大幅度提升重型柴油机铝活塞毛坯铸造成品率的模具组件的制作方法



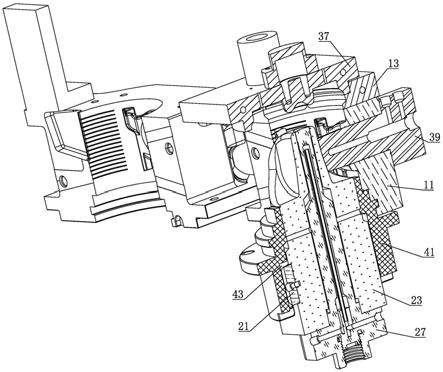
[0001]
本发明涉及大幅度提升重型柴油机铝活塞毛坯铸造成品率的模具组件,应用于使用模具铸造重型柴油机铝活塞毛坯。
背景技术:
[0002]
重型柴油机铝活塞同普通汽油机铝活塞相比有许多不同。第一,它的重量是普通汽油机的5~8倍。第二,为了提高耐磨性能,铸造时需要在柴油机铝活塞毛坯中镶嵌合金耐磨圈。合金耐磨圈铸造在铝活塞毛坯中,用于后续加工车出顶部第一道环槽。第三,为了改善混合气流动性能和燃烧性能,增大燃烧室的容积,增大压缩比,成品柴油机铝活塞顶部燃烧室的凹坑一般设计的大且深。第四,重型柴油机气缸中燃烧产生的热量非常高,需要对活塞进行强制冷却,为此目的还需要在柴油机铝活塞毛坯内部开设内冷油道。第五,重型柴油机铝活塞的头部需要有3~5道环槽,上面2~3道用以安装气环,下面1~2道用以安装油环。第六,柴油机活塞的裙部受力较大,一般比较厚,在5毫米以上。
[0003]
随着各国基建、运输要求的不断提高,发动机功率、载荷越来越大。对重型柴油机铝活塞结构提出了很高的要求,要求能够满足现代高速高负荷,大功率发动机的需要。重型柴油机活塞作为气缸中往复运动最大的一个零部件,其工作条件严酷,强度最大,不仅承受着高的热负荷、机械负荷和强烈的磨损,还经常处于润滑不良、冷却困难的极端境况,因而极易出现故障。正因为如此,人们对成品重型柴油机活塞有着严苛的各种要求。重型柴油机铝活塞毛坯铸造过程在短时间内需经历的步骤繁琐复杂,影响质量的环节多,故而成品率很低。因此,重型柴油机铝活塞毛坯具有铸造成本高,利润高,报废率高,产量低“三高一低”的特点。
[0004]
现行重型柴油机铝活塞铸造模具由顶模、外模i、外模ii、销孔模i、销孔模ii、芯模、止口固定座五个组件组成。止口固定座固定在操作台上,销孔模i、销孔模ii分别插在外模i、外模ii的销孔中。而顶模、外模i、外模ii、芯模则分别由安装在操作台及台架上的数控液压牵引机构从上、下、左、右四个方向牵引,通过这种牵引实现模具的自动组合和自动分离脱模。
[0005]
合金耐磨圈置于顶模和外模拼合成的环形空腔中。外模半环形空腔和顶模半环形空腔中皆从模本体延伸出三只均分于半环形空腔中的支撑片,作为支架使用,用于支撑合金耐磨圈并将合金耐磨圈紧固。顶模和外模组合时,各对支撑片将合金耐磨圈环形中心线固定在水平面上,也即合金耐磨圈中心轴线在竖直方向上。这种结构的缺点是:相同批次铸造成品中存在合金耐磨圈镶嵌位置偏移、上下移位、与铝合金结合面脱落等问题。
[0006]
重型柴油机铝活塞内冷油道制作方法是铸造铝活塞毛坯时在模具中镶嵌盐芯环,待铝活塞毛坯冷却后用水将盐芯环溶解即可冲出环位所占空间,形成内冷油道。所述盐芯环开轴向的两个通孔,分别位于两个半环部分的中间。盐芯环置于芯模两侧同芯模连结为一体的、相互间等高的两支杆上,各支杆中心线上开盲孔。盐芯环上的通孔与支杆上的盲孔对正,两只短销钉从盐芯环通孔中插入将盐芯环固定在两支杆上,让盐芯环的环形中心线
处于水平面上。盐芯环这种安装结构缺点是:盐芯环铸造过程中存在安放位置上浮、隐形加热开裂注铝,安放位置结合面飞边严重,铸造成品率低等问题。造成这些问题的原因是铸液注入模腔过程中,随着液面的不断上升,盐芯环因受浮力作用改变着自身所处的方位,致使局部冷热不均出现开裂。
[0007]
重型柴油机铝活塞毛坯生产具有批次多,每批次生产的数量少的特点。所以芯模装上卸下比较频繁。芯模约有15~20斤重,绕竖直中心轴线旋转通过螺纹紧固在液压缸的活塞杆上,旋转安装过程中容易局部错牙,烂牙。因活塞杆作往复的直线运动,芯模被限定在止口固定座内部作竖直方向上的向上和向下运动。一个工作日内由液压缸活塞杆反复推送数千次,芯模和活塞杆互锁的螺纹承受着活塞杆向上推动芯模过程中芯模的全部重量,以及活塞杆向下抽动时铸造冷却收缩的阻力。因此芯模的螺纹极易损坏。芯模是整体件,一旦纹牙损毁,整个芯模也就报废。并且,芯模重、液压推动杆长、以及芯模与活塞杆之间连接状态不良,会造成芯模在运动中的偏摆,受到碰撞损伤,也会绕自身的中心轴线偏转,最终导致铸造定位差。芯模整体因为要水冷,无法作排气设计,铸造冷却时间长,铸造中会多处产生冷隔。所述冷隔是指冷却后所铸活塞毛坯内部出现断层、中空或者外表面出现局部塌陷等现象。
[0008]
合金耐磨圈、盐芯环、芯模在铸造中引发的上述问题皆是报废率高的直接原因。活塞生产厂家期望一种铸造成品率高的模具组件。
技术实现要素:
[0009]
本发明的目的在于克服上述现有技术中的不足之处,提供一种铸造重型柴油机铝活塞毛坯成品率高的大幅度提升重型柴油机铝活塞毛坯铸造成品率的模具组件,它避免了耐磨圈、盐芯环因现有固定方式导致的报废率高的问题,它还避免了芯模螺纹孔螺牙损坏因芯模安装不能实际到位引起的,以及受长活塞杆推动作竖向运动的芯模因微小幅度偏离竖直轨道引起的报废率高的问题。
[0010]
本发明的目的可以通过下述技术方案来达到:大幅度提升重型柴油机铝活塞毛坯铸造成品率的模具组件,它由顶模、外模i、外模ii、销孔模i、销孔模ii、芯模、止口固定座五个组件组成;顶模、外模i、外模ii、芯模皆通过螺纹孔分别与安装在操作台及台架上的四只数控液压缸的活塞杆末端螺纹连接;四只数控液压缸的活塞杆分别从上、左、右、下四个方向牵引顶模、外模i、外模ii、芯模;销孔模i插在外模i销孔i中由螺丝紧固;销孔模ii插在外模ii的销孔ii中由螺丝紧固;止口固定座套在芯模外与操作台相紧固;
[0011]
(i)所述顶模带顶模耐磨圈半环形空腔,所述顶模耐磨圈半环形空腔从模本体延伸出均分于顶模耐磨圈半环形空腔中的支撑片;
[0012]
(ii)所述外模i、外模ii拼合时带外模耐磨圈半环形空腔,所述外模耐磨圈半环形空腔从模本体延伸出均分于外模耐磨圈半环形空腔中的支撑片;
[0013]
(iii)所述芯模两侧带相间等高的盐芯环支杆i和盐芯环支杆ii,两支杆中心线开盐芯环支杆i中心线孔和盐芯环支杆ii中心线孔;
[0014]
(iv)所述芯模中心轴线上带芯模水冷却通道;所述芯模螺纹孔在芯模中心轴线上位于底面处;
[0015]
其特征是:
[0016]
(v)i所述的均分于顶模耐磨圈半环形空腔中的支撑片共有4片;
[0017]
(vi)ii所述的均分于外模耐磨圈半环形空腔中的支撑片共有4片;外模耐磨圈半环形空腔是柱面平底托盘中的空腔,柱面平底托盘由2个相同的半块托盘拼合而成,每半块托盘中的支撑片为2片,两半块托盘分别通过螺孔和螺丝紧固在外模i、外模ii本体的平台上;
[0018]
(vii)iii所述盐芯环支杆i和盐芯环支杆ii中心线开的盐芯环支杆i中心线孔和盐芯环支杆ii中心线孔为通孔,孔内分别插钢丝i和钢丝ii,钢丝i和钢丝ii上端露头,下端通过螺丝与芯模底面紧固;
[0019]
(viii)iv所述芯模水冷却通道和芯模螺纹孔集中在阶梯柱面芯轴内,所述阶梯柱面芯轴上端外侧面带轴向微形槽,下端带芯轴法兰;阶梯柱面芯轴嵌入在芯模本体沿芯模中心轴线开的芯模本体空腔通孔中通过芯轴法兰和螺丝与芯模本体下部紧固;阶梯柱面芯轴上端与芯模本体空腔通孔内侧壁紧密接触;芯模本体中部径向开排气出口并与芯模本体空腔通孔连通;
[0020]
(ix)止口固定座套在芯模外通过止口固定座轴向导向槽和芯模轴向导向块同芯模连接。
[0021]
本发明同现有技术相比具有如下优点:
[0022]
1、顶模耐磨圈半环形空腔、外模耐磨圈半环形空腔合拢时,通过4对支撑片共同将耐磨圈固定,根据3点确定一个平面原理,在浇铸中4者之一失去作用皆有其余3对支撑片将耐磨圈环形中心线所处平面限定在水平面内,这就避免了因耐磨圈固定位置不稳定造成的铸件报废。同时,铝液浇铸过程中及浇铸结束后的冷却凝固过程,铸液的流体力学、热力学过程导致的变化过程复杂,在允许1对支撑片临时失去作用的情况下,4对支撑片共有24种组合方式形成符合规范要求的3对支撑片将耐磨圈环形中心线所处平面限定在水平面内,提高了对浇铸过程中的可控性,降低了报废率。
[0023]
2、外模耐磨圈半环形空腔是柱面平底托盘中的空腔,柱面平底托盘置于外模i、外模ii本体的平台上,从而通过磨去底面或通过焊接垫高底面可以实现参照铸样进行铸件耐磨圈所处高度的微调,准确做到所设高度即为所得,提高了成品率。
[0024]
3、盐芯环支杆中心线通孔中的钢丝,下端由螺丝紧固,上端露头段用于销入盐芯环通孔。露头段笔直生根,盐芯环环形中心线所处的平面被限定在与两露头段(两条竖直线)确定的竖直面相垂直的水平面上,依靠自身的重量保持着与支杆端面的密切接触,在铸液浇入过程中,随着铸液面的上升,盐芯环与液面的热接触始终为环形面接触,有效避免了受热不均匀引起的裂纹及飞边的问题。
[0025]
4、芯模水冷却通道和芯模螺纹孔从现有芯模本体一体连接中分离出来,被集中在阶梯柱面芯轴内;而阶梯柱面芯轴可单独制作,作为一个不可少的芯模配件使用。因此可以根据生产中因频繁装卸引起的芯模螺纹螺牙损坏情况配置2~3只阶梯柱面芯轴,做到及时更换新螺牙。
[0026]
阶梯柱面芯轴上部外侧所带的轴向微形槽制作简单,轻松解决了现有芯模本体中因沿着芯模轴向中心轴线在已开设水冷通道情况下却很难再开设排气通道的技术难题(需要钻轴向长距离排气微孔),避免了无芯模排气通道造成的报废。
[0027]
芯模在止口固定座中作线性轨道运动,芯模轴向导向块限定在止口固定座轴向导
向槽中滑动,芯模在竖直方向的运动平稳,克服了因人力螺纹连接不当、原动力活塞杆推动作用力方向造成的芯模运动偏离造成的铸件报废。
附图说明
[0028]
图1是顶模结构示意图。
[0029]
图中1是均分于顶模耐磨圈半环形空腔中的支撑片。
[0030]
图2是柱面平底托盘结构示意图。
[0031]
图中3是均分于外模耐磨圈半环形空腔中的支撑片。
[0032]
图3是去掉柱面平底托盘后的外模i、外模ii结构示意图。
[0033]
图中5是外模i、外模ii本体的平台。
[0034]
图4是外模i、外模ii结构示意图。
[0035]
图中7是半块托盘i,9是外模i本体;11是外模ii本体,13是半块托盘ii。
[0036]
图5是芯模结构示意图。
[0037]
图中15是盐芯环支杆i中心线孔,17是芯模本体空腔通孔,18是盐芯环支杆ii中心线孔,19是排气出口,21是芯模轴向导向块,23是芯模本体,25是轴向微形槽,27是阶梯柱面芯轴,29是芯轴法兰。
[0038]
图6是插入钢丝i和钢丝ii后的芯模轴向中心线剖视图。
[0039]
图中23是芯模本体,31是钢丝i,33是钢丝ii,27是阶梯柱面芯轴,34是芯模螺纹孔。
[0040]
图7是盐芯环同芯模组合在一起的分解图。
[0041]
图中31是钢丝i,35是盐芯环,33是钢丝ii,19是排气出口,23是芯模本体,27是阶梯柱面芯轴,21是芯模轴向导向块。
[0042]
图8是本发明未镶入耐磨圈和盐芯环组装图的局部剖视图。
[0043]
图中37是顶模,13是半块托盘ii,39是销孔模ii,11是外模ii本体,41是止口固定座,23是芯模本体,27是阶梯柱面芯轴,21是芯模轴向导向块,41是止口固定座轴向导向槽。
具体实施方式
[0044]
大幅度提升重型柴油机铝活塞毛坯铸造成品率的模具组件,它由顶模、外模i、外模ii、销孔模i、销孔模ii、芯模、止口固定座五个组件组成;顶模、外模i、外模ii、芯模皆通过螺纹孔分别与安装在操作台及台架上的四只数控液压缸的活塞杆末端螺纹连接;四只数控液压缸的活塞杆分别从上、左、右、下四个方向牵引顶模、外模i、外模ii、芯模;销孔模i插在外模i销孔i中由螺丝紧固;销孔模ii插在外模ii的销孔ii中由螺丝紧固;止口固定座套在芯模外与操作台相紧固;
[0045]
(i)所述顶模带顶模耐磨圈半环形空腔,所述顶模耐磨圈半环形空腔从模本体延伸出均分于顶模耐磨圈半环形空腔中的支撑片(1);
[0046]
(ii)所述外模i、外模ii拼合时带外模耐磨圈半环形空腔,所述外模耐磨圈半环形空腔从模本体延伸出均分于外模耐磨圈半环形空腔中的支撑片(3);
[0047]
(iii)所述芯模两侧带相间等高的盐芯环支杆i和盐芯环支杆ii,两支杆中心线开盐芯环支杆i中心线孔(15)和盐芯环支杆ii中心线孔(18);
[0048]
(iv)所述芯模中心轴线上带芯模水冷却通道;所述芯模螺纹孔(34)在芯模中心轴线上位于底面处;
[0049]
本发明的改进之处是:
[0050]
(v)i所述的均分于顶模耐磨圈半环形空腔中的支撑片共有4片。
[0051]
(vi)ii所述的均分于外模耐磨圈半环形空腔中的支撑片共有4片。
[0052]
现有技术采用3对支撑片,每对支撑片上、下对正,夹持耐磨圈。由于铸造精度要求很高,只要其中1对支撑片失去作用,耐磨圈在铸液浮力及自身重力的作用下可以绕着另2对支撑片(2个点)确定的直线作微幅度旋转,进而导致铸件的报废。本发明采用4对支撑片,只要其中1对支撑片失去作用,当耐磨圈试图绕2对支撑片确立的直线旋转时,第4对支撑片必然适时阻止此方向的旋转而使耐磨圈处于其余3对支撑片(3个点)确立的平面上。所以,本发明采用4对支撑片,直接提高了置于模腔中耐磨圈的抗扰能力,促成了成品率的提升。
[0053]
外模耐磨圈半环形空腔是柱面平底托盘中的空腔,柱面平底托盘由2个相同的半块托盘拼合而成,每半块托盘中的支撑片为2片,两半块托盘分别通过螺孔和螺丝紧固在外模i、外模ii本体的平台(5)上。本发明将外模耐磨圈半环形空腔从现有技术模本体中分离出来,制作成柱面平底托盘。由于可以通过加焊或磨去调整托盘的高度,也就可以根据铸样耐磨圈实际处的高度调整成品铸件中耐磨圈的高度,满足了客户对精度的要求,提高了成品率。将柱面平底托盘制作成两半块托盘,适应外模分型成外模i和外模ii的需要。
[0054]
(vii)iii所述盐芯环支杆i和盐芯环支杆ii中心线开的盐芯环支杆i中心线孔(15)和盐芯环支杆ii中心线孔(18)为通孔,孔内分别插钢丝i(31)和钢丝ii(33),钢丝i和钢丝ii上端露头,下端通过螺丝与芯模底面紧固。两钢丝下端因螺丝紧固生根,上端露头段能保持竖直状态,盐芯环两通孔套插在两露头段,盐芯环环形中心线所确定的平面在水平面上,克服了现有技术中采用自上而下的销钉固定方式会发生的盐芯环微小幅度的翻转运动,进而避免了盐芯环因受热不均匀出现的隐形开裂注铝和铸造中的飞边现象。
[0055]
(viii)iv所述芯模水冷却通道和芯模螺纹孔集中在阶梯柱面芯轴(27)内,所述阶梯柱面芯轴上端外侧面带轴向微形槽(25),下端带芯轴法兰(29)。将芯模水冷却通道和芯模螺纹孔从现有技术模本体中分离出来,制作成配件阶梯柱面芯轴。在阶梯柱面芯轴外侧面开轴向微形槽,用于排气。
[0056]
阶梯柱面芯轴嵌入在芯模本体沿芯模中心轴线开的芯模本体空腔通孔(17)中通过芯轴法兰和螺丝与芯模本体下部紧固。阶梯柱面芯轴这种嵌入式通过法兰紧固的结构,方便了更换和组装。芯模螺纹孔若有损坏,可以只更换阶梯柱面芯轴,而不用报废整个芯模。所以,可根据生产量和螺纹损坏情况,多配1~2只阶梯柱面芯轴,做到适时更新芯模用于连接活塞杆的内螺纹。
[0057]
阶梯柱面芯轴上端与芯模本体空腔通孔内侧壁紧密接触。阶梯柱面芯轴上端的轴向微形槽同芯模本体空腔通孔内表面结合形成排气进口。排气进口很小,不渗铸液。芯模本体中部径向开排气出口(19)并与芯模本体空腔通孔(17)连通。阶梯柱面芯轴阶梯状,上小下大,以使排气进口、排气出口通过芯模本体空腔相连通。
[0058]
(ix)止口固定座套(41)在芯模外通过止口固定座轴向导向槽(43)和芯模轴向导向块(21)同芯模连接。止口固定座轴向导向槽和芯模轴向导向块组成线性轨道。确保芯模在组模和脱模过程作竖直方向上的运动,保持同止口固定座的同轴配合状态,提高产品的
成品率。
[0059]
本发明在组模时,止口固定座与操作台相固定,按常规操作将芯模、外模i和外模ii组合到位后,将盐芯环穿插在钢丝i和钢丝ii露头段,保持同盐芯环支杆i和盐芯环支杆ii两端面的自然接触。然后将耐磨圈搁在外模耐磨圈半环形空腔中,最后将顶模推到位即可开始浇铸铝液。脱模常规操作即可。
起点商标作为专业知识产权交易平台,可以帮助大家解决很多问题,如果大家想要了解更多知产交易信息请点击 【在线咨询】或添加微信 【19522093243】与客服一对一沟通,为大家解决相关问题。
此文章来源于网络,如有侵权,请联系删除



tips