高磷鲕状铁矿悬浮焙烧提铁-酸浸除磷的方法与流程



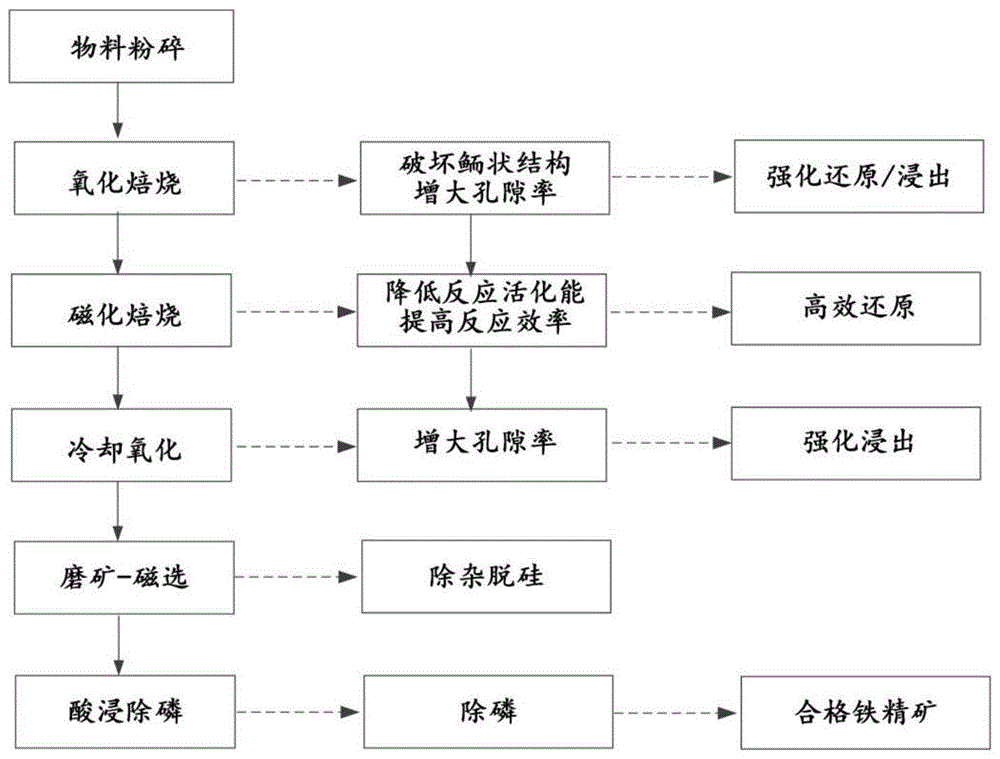
本发明属于矿物加工技术领域,尤其涉及一种高磷鲕状铁矿悬浮焙烧提铁-酸浸除磷的方法。
背景技术:
众多难选铁矿中,高磷鲕状铁矿尤其是弱磁性的高磷鲕状赤铁矿是最难选的铁矿石之一。鲕状铁矿矿石多呈现鲕状、豆状和肾状;以铁矿(或石英等)为核心,由铁矿、石英、绿泥石相互逐层包裹而成鲕状颗粒,形成胶体化学沉积作用形成的鲕状构造;由于其自身特点,鲕状铁矿一直无法得到有效的开发利用。高磷鲕状铁矿中的胶磷矿和绿泥石是主要含磷矿物,嵌布粒度细,主要以鲕状或鲕粒的同心结构存在,磷含量一般为0.4%~1.1%,甚至更高,远不能满足炼铁对原料的需求。因此高磷鲕状铁矿的选矿难度极大,成本高,导致了高磷鲕状铁矿尚未得到有效的开发利用。
高磷鲕状铁矿的结构决定了只有细磨至几十或几个微米以下,才能破坏鲕粒结构完成铁矿物的解离,才能得到有效利用,但破碎后的鲕状铁矿粒度细,回收困难。通过物理选矿法,(反)浮选法与选择性絮凝-(反)浮选法,浸出法(生物浸出、化学浸出)等选矿工艺均难以获得合格铁精矿。近年来,科研工作者利用火法焙烧工艺处理高磷鲕状铁矿获得了诸多进展。通过焙烧,将弱磁性赤铁矿转化为强磁性磁铁矿,扩大铁矿物与脉石的磁性差异,可有效的回收细粒的铁矿物,但该方法存在产品质量不均,能耗高等问题。
技术实现要素:
本发明的目的在于提供一种高磷鲕状铁矿悬浮焙烧提铁-酸浸除磷的方法,本发明中的方法在节能降耗、绿色生产的同时,提高了提铁降磷的效果。
本发明提供一种高磷鲕状铁矿悬浮焙烧提铁-酸浸除磷的方法,包括以下步骤:
a)将高磷鲕状铁矿石粉碎后在流化态下进行氧化焙烧,得到氧化焙烧产品;
b)将所述氧化焙烧的产品在还原性气氛和流化态下进行磁化焙烧,得到磁化焙烧产品;
c)将所述磁化焙烧产品在惰性气氛下快速冷却至180~250℃,然后接触空气氧化冷却,得到冷却后的焙烧产品;
所述冷却的降温速率为50~100℃/min;
d)将冷却后的焙烧产品依次进行磨矿-磁选和酸浸除磷,得到铁精矿。
优选的,所述高磷鲕状铁矿石为高磷鲕状赤铁矿、高磷鲕状磁铁矿和高磷鲕状赤/磁铁矿中的一种或几种。
优选的,粉碎后的高磷鲕状铁矿的粒径为-2mm,其中,-0.074mm的物料的质量分数为40~60%。
优选的,所述步骤a)中氧化焙烧的温度为1000~1050℃;所述步骤a)中氧化焙烧的时间为30~90min。
优选的,所述还原性气氛包括惰性气体和还原性气体,所述还原性气体在所述还原性气氛中的体积分数为20~40%;
所述惰性气体为氮气、氩气和氦气中的一种或几种;所述还原性气体为co、h2和煤制气中的一种或几种。
优选的,所述步骤b)中磁化焙烧的温度为520~550℃,所述步骤b)中磁化焙烧的时间为30~60min。
优选的,所述步骤c)中氧化冷却至20~90℃。
优选的,所述步骤d)中的磨矿-磁选具体步骤如下:
将冷却后的焙烧产品磨矿至-0.038mm的物料的质量分数为40~70%,然后进行弱磁选,得到弱磁选铁精矿;
所述弱磁场的磁场强度为1000~2000oe。
优选的,所述步骤d)中酸浸除磷的具体步骤如下:
将弱磁选铁精矿在酸液中浸泡30~50min,过滤后洗涤、烘干,得到铁精矿;
所述酸液的浓度0.2~0.6mol/l。
优选的,所述步骤a)中高磷鲕状铁矿石中铁品位为40~60%,磷的质量分数为0.5~1.2%。
本发明提供一种高磷鲕状铁矿悬浮焙烧提铁-酸浸除磷的方法,包括以下步骤:a)将高磷鲕状铁矿石粉碎后在流化态下进行氧化焙烧,得到氧化焙烧产品;b)将所述氧化焙烧的产品在还原性气氛和流化态下进行磁化焙烧,得到磁化焙烧产品;c)将所述磁化焙烧产品在惰性气氛下快速冷却至180~250℃,然后接触空气氧化冷却,得到冷却后的焙烧产品;所述冷却的降温速率为50~100℃/min;d)将冷却后的焙烧产品依次进行磨矿-磁选和酸浸除磷,得到铁精矿。本发明采用高温氧化焙烧对流化态的物料进行处理,颗粒内生成大量的裂隙,一定程度上破坏了鲕状结构,增大孔隙率和比表面积,使其有利于还原和浸出,同时流化态具有极高的传质传热效率。同时,本发明对还原物料进行快速降温,致使矿物颗粒表面出现裂隙,进一步提高了孔隙率,有助于后续浸出,冷却后进行氧化,使还原后的人工磁铁矿fe3o4氧化生成了矫顽力较低的强磁性矿物—γ-fe2o3,可降低铁矿物的磁团聚现象,提高磁选产品的质量。实验结果表明,本发明中的方法制备得到的铁精矿的铁品位≥63.00%,铁回收率≥92.00%,p品位≤0.20%。
附图说明
为了更清楚地说明本发明实施例或现有技术中的技术方案,下面将对实施例或现有技术描述中所需要使用的附图作简单地介绍,显而易见地,下面描述中的附图仅仅是本发明的实施例,对于本领域普通技术人员来讲,在不付出创造性劳动的前提下,还可以根据提供的附图获得其他的附图。
图1为本发明中高磷鲕状铁矿悬浮焙烧提铁-酸浸除磷的方法流程及原理图。
具体实施方式
本发明提供了一种高磷鲕状铁矿悬浮焙烧提铁-酸浸除磷的方法,包括以下步骤:
a)将高磷鲕状铁矿石粉碎后在流化态下进行氧化焙烧,得到氧化焙烧产品;
b)将所述氧化焙烧的产品在还原性气氛和流化态下进行磁化焙烧,得到磁化焙烧产品;
c)将所述磁化焙烧产品在惰性气氛下快速冷却至180~250℃,然后接触空气氧化冷却,得到冷却后的焙烧产品;
所述冷却的降温速率为50~100℃/min;
d)将冷却后的焙烧产品依次进行磨矿-磁选和酸浸除磷,得到铁精矿。
本发明中的方法流程及各步骤原理详见图1,图1为本发明中高磷鲕状铁矿悬浮焙烧提铁-酸浸除磷的方法流程及原理图。
本发明首先将高磷鲕状铁矿石进行粉碎,作为焙烧给矿。
在本发明中,所述高磷鲕状铁矿石优选为高磷鲕状赤铁矿、高磷鲕状磁铁矿和高磷鲕状赤/磁铁矿等,其中,所述高磷鲕状赤/磁铁矿指的是矿石中既含有高磷鲕状赤铁矿同时也含有高磷鲕状磁铁矿;
在本发明中,所述高磷鲕状铁矿石中铁品位优选为40~60%,更优选为45~55%,具体的,在本发明的实施例中,可以是55.61%、53.72%或41.46%;所述高磷鲕状铁矿石中磷的质量分数优选为0.5~1.2%,更优选为0.8~1.2%,具体的,在本发明的实施例中,可以是0.81%、0.98%或1.18%。
在本发明中,所述粉碎为本领域技术人员常用的铁矿石粉碎技术,本发明在此不再对其进行进一步的限定,只需粉碎后的铁矿石的粒径能够满足本发明的氧化焙烧的需求即可。在本发明中,所述粉碎后的高磷鲕状铁矿石的粒径为-2mm,即粒径均在2mm以下,其中,粒径小于0.074mm即-0.074mm的物料的质量分数优选为40~60%,更优选为45~55%,最优选为50%,具体的,在本发明的实施例中,可以是45%、55%或60%。本发明将高磷鲕状铁矿石粉碎至上述粒径范围内,能够改善后续焙烧过程中的流化状态,更好的实现后续的流化态焙烧。
粉碎后得到的焙烧给矿送入氧化焙烧炉,所述焙烧给矿颗粒在炉中以流化态进行氧化焙烧,得到氧化焙烧产品。
在本发明中,所述氧化焙烧在氧化气氛下进行,所述氧化气氛优选为空气;所述氧化焙烧的温度优选为1000~1050℃,更优选为1030~1050℃,具体的,在本发明的实施例中,可以是1030℃、1040℃或1050℃;所述氧化焙烧的时间优选为30~90min,更优选为40~80min,最优选为50~70min,具体的,在本发明的实施例中,可以是60℃或70℃。
本发明对形成所述物料流化态的气流量没有特殊的限制,按照本领域技术人员的常用方法,在确定所述焙烧给矿的粒径、给料速度以及焙烧装置的大小之后,再确定临界流化风速,如,在上文所述的粒径条件下,在给料速度100kg/h时,流化气量大约在10~15m3/h。
在上述氧化焙烧的过程中,高磷鲕状铁矿受热将脱除其中的吸附水、结晶水及其他挥发份组成,同时,由于矿物的膨胀系数系数不同,高温将导致可颗粒内部出现不均匀膨胀,导致裂隙的生成,一定程度上破坏了鲕状结构,增大孔隙率和表面积,使其有利于后续还原和浸出。
完成所述氧化焙烧之后,本发明将所述氧化焙烧产物送入磁化焙烧炉中,在还原性气氛下,所述氧化焙烧产品颗粒以流化态进行磁化焙烧,将物料中的铁矿还原为强磁性的磁铁矿,得到磁化焙烧产品。
在本发明中,所述还原性气氛优选为包括惰性气体和还原性气体,所述惰性气体优选为氮气、氩气和氦气中的一种或几种,所述还原性气体优选为co、h2和煤制气中的一种或几种;在本发明中,所述还原性气体在所述还原性气氛中的体积分数优选为20~40%,更优选为25~35%,具体的,在本发明的实施例中,可以是25%、30%或40%。
在本发明中,所述磁化焙烧的温度优选为520~550℃,更优选为530~540℃,具体的,在本发明的实施例中,可以是520℃或530℃;本发明可依靠氧化焙烧产品自身的热量,将所述磁化焙烧炉内的温度维持在上述范围内;所述磁化焙烧的时间优选为30~60min,更优选为40~50min,具体的,在本发明的实施例中,可以是30min或55min。
完成上述磁化焙烧之后,本发明将磁化焙烧产品在惰性气氛下快速冷却至180~250℃,然后接触空气氧化冷却,得到冷却后的焙烧产品。
在本发明中,快速冷却后的氧化冷却能够将还原后的强磁性的磁铁矿(fe3o4)氧化,使其转化为矫顽力较低的强磁性矿物γ-fe2o3,可降低铁矿物的磁团聚现象,由于降低了磁团聚,分选过程带有石英的脉石矿物就不会随着团聚矿进入精矿,而是进入了尾矿,这样磁选产品精矿的铁含量获得提高,硅含量降低,提高磁选产品的质量;同时,矿物在快速冷却时迅速收缩,致使矿物颗粒表面出现裂隙,提高了孔隙率,有助于后续浸出。
在本发明中,所述冷却的气氛优选为氮气、氩气和氦气中的一种或几种,所述冷却的速率优选为50~100℃/min,更优选为60~90℃/min,最优选为70~80℃/min;先将所述磁化焙烧产品冷却至180~250℃,优选冷却至190~240℃,具体的,在本发明的实施例中,可以是190℃、200℃或240℃;然后将冷却至180~250℃下的物料接触空气,进行氧化和进一步的冷却,在该步骤的氧化冷却过程中,所述降温的速率不作特殊的限制,可以选用自然冷却至90℃以下,优选的,氧化冷却至20~90℃,更优选为30~80℃,最优选为40~70℃。
得到冷却后的焙烧产品后,本发明将所述冷却后的焙烧产品依次进行磨矿-磁选和酸浸除磷,得到铁精矿。
在本发明中,所述磨矿-磁选能够将冷却后的焙烧产品除杂脱硅,得到铁精矿,优选按照以下步骤进行:
将冷却后的焙烧产品磨矿至-0.038mm的物料的质量分数为40~70%,然后进行弱磁选,得到弱磁选铁精矿;
在本发明中,所述弱磁选的磁场强度优选为1000~2000oe,更优选1200~1900oe,最优选为1300~1800oe,具体的,在本发明的实施例中,可以是1200oe、1300oe或1900oe。
针对于本申请中的工艺所得到的焙烧产品,本发明使用了相对较高的磁场强度进行磁选,能够获得更高的回收率。
然后,将磁选完的产品按照以下步骤进行酸浸除磷:
将弱磁选铁精矿在酸液中浸泡30~50min,过滤后洗涤、烘干,得到铁精矿。
在本发明中,所述酸液优选为硫酸,所述硫酸的浓度优选为0.2~0.6mol/l,更优选为0.3~0.5mol/l,最优选为0.4~0.5mol/l;所述酸液与所述弱磁选精铁矿的液固比优选为(3~20)ml:1g,更优选为(5~15)ml:1g,具体的,在本发明的实施例中,可以是8ml:1g、10ml:1g或16ml:1g;所述浸泡的时间优选为30~50min,更优选为35~45min,具体的,在本发明的实施例中,可以是30min、35min或40min。
在本发明中,所述过滤、洗涤和烘干均为本领域技术人员所熟知的处理方法,本发明在此不进行特殊的限制。
按照上述方法得到的铁精矿铁品位≥63.00%,铁回收率≥92.00%,p品位≤0.20%。
本发明提供一种高磷鲕状铁矿悬浮焙烧提铁-酸浸除磷的方法,包括以下步骤:a)将高磷鲕状铁矿石粉碎后在流化态下进行氧化焙烧,得到氧化焙烧产品;b)将所述氧化焙烧的产品在还原性气氛和流化态下进行磁化焙烧,得到磁化焙烧产品;c)将所述磁化焙烧产品在惰性气氛下快速冷却至180~250℃,然后接触空气氧化冷却,得到冷却后的焙烧产品;所述冷却的降温速率为50~100℃/min;d)将冷却后的焙烧产品依次进行磨矿-磁选和酸浸除磷,得到铁精矿。本发明采用高温氧化焙烧对流化态的物料进行处理,颗粒内生成大量的裂隙,一定程度上破坏了鲕状结构,增大孔隙率和比表面积,使其有利于还原和浸出,同时流化态具有极高的传质传热效率。同时,本发明对还原物料进行快速降温,致使矿物颗粒表面出现裂隙,进一步提高了孔隙率,有助于后续浸出,冷却后进行氧化,使还原后的人工磁铁矿fe3o4氧化生成了矫顽力较低的强磁性矿物—γ-fe2o3,可降低铁矿物的磁团聚现象,提高磁选产品的质量。实验结果表明,本发明中的方法制备得到的铁精矿的铁品位≥63.00%,铁回收率≥92.00%,p品位≤0.20%。
为了进一步说明本发明,以下结合实施例对本发明提供的一种高磷鲕状铁矿悬浮焙烧提铁-酸浸除磷的方法进行详细描述,但不能将其理解为对本发明保护范围的限定。
实施例1
1.粉碎:准备高磷鲕状赤铁矿石作为原料,其铁品位在55.61%,磷的质量百分含量为0.81%,将原料破碎至-2mm后,磨矿至-0.074mm的物料占总体质量的45%,作为焙烧给矿;
2.氧化焙烧:将焙烧给矿送入氧化焙烧炉进行高温氧化焙烧,在氧化气氛条件下,将物料加热至1030℃,焙烧60min得到氧化焙烧产品;
3.磁化焙烧:氧化焙烧的产品,在530℃的还原气氛下焙烧30min,得到磁化焙烧产品,其中co气体占混合气体(n2和co)总体积的30%;
4.冷却氧化:将磁化焙烧的产品在氮气保护下快速冷却至200℃后,再接触空气氧化冷却至90℃以下。
5.磨矿-磁选:将焙烧矿磨矿至-0.038mm的物料占总体质量的60%,磁场强度为1200oe,弱磁选后得到弱磁选铁精矿;
6.酸浸除磷:将弱磁选铁精矿用硫酸进行酸浸脱磷,其中硫酸浓度为0.4mol/l,硫酸与磁选铁精矿的液固比为8ml/g,酸浸脱磷的时间为35min;酸浸后的产品,经过过滤、洗涤及烘干,制成最终铁精矿,其铁品位63.59%,铁回收率93.76%,p含量0.18%。
实施例2
1.粉碎:准备高磷鲕状赤铁矿石作为原料,其铁品位在53.72%,p的质量百分含量为0.98%,将原料破碎至-2mm后,磨矿至-0.074mm的物料占总体质量的55%,作为焙烧给矿;
2.氧化焙烧:将焙烧给矿送入氧化焙烧炉进行高温氧化焙烧,在氧化气氛条件下,将物料加热至1040℃,焙烧70min得到氧化焙烧产品;
3.磁化焙烧:氧化焙烧的产品,在530℃的还原气氛下焙烧55min,得到磁化焙烧产品,其中co气体占混合气体(n2和co)总体积的25%;
4.冷却氧化:将磁化焙烧的产品在氮气保护下快速冷却至190℃后,再接触空气氧化冷却至90℃以下。
5.磨矿-磁选:将焙烧矿磨矿至-0.038mm的物料占总体质量的65%,磁场强度为1300oe,弱磁选后得到弱磁选铁精矿;
6.酸浸除磷:将弱磁选铁精矿用硫酸进行酸浸脱磷,其中硫酸浓度为0.2mol/l,硫酸与磁选铁精矿的液固比为10ml/g,酸浸脱磷的时间为40min;酸浸后的产品,经过过滤、洗涤及烘干,制成最终铁精矿,其铁品位64.21%,铁回收率93.32%,p含量0.16%。
实施例3
1.粉碎:准备高磷鲕状赤铁矿石作为原料,其铁品位在41.46%,p的质量百分含量为1.18%,将原料破碎至-2mm后,磨矿至-0.074mm的物料占总体质量的60%,作为焙烧给矿;
2.氧化焙烧:将焙烧给矿送入氧化焙烧炉进行高温氧化焙烧,在氧化气氛条件下,将物料加热至1050℃,焙烧70min得到氧化焙烧产品;
3.磁化焙烧:氧化焙烧的产品,在520℃的还原气氛下焙烧30min,得到磁化焙烧产品,其中co气体占混合气体(n2和co)总体积的40%;
4.冷却氧化:将磁化焙烧的产品在氮气保护下快速冷却至240℃后,再接触空气氧化冷却至90℃以下。
5.磨矿-磁选:将焙烧矿磨矿至-0.038mm的物料占总体质量的70%,磁场强度为1900oe,弱磁选后得到弱磁选铁精矿;
6.酸浸除磷:将弱磁选铁精矿用硫酸进行酸浸脱磷,其中硫酸浓度为0.6mol/l,硫酸与磁选铁精矿的液固比为16ml/g,酸浸脱磷的时间为30min;酸浸后的产品,经过过滤、洗涤及烘干,制成最终铁精矿,其铁品位63.31%,铁回收率92.11%,p含量0.19%。
以上所述仅是本发明的优选实施方式,应当指出,对于本技术领域的普通技术人员来说,在不脱离本发明原理的前提下,还可以做出若干改进和润饰,这些改进和润饰也应视为本发明的保护范围。
起点商标作为专业知识产权交易平台,可以帮助大家解决很多问题,如果大家想要了解更多知产交易信息请点击 【在线咨询】或添加微信 【19522093243】与客服一对一沟通,为大家解决相关问题。
此文章来源于网络,如有侵权,请联系删除


