含杂质工业级偏钛酸粉体制备克级以上高纯相Ti4O7纳米材料的方法与流程



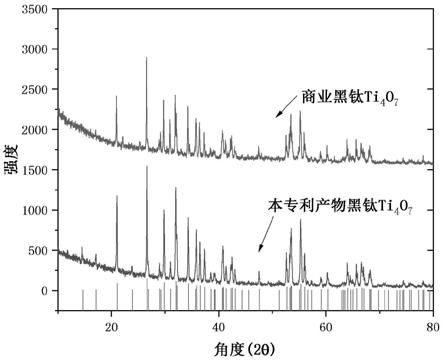
含杂质工业级偏钛酸粉体制备克级以上高纯相ti4o7纳米材料的方法
技术领域
[0001]
本发明涉及材料科学技术领域,尤其涉及含杂质工业级偏钛酸粉体制备克级以上高纯相ti4o7纳米材料的方法。
背景技术:
[0002]
magneli相氧化钛,又称亚氧化钛,具有通式(ti
n
o
2n-1
,4≤n≤10)。亚氧化钛对反应合成条件(气体速度、温度区间、还原组成等)非常敏感,且 magneli各相之间的反应条件非常接近,难以合成高纯相亚氧化钛。
[0003]
ti4o7又被称为黑钛,在现有的工艺生产技术中,合成ti4o7大部分使用的前驱物是tio2,还原剂使用还原性气体(如h2,nh3等)的前提下,对设备的要求较高;使用还原剂粉末,但反应完成后,还原剂和产物无法有效分离,且工艺流程的步骤和复杂性提高,成本高昂、晶体结构调控难等缺点,难以实现大规模生产。
技术实现要素:
[0004]
本发明的目的在于克服现有技术中的缺陷,提供一种ti4o7的制备方法。
[0005]
为了实现上述发明目的,本发明提供以下技术方案:
[0006]
本发明提供了一种ti4o7的制备方法,包含下列步骤:
[0007]
在惰性氛围下,将偏钛酸粉末和还原剂混合后进行变温处理,即得所述 ti4o7;
[0008]
所述还原剂和偏钛酸粉末的摩尔比为3:4~8。
[0009]
作为优选,所述偏钛酸粉末为将偏钛酸顺次进行抽滤、干燥、细化后得到的粉末。
[0010]
作为优选,所述抽滤的压力为0.5~1.5kg,所述抽滤的时间为0.5~2h。
[0011]
作为优选,所述干燥为顺次进行的鼓风干燥和真空干燥;
[0012]
所述鼓风干燥的温度为65~75℃,所述鼓风干燥的时间为5~8h;
[0013]
所述真空干燥的温度为50~65℃,所述真空干燥的时间为22~26h,所述真空干燥的真空度为-0.1~-0.2mpa。
[0014]
作为优选,所述细化为研磨,所述研磨的溶剂为乙醇,所述研磨的时间为0.5~1h,所述研磨的转速为180~220r/min;
[0015]
所述偏钛酸粉末的粒径为50~100nm。
[0016]
作为优选,所述还原剂为碳粉、铁粉或硫粉;
[0017]
所述混合在研磨状态下进行,所述研磨的溶剂为乙醇,所述研磨为顺次进行的第一步研磨和第二步研磨;
[0018]
所述第一步研磨的转速为160~200r/min,所述第一步研磨的时间为 10~30min;
[0019]
所述第二步研磨的转速为300~320r/min,所述第二步研磨的时间为 30~55min。
[0020]
作为优选,所述惰性氛围为氮气、氦气或氩气,所述惰性氛围的流量为 30~70sccm。
[0021]
作为优选,所述变温处理为顺次进行的第一步变温处理和第二步变温处理。
[0022]
作为优选,所述第一步变温处理的目标温度为750~830℃,所述第一步变温处理的升温速率为5~10℃/min,所述第一步变温处理到达目标温度后的保温时间为3.5~8h。
[0023]
作为优选,所述第二步变温处理的目标温度为938~1138℃,由所述第一步变温处理的目标温度升温至第二步变温处理的目标温度的升温速率为 1~5℃/min,所述第二步变温处理到达目标温度后的保温时间为2.5~11.5h。
[0024]
本发明提供了一种ti4o7的制备方法。在惰性氛围中将偏钛酸粉末和还原剂进行变温处理;工艺简单,工艺要求低,还原剂在反应过程中自动消除,无需后续的分离步骤,简化了工艺流程,提高了ti4o7的纯度,实现了克级以上ti4o7的制备。
附图说明
[0025]
图1为实施例1制备ti4o7的xrd图谱;
[0026]
图2为实施例1制备的ti4o7导电率测试实验图;
[0027]
图3为实施例1制备的ti4o7波长吸收图;
[0028]
图4为实施例1制备的ti4o7电镜图;
[0029]
图5为实施例1制备的ti4o7能谱图。
具体实施方式
[0030]
本发明提供了一种ti4o7的制备方法,包含下列步骤:
[0031]
在惰性氛围下,将偏钛酸粉末和还原剂混合后进行变温处理,即得所述 ti4o7;
[0032]
所述还原剂和偏钛酸粉末的摩尔比为3:4~8,优选为3:5~7,更优选为3:5.5~6.5。
[0033]
在本发明中,所述偏钛酸粉末优选为将偏钛酸顺次进行抽滤、干燥、细化后得到的粉末;所述偏钛酸优选为工业级偏钛酸。
[0034]
在本发明中,所述抽滤的压力优选为0.5~1.5kg,进一步优选为 0.8~1.2kg,更优选为0.9~1.1kg;所述抽滤的时间优选为0.5~2h,进一步优选为0.8~1.7h,更优选为1.2~1.3h。
[0035]
在本发明中,所述干燥优选为顺次进行的鼓风干燥和真空干燥。
[0036]
在本发明中,所述鼓风干燥的温度优选为65~75℃,进一步优选为 67~73℃,更优选为69~71℃;所述鼓风干燥的时间优选为5~8h,进一步优选为5.5~7.5h,更优选为6~7h。
[0037]
在本发明中,所述真空干燥的温度优选为50~65℃,进一步优选为 53~62℃,更优选为55~60℃;所述真空干燥的时间优选为22~26h,进一步优选为23~25h,更优选为23.5~24.5h;所述真空干燥的真空度优选为
ꢀ-
0.1~-0.2mpa,进一步优选为-0.12~-0.18mpa,更优选为-0.14~-0.16mpa。
[0038]
在本发明中,所述细化优选为研磨,所述研磨的溶剂优选为乙醇,所述研磨的时间优选为0.5~1h,进一步优选为0.6~0.9h,更优选为0.7~0.8h;所述研磨的转速优选为180~220r/min,进一步优选为190~210r/min,更优选为 195~205r/min。
[0039]
在本发明中,所述溶剂的用量无特别限定,能在研磨过程中防止粉末飘散即可;溶
剂完全挥发出去,完成研磨。
[0040]
在本发明中,所述偏钛酸粉末的粒径优选为50~100nm,进一步优选为 60~90nm,更优选为70~80nm。
[0041]
在本发明中,所述还原剂优选为碳粉、铁粉或硫粉。
[0042]
在本发明中,所述混合优选在研磨状态下进行,所述研磨的溶剂优选为乙醇,所述研磨优选为顺次进行的第一步研磨和第二步研磨。
[0043]
在本发明中,所述第一步研磨的转速优选为160~200r/min,进一步优选为170~190r/min,更优选为175~185r/min;所述第一步研磨的时间优选为 10~30min,进一步优选为14~26min,更优选为18~22min。
[0044]
在本发明中,所述第二步研磨的转速优选为300~320r/min,进一步优选为304~316r/min,更优选为308~312r/min;所述第二步研磨的时间优选为 30~55min,进一步优选为35~50min,更优选为40~45min。
[0045]
在本发明中,所述溶剂的用量无特别限定,能在研磨过程中防止粉末飘散即可;溶剂完全挥发出去,完成研磨。
[0046]
在本发明中,所述惰性氛围优选为氮气、氦气或氩气,更优选为氮气或氩气;所述惰性氛围的流量优选为30~70sccm,进一步优选为40~60sccm,更优选为45~55sccm。
[0047]
在本发明中,所述变温处理优选为顺次进行的第一步变温处理和第二步变温处理。
[0048]
在本发明中,所述第一步变温处理的目标温度优选为750~830℃,进一步优选为770~810℃,更优选为780~800℃;所述第一步变温处理的升温速率优选为5~10℃/min,进一步优选为6~9℃/min,更优选为7~8℃/min;所述第一步变温处理到达目标温度后的保温时间优选为3.5~8h,进一步优选为 4~7.5h,更优选为5~6.5h。
[0049]
在本发明中,进行第一步变温处理可以保证样品在第二步变温处理的受热均匀性;同时使还原剂在第一步变温处理的目标温度中与氧气反应,排除反应氛围中剩余的氧气,保证反应氛围中的氧气含量极低,为第二步变温处理创造了反应环境。
[0050]
在本发明中,所述第二步变温处理的目标温度优选为938~1138℃,进一步优选为968~1108℃,更优选为1020~1050℃;由所述第一步变温处理的目标温度升温至第二步变温处理的目标温度的升温速率优选为1~5℃/min,进一步优选为2~4℃/min,更优选为2.5~3.5℃/min;所述第二步变温处理到达目标温度后的保温时间优选为2.5~11.5h,进一步优选为5~9h,更优选为6~8h。
[0051]
在本发明中,在进行变温处理时,只需通入惰性气体对反应进行保护,无需进行抽真空等操作;最高反应温度为1138℃,降低了反应温度和工艺难度,节省了能源,提高了产物的纯度。
[0052]
在本发明中,第二步变温处理保温结束后优选自然冷却至室温;当温度优选降低至400℃以下时可停止惰性气体保护,进一步优选为380℃,更优选为350℃。
[0053]
在本发明中,当还原剂优选为碳粉时,化学反应式如下:
[0054][0055]
在本发明中,当还原剂优选为铁粉时,化学反应式如下:
[0056][0057]
在本发明中,当还原剂优选为硫粉时,化学反应式如下:
[0058][0059]
在本发明中,作为原料的偏钛酸含有少量的铁单质,在反应过程中会与偏钛酸受热分解的水蒸气反应,生成四氧化三铁,随着气流排出,反应式如下:
[0060][0061]
在本发明中,还原剂会在反应过程中生成相应的氧化物,随着气流以蒸汽的形式溢出自动消除,无需后续的分离步骤,简化工艺流程,提高了还原产物的纯度。
[0062]
下面结合实施例对本发明提供的技术方案进行详细的说明,但是不能把它们理解为对本发明保护范围的限定。
[0063]
实施例1
[0064]
称取5mol的工业级偏钛酸,在1kg压力下抽滤1h;然后在70℃下鼓风干燥6h,将经过鼓风干燥的偏钛酸置于-0.1mpa、60℃下真空干燥24h;将经过干燥后的偏钛酸进行细化,添加适量乙醇,以180r/min转速研磨1h至乙醇完全挥发,得到粒度为80nm的偏钛酸粉末。
[0065]
将偏钛酸粉末和3.75mol的碳粉在研磨状态下混合,添加适量的乙醇,以180r/min的转速研磨10min完成第一步研磨,然后调整参数以300r/min 的转速研磨35min完成第二步研磨,直至乙醇完全挥发。
[0066]
将混合后的粉末放入反应舟,将反应舟放入管式炉,然后将cvd管式炉密封,以40sccm的流量通入氮气开始升温。以8℃/min的升温速率将温度从20℃升温至750℃,达到750℃后保温5.5h完成第一步变温处理;第一步变温处理的保温结束后,以3℃/min的升温速率从750℃升温至1020℃,到达1020℃后保温8h,完成第二步变温处理。
[0067]
第二步变温处理结束后,自然冷却至室温,反应产物中的水蒸气、一氧化碳和四氧化三铁随气流排出,剩余产物为ti4o7。
[0068]
本实施例制备得到了3.75mol的ti4o7,本实施例制备得到的ti4o7纯度为99.9%。
[0069]
将本实施例制备的ti4o7和纯度为99%的商业ti4o7进行x射线衍射实验,xrd图谱如图1所示,从图1可以看出,本实施例制备得到的ti4o7比商业ti4o7纯度高,商业ti4o7中在2θ角为22
°
和25
°
处为其它亚氧化钛的杂峰。
[0070]
将本实施例制备的ti4o7、商业ti4o7、ti5o9和ti6o
11
进行导电率测试实验,测试结果如图2所示;从图2中可以看出,本实施例制备的ti4o7的导电率大于商业ti4o7的导电率,证明本实施例制备的ti4o7纯度比商业ti4o7纯度更高。
[0071]
将本实施例制备的ti4o7、商业ti4o7、石墨碳粉和tio2进行波长吸收实验,结果如图3所示;从图3中可以看出,本实施例制备ti4o7的在整个可见光、紫外波段和红外波段都具有很好的吸收性,且吸收性能优于商业 ti4o7。
[0072]
将本实施例制备的ti4o7在扫描电子显微镜下观察,如图4所示。
[0073]
将本实施例制备的ti4o7进行能谱分析实验,结果如图5所示,从图中可以看出ti元素均匀分布而氧元素是不均匀分布。
[0074]
实施例2
[0075]
称取3mol的工业级偏钛酸,在1.2kg压力下抽滤0.8h;然后在65℃下鼓风干燥7h,
将经过鼓风干燥的偏钛酸置于-0.15mpa、65℃下真空干燥25h;将经过干燥后的偏钛酸进行细化,添加适量乙醇,以190r/min转速研磨0.5h 至乙醇完全挥发,得到粒度为70nm的偏钛酸粉末。
[0076]
将偏钛酸粉末和2.25mol的铁粉在研磨状态下混合,添加适量的乙醇,以160r/min的转速研磨25min完成第一步研磨,然后调整参数以310r/min 的转速研磨40min完成第二步研磨,直至乙醇完全挥发。
[0077]
将混合后的粉末放入反应舟,将反应舟放入管式炉,然后将cvd管式炉密封,以60sccm的流量通入氮气开始升温。以8℃/min的升温速率将温度从20℃升温至780℃,达到780℃后保温4.5h完成第一步变温处理;第一步变温处理的保温结束后,以2℃/min的升温速率从780℃升温至1030℃,到达1030℃后保温7h,完成第二步变温处理。
[0078]
第二步变温处理结束后,自然冷却至室温,反应产物中的水蒸气、氧化铁和四氧化三铁随气流排出,剩余产物为ti4o7。
[0079]
本实施例制备得到了2.25mol的ti4o7;本实施例制备得到的ti4o7纯度为99.7%。
[0080]
实施例3
[0081]
称取7mol的工业级偏钛酸,在1.5kg压力下抽滤1.3h;然后在75℃下鼓风干燥5.5h,将经过鼓风干燥的偏钛酸置于-0.13mpa、65℃下真空干燥 25h;将经过干燥后的偏钛酸进行细化,添加适量乙醇,以210r/min转速研磨1h至乙醇完全挥发,得到粒度为60nm的偏钛酸粉末。
[0082]
将偏钛酸粉末和2.62mol的硫粉在研磨状态下混合,添加适量的乙醇,以190r/min的转速研磨15min完成第一步研磨,然后调整参数以310r/min 的转速研磨40min完成第二步研磨,直至乙醇完全挥发。
[0083]
将混合后的粉末放入反应舟,将反应舟放入管式炉,然后将cvd管式炉密封,以60sccm的流量通入氮气开始升温。以8℃/min的升温速率将温度从20℃升温至820℃,达到820℃后保温5h完成第一步变温处理;第一步变温处理的保温结束后,以4℃/min的升温速率从820℃升温至1100℃,到达1100℃后保温9h,完成第二步变温处理。
[0084]
第二步变温处理结束后,自然冷却至室温,反应产物中的水蒸气、二氧化硫和四氧化三铁随气流排出,剩余产物为ti4o7。
[0085]
本实施例制备得到了5.25mol的ti4o7;本实施例制备得到的ti4o7纯度为99.7%。
[0086]
实施例4
[0087]
称取8mol的工业级偏钛酸,在1.2kg压力下抽滤1.2h;然后在68℃下鼓风干燥5.5h,将经过鼓风干燥的偏钛酸置于-0.14mpa、58℃下真空干燥 23h;将经过干燥后的偏钛酸进行细化,添加适量乙醇,以200r/min转速研磨0.6h至乙醇完全挥发,得到粒度为82nm的偏钛酸粉末。
[0088]
将偏钛酸粉末和6mol的碳粉在研磨状态下混合,添加适量的乙醇,以 170r/min的转速研磨20min完成第一步研磨,然后调整参数以310r/min的转速研磨40min完成第二步研磨,直至乙醇完全挥发。
[0089]
将混合后的粉末放入反应舟,将反应舟放入管式炉,然后将cvd管式炉密封,以45sccm的流量通入氮气开始升温。以9℃/min的升温速率将温度从20℃升温至810℃,达到810℃后保温6h完成第一步变温处理;第一步变温处理的保温结束后,以3℃/min的升温速
率从810℃升温至980℃,到达980℃后保温7.5h,完成第二步变温处理。
[0090]
第二步变温处理结束后,自然冷却至室温,反应产物中的水蒸气、一氧化碳和四氧化三铁随气流排出,剩余产物为ti4o7。
[0091]
本实施例制备得到了3mol的ti4o7,本实施例制备得到的ti4o7纯度为 99.8%。
[0092]
实施例5
[0093]
称取1mol的工业级偏钛酸,在1.5kg压力下抽滤1.8h;然后在70℃下鼓风干燥8h,将经过鼓风干燥的偏钛酸置于-0.18mpa、60℃下真空干燥24h;将经过干燥后的偏钛酸进行细化,添加适量乙醇,以190r/min转速研磨1h 至乙醇完全挥发,得到粒度为60nm的偏钛酸粉末。
[0094]
将偏钛酸粉末和0.75mol的碳粉在研磨状态下混合,添加适量的乙醇,以190r/min的转速研磨25min完成第一步研磨,然后调整参数以310r/min 的转速研磨50min完成第二步研磨,直至乙醇完全挥发。
[0095]
将混合后的粉末放入反应舟,将反应舟放入管式炉,然后将cvd管式炉密封,以60sccm的流量通入氮气开始升温。以7℃/min的升温速率将温度从20℃升温至790℃,达到790℃后保温6h完成第一步变温处理;第一步变温处理的保温结束后,以3℃/min的升温速率从790℃升温至1050℃,到达1050℃后保温8h,完成第二步变温处理。
[0096]
第二步变温处理结束后,自然冷却至室温,反应产物中的水蒸气、一氧化碳和四氧化三铁随气流排出,剩余产物为ti4o7。
[0097]
本实施例制备得到了0.75mol的ti4o7,本实施例制备得到的ti4o7纯度为99.9%。
[0098]
由以上实施例可知,本发明提供了工业级含铁杂质偏钛酸粉体制备克级以上高纯相ti4o7纳米材料的方法,在惰性氛围中将偏钛酸粉末和还原剂进行变温处理;工艺简单,工艺要求低,还原剂在反应过程中自动消除,无需后续的分离步骤,简化了工艺流程,提高了ti4o7的纯度,实现了克级以上 ti4o7的制备。
[0099]
以上所述仅是本发明的优选实施方式,应当指出,对于本技术领域的普通技术人员来说,在不脱离本发明原理的前提下,还可以做出若干改进和润饰,这些改进和润饰也应视为本发明的保护范围。
起点商标作为专业知识产权交易平台,可以帮助大家解决很多问题,如果大家想要了解更多知产交易信息请点击 【在线咨询】或添加微信 【19522093243】与客服一对一沟通,为大家解决相关问题。
此文章来源于网络,如有侵权,请联系删除
相关标签:



tips