一种高氮钢粉末的制备方法与流程



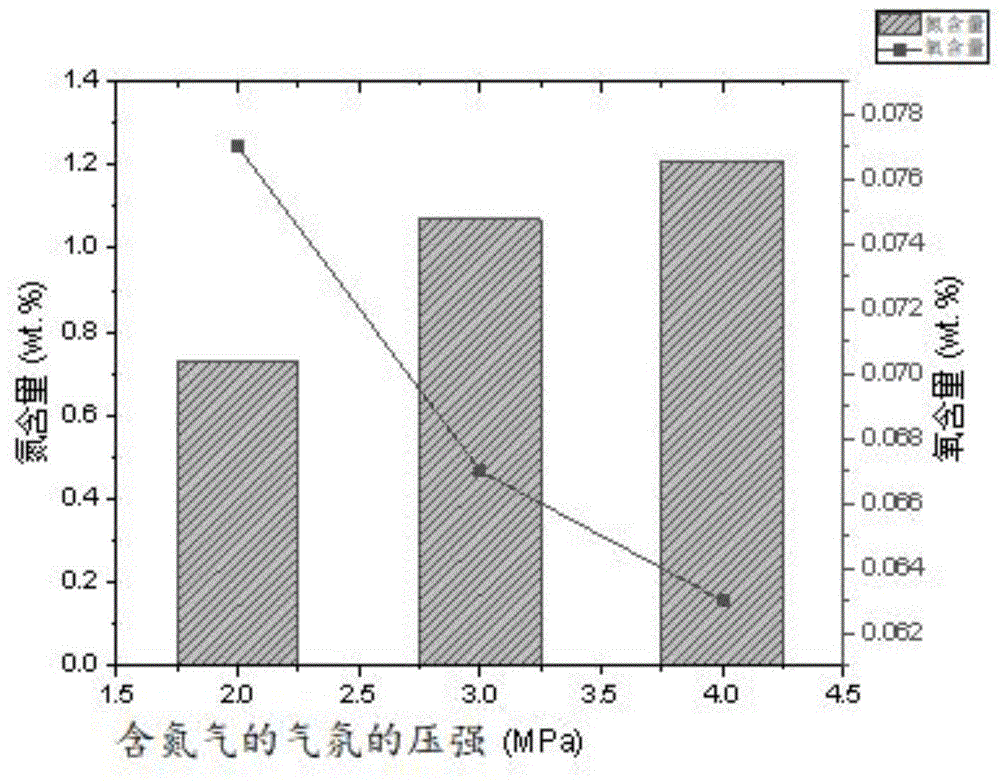
本发明涉及粉末冶金技术领域,具体涉及一种高氮钢粉末的制备方法。
背景技术:
近年来,工业应用领域不断发展,对材料的性能提出了更高的要求。高氮钢相比传统钢材具有更加出色的力学性能、耐腐蚀性能以及生物相容性。有研究显示,氮的固溶强化作用可以显著提高钢的屈服强度,可以达到传统钢材屈服强度的200~350%;在耐腐蚀方面,1%的氮就可以达到含20%的铬的耐腐蚀性;而在稳定奥氏体方面,不锈钢中1%的氮相当于18%的镍,此外氮比镍具有更好的生物相容性且价格低廉,因此高氮钢被广泛应用于海洋工程、航空航天和生物医学等领域。
目前,高氮钢的制备主要有熔炼法、粉末冶金法和金属增材制造三种方法。由于氮在固态奥氏体中的溶解度比熔体中大很多,所以利用粉末冶金法可以在较低的氮气压力和温度下制备高氮钢,此外粉末冶金制备的高氮钢成型件晶粒细小,且含有大量的细小沉淀,因此可以通过沉淀强化提高钢材的力学性能。此外,使用金属增材制造技术制造高氮钢几何零件也逐渐得到发展,这种技术可以制造一些传统制造工艺无法制造的复合结构零件,解决了复杂零件生产周期长、加工困难和成本高等问题。
而粉末冶金和金属增材制造方法制备高氮钢成型件主要使用高氮钢粉末作为原材料。目前高氮钢粉末的制备方法主要有固态粉末氮化法、等离子旋转电极雾化法以及气体雾化法。
目前广泛使用的高压熔炼气体雾化法制备高氮钢粉末主要采用的方法是选用已设计好的高氮钢合金作为原材料进行熔炼,由于熔炼时间较长,过程中没有补充氮,且熔炼时氮气压力依然偏小,导致制备的高氮钢粉末氮含量相较于高氮钢合金母材原料依然有较大损失,制备得到的高氮钢在氮含量以及细粉收得率仍不能达到使用要求。
技术实现要素:
有鉴于此,本发明提供了一种高氮钢粉末的制备方法,本发明提供的制备方法制备得到的高氮钢粉末氮含量高、细粉收得率高、氧含量低且球形度高、流动性较好。
为实现上述目的,本发明提供了如下方案:
本发明提供了一种高氮钢粉末的制备方法,包括以下步骤:
在含氮气的气氛中,将合金钢母材依次进行熔炼、吹炼和雾化,得到所述高氮钢粉末;
所述吹炼采用的气体为氮气。
优选的,所述吹炼的时间为25~40min。
优选的,所述吹炼时氮气的流量为0.3~0.7l/min。
优选的,所述含氮气的气氛为氮气和氩气的混合气体、氮气和氦气的混合气体或氮气。
优选的,当所述含氮气的气氛为氮气和氩气的混合气体或氮气和氦气的混合气体时,所述含氮气的气氛中氮气的体积分数为≥90%。
优选的,所述含氮气的气氛的压力为2.0~4.0mpa,所述熔炼的温度为1550~1700℃。
优选的,所述雾化的保温线圈的加热温度为1100~1300℃。
优选的,所述雾化的过程中,进行雾化的导流管的内径为1~4mm。
优选的,所述雾化的方式为紧耦合式雾化、自由落体式雾化或层流雾化。
优选的,所述合金钢母材,按质量百分比计,包括以下元素组分:
c0.03~0.25%,mn0.20~2.00%,si0.28~1.00%,ni0.60~10.81%,cr8.51~22.35%,mo0.04~2.95%,p≤0.045%,s≤0.03%,余量为fe。
本发明相对于现有技术取得了以下技术效果:
本发明提供的高氮钢粉末制备方法,包括以下步骤:在含氮气的气氛中,将合金钢母材依次进行熔炼、吹炼和雾化,得到所述高氮钢粉末;所述吹炼采用的气体为氮气。本发明提供的高氮钢粉末的制备方法,在熔炼和雾化之间添加了吹炼的步骤,且吹炼采用的气体为氮气,增加了合金钢熔体中的氮含量,同时在含氮气的气氛中进行熔炼、吹炼和雾化,能够抑制合金钢熔体中氮的逸出,得到的高氮钢粉末含氮量较高,氧含量低;同时,雾化过程中,在含氮气的气氛的冲击作用,将合金钢熔体破碎成小液滴,并凝固成细粉,使制得的高氮钢粉末粒径较细,粒径分布均匀,细粉收得率高(d95≤100μm),且流动性较好,生产效率大大提高。由实施例的结果表明,本发明提供的高氮钢粉末制备方法制备得到高氮钢粉末的粒径分布d95为91~98μm,粉末中的氮含量为0.73~1.21%,氧含量为0.063~0.077%,平均球形度为0.77~0.84,流动性较好,为18.7~19.2s/50g。
附图说明
图1为本发明实施例1~3所述的高氮钢粉末的氮含量和氧含量与含氮气的气氛的压强的关系图;
图2为本发明实施例1~3采用的具有氮气吹炼功能的熔炼坩埚示意图;
其中,1-熔炼坩埚,2-感应线圈,3-合金母液。
具体实施方式
本发明提供了一种高氮钢粉末的制备方法,包括以下步骤:
在含氮气的保护气氛中,将合金钢母材依次进行熔炼、吹炼和雾化,得到所述高氮钢粉末;
所述吹炼采用的气体为氮气。
在本发明中,若无特殊说明,所有原料均为本领域技术人员熟知的市售产品。
在本发明中,所述合金钢母材,按质量百分比计,优选包括以下元素组分:c0.03~0.25%,mn0.20~2.00%,si0.28~1.00%,ni0.60~10.81%,cr8.51~22.35%,mo0.04~2.95%,p≤0.045%,s≤0.03%,余量为fe。
按元素质量百分比计,所述合金钢母材更优选包括0.05~0.2%c,最优选为0.1~0.15%。
按元素质量百分比计,所述合金钢母材更优选包括0.5~1.5%mn,最优选为0.75~1.2%。
按元素质量百分比计,所述合金钢母材更优选包括0.35~0.85%si,最优选为0.45~0.75%。
按元素质量百分比计,所述合金钢母材更优选包括1.5~10%ni,最优选为2.75~8.2%。
按元素质量百分比计,所述合金钢母材更优选包括10.5~20%cr,最优选为12.5~18.5%。
按元素质量百分比计,所述合金钢母材更优选包括0.06~2.5%mo,最优选为1.0~2.0%。
按元素质量百分比计,所述合金钢母材更优选包括p≤0.035%,最优选为≤0.025%。
按元素质量百分比计,所述合金钢母材更优选包括s≤0.02%,最优选为≤0.01%。
按元素质量百分比计,所述合金钢母材,除上述元素组分外,包括余量的fe。
本发明中所述合金钢母材优选为按照普通不锈钢所需成分进行配料得到的熔铸原料,后经过熔炼得到的不锈钢铸锭。
在本发明中,所述熔炼的温度优选为1550~1700℃,更优选为1600~1650℃,在本发明中,所述熔炼在含氮气的气氛下进行,所述含氮气的气氛优选为氮气和氩气的混合气体、氮气和氦气的混合气体或氮气。在本发明中,当所述含氮气的气氛优选为氮气和氩气的混合气体或氮气和氦气的混合气体时,所述含氮气的气氛中氮气的体积分数优选为≥90%,更优选为≥95%。在本发明中,所述含氮气的气氛的压力优选为2.0~4.0mpa,更优选为2.5~4mpa。
本发明对所述熔炼时间没有特殊要求,实现合金母材熔化即可。
在本发明中,所述熔炼优选在熔炼坩埚中进行,所述熔炼坩埚在通入含氮气的气体之前,本发明优选将所述熔炼坩埚抽至真空,真空度优选为0.1~100pa,更优选为0.5~85pa,最优选为1.5~30pa。
在本发明中,合金钢母液熔化后,进行吹炼,所述吹炼采用的气体为氮气。在本发明中,所述吹炼的时间优选为25~40min,更优选为28~35min,所述吹炼时氮气的流量优选为0.3~0.7l/min,更优选为0.45~0.7l/min。在本发明中,所述吹炼时的气氛和熔炼时的气氛保持一致,所述吹炼在含氮气的气氛下进行,所述含氮气的气氛优选为氮气和氩气的混合气体、氮气和氦气的混合气体或氮气。在本发明中,当所述含氮气的气氛优选为氮气和氩气的混合气体或氮气和氦气的混合气体时,所述含氮气的气氛中氮气的体积分数优选为≥90%,更优选为≥95%。
在本发明中,吹炼时所述氮气优选从所述熔炼坩埚底部进入(如图2所示)。
所述吹炼完成后,本发明优选将得到的合金熔体转移至中间漏包中,以便于后续的雾化。进行转移之前,本发明优选将所述中间漏包进行预热,所述中间漏包的预热温度优选为1100~1300℃,更优选为1150~1250℃。本发明优选将预热中间漏包和熔炼同时进行。
在本发明中,所述雾化的保温线圈的加热温度优选为1100~1300℃,更优选为1150~1250℃。在本发明中,所述雾化在含氮气的气氛下进行,所述含氮气的气氛优选为氮气和氩气的混合气体、氮气和氦气的混合气体或氮气。在本发明中,当所述含氮气的气氛优选为氮气和氩气的混合气体或氮气和氦气的混合气体时,所述含氮气的气氛中氮气的体积分数优选为≥90%,更优选为≥95%。在本发明中,所述含氮气的气氛的压力优选为2.0~4.0mpa,更优选为2.5~4mpa,在本发明中,所述雾化过程中,含氮气的气氛的气体流速优选为500~650m/s,本发明进行一次雾化可熔炼合金钢母材10~30kg。
在本发明中,所述雾化优选在雾化室中进行,在雾化之前,本发明优选将所述雾化室抽至真空,所述真空度优选为为0.1~100pa,更优选为0.5~85pa,最优选为1.5~30pa。在本发明中,将所述雾化室抽至真空条件后,再通入含氮气的气氛。
在本发明中,所述雾化室和中间漏包之间通过导流管连接,所述导流管内直径优选为1~4mm,更优选为2~3.5mm。在本发明中,所述雾化的方式优选为紧耦合式雾化、自由落体式雾化或层流雾化,更优选为紧耦合式雾化或层流雾化。本发明对所述紧耦合式雾化、自由落体式雾化或层流雾化的具体实施过程没有特殊要求,采用本领域技术人员熟知的操作即可。
在本发明中,所述雾化过程中,通过含氮气的气氛将合金熔体破碎成小液滴,并凝固成粉末。
所述雾化后,本发明优选对得到的雾化粉料进行后处理,得到高氮钢粉末。在本发明中,所述后处理优选包括依次进行的分级和筛分。
在本发明中,所述分级的方式优选为气流分级,本发明对所述气流分级的具体实施过程没有特殊要求,采用本领域技术人员熟知的操作即可。
在本发明中,所述筛分的方式优选为超声振动筛分,所述超声振动筛分的筛孔的目数优选为140目。本发明对所述超声振动筛分的具体实施过程没有特殊要求,采用本领域技术人员熟知的操作即可。
在本发明中,对所述雾化粉料进行后处理的目的是为了去除粗大粉末,以便应用于激光增材制造和粉末冶金。
为了更好地理解本发明,下面结合实施例进一步阐明本发明的内容,但本发明的内容不仅仅局限于下面的实施例。
实施例1
将合金钢母材放入熔炼室的感应熔炼坩埚中,如图2所示,其中合金钢母材包括以下组分,按质量百分比计,c0.03%,mn1.80%,si0.40%,ni9.43%,cr16.25%,mo2.31%,p≤0.03%,s≤0.03%,余量为fe,关闭熔炼室顶盖,抽真空至真空度为10pa,充入高压氮气,使熔炼室中的氮气压强达到2mpa,利用感应线圈将坩埚中的钢母材加热熔化,加热至1600℃,在此温度下氮气吹炼35min,加热中间漏包至温度为1220℃,将吹炼熔液倾倒入中间包中,开始雾化过程,采用紧耦合式雾化喷嘴,中间包到雾化喷嘴之间的导流管内径为2mm,雾化氮气压强为2.5mpa,在高压氮气的冲击作用下,金属液细柱被冲碎形成微小的金属液滴,并在雾化室下落的过程中快速冷却凝固成高氮钢粉末,并落入粉末收集罐中,得到高氮钢粉末。
使用激光粒度分布仪测得高氮钢粉末的平均粒径d95为95μm,平均球形度为0.81,流动性为18.8s/50g,对粉末进行超声振动筛分(140目)和气流分级,得到粒径在10~106μm范围的粉末,使用lecoonh836氧氮氢分析仪测得高氮钢粉末中的氮元素的质量含量为0.73%,氧元素的含量为0.077%。
实施例2
将合金钢母材放入熔炼室的感应熔炼坩埚(如图2所示)中,其中合金钢母材包括以下组分,按质量百分比计,c0.08%,mn1.69%,si0.29%,ni7.75%,cr18.46%,mo1.06%,p≤0.03%,s≤0.03%。余量为fe,关闭熔炼室顶盖,抽真空至真空度为10pa,充入高压氮气,使熔炼室中的氮气压强达到3mpa,利用感应线圈将坩埚中的钢母材加热熔化,加热至1650℃,在此温度下氮气吹炼35min,加热中间漏包至温度为1250℃,将吹炼熔液倾倒入中间包中,开始雾化过程,采用自由落体式喷嘴,中间包到雾化喷嘴之间的导流管内径为2mm,雾化氮气压强为3.0mpa,在高压氮气的冲击作用下,金属液细柱被冲碎形成微小的金属液滴,并在雾化室下落的过程中快速冷却凝固成高氮钢粉末,并落入粉末收集罐中,得到高氮钢粉末。
使用激光粒度分布仪测得粉末平均粒径d95为98μm,平均球形度为0.77,流动性为19.2s/50g,对粉末进行超声振动筛分(140目)和气流分级,得到粒径在10~106μm范围的粉末,使用lecoonh836氧氮氢分析仪测得高氮钢粉末中的氮元素的质量含量为1.07%,氧含量为0.067%。
实施例3
将合金钢母材放入熔炼室的感应熔炼坩埚(如图2所示)中,其中合金钢母材包括以下组分,按质量百分比计,c0.06%,mn1.33%,si0.30%,ni8.35%,cr20.03%,mo0.05%,p≤0.03%,s≤0.03%;余量为fe,关闭熔炼室顶盖,抽真空至真空度为10pa,充入高压氮气,使熔炼室中的氮气压强达到4mpa,利用感应线圈将坩埚中的钢母材加热熔化,加热至1650℃,在此温度下氮气吹炼35min,加热中间漏包至温度为1280℃,将吹炼熔液倾倒入中间包中,开始雾化过程,采用层流雾化喷嘴,中间包到雾化喷嘴之间的导流管内径为2mm,雾化氮气压强为3.5mpa,在高压氮气的冲击作用下,金属液细柱被冲碎形成微小的金属液滴,并在雾化室下落的过程中快速冷却凝固成高氮钢粉末,并落入粉末收集罐中,得到高氮钢粉末。
使用激光粒度分布仪测得粉末平均粒径d95为91μm,平均球形度为0.84,流动性为18.7s/50g,对粉末进行超声振动筛分(140目)和气流分级,得到粒径在10-106μm范围的粉末,使用lecoonh836氧氮氢分析仪测得粉末中的氮元素的质量含量为1.21%,氧含量为0.063%。
图1为本发明实施例1~3所述的高氮钢粉末的氮含量和氧含量与含氮气的气氛的压强的关系图。
本发明中应用了具体个例对本发明的原理及实施方式进行了阐述,以上实施例的说明只是用于帮助理解本发明的方法及其核心思想;同时,对于本领域的一般技术人员,依据本发明的思想,在具体实施方式及应用范围上均会有改变之处。综上所述,本说明书内容不应理解为对本发明的限制。
起点商标作为专业知识产权交易平台,可以帮助大家解决很多问题,如果大家想要了解更多知产交易信息请点击 【在线咨询】或添加微信 【19522093243】与客服一对一沟通,为大家解决相关问题。
此文章来源于网络,如有侵权,请联系删除


