多级反应系统、锂离子多元正极材料前驱体及其制备方法及锂离子多元正极材料的制备方法与流程



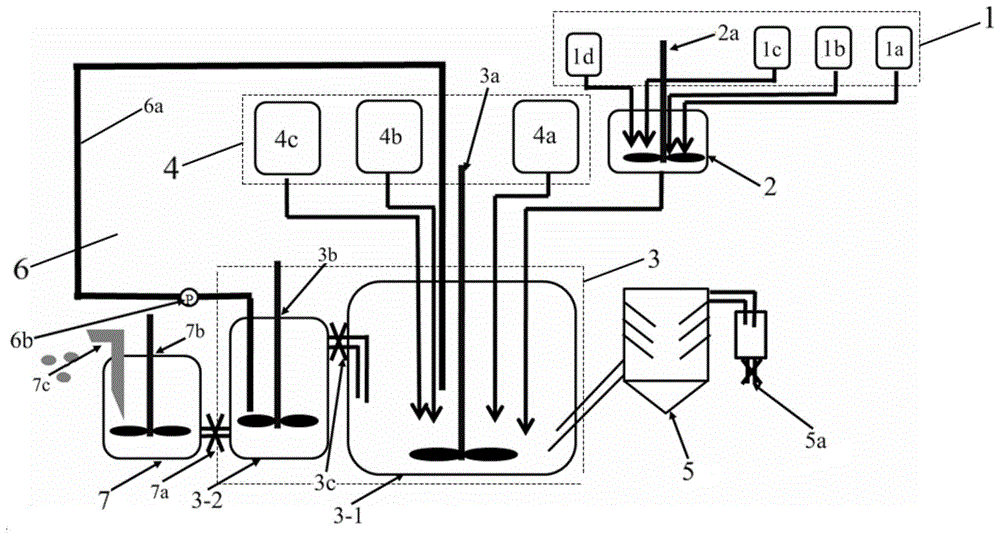
本发明涉及锂离子电池材料领域,特别涉及多级反应系统、锂离子多元正极材料前驱体及其制备方法及锂离子多元正极材料的制备方法。
背景技术:
锂离子电池作为二级电池,已经成熟商业化应用于3c电子产品、移动电源、电动工具及电动自行车等小型动力电池领域,所使用的正极材料主要包括磷酸铁锂、锰酸锂、钴酸锂及三元材料等,其实际比容量均低于200ma·h/g。随着全球能源格局的改变及镍钴锰资源的供应限制,具有高比容量(>250ma·h/g)、低成本的富锂锰基正极材料引起了研究人员的广泛关注,有望商业化作为下一代动力电池的正极材料,例如混合动力车(hev)或者纯电动车(ev)。
目前合成富锂锰基三元材料的方法主要包括高温固相法、溶胶凝胶法、水热合成法及共沉淀法等。其中,共沉淀法在液相化学合成粉体材料中应用最为广泛,产物中的有效组成可以实现原子、分子级别的均匀混合,设备简单,操作容易。
但是,受制于该工艺严格的生产条件,存在早期晶体颗粒成长过快过大,最终所制备的前驱体颗粒粒径分布宽,颗粒振实密度低等不足。例如cn108054371a公开了一种富锂锰基正极材料的制备方法,采用共沉淀法制备富锂锰基材料的前驱体,然而,其共沉淀方法所得前驱体便存在上述问题(颗粒粒径分布宽、振实密度低,电化学性能欠佳等),还需要进行后续水热处理来调整颗粒微观结构以期改善电化学性能,使流程繁杂,成本增加,且改善效果欠佳。而近年来很多方法集中在多元正极材料前驱体合成工艺上,但是都存在前驱体工艺放大后存在不可控或者难以控制等情况,从而限制了后续成品正极材料性能提升空间。
技术实现要素:
有鉴于此,本发明的目的在于提供一种多级反应系统、锂离子多元正极材料前驱体及其制备方法及锂离子多元正极材料的制备方法。本发明提供的多级反应系统和锂离子多元正极材料前驱体的制备方法能够有效缩窄富锂锰基材料前驱体的粒径分布、提高颗粒振实密度,还能够减小材料一次颗粒层间距,提升富锂锰基材料的电化学性能。
本发明提供了一种多级反应系统,包括:
原料罐(1);
进料口与所述原料罐(1)的出料口相连通的配盐釜(2);
进料口与所述配盐釜(2)的出料口相连通的反应釜(3);
出料口与所述反应釜(3)的配料口相连通的配料罐(4);
进料口与所述反应釜(3)的抽液口相连通的抽液釜(5);
进料口与所述反应釜(3)的出料口相连通的陈化釜(7);
所述反应釜(3)为相互串联的两级反应釜;其中,一级反应釜(3-1)与所述配盐釜(2)、配料罐(4)及抽液釜(5)相连通,二级反应釜(3-2)与所述陈化釜(7)相连通;
所述一级反应釜(3-1)和二级反应釜(3-2)之间连通有循环装置(6);
所述循环装置(6)包括:循环管(6a)和设置所述循环管(6a)上的循环泵(6b);所述循环管(6a)的一端开口伸入所述一级反应釜(3-1)内,另一端开口伸入所述二级反应釜(3-2)内。
优选的,所述一级反应釜(3-1)的容积为200~10000l,高度为50~300cm;
所述二级反应釜(3-2)的容积为50~90000l,高度为65~650cm;
所述循环管(6a)的一端从一级反应釜(3-1)的顶部竖直伸入一级反应釜(3-1)内,且端口的高度为一级反应釜(3-1)高度的15%~35%;
所述循环管(6a)的另一端从二级反应釜(3-2)的顶部竖直伸入二级反应釜(3-2)内,且端口的高度为二级反应釜(3-2)高度的15%~35%;
所述循环管(6a)的内径为40~160cm。
优选的,所述抽液釜(5)的排液管上设置有第一放液阀(5a);
所述一级反应釜(3-1)与二级反应釜(3-2)之间的输料管上设置有第二放液阀(3c);
所述二级反应釜(3-2)与陈化釜(7)之间的输料管上设置有第三放液阀(7a);
所述配盐釜(2)内设置有第一搅拌装置(2a);
所述一级反应釜(3-1)内设置有第二搅拌装置(3a);
所述二级反应釜(3-2)内设置有第三搅拌装置(3b);
所述陈化釜(7)内设置有第四搅拌装置(7b)。
优选的,所述原料罐(1)包括:分别与所述配盐釜并联连通的镍盐溶液罐(1a)、钴盐溶液罐(1b)、锰盐溶液罐(1c)和添加剂溶液罐(1d);
所述配料罐(4)包括:分别与所述一级反应釜(3-1)并联连通的沉淀剂溶液罐(4a)、络合剂溶液罐(4b)和助剂溶液罐(4c)。
本发明还提供了一种锂离子多元正极材料前驱体的制备方法,利用上述技术方案中所述的多级反应系统进行制备,具体包括以下步骤:
a)将原料罐中的物料送至配盐釜中,在配盐釜中混合,得到混合盐溶液;
b)将配盐釜中的混合盐溶液送至一级反应釜中,同时,将配料罐中的配料送至一级反应釜中,在搅拌条件下,所述混合盐溶液与配料在一级反应釜中进行共沉淀反应;
c)在所述共沉淀反应的过程中,通过抽液釜将一级反应釜内的上清液抽出,至一级反应釜内的物料达到目标固含量;之后,将一级反应釜内的物料向二级反应釜内输送,直至二级反应釜内的物料达到目标液位;然后开启循环装置,使一级反应釜内的物料与二级反应釜内的物料进行内循环;
d)经步骤c)中的内循环后,将二级反应釜内的物料输送至陈化釜中进行陈化;经陈化后,将陈化釜内的物料排出,得到锂离子多元正极材料前驱体;
所述锂离子多元正极材料前驱体具有式(1)或式(2)所示结构:
lixniycozmnamh(oh)2式(1),lixniycozmnamhco3式(2);
其中,
1<x≤1.6,0.1<y≤0.95,0.1<z≤0.5,0.1<a≤0.8,0.01<h≤0.15;
m为mg、al、ti、zr、nb、ca和sr的一种或几种。
优选的,所述步骤d)包括:
d1)经步骤c)中的内循环后,将二级反应釜内的物料输送至陈化釜中进行陈化;经陈化后,将陈化釜内的物料排出,得到锂离子多元正极材料前驱体;
d2)在步骤d1)中开始陈化的同时,通过抽液釜将一级反应釜内的上清液抽出,至一级反应釜内的物料达到目标固含量;之后,将一级反应釜内的物料向二级反应釜内输送,直至二级反应釜内的物料达到目标液位;之后,开启循环装置,使一级反应釜内的物料与二级反应釜内的物料进行内循环;
d3)在步骤d1)中陈化结束且陈化釜内的物料排出后,将所述步骤d2)中内循环后二级反应釜内的物料输送至陈化釜中进行陈化;经陈化后,将陈化釜内的物料排出,再次得到锂离子多元正极材料前驱体;如此重复处理,不断的从陈化釜中排出锂离子多元正极材料前驱体。
优选的,所述步骤a)具体包括:将镍盐溶液罐中的镍盐化合物溶液、钴盐溶液罐中的钴盐化合物溶液、锰盐溶液罐中的锰盐化合物溶液和添加剂溶液罐中的添加剂溶液分别送至配盐釜中,在配盐釜中混合,得到混合盐溶液;
所述步骤a)中,所述共沉淀反应的条件为:在保护性气体氛围下进行,温度为50~65℃,ph值为7~12,搅拌速率为300~1500r/min;
所述步骤b)中,所述将配料罐中的配料送至一级反应釜中具体包括:将沉淀剂溶液罐中的沉淀剂溶液、络合剂溶液罐中的络合剂溶液和助剂溶液罐中的助剂溶液分别送至一级反应釜中;
所述步骤c)中,所述内循环的流速为1~200m3/min;所述陈化的温度为40~60℃;所述目标固含量为15wt%~35wt%;所述目标液位为二级反应釜高度的60%~95%。
优选的,所述镍盐化合物、钴盐化合物和锰盐化合物的摩尔比为(0.5~9):(0.5~3):(0.5~9);
所述混合盐溶液中镍盐化合物、钴盐化合物和锰盐化合物总的摩尔浓度为0.5~5mol/l;
所述镍盐化合物选自硫酸镍、乙酸镍和硝酸镍中的一种或几种;
所述钴盐化合物选自硫酸钴、乙酸钴和硝酸钴中的一种或几种;
所述锰盐化合物选自硫酸锰、乙酸锰和硝酸锰中的一种或几种;
所述添加剂选自硫酸镁、铝酸铵、硫酸锆、醋酸铌、醋酸钙和硝酸锶中的一种或几种;
所述沉淀剂选自氢氧化钠、碳酸钠、碳酸铵和碳酸氢铵中的一种或几种;
所述沉淀剂溶液的浓度为0.5~5mol/l;
所述络合剂选自氨水、尿素和柠檬酸钠中的一种或几种;
所述络合剂溶液的浓度为0.5~4mol/l;
所述助剂为表面活性剂;
所述助剂溶液的浓度为0.1~2mol/l。
本发明还提供了一种上述技术方案中所述的制备方法制得的锂离子多元正极材料前驱体。
本发明还提供了一种锂离子多元正极材料的制备方法,包括:
将锂离子多元正极材料前驱体与锂盐混合烧结,得到式(3)所示的锂离子多元正极材料;
li(lixniycozmnamh)o2式(3);
其中,
1<x≤1.6,0.1<y≤0.95,0.1<z≤0.5,0.1<a≤0.8,0.01<h≤0.15;
m为mg、al、ti、zr、nb、ca和sr的一种或几种;
所述锂离子多元正极材料前驱体为上述技术方案中所述的锂离子多元正极材料前驱体。
本发明提供的多级反应系统和锂离子多元正极材料前驱体的制备方法,通过设置两级反应釜,在两级反应釜之间设置循环装置,以及两级反应釜内设置搅拌装置,能够从多方面有效提升所制材料的性能。具体的,通过多级反应共沉淀,可使合成的前驱体,颗粒粒径可控均一,形貌规整,振实密度高,能够改进正极材料的结构稳定性,提高正极材料的循环性能;而且通过两级反应结合内循环,增加了反应中的能量,促进反应的进行,利于多元金属离子供沉淀过程中在搅拌分数过程中内循环的作用下,加快不同金属离子的耦合速度,不同沉积系数的金属离子在双搅拌和循环流体的共同作用下能够精确按比例生成更多的晶核、抑制晶核生长、避免在共沉淀过程中和陈化过程中二次颗粒之间过多的团聚;同时,多级反应及内循环的作用使正极材料前驱体的一次颗粒层间距减小、增大了材料的比表面积以及振实密度,降低了循环过程中的界面内阻,提高了正极材料的倍率性能,从而提高锂离子电池的能量密度。
实验结果表明,本发明制得的锂离子多元正极材料前驱体的粒径多分散指数pdi在0.15以下,振实密度在2.0g/ml以上。
附图说明
为了更清楚地说明本发明实施例或现有技术中的技术方案,下面将对实施例或现有技术描述中所需要使用的附图作简单地介绍,显而易见地,下面描述中的附图仅仅是本发明的实施例,对于本领域普通技术人员来讲,在不付出创造性劳动的前提下,还可以根据提供的附图获得其他的附图。
图1为本发明实施例提供的富锂锰基材料前驱体反应系统的结构示意图;
图2为实施例1所得前驱体的xrd测试图;
图3为实施例1所得前驱体的粒径分布图;
图4为实施例1所得前驱体的sem图;
图5为实施例1所得正极材料的电化学性能测试图;
图6为实施例2所得前驱体的粒径分布图;
图7为实施例2所得前驱体的sem图;
图8为实施例2所得正极材料的电化学性能测试图;
图9为实施例3所得前驱体的粒径分布图;
图10为实施例3所得前驱体的sem图;
图11为实施例3所得正极材料的电化学性能测试图。
具体实施方式
本发明提供了一种多级反应系统,包括:
原料罐1;
进料口与所述原料罐1的出料口相连通的配盐釜2;
进料口与所述配盐釜2的出料口相连通的反应釜3;
出料口与所述反应釜3的配料口相连通的配料罐4;
进料口与所述反应釜3的抽液口相连通的抽液釜5;
进料口与所述反应釜3的出料口相连通的陈化釜7;
所述反应釜3为相互串联的两级反应釜;其中,一级反应釜3-1与所述配盐釜2、配料罐4及抽液釜5相连通,二级反应釜3-2与所述陈化釜7相连通;
所述一级反应釜3-1和二级反应釜3-2之间连通有循环装置6;
所述循环装置6包括:循环管6a和设置所述循环管6a上的循环泵6b;所述循环管6a的一端开口伸入所述一级反应釜3-1内,另一端开口伸入所述二级反应釜3-2内。
参见图1,图1为本发明实施例提供的富锂锰基材料前驱体反应系统的结构示意图。其中,1为原料罐,1a为镍盐溶液罐,1b为钴盐溶液罐,1c为锰盐溶液罐,1d为添加剂溶液罐;2为配盐釜,2a为第一搅拌装置;3为反应釜,3-1为一级反应釜,3-2为二级反应釜,3a为第二搅拌装置,3b为第三搅拌装置,3c为第二放液阀;4为配料罐,4a为沉淀剂溶液罐,4b为络合剂溶液罐,4c为助剂溶液罐;5为抽液釜,5a为第一放液阀;6为循环装置,6a为循环管,6b为循环泵;7为陈化釜,7a为第三放液阀,7b为第四搅拌装置,7c为陈化釜的出料口。
原料罐1主要用于配制富锂锰基前驱体的各种原料,其出料口与配盐釜2相连通,各原料通过原料罐1送入配盐釜2中,将各原料混匀。在本发明的一些实施例中,原料罐1包括相互并联的4个原料罐:镍盐溶液罐1a、钴盐溶液罐1b、锰盐溶液罐1c和添加剂溶液罐1d。上述4个原料罐的出料口分别与配盐釜2相连通,通过各原料罐将相应的原料分别送入配盐釜2中。其中,以镍盐溶液罐1a为例,其用于将镍盐与水混匀配制成镍盐溶液并储存,以及在系统启动运行时将镍盐溶液向配盐釜2输送,其它原料罐同理。
配盐釜2的进料口与原料罐1的出料口相连通,用于接收来自原料罐1的原料,并将接收的原料混匀。在本发明的一些实施例中,配盐釜2的进料口设置在配盐釜2的顶部。在本发明的一些实施例中,配盐釜2设置有4个进料口,分别与上述4个原料罐1a、1b、1c、1d的出料口相连通。
在本发明的一些实施例中,配盐釜2内设置有第一搅拌装置2a。所述第一搅拌装置2a的结构没有特殊限制,为本领域技术人员熟知的常规搅拌装置即可,具体包括:搅拌轴,与搅拌轴的一端连接的传动装置,与搅拌轴的另一端连接的搅拌桨叶;其中,搅拌轴竖直伸入配盐釜2内,搅拌桨叶连接在搅拌轴底部且位于配盐釜2内,传动装置连接在搅拌轴的顶部且位于配盐釜2外部、固定于配盐釜2的顶盖上。优选的,沿搅拌轴自上而下的方向,所述搅拌桨叶包括上下两层;上层桨叶和下层桨叶的桨叶优选为直叶圆盘涡轮桨。在本发明的一些实施例中,所述配盐釜2的容积为0.2~5l,高度为50~250cm;其中,上层浆叶与下层桨叶之间的垂直距离为20~250cm,上层桨叶距离配盐釜2顶部的垂直距离为20~150cm;所述上层桨叶形成的圆盘直径为10~80cm,所述下层桨叶形成的圆盘直径为10~80cm。通过上述第一搅拌装置2a将配盐釜2内接收的各种物料搅拌混合均匀,形成混合盐溶液。
反应釜3为相互串联的两级反应釜:一级反应釜3-1和二级反应釜3-2。
一级反应釜3-1与配盐釜2的出料口相连通,用于接收来自配盐釜2中配好的混合盐溶液。
一级反应釜3-1还与配料罐4的出料口相连通,接收来自配料罐4的配料,并将配料与来自配盐釜2的混合盐溶液进一步混合、反应。在本发明的一些实施例中,所述配料罐4包括3个相互并联的配料罐:沉淀剂溶液罐4a、络合剂溶液罐4b和助剂溶液罐4c。上述3个配料罐的出料口分别与一级反应釜3-1相连通,通过各配料罐将相应的配料送入一级反应釜3-1中。其中,以沉淀剂溶液罐4a为例,其用于将沉淀剂与水混匀配制成沉淀剂溶液并储存,以及在系统启动运行时将沉淀剂溶液向一级反应釜3-1输送,其它配料罐同理。
在本发明的一些实施例中,一级反应釜3-1的进料口设置在一级反应釜3-1的顶部。在本发明的一些实施例中,一级反应釜3-1设置有4个进料口,分别与配盐釜2的出料口以及上述3个配料罐4a、4b、4c的出料口相连通。
在本发明的一些实施例中,上述3个配料罐4a、4b、4c及配盐釜2与一级反应釜3-1之间的4个连通管道上分别设置有计量泵,将混合盐溶液、沉淀剂溶液、络合剂溶液和助剂溶液分别通过计量泵送入一级反应釜3-1内。
在本发明的一些实施例中,一级反应釜3-1内设置有第二搅拌装置3a。所述第二搅拌装置3a的结构没有特殊限制,为本领域技术人员熟知的常规搅拌装置即可,具体包括:搅拌轴,与搅拌轴的一端连接的传动装置,与搅拌轴的另一端连接的搅拌桨叶;其中,搅拌轴竖直伸入一级反应釜3-1内,搅拌桨叶连接在搅拌轴底部且位于一级反应釜3-1内,传动装置连接在搅拌轴的顶部且位于一级反应釜3-1外部、固定于一级反应釜3-1的顶盖上。优选的,沿搅拌轴自上而下的方向,所述搅拌桨叶包括上下两层;上层桨叶和下层桨叶的桨叶优选为直叶圆盘涡轮桨。在本发明的一些实施例中,所述一级反应釜3-1的容积为200~10000l,高度为50~300cm;其中,上层浆叶与下层桨叶之间的垂直距离为15~150cm,上层桨叶距离一级反应釜3-1顶部的垂直距离为15~50cm;所述上层桨叶形成的圆盘直径为10~90cm,所述下层桨叶形成的圆盘直径为10~90cm。通过上述第二搅拌装置3a将一级反应釜3-1内接收的各种物料搅拌混合均匀,并进行共沉淀反应,得到镍钴锰前驱体混合溶液。
一级反应釜3-1还与抽液釜5相连通,抽液釜5的出液管道上设置有第一放液阀5a。抽液釜5用于将一级反应釜3-1内混合体系中的上清液抽出,提高一级反应釜3-1内混合体系的固含量。具体的,在一级反应釜3-1内物料搅拌混匀后,开启加热,一级反应釜3-1内物料进行共沉淀反应,反应过程中,打开第一放液阀5a并通过抽液釜5将一级反应釜3-1内的上清液抽出并排掉,使一级反应釜3-1内混合体系的固含量达到一定程度,再关闭第一放液阀5a,停止抽液釜5的抽液。
二级反应釜3-2的进料口与一级反应釜3的出料口相连通,用于接收来自一级反应釜3-1的物料。
在本发明的一些实施例中,二级反应釜3-2内设置有第三搅拌装置3b。所述第三搅拌装置3b的结构没有特殊限制,为本领域技术人员熟知的常规搅拌装置即可,具体包括:搅拌轴,与搅拌轴的一端连接的传动装置,与搅拌轴的另一端连接的搅拌桨叶;其中,搅拌轴竖直伸入二级反应釜3-2内,搅拌桨叶连接在搅拌轴底部且位于二级反应釜3-2内,传动装置连接在搅拌轴的顶部且位于二级反应釜3-2外部、固定于二级反应釜3-2的顶盖上。优选的,沿搅拌轴自上而下的方向,所述搅拌桨叶包括上下两层;上层桨叶和下层桨叶的桨叶优选为直叶圆盘涡轮桨。在本发明的一些实施例中,所述二级反应釜3-2的容积为50~90000l,高度为65~650cm;其中,上层浆叶与下层桨叶之间的垂直距离为10~190cm,上层桨叶距离二级反应釜3-2顶部的垂直距离为10~50cm;所述上层桨叶形成的圆盘直径为10~90cm,所述下层桨叶形成的圆盘直径为10~90cm。通过上述第三搅拌装置3b将二级反应釜3-2内接收的各种物料搅拌混合均匀。
在本发明的一些实施例中,所述一级反应釜3-1与二级反应釜3-2之间的输料管上设置有第二放液阀3c,通过第二放液阀3c控制一级反应釜3-1与二级反应釜3-2之间物料输送的开启和闭停。具体的,当一级反应釜3-1内物料通过抽液达到一定固含量后,打开第二放液阀3c,一级反应釜3-1开始向二级反应釜3-2内输送物料,同时开启第三搅拌装置3b,对二级反应釜3-2内的物料进行搅拌。
一级反应釜3-1和二级反应釜3-2之间连通有循环装置6;所述循环装置6包括:循环管6a和设置所述循环管6a上的循环泵6b;所述循环管6a的一端开口伸入所述一级反应釜3-1内,另一端开口伸入所述二级反应釜内3-2。通过上述循环装置6与第二放液阀3c的配合,能够使一级反应釜3-1与二级反应釜3-2的物料之间形成内循环。
在本发明的一些实施例中,循环管6a的一端从一级反应釜3-1的顶部竖直伸入一级反应釜3-1内,且端口的高度为一级反应釜高度3-1的15%~35%;循环管6a的另一端从二级反应釜3-2的顶部竖直伸入二级反应釜3-2内,且端口的高度为二级反应釜3-2高度的15%~35%。其中,端口的高度是指循环管端口距离反应釜底部之间的垂直距离。在本发明的一些实施例中,所述循环管6a的内径为40~160cm。具体的,一级反应釜3-1向二级反应釜3-2内输送物料,并开启第三搅拌装置3b对二级反应釜3-2内的物料进行搅拌,当二级反应釜3-2内的物料达到一定液位后,打开循环装置6(具体为开启循环管上的循环泵),使一级反应釜3-1与二级反应釜3-2的物料之间形成内循环(具体为二级反应釜3-2的物料通过循环管6a又回到一级反应釜3-1内,一级反应釜3-1内的物料通过第二放液阀3c又持续输送至二级反应釜3-2内,使物料在一级反应釜3-1与二级反应釜3-2之间形成循环),整个反应体系形成内外循环。内循环一定时间后,关闭循环装置6(通过停止循环泵来实现闭停),进行后续陈化程序。
本发明中,所述循环泵6b优选为高速循环泵,优选通过循环装置6的循环泵6b控制内循环的流速为1~200m3/min,更优选为控制每分钟流量为一级反应釜3-1容积的5~20倍。
本发明通过设置两级反应釜,在两级反应釜之间设置循环装置,以及两级反应釜内设置搅拌装置,能够从多方面有效提升所制材料的性能。具体的,通过多级反应共沉淀,可使合成的前驱体,颗粒粒径可控均一,形貌规整,振实密度高,能够改进正极材料的结构稳定性,提高正极材料的循环性能;而且通过两级反应结合内循环,增加了反应中的能量,促进反应的进行,利于多元金属离子供沉淀过程中在搅拌分数过程中内循环的作用下,加快不同金属离子的耦合速度,不同沉积系数的金属离子在双搅拌和循环流体的共同作用下能够精确按比例生成更多的晶核、抑制晶核生长、避免在共沉淀过程中和陈化过程中二次颗粒之间过多的团聚;同时,多级反应及内循环的作用使正极材料前驱体的一次颗粒层间距减小、增大了材料的比表面积以及振实密度,降低了循环过程中的界面内阻,提高了正极材料的倍率性能,从而提高锂离子电池的能量密度。
陈化釜7的进料口与二级反应釜3-2的出料口相连通,用于接收二级反应釜3-2的物料,对其陈化。
在本发明的一些实施例中,陈化釜7内设置有第四搅拌装置7b。所述第四搅拌装置7b的结构没有特殊限制,为本领域技术人员熟知的常规搅拌装置即可,具体包括:搅拌轴,与搅拌轴的一端连接的传动装置,与搅拌轴的另一端连接的搅拌桨叶;其中,搅拌轴竖直伸入陈化釜7内,搅拌桨叶连接在搅拌轴底部且位于陈化釜7内,传动装置连接在搅拌轴的顶部且位于陈化釜7外部、固定于陈化釜7的顶盖上。优选的,沿搅拌轴自上而下的方向,所述搅拌桨叶包括上下两层;上层桨叶和下层桨叶的桨叶优选为直叶圆盘涡轮桨。在本发明的一些实施例中,所述陈化釜7的容积为20~200l,高度为35~150cm;其中,上层浆叶与下层桨叶之间的垂直距离为10~80cm,上层桨叶距离陈化釜7顶部的垂直距离为10~40cm;所述上层桨叶形成的圆盘直径为10~50cm,所述下层桨叶形成的圆盘直径为10~50cm。通过上述第四搅拌装置7b将陈化釜7内接收的各种物料搅拌混合均匀。
在本发明的一些实施例中,二级反应釜3-2与陈化釜7之间的输料管上设置有第三放液阀7a,通过开关第三放液阀7a控制二者之间物料的输送。
具体的,当一级反应釜3-1与二级反应釜3-2之间内循环一定时间后,关闭内循环,打开第三放液阀7a,二级反应釜3-2的物料向陈化釜7中输送,在陈化釜7中进行陈化。其中,在陈化釜7中料满后即可关闭第三放液阀7a,停止向陈化釜7中输料,使陈化釜7中的物料进行陈化。陈化一定时间后,即可将陈化釜7中的物料从出料口7c排出,得到锂离子多元正极材料前驱体。本发明中,所述陈化的温度优选为40~60℃,陈化的时间优选为1~35h。
本发明中,在陈化釜7开始陈化的同时,打开第一放液阀5a,通过抽液釜5对一级反应釜3-1进行抽上清液,至一级反应釜3-1内物料的固含量达到一定程度后,停止抽上清液;打开第二放液阀3c,使一级反应釜3-1向二级反应釜3-2输料,待二级反应釜3-2内的物料达到一定液位后,开启循环装置6,使一级反应釜3-1与二级反应釜3-2之间形成内循环;循环一定时长后,关闭内循环,打开第三放液阀7a,二级反应釜3-2继续向陈化釜7中输送物料,在陈化釜7中进行陈化。陈化一定时间后,将陈化釜7中的物料再次排出,从而再次得到锂离子多元正极材料前驱体。如此重复进行上述过程,从而不断的得到锂离子多元正极材料前驱体。
本发明中,在反应釜3进行共沉淀反应以及陈化釜7进行陈化的过程中,优选控制搅拌一直持续进行。本发明中,上述含两级反应釜的整个反应体系可以为连续式,也可以为间歇式。
本发明中,在陈化釜7排出锂离子多元正极材料前驱体后,优选还进行:水洗、脱水和干燥。经上述后处理后,即可得到锂离子多元正极材料前驱体。在本发明的一些实施例中,所述锂离子多元正极材料前驱体为富锂锰基材料前驱体。
本发明提供了一种锂离子多元正极材料前驱体的制备方法,利用上述技术方案中所述的多级反应系统进行制备,具体包括以下步骤:
a)将原料罐中的物料送至配盐釜中,在配盐釜中混合,得到混合盐溶液;
b)将配盐釜中的混合盐溶液送至一级反应釜中,同时,将配料罐中的配料送至一级反应釜中,在搅拌条件下,所述混合盐溶液与配料在一级反应釜中进行共沉淀反应;
c)在所述共沉淀反应的过程中,通过抽液釜将一级反应釜内的上清液抽出,至一级反应釜内的物料达到目标固含量;之后,将一级反应釜内的物料向二级反应釜内输送,直至二级反应釜内的物料达到目标液位;然后开启循环装置,使一级反应釜内的物料与二级反应釜内的物料进行内循环;
d)经步骤c)中的内循环后,将二级反应釜内的物料输送至陈化釜中进行陈化;经陈化后,将陈化釜内的物料排出,得到锂离子多元正极材料前驱体;
所述锂离子多元正极材料前驱体具有式(1)或式(2)所示结构:
lixniycozmnamh(oh)2式(1),lixniycozmnamhco3式(2);
其中,
1<x≤1.6,0.1<y≤0.95,0.1<z≤0.5,0.1<a≤0.8,0.01<h≤0.15;
m为mg、al、ti、zr、nb、ca和sr的一种或几种。
关于步骤a):
本发明中,所述步骤a)具体包括:将镍盐溶液罐中的镍盐化合物溶液、钴盐溶液罐中的钴盐化合物溶液、锰盐溶液罐中的锰盐化合物溶液和添加剂溶液罐中的添加剂溶液分别送至配盐釜中,在配盐釜中混合,得到混合盐溶液。
本发明中,所述镍盐化合物溶液中的镍盐化合物优选为硫酸镍、乙酸镍和硝酸镍中的一种或几种。所述镍盐化合物溶液优选为镍盐化合物的水溶液,即将镍盐化合物与水混合,形成镍盐化合物溶液,储存于原料罐1中;具体的,储存于镍盐溶液罐1a中。本发明中,所述镍盐化合物溶液的浓度优选为0.5~2.5mol/l。
本发明中,所述钴盐化合物溶液中的钴盐化合物优选为硫酸钴、乙酸钴和硝酸钴中的一种或几种。所述钴盐化合物溶液优选为钴盐化合物的水溶液,即将钴盐化合物与水混合,形成钴盐化合物溶液,储存于原料罐1中;具体的,储存于钴盐溶液罐1b中。本发明中,所述钴盐化合物溶液的浓度优选为0.5~2.5mol/l。
本发明中,所述锰盐化合物溶液中的锰盐化合物优选为硫酸锰、乙酸锰和硝酸锰中的一种或几种。所述锰盐化合物溶液优选为锰盐化合物的水溶液,即将锰盐化合物与水混合,形成锰盐化合物溶液,储存于原料罐1中;具体的,储存于锰盐溶液罐1c中。本发明中,所述锰盐化合物溶液的浓度优选为0.5~3mol/l。
本发明中,所述镍盐化合物、钴盐化合物和锰盐化合物的摩尔比优选为(0.5~9):(0.5~3):(0.5~9),更优选为(3~8):(0.5~2.5):(1~7)。所述混合盐溶液中,镍盐化合物、钴盐化合物和锰盐化合物总的摩尔浓度优选为0.5~5mol/l,更优选为1.5~4mol/l,最优选为2.5~3mol/l。
本发明中,所述添加剂溶液中的添加剂选自硫酸镁、铝酸铵、硫酸锆、醋酸铌、醋酸钙和硝酸锶中的一种或几种。所述添加剂溶液优选为添加剂的水溶液,即将添加剂与水混合,形成添加剂溶液,储存于原料罐1中;具体的,储存于添加剂溶液罐1d中。本发明中,所述添加剂溶液的浓度优选为0.1~2mol/l。本发明中,所述添加剂与镍盐化合物的摩尔比优选为(0.05~1):(0.5~9)。
本发明中,将镍盐化合物溶液、钴盐化合物溶液、锰盐化合物溶液和添加剂溶液在配盐釜2中混合,具体通过原料罐1向配盐釜2中输送物料,更具体通过镍盐溶液罐1a、钴盐溶液罐1b、锰盐溶液罐1c和添加剂溶液罐1d分别向配盐釜2中输送镍盐化合物溶液、钴盐化合物溶液、锰盐化合物溶液和添加剂溶液。本发明中,所述输送物料的方式优选为滴加,即通过各个原料罐向配盐釜2中分别滴加各种物料。本发明中,所述滴加的速率优选为10~2000ml/min。各种原料送至配盐釜2中后,优选通过搅拌混合,使物料混匀,在配盐釜2内形成混合盐溶液。
关于步骤b):
本发明中,将混合盐溶液及其它配料送入一级反应釜3-1内。其中,所述其它配料包括:沉淀剂溶液、络合剂溶液及助剂溶液。所述将配料罐中的配料送至一级反应釜中具体包括:将沉淀剂溶液罐中的沉淀剂溶液、络合剂溶液罐中的络合剂溶液和助剂溶液罐中的助剂溶液分别送至一级反应釜中。
所述沉淀剂溶液中的沉淀剂优选为氢氧化钠、碳酸钠、碳酸铵和碳酸氢铵中的一种或几种。所述沉淀剂溶液优选为沉淀剂的水溶液,即将沉淀剂与水混合,形成沉淀剂溶液,储存于配料罐4中;具体的,储存于沉淀剂溶液罐4a中。本发明中,所述沉淀剂溶液的浓度优选为0.5~5mol/l,更优选为1.5~4mol/l,最优选为2.5~3mol/l。
所述络合剂溶液中的络合剂优选为氨水、尿素和柠檬酸钠中的一种或几种,更优选为氨水。所述络合剂溶液优选为络合剂的水溶液,即将络合剂与水混合,形成络合剂溶液,储存于配料罐4中;具体的,储存于络合剂溶液罐4b中。本发明中,所述络合剂溶液的浓度优选为0.5~4mol/l,更优选为1.5~4mol/l,最优选为2.5~3mol/l。
所述助剂溶液中的助剂优选为表面活性剂中的一种或几种;更优选为硬脂酸、十二烷基苯磺酸钠、卵磷脂、氨基酸型、甜菜碱型烷基葡糖苷(apg)、脂肪酸甘油酯、脂肪酸山梨坦(即司盘)、聚山梨酯(即吐温)和黄原胶中的一种或几种。所述助剂溶液优选为助剂的水溶液,即将助剂与水混合,形成助剂溶液,储存于配料罐4中;具体的,储存于助剂溶液罐4c中。本发明中,所述助剂溶液的浓度优选为0.1~2mol/l。
本发明中,将步骤a)得到的混合盐溶液、上述沉淀剂溶液、络合剂溶液、和助剂溶液在一级反应釜3-1中混合反应,具体通过配盐釜2向一级反应釜3-1中输送混合盐溶液,同时,通过配料罐4向一级反应釜3-1中输送配料,更具体通过沉淀剂溶液罐4a、络合剂溶液罐4b、助剂溶液罐4c分别向一级反应釜3-1中输送沉淀剂溶液、络合剂溶液和助剂溶液。
本发明中,优选通过上述各物料的输送管道的上的计量泵控制向一级反应釜3-1中输送物料的速率,其中,所述混合盐溶液的流速优选为10~1000ml/min;所述沉淀剂溶液的流速优选为10~1000ml/min;所述络合剂溶液的流速优选为2~500ml/min,当络合剂为氨水时,优选通过控制其流量使反应釜体系内物料ph为7~12,更优选为8~11,最优选为9~10;所述助剂溶液的流速优选为2~500ml/min。其中,所述沉淀剂溶液中的沉淀剂优选为所述混合盐溶液中所用盐类用量的80wt%~120wt%;所述络合剂溶液中的络合剂优选为所述混合盐溶液中所用盐类用量的20wt%~50wt%;所述助剂溶液中的助剂优选为所述混合盐溶液中所用盐类用量的2wt%~15wt%。各种物料送至一级反应釜3-1中后,优选通过搅拌混合,使物料混匀,并开启加热,使反应釜升温,从而使釜内物料进行共沉淀反应。
本发明中,所述一级反应釜3-1内的气氛为保护性气体氛围;本发明对所述保护性气体氛围的气体种类没有特殊限制,为本领域技术人员熟知的常规保护性气体即可,如氮气或氩气等。所述一级反应釜3-1内的气压没有特殊限制,为常压即可。所述一级反应釜3-1内共沉淀反应的条件优选为:①温度为50~65℃,更优选为55~60℃,在本发明的一些实施例中为55℃或60℃;②ph值为7~12,更优选为8~11,最优选为9~10,在本发明的一些实施例中为8.5、8.9或11.2;搅拌速率为300~1500r/min,在本发明的一些实施例中为300r/min或750r/min;反应的时间为10~120h,在本发明的一些实施例中为20h或30h。
本发明中,由于发生共沉淀反应,物质之间相互反应逐渐生成产物沉淀下来,上层泌出清液,上述反应过程中,通过抽液釜5将一级反应釜3-1内的上清液抽出,直至一级反应釜内混合液达到一定的固含量,再关闭抽液釜停止抽上清液。本发明中,优选抽至一级反应釜3-1内物料固含量为15wt%~35wt%。
停止抽上清液后,打开第二放液阀3c,将一级反应釜内的料液向二级反应釜内输送。本发明中,所述二级反应釜3-2内的气氛为保护性气体氛围;本发明对所述保护性气体氛围的气体种类没有特殊限制,为本领域技术人员熟知的常规保护性气体即可,如氮气或氩气等。所述二级反应釜3-2内的气压没有特殊限制,为常压即可。所述二级反应釜3-2内共沉淀反应的条件优选为:①温度为50~65℃,更优选为55~60℃,在本发明的一些实施例中为55℃或60℃;②搅拌速率为300~1500r/min,在本发明的一些实施例中为300r/min或750r/min。
本发明中,向二级反应釜内输送料液,直至二级反应釜3-2内的料液的液位达到一定程度。本发明中,优选使二级反应釜3-2内料液的液位达到二级反应釜3-2高度的60%~95%。
待二级反应釜3-2内的物料液位达到上述程度后,开启循环装置6(具体为开启循环管上的循环泵),使一级反应釜3-1与二级反应釜3-2的物料之间形成内循环。本发明中,所述循环装置6的循环泵6b的流速优选为1~200m3/min,更优选为控制每分钟流量为一级反应釜3-1容积的5~20倍。所述内循环的时间优选为1~25min。
内循环一定时间后,关闭循环装置6,停止内循环,并关闭两级反应釜之间的放液阀,停止两级反应釜之间的物料传输;然后,打开第三放液阀7a,将二级反应釜3-2内的料液输送至陈化釜7中进行陈化。本发明中,所述陈化的温度优选为40~60℃;陈化的时间优选为1~35h,在本发明的一些实施例中,陈化的时间为2h或4h。陈化结束后,将陈化釜7内的物料排出,得到前驱体材料。
本发明中,在上述陈化开始的同时,开启抽液釜5将一级反应釜3-1内的上清液抽出,陈化结束时,关闭抽液釜停止上清液的抽出;然后,开启两级反应釜之间的放液阀,将一级反应釜3-1内的料液向二级反应釜3-2内输送,直至二级反应釜3-2内料液的液位达到一定程度后,开启所述循环装置6的循环泵6b,使一级反应釜3-1内的料液与二级反应釜3-2内的料液进行内循环,待循环一定时间后,关闭内循环和两级反应釜之间的放液阀,将二级反应釜3-2内的料液输送至陈化釜7中进行陈化;经陈化后,将陈化釜7内的料液排出,再次得到前驱体材料。其中,二级反应釜3-2料液的液位优选为达到二级反应釜3-2高度的60%~95%;内循环的时长优选为1~25min。如此重复上述处理,从而使陈化釜7内不断排出前驱体材料。
本发明中,在反应釜共沉淀反应过程及陈化釜陈化过程中,搅拌一直持续进行。
本发明中,每次从陈化釜7中的排出前驱体材料后,优选还进行:水洗、脱水和干燥。本发明对所述水洗、脱水和干燥的方式没有特殊限制,按照本领域技术人员熟知的常规方式进行即可。经上述后处理后,得到前驱体材料。所述前驱体为锂离子正极多元材料前驱体,具体为富锂锰基材料前驱体,具有式(1)或式(2)所示结构:
lixniycozmnamh(oh)2式(1),lixniycozmnamhco3式(2);
其中,
1<x≤1.6,0.1<y≤0.95,0.1<z≤0.5,0.1<a≤0.8,0.01<h≤0.15;
m为mg、al、ti、zr、nb、ca和sr的一种或几种。
本发明提供的上述制备方法中,采用两级反应,且两级反应之间进行内循环,并伴随搅拌,能够从多方面有效提升所制材料的性能。具体的,通过多级反应共沉淀,可使合成的前驱体,颗粒粒径可控均一,形貌规整,振实密度高,能够改进正极材料的结构稳定性,提高正极材料的循环性能;而且通过两级反应结合内循环,增加了反应中的能量,促进反应的进行,利于多元金属离子供沉淀过程中在搅拌分数过程中内循环的作用下,加快不同金属离子的耦合速度,不同沉积系数的金属离子在双搅拌和循环流体的共同作用下能够精确按比例生成更多的晶核、抑制晶核生长、避免在共沉淀过程中和陈化过程中二次颗粒之间过多的团聚;同时,多级反应及内循环的作用使正极材料前驱体的一次颗粒层间距减小、增大了材料的比表面积以及振实密度,降低了循环过程中的界面内阻,提高了正极材料的倍率性能,从而提高锂离子电池的能量密度。
本发明还提供了一种上述技术方案中所述的制备方法制得的锂离子多元正极材料前驱体。
本发明还提供了一种锂离子多元正极材料的制备方法,包括:
将锂离子多元正极材料前驱体与锂盐混合烧结,得到式(3)所示锂离子多元正极材料;
li(lixniycozmnamh)o2式(3);
其中,
1<x≤1.6,0.1<y≤0.95,0.1<z≤0.5,0.1<a≤0.8,0.01<h≤0.15;
m为mg、al、ti、zr、nb、ca和sr的一种或几种;
所述锂离子多元正极材料前驱体为上述技术方案中所述的锂离子多元正极材料前驱体。
本发明中,所述锂盐优选为碳酸锂和氢氧化锂中的一种或几种。所述锂盐与富锂锰基材料前驱体的摩尔比没有特殊限制,为本领域常规比例即可,优选为(1.01~1.6):1。本发明中,所述烧结的温度优选为735~975℃;所述烧结的时间优选为8~20h。经上述烧结处理后,富锂锰基材料前驱体与锂盐之间反应,形成式(3)所示富锂锰基材料。本发明提供制备方法制得的富锂锰基材料能有效提高锂离子电池的电化学性能。
为了进一步理解本发明,下面结合实施例对本发明优选实施方案进行描述,但是应当理解,这些描述只是为进一步说明本发明的特征和优点,而不是对本发明权利要求的限制。以下实施例采用图1所示的多级反应系统。
实施例1
1.1制备
s1、按照目标产物li(li0.5ni0.25co0.15mn0.6mg0.05)o2中的摩尔比,分别称取定量的硫酸镍、硫酸钴和硫酸锰,以及添加剂硫酸镁,分别搅拌溶于去离子水中形成硫酸镍溶液、硫酸钴溶液、硫酸锰溶液和添加剂溶液;
分别通过镍盐溶液罐1a、钴盐溶液罐1b、锰盐溶液罐1c、添加剂溶液罐1d向配盐釜2中滴加上述各物料,滴加速率均为50ml/min。在配盐釜2中搅拌混匀,配制成2mol/l的混合盐溶液。
s2、配制配料:
沉淀剂溶液的配制:将碳酸钠溶搅拌溶于去离子水中,配制成2mol/l的碳酸钠溶液。
络合剂溶液的配制:取浓度为25%的氨水,用去离子水稀释,配制成0.2mol/l的络合剂溶液。
助剂溶液的配制:将表面活性剂吐温80溶于去离子水中,配制成0.05mol/l的助剂溶液。
s3、将步骤s1的混合盐溶液和步骤s2的配料分别按一定速率向一级反应釜3-1(容积为200l)内输送:混合盐溶液的速率为100ml/min;沉淀剂溶液的速率为100ml/min,沉淀剂总用量为混合盐溶液中所有盐类的95wt%;络合剂溶液的速率为35ml/min并通过其流量控制一级反应釜3-1内体系ph值为8.5,反应过程中间歇性加入助剂溶液,其中的表面活性剂总用量为混合盐溶液中所有盐类的2.5wt%。采用直接电加热的方式将反应釜3中的体系恒温加热至60℃。
s4、控制反应釜3中搅拌桨转速为750r/min,在一级反应釜3-1反应过程中,通过抽液釜抽出上清液,反应30h后关闭抽液釜停止抽上清液(此时一级反应釜3-1内物料固含量达到25wt%)。开启放液阀3c将一级反应釜3-1的物料自由进入二级反应釜3-2中,待二级反应釜3-2内液位达到65%高度后,开启循环泵6b,在一级反应釜3-1与二级反应釜3-2之间建立内循环(流速为0.8m3/min),10min后关闭内循环。打开放液阀7a,将二级反应釜3-2内的物料送至陈化釜7中,至陈化釜7料满后关闭放液阀7a,于45℃下陈化2h后,出料排空陈化釜,得到前驱体材料。
s5、步骤s4中,陈化开始的同时,通过抽液釜对一级反应釜3-1抽出上清液,陈化结束后,停止抽上清液(此时一级反应釜3-1内物料固含量达到35wt%)。开启放液阀3c将一级反应釜3-1的物料自由进入二级反应釜3-2中,待二级反应釜3-2内液位达到60%高度后,开启循环泵6b,在一级反应釜3-1与二级反应釜3-2之间建立内循环(流速为1m3/min),10min后关闭内循环。打开放液阀7a,将二级反应釜3-2内的物料再次送至陈化釜7中,至陈化釜7料满后关闭放液阀7a,于45℃下陈化2h后,出料排空陈化釜,再次得到前驱体材料。如此重复处理,不断的从陈化釜7中排出前驱体材料。
s6、将得到的前驱体材料进行多次水洗、脱水和烘干,得到富锂锰基三元材料前驱体ni0.25co0.15mn0.6mg0.05co3。
1.2表征及测试
(1)对所得前驱体进行x射线衍射测试,结果如图2所示,图2为实施例1所得前驱体的xrd测试图。可以看出,所得前驱体为ni0.25co0.15mn0.6mg0.05co3结构组成。
(2)对所得前驱体的颗粒粒径分布、形貌特征进行分析测试,结果分别如图3和图4所示,其中,图3为实施例1所得前驱体的粒径分布图,图4为实施例1所得前驱体的sem图。由图3和图4可以看出,所得前驱体颗粒球形度高,且采用本发明的方法能够有效控制合成过程中前驱体粒径过快增长,中值粒径d50为8.5μm。同时测试其多分散指数和振实密度,结果显示,其粒径的多分散指数pdi为0.12,振实密度为2.18g/ml;证明,本发明提供的方法能够有效使前驱体获得高振实密度,且使颗粒粒径分布均匀。
(3)电化学性能测试:
将所得前驱体颗粒与碳酸锂按照锂化比1.5(锂化比为锂与前驱体混合的计量比)混合,未进行其它任何掺杂和包覆等改性处理,直接于825℃烧结18h,得到富锂锰基正极材料li(li0.5ni0.25co0.15mn0.6mg0.05)o2。
将所得正极材料组装成半电池:将上述正极材料、导电碳和聚偏氟乙烯(pvdf)粘合剂(重量比为80:10:10)混合在铝箔上制备电极。为去除残余n-methyl-2-pyrrolidone(nmp)和少量的水,电极真空80℃干燥12h。从工作电极上打出直径为13毫米的电极盘。以金属锂为对电极,celgard2502为隔膜,1mol/l-1lipf6按照体积比为3:7溶于碳酸乙酯(ec)-碳酸二甲酯(dmc)中作为电解液。这些组件在一个充满ar的手套盒(h2o<0.1ppm,o2<0.1ppm)中被组装,并在一个land-ct2001a电池。
对上述半电池进行电化学性能测试,结果参见图5,图5为实施例1所得正极材料的电化学性能测试图。可以看出,正极材料首次放电容量达到301mah/g,且正极材料在循环过程中能保持优异的循环性能,在循环100圈以后,放电容量保持率仍达到95%。
实施例2
1.1制备
s1、按照目标产物li(li0.4ni0.13co0.09mn0.5al0.08)o2中的摩尔比,分别称取定量的硫酸镍、硫酸钴和硫酸锰,以及添加剂铝酸铵,分别搅拌溶于去离子水中形成硫酸镍溶液、硫酸钴溶液、硫酸锰溶液和添加剂溶液;
按照实施例1步骤s1滴加传输物料,在配盐釜2中搅拌混匀,配制成2mol/l的混合盐溶液。
s2、配制配料:
沉淀剂溶液的配制:将碳酸钠溶搅拌溶于去离子水中,配制成2mol/l的碳酸钠溶液。
络合剂溶液的配制:取浓度为25%的氨水,用去离子水稀释,配制成浓度为16%的络合剂溶液。
助剂溶液的配制:将表面活性剂黄原胶溶于去离子水中,配制成0.02mol/l的助剂溶液。
s3、将步骤s1的混合盐溶液和步骤s2的配料分别按一定速率向一级反应釜3-1(容积为2000l)内输送:混合盐溶液的速率为1000ml/min;沉淀剂溶液的速率为1000ml/min,沉淀剂总用量为混合盐溶液中所有盐类的95wt%;络合剂溶液的速率为800ml/min并通过其流量控制一级反应釜3-1内体系ph值为8.9,反应过程中间歇性加入助剂溶液,其中的表面活性剂总用量为混合盐溶液中所有盐类的2wt%。采用直接电加热的方式将反应釜3中的体系恒温加热至60℃。
s4、控制反应釜3中搅拌桨转速为300r/min,在一级反应釜3-1反应过程中,通过抽液釜抽出上清液,反应20h后关闭抽液釜停止抽上清液(此时一级反应釜3-1内物料固含量达到20wt%)。开启放液阀3c将一级反应釜3-1的物料自由进入二级反应釜3-2中,待二级反应釜3-2内液位达到50%高度后,开启循环泵6b,在一级反应釜3-1与二级反应釜3-2之间建立内循环(流速为0.5m3/min),15min后关闭内循环。打开放液阀7a,将二级反应釜3-2内的物料送至陈化釜7中,至陈化釜7料满后关闭放液阀7a,于60℃下陈化2h后,出料排空陈化釜,得到前驱体材料。
s5、步骤s4中,陈化开始的同时,通过抽液釜对一级反应釜3-1抽出上清液,陈化结束后,停止抽上清液(此时一级反应釜3-1内物料固含量达到30wt%)。开启放液阀3c将一级反应釜3-1的物料自由进入二级反应釜3-2中,待二级反应釜3-2内液位达到60%高度后,开启循环泵6b,在一级反应釜3-1与二级反应釜3-2之间建立内循环(流速为0.8m3/min),10min后关闭内循环。打开放液阀7a,将二级反应釜3-2内的物料再次送至陈化釜7中,至陈化釜7料满后关闭放液阀7a,于60℃下陈化4h后,出料排空陈化釜,再次得到前驱体材料。如此重复处理,不断的从陈化釜7中排出前驱体材料。
s6、将得到的前驱体材料进行多次水洗、脱水和烘干,得到富锂锰基三元材料前驱体ni0.13co0.09mn0.5al0.08(oh)2。
1.2表征及测试
(1)对所得前驱体的颗粒粒径分布、形貌特征进行分析测试,结果分别如图6和图7所示,其中,图6为实施例2所得前驱体的粒径分布图,图7为实施例2所得前驱体的sem图。由图6和图7可以看出,所得前驱体颗粒球形度高,且采用本发明的方法能够有效控制合成过程中前驱体粒径过快增长,中值粒径d50为6.5μm。同时测试其多分散指数和振实密度,结果显示,其粒径的多分散指数pdi为0.15,振实密度为2.28g/ml;证明,本发明提供的方法能够有效使前驱体获得高振实密度,且使颗粒粒径分布均匀。
(3)电化学性能测试:
将所得前驱体颗粒与氢氧化锂按照锂化比1.4混合,未进行其它任何掺杂和包覆等改性处理,直接于755℃烧结18h,得到富锂锰基正极材料li(li0.4ni0.13co0.09mn0.5al0.08)o2。
按照实施例1将所得正极材料组装成半电池。
对上述半电池进行电化学性能测试,结果参见图8,图8为实施例2所得正极材料的电化学性能测试图。可以看出,正极材料首次放电容量达到265mah/g,且正极材料在循环过程中能保持优异的循环性能,在循环100圈以后,放电容量保持率仍达到96%。
实施例3
1.1制备
s1、按照目标产物li(li0.1ni0.3co0.1mn0.5mg0.02al0.02zr0.05ti0.01)o2中的摩尔比,分别称取定量的硫酸镍、硫酸钴和硫酸锰,以及添加剂硫酸镁、硫酸锆和铝酸铵,分别搅拌溶于去离子水中形成硫酸镍溶液、硫酸钴溶液、硫酸锰溶液和添加剂溶液;
按照实施例1步骤s1滴加传输物料,在配盐釜2中搅拌混匀,配制成2mol/l的混合盐溶液。
s2、配制配料:
沉淀剂溶液的配制:将碳酸钠溶搅拌溶于去离子水中,配制成2mol/l的碳酸钠溶液。
络合剂溶液的配制:取浓度为25%的氨水,用去离子水稀释,配制成浓度为16%的络合剂溶液。
助剂溶液的配制:将表面活性剂黄原胶溶于去离子水中,配制成0.02mol/l的助剂溶液。
s3、将步骤s1的混合盐溶液和步骤s2的配料分别按一定速率向一级反应釜3-1(容积为2000l)内输送:混合盐溶液的速率为1000ml/min;沉淀剂溶液的速率为1050ml/min,沉淀剂总用量为混合盐溶液中所有盐类的105wt%;络合剂溶液的速率为800ml/min并通过其流量控制一级反应釜3-1内体系ph值为8.9,反应过程中间歇性加入助剂溶液,其中的表面活性剂总用量为混合盐溶液中所有盐类的3wt%。采用直接电加热的方式将反应釜3中的体系恒温加热至60℃。
s4、控制反应釜3中搅拌桨转速为300r/min,在一级反应釜3-1反应过程中,通过抽液釜抽出上清液,反应20h后关闭抽液釜停止抽上清液(此时一级反应釜3-1内物料固含量达到25wt%)。开启放液阀3c将一级反应釜3-1的物料自由进入二级反应釜3-2中,待二级反应釜3-2内液位达到65%高度后,开启循环泵6b,在一级反应釜3-1与二级反应釜3-2之间建立内循环(流速为1.1m3/min),15min后关闭内循环。打开放液阀7a,将二级反应釜3-2内的物料送至陈化釜7中,至陈化釜7料满后关闭放液阀7a,于50℃下陈化2h后,出料排空陈化釜,得到前驱体材料。
s5、步骤s4中,陈化开始的同时,通过抽液釜对一级反应釜3-1抽出上清液,陈化结束后,停止抽上清液(此时一级反应釜3-1内物料固含量达到26wt%)。开启放液阀3c将一级反应釜3-1的物料自由进入二级反应釜3-2中,待二级反应釜3-2内液位达到65%高度后,开启循环泵6b,在一级反应釜3-1与二级反应釜3-2之间建立内循环(流速为1.15m3/min),10min后关闭内循环。打开放液阀7a,将二级反应釜3-2内的物料再次送至陈化釜7中,至陈化釜7料满后关闭放液阀7a,于50℃下陈化4h后,出料排空陈化釜,再次得到前驱体材料。如此重复处理,不断的从陈化釜7中排出前驱体材料。
s6、将得到的前驱体材料进行多次水洗、脱水和烘干,得到富锂锰基三元材料前驱体li0.1ni0.3co0.1mn0.5mg0.02al0.02zr0.05ti0.01(oh)2。
1.2表征及测试
(1)对所得前驱体的颗粒粒径分布、形貌特征进行分析测试,结果分别如图9和图10所示,其中,图9为实施例3所得前驱体的粒径分布图,图10为实施例3所得前驱体的sem图。由图9和图10可以看出,所得前驱体颗粒球形度高,且采用本发明的方法能够有效控制合成过程中前驱体粒径过快增长,中值粒径d50为7.5μm。同时测试其多分散指数和振实密度,结果显示,其粒径的多分散指数pdi为0.13,振实密度为2.03g/ml;证明,本发明提供的方法能够有效使前驱体获得高振实密度,且使颗粒粒径分布均匀。
(3)电化学性能测试:
将所得前驱体颗粒与氢氧化锂按照锂化比1.4混合,未进行其它任何掺杂和包覆等改性处理,直接于755℃烧结18h,得到富锂锰基正极材料li(li0.1ni0.3co0.1mn0.5mg0.02al0.02zr0.05ti0.01)o2。
按照实施例1将所得正极材料组装成半电池。
对上述半电池进行电化学性能测试,结果参见图11,图11为实施例3所得正极材料的电化学性能测试图。可以看出,正极材料首次放电容量达到249mah/g,且正极材料在循环过程中能保持优异的循环性能,在循环100圈以后,放电容量保持率仍达到96.5%。
实施例4
1.1制备
s1、按照目标产物li1.02ni0.8co0.05mn0.1mg0.02al0.03o2中的摩尔比,分别称取定量的硫酸镍、硫酸钴和硫酸锰,以及添加剂硫酸镁、硫酸锆和铝酸铵,分别搅拌溶于去离子水中形成硫酸镍溶液、硫酸钴溶液、硫酸锰溶液和添加剂溶液;
按照实施例1步骤s1滴加传输物料,在配盐釜2中搅拌混匀,配制成2mol/l的混合盐溶液。
s2、配制配料:
沉淀剂溶液的配制:将氢氧化钠钠溶搅拌溶于去离子水中,配制成2mol/l的氢氧化钠溶液。
络合剂溶液的配制:取浓度为25%的氨水,用去离子水稀释,配制成浓度为18%的络合剂溶液。
助剂溶液的配制:将表面活性剂黄原胶溶于去离子水中,配制成0.2mol/l的助剂溶液。
s3、将步骤s1的混合盐溶液和步骤s2的配料分别按一定速率向一级反应釜3-1(容积为2000l)内输送:混合盐溶液的速率为1000ml/min;沉淀剂溶液的速率为900ml/min,沉淀剂总用量为混合盐溶液中所有盐类的92wt%;络合剂溶液的速率为1.6l/min并通过其流量控制一级反应釜3-1内体系ph值为11.2,反应过程中间歇性加入助剂溶液,其中的表面活性剂总用量为混合盐溶液中所有盐类的3wt%。采用直接电加热的方式将反应釜3中的体系恒温加热至55℃。
s4、控制反应釜3中搅拌桨转速为300r/min,在一级反应釜3-1反应过程中,通过抽液釜抽出上清液,反应20h后关闭抽液釜停止抽上清液(此时一级反应釜3-1内物料固含量达到30wt%)。开启放液阀3c将一级反应釜3-1的物料自由进入二级反应釜3-2中,待二级反应釜3-2内液位达到70%高度后,开启循环泵6b,在一级反应釜3-1与二级反应釜3-2之间建立内循环(流速为1.2m3/min),15min后关闭内循环。打开放液阀7a,将二级反应釜3-2内的物料送至陈化釜7中,至陈化釜7料满后关闭放液阀7a,于55℃下陈化2h后,出料排空陈化釜,得到前驱体材料。
s5、步骤s4中,陈化开始的同时,通过抽液釜对一级反应釜3-1抽出上清液,陈化结束后,停止抽上清液(此时一级反应釜3-1内物料固含量达到35wt%)。开启放液阀3c将一级反应釜3-1的物料自由进入二级反应釜3-2中,待二级反应釜3-2内液位达到70%高度后,开启循环泵6b,在一级反应釜3-1与二级反应釜3-2之间建立内循环(流速为1.3m3/min),10min后关闭内循环。打开放液阀7a,将二级反应釜3-2内的物料再次送至陈化釜7中,至陈化釜7料满后关闭放液阀7a,于55℃下陈化4h后,出料排空陈化釜,再次得到前驱体材料。如此重复处理,不断的从陈化釜7中排出前驱体材料。
s6、将得到的前驱体材料进行多次水洗、脱水和烘干,得到富锂锰基三元材料前驱体ni0.8co0.05mn0.1mg0.02al0.039(oh)2。
1.2表征及测试
(1)对所得前驱体的颗粒粒径分布、形貌特征、振实密度进行分析测试,结果显示:中值粒径d50为9.5μm,其粒径的多分散指数pdi为0.10,振实密度为2.08g/ml。证明,本发明提供的方法能够有效使前驱体获得高振实密度,且使颗粒粒径分布均匀。
(3)电化学性能测试:
将所得前驱体颗粒与氢氧化锂按照锂化比1.05混合,未进行其它任何掺杂和包覆等改性处理,直接于755℃烧结18h,得到富锂锰基正极材料lili1.02ni0.8co0.05mn0.1mg0.02al0.03o2。
按照实施例1将所得正极材料组装成半电池。
对上述半电池进行电化学性能测试,结果显示,所得正极材料首次放电容量达到218mah/g,且正极材料在循环过程中能保持优异的循环性能,在循环100圈以后,放电容量保持率仍达到97%。
以上实施例的说明只是用于帮助理解本发明的方法及其核心思想。对这些实施例的多种修改对本领域的专业技术人员来说将是显而易见的,本文中所定义的一般原理可以在不脱离本发明的精神或范围的情况下,在其它实施例中实现。因此,本发明将不会被限制于本文所示的这些实施例,而是要符合与本文所公开的原理和新颖特点相一致的最宽的范围。
起点商标作为专业知识产权交易平台,可以帮助大家解决很多问题,如果大家想要了解更多知产交易信息请点击 【在线咨询】或添加微信 【19522093243】与客服一对一沟通,为大家解决相关问题。
此文章来源于网络,如有侵权,请联系删除


