高比例镁球团高炉炼铁方法及设置在高炉上的自动布料器与流程



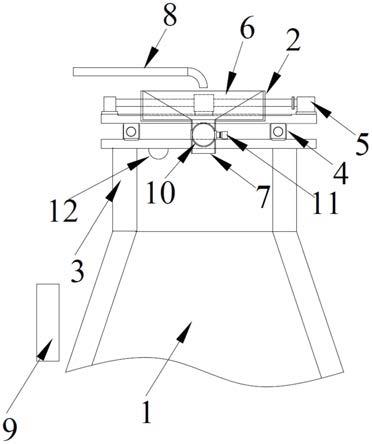
[0001]
本发明涉及冶金炼铁技术领域,具体涉及一种使用高比例镁球团高炉炼铁方法。
背景技术:
[0002]
目前,国内高炉炼铁时,球团矿入炉比例一般小于18%,个别钢铁企业炼铁的入炉球团矿达到26%比例,但是长期保持55%以上的高球团矿比例的高炉炼铁技术,现在还没有。国外炼铁技术中,球团矿有达到100%的入炉比例,但其球团矿是熔剂性球团,非酸性氧化球团矿,且其sio
2
含量在2.5%以下,与国内球团矿分属两种不同种类球团矿。
[0003]
现有技术中高炉炼铁,因烧结矿原料不足,所以入炉矿石中球团矿比例需增大至50%以上。这种情况下,高炉在冶炼过程中会出现明显的憋风现象,且崩塌料、悬料增多,频繁出现管道行程(因高炉料柱透气性差而使炉内煤气流从局部透气性好的地方,在高炉内由下到上吹成一个通道),这使得生料未经充分预热和还原便落至炉底,导致高炉温度降低、热能利用性差,炉内上部经常结瘤。为解决上述技术问题,生产工艺只能被迫降低球团矿的入炉比例(即在入炉总矿石中的质量含量)至35%以下,降低冶炼强度,炉况才能好转。所以,国内现有技术中的高炉炼铁工艺长期困扰于烧结紧张
→
提球团矿比例
→
炉况失常
→
降球团矿比例
→
烧结又紧张的恶性循环怪圈,炼铁高炉很难保持长时间的稳定运行,技术经济指标不理想。
[0004]
熔剂性球团生产工艺把铁矿粉经过链蓖机回转窑或带式焙烧机在密封循环的设备上进行焙烧,可以极大降低环境污染和工序消耗。目前国内高炉使用大比例烧结矿,球团矿比例平均在15%左右,太钢、首钢京唐等不超过30%,国内极个别小高炉球团矿比例达到45%左右。研究开发一种能够少使用烧结矿,而大比例使用球团高炉冶炼工艺,在高炉内冶炼可以降低渣比,减少燃料消耗,降低co
2
排放量,是节能环保的高炉冶炼模式。
[0005]
然而,物料的配比、放置位置、分布方式对高炉的运行有重要影响,精确的物料布放,对高炉运行有着重要意义。现有技术采用在无料钟炉顶通过料流调节阀的开度控制料流控制物料速度,通过布料溜槽的倾动和旋转控制物料布放的位置,其中溜槽的控制方式有重量和时间方式。
[0006]
其中,重量方式在读取预先设定的布料矩阵之后,将矩阵中数据转换为重量参数,在布料时,把设定重量的物料放置在设定的位置。而时间方式,在读取预先设定的布料矩阵之后,将矩阵中数据转换为旋转圈数,在布料时,在设定的角度旋转设定的圈数,从而达到在特定位置布放特定重量物料的目的。
[0007]
实际应用中因为重量方式能更准确的布放物料,生产中大多数情况采用重量方式,但是重量方式对称量设备的稳定非常依赖,在实际生产中,高炉压力变化,料罐上物料的堆积,经常影响称量的稳定,而造成布料的不稳定。时间方式对称量设备不依赖,然而,传统的时间方式按照圈数控制物料布放,精度很差,同时也限制了布料矩阵的形式,有效值必须是合理的自然数。
[0008]
另外现有布料器的出料口都是设置在按固定部位,通过溜槽的旋转及改变溜槽的
倾角达到将物料投入到高炉内设定部位的目的。然而采用这种投料方式并不能达到精准控制,将物料按照设想的方式排布投入到高炉内。
技术实现要素:
[0009]
本发明的目的在于克服现有技术中存在的缺陷,提供一种使用高比例镁球团高炉炼铁方法。该方法工艺简单,通过改善球团矿的组分含量和组织结构,加之调整高炉冶炼时的一些技术参数,使得高炉在冶炼球团矿质量含量高达65%以上的矿石时稳定运行,提高了企业效益。
[0010]
为实现上述目的,本发明的技术方案是提供了一种高比例镁球团高炉炼铁方法,包括以下步骤:
[0011]
第一步,冶炼镁球团:将烧结矿、含氟熔剂、焦炭、矿料装入受料槽,而后通过控制受料槽上自动振动筛按照设定的程序对四种物料按配比及设定的投料布局进行投料;
[0012]
第二步,各种物料均按设定配比放置在传送设备上,而后运上高炉顶部的受料器内,将每批料通过炉顶布料器按照自动布料程序装入高炉,并将热风从风口按照送风制度鼓入高炉;
[0013]
第三步,将第一步所得镁球团为65%~75%的矿石及铁矿石、焦炭放入高炉,布料、低硅冶炼,得生铁;布料时,外环矿石的α角为18
°
~24
°
,内环矿石的α角为20
°
~24
°
,焦碳与矿石的质量配比0.3~0.5%;低硅冶炼时,高炉的风口面积为0.12~0.13m
2
,风口长度为250~380mm,风口向下倾斜角度为3
°
~5
°
。
[0014]
其中镁球团矿的生产方法,包括如下步骤:
[0015]
s1、配料工序:将计算好质量配比的原料进行充分混合;
[0016]
s2、烘干、润磨工序:将s1中的原料进行烘干,烘干温度控制在850
±
50℃,经过润磨机润磨的原料粒度要求-200目≥80%,确保原料的润磨效果;
[0017]
s3、造球工序:将s2中的原料进行圆盘造球机造球,生球水分控制8.5-9.5%,粒度15-20mm≥90%,生球每米落下强度不低于5次;
[0018]
s4、热工参数控制:将s3中的生球均匀布置在竖炉的烘干床上,竖炉的烘干床温度控制。
[0019]
在500
±
50℃,燃烧室温度控制在1060
±
20℃,烟罩温度控制在90-120℃。
[0020]
优选的技术方案是,将所述热风送风控制在:风量为3800-4200m
3
/min,鼓风动能为12000-14000,炉顶压力为0.150mpa-0.185mpa,透气性指数2.10-2.30,热风温度为1200
±
3.0℃,富氧率为1.2%-1.5%,炉腹燃气指数51.5-60.5,炉顶高温为300℃-320℃,炉顶低温为210℃-220℃,理论燃烧温度2320℃-2520℃;
[0021]
高炉的热制度及造渣制度分别为:热制度控制要求:铁水温度≥1525℃,[si]含量≤0.630%,[p]含量≤0.030%;造渣制度控制要求:全碱度为1.20
±
0.30,自由碱度为1.03
±
0.06,二元碱度0.82
±
0.03,al
2
o
3
含量≤14.0%,mgo含量≥10.2%;
[0022]
优选的技术方案还有,其中所述物料的按重量份计包括烧结矿和镁球团50份,焦炭10.2-10.5份,矽石,0-0.3份;其中所述烧结矿与镁球团的重量比为70-58:20-28;
[0023]
优选的技术方案还有,所述镁球团质量控制要求:tfe≥68.5%,feo含量<0.8%,s含量<0.13%,mgo含量≥3.0%,sio
2
含量≤2.5,na
2
o与k
2
o的总含量小于0.05%、zno<
0.08%,f含量≤0.45%,ro≥0.85,抗压强度≥2450n/p,转鼓强度≥89%,抗磨指数≤2.6%。
[0024]
优选的技术方案还有,所述第一部中焙烧所得的球团矿中,强度低于1000n的球团矿质量含量低于10%。
[0025]
优选的技术方案还有,所述低硅高镁含氟熔剂性球团的配料时通过添加高镁粉、高镁矿或炼钢污泥中一种或几种调控原料中mgo含量。
[0026]
本发明的另一个发明目的是,提供一种结构简单,便于操作、自动化程度高、控制精准,可按照任意设定的投料布局结构将物料投入到高炉内的一种设有移动式投料口的高炉布料器。
[0027]
为实现另一个目的,本发明的技术方案还提供了一种设置在高炉上的自动布料器,包括架设在高炉顶部的支撑架,支撑架上设有纵向驱动机构,在纵向驱动机构的驱动部件上通过横向驱动框架或横向驱动板设置有横向驱动机构,在横向驱动机构的驱动部件上通过布料器驱动框架或布料器驱动板设置有布料器,布料器的主体内设有由上向下的投料锥斗,投料斗的下端口与投料管的一端连接,投料管的另一端通向高炉的上端口,投料斗的上端口的形状及大小应满足布料器移动到任意极限位置,投料斗的上端口都在原料固定传送设备的原料落下点的范围内;物料由布料器的主体上端投入通过投料锥斗、投料管,由投料管下端的投料口投入到高炉内,而布料器在横向驱动机构、纵向驱动机构的驱动下可将物料按照投料分布需求投送到高炉内的设定部位,并可通过在每个设定部位的设定投料时间控制设定部位的投料量,从而构成3维空间投料布局。
[0028]
优选的技术方案是,所横向驱动机构包括横向驱动螺母,横向驱动螺母的一侧与布料器驱动框架或布料器驱动板连接,横向横驱动螺母的螺孔与横向丝杆螺纹配合,横向丝杠的两端通过轴承、轴承座与横向驱动框架或横向驱动板连接,其中横向丝杆的一端连接有横向驱动电机,横向驱动电机通过基座与横向驱动框架或横向驱动板连接,在横向驱动螺母的另一侧设置有横向导向块,横向导向块与设置在横向驱动框架或横向驱动板上的横向导向槽滑动配合。
[0029]
优选的技术方案还有,所纵向驱动机构包括纵向驱动螺母,纵向驱动螺母的一侧与横向驱动框架或横向驱动板的底部连接,纵向驱动螺母的螺孔与纵向丝杆螺纹配合,纵向丝杠的两端通过轴承、轴承座与支撑架连接,其中纵向丝杆的一端连接有纵向驱动电机,纵向驱动电机通过基座与支撑架连接,在纵向驱动螺母的另一侧设置有纵向导向块,纵向导向块与设置在支撑架上的纵向导向槽滑动配合。
[0030]
优选的技术方案还有,所述横向驱动电机与纵向驱动电机均为伺服电机,每个伺服电机与plc控制器电连接,所述投料管上装有球阀,球阀的一端与球阀开关控制伺服电机连接,球阀开关控制伺服电机与plc控制器电连接,所述支撑架直接支撑在高炉的顶部,或所述支撑架直接支撑在地面,在所述支撑架的底部设置有与plc控制器电连接的摄像头和/或超声波探测仪。
[0031]
本发明的优点和有益效果在于:该使用高比例镁球团高炉炼铁方法具有工艺简单,通过改善球团矿的组分含量和组织结构,加之调整高炉冶炼时的一些技术参数,使得高炉在冶炼球团矿质量含量高达65%以上的矿石时稳定运行,可提高了企业效益等特点。
[0032]
球团矿在入炉总矿石中的质量配加比例已经稳定65%以上,最高可达到75%,解
决了生产中烧结矿原料不足的问题;
[0033]
通过对现有技术中采用低比例球团矿高炉炼铁的工艺进行改进和对球团矿本身性质的制备工艺要求,使得高炉在炼铁过程中的顺行程度逐渐得到改善;
[0034]
炼铁过程中,较现有技术中采用低比例球团矿高炉炼铁的工艺,燃料与矿石的比值从538kg/t下降为目前的530kg/t,降低了8kg/t,降低能耗;
[0035]
较现有技术中采用低比例球团矿高炉炼铁的工艺,冶炼所得的生铁质量提高,平均si含量降低到0.42%,s含量稳定在0.23%。
[0036]
采用高炉上的移动式布料器具有结构简单,便于操作、自动化程度高、投料方位投料量控制精准,可按照任意设定的投料布局结构将物料投入到高炉内等特点。可将不同的物料按照3d打印的方式投到高炉内,这种投料方式彻底改变了现有技术中通过溜槽选装及溜槽俯仰角调节的投料方式。
附图说明
[0037]
图1.1、1.2、1.3是本发明设置在高炉上的移动式布料器的3个位置状态主视剖视结构示意图;
[0038]
图2.1、2.2、2.3是本发明设置在高炉上的移动式布料器的3个位置状态俯视剖视结构示意图;
[0039]
图3.1、3.2是图1中横向驱动机构的主视与俯视结构示意图;
[0040]
图4.1、4.2是图1中纵向驱动机构的主视与俯视结构示意图。
[0041]
图中:1、高炉;2、布料器;3、支撑架;4、纵向驱动机构;4.1、纵向驱动螺母;4.2、纵向丝杠;4.3、纵向驱动框架;4.4、纵向导向块;4.5、纵向导向槽;5、横向驱动机构;5.1、横向驱动螺母;5.2、横向丝杆;5.3、横向驱动框架;5.4、横向驱动电机;5.5、横向导向块;5.6、横向导向槽;6、投料锥斗;7、投料管;8、原料固定传送设备;9、plc控制器;10、球阀;11、球阀开关控制伺服电机;12、摄像头。
具体实施方式
[0042]
下面结合实施例,对本发明的具体实施方式作进一步描述。以下实施例仅用于更加清楚地说明本发明的技术方案,而不能以此来限制本发明的保护范围。
[0043]
实施例1
[0044]
本发明是一种高比例镁球团高炉炼铁方法,包括以下步骤:
[0045]
第一步,冶炼镁球团:将烧结矿、含氟熔剂、焦炭、矿料装入受料槽,而后通过控制受料槽上自动振动筛按照设定的程序对四种物料按配比及设定的投料布局进行投料;
[0046]
第二步,各种物料均按设定配比放置在传送设备上,而后运上高炉顶部的受料器内,将每批料通过炉顶布料器按照自动布料程序装入高炉,并将热风从风口按照送风制度鼓入高炉;
[0047]
第三步,将第一步所得镁球团为65%的矿石及铁矿石、焦炭放入高炉,布料、低硅冶炼,得生铁;布料时,外环矿石的α角为18
°
,内环矿石的α角为20
°
,焦碳与矿石的质量配比0.3;低硅冶炼时,高炉的风口面积为0.12m
2
,风口长度为250mm,风口向下倾斜角度为3
°
。
[0048]
其中镁球团矿的生产方法,包括如下步骤:
[0049]
s1、配料工序:将以下质量分数的原料进行混合:精粉25.7%,卡拉拉粉70%,镁粉1.8%,皂土2.5%;
[0050]
s2、烘干、润磨工序:将s1中的原料进行烘干,烘干温度控制在850
±
50℃,经过润磨机润磨的原料粒度要求-200目≥80%,确保原料的润磨效果;
[0051]
s3、造球工序:将s2中的原料进行圆盘造球机造球,生球水分控制8.5-9.5%,粒度15-20mm≥90%,生球每米落下强度不低于5次;
[0052]
s4、热工参数控制:将s3中的生球均匀的布在竖炉的烘干床上,竖炉的烘干床温度控制在500
±
50℃,燃烧室温度控制在1060
±
20℃,烟罩温度控制在90-120℃。
[0053]
本发明优选的实施方案是,将所述热风送风控制在:风量为38003/min,鼓风动能为12000,炉顶压力为0.150mpa,透气性指数2.10-2.30,热风温度为1200
±
3.0℃,富氧率为1.2%%,炉腹燃气指数51.5,炉顶高温为300℃,炉顶低温为210℃℃,理论燃烧温度2320℃;
[0054]
高炉的热制度及造渣制度分别为:热制度控制要求:铁水温度≥1525℃,[si]含量≤0.630%,[p]含量≤0.030%;造渣制度控制要求:全碱度为1.20
±
0.30,自由碱度为1.03
±
0.06,二元碱度0.82
±
0.03,al
2
o
3
含量≤14.0%,mgo含量≥10.2%;
[0055]
本发明优选的实施方案还有,其中所述物料的按重量份计包括烧结矿和镁球团50份,焦炭10.2份,矽石,0.3份;其中所述烧结矿与镁球团的重量比为70:20;
[0056]
本发明优选的实施方案还有,所述镁球团质量控制要求:tfe≥68.5%,feo含量<0.8%,s含量<0.13%,mgo含量≥3.0%,sio
2
含量≤2.5,na
2
o与k
2
o的总含量小于0.05%、zno<0.08%,f含量≤0.45%,ro≥0.85,抗压强度≥2450n/p,转鼓强度≥89%,抗磨指数≤2.6%。
[0057]
本发明优选的实施方案还有,所述第一部中焙烧所得的球团矿中,强度低于1000n的球团矿质量含量低于10%。
[0058]
本发明优选的实施方案还有,所述低硅高镁含氟熔剂性球团的配料时通过添加高镁粉、高镁矿或炼钢污泥中一种或几种调控原料中mgo含量。
[0059]
实施例3
[0060]
一种高比例镁球团高炉炼铁方法,包括以下步骤:
[0061]
第一步,冶炼镁球团:将烧结矿、含氟熔剂、焦炭、矿料装入受料槽,而后通过控制受料槽上自动振动筛按照设定的程序对四种物料按配比及设定的投料布局进行投料;
[0062]
第二步,各种物料均按设定配比放置在传送设备上,而后运上高炉顶部的受料器内,将每批料通过炉顶布料器按照自动布料程序装入高炉,并将热风从风口按照送风制度鼓入高炉;
[0063]
第三步,将第一步所得镁球团为75%的矿石及铁矿石、焦炭放入高炉,布料、低硅冶炼,得生铁;布料时,外环矿石的α角为24
°
,内环矿石的α角为24
°
,焦碳与矿石的质量配比0.5%;低硅冶炼时,高炉的风口面积为0.13m
2
,风口长度为380mm,风口向下倾斜角度为5
°
。
[0064]
其中镁球团矿的生产方法,包括如下步骤:
[0065]
s1、配料工序:将以下质量分数的原料进行混合:精粉35.7%,卡拉拉粉60%,镁粉1.8%,皂土2.5%;
[0066]
s2、烘干、润磨工序:将s1中的原料进行烘干,烘干温度控制在850
±
50℃,经过润
磨机润磨的原料粒度要求-200目≥80%,确保原料的润磨效果;
[0067]
s3、造球工序:将s2中的原料进行圆盘造球机造球,生球水分控制8.5-9.5%,粒度15-20mm≥90%,生球每米落下强度不低于5次;
[0068]
s4、热工参数控制:将s3中的生球均匀的布在竖炉的烘干床上,竖炉的烘干床温度控制在500
±
50℃,燃烧室温度控制在1060
±
20℃,烟罩温度控制在90-120℃。
[0069]
本发明优选的实施方案是,将所述热风送风控制在:风量为4200m
3
/min,鼓风动能为14000,炉顶压力为0.185mpa,透气性指数2.30,热风温度为1200
±
3.0℃,富氧率为1.5%,炉腹燃气指数60.5,炉顶高温为320℃,炉顶低温为220℃,理论燃烧温度2520℃;
[0070]
高炉的热制度及造渣制度分别为:热制度控制要求:铁水温度≥1525℃,[si]含量≤0.630%,[p]含量≤0.030%;造渣制度控制要求:全碱度为1.20
±
0.30,自由碱度为1.03
±
0.06,二元碱度0.82
±
0.03,al
2
o
3
含量≤14.0%,mgo含量≥10.2%;
[0071]
本发明优选的实施方案还有,其中所述物料的按重量份计包括烧结矿和镁球团50份,焦炭10.5份;其中所述烧结矿与镁球团的重量比为58:20;
[0072]
本发明优选的实施方案还有,所述镁球团质量控制要求:tfe≥68.5%,feo含量<0.8%,s含量<0.13%,mgo含量≥3.0%,sio
2
含量≤2.5,na
2
o与k
2
o的总含量小于0.05%、zno<0.08%,f含量≤0.45%,ro≥0.85,抗压强度≥2450n/p,转鼓强度≥89%,抗磨指数≤2.6%。
[0073]
本发明优选的实施方案还有,所述第一部中焙烧所得的球团矿中,强度低于1000n的球团矿质量含量低于10%。
[0074]
优选的技术方案还有,所述低硅高镁含氟熔剂性球团的配料时通过添加高镁粉、高镁矿或炼钢污泥中一种或几种调控原料中mgo含量。
[0075]
实施例3
[0076]
一种高比例镁球团高炉炼铁方法,包括以下步骤:
[0077]
第一步,冶炼镁球团:将烧结矿、含氟熔剂、焦炭、矿料装入受料槽,而后通过控制受料槽上自动振动筛按照设定的程序对四种物料按配比及设定的投料布局进行投料;
[0078]
第二步,各种物料均按设定配比放置在传送设备上,而后运上高炉顶部的受料器内,将每批料通过炉顶布料器按照自动布料程序装入高炉,并将热风从风口按照送风制度鼓入高炉;
[0079]
第三步,将第一步所得镁球团为70%的矿石及铁矿石、焦炭放入高炉,布料、低硅冶炼,得生铁;布料时,外环矿石的α角为21
°
,内环矿石的α角为22
°
,焦碳与矿石的质量配比0.4%;低硅冶炼时,高炉的风口面积为0.125m
2
,风口长度为265mm,风口向下倾斜角度为4
°
。
[0080]
其中镁球团矿的生产方法,包括如下步骤:
[0081]
s1、配料工序:将以下质量分数的原料进行混合:精粉15.8%,卡拉拉粉80%,镁粉1.8%,皂土2.4%;
[0082]
s2、烘干、润磨工序:将s1中的原料进行烘干,烘干温度控制在850
±
50℃,经过润磨机润磨的原料粒度要求-200目≥80%,确保原料的润磨效果;
[0083]
s3、造球工序:将s2中的原料进行圆盘造球机造球,生球水分控制8.5-9.5%,粒度15-20mm≥90%,生球每米落下强度不低于5次;
[0084]
s4、热工参数控制:将s3中的生球均匀的布在竖炉的烘干床上,竖炉的烘干床温度控制在500
±
50℃,燃烧室温度控制在1060
±
20℃,烟罩温度控制在90-120℃。
[0085]
经检验,本发明以上3个实施例与现有技术中球团矿的各项数据如表1所示:
[0086]
表1本发明实施例与现有技术的球团矿数据对比
[0087]
实施例序号球团矿转鼓指数氧化镁含量现有技术88%0.75实施例193.07%1.61实施例293.29%1.58实施例393.15%1.65
[0088]
由表1可以看出,本发明的球团矿转鼓指数提高显著,球团矿氧化镁含量明显升高,有利于高炉的强化冶炼。
[0089]
本发明优选的实施方案是,将所述热风送风控制在:风量为4000m
3
/min,鼓风动能为13000,炉顶压力为0.170mpa,透气性指数2.20,热风温度为1200
±
3.0℃,富氧率为1.35%,炉腹燃气指数55.5,炉顶高温为310℃,炉顶低温为215℃,理论燃烧温度2420℃;
[0090]
高炉的热制度及造渣制度分别为:热制度控制要求:铁水温度≥1525℃,[si]含量≤0.630%,[p]含量≤0.030%;造渣制度控制要求:全碱度为1.20
±
0.30,自由碱度为1.03
±
0.06,二元碱度0.82
±
0.03,al
2
o
3
含量≤14.0%,mgo含量≥10.2%;
[0091]
本发明优选的实施方案还有,其中所述物料的按重量份计包括烧结矿和镁球团50份,焦炭10.3份,矽石,0.15份;其中所述烧结矿与镁球团的重量比为64:24;
[0092]
本发明优选的实施方案还有,所述镁球团质量控制要求:tfe≥68.5%,feo含量<0.8%,s含量<0.13%,mgo含量≥3.0%,sio
2
含量≤2.5,na
2
o与k
2
o的总含量小于0.05%、zno<0.08%,f含量≤0.45%,ro≥0.85,抗压强度≥2450n/p,转鼓强度≥89%,抗磨指数≤2.6%。
[0093]
本发明优选的实施方案还有,所述第一部中焙烧所得的球团矿中,强度低于1000n的球团矿质量含量低于10%。
[0094]
本发明优选的实施方案还有,所述低硅高镁含氟熔剂性球团的配料时通过添加高镁粉、高镁矿或炼钢污泥中一种或几种调控原料中mgo含量。
[0095]
实施例4
[0096]
本发明的技术方案还提供了一种设置在高炉1上的移动式布料器2,包括架设在高炉1顶部的支撑架3,支撑架3上设有纵向驱动机构4,在纵向驱动机构4的驱动部件上通过横向驱动框架或横向驱动板设置有横向驱动机构5,在横向驱动机构5的驱动部件上通过布料器驱动框架或布料器驱动板设置有布料器2,布料器2的主体内设有由上向下的投料锥斗6,投料斗6的下端口与投料管7的一端连接,投料管7的另一端通向高炉1的上端口,投料斗6的上端口的形状及大小应满足布料器移动到任意极限位置,投料斗6的上端口都在原料固定传送设备8的原料落下点的范围内;物料由布料器2的主体上端投入通过投料锥斗6、投料管7,由投料管7下端的投料口投入到高炉1内,而布料器2在横向驱动机构5、纵向驱动机构4的驱动下可将物料按照投料分布需求投送到高炉1内的设定部位,并可通过在每个设定部位的设定投料时间控制设定部位的投料量,从而构成3d打印式的投料布局。
[0097]
为了便于将不同的物料按照投料布局的需要分别或同时投入到高炉内,同时也为
了提高投料的效率,本发明优选的实施方案是,在所述布料器2的上端设置有2-3台原料固定传送设备8,分别用于向高炉内投送烧结矿、球团矿和溶剂。
[0098]
为了确保布料器2的投料口能够沿横向方向(x方向)灵活移动,同时又能简化驱动机构,还能将投料管7的投料口固定在框架或板面上,使其不能任意摆动,本发明进一步优选的实施方案还有,所横向驱动机构5包括横向驱动螺母5.1,横向驱动螺母5.1的一侧与布料器驱动框架连接,横向横驱动螺母5.1的螺孔与横向丝杆5.2螺纹配合,横向丝杠5.2的两端通过轴承、轴承座与横向驱动框架5.3连接,其中横向丝杆5.2的一端连接有横向驱动电机5.4,横向驱动电机5.4通过基座与横向驱动框架5.3连接,在横向驱动螺母5.1的另一侧设置有横向导向块5.5,横向导向块5.5与设置在横向驱动框架5.3上的横向导向槽5.6滑动配合。
[0099]
为了确保布料器2能够沿纵向方向(y方向)灵活移动,同时又能简化驱动机构,还能将横向驱动框架5.3固定在纵向驱动部件上,使其移动平稳,本发明进一步优选的实施方案还有,所纵向驱动机构4包括纵向驱动螺母4.1,纵向驱动螺母4.1的一侧与横向驱动框架5.3的底部连接,纵向驱动螺母4.1的螺孔与纵向丝杆4.2螺纹配合,纵向丝杠4.2的两端通过轴承、轴承座与支撑架3连接,其中纵向丝杆4.2的一端连接有纵向驱动电机4.3,纵向驱动电机4.3通过基座与支撑架3连接,在纵向驱动螺母4.1的另一侧设置有纵向导向块4.4,纵向导向块3与设置在支撑架上的纵向导向槽4.5滑动配合。
[0100]
由于布料器3、投料管7、横向驱动机构5、纵向驱动机构4的尺寸及重量都较大,为了确保各驱动机构及投料管7的安全平稳运行,本发明进一步优选的实施方案还有,所述横向驱动机构5、纵向驱动机构4分别对称的设有两套。
[0101]
为了便于控制布料器2的位置移动灵活快捷,而且便于控制投料口的移动速度或停留时间,本发明进一步优选的实施方案还有,所述横向驱动电机5.4与纵向驱动电机4.3均为伺服电机,每个伺服电机与plc控制器9电连接。
[0102]
为了便于控制投料口开始投料时间和停止投料时间,本发明进一步优选的实施方案还有,所述投料管7上装有球阀10,球阀10的一端与球阀开关控制伺服电机11连接,球阀开关控制伺服电机11与plc控制器9电连接。
[0103]
为了减轻布料器2的支撑架3、横向驱动机构5和纵向驱动机构4的整体重量,同时使其具有良好的耐高温、耐腐蚀性能,本发明进一步优选的实施方案还有,所述支撑架3、横向驱动框架5.3用碳纤维制成,或在支撑架3、横向驱动框架5.3的表面附着有碳纤维层。
[0104]
为了便于缩小支撑架3的整体结构尺寸,并能将支撑架3牢固地固定在高炉1的顶部,本发明进一步优选的实施方案还有,所述支撑架3直接支撑在高炉1的顶部,或所述支撑架3直接支撑在地面上。
[0105]
为了便于随时监测炉料添加到高炉1内部的情况,以便于随时调整添加方案,本发明进一步优选的实施方案还有,在所述支撑架3的底部设置有与plc控制器9电连接的摄像头12和/或超声波探测仪。
[0106]
以上所述仅是本发明的优选实施方式,应当指出,对于本技术领域的普通技术人员来说,在不脱离本发明技术原理的前提下,还可以做出若干改进和润饰,这些改进和润饰也应视为本发明的保护范围。
起点商标作为专业知识产权交易平台,可以帮助大家解决很多问题,如果大家想要了解更多知产交易信息请点击 【在线咨询】或添加微信 【19522093243】与客服一对一沟通,为大家解决相关问题。
此文章来源于网络,如有侵权,请联系删除



tips