一种适用于多种形状铸模的脱模系统及脱模方法与流程



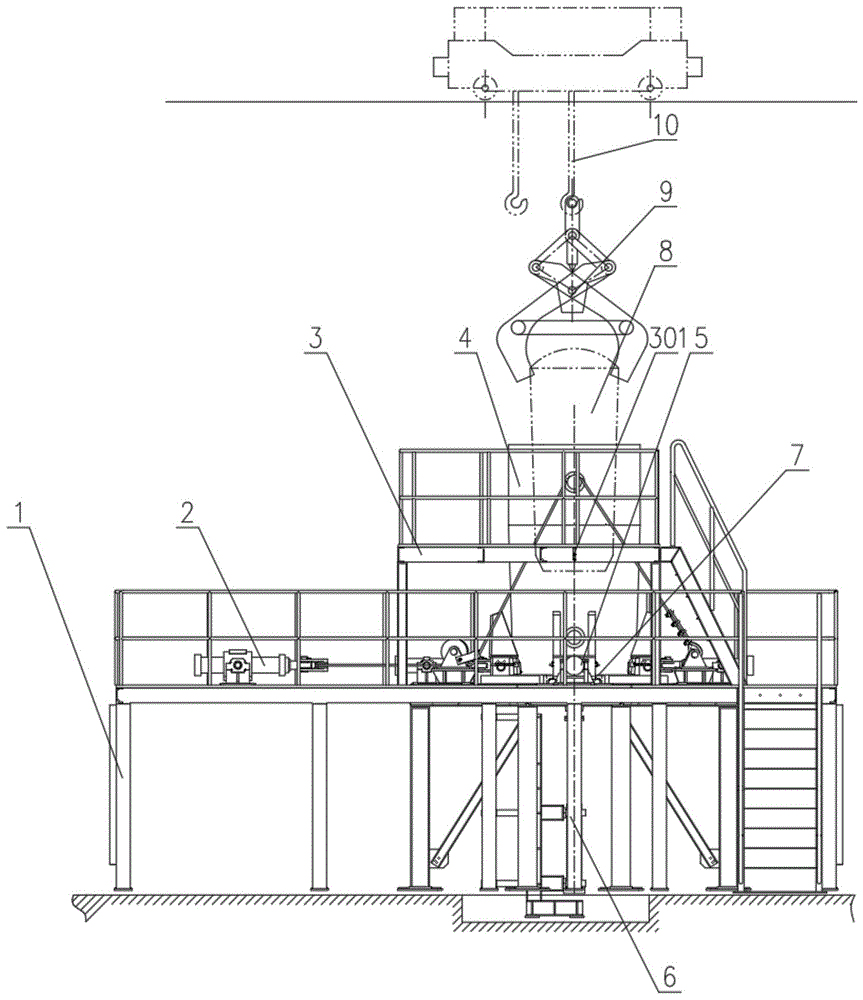
本发明属于冶金脱模技术领域,更具体地说,涉及一种适用于多种形状铸模的脱模系统及脱模方法。
背景技术:
在大多数的钢厂内,不同形状规格的钢锭脱模主要是利用行车将铸模由竖直旋转成水平状态,并移动行车,对铸模底部浇铸口进行撞击或者人工锤击底部,然后人工去掉悬挂在铸模上吊耳,铸模再由水平状态旋转为冒口朝下的竖直状态,最后铸模内钢锭顺着锥度的内壁滑落到地面上。这种脱模方式经过多次人工干预,工作效率低,有安全隐患,而且经过长期的锤击,容易造成铸模报废。并且在现有铸模浇铸工艺中,铸模形状分为:圆形铸模、方形铸模、六角铸模以及梅花铸模等多种形状规格。在传统的脱模工艺中,往往只针对一种特定形状规格的铸模进行相应设计,存在局限性。
针对上述问题也进行了相应的改进,如中国专利申请号cn201610534706.5,公开日为2016年9月28日,该专利公开了一种钢锭液压脱模装置,其包括:卡具机构,其设置有用于卡持钢锭模上沿的卡具头;液压机构,设置于卡具机构的顶部;所述液压机构的动力输出端设置有大活塞,所述大活塞沿竖直方向伸出或收回,且所述大活塞伸出后与钢锭模内的钢锭相接触。该专利的不足之处在于:该装置直接在浇铸位进行脱模,浇铸位环境温度高达500℃,很容易造成液压缸密封及液压系统损坏,并且针对多边形及尺寸不一的铸模,大多数铸模底部没有凸台时,该特定的卡具头无法夹紧,该装置下方没有承载钢锭平台,脱模后直接掉落,有安全隐患。
又如中国专利申请号cn201911118263.1,公开日为2020年2月28日,该专利公开了一种脱模机组及脱模方法,该脱模机组包括多自由度升降翻转装置、顶出装置和导向装置,多自由度升降翻转装置包括移动平台、翻转平台和升降机构,升降机构的顶部与翻转平台的底部枢接,翻转平台的底部设置有推动翻转平台翻转的第一驱动装置,移动平台能移动地设置在翻转平台的顶部,移动平台的顶部固定钢锭模,以使移动平台的移动方向与感应棒的轴向相垂直;顶出装置和导向装置分别设置于多自由度升降翻转装置的两侧,顶出装置与感应棒的端部相抵,并自钢锭模的推力施加端向感应棒施加推力,导向装置连接在钢锭模与接收缓冲区之间。该专利的不足之处在于:该装置解决了由于重力强制脱模带来的损坏,减少了安全隐患,但是水平顶出装置需要将钢锭至少顶出一般长度,才可滑落,对于长度较长钢锭,顶出装置的油缸和顶杆需要设计很长,在顶出过程中,较长的顶杆受压力变形,导致顶出力不在中心线上,并且铸模内一般都为上大下小的锥形,在顶出过程中,锥形钢锭容易偏心,造成脱模卡顿;平台上的限位通槽只能适用于圆形铸模,针对方形、六边形、梅花形铸模无法适用。
技术实现要素:
1、要解决的问题
针对现有铸模脱模效率低和安全性差的问题,本发明提供一种适用于多种形状铸模的脱模系统及脱模方法。本发明所述的脱模系统能够适应不同形状的铸模进行脱模操作,同时对对铸模夹紧牢固,工作效率和安全稳定高;本发明所述的脱模方法操作简便,全程实现自动化操作,节省人力成本。
2、技术方案
为解决上述问题,本发明采用如下的技术方案。
一种适用于多种形状铸模的脱模系统,包括工作平台,工作平台上设置有放置铸模的工作位,工作位的下方设置有用于顶升铸模内钢锭的脱模装置,工作位上还设置有铸模夹紧装置,铸模夹紧装置包括驱动件,与驱动件连接的滑座,滑座通过滑块与压板滑动连接,滑座上设置有导向板,滑座中与铸模接触的侧面设置有夹紧机构,夹紧机构与滑座活动连接,且夹紧机构与滑座上的弹性件连接。
更进一步的,所述夹紧机构包括夹紧座,所述夹紧座呈倒“v”形,夹紧座中与铸模接触的侧面设置有夹板,夹紧座通过旋转轴与滑座连接,夹紧座的一端与弹性件固定连接。
更进一步的,铸模夹紧装置的数量为四个,在工作位上两两呈一条直线设置,同时每个驱动件上设置有线性位移传感器。
更进一步的,工作位上还设置有拉紧装置,所述拉紧装置包括钢丝绳,钢丝绳的两端分别依次通过导向定滑轮、铸模上的吊耳与固定座连接,钢丝绳的中部通过连接头与拉紧油缸连接。
更进一步的,所述拉紧油缸通过拉紧油缸上的连接耳轴设置在多自由度安装座内,多自由度安装座的两侧设置有焊接轴,多自由度安装座通过焊接轴与固定底座连接。
更进一步的,导向定滑轮的下方设置对钢丝绳起导向作用的楔块,所述楔块包括上部和下部,上部的截面呈矩形状,且上部的顶端设置有圆弧槽,圆弧槽的形状与导向定滑轮形状相匹配;下部的截面呈倒锥形状。
更进一步的,所述顶升装置包括脱模油缸,脱模油缸与脱模杆连接,脱模杆的顶端设置有顶头。
更进一步的,顶升装置还包括导向机构,所述导向机构包括上导向座,上导向座内设置有供脱模杆穿过的导向套,且上导向座的上下两端均设置有毡圈密封盖。
更进一步的,工作平台设置在检修平台上,检修平台设置在地面上,检修平台上铺设钢格板,且检修平台与工作平台的四周均设置有护栏。
一种利用如上述任一项所述的适用于多种形状铸模的脱模系统的脱模方法,包括如下步骤:
s1:铸模通过行车吊运至工作位上方;
s2:行车继续将铸模向下吊运,吊运至工作位上,此时铸模夹紧装置动作对铸模进行夹紧;
s3:夹紧铸模后脱模装置动作,完成铸模内钢锭与铸模内壁的分离;
s4:对钢锭进行起吊,整个脱模过程结束。
3、有益效果
相比于现有技术,本发明的有益效果为:
(1)本发明中的滑座通过在压板上的滑行实现导向板与铸模的接触,动作平稳;在铸模放入工作位这一过程中导向板起到导向作用,保证铸模进入工作位的准确性能;同时当铸模放入工作位时,通过夹紧机构对铸模进行进一步夹紧固定,并且不同的铸模其表面形状也不一致,夹紧机构能够根据不同形状的铸模进行位置调整,便于与铸模更紧密的贴合,提高夹紧效果;并且通弹性件实现夹紧机构的复位,操作简单;整个系统工作效率高且减小人员干预,增加安全性,同时成本较低;
(2)本发明夹紧机构中的夹紧座设计成倒“v”形是为了适应与多种不同形状的铸模进行夹紧,且在夹紧座与铸模接触的表面设置夹板,夹板与铸模直接接触避免铸模对夹紧座造成损坏,提高部件的使用寿命;不同形状的铸模重量不一致,在铸模重力的作用下,铸模推动夹紧座绕着旋转轴旋转一定角度,使得夹板与铸模贴合紧密,增加部件的使用性能;
(3)本发明在工作位上设置四个铸模夹紧装置,并且两两在一条直线上,实现对铸模不同的角度的夹紧,进一步提高铸模夹紧力,保证脱模工作的顺利进行;同时在每个铸模夹紧装置中的驱动件上设置有线性位移器,线性位移器内依据铸模形状不同设定不同参数,能够在铸模未吊运至工作位时对四组铸模夹紧装置进行一个开口度的调节,使四个铸模夹紧装置围成的工作位适应于对应铸模的大小,增加了整个过程的智能化处理,工作效率高;
(4)本发明在工作位上还设置有拉紧装置,铸模夹紧装置对铸模进行一个左右方向的约束,拉紧装置进一步实现铸模向上的约束,进一步保证在进行脱模过程中铸模的稳固性能和安全性能;通过拉紧油缸缩回过程实现钢丝绳对铸模上吊耳的拉紧,拉紧油缸伸出实现钢丝绳对铸模上吊耳的松开,结构新颖,同时操作简便,成本较低;
(5)本发明中的拉紧油缸通过拉紧油缸上的连接耳轴固定在多自由度安装座上,使得拉紧油缸可绕着连接耳轴进行摆动;同时在多自由度安装座的两侧设置有焊接轴,焊接轴的一端与多自由度安装座连接,另一端通过铜套与固定底座连接,固定底座设置在多自由度安装座的下方,使得多自由度安装座可绕着焊接轴进行摆动,以便在钢丝绳进行拉紧过程中,补偿由于铸模上两个吊耳制造误差带来的影响以及两端钢丝绳拉紧力不同步的影响;
(6)本发明在导向定滑轮的下方两端均设置有楔块,楔块的设置对钢丝绳起到一个导向作用,将楔块的上部顶端设置成与导向定滑轮形状匹配的圆弧槽,便于钢丝绳的滑动;同时将下部截面设置成锥形状,有效帮助钢丝绳从导向定滑轮的底部继续滑入导向定滑轮中,避免钢丝绳发生卡阻现象;
(7)本发明中的脱模装置通过脱模油缸驱动脱模杆穿过铸模底部的孔对钢锭进行顶升,使得钢锭与铸模内壁脱离,整个动作简单平稳;并且还设置有导向机构,通过脱模杆在导向机构中的导向套内上下移动,避免由于导向杆的脱模力与重力偏移带来的卡顿和卡死现象;且上导向座的两端均设置有毡圈密封盖,对导向套起到保护作用,提高导向套的使用寿命;
(8)本发明所述的一种脱模方法操作简便,全程可实现自动化脱模操作,极大提高了钢锭脱模的效率,同时节省了人力资源成本的投入,保证脱模过程的安全性,具有较高的经济使用价值和应用前景。
附图说明
图1为本发明的系统主视图;
图2为本发明的系统立体图;
图3为本发明的拉紧装置的主视图;
图4为本发明的拉紧装置的俯视图;
图5为图4中a-a方向视图;
图6为图4中b-b方向视图;
图7为本发明的铸模夹紧装置安装图;
图8为本发明的铸模夹紧装置主视图;
图9为本发明的铸模夹紧装置侧视图
图10为本发明的脱模装置主视图;
图11为本发明楔块的主视图;
图12为本发明楔块的侧视图。
图中:
1、检修平台;101、护栏;102、钢格板;103、楼梯;
2、拉紧装置;201、拉紧油缸;202、连接头;203、钢丝绳;204、导向定滑轮;205、钢丝绳夹;206、套环;207、固定座;208、多自由度安装座;209、铜套;210、焊接轴;211、固定底座;212、楔块;213、圆弧槽;214、下部;
3、工作平台;301、挂钩;302、扶梯;
4、铸模;
5、铸模夹紧装置;501、支撑架台;502、平板;503、压板;504、夹板;505、复位弹簧;506、导向板;507、旋转轴;508、夹紧油缸;509、安装座;510、滑块;511、滑座;512、夹紧机构;
6、脱模装置;601、连接座;602、脱模油缸;603、螺纹套;604、脱模杆;605、毡圈密封盖;606、导向套;607、顶头;608、上导向座;
7、垫板;8、钢锭;9、冒口夹具;10、行车。
具体实施方式
下面结合具体实施例和附图对本发明进一步进行描述。
实施例1
如图1、图2、图7、图8和图9所示,一种适用于多种形状铸模的脱模系统,包括工作平台3,工作平台3上设置有放置铸模4的工作位,所述工作位为设置在工作平台3上的垫板7,垫板7用于放置铸模4。工作位的下方设置有用于顶升铸模4内钢锭8的脱模装置6,所述脱模装置6设置在垫板7的正下方。具体的,如图10所示,所述脱模装置6包括脱模油缸602,脱模油缸602与连接座601固定连接,连接座601的底部可安装在地坑中。脱模油缸602与脱模杆604连接,脱模杆604的顶端设置有顶头607,优选的,所述顶头607设置呈弧面,增大与钢锭8的接触。通过脱模油缸602驱动脱模杆604进行上下直线运动,因铸模4的底部均会设置有孔,脱模杆604上的顶头607穿过该孔对铸模4内的钢锭8进行顶升从而完成钢锭8的脱模操作,脱模油缸602不直接与钢锭8接触,保护脱模油缸602不受损坏。为了进一步保证脱模杆604与脱模油缸602之间连接的稳固性,脱模油缸602中的活塞杆通过螺纹连接在螺纹套603中,螺纹套603内设置有下沉卡槽,脱模杆604通过法兰与活塞杆连接且同时脱模杆604与下沉卡槽配合,这样的设置使得脱模油缸602中活塞杆中心与脱模杆604中心直线重合度高,使得脱模杆604的工作稳定性能高。为了进一步保证脱模装置6的脱模效果,顶升装置6还包括导向机构,所述导向机构包括上导向座608,上导向座608内设置有供脱模杆604穿过的导向套606,且上导向座608的上下两端均设置有毡圈密封盖605,上导向座608通过螺栓固定在工作位上,毡圈密封盖605即为在盖板内设置有毡圈槽,在槽内安装毡圈,能够有效避免导向套606受到外界环境的污染,提高导向套606的使用寿命。其它能够实现铸模4内钢锭8脱离铸模内壁的脱模装置6均可使用在本发明中。
工作位上还设置有铸模夹紧装置5,铸模夹紧装置5和工作位均设置在支撑架台501上,铸模夹紧装置5包括驱动件,与驱动件连接的滑座511,滑座511通过滑块510与压板503滑动连接。具体的,所述驱动件在本实施中采用夹紧油缸508,结构简单,动力传输平稳。夹紧油缸508通过销轴安装在安装座509上,并且在销轴和安装座509之间设置有铜套,润滑销轴。夹紧油缸508的头部连接滑座511,滑座511设置在平板502上。在滑座511的底部设置有滑块510,且在平板502上设置有两条相对的压板503,压板503上开设有滑槽,滑块510可以在滑槽内进行滑行。通过夹紧油缸508驱动滑座511带动滑块510在压板503内滑行实现滑座511与铸模4的接触。滑座511上设置有导向板506。具体的,所述导向板506设置在滑座511的上部,且导向板506与铸模4接触的表面设置有凹槽,所述凹槽呈“v”形,在导向板506上开设凹槽一来减轻导向板506的整体重量从而减轻对滑座511的压力;二来使得与铸模4接触的导向板506具有一定斜度,能够对铸模4起到较好的导向作用,使得铸模4顺着导向板506继续下降直至到工作位上。具体的,因导向板506的表面设置有“v”形凹槽,且导向板506两端的截面为梯形,梯形中靠近铸模4的一个腰边与下底之间的夹角设置在50°~70°之间,角度过大或过小均不利于整体导向板506的导向作用。滑座511中与铸模4接触的侧面设置有夹紧机构512,夹紧机构512通过旋转轴507与滑座511活动连接,夹紧机构512能够绕着旋转轴507的中心旋转,且夹紧机构512与滑座511上的弹性件连接。一般来说,工厂内的铸模4形状主要由圆形、方形和六角形,不同的铸模4形状其外表面的形状也不一致,因夹紧机构512与铸模4直接接触,夹紧机构512受到不同形状铸模4的挤压从而绕着旋转轴507能够自动旋转一定角度增大与铸模4的接触面积,同时挤压弹性件,从而更好的与铸模4进行接触挤压,提高对铸模4的夹紧效果,且利用弹性件的弹力,在铸模4离开工作位后夹紧机构512能够自动恢复原状。
在本实施中夹紧机构512的具体结构如下:夹紧机构512包括夹紧座,所述夹紧座呈倒“v”形,本实施将夹紧座设计呈倒“v”形,一来因导向板506设计成v形,夹紧座和导向板506均是设置在滑座511上的,将夹紧座的形状与导向板506形状相匹配,方便二者在滑座511上的安装;二来因铸模4常用的形状为方形、圆形和六边形,倒“v”的形状方便与这三种形状的贴合达到夹紧效果,从而夹紧机构512能够实现对不同形状的铸模4进行夹紧工作。夹紧座中与铸模4接触的侧面设置有夹板504,夹板504的设置使得铸模4直接接触夹板504而不与夹紧座直接接触,保证夹紧座不受铸模4的损坏,提高部件的使用寿命。夹紧座通过旋转轴507与滑座511连接,夹紧座的一端与弹性件固定连接。此处所述弹性件为复位弹簧505,结构简单,易于安装且弹性较好。
在此之前,发明人之前申请过一篇专利名称为“一种多工位钢锭脱模系统及方法”,发明人在使用过程中发现通过移动电动平车将铸模4移动至脱模工作,通过底部曲柄和油缸顶升机构,进行脱模操作,操作过程繁琐,并且设置多个脱模工位时靠电动平车来回移动增加脱模时间,极大降低了脱模效率,同时脱模效果也并不是很理想。因此,经过发明人的不断探索与研究试验得到了本申请。本发明所述的适用于多种形状铸模的脱模系统能够适用多种不同形状的铸模4进行脱模操作,适用性广,且通过导向板506实现导向作用,夹紧机构512实现夹紧作用,夹紧机构512能够根据不同形状的铸模4进行位置调整,便于与铸模4更紧密的贴合,提高夹紧效果。整个系统结构简单,工作效率高且减小人员干预,增加安全性,同时成本较低。
一种利用如上述所述的适用于多种形状铸模的脱模系统的脱模方法,包括如下步骤:
s1:铸模4通过行车10吊运至工作位上方,行车10通过起吊铸模4上的两个吊耳将铸模4从浇铸位竖直吊运到工作位上方;
s2:行车10继续将铸模4向下吊运,吊运至工作位上,此时铸模夹紧装置5动作对铸模4进行夹紧;
s3:夹紧铸模4后脱模装置6动作,完成铸模4内钢锭8与铸模内壁的分离;
s4:行车10中的冒口夹具9对钢锭8中的冒口进行起吊直至钢锭8完全脱离铸模内壁,整个脱模过程结束。
本发明所述的脱模方法操作简便,全程实现自动化操作,节省人力成本。
实施例2
基本同实施例1,具体的,在本实施中,在工作位上设置有四个铸模夹紧装置5,两两为一组,且一组内的两个铸模夹紧装置5在一条直线上,四个铸模夹紧装置5所围成的区域即是铸模4放置的工作位。四组铸模夹紧装置5能够对铸模4进行全方面的夹紧,进一步提高夹紧效果,从而提高脱模过程的安全性。并且更进一步的,在夹紧油缸508上设置有线性位移传感器,每个线性位移传感器内设定有固定参数,该参数依照不同规格的铸模4进行选取。在进行吊运铸模4至工作位之前时,首先四个铸模夹紧装置5进行工作,使其围成的区域能够使用该铸模4的大小,每个夹紧油缸508开始动作,等到夹紧油缸508工作达到线性位移传感器固定参数时,夹紧油缸508停止动作,实现四个铸模夹紧装置5围成区域的工作位开口度调节,及时针对不同规格大小的铸模4进行调整,进一步提高工作效率以及提高工作的稳定性和准确性,保证铸模4准确落入工作位中。
实施例3
基本同实施例2,为了进一步保证铸模4在进行脱模过程中铸模4的稳定性,在本实施中如图3、图4、图5和图6所示,工作位上还设置有拉紧装置2,拉紧装置2包括钢丝绳203,钢丝绳203的两端分别依次通过导向定滑轮204、铸模4上的吊耳与固定座207连接,钢丝绳203的中部通过连接头202与拉紧油缸201连接。具体的,一根钢丝绳203弯成两段,两段分别依次穿过导向定滑轮204和铸模4上的吊耳,从吊耳延伸出的一端钢丝绳203通过钢丝绳夹205和套环206与固定底座211固定连接,这里将导向定滑轮204进行安装时,将导向定滑轮204与中心线偏摆角度β为6°-10°,这里的中心线与拉紧油缸201在工作方向的中心线保持在一条直线上,以便同时适用于最小和最大规格的铸模4拉力方向。钢丝绳203折弯的一端通过连接头202与拉紧油缸201连接,连接头202上设置有圆弧滑槽,钢丝绳203设置在圆弧滑槽内。本实施例所述的拉紧装置2通过拉紧油缸201缩回过程实现钢丝绳203对铸模4上吊耳的拉紧,拉紧油缸201伸出实现钢丝绳203对铸模4上吊耳的松开,结构新颖,同时操作简便,成本较低。铸模夹紧装置5对铸模4进行一个左右方向的约束,拉紧装置2进一步实现铸模4向上的约束,进一步保证在进行脱模过程中铸模4的稳固性能和安全性能。此处的钢丝绳203也可替换为起重链条或高强度拉绳。
同时,为了进一步提高自动化设置,将拉紧油缸201与夹紧油缸508进行联锁设置并且两个油缸均与脱模控制系统电连接,具体如下:因在进行脱模操作时,会在控制系统中设定夹紧压力值和拉紧压力值,这两个参数依据铸模4的不同进行具体设定,而拉紧油缸201与夹紧油缸508也会设定工作值。夹紧油缸508会设定一个工作压力值a,控制系统中夹紧压力值b,并且a<b;拉紧油缸201设定工作压力值c,控制系统中拉紧压力值d,并且c<d。脱模过程中,如果特殊情况下,夹紧油缸508发生泄漏,夹紧油缸508的压力值会急剧下降,此时铸模夹紧装置5不能夹紧铸模4,有极大的安全隐患,此时,拉紧油缸201与夹紧油缸508进行联锁,控制系统增加拉紧油缸201的工作压力至压力值d,即增大了铸模4的向下拉紧力,保证在特殊情况下,夹紧力失效情况下,脱模过程的安全性。同理,当脱模过程中,如果拉紧油缸201发生泄漏,拉紧油缸201压力值会急剧下降,此时拉紧装置2不能拉紧铸模4,也有极大的安全隐患,此时,拉紧油缸201与夹紧油缸508进行联锁,控制系统增加夹紧油缸508的工作压力值至压力值b,即增大了铸模4的夹紧力,保证在特殊情况下,拉紧力失效情况下,脱模过程的安全性。即拉紧装置2与铸模夹紧装置5相辅相成,联锁过程保证了脱模过程的安全性。因两个油缸进行联锁并且与控制系统进行电连接在现有技术中较为常见,因此在本实施中便不再详细赘述。
更进一步的,在本实施中将拉紧油缸201通过拉紧油缸201上的连接耳轴设置在多自由度安装座208内。具体的,拉紧油缸201的上下均设置有连接耳轴,连接耳轴通过铜套209竖直安装在多自由安装座208内,这样的设置使得拉紧油缸201能够绕着连接耳轴进行摆动。同时多自由度安装座208的两侧设置有焊接轴210,多自由度安装座208通过焊接轴210与固定底座211连接,焊接轴210一端与多自由安装座208连接,另一端通过铜套209插进固定底座211的孔中,铜套209设置在该孔内,而多自由安装座208是设置在固定底座211上的,这样的设置使得多自由度安装座208能够绕着焊接轴210进行摆动。整体可以实现拉紧油缸201的上下摆动和多自由度安装座208的左右摆动,以便在钢丝绳203拉紧过程中,补偿由于铸模4上两个吊耳制造误差带来的影响和两段钢丝绳203拉紧力不同步的影响,进一步保证了拉紧效果。
如图11和图12所示,导向定滑轮204的下方设置对钢丝绳203起导向作用的楔块212,在本实施中,在导向定滑轮204的两端下方均设置有楔块212,导向定滑轮204的两端即导向定滑轮204上钢丝绳203进出的两端。所述楔块212包括上部和下部214,上部的截面呈矩形状,且上部的顶端设置有圆弧槽213,圆弧槽213的形状与导向定滑轮204形状相匹配,同时圆弧槽213与导向定滑轮204之间留有5~10mm的间隙,以便导向定滑轮204的转动不受阻碍;下部214的截面呈倒锥形状,将下部214设置成倒锥形状,下部214截面中的斜边与水平线的夹角δ为60°~80°,同时下部214截面中的斜边延伸后与导向定滑轮204相切,当钢丝绳203从导向定滑轮204上滑出时,下部214中倒锥形状的截面能够有效帮助钢丝绳203重新滑入至导向定滑轮204上,避免钢丝绳203发生卡阻现象。
一种利用如上述所述的适用于多种形状铸模的脱模系统的脱模方法,包括如下步骤:
s1:铸模4通过行车10吊运至工作位上方,行车10通过起吊铸模4上的两个吊耳将铸模4从浇铸位竖直吊运到工作位上方;在这值得说明的是,在进行s1步骤之前,先进行一个预夹紧的操作。根据需进行脱模操作的铸模4形状大小设定线性位移传感器参数,此时四个夹紧油缸508同时动作,当夹紧油缸508上的线性位移传感器达到设定参数时,夹紧油缸508停止动作,此时四个夹紧油缸508所围成的区域形成工作位,该区域内放置铸模4。该步骤能够保证铸模4精准的进入到工作位,提高工作效率;
s2:行车10继续将铸模4向下吊运,在铸模4向下的过程中通过导向板506的导向作用顺利放置在工作位上,此时夹紧油缸508动作,直至夹板504与铸模4接触并夹紧,夹紧油缸508停止工作;夹紧完成后,将钢丝绳203挂在铸模4的吊耳上,此时拉紧装置2动作,拉紧油缸201收缩完成对钢丝绳203的拉紧,从而对铸模4进行拉紧;
s3:夹紧和拉紧铸模4后脱模装置6动作,完成铸模4内钢锭8与铸模内壁的分离;
s4:行车10中的冒口夹具9对钢锭8中的冒口进行起吊直至钢锭8完全竖直向上脱离铸模内壁,此时,拉紧装置2、铸模夹紧装置5和脱模装置6均回到初始工作状态,整个脱模过程结束。
实施例4
基本同实施例3,为了保证整个脱模过程现场环境的安全性,在本实施中将工作平台3设置在检修平台1上,检修平台1设置在地面上,检修平台1上铺设钢格板102,保证强度;同时检修平台1上还设置有人员检修通道和设备的放置空间。且检修平台1与工作平台3的四周均设置有护栏101。同时地面到检修平台1之间设置有楼梯103。工作平台3安装在检修平台1中的钢架上,且工作平台3与检修平台1之间设置有扶梯302,且在工作平台3上安装有挂钩301,挂钩301的设置用于放置钢丝绳203。当不进行脱模操作时,拉紧装置2中的钢丝绳203通过人工放置在挂钩301上,避免钢丝绳203散落在工作平台3上具有一定的安全隐患,进一步保证整个工作环境的安全能。
本发明所述实例仅仅是对本发明的优选实施方式进行描述,并非对本发明构思和范围进行限定,在不脱离本发明设计思想的前提下,本领域工程技术人员对本发明的技术方案作出的各种变形和改进,均应落入本发明的保护范围。
起点商标作为专业知识产权交易平台,可以帮助大家解决很多问题,如果大家想要了解更多知产交易信息请点击 【在线咨询】或添加微信 【19522093243】与客服一对一沟通,为大家解决相关问题。
此文章来源于网络,如有侵权,请联系删除


