一种铜基复合材料及其制备方法与流程



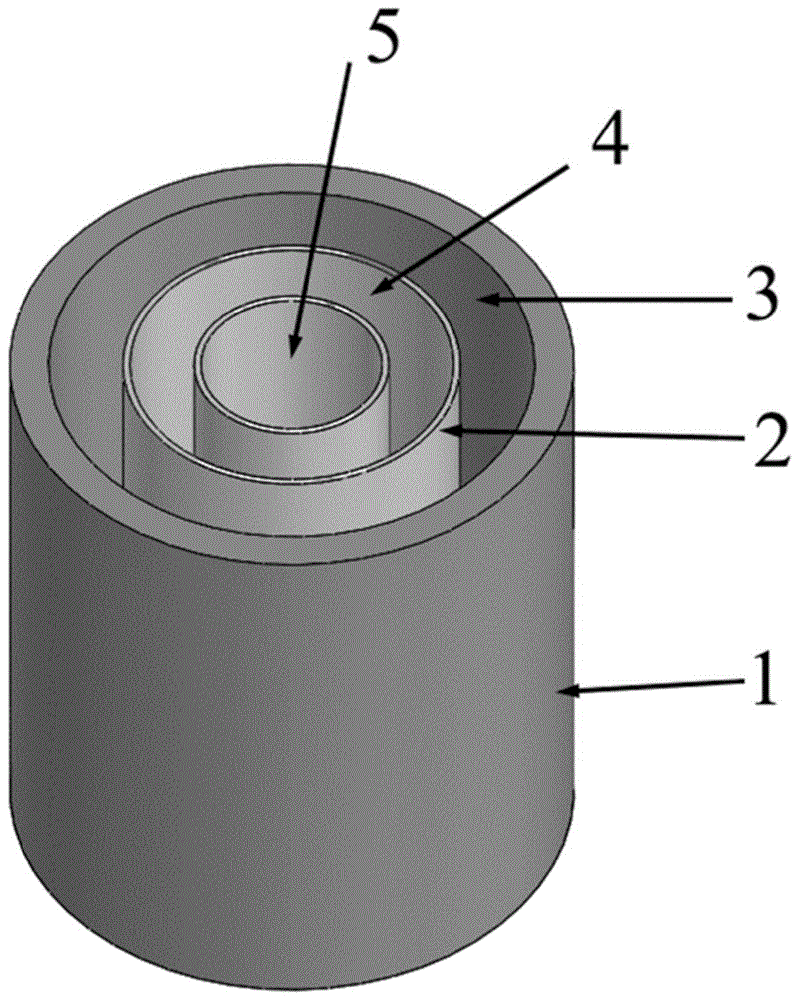
本发明涉及一种铜基复合材料及其制备方法,属于金属基复合材料
技术领域:
。
背景技术:
:铜作为导电、导热功能材料广泛应用于工业生产。但铜的强度低,耐热性和耐磨性差,高温下易软化变形。通过在铜中添加增强材料的方式制备得到的铜基复合材料,虽然可提高铜基复合材料的强度、耐热性和耐磨性,以及缓解铜高温下易软化变形的缺陷,但铜基复合材料的导电或导热性较差,随着信息技术的不断发展,对特殊环境下铜基复合材料的要求日益提高,普通的铜基复合材料很难满足苛刻条件下对其性能的需求。技术实现要素:本发明的第一个目的在于提供一种铜基复合材料,该铜基复合材料具有优良的导电、导热和耐磨性。本发明的第二个目的在于提供一种铜基复合材料的制备方法,该制备方法操作简单,具有可控性。一种铜基复合材料,所述铜基复合材料包括增强材料和铜基体,所述铜基复合材料的形状为柱体,沿垂直于柱体中心轴的方向,所述增强材料的含量由内向外呈梯度分布;其中,所述增强材料为金属氧化物、金属碳化物、金属硼化物或难熔金属。应当理解的是,沿垂直于柱体中心轴的方向,所述增强材料的含量由内向外呈梯度分布可以是,沿垂直于柱体中心轴的方向,所述增强材料的含量由内向外呈梯度升高,此时,铜基复合材料最内部材料中增强材料含量最少,铜基复合材料最内部材料中增强材料含量可以是0wt%,也可以大于0wt%,如2wt%,铜基复合材料最外部材料中增强材料含量最高。本发明的铜基复合材料中增强材料的含量由内向外呈梯度分布,铜基复合材料中增强材料的含量较高的梯度层材料中,增强材料提高了铜基体的强度,耐热性和耐磨性等性能,缓解了铜基体在高温下易软化变形的缺陷,铜基复合材料中增强材料的含量较少甚至不含增强材料的梯度层材料中,具有良好的导电性和导热性。该铜基复合材料兼顾了铜基体和铜基复合材料的优点,综合性能优良,具有良好的导电性和导热性,强度高,耐热性和耐磨性好。优选地,所述由内向外呈梯度分布为由内向外呈梯度升高。沿垂直于柱体中心轴的方向,所述增强材料的含量由内向外呈梯度升高,铜基复合材料的外部材料中的增强材料的含量较高,使得铜基复合材料具有较高的强度,耐热性和耐磨性,铜基复合材料的内部材料中的增强材料的含量较低,具有较优的导电性和导热性。实际应用中,可以根据需要选用具有特定增强材料的梯度分布的铜基复合材料。优选地,所述柱体为圆柱体。以环形梯度铜基复合材料为优选。优选地,所述铜基复合材料中增强材料的最高含量为25wt%。铜基复合材料中增强材料的最高含量为25wt%有助于使得铜基复合材料具有良好的强度,以及耐热性和耐磨性,且不影响铜基复合材料的加工性。应当理解的是,所述铜基复合材料中增强材料的最高含量为25wt%指的是,铜基复合材料任意一位置的材料中的增强材料的含量均在25wt%以下。沿垂直于柱体中心轴的方向,所述增强材料的含量由内向外呈梯度升高,铜基复合材料的最外部材料中的增强材料的含量在25wt%以下。优选地,所述金属氧化物为al2o3、zro2、tio2、mgo、ceo2或la2o3;所述金属碳化物为tic、wc、b4c或cr3c2;所述金属硼化物为crb2、tib2或zrb2;所述难熔金属为w或mo。上述金属氧化物、金属碳化物、金属硼化物或难熔金属为铜基复合材料增强相,具有较好的增强效果,有利于提高铜基复合材料中强度,耐热性和耐磨性。优选地,所述铜基体为cu,或cu与cr、zr、ti和fe中至少一种金属组成的铜合金。优选地,所述铜合金为cu-cr合金、cu-zr合金、cu-cr-zr合金、cu-ti合金或cu-fe合金;其中,所述cu-cr合金中cu和cr的质量比为100:0.4~1.2;所述cu-cr-zr合金中cu、cr和zr的质量比为100:0.4~1.2:0.03~0.3;所述cu-zr合金中cu和zr的质量比为100:0.03~0.3;所述cu-ti合金中cu和ti的质量比为100:0.5~5;所述cu-fe合金中cu和fe的质量比为100:0.3~4。一种铜基复合材料的制备方法,包括以下步骤:在设置有环形隔板的柱形模具中装入含增强材料和铜基材的混合粉,沿垂直于模具中心轴的方向,使混合粉中的增强材料的含量由内向外呈梯度分布,移去隔板后,进行压制和烧结,即得;其中,所述增强材料为金属氧化物、金属碳化物、金属硼化物或难熔金属。可以理解的是,环形隔板与柱形模具的轴线重合为优化的方案,环形隔板的厚度应当尽量小,需要满足能够将柱形模具分割为多个空间,并且在环形隔板移去后,对于梯度分布的混合粉的影响较小或可忽略不计。环形隔板的数量可以是1个、2个、3个、4个、5个、6个或7个,也可以是更多数目的隔板,隔板数量的增多,可使得隔板两侧混合粉中的增强材料的含量差减小,有利于提高过渡层的均匀性,可根据生产和成本的要求,调整隔板的数量。可以理解的是,当隔板数量为多个时,对于相邻环形隔板的间距不作限定,可以是等间距的,如3个环形隔板的直径可以依次为柱形模具的直径的0.9倍、0.8倍、0.7倍,也可以是不等间距的,如3个环形隔板的直径可以依次为柱形模具的直径的0.9倍、0.75倍、0.7倍。可以理解的是,当隔板数量大于2个时,各隔板两侧的混合粉中增强材料的含量差可以是相同的,如设置有3个环形隔板的柱形模具中装入的混合粉中的增强材料的含量由外环空间到内环空间依次为15%、10%、5%、0%,也可以是不同的,如设置有3个环形隔板的柱形模具中装入的混合粉中的增强材料的含量由外环空间到内环空间依次为12%、8%、5%、0%。本发明的铜基复合材料的制备方法只需要将含有不同增强材料的混合粉进行梯度装粉,然后经压制和烧结,即可制备得到铜基复合材料,该方法工艺简单,设备较为常规,可操作性强,且具有较强的可控性,可根据实际需要调整环形隔板的数量,环形隔板的间距,混合粉中增强材料的含量等,从而调整铜基复合材料的梯度分布,经过压制和烧结即可得到梯度分布可控的铜基复合材料,烧结有利于提高铜基复合材料的致密性。优选地,所述环形隔板两侧装入的混合粉中的增强材料的含量差为5%以内。环形隔板两侧装入的混合粉中的增强材料的含量差为5%以内时,相邻两层的混合粉中的增强材料的含量差较小,过渡层更加平缓。优选地,所述由内向外呈梯度分布为由内向外呈梯度升高。优选地,所述柱形模具为圆柱形模具。优选地,所述混合粉中增强材料的最高含量为25wt%。优选地,所述金属氧化物为al2o3、zro2、tio2、mgo、ceo2或la2o3;所述金属碳化物为tic、wc、b4c或cr3c2;所述金属硼化物为crb2、tib2或zrb2;所述难熔金属为w或mo。优选地,所述铜基材为cu粉,或cu粉与cr粉、zr粉、ti粉和fe粉中至少一种金属粉组成的合金粉。优选地,所述合金粉为cu-cr合金粉、cu-zr合金粉、cu-cr-zr合金粉、cu-ti合金粉或cu-fe合金粉;其中,所述cu-cr合金粉中cu粉和cr粉的质量比为100:0.4~1.2;所述cu-cr-zr合金粉中cu粉、cr粉和zr粉的质量比为100:0.4~1.2:0.03~0.3;所述cu-zr合金粉中cu粉和zr粉的质量比为100:0.03~0.3;所述cu-ti合金粉中cu粉和ti粉的质量比为100:0.5~5;所述cu-fe合金粉中cu粉和fe粉的质量比为100:0.3~4。优选地,所述压制的压力为180~300mpa,所述压制的时间为6~8min。在180~300mpa的压力下压制6~8min,有利于提高坯料的致密化,过高的压力对设备要求较高,能源消耗较大。在此压力和时间内最经济。优选地,所述烧结的温度为950~1060℃,所述烧结的时间为1~5h,所述烧结的真空度为1×10-3~1×10-1pa。在950~1060℃和1×10-3~1×10-1pa烧结1~5h,有利于得到高致密化的铜基复合材料,真空条件下进行烧结有利于降低复合材料中的气体含量,有利于提高复合材料的致密度。优选地,所述铜基复合材料的制备方法还包括以下步骤:将烧结得到的铜基复合材料坯体作为自耗电极经真空自耗电弧熔炼法进行熔炼,熔炼过程中自耗电极熔融形成的熔体在电磁力的作用下垂直滴落形成熔池,熔池在电磁力的作用下旋转,冷却后,即得。铜基复合材料经真空自耗电弧熔炼法进行熔炼后,进一步提高了过渡层的均匀性,熔炼过程中,在电磁力的作用下,形成离心力,使得熔池定向旋转,使增强材料颗粒在铸坯的边部增多,心部减小,使过渡更加均匀,衔接更加流畅,提高材料的综合性能。真空电弧熔炼使自耗电极棒熔化再结晶,在真空和电磁力的作用下,在熔炼过程中保持负压,使气体排出熔炼炉外,保证了铸锭的致密化,同时杂质一般较轻,可以浮于熔体上方或在离心力的作下使杂质分布于边部,保证了铸锭的纯度。优选地,所述熔炼的电流为2500~4500a,所述熔炼的电压为23~28v。在2500~4500a的电流和23~28v的电压下进行熔炼,有利于电极进给量和熔化速度匹配,获得组织均匀的铸锭。优选地,所述电磁力是由稳弧电流产生的,所述稳弧电流为5~18a。5~18a的稳弧电流使得熔池旋转,形成离心力,使得增强材料颗粒在铸坯的边部增多,心部减小,使过渡更加均匀,衔接更加流畅,提高材料的综合性能。优选地,所述稳弧电流为7~15a。7~15a的稳弧电流更有利于相邻两层的混合粉中的增强材料的含量差较小,过渡层更加平缓。优选地,所述稳弧电流为7~12a。优选地,所述稳弧电流为7~10a。附图说明图1为实施例1的设置有环形隔板的柱形模具的示意图;图2为实施例1熔炼得到的铜基复合材料的示意图。具体实施方式下面结合具体实施方式对本发明作进一步说明。本发明的铜基复合材料的制备方法中,移去隔板后,进行震动、擀料、反向墩料,然后压制。优选的,所述震动为机械震动。所述震动时间为30~70s。优选的,所述擀料的时间为4~8min。优选的,所述反向墩料的次数为4~6次。本发明的铜基复合材料的制备方法中,所述压制的方法为冷等静压法。本发明的铜基复合材料的制备方法中,所述铜基材的粒径为1~200μm。所述增强材料的粒径为0.5~100μm。本发明的铜基复合材料的制备方法中,增强材料和铜基材的混合粉的制备方法为:将增强材料和铜基材在混料机内混粉2~16h。本发明的铜基复合材料的制备方法中,所述熔炼是在保护气体中进行的。所述保护气体为氦气。一、本发明的铜基复合材料的制备方法的具体实施例如下:实施例1本实施例的铜基复合材料的制备方法,以tic和纯铜组成的铜基复合材料为例,tic的质量百分含量沿垂直于柱体的铜基复合材料中心轴的方向由外环到内环依次为10%、5%和0%,步骤如下:(一)装粉(1)柱形模具的直径为80mm,两隔板的直径依次为60和40,将两隔板放入模具中,将模具分割成三个环状空间,如图1所示,1为模具,2为隔板,3为外环空间,4为两隔板间的中环空间,5为内环空间。(2)称取tic与铜粉,使得tic与铜粉的重量比为10:90,在混料机内混粉3h,记为混合粉ⅰ。称取tic与铜粉,使得tic与铜粉的重量比为5:95,在混料机内混粉3h,记为混合粉ⅱ。称取铜粉,记为混合粉ⅲ。(3)将混合粉ⅰ装入图1所示的外环空间中,混合粉ⅱ装入图1所示的中环空间中,混合粉ⅲ装入图1所示的内环空间中,然后将隔板抽出,进行震动40s、擀料5min、反向墩料4次。(二)压制采用冷等静压机步骤(一)得到的梯度混合粉进行压制,压制压力为250mpa,压制时间为7min,得到环型梯度坯料。(三)烧结对步骤(二)得到的坯料进行烧结,烧结的真空度为1×10-2pa,真空烧结有效降低了复合材料中的气体含量,有利于提高复合材料的致密度,真空烧结的温度为1000℃,真空烧结的时间为3h,得到铜基复合材料。实施例2本实施例的铜基复合材料的制备方法,与实施例1的不同之处在于,将实施例1步骤(三)得到的铜基复合材料作为自耗电极进行熔炼,步骤如下:将实施例1步骤(三)得到的铜基复合材料作为自耗电极,将自耗电极放入真空自耗电弧炉中,关闭炉门后对真空自耗电弧炉进行抽真空,随后充入保护气体氦气,进行真空自耗电弧炉熔炼,熔炼电流为3500a,熔炼电压为25v,在电弧的作用下,自耗电极熔化后滴落到水冷铜坩埚中,快速凝固成铸锭,稳弧电流为10a,保证了熔池旋转,形成离心力,增强材料颗粒在铸坯的边部增多,心部减小,使过渡更加均匀、流畅,得到铜基复合材料,如图2所示,图2为熔炼得到的铜基复合材料的示意图,图2中的黑点为增强相颗粒,增强相沿箭头方向由高到低分布。实施例3本实施例的铜基复合材料的制备方法,以al2o3和cu-ti合金粉组成的铜基复合材料为例,al2o3的质量百分含量沿垂直于柱体的铜基复合材料中心轴的方向由外环到内环依次为16%、12%、8%、4%和1%,步骤如下:(一)装粉(1)柱形模具的直径为80mm,四隔板的直径依次为70、60、50和40,将四隔板放入模具中,将模具分割成五个环状空间。(2)将cu粉和ti粉按照100:2的质量比混合,在混料机内混粉3h,得到cu-ti合金粉。称取al2o3与cu-ti合金粉,使得al2o3与cu-ti合金粉的重量比为16:84,在混料机内混粉5h,记为混合粉ⅰ。称取al2o3与cu-ti合金粉,使得al2o3与cu-ti合金粉的重量比为12:88,在混料机内混粉3h,记为混合粉ⅱ。称取al2o3与cu-ti合金粉,使得al2o3与cu-ti合金粉的重量比为8:92,在混料机内混粉5h,记为混合粉ⅲ。称取al2o3与cu-ti合金粉,使得al2o3与cu-ti合金粉的重量比为4:96,在混料机内混粉3h,记为混合粉ⅳ。称取al2o3与cu-ti合金粉,使得al2o3与cu-ti合金粉的重量比为1:99,在混料机内混粉3h,记为混合粉ⅴ。(3)将混合粉ⅰ、混合粉ⅱ、混合粉ⅲ、混合粉ⅳ和混合粉ⅴ分别装入五个环状空间中,使混合粉中的al2o3的含量由外环空间到内环空间呈梯度降低分布,然后将隔板抽出,进行震动40s、擀料5min、反向墩料4次。(二)压制采用冷等静压机步骤(一)得到的梯度混合粉进行压制,压制压力为180mpa,压制时间为8min,得到环型梯度坯料。(三)烧结对步骤(二)得到的坯料进行烧结,烧结的真空度为1×10-3pa,真空烧结有效降低了复合材料中的气体含量,有利于提高复合材料的致密度,真空烧结的温度为950℃,真空烧结的时间为2.5h,得到铜基复合材料自耗电极。(四)熔炼将步骤(三)得到的铜基复合材料自耗电极放入真空自耗电弧炉中,关闭炉门后对真空自耗电弧炉进行抽真空,随后充入保护气体氦气,进行真空自耗电弧炉熔炼,熔炼电流为4500a,熔炼电压为23v,在电弧的作用下,自耗电极熔化后滴落到水冷铜坩埚中,快速凝固成铸锭,稳弧电流为13a,得到铜基复合材料。实施例4本实施例的铜基复合材料的制备方法,以tib2和cu-fe合金粉组成的铜基复合材料为例,tib2的质量百分含量沿垂直于柱体的铜基复合材料中心轴的方向由外环到内环依次为25%、20%、15%、10%、5%和0%,步骤如下:(一)装粉(1)柱形模具的直径为80,五隔板的直径依次为70、60、50、40和30,将五隔板放入模具中,将模具分割成六个环状空间。(2)将cu粉和fe粉按照100:4的质量比混合,在混料机内混粉3h,得到cu-fe合金粉。称取tib2与cu-fe合金粉,使得tib2与cu-fe合金粉的重量比为25:75,在混料机内混粉5h,记为混合粉ⅰ。称取tib2与cu-fe合金粉,使得tib2与cu-fe合金粉的重量比为20:80,在混料机内混粉3h,记为混合粉ⅱ。称取tib2与cu-fe合金粉,使得tib2与cu-fe合金粉的重量比为15:85,在混料机内混粉5h,记为混合粉ⅲ。称取tib2与cu-fe合金粉,使得tib2与cu-fe合金粉的重量比为10:90,在混料机内混粉3h,记为混合粉ⅳ。称取tib2与cu-fe合金粉,使得tib2与cu-fe合金粉的重量比为5:95,在混料机内混粉3h,记为混合粉ⅴ。称取cu-fe合金粉,记为混合粉ⅵ。(3)将混合粉ⅰ、混合粉ⅱ、混合粉ⅲ、混合粉ⅳ、混合粉ⅴ和混合粉ⅵ分别装入六个环状空间中,使混合粉中的tib2的含量由外环空间到内环空间呈梯度降低分布,然后将隔板抽出,进行震动40s、擀料5min、反向墩料4次。(二)压制采用冷等静压机步骤(一)得到的梯度混合粉进行压制,压制压力为300mpa,压制时间为6min,得到环型梯度坯料。(三)烧结对步骤(二)得到的坯料进行烧结,烧结的真空度为1×10-1pa,真空烧结有效降低了复合材料中的气体含量,有利于提高复合材料的致密度,真空烧结的温度为1060℃,真空烧结的时间为3h,得到铜基复合材料自耗电极。(四)熔炼将步骤(三)得到的铜基复合材料自耗电极放入真空自耗电弧炉中,关闭炉门后对真空自耗电弧炉进行抽真空,随后充入保护气体氦气,进行真空自耗电弧炉熔炼,熔炼电流为2500a,熔炼电压为28v,在电弧的作用下,自耗电极熔化后滴落到水冷铜坩埚中,快速凝固成铸锭,稳弧电流为10a,得到铜基复合材料。实施例5本实施例的铜基复合材料的制备方法,以w和cu-cr-zr合金粉组成的铜基复合材料为例,w的质量百分含量沿垂直于柱体的铜基复合材料中心轴的方向由外环到内环依次为12%、9%、6%、3%和0%,步骤如下:(一)装粉(1)柱形模具的直径为80,四隔板的直径依次为70、60、50和40,将四隔板放入模具中,将模具分割成五个环状空间。(2)将cu粉、cr粉和zr粉按照100:1:0.2的质量比混合,在混料机内混粉3h,得到cu-cr-zr合金粉。称取w与cu-cr-zr合金粉,使得w与cu-cr-zr合金粉的重量比为12:88,在混料机内混粉5h,记为混合粉ⅰ。称取w与cu-cr-zr合金粉,使得w与cu-cr-zr合金粉的重量比为9:91,在混料机内混粉3h,记为混合粉ⅱ。称取w与cu-cr-zr合金粉,使得w与cu-cr-zr合金粉的重量比为6:94,在混料机内混粉5h,记为混合粉ⅲ。称取w与cu-cr-zr合金粉,使得w与cu-cr-zr合金粉的重量比为3:97,在混料机内混粉3h,记为混合粉ⅳ。称取cu-cr-zr合金粉,记为混合粉ⅴ。(3)将混合粉ⅰ、混合粉ⅱ、混合粉ⅲ、混合粉ⅳ和混合粉ⅴ分别装入五个环状空间中,使混合粉中的w的含量由外环空间到内环空间呈梯度降低分布,然后将隔板抽出,进行震动40s、擀料5min、反向墩料4次。(二)压制采用冷等静压机步骤(一)得到的梯度混合粉进行压制,压制压力为220mpa,压制时间为7.5min,得到环型梯度坯料。(三)烧结对步骤(二)得到的坯料进行烧结,烧结的真空度为1×10-2pa,真空烧结有效降低了复合材料中的气体含量,有利于提高复合材料的致密度,真空烧结的温度为1020℃,真空烧结的时间为3h,得到铜基复合材料自耗电极。(四)熔炼将步骤(三)得到的铜基复合材料自耗电极放入真空自耗电弧炉中,关闭炉门后对真空自耗电弧炉进行抽真空,随后充入保护气体氦气,进行真空自耗电弧炉熔炼,熔炼电流为3000a,熔炼电压为25v,在电弧的作用下,自耗电极熔化后滴落到水冷铜坩埚中,快速凝固成铸锭,稳弧电流为14a,得到铜基复合材料。实施例6本实施例的铜基复合材料的制备方法,以wc和cu-zr合金粉组成的铜基复合材料为例,wc的质量百分含量沿垂直于柱体的铜基复合材料中心轴的方向由外环到内环依次为5%、3%和0%,步骤如下:(一)装粉(1)柱形模具的直径为80,两隔板的直径依次为60和40,将两隔板放入模具中,将模具分割成三个环状空间。(2)将cu粉和zr粉按照100:0.3的质量比混合,在混料机内混粉3h,得到cu-zr合金粉。称取wc与cu-zr合金粉,使得wc与cu-zr合金粉的重量比为5:95,在混料机内混粉5h,记为混合粉ⅰ。称取wc与cu-zr合金粉,使得wc与cu-zr合金粉的重量比为3:97,在混料机内混粉3h,记为混合粉ⅱ。称取cu-zr合金粉,记为混合粉ⅲ。(3)将混合粉ⅰ、混合粉ⅱ和混合粉ⅲ分别装入三个环状空间中,使混合粉中的wc的含量由外环空间到内环空间呈梯度降低分布,然后将隔板抽出,进行震动40s、擀料5min、反向墩料4次。(二)压制采用冷等静压机步骤(一)得到的梯度混合粉进行压制,压制压力为220mpa,压制时间为7.5min,得到环型梯度坯料。(三)烧结对步骤(二)得到的坯料进行烧结,烧结的真空度为1×10-2pa,真空烧结有效降低了复合材料中的气体含量,有利于提高复合材料的致密度,真空烧结的温度为1020℃,真空烧结的时间为2.5h,得到铜基复合材料自耗电极。(四)熔炼将步骤(三)得到的铜基复合材料自耗电极放入真空自耗电弧炉中,关闭炉门后对真空自耗电弧炉进行抽真空,随后充入保护气体氦气,进行真空自耗电弧炉熔炼,熔炼电流为3000a,熔炼电压为25v,在电弧的作用下,自耗电极熔化后滴落到水冷铜坩埚中,快速凝固成铸锭,稳弧电流为9a,得到铜基复合材料。实施例7-16实施例7-16与实施例3的不同之处仅在于,增强材料或铜基材不同,其余步骤同实施例3,实施例7-16的增强材料和铜基材如表1所示。表1实施例3和实施例7-16的增强材料和铜基材增强材料铜基材实施例3al2o3cu-ti合金粉(cu粉和ti粉的质量比为100:2)实施例7zro2cu-ti合金粉(cu粉和ti粉的质量比为100:2)实施例8tio2cu-ti合金粉(cu粉和ti粉的质量比为100:2)实施例9ticcu-ti合金粉(cu粉和ti粉的质量比为100:2)实施例10wccu-ti合金粉(cu粉和ti粉的质量比为100:2)实施例11b4ccu-ti合金粉(cu粉和ti粉的质量比为100:2)实施例12tib2cu-ti合金粉(cu粉和ti粉的质量比为100:2)实施例13mocu-ti合金粉(cu粉和ti粉的质量比为100:2)实施例14al2o3cu-ti合金粉(cu粉和ti粉的质量比为100:1)实施例15al2o3cu-ti合金粉(cu粉和ti粉的质量比为100:5)实施例16al2o3cu-fe合金粉(cu粉和fe粉的质量比为100:4)实施例17-20实施例17-20与实施例2的不同之处仅在于,增强材料或铜基材不同,其余步骤同实施例2,实施例17-20的增强材料和铜基材如表2所示。表2实施例17-20与实施例2的稳弧电流实施例21-28实施例21-28与实施例3的不同之处仅在于,增强材料或铜基材不同,其余步骤同实施例3,实施例21-28的增强材料和铜基材如表3所示。表3实施例21-28与实施例3的稳弧电流稳弧电流(a)实施例313实施例215实施例226实施例237实施例248实施例259实施例2610实施例2711实施例2812实施例29-36实施例29-36与实施例4的不同之处仅在于,增强材料或铜基材不同,其余步骤同实施例4,实施例29-36的增强材料和铜基材如表4所示。表4实施例29-36与实施例4的稳弧电流实施例37-41实施例37-41与实施例4的不同之处仅在于,增强材料或铜基材不同,其余步骤同实施例4,实施例37-41的增强材料和铜基材如表4所示。表5实施例37-41与实施例5的稳弧电流稳弧电流(a)实施例59实施例374实施例385实施例396实施例407实施例418实施例42实施例42的铜基复合材料的制备方法,与实施例2的不同之处在于,稳弧电流为5a,其余步骤同实施例2。二、本发明的铜基复合材料的实施例,分别对应铜基复合材料的制备方法实施例1-42的最终产品。三、实验例对以上典型实施例的铜基复合材料进行性能测试,测试项目包括导电率、硬度和摩擦率。具体地,按照gb/t32791-2016铜及铜合金导电率涡流测试方法检测导电率;按照gb/t231.1-2009金属布氏硬度测试方法检测硬度;耐磨性的检测采用高速载流摩擦磨损试验机进行测试,测试条件为:压力60n,电流70a,检测结果如表6所示。表6典型实施例的铜基复合材料的性能测试结果材料导电率/%iacs硬度/hwb摩擦率/mg/m实施例1:tic/cu505525实施例2:tic/cu678315实施例6:wc/cu-cr839212实施例42:tic/cu657917(注:1)基体为合金基体时,如实施例6的cu-cr合金基体时,将熔炼所得制品在475℃进行时效处理4h,然后再进行导电率、硬度和载流摩擦率测试。2)导电率、硬度和载流摩擦率测试均是测量增强相含量最大端/面,在本发明的实施例中为圆柱体的外周面。)烧结态纯铜的导电率为75%iacs,硬度为42hwb;熔铸态纯铜的导电率为99%iacs,硬度为51hwb。。通过表6的实验结果可知,本发明的铜基复合材料在纯铜端和增强相含量最大端表现出不同性质,从而可以适用于特殊领域的连接需求。当前第1页1 2 3 
起点商标作为专业知识产权交易平台,可以帮助大家解决很多问题,如果大家想要了解更多知产交易信息请点击 【在线咨询】或添加微信 【19522093243】与客服一对一沟通,为大家解决相关问题。
此文章来源于网络,如有侵权,请联系删除



tips