一种连铸过程高低频数据与切割铸坯号匹配的方法与流程



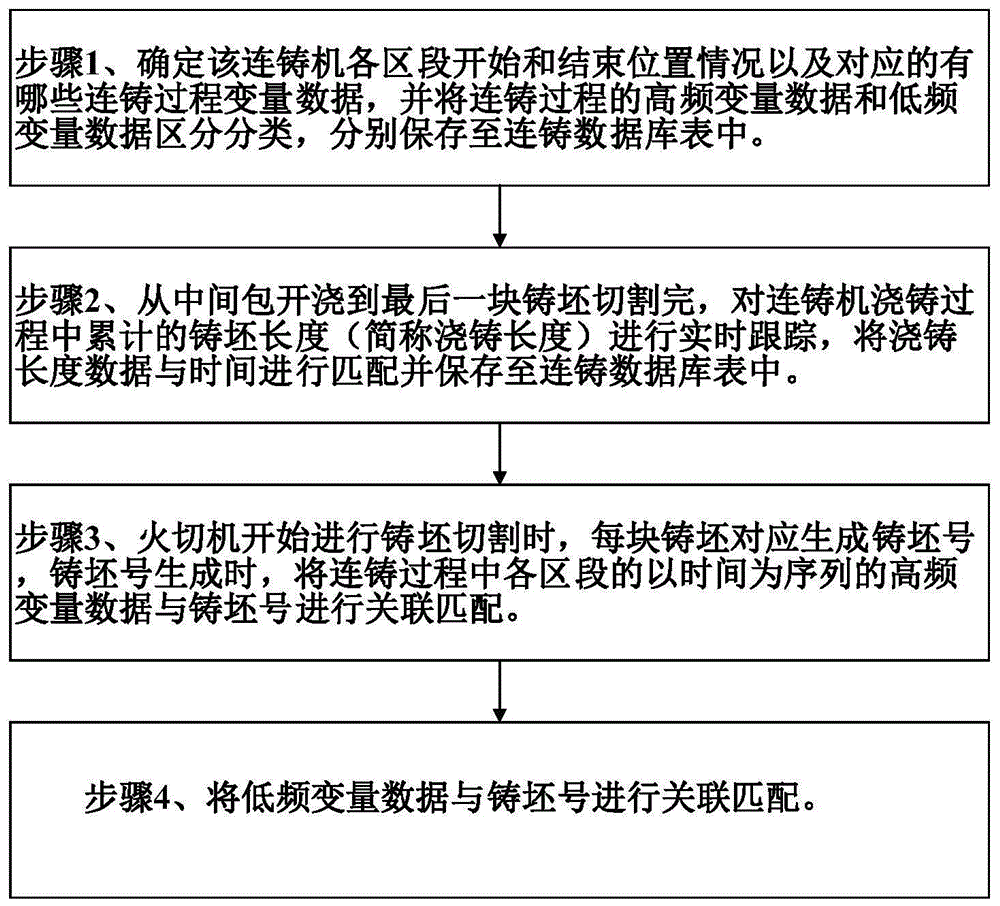
本发明属于智能制造领域,更具体地说,涉及一种连铸过程高低频数据与切割铸坯号匹配的方法。
背景技术:
我国工业和信息化部选择在包括钢铁行业在内的重点制造业领域推进智能制造的发展,借助智能制造实现转型升级。智能制造适合自动化程度较高的行业,我国钢铁行业基本已经实现了较完善的一级到五级自动化控制系统,自动化程度最高的制造业之一,已经完全具备实现智能制造的基础。开展钢铁行业全流程的质量分析、管理和智能化控制技术研究是实现钢铁行业智能制造水平根本性提升的领先技术,其中连铸过程铸坯质量大数据分析和管控是其中非常重要的一部分。针对连铸过程铸坯质量大数据分析和管控,首先要解决连铸过程不同系统(一级、二级和三级)的过程数据与切割铸坯的关联关系,因为铸坯质量的产生是由于连铸过程工艺或设备等参数数据异常等引起的,或者说铸坯质量的影响因素是连铸过程众多复杂的工艺或设备等参数。有了连铸过程数据与切割铸坯的关联关系,这样才能根据铸坯精整检查的实际质量问题溯源分析连铸过程数据,构建铸坯质量预测、判定模型以及进行连铸过程工艺参数优化,才能深度挖掘数据内在价值。连铸过程不同系统(一级、二级和三级)的过程数据采集频率是不一样的,分为高频和低频数据。连铸切割铸坯以铸坯号为索引进行标记。所以,研究连铸过程高低频数据与切割铸坯号匹配的方法,是实现连铸过程铸坯质量大数据分析和管控的基础,对实现数字化连铸坯具有重要意义。
目前连铸过程高低频数据与切割铸坯号匹配的方法,主要是采用铸坯切片或单元实时跟踪的方法,如专利cn109047683a、cn109034665a、cn106735029a、cn103920859a和cn102319883a等。铸坯切片实时跟踪的具体过程是:将整个铸流的铸坯长度(从结晶器到切割点)分成若干个小铸坯段作为基本处理单元或切片,对所有单元或切片进行跟踪和管理;切片的标识以产生的流水号、时间和浇铸长度定义,切片的移动位置(距弯月面的距离)根据该时刻的浇铸长度与切片产生时刻的浇铸长度差确定,当切片在铸机内经过结晶器、二冷分区等位置时,根据该区开始和结束位置(距弯月面的距离)与切片位置比较判定,如果条件满足,则该区的生产过程参数数据实时采集记录时标记上该切片流水号;当不断移动的切片到达切割点,不再跟踪管理;对切割的定尺铸坯,根据包含的切片流水号,搜集各切片的数据信息,汇总起来即该切割铸坯相匹配的连铸过程数据或者说数字化信息。以上这种铸坯切片跟踪的方法的缺点主要有:①需要对铸流内所有的切片及其过程数据进行动态跟踪、存储和管理,在程序实现方面也是非常繁琐的;②铸坯切片划分的越细,对内存要求越高,切片划分的越粗,大量的切片数据组合到定尺铸坯上误差越大;③在铸坯切割时,将定尺铸坯内所有切片上的高低频数据信息汇总起来,组成该切割铸坯的数字化信息,这里面主要问题是各切片上高频数据的时间点在很多情况下由于跟踪误差无法连续衔接起来,造成该切割铸坯上高频数据时间轴不正常,直接影响该切割铸坯数字化信息的准确性;④要实现切割定尺铸坯的数字化管控,匹配上连续、完整、准确地连铸过程高低频数据是非常重要的,即使采用切片跟踪,最终还是要转化到切割铸坯上;⑤切割铸坯在精整检查时的质量缺陷类别、等级标签信息均是以铸坯号为索引给出,要进行这块铸坯质量缺陷原因溯源分析或者构建质量缺陷预测模型,均需要这块铸坯的铸坯号匹配上连续、完整、准确的连铸过程。
技术实现要素:
1.要解决的问题
针对上述现有技术的不足,本发明提供了一种连铸过程高低频数据与切割铸坯号匹配的方法,不采用繁琐的切片跟踪方法,直接以切割的定尺铸坯为对象,将连铸过程的高低频数据连续、完整、准确地定位到该定尺铸坯上,该方法实现起来简单而且准确可靠,适用性更强,为实现铸坯的数字化管控和质量智能化分析奠定重要基础。
2.技术方案
为了解决上述问题,本发明所采用的技术方案如下:
本发明的一种连铸过程高低频数据与切割铸坯号匹配的方法,包括以下步骤:
步骤1、确定该连铸机各区段开始和结束位置情况以及对应的有哪些连铸过程变量数据,并将连铸过程的高频变量数据和低频变量数据区分分类,分别保存至连铸数据库表中;
步骤2、从中间包开浇到最后一块铸坯切割完,对连铸机浇铸过程中累积的铸坯长度(简称浇铸长度)进行实时跟踪,将浇铸长度数据与时间进行匹配并保存至连铸数据库表中;
步骤3、火切机开始进行铸坯切割时,每块铸坯对应生成铸坯号,铸坯号生成时,将连铸过程中各区段的以时间为序列的高频变量数据与铸坯号进行关联匹配;
步骤4、将低频变量数据与铸坯号进行关联匹配。
作为本发明的进一步说明,所述步骤4中,连铸过程中每一炉钢水浇铸时,将该炉的炉次号与低频变量数据进行关联匹配,然后在铸坯切割时再将炉次号对应的低频变量数据与铸坯号进行匹配。
作为本发明的进一步说明,所述步骤1中,高频变量数据以时间为索引保存的,低频变量数据以炉次号为索引保存的。高频数据采集频率是0.5或者1s级别的,低频数据以炉次号为索引的,每一炉钢水对应一个炉次号,低频数据采集频率是两个炉次之间的间隔,在30分钟到60分钟。
作为本发明的进一步说明,所述步骤2中,浇铸长度数据为高频变量数据,要求采集保存时间间隔不大于500ms。
作为本发明的进一步说明,所述步骤3中,具体包括:
a、根据切割点固定位置和此时总浇铸长度,反推每一块铸坯坯头和坯尾在结晶器弯月面形成时的浇铸长度数据,并在铸坯号生成时,将每一块铸坯坯头和坯尾在结晶器弯月面形成时的浇铸长度数据、开始切割时刻与铸坯号相匹配,一起保存至连铸数据库表中;
b、根据每一块铸坯坯头和坯尾在结晶器弯月面形成时的浇铸长度数据和连铸各区段高频变量数据影响位置范围,计算每一块铸坯经过连铸各区段开始和结束位置时的当前总浇铸长度;
c、根据每一块铸坯经过连铸各区段开始和结束位置时的当前总浇铸长度,以及浇铸长度数据与时间进行匹配的对应关系表,查询确定每一块铸坯坯头和坯尾经过连铸各区段开始和结束位置的时刻,根据每一块铸坯坯头和坯尾经过连铸各区段的时间范围,查询数据库中连铸高频变量的时间序列数据表,得到每一块铸坯在连铸各区段的以时间为序列的高频变量数据,将相关高频变量数据以铸坯号为关键字保存至连铸数据库表中。
作为本发明的进一步说明,所述步骤4中,低频变量数据包括大包浇铸开始时刻、大包浇铸结束时刻和大包实际浇铸的钢水重量、钢种、钢水实际成分。
作为本发明的进一步说明,所述步骤4中,具体包括:
大包开浇开始后,记录保存当前浇次第一炉实际浇铸钢水重量、第一炉和第二炉实际浇铸钢水重量累积之和、第一炉到第三炉实际浇铸钢水重量累积之和、……、第一炉到最后一炉实际浇铸钢水重量累积之和数据;通过铸坯称重系统依次获取每一流每一块切断铸坯的重量,采集所有铸流超过切割点未切割铸坯的浇铸长度、铸坯断面和铸坯密度,计算得到超过切割点未切割铸坯的重量。
作为本发明的进一步说明,所述步骤4中,通过已切断铸坯重量加超出切割点未切割铸坯重量,与实际浇铸钢水重量累积之和的数据进行对比,判断当前切断铸坯对应的钢水炉次号,将铸坯号信息与炉次号信息相匹配。
作为本发明的进一步说明,所述步骤4中,铸坯上存在不同炉次换包的相邻两个炉次钢水时,该铸坯为交接坯,通过计算相邻两个炉次钢水在铸坯重量上的占比,选取钢水重量占比比重大的炉次号及对应所有炉次信息数据(低频变量数据)与交接坯铸坯号匹配。
3.有益效果
相比于现有技术,本发明的有益效果为:
(1)本发明的一种连铸过程高低频数据与切割铸坯号匹配的方法,无需繁琐的切片跟踪方法,可直接以切割的定尺铸坯为对象,将连铸过程的高低频数据连续、完整、准确地定位到该定尺铸坯上,该方法实现起来简单而且准确可靠,适用性更强,可推广到任何单流或多流板坯、薄板坯、方坯、圆坯和异型坯等断面连铸机生产过程,与高低频数据与切割铸坯号的匹配,为实现不同断面铸坯的数字化管控和质量智能化分析奠定了重要基础;
(2)本发明的一种连铸过程高低频数据与切割铸坯号匹配的方法,针对连铸过程高频变量数据和低频变量数据特征及实际工艺特点,将高频变量数据和低频变量数据分开,分别提出了一种与切割铸坯号匹配的方法,对于连铸过程高频变量数据与切割铸坯号匹配,是采用浇铸长度、连铸各段(如中间包、结晶器或一冷区、足辊宽面、足辊窄面、二冷0段上部和下部等)高频数据对铸坯影响位置范围等来判断确定;对于连铸过程低频变量数据(主要是中间包内浇铸的炉次钢水信息)与切割铸坯号匹配,是采用一个浇次累积浇铸的次钢水重量、超过切割点的铸坯重量和交接坯等来判断确定,本发明方法相比较笼统的把高低频变量数据放在一起与切割铸坯号进行匹配更准确更合理。
附图说明
以下将结合附图和实施例来对本发明的技术方案作进一步的详细描述,但是应当知道,这些附图仅是为解释目的而设计的,因此不作为本发明范围的限定。此外,除非特别指出,这些附图仅意在概念性地说明此处描述的结构构造,而不必要依比例进行绘制。
图1为本发明的一种连铸过程高低频数据与切割铸坯号匹配的方法的基本流程图;
图2为本发明的一种连铸过程高低频数据与切割铸坯号匹配的方法实施例连铸机各段示意图及具体位置。
具体实施方式
下文对本发明的示例性实施例的详细描述参考了附图,该附图形成描述的一部分,在该附图中作为示例示出了本发明可实施的示例性实施例。尽管这些示例性实施例被充分详细地描述以使得本领域技术人员能够实施本发明,但应当理解可实现其他实施例且可在不脱离本发明的精神和范围的情况下对本发明作各种改变。下文对本发明的实施例的更详细的描述并不用于限制所要求的本发明的范围,而仅仅为了进行举例说明且不限制对本发明的特点和特征的描述,以提出执行本发明的最佳方式,并足以使得本领域技术人员能够实施本发明。因此,本发明的范围仅由所附权利要求来限定。
实施例
本发明实施例中,一种连铸过程高低频数据与切割铸坯号匹配的方法,如图1所示,包括如下步骤:
步骤1、根据实际连铸机结构、工艺、设备和自动化系统情况,确定该连铸机各段开始和结束位置情况以及对应的有哪些连铸过程变量数据,并将实际高频和低频变量数据区别分开,高频变量数据一般要求秒数数据方式保存到对应数据库表中(唯一的索引是时间字段),低频变量数据根据数据特征采用不同方式保存到数据库表中,比如是炉次数据,可以炉次为索引进行保存。
本发明实施例为一台两机两流板坯连铸机,浇铸钢种范围宽,包括超低碳钢、低碳钢、包晶钢和中碳钢等,浇铸板坯断面为230×(900~2150)mm2,采用组合式直结晶器,两块宽面铜板,两块窄面铜板,长度均为900mm,结晶器宽度和厚度根据板坯断面调整。整个连铸过程如下:首先钢水从浇铸位大包开浇,通过长水口流入中间包,中间包内钢水达到一定液位后开浇,通过浸入式水口流入结晶器,钢水在结晶器内凝固成一定厚度坯壳,在结晶器内的过程即为一冷,出结晶器后进入足辊段受到喷水冷却,坯壳宽面内弧侧和外弧侧分别受到一根足辊支撑,坯壳窄面左侧和右侧分别受到三根足辊支撑,为了防止窄面漏钢,足辊段窄面冷却长度比宽面冷却长度不同大,然后坯壳随拉坯进行,进入二冷0段、1段、2段、3段、4段、5段、7段、8段等,采用高压气雾冷却铸坯,最后进入空冷直到固定的切割点,火切机将其切成一块一块的定尺铸坯。该连铸机各段示意图及具体位置如图2所示。当大包回转台浇铸位大包钢水浇完后,会快速的连浇下一包钢水,每一包钢水对应唯一的炉次号。
当连铸开始生产时,每一包钢水调度到浇铸位开浇前,连铸操作工都会确认当前大包钢水对应炉次号,一旦大包开浇,该炉次号即为在浇炉次号,可根据浇铸位大包重量变化来判断当前炉次的开浇和浇铸结束。根据在浇炉次号和浇铸位大包净重的时间序列高频数据,用大包浇铸结束时刻浇铸位大包净重减去大包浇铸开始时刻浇铸位大包净重,得到该在浇炉次号对应的大包实际浇铸的钢水重量,再以该炉次号为索引,保存大包浇铸开始时刻、大包浇铸结束时刻和大包实际浇铸的钢水重量数据。然后,根据炉次号,从炼钢、精炼和连铸二级、三级生产数据库中查询匹配得到该炉次对应的钢种、钢水实际成分等历史实绩信息。最终得到的是一个以炉次号为索引,大包浇铸开始时刻、大包浇铸结束时刻和大包实际浇铸的钢水重量、钢种、钢水实际成分等的低频变量数据表。
连铸过程高频变量数据(一般为秒级数据)众多复杂,主要从中间包、结晶器到二冷各段的生产过程时间序列数据,铸机不同位置对应的高频数据由各段工艺和设备特点决定。中间包冶金过程的高频数据主要是连续测温的中间包温度及过热度、中间包塞棒位置、中间包塞棒吹氩量等。结晶器冶金过程(一冷段)的高频变量数据有:结晶器液位、结晶器四面铜板各自的冷却水流量、进出水温度和温差、结晶器振动负滑脱时间、振频和振幅、结晶器振动偏斜角、结晶器浇铸速度(拉速)、结晶器振动摩擦力、结晶器窄面左和右锥度、结晶器下口厚度和宽度等。二冷各段的高频变量数据有:足辊宽面水量、足辊窄面水量、二冷各冷却水回路水量和压力、二冷各段辊缝和夹紧辊压下力等。连铸过程高频变量数据直接影响到铸坯的表面和内部质量。
图2给出了铸机从结晶器到二冷各段具体的起始和结束位置,实际就是对应各段的高低频数据对铸坯的影响位置范围。而要特别注意,中间包内的高低频数据对铸坯的影响位置范围,这里取距离弯月面0m到0.4m这个范围。
步骤2、从中间包开浇到最后一块铸坯切割完,整个过程要实时跟踪该铸机当前浇次已经累积浇铸的铸坯总长度,简称浇铸长度,将不同时刻的实时浇铸长度保存到连铸数据库表(称为浇铸长度与时间对应关系表)中,该表字段主要是时间和浇铸长度,浇铸长度属于高频数据,要求采集保存时间间隔不大于500ms。
针对连铸开浇过程,一般是先将引锭杆通过上装方式装入结晶器内距离弯月面0.4m位置,当打开中间包出水口浇铸时,直到结晶器钢水装到靠近设定液位时引锭杆才拉坯,所以在开浇过程,浇铸长度数据在一开始始终为0.4m,直到拉坯,浇铸长度数据才随着拉坯速度慢慢增长。在拉坯以后,铸坯通过引锭杆和铸流流道内不同位置的编码器进行浇铸长度计算和位置跟踪。为了防止铸坯在流道内打滑引起浇铸长度的计算误差,在切割点实时对浇铸长度进行校正,因为切割点是固定位置(距弯月面47.355m)。尤其值得注意的是,在一个完整浇次中间包最后一包浇完或者断浇过程中间包浇完以后,实际浇铸长度会一直保持不变,该浇铸长度即为最后一块铸坯坯尾的浇铸长度。为了后续计算需要,本发明在此时仍通过拉速和时间的积分累积计算,再加上最后一块铸坯坯尾的浇铸长度,也就是假设中间包仍在浇铸,继续跟踪记录和保存实时的浇铸长度到对应数据库表中,直到全部铸坯切割完毕结束,也就是浇铸长度达到最后一块铸坯坯尾的浇铸长度和切割点到弯月面距离47.355m之和停止跟踪。
步骤3、基于以上步骤,进行连铸过程中间包、结晶器到二冷各段时间序列高频数据与切割铸坯号的匹配关联。这个步骤要在铸坯号生成时进行,实际生产时,铸坯号是在火切机开始切割时生成。
步骤3.1、当接收到火切机的开始切割信号,生成正在切割的铸坯编号(铸坯号)。此时火切机在固定的切割点(距离弯月面47.355m),记录下当前时刻(开始切割时刻)和当前总浇铸长度,从切割的第一块铸坯开始,依次计算当前切割铸坯的坯头和坯尾对应的浇铸长度,比如第一块铸坯(编号为100001)在08:50:00开始切割,此时实时总浇铸长度为56m,那么可算得100001铸坯坯头浇铸长度为0m,坯尾浇铸长度为:当前实时浇铸长度56m-切割点离弯月面距离47.355m=8.645m,第二块铸坯(编号为100002)在09:05:00开始切割,此时实时浇铸长度为65m,那么可算得100002铸坯坯头浇铸长度(即上一块铸坯坯尾浇铸长度)为:8.645m,坯尾浇铸长度为:当前实时浇铸长度65m-切割点离弯月面距离47.355m-上一块铸坯坯尾浇铸长度8.645m=9m;按照以上方法依次计算切割的每一块铸坯的坯头和坯尾对应的浇铸长度。将每一块铸坯的开始切割时刻、坯头和坯尾对应的在结晶器弯月面形成时的浇铸长度数据,保存到以该切割铸坯号为索引的数据库表中。
步骤3.2、在切割点,每开始切割一块铸坯,都生成一个铸坯号并计算对应的坯头和坯尾浇铸长度,然后根据该浇铸长度数据和连铸各段(如中间包、结晶器或一冷区、足辊宽面、足辊窄面、二冷0段上部和下部等)高频数据影响位置范围,计算每一块铸坯经过连铸各段开始和结束位置时的当前总浇铸长度。比如,以正开始切割的100001铸坯为例进行说明,根据100001铸坯坯头浇铸长度0m和坯尾浇铸长度8.645m,以及连铸各段高频数据影响位置范围,计算100001铸坯经过连铸各段开始和结束位置时的当前总浇铸长度,如表1所示。其中,100001铸坯经过各段开始位置时当前总浇铸长度=该段开始位置距弯月面距离+100001铸坯坯头浇铸长度0m,100001铸坯经过各段结束位置时当前总浇铸长度=该段结束位置距弯月面距离+100001铸坯坯尾浇铸长度8.645m。
表1100001铸坯经过连铸各段开始和结束位置时的当前总浇铸长度
步骤3.3、根据上述表1,以及步骤2中保存的浇铸长度与时间历史对应关系表,可查询确定每一块铸坯坯头和坯尾经过连铸各段开始和结束位置时的时刻,也就是每一块铸坯经过连铸各段时被该段高频变量数据的影响时间范围,由此可以根据此时间范围,查询数据库中连铸高频变量的时间序列数据表,取得影响每一块铸坯的各段高频变量时间序列数据,以切割铸坯号为关键字保存这些时间序列数据。
步骤4、基于以上步骤,再进行连铸过程低频变量数据与切割铸坯号的匹配关联,这里低频变量数据主要是在以炉次号为索引的,包含大包浇铸开始时刻、大包浇铸结束时刻和大包实际浇铸的钢水重量、钢种、钢水实际成分等的低频变量数据表,主要是中间包内浇铸的炉次钢水信息。
步骤4.1、从大包开浇开始,记录保存当前浇次第一炉实际浇铸钢水重量、第一炉和第二炉实际浇铸钢水重量累积之和、第一炉到第三炉实际浇铸钢水重量累积之和、……、第一炉到最后一炉实际浇铸钢水重量累积之和数据。同时,通过铸坯称重系统依次获取每一流每一块切断铸坯的重量,以及采用所有铸流超过切割点浇铸长度、铸坯断面和铸坯密度,计算超过切割点未切断的铸坯重量。当某一流某铸坯开始切割时,计算所有流已经切割的铸坯重量累积之和、以及各流超过切割点未切断的铸坯重量,与前面连浇到不同炉次时的钢水重量累积之和相比较,判断当前切断铸坯是对应哪一炉钢水浇铸而成的。
比如,对于双流板坯连铸机,两流浇铸断面相同,第1流正开始切割某一铸坯,生成铸坯号为100005,此时计算两个流已经切割的铸坯重量累积之和为276.46t,同时查询当前浇次第1炉(炉次号为30001)实际浇铸钢水重量为255.46t、第1炉和第2炉(炉次号为30002)实际浇铸钢水重量累积之和为512.09t,相比较明显可知,第1流正在切割的100005铸坯根据重量判断该铸坯是由当前浇次第2炉钢水浇铸而成。所以,与100005铸坯匹配的炉次低频数据为30002炉次信息数据,包括钢种、钢水实际成分等重要的低频变量数据。
步骤4.2、考虑到一个浇次会连浇很多炉次钢水,在不同炉次换包时就会存在相邻两个炉次钢水浇铸到一块铸坯上,该铸坯称为交接坯。在交接坯上有相邻两个炉次钢水,选择所占钢水重量大的炉次为该交接坯对应的炉次,这样就可以把炉次号匹配到交接坯铸坯号上,因此就可以以炉次号为索引的所有炉次信息数据(低频变量数据)匹配到交接坯铸坯号上。
比如,对于双流板坯连铸机,两流浇铸断面相同,第2流正开始切割某一铸坯,生成铸坯号为200004,此时计算两个流已经切割的铸坯重量累积之和为231.81t,第1流超过切割点未切断的铸坯重量约为6.52t,第2流超过切割点未切断的铸坯重量约为27.39t。同时查询当前浇次第1炉(炉次号为30001)实际浇铸钢水重量为255.46t、第1炉和第2炉(炉次号为30002)实际浇铸钢水重量累积之和为512.09t。相比较可知,第2流正在切割的200004铸坯根据重量判断它是交接坯,同时包含了第1炉和第2炉钢水,所以,需要看200004铸坯上所占哪一炉钢水重量大,根据以上数据计算可知,200004铸坯上所占第1炉钢水重量为:(255.46-231.81-(27.39-6.52))/2+(27.39-6.52)=22.26t,约占该铸坯总重量的81.27%,因此,与200004铸坯匹配的炉次低频数据为30001炉次信息数据,包括钢种、钢水实际成分等重要的低频变量数据。
本发明提出的一种连铸过程高低频数据与切割铸坯号匹配的方法可推广到任何单流或多流板坯、薄板坯、方坯、圆坯和异型坯等断面连铸机生产过程几乎所有高低频数据与切割铸坯号的匹配,为实现不同断面铸坯的数字化管控和质量智能化分析奠定了重要基础。
起点商标作为专业知识产权交易平台,可以帮助大家解决很多问题,如果大家想要了解更多知产交易信息请点击 【在线咨询】或添加微信 【19522093243】与客服一对一沟通,为大家解决相关问题。
此文章来源于网络,如有侵权,请联系删除


