一种有机硅浆渣水解渣及废触体资源化利用的方法与流程



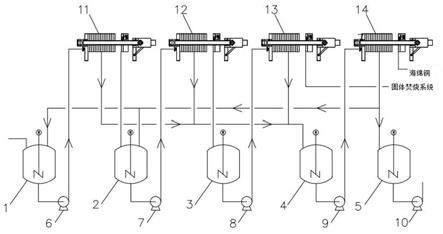
[0001]
本发明属于有机硅废渣利用的技术领域,具体是涉及一种有机硅浆渣水解渣及废触体资源化利用的方法。
背景技术:
[0002]
有机氯硅烷生产过程中会产生废触体,主要为流化床反应器中反应失活的硅铜触体和气固分离系统连续排出的表面污染严重的细粉。因废触体中含有大量的硅、铜,触体的平均粒径较细并且铜粉的活性较高,暴露在空气中容易引起氧化甚至燃烧。目前,对该类废触体的处理通常采用堆埋方式,这不仅需要大量的堆埋场而且对于可回收利用的硅和铜将是大量的浪费,另外对环境造成了严重的污染并存在严重的安全隐患;在合成氯硅烷过程中会产生一些沸点较高成分极其复杂的氯硅烷液态物质,这些物质会夹带部分催化剂粉末形成一种黑色的油状物质被排除反应体系,这就是浆渣。由于浆渣是一种易燃、易水解、有强烈刺激性的物质所以浆渣必须就近处理,目前浆渣的处理手段主要是水解,即浆渣水解,使其中的氯硅烷与水反应生成一种黑色的固体粉末以便作进一步的处理,这种水解后的固体粉末就是浆渣水解废渣。
[0003]
废触体及浆渣水解渣中的硅粉和铜回收后都可以作为原料使用,铜属于重金属,若不进行回收利用,将造成严重的环境污染,不利于环保。
[0004]
专利cn101391775公开了一种有机氯硅烷生产中的废触体合成三氯氢硅的方法,其中提到利用废触体制备三氯氢硅,由于废触体中含有大量的铜及少量的锌等杂质,无法制备高纯度的三氯氢硅。
技术实现要素:
[0005]
为了解决上述技术问题,本发明提供一种有机硅浆渣水解渣及废触体资源化利用方法,能够有效处理有机硅浆渣。
[0006]
具体技术方案为:一种有机硅浆渣水解渣及废触体资源化利用的方法,包括以下步骤:(1)浆渣水解渣及废触体投入酸侵槽a中,加入5-10%(浓度)盐酸溶液,投入氯酸钠,在搅拌机的搅拌下使废渣中的铜充分接触酸侵液,反应停留时间为2-5小时; (2)酸侵槽a中的固液混合物通过酸侵槽a输送泵送入压滤机a进行固液分离,滤液进入还原槽,滤渣进入酸侵槽b; (3)酸侵槽b中加入5-10%(浓度)盐酸溶液,投入氯酸钠,在搅拌机的搅拌下使废渣中的铜充分接触酸侵液,反应停留时间为2-4小时;(4)酸侵槽b中的固液混合物通过酸侵槽b输送泵送入压滤机b进行固液分离,滤液进入还原槽,滤渣进入洗涤槽,经两次酸浸及洗涤后后硅粉中铜含量低于0.15%;(5)经洗涤槽洗涤后通过洗涤槽输送泵送入压滤机进行过夜分离,滤液进入还原槽,滤渣送固废焚烧系统焚烧处理;(6)检测还原槽中的铜含量,在还原槽中加入铁粉,铁粉与铜的比例1.2-1.5:1,铁粉与cucl
2
溶液发生化学反应,将铜置换出来,得到铜和fecl
2
溶液; (7)通过还原槽输送泵将混
合液送入压滤机c进行固液分离,得到的固体为铜含量大于50%的海绵铜产品,滤液进入中和沉淀槽;(8)中和沉淀槽中加入naoh,fecl
2
溶液与naoh中和沉淀得到铁渣,铁渣可作为炼钢原料,清液送至污水处理站处理。中和沉淀槽中如何得到铁渣的; 氢氧化钠与氯化铁反应生成氢氧化铁沉淀。
[0007]
进一步,经酸侵及二次洗涤后的固渣含铜量小于浸出毒性鉴别标准规定的100mg/l。
[0008]
进一步,所述浆渣水解渣与废触体的混合比例为2~5:1。氯酸钠投入量为以浆渣水解渣及废触体干渣计,投入氯酸钠30~60千克/吨。
[0009]
一种有机硅浆渣水解渣及废触体资源化利用系统,包括酸侵槽a,酸侵槽a上设置有加料口,用于加入浆渣和酸,酸侵槽a底部设置有酸侵液a出口,酸侵液a出口通过酸侵槽a输送泵与压滤机a连接,压滤机a滤液与还原槽连接,压滤机a滤渣与酸侵槽b连接;酸侵槽b上设置有加料口,用于加入酸,酸侵槽b底部设置有酸侵液b出口,酸侵液b出口通过酸侵槽b输送泵与压滤机b连接,压滤机b滤液与还原槽连接,压滤机b滤渣与洗涤槽连接;洗涤槽上设置有加料口,用于加入洗涤液(水),洗涤槽底部设置有洗涤液出口,洗涤液出口通过洗涤槽输送泵与压滤机c连接,压滤机c滤液与还原槽连接,压滤机c滤渣与外接固废焚烧系统连接;还原槽上设置有加料口,用于加入铁粉,还原槽底部设置有还原槽液出口,还原槽液出口通过还原槽输送泵与压滤机d连接,压滤机d滤液与中和沉淀槽连接,压滤机d滤渣为海绵铜;中和沉淀槽上设置有加料口,用于加入naoh溶液,中和沉淀槽底部设置有中和沉淀槽液出口,中和沉淀槽液出口通过中和沉淀槽输送泵后收集;酸侵槽a、酸侵槽b、洗涤槽、还原槽、中和沉淀槽上均设置有搅拌装置,所述搅拌装置包括搅拌轴、搅拌叶片和电机,搅拌轴伸入槽体内设置有搅拌叶片,搅拌轴上端设置有电机。
[0010]
有益效果:1.使用盐酸加氯酸钠的方式溶解单质铜。
[0011]
2.选择两次酸浸是盐酸的容易挥发对设备的密封要求较高。两次酸浸可以更好的浸出铜,主要是采用利用有机硅生产中的废盐酸,使用高浓度盐酸挥发性较强,所有生产设备都要又较高的密封要求,压滤机设备达不到密封要求,浓度太低的盐酸浸出效果不好,不能很好的浸出铜。
[0012]
3.就地取材,利用浆渣水解产生盐酸,效率高成本低。4.使用盐酸酸浸相较于硫酸酸浸减少了废水的复杂性,有机硅生产主要是盐酸废水,采用硫酸酸浸需外购硫酸以及产生硫酸废水。5.生产海绵铜产品,提铜后硅粉外售,增加经济效益。6.将危废变为资源,减少环境危害。
[0013]
经毒性浸出实验后,浸出液中铜含量在3.25-33.6mg/l,小于100mg/l的危废最低标准,固渣可不作为危废认定。
[0014]
本方法采用盐酸作为酸侵液,采用二次酸侵的方式,酸侵槽一、酸侵槽二中加入酸侵液,在添加剂的作用下促使浆渣水解渣与废触体中的铜与盐酸反应生成cucl
2
溶液,混合
液经固液分离后含cucl
2
的滤液进入还原槽,固体则进入洗涤槽进行洗涤,洗涤槽内的固液混合物再经压滤机进行固液分离,滤液进入还原槽,滤渣送至固废焚烧系统焚烧处理。在还原槽中加入铁粉及其他催化剂,使cucl
2
溶液中的铜还原出来,经过滤后等到海绵铜,滤液进入中和沉淀槽沉淀得到铁泥。本发明解决了有机硅浆渣及水解渣含铜作为危险废物的处理难题,并且将废渣中有用的铜提取出来,实现了废物的资源化利用。
附图说明
[0015]
图1为本发明的设备联系图。
[0016]
其中,1酸侵槽a,2为酸侵槽b,3洗涤槽,4还原槽,5为中和沉淀槽,6为酸侵槽a输送泵,7为酸侵槽b输送泵,8为洗涤槽输送泵,9为还原槽输送泵,10为中和沉淀槽输送泵,11为压滤机a,12为压滤机b,13为压滤机c,14为压滤机d。
具体实施方式
[0017]
下面结合具体实施例对本发明作进一步的说明,但本发明的保护范围并不限于此。
[0018]
如图1所示的一种有机硅浆渣水解渣及废触体资源化利用系统,包括酸侵槽a1,酸侵槽a1上设置有加料口,用于加入浆渣和酸,酸侵槽a1底部设置有酸侵液a出口,酸侵液a出口通过酸侵槽a输送泵6与压滤机a11连接,压滤机a11滤液与还原槽4连接,压滤机a6滤渣与酸侵槽b2连接;酸侵槽b2上设置有加料口,用于加入酸,酸侵槽b2底部设置有酸侵液b出口,酸侵液b出口通过酸侵槽b输送泵7与压滤机b12连接,压滤机b12滤液与还原槽4连接,压滤机b滤渣与洗涤槽3连接;洗涤槽3上设置有加料口,用于加入洗涤液(水),洗涤槽3底部设置有洗涤液出口,洗涤液出口通过洗涤槽输送泵8与压滤机c13连接,压滤机c13滤液与还原槽4连接,压滤机c滤渣与外接固废焚烧系统连接;还原槽4上设置有加料口,用于加入铁粉,还原槽4底部设置有还原槽液出口,还原槽液出口通过还原槽输送泵9与压滤机d14连接,压滤机d滤液与中和沉淀槽连接,压滤机d滤渣为海绵铜;中和沉淀槽5上设置有加料口,用于加入naoh溶液,中和沉淀槽5底部设置有中和沉淀槽液出口,中和沉淀槽液出口通过中和沉淀槽输送泵10后收集;酸侵槽a1、酸侵槽b2、洗涤槽3、还原槽4、中和沉淀槽5上均设置有搅拌装置,所述搅拌装置包括搅拌轴、搅拌叶片和电机,搅拌轴伸入槽体内设置有搅拌叶片,搅拌轴上端设置有电机。
[0019]
实施例1(1)浆渣水解渣及废触体按3:1配比后投入酸侵槽a中,加入5%(浓度)盐酸溶液,投入30千克氯酸钠,在搅拌机的搅拌下使废渣中的铜充分接触酸侵液,反应停留时间为2小时; (2)酸侵槽a中的固液混合物通过酸侵槽a输送泵送入压滤机a进行固液分离,滤液进入还原槽,滤渣进入酸侵槽b; (3)酸侵槽b中加入5%盐酸溶液,每吨干渣投入30千克氯酸钠,在搅拌机的搅拌下使废渣中的铜充分接触酸侵液,反应停留时间为2小时; (4)酸侵槽b中的固
液混合物通过酸侵槽b输送泵送入压滤机b进行固液分离,滤液进入还原槽,滤渣进入洗涤槽,经两次酸浸及洗涤后后硅粉中铜含量低于0.15%;(5)经洗涤槽洗涤后通过洗涤槽输送泵送入压滤机c进行过夜分离,滤液进入还原槽,滤渣送固废焚烧系统焚烧处理;(6)检测还原槽中的铜含量,在还原槽中加入铁粉,铁粉与铜的比例1.2:1,铁粉与cucl2溶液发生化学反应,将铜置换出来,得到铜和fecl2溶液; (7)通过还原槽输送泵将混合液送入压滤机d进行固液分离,得到的固体为铜含量大于50%的海绵铜产品,滤液进入中和沉淀槽;(8)中和沉淀槽中加入naoh,fecl2溶液与naoh中和沉淀得到铁渣,铁渣可作为炼钢原料,清液送至污水处理站处理。
[0020]
(9)经毒性浸出实验后,浸出液中铜含量在浸出液中铜含量在3.25-33.6mg/l,小于100mg/l的危废最低标准,固渣可不作为危废认定。
[0021]
实施例2(1)浆渣水解渣及废触体按3:1配比后投入酸侵槽a中,加入10%(浓度)盐酸溶液,投入40千克氯酸钠,在搅拌机的搅拌下使废渣中的铜充分接触酸侵液,反应停留时间为4小时; (2)酸侵槽a中的固液混合物通过酸侵槽a输送泵送入压滤机a进行固液分离,滤液进入还原槽,滤渣进入酸侵槽b; (3)酸侵槽b中加入8%盐酸溶液,每吨干渣投入40千克氯酸钠,在搅拌机的搅拌下使废渣中的铜充分接触酸侵液,反应停留时间为3小时; (4)酸侵槽b中的固液混合物通过酸侵槽b输送泵送入压滤机b进行固液分离,滤液进入还原槽,滤渣进入洗涤槽,经两次酸浸及洗涤后后硅粉中铜含量低于0.15%;(5)经洗涤槽洗涤后通过洗涤槽输送泵送入压滤机c进行过夜分离,滤液进入还原槽,滤渣送固废焚烧系统焚烧处理;(6)检测还原槽中的铜含量,在还原槽中加入铁粉,铁粉与铜的比例1.3:1,铁粉与cucl2溶液发生化学反应,将铜置换出来,得到铜和fecl2溶液; (7)通过还原槽输送泵将混合液送入压滤机d进行固液分离,得到的固体为铜含量大于50%的海绵铜产品,滤液进入中和沉淀槽;(8)中和沉淀槽中加入naoh,fecl2溶液与naoh中和沉淀得到铁渣,铁渣可作为炼钢原料,清液送至污水处理站处理。
[0022]
(9)经毒性浸出实验后,浸出液中铜含量在浸出液中铜含量在3.25-33.6mg/l,小于100mg/l的危废最低标准,固渣可不作为危废认定。
[0023]
实施例3(1)浆渣水解渣及废触体按3:1配比后投入酸侵槽a中,加入10%(浓度)盐酸溶液,投入60千克氯酸钠,在搅拌机的搅拌下使废渣中的铜充分接触酸侵液,反应停留时间为5小时; (2)酸侵槽a中的固液混合物通过酸侵槽a输送泵送入压滤机a进行固液分离,滤液进入还原槽,滤渣进入酸侵槽b; (3)酸侵槽b中加入10%盐酸溶液,每吨干渣投入60千克氯酸钠,在搅拌机的搅拌下使废渣中的铜充分接触酸侵液,反应停留时间为4小时; (4)酸侵槽b中的固液混合物通过酸侵槽b输送泵送入压滤机b进行固液分离,滤液进入还原槽,滤渣进入洗涤槽,经两次酸浸及洗涤后后硅粉中铜含量低于0.15%;(5)经洗涤槽洗涤后通过洗涤槽输送泵送入压滤机c进行过夜分离,滤液进入还原槽,
滤渣送固废焚烧系统焚烧处理;(6)检测还原槽中的铜含量,在还原槽中加入铁粉,铁粉与铜的比例1.5:1,铁粉与cucl2溶液发生化学反应,将铜置换出来,得到铜和fecl2溶液; (7)通过还原槽输送泵将混合液送入压滤机d进行固液分离,得到的固体为铜含量大于50%的海绵铜产品,滤液进入中和沉淀槽;(8)中和沉淀槽中加入naoh,fecl2溶液与naoh中和沉淀得到铁渣,铁渣可作为炼钢原料,清液送至污水处理站处理。
[0024]
(9)经毒性浸出实验后,浸出液中铜含量在3.25-33.6mg/l,小于100mg/l的危废最低标准,固渣可不作为危废认定。
起点商标作为专业知识产权交易平台,可以帮助大家解决很多问题,如果大家想要了解更多知产交易信息请点击 【在线咨询】或添加微信 【19522093243】与客服一对一沟通,为大家解决相关问题。
此文章来源于网络,如有侵权,请联系删除



tips