,铝水反应制氢受到了人们的很大关注,被认为是一种潜在的低成本、高安全车载储氢技术。
铝水反应制氢的优点有:铝作为地壳中含量最多的元素,来源广泛,价格低廉;且铝水反应过程中不产生有害物质,产物环境友好;其次,金属铝水解具有很高的氢气产量(1245ml/g),储氢密度高;另外,金属铝结构稳定,在与水反应之前不存在安全性问题。以上优势可以使得系统就会变得更加小型化且更加安全,在目前的几种现场制氢材料体系中,铝水反应最有可能实现工业化应用。
现阶段,基于铝水反应制氢的研究主要有两大问题:一是纯铝表面的致密氧化铝薄膜以及水解反应的沉淀,会附着在铝材料表面,限制铝的继续反应,降低产氢效率。目前,铝基复合材料,包括金属铝/无机盐、纳米铝、铝合金、金属铝/氢化物等体系的研究与发展,能够有效克服氧化铝薄膜以及水解沉淀带来的问题;第二个问题是铝水反应制氢反应器的研发问题。想要实现铝水反应的实际应用,还需要配备适当的铝水制氢设备,实现氢气的释放与应用。目前针对铝水反应制氢的研究技术,国内外已经有一些相关的设计与发明,但没有相关商业上的推广与使用。传统的制氢反应器,能够实现氢气的即产即用,但产氢效率较低。
技术实现要素:
基于此,针对传统的制氢反应器产氢效率较低得问题,本申请提供一种氢气制储系统及方法。
一种氢气制储系统,包括:
储料桶,用于盛放固体原料,一端设有出料口;
第一进料控制部件,至少部分设置于所述储料桶;
多级反应腔,包括多个腔室,与所述出料口对应设置的腔室作为反应腔,所述第一进料控制部件开启时,所述固体原料通过所述出料口进入所述反应腔;
多个相对固定设置的隔板,设置于所述多级反应腔腔内,相邻的两个所述隔板之间的间距与一个腔室的宽度相等;
第二进料控制部件,与所述反应腔对应设置,用于将液体原料输入至所述反应腔内;以及
物料转移部件,设置于所述多级反应腔,并与所述多个相对固定设置的隔板连接,用于推动所述隔板,以将所述反应腔内的剩余物料转移至其他腔室内。
在其中一个实施例中,所述第一进料控制部件包括:
第一活塞杆,设置于所述储料桶,与所述出料口对应设置;以及
第一步进电机,与所述第一活塞杆电连接,用于控制所述第一活塞杆在所述储料桶内往返运动,以使得所述固体原料通过所述出料口进入所述反应腔。
在其中一个实施例中,所述物料转移部件包括:
第二活塞杆,设置于所述多级反应腔,并与所述隔板连接;以及
第二步进电机,与所述第二活塞杆电连接,用于控制所述第二活塞杆在多级反应腔内往返运动,以将所述反应腔内的剩余物料转移至其他腔室内。
在其中一个实施例中,还包括和氢气管路,所述储氢装置通过氢气管路分别与每一个所述腔室连接。
在其中一个实施例中,所述氢气管路沿所述储料桶的外边缘设置。
在其中一个实施例中,还包括:
残料收集装置,与除所述反应腔以外的其他腔室连通,用于收集所述剩余物料。
在其中一个实施例中,还包括:
残料排出管路,设置于所述残料收集装置;以及
电磁阀,设置于所述残料排出管路上,用于控制所述剩余物料的排出。
在其中一个实施例中,还包括:
除杂器,与所述氢气管路连接,用于净化氢气;以及
安全阀,设置于所述氢气管路上,用于排出多余氢气。
一种氢气制储方法,包括:
利用第一进料控制部件定量控制固体原料进入反应腔内,并利用第二进料控制部件定量控制液体原料进入所述反应腔内,以在所述反应腔内生成氢气;
经预设时间后,利用物料转移部件将所述反应腔内的剩余物料转移至空腔内,并利用所述第一进料控制部件定量控制固体原料再次进入所述反应腔内,并利用所述第二进料控制部件定量控制液体原料再次进入所述反应腔内,以在所述反应腔内和所述空腔内均生成氢气。
在其中一个实施例中,还包括:
利用残料收集装置收集所述剩余物料;
当所述残料收集装置中的所述剩余物料高于预设值时,电磁阀开启,以控制所述剩余物料经残料排出管路排出。
上述氢气制储系统包括储料桶、第一进料控制部件、多级反应腔、多个相对固定设置的隔板、第二进料控制部件以及物料转移部件。所述储料桶用于盛放固体原料。所述储料桶的一端设有出料口。所述第一进料控制部件至少部分设置于所述储料桶。所述多级反应腔包括多个腔室。与所述出料口对应设置的腔室为反应腔。所述第一进料控制部件开启时,所述固体原料通过所述出料口进入所述反应腔。多个相对固定设置的隔板设置于所述多级反应腔腔内,相邻的两个所述隔板之间的间距与一个腔室的宽度相等。所述第二进料控制部件与每一个腔室对应设置,用于将液体原料输入至所述反应腔内。所述物料转移部件设置于所述多级反应腔,并与所述隔板连接,用于推动所述隔板,以将所述反应腔内的剩余物料转移至其他腔室内。上述氢气制储系统反应腔室独立存在,液体原料独立进入,节约了用水量的同时提高了反应物料与液体原料的有效利用率。并且设置多级反应腔,可以在多个腔室内进行制氢反应提高了反应速率,并且提高了固体原料的有效利用率,实现了快速供应氢气的效果。
附图说明
为了更清楚地说明本申请实施例或传统技术中的技术方案,下面将对实施例或传统技术描述中所需要使用的附图作简单地介绍,显而易见地,下面描述中的附图仅仅是本申请的一些实施例,对于本领域普通技术人员来讲,在不付出创造性劳动的前提下,还可以根据这些附图获得其他的附图。
图1为本申请一个实施例提供的氢气制储系统的结构示意图;
图2为本申请一个实施例提供的氢气制储系统反应制氢的局部示意图;
图3为本申请一个实施例提供的氢气制储系统反应物料转移的局部示意图;
图4为本申请一个实施例提供的氢气制储系统多级反应腔室示意图;
图5为本申请一个实施例提供的燃料电池系统与氢气制储系统的连接方式示意图;
图6为本申请一个实施例提供的氢气制储方法的流程示意图。
主要元件附图标号说明
10、储料桶;20、第一进料控制部件;21、第一活塞杆;22、第一步进电机;30、多级反应腔;31、反应腔;32、空腔;40、第二进料控制部件;50、物料转移部件;51、第二活塞杆;52、第二步进电机;60、储氢装置、70、残料收集装置;71、残料排出管路;72、电磁阀;80、除杂器;90、安全阀;101、外部水流通水管;102、氢气管路;103、隔板;104、出料口。
具体实施方式
为使本申请的上述目的、特征和优点能够更加明显易懂,下面结合附图对本申请的具体实施方式做详细的说明。在下面的描述中阐述了很多具体细节以便于充分理解本申请。但是本申请能够以很多不同于在此描述的其它方式来实施,本领域技术人员可以在不违背本申请内涵的情况下做类似改进,因此本申请不受下面公开的具体实施的限制。
可以理解,本申请所使用的术语“第一”、“第二”等可在本文中用于描述各种元件,但这些元件不受这些术语限制。这些术语仅用于将第一元件与另一个元件区分。举例来说,在不脱离本申请的范围的情况下,可以将第一获取模块称为第二获取模块,且类似地,可将第二获取模块称为第一获取模块。第一获取模块和第二获取模块两者都是获取模块,但其不是同一个获取模块。
需要说明的是,当元件被称为“设置于”另一个元件,它可以直接在另一个元件上或者也可以存在居中的元件。当一个元件被认为是“连接”另一个元件,它可以是直接连接到另一个元件或者可能同时存在居中元件。
除非另有定义,本文所使用的所有的技术和科学术语与属于本申请的技术领域的技术人员通常理解的含义相同。本文中在本申请的说明书中所使用的术语只是为了描述具体的实施例的目的,不是旨在于限制本申请。本文所使用的术语“及/或”包括一个或多个相关的所列项目的任意的和所有的组合。
目前,针对大型移动电源使用的铝水制氢系统,仍然存在着很多问题。首先,大型移动电源的氢气需求量高、耗氢速度快,传统的铝水制氢系统制氢量小,反应速率慢,并不能满足需求;其次,铝水制氢系统作为移动端的制储氢系统使用时,需要满足储氢密度高、储存能量高等要求,以满足移动端续航里程以及空间优化的需求。目前的技术集成度仍然很低,且不能实现产物的随产随排,增加了额外的废液收集系统,造成制储氢系统储氢密度低的现象。其中,储氢密度为储氢量与系统总质量的比。系统总质量包括了制氢装置的重量、所携带制氢材料的重量以及反应用水的重量。这就限制了铝水制氢系统在车载场景的应用与推广。因此,可应用于车载环境的高集成大速率铝水制氢系统设计研究还很缺乏。
针对上述现状,本申请提供一种氢气制储系统。所述氢气制储系统包括储料桶10、第一进料控制部件20、多级反应腔30、多个相对固定设置的隔板103、第二进料控制部件40以及物料转移部件50。所述储料桶10用于盛放固体原料。所述储料桶10的一端设有出料口104。所述第一进料控制部件20至少部分设置于所述储料桶10内。所述多级反应腔30包括多个腔室。所述多个腔室中的至少一个腔室与所述出料口104对应设置。与所述出料口104对应设置的腔室为反应腔31。所述第一进料控制部件20开启时,所述固体原料通过所述出料口104进入所述反应腔31。多个相对固定设置的隔板103设置于所述多级反应腔腔30内,相邻的两个所述隔板103之间的间距与一个腔室的宽度相等。所述第二进料控制部件40与所述反应腔31对应设置,用于将液体原料输入至所述反应腔31内。所述物料转移部件50设置于所述多级反应腔30,并与所述隔板103连接,用于推动所述隔板103,以将所述反应腔31内的剩余物料转移至其他腔室内。当然,所述第二进料控制部件40可以包括多个,每一个腔室上均对应设置一个第二进料控制部件40。
可以理解的是,所述固体原料不做具体限定,只要是制氢反应物即可。在一个实施例中,所述固体原料为铝基复合材料。所述铝基复合材料是一种通用材料,包含铝合金类材料、铝/无机盐复合材料、铝/金属氢化物材料、铝/铋/氢化物类材料等。在另一个实施例中,所述固体原料为氢化镁或钙。可以根据不同的使用环境去切换固体材料,能够帮助延长特种环境下燃料电池移动装置的续航里程。
具体请参见图1,所述储料桶10为一腔状结构,其一端具有出料口104,具有出料口104的一端为下端。在所述储料桶10上端可以开设有固态原料进料口。所述第一进料控制部件20的结构不做具体限定,只要可以控制进入所述反应腔31的固态原料的量即可。
在一个实施例中,所述第一进料控制部件20为液压活塞控制部件。所述第一进料控制部件20第一活塞杆21和第一步进电机22。所述第一活塞杆21设置于所述储料桶10内,并且在静置状态下,所述第一活塞杆21的端部与所述出料口104接触,避免所述固态原料进入所述反应腔31。所述第一步进电机22与所述第一活塞杆21电连接,用于控制所述第一活塞杆21在所述储料桶10内往返运动。可选地,所述第一步进电机22可以定时控制所述第一活塞杆21做间歇式运动,从而实现定量控制进料。可以根据燃料电池系统的氢气需求量设置所述第一步进电机22控制所述第一活塞杆21做间歇式运动的时间,以实现氢气需求量与制氢量的匹配。
所述多级反应腔30也为腔状结构,并利用可活动的且相对固定的隔板103将所述腔状结构分割为多个腔室。多个腔室可以包括反应腔31和空腔32。反应腔31和空腔32的数量均不作具体限定。具体请参见请参见图4,增加反应腔31,可以使得多级反应的连续进行,保证了制氢速率能够满足燃料电池电堆高氢气消耗量的需求。所述多级反应腔30设置在所述储料桶10的出料口104的下端。
所述第二进料控制部件40的数量可以与所述多级反应腔30的腔室的数量对应。任意一个第二进料控制部件40设置在外部水流通水管101上,并对应一个腔室设置。外部水流通水管101可以与储水罐连接。所述第二进料控制部件40可以为水喷淋器。
所述物料转移部件50的结构不做具体限定,只要可以推动所述隔板103,以将所述反应腔31内的剩余物料转移至其他腔室内即可。在一个实施例中,所述物料转移部件50包括第二活塞杆51和第二步进电机52。所述第二活塞杆51设置于所述多级反应腔30,并与所述隔板103连接。所述第二步进电机52与所述第二活塞杆51电连接,用于控制所述第二活塞杆51在多级反应腔30内往返运动。可选地,所述第二步进电机52可以定时控制所述第二活塞杆51做间歇式运动,从而实现定时控制排料。可以根据燃料电池系统的氢气需求量设置所述第二步进电机52控制所述第二活塞杆51做间歇式运动的时间。
所述氢气制储系统的工作方式为,相应质量的铝基复合材料储存在储料桶10内;储料桶10内的铝基复合材料通过第一进料控制部件20定量打入到反应腔31内,同时,外部水流经过外部水流通水管101、第二进料控制部件40进入到反应腔31内,发生铝水制氢反应,产生氢气与其他水解产物。
如图2(a)所示,静置状态下,第一进料控制部件20处于关闭状态;如图2(b)所示,在进料状态时,第一进料控制部件20开启,反应物料进入反应腔31内,与此同时第二进料控制部件40开启,反应用水定量打入反应腔31内;如图2(c)所示,进料结束后,第一进料控制部件20与第二进料控制部件40关闭,反应物料与反应水在反腔体内充分反应生成氢气。
如图3(a)所示为反应物料的制氢状态,制氢结束后固体产物、未反应的残渣以及多余的水分由物料转移部件50转移至空腔32,如图3(b)所示,未反应的残渣以及多余的水分此时仍在反应。随后进入排料/进料状态,如图3(c)所示,第二进料控制部件40开启,废料排出。如图3(d)所示,排料的同时,中间进料口开启,继续进行制氢反应。如图3(e)所示,随后,物料转移部件50向左移动,固体产物、未反应的残渣以及多余的水分被推至左侧空腔32内继续反应生成氢气;之后,如图3(f)所示,最左侧物料转移部件50打开,左侧的空腔32内的废料排出。至此,完成一个进料-反应-排料周期。
上述氢气制储系统包括储料桶10、第一进料控制部件20、多级反应腔30、第二进料控制部件40以及物料转移部件50。所述储料桶10用于盛放固体原料。所述储料桶10的一端设有出料口104。所述第一进料控制部件20设置于所述储料桶10内。所述多级反应腔30包括多个腔室。相邻腔室之间设置隔板103。所述多个腔室中的至少一个腔室与所述出料口104对应设置。此时,与所述出料口104对应设置的腔室为反应腔31。所述第一进料控制部件20开启时,所述固体原料通过所述出料口104进入所述反应腔31。所述第二进料控制部件40与每一个腔室对应设置,用于将液体原料输入至所述反应腔31内。所述物料转移部件50设置于所述多级反应腔30,并与所述隔板103连接,用于推动所述隔板103,以将所述反应腔31内的剩余物料转移至其他腔室内。上述氢气制储系统反应腔31室独立存在,液体原料独立进入,节约了用水量的同时提高了反应物料与液体原料的有效利用率。并且设置多级反应腔30,可以在多个腔室内进行制氢反应提高了反应速率,并且提高了固体原料的有效利用率,实现了快速供应氢气的效果。
在其中一个实施例中,所述氢气制储系统还包括储氢装置60。是储氢装置60通过氢气管路102分别与每一个所述腔室连接。在反应腔31或者在空腔32中反应生成的氢气可以通过相应的氢气管路102进入储氢装置60。可选地,所述沿所述储料桶10的外边缘设置。可选地,为了净化氢气,除去杂质,可以在进入储氢装置60前的氢气管路102上设置除杂器80。可选地,可以在氢气管路102上设置压力监测器和安全阀90。当压力监测器检测到压力过高时,开启所述安全阀90以排出多余氢气。此时,也可以根据压力监测器的检测结果控制第一步进电机22和第二步进电机52的转速,进而实现定量控制进料和排料。
在其中一个实施例中,所述氢气制储系统还包括残料收集装置70。残料收集装置70与除所述反应腔31以外的其他腔室(即空腔32)连通,用于收集所述剩余物料。在空腔32中固液混合物(如图1所示)进入残料收集装置70内,仍在反应,生成氢气经氢气管路102导出,提升了反应物料的有效利用率。通过分离储料桶10、反应腔31以及残料收集装置70,实现了高集成度氢气制储系统的设计。并且,残料收集装置70独立存在,确保生成产物不会覆盖在未反应的物料表面影响反应程度。
在其中一个实施例中,在一些空间受限的环境下,所述氢气制储系统还包括残料排出管路71和电磁阀72。
所述残料排出管路71设置于所述残料收集装置70。所述电磁阀72设置于所述残料排出管路71上,用于控制所述剩余物料的排出。所形成固液混合物经残料排出管、电磁阀72排出,当固液混合物的水位线低于临界线时,电磁阀72关闭。当固液混合物的水位线高于临界线时,电磁阀72重新开启。本申请通过设置残料排出管路71和电磁阀72实现了反应物残料的即时排出,减小系统重量与体积,提升了氢气制储系统的储氢密度。
燃料电池系统与氢气制储系统的连接方式如图5所示,主要包括燃料电池电堆、储水罐以及氢气制储系统。其工作方式为:氢气制储系统内产生干燥氢气,进入储水罐加湿后,进入到燃料电池电堆内反应;在燃料电池系统内,氢气与空气发生电化学反应生成水;生成水排出电堆后进入储水罐继续用于制储氢系统以及加湿系统使用。在该系统中,储水罐既可以为制储氢系统供应反应用水,又可以作为反应气的加湿系统,大大简化了系统的复杂程度,降低了系统整体的体积。通过循环水的有效利用,可以减轻所携带储水罐的重量,进一步提高了装置的储氢密度,从而满足了移动端续航里程以及空间优化的需求。
请参见图6,本申请提供一种氢气制储方法。所述氢气制储方法包括:
s10,利用第一进料控制部件20定量控制固体原料进入反应腔31内,并利用第二进料控制部件40定量控制液体原料进入所述反应腔31内,以在所述反应腔31内生成氢气。
s20,经预设时间后,利用物料转移部件50将所述反应腔31内的剩余物料转移至空腔32内,并利用所述第一进料控制部件20定量控制固体原料再次进入所述反应腔31内,并利用所述第二进料控制部件40定量控制液体原料再次进入所述反应腔31内,以在所述反应腔31内和所述空腔32内均生成氢气。
可以理解的是,所述固体原料不做具体限定,只要是制氢反应物即可。在一个实施例中,所述固体原料为铝基复合材料。所述铝基复合材料是一种通用材料,包含铝合金类材料、铝/无机盐复合材料、铝/金属氢化物材料、铝/铋/氢化物类材料等。在另一个实施例中,所述固体原料为氢化镁或钙。可以根据不同的使用环境去切换固体材料,能够帮助延长特种环境下燃料电池移动装置的续航里程。
在一个实施例中,所述第一进料控制部件20为液压活塞控制部件。所述第一进料控制部件20第一活塞杆21和第一步进电机22。所述第一活塞杆21设置于所述储料桶10内,并且在静置状态下,所述第一活塞杆21的端部与所述出料口104接触,避免所述固态原料进入所述反应腔31。所述第一步进电机22与所述第一活塞杆21电连接,用于控制所述第一活塞杆21在所述储料桶10内往返运动。可选地,所述第一步进电机22可以定时控制所述第一活塞杆21做间歇式运动,从而实现定量控制进料。可以根据燃料电池系统的氢气需求量设置所述第一步进电机22控制所述第一活塞杆21做间歇式运动的时间,以实现氢气需求量与制氢量的匹配。
多级反应腔30也为腔状结构,并利用可活动的隔板103将所述腔状结构分割为多个腔室。多个腔室可以包括反应腔31和空腔32。反应腔31和空腔32的数量均不作具体限定。具体请参见请参见图4,增加反应腔31,可以使得多级反应的连续进行,保证了制氢速率能够满足燃料电池电堆高氢气消耗量的需求。所述多级反应腔30设置在所述储料桶10的出料口104的下端。
所述第二进料控制部件40的数量可以与所述多级反应腔30的腔室的数量对应。任意一个第二进料控制部件40设置在外部水流通水管101上,并对应一个腔室设置。外部水流通水管101可以与储水罐连接。所述第二进料控制部件40可以为水喷淋器。
所述物料转移部件50的结构不做具体限定,只要可以推动所述隔板103,以将所述反应腔31内的剩余物料转移至其他腔室内即可。在一个实施例中,所述物料转移部件50包括第二活塞杆51和第二步进电机52。所述第二活塞杆51设置于所述多级反应腔30,并与所述隔板103连接。所述第二步进电机52与所述第二活塞杆51电连接,用于控制所述第二活塞杆51在多级反应腔30内往返运动。可选地,所述第二步进电机52可以定时控制所述第二活塞杆51做间歇式运动,从而实现定时控制排料。可以根据燃料电池系统的氢气需求量设置所述第二步进电机52控制所述第二活塞杆51做间歇式运动的时间。
上述氢气制储方法中,反应腔31室独立存在,液体原料独立进入,节约了用水量的同时提高了反应物料与液体原料的有效利用率。并且设置多级反应腔30,可以在多个腔室内进行制氢反应提高了反应速率,并且提高了固体原料的有效利用率,实现了快速供应氢气的效果。
在其中一个实施例中,所述氢气制储方法还包括:
利用残料收集装置70收集所述剩余物料。当所述残料收集装置70中的所述剩余物料高于预设值时,电磁阀72开启,以控制所述剩余物料经残料排出管路71排出。
可选地,当固液混合物的水位线低于临界线时,电磁阀72关闭。当固液混合物的水位线高于临界线时,电磁阀72重新开启。本申请通过设置残料排出管路71和电磁阀72实现了反应物残料的即时排出,减小系统重量与体积,提升了氢气制储系统的储氢密度。
以上所述实施例的各技术特征可以进行任意的组合,为使描述简洁,未对上述实施例中的各个技术特征所有可能的组合都进行描述,然而,只要这些技术特征的组合不存在矛盾,都应当认为是本说明书记载的范围。
以上所述实施例仅表达了本申请的几种实施方式,其描述较为具体和详细,但并不能因此而理解为对申请专利范围的限制。应当指出的是,对于本领域的普通技术人员来说,在不脱离本申请构思的前提下,还可以做出若干变形和改进,这些都属于本申请的保护范围。因此,本申请专利的保护范围应以所附权利要求为准。
起点商标作为专业知识产权交易平台,可以帮助大家解决很多问题,如果大家想要了解更多知产交易信息请点击 【在线咨询】或添加微信 【19522093243】与客服一对一沟通,为大家解决相关问题。
此文章来源于网络,如有侵权,请联系删除


