一种钢包用引流砂及加砂方法与流程



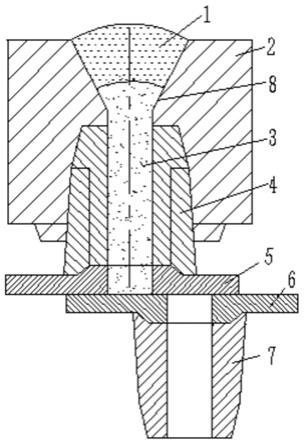
[0001]
本发明涉及钢铁冶金技术领域,特别是在常规钢种的精炼和连铸工序中的钢包用引流砂及加砂方法。
背景技术:
[0002]
钢包引流砂是填充于钢包水口的一种引流物质。钢包承接钢液之前,通过加砂装置向钢包水口加入引流砂;加入钢液后,与钢液直接接触的上层引流砂在高温下烧结,形成一定厚度的烧结层,下层的引流砂仍然呈颗粒状。精炼结束后,钢包运送至连铸工位,打开滑板浇注时,下层的引流砂自动流出;由于下方没有支撑,与钢液接触的烧结层在钢液的静压力作用下被压破,钢液便自动从钢包水口中流出。浇注时钢液自动流出称之为自动开浇;钢包自动开浇的次数与钢包浇注的总次数之比为钢包自动开浇率。钢包如果无法自动开浇,就需要进行烧氧处理。钢包烧氧操作不仅危险,而且严重影响钢液的洁净度,有时甚至会使连铸断浇,严重打乱生产节奏。
[0003]
钢包自动开浇率受很多方面的影响,如:精炼时间、温度,引流砂的性质及钢液中合金元素的含量等。其中需要引流砂在较低的温度下烧结,同时要求形成的烧结层不能过厚,否则影响自动开浇率。目前普遍使用的有铬质、硅质和镁质引流砂,其中铬质引流砂对于常规钢种的引流效果明显,钢包的自动开浇率高,因此被广泛使用,但其价格相对较高,不利于降低企业的吨钢成本。因此选择合适的引流砂使其既能保证钢包的自动开浇率,又能降低生产成本,成为生产过程中亟待解决的问题。
技术实现要素:
[0004]
本发明所要解决的技术问题是克服已有技术之缺陷,提供一种钢包用引流砂及加砂方法,引流砂分为上下两层,上层为铬质引流砂、下层采用河砂或石英砂,在保证常规钢种自动开浇率的前提下,降低精炼过程的生产成本。
[0005]
本发明所述技术问题是以下述技术方案实现的:一种钢包用引流砂,所述引流砂填充在钢包底部水口内,所述钢包底部水口包括钢包水口座砖、上水口和下水口,上水口外部包裹有钢包水口座砖,钢包水口座砖上开有座砖孔,座砖孔下部为圆形通孔,圆形通孔与上水口相连通,座砖孔上部为上大下小的圆锥台形孔;所述引流砂包括上引流砂层和下引流砂层,上引流砂层位于下引流砂层的上部;上引流砂层为铬质引流砂,下引流砂层为硅质引流砂,硅质引流砂包括河砂或石英砂,硅质引流砂重量占引流砂总重量的70%~85%。上述钢包用引流砂,所述上水口和座砖孔下部填充硅质引流砂,成为下引流砂层,下引流砂层的上缘距离钢包水口座砖的顶部5~10cm;下引流砂层上面填充铬质引流砂,在座砖孔外自然堆积成球冠状,形成上引流砂层。
[0006]
上述钢包用引流砂,所述硅质引流砂的砂粒度范围为0.1~1.5mm,其粒径分布为0.1~0.5mm的颗粒占硅质引流砂颗粒10~35%,粒径0.5~1.0mm的颗粒占35~65%,粒径1.0~
1.5mm的颗粒占10~30%。
[0007]
上述钢包用引流砂,所述铬质引流砂包括按重量百分比计的cr
2
o
3 28%~45%、al
2
o
3 6%~18%、sio
2 15%~35%、fe
2
o
3 15%~35%、mgo 3%~12%;铬质引流砂的砂粒度范围为0.1~1.5mm。上述钢包用引流砂,所述铬质引流砂包括按重量百分比计的cr
2
o
3 30%~45%、al
2
o
3 10%~18%、sio
2 20%~25%、fe
2
o
3 15%~20%、mgo 3%~12%。
[0008]
一种上述钢包用引流砂的加砂方法,包括如下步骤:a. 清理钢包底部水口;b. 使用加砂装置从钢包上方装入硅质引流砂,使硅质引流砂的上缘距钢包水口座砖顶部5~10cm;c. 使用加砂装置从钢包上方装入铬质引流砂,填满钢包水口,且在座砖孔外的部分呈自然堆积的球冠状;d. 向钢包注入钢液,铬质引流砂与钢液接触形成烧结层;浇注时上水口与下水口连通,下层的硅质引流砂和上层的部分铬质引流砂从钢包下水口流出;钢液在重力的作用下冲破烧结层,实现自动开浇。
[0009]
上述钢包用引流砂的加砂方法,所述加砂装置为长颈漏斗。
[0010]
本发明使用的引流砂分为上下两层,上层为铬质引流砂,可以保持常规钢种生产过程中的钢包自动开浇率;下层用硅质引流砂,由于硅质引流砂占总引流砂重量的四分之三左右,且铬质引流砂的成本是河砂和石英砂的8~10倍,因此精炼过程的生产成本明显降低。
[0011]
上层引流砂和钢液接触,在烧结作用下形成烧结层,下层的引流砂只起到支撑烧结层的作用,因此下层如同样采用铬质引流砂明显浪费。本发明在下层采用河砂或石英砂的硅质引流砂代替铬质引流砂,不仅有效降低成本,而且可以保持钢包自开动开浇率大于95%,有效保证精炼钢水的质量和连铸工艺的安全顺利进行。相较于全部采用普通引流砂大幅降低烧氧的频次,提高生产效率,减少钢水污染,同时降低烧氧操作的生产风险,提高生产安全系数。
附图说明
[0012]
图1是本发明的钢包底部水口中引流砂填充结构的纵剖面示意图;图2是本发明钢包浇注时下层的引流砂流出后的剖面示意图。
[0013]
图中各标号清单为:1、上引流砂层,2、钢包水口座砖,3、下引流砂层,4、上水口,5、上滑板,6、下滑板,7、下水口,8、座砖孔。
具体实施方式
[0014]
下面结合附图和实施例对本发明作进一步详细说明。本发明用于填充底部水口的引流砂包括上引流砂层1和下引流砂层3,上引流砂层1位于下引流砂层3的上部。所述上引流砂层为铬质引流砂,其成分包括按重量百分比计的cr
2
o
3 28%~45%、al
2
o
3 6%~18%、sio
2 15%~35%、fe
2
o
3 15%~35%、mgo 3%~12%;各成分优选含量为cr
2
o
3 30%~45%、al
2
o
3 10%~18%、sio
2 20%~25%、fe
2
o
3 15%~20%、mgo 3%~12%。铬质引流砂的
砂粒度范围为0.1~1.5mm,粒径分布为0.1~0.4mm的颗粒占铬质引流砂颗粒的10~30%,粒径0.4~0.8mm的颗粒占35~75%,粒径0.8~1.5mm的颗粒占15~35%。粗、中、细颗粒的粒度分布适宜,可以避免粒度过细导致烧结层厚,影响自动开浇。砂的耐火温度不小于1600℃;砂的水分小于0.05%。
[0015]
下引流砂层为硅质引流砂,硅质引流砂包括河砂或石英砂,硅质引流砂的砂粒度范围为0.1~1.5mm,其粒径分布为0.1~0.5mm的颗粒占硅质引流砂颗粒10~35%,粒径0.5~1.0mm的颗粒占35~65%,粒径1.0~1.5mm的颗粒占10~30%。上述颗粒分布在具有透气性的同时,使下引流砂层结构致密,有效支撑上引流砂层。砂的耐火温度不小于1500℃;砂的水分小于0.05%。下引流砂层的重量占引流砂总重量的70%~85%。
[0016]
如图1所示,钢包底部水口包括钢包水口座砖2、上水口4和下水口7,所述上水口4和下水口7通过滑板机构对接,上水口4外部包裹钢包水口座砖2。钢包水口座砖2上开有座砖孔8,所述上水口与座砖孔的位置相对应。座砖孔分为上下两部分,下部为圆形通孔,圆形通孔与钢包的上水口相连通且内径相同;上部为上大下小的圆锥台形孔。锥台形的锥角为40
°-
60
°
。
[0017]
在上水口4和座砖孔8的中下部(即座砖孔的圆形通孔和圆锥台形孔的下部)填充硅质引流砂,形成下引流砂层3,下引流砂层的上缘距离钢包水口座砖的顶部为5~10cm。座砖孔的上部(即圆锥台形孔的中上部)填充铬质引流砂,形成上引流砂层1;铬质引流砂在座砖孔外的部分为自然堆积形成的球冠状结构。
[0018]
所述滑板机构包括相互配合的上滑板5和下滑板6,上水口4底部固定有上滑板5,下水口7的顶部固定下滑板6,上滑板和下滑板之间可相互滑动,通过推动下滑板6可使上水口4和下水口7相互连通或阻断。
[0019]
以下对本发明的工作过程做进一步说明:常规钢种的引流砂的加砂方法和使用步骤为:1)清理钢包底部水口:钢包浇铸完成后,对钢包进行检查和维修,通过烧氧的方式将水口的残渣和冷钢清理干净。
[0020]
2)使用加砂装置从钢包上方装入硅质引流砂,硅质引流砂的加入量为总重量的70~85%,并使下引流砂层的上缘距钢包水口座砖顶部5~10cm,所述加砂装置为长颈漏斗。
[0021]
3)硅质引流砂装填完毕,再装入铬质引流砂,使钢包水口填满且上部呈球冠状,加入铬质引流砂的质量为总重量的15~30%。
[0022]
4)向钢包注入钢液进行炉外精炼。上层的铬质引流砂与钢水接触,表面受高温作用迅速形成烧结层,阻止钢水持续渗入到下引流砂层。精炼结束后,钢包运送至连铸工位进行浇注,如图2所示,移动下滑板6至上滑板5处,上水口与下水口成连通状态,下层的引流砂和部分上层的引流砂从钢包的下水口流出。钢水在重力的作用下冲破烧结层,实现自动开浇。
[0023]
实施例1应用120吨钢包生产q195的工艺流程。
[0024]
在精炼工序,转炉出钢之前,将钢包烘烤至使用温度,水口清理干净之后,从钢包上部向钢包水口中添加石英砂,石英砂占引流砂总重量的85%。所述石英砂的各粒度的占比为:粒径0.1~0.5mm的颗粒占20%,粒径0.5~1.0mm的颗粒占60%,粒径1.0~1.5mm的颗粒占
20%。砂的耐火度1580℃,水分0.03%。后向座砖孔中添加铬质引流砂,填满钢包水口,并使顶部呈球冠状。所述铬质引流砂的成分为:cr
2
o
3
=40%;al
2
o
3
=15%;sio
2
=25%;fe
2
o
3
=15%;mgo=5%。砂的各粒度的占比为:粒径在0.1~0.4mm范围的颗粒占20%,粒径在0.4~0.8mm范围的颗粒占55%,粒径在0.8~1.5mm范围的颗粒占25%。水分0.05%。
[0025]
引流砂填充完毕,纵剖面如图1所示,以下实施例均采用实施例1的引流砂填充方式。钢包承接转炉出来的钢液,钢液注入进行精炼。浇注时移动下滑板,石英砂流出,钢液冲破上引流砂层,实现自动开浇。
[0026]
实施例2应用80吨钢包生产q235的工艺流程。
[0027]
精炼工序,转炉出钢之前,将钢包烘烤至使用温度,水口清理干净之后,从钢包上部向钢包水口中添加引流砂总重量80%的河砂,所述河砂各粒度的占比为:粒径在0.1~0.5mm范围的颗粒占25%,粒径在0.5~1.0mm范围的颗粒占55%,粒径在1.0~1.5mm范围的颗粒占20%。砂的耐火度1500℃ ,水分0.05%。再向水口中添加铬质引流砂,填满水口,并使顶部呈球冠状。所述铬质引流砂的成分为:cr
2
o
3
=45%;al
2
o
3
=12%;sio
2
=20%;fe
2
o
3
=15%;mgo=8%。砂粒中各粒度的占比为:粒径在0.1~0.4mm范围的颗粒占25%,粒径在0.4~0.8mm范围的颗粒占60%,粒径在0.8~1.5mm范围的颗粒占15%。水分0.04%。
[0028]
引流砂填充完毕,钢包承接转炉出来的钢液,精炼完成后移动下滑板,石英砂流出,钢液冲破上引流砂层,实现自动开浇。
[0029]
实施例3应用120吨钢包生产40号钢的工艺流程。
[0030]
在精炼工序,转炉出钢之前,将钢包烘烤至使用温度,水口清理干净之后,从钢包上部向水口内添加石英砂。首先向钢包水口中添加引流砂总重量75%的石英砂,所述石英砂的粒度为0.1~1.5mm,其中粒径在0.1~0.5mm范围的颗粒占30%,粒径在0.5~1.0mm范围的颗粒占55%,粒径在1.0~1.5mm范围的颗粒占15%。砂耐火度1600℃,水分0.02%。再向水口中添加铬质引流砂,填满水口,并使顶部呈球冠状。所述铬质引流砂的成分为:cr
2
o
3
=30%;al
2
o
3
=15%;sio
2
=23%;fe
2
o
3
=20%;mgo=12%。砂粒度为0.1~1.5mm,其中粒径在0.1~0.4mm范围的颗粒占25%,粒径在0.4~0.8mm范围的颗粒占50%,粒径在0.8~1.5mm范围的颗粒占25%。水分0.02%。
[0031]
引流砂填充完毕,钢包承接转炉出来的钢液,精炼完成后移动下滑板,石英砂流出,钢液冲破上引流砂层,实现自动开浇。
[0032]
根据说明书的指导,本发明所述领域的技术人员还可以对上述实施方式进行适当的变更和修改,不限于上述的具体实施方式。凡采用同等替换或有效变形形成的技术方案,均落在本发明权利要求的保护范围内。
起点商标作为专业知识产权交易平台,可以帮助大家解决很多问题,如果大家想要了解更多知产交易信息请点击 【在线咨询】或添加微信 【19522093243】与客服一对一沟通,为大家解决相关问题。
此文章来源于网络,如有侵权,请联系删除
相关标签:



tips