一种磁控管阴极组件的组装工艺的制作方法



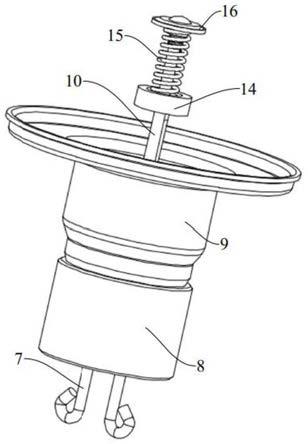
[0001]
本发明涉及产生微波设备的磁控管领域,具体而言,涉及一种磁控管阴极组件的组装工艺。
背景技术:
[0002]
磁控管是一种用来产生微波能的电真空器件,实质上是一个置于恒定磁场中的二极管,管内电子在相互垂直的恒定磁场和恒定电场的控制下,与高频电磁场发生相互作用,把从恒定电场中获得能量转变成微波能量,从而达到产生微波能的目的,磁控管的特点是功率大、效率高、工作电压低、尺寸小、重量轻、成本低。
[0003]
现有技术中,磁控管主要包括阳极组件、阴极组件及排气管组件等,而各部件的同心度及真空度是决定磁控管是否合格的重要指标。通常阴极组件包括端子、支撑本体、k侧管以及引线等,焊接装配时的轻微移位都可能造成漏气和/或导致同心度不达标。此外,阴极组件的零部件众多,如果依次两两焊接,则装配步骤多且部分零部件可能频繁升温,产品的装配效率及合格率均较低。
[0004]
磁控管组装以后,为了把磁控管变成真空状态切断的部分,在磁控管的下端设置阴极组件,阴极组件包括本体、侧管、下端帽组件和长引线,阴极组件通过侧管与阳极筒连接在安装阴极组件之前,需保证阴极组件中各个零件之间密封良好
[0005]
如何控制阴极组件的组装工艺,避免焊接变形对引线组件的不良影响,提高检漏效率,同时提高组装效率及产品合格率,成为本领域技术人员亟待解决的技术问题。
技术实现要素:
[0006]
本发明旨在提出一种磁控管阴极组件组装工艺,以解决使用现有技术中的阴极组件组装工艺得到的阴极组件装配效率差、良品率低、引线组件易发生位移的问题。
[0007]
为解决上述问题,本发明的技术方案是这样实现的:
[0008]
一种磁控管阴极组件的组装工艺,包括如下的步骤:
[0009]
s1:预装部件与模具之间的预组装;
[0010]
s2:焊接、拆模;
[0011]
s3:检漏;
[0012]
s4:安装灯丝、上端帽,并将所述灯丝、上端帽焊接固定;
[0013]
s5:灯丝碳化;
[0014]
s6:电阻检测、涂钛粉;
[0015]
其中,预装部件包括下端帽、长引线、反射板、k侧管、焊料板、支撑本体、端子组件;所述模具包括上模具和下模具。
[0016]
采用上下模具配合的方式首先将预装部件与上下模具预组装,通过上模具和下模具内部结构的设置,使得阴极组件各个零部件保持同心,避免出现错位的情况,提高焊接后成品的良品率,并且焊接后拆模时,通过逐级拆模的形式,避免拆模时损坏阴极组件。
[0017]
进一步的,步骤s1包括:
[0018]
s11:装配下模具,放入下端帽和长引线;
[0019]
s12:放上上模具及反射板、k侧管、焊料板、支撑本体、端子组件;
[0020]
其中,所述下模具包括钎焊底座、引线固定块、钎焊顶杆和反射板定位块。
[0021]
通过下模具的设置,保持长引线与下端帽保持同心,同时为安装下模具及其余部件提供支持,通过上下模具的配合设置,将预装部件同轴心装配,有效地预防了焊接变形,同时也有利于后续拆模。
[0022]
进一步的,步骤s11包括:
[0023]
s111:将所述钎焊顶杆限位装配至所述钎焊底座的第二凹槽内;
[0024]
s112:将引线固定块放入所述钎焊顶杆内,使所述引线固定块的下表面与钎焊底座相连,所述引线固定块的侧壁面与所述钎焊顶杆的内壁面相连;
[0025]
s113:将下端帽的一端限位装配至所述引线固定块的第二凸台上;
[0026]
s114:将长引线的一端穿过所述下端帽限位至所述引线固定块上的引线孔内将所述长引线插入所述引线固定块;
[0027]
s115:将反射板定位块的凸柱置于钎焊顶杆的第三凹槽内;
[0028]
其中,s113和s114的顺序可以互换。
[0029]
所述钎焊底座用于固定所述长引线,所述钎焊顶杆和所述引线固定块用于配合固定所述下端帽,使得所述下端帽上的通孔与所述长引线同轴心设置。
[0030]
进一步的,步骤s12包括:
[0031]
s121:将所述k侧管套设在所述钎焊顶杆上,其敞口的一端与所述钎焊底座抵接;
[0032]
s122:将所述反射板设置在所述反射板定位块上;
[0033]
s123:将所述焊料板覆盖在所述k侧管上;
[0034]
s124:将所述支撑本体和端子组件设置在所述反射板定位块上,其中,端子组件的一端依次穿过支撑本体、焊料板后固定在反射板上;
[0035]
s125:将所述上模具套设在所述k侧管外侧。
[0036]
该设置使得所有的预装部件处于同轴心状态,同时各个模具对其进行限位,有效地预防了焊接变形,提高了所述阴极组件的组装精度。
[0037]
进一步的,步骤s2包括:
[0038]
s21:检查预装部件已组装到位,且所述上模具已盖设到位;
[0039]
s22:将所述预装部件放入氢炉链条中间,所述氢炉链条将所述预装部件送入氢炉中焊接;
[0040]
s23:拆除所述上模具;
[0041]
s24:拆除其余模具。
[0042]
检查所述上模具已盖设到位,可确保所述预装部件之间紧密结合,在焊接时不会发生变形。
[0043]
进一步的,步骤s3包括:
[0044]
s31:启动检漏设备,在检漏仪自启完成、运行稳定的条件下启动检漏仪的检测状态;
[0045]
s32:执行检漏操作,筛选出不合格工件。
[0046]
所述检漏操作依次包括大漏检测工序、小漏检测工序和氦漏检测工序;
[0047]
执行检漏操作时,阴极组件倒扣在下夹具上,上夹具包裹在阴极组件的k 侧管、支撑本体和端子组件的外部。
[0048]
进一步的,步骤s32包括:
[0049]
s321、执行大漏检测工序,在预设时间内阴极组件内部真空度达到第一预设值p1,继续执行小漏检测工序;
[0050]
s322、执行小漏检测工序时,在预设时间内阴极组件和内部真空度达到第二预设值p2时,继续执行氦漏检测工序;
[0051]
s323、执行氦漏检测工序时,若氦气检测仪检测到阴极组件内部有氦气,说明对应的阴极组件有氦漏现象。
[0052]
进一步的,步骤s4包括:
[0053]
s41:将灯丝套设在所述长引线上,灯丝的一端抵接所述下端帽;
[0054]
s42:将所述上端帽套设在所述长引线上,所述上端帽与所述灯丝的另一端抵接;
[0055]
s43:将所述上端帽与所述长引线焊接固定;
[0056]
s44:投影,根据投影情况调整上端帽、下端帽上的引线和灯丝;
[0057]
s45:将所述灯丝的两端分别于与所述上端帽、下端帽焊接固定。
[0058]
在该设置中,通过上下端帽将所述灯丝初步固定,再通过投影调整所述上端帽、下端帽和灯丝使其满足要求,然后通过焊接将所述上端帽固定,对所述灯丝起到了良好的限位效果,为后续的焊接提供便利。
[0059]
进一步的,步骤s5包括:
[0060]
s51:将阴极组件放入炭化炉中,进行灯丝碳化;
[0061]
s52:将碳化后的阴极组件取出冷却;
[0062]
s53:对冷却后的阴极组件检测电阻,符合预设值的阴极组件执行s6。
[0063]
具体的,所述端子组件之间的电阻值是指第一端子与第二端子之间的电阻值,应当注意的是,在将阴极组件放入炭化炉时,需抓取k侧管部位,避免触碰阴极组件的引线和端子,以确保阴极组件的组装良品率。
[0064]
进一步的,步骤s6包括:
[0065]
s61:检测第一端子和第二端子之间的电阻值,符合预设值的阴极组件执行s63;
[0066]
s62:将钛粉和粘合剂按照一定比例混合,将混合后的钛粉涂在所述上端帽上。
[0067]
具体的,在涂钛粉时需要注意,钛粉需要填满所述上端帽,且不能从所述上端帽中溅出。
[0068]
相对于现有技术,本发明所述的磁控管阴极组件的组装工艺具有以下优势:采用上模具、下模具的设置,使得所述阴极组件在焊接时不会发生变形,从而确保所述阴极组件的结构精度,然后通过检漏仪上下夹具的设置,使得对阴极组件进行检漏时,上夹具与下夹具之间通过阴极组件隔离,当阴极组件有细小裂缝或焊接不严密时,下夹具或上夹具内部的氦气分子会通过阴极组件上的裂缝进入下夹具或上夹具内部,破坏真空度,由此对阴极组件上的细小裂缝进行检测,灵敏度和检测精度更高,本发明提供的磁控管阴极组件组装工艺,步骤简单,模具使用简便,大大提高了阴极组件的组装效率和良品率。
附图说明
[0069]
图1为本发明实施例中所述模具组装并且焊接后形成的阴极组件整体示意图;
[0070]
图2为本发明实施例中所述阴极组件的爆炸示意图;
[0071]
图3为本发明实施例中所述阴极组件对应模具结构的爆炸示意图;
[0072]
图4为本发明实施例中所述钎焊底座的结构示意图;
[0073]
图5为本发明实施例中所述钎焊底座的俯视图;
[0074]
图6为本发明实施例中所述引线固定块的结构示意图;
[0075]
图7为本发明实施例中所述钎焊顶杆的结构示意图;
[0076]
图8为本发明实施例中所述钎焊顶杆的剖示图;
[0077]
图9为本发明实施例中所述反射板定位块的结构示意图;
[0078]
图10为本发明实施例中所述反射板定位块的仰视图;
[0079]
图11为本发明实施例中所述分体式上模具的剖视图;
[0080]
图12为本发明实施例中所述第二装配部的结构示意图;
[0081]
图13为本发明实施例中所述一体式上模具的结构示意图;
[0082]
图14为本发明实施例中所述一体式上模具的剖视图;
[0083]
图15为本发明实施例中所述检漏仪的结构示意图;
[0084]
图16为本发明实施例所述往阴极组件上安装灯丝和上端帽的爆炸示意图;
[0085]
图17为本发明实施例所述组装完成后的阴极组件结构示意图。
[0086]
附图标记说明:
[0087]
1、钎焊底座;101、底座本体;102、第一凹槽;103、第一凸台;104、第二凹槽;105、第一通孔;106、第二通孔;2、引线固定块;21、引线孔; 22、第二凸台;23、导向部;3、钎焊顶杆;31、第三通孔;311、第一容腔; 312、第二容腔;32、第三凹槽;33、第一导向结构;331、第一倒角;332、第二倒角;4、反射板定位块;41、定位块本体;42、凸柱;43、通槽;44、第三倒角;45、第二导向结构;451、第一凹陷部;452、第二凹陷部;5、上模具;51、第一装配部;511、第一腔体;5111、第三导向结构;512、第二腔体;513、收缩部;52、第二装配部;521、限位结构;5211、导向槽;5212、限位槽;522、第四通孔;7、端子组件;71、第一端子;72、第二端子;8、支撑本体;9、k侧管;10、引线组件;11、焊料板;12、反射板;13、下端帽;14、长引线;15、灯丝;16、上端帽;18、检漏仪;181、上夹具;182、下夹具。
具体实施方式
[0088]
为使本发明目的、技术方案和优点更加清楚,下面将结合附图及实施例,对本发明进行进一步详细说明。应当理解,所描述的实施例是本发明一部分实施例,而不是全部的实施例。此处所描述的具体实施例仅仅用以解释本发明,并不用于限定本发明。需要说明的是,在不冲突的情况下,本发明中的实施例及实施例中的特征可以相互组合。
[0089]
下面结合附图具体描述本发明实施例的一种磁控管阴极组件的组装工艺。
[0090]
为了方便说明,首先对阴极组件的结构进行说明,如图1、图2、图17 所示,一种阴极组件,用于磁控管的装配,包括由下自上依次设置的端子组件7、支撑本体8、焊料板11、反射板12、k侧管9、引线组件10,所述端子组件7包括依次穿过支撑本体8、焊料板11后固定在所述反射板12的上端面上的第一端子71、第二端子72;装配时,所述第一端子71、第二端子
72 的上端与磁控管的电源相连;所述支撑本体8为陶瓷材质,所述引线组件10 包括下端帽13、长引线14,所述长引线14的一端穿过所述下端帽13,调整同心度后用于安装灯丝15。所述下端帽13、长引线14的另一端穿过k侧管 9、反射板12后固定在支撑本体8内。优选的,所述反射板12有两个,其结构可相同或不同,单独每一个上分别设有端子组件7、引线组件10的固定孔;装配时,所述反射板12位于k侧管9内且与位于正上方的焊料板11抵接相连。优选的,所述两个反射板12的结构不同,其中一块上设有缺脚,用于连接下端帽13;另一块上没有缺脚,用于连接长引线14。所述焊料板11设在支撑本体8、k侧管9之间,用于二者的焊接固定;同时,所述焊料板11可将反射板12焊接在支撑本体8靠近k侧管9的端面上,并提高端子组件7、引线组件10与反射板12的连接强度。所述焊料板11可以是一块,也可以是多块;例如将两块焊料板11叠放,可降低焊接后阴极组件存在漏气情况的发生率。
[0091]
为了提高装配效率及合格率,本发明提供了一种模具组件,包括相互配合的上模具5、下模具,如图3所示。该设置可避免阴极组件的各部分在焊接过程中发生偏移,提高装配效率及良品率。具体的,所述上模具5包括同轴设置的钎焊底座1、引线固定块2、钎焊顶杆3、反射板定位块4,所述钎焊底座1上设有第二凹槽104,所述第二凹槽104内套设有钎焊顶杆3,所述钎焊顶杆3上设有第三通孔31,所述第三通孔31内套设有引线固定块2,所述反射板定位块4装配到第三通孔31的上端部。所述上模具5包括第一装配部 51及第二装配部52,所述第一装配部51和第二装配部52为分体设置或一体成型设置。具体的,将钎焊顶杆3装入钎焊底座1的第二凹槽104内,再从上方将引线固定块2限位到钎焊顶杆3的第三通孔31内,所述引线固定块2 的下表面与钎焊底座1相连,所述引线固定块2的侧壁面与第三通孔31的内壁面相连;依次将下端帽13、长引线14放到下模具上;之后将反射板定位块 4放在钎焊顶杆3的上端面上,再把k侧管9套设在反射板定位块4上,之后分别放反射板12、焊料板11、支撑本体8,将端子组件7的一端向下穿过支撑本体8、焊料板11后固定在反射板12的固定孔上;之后套上上模具5,第一装配部51,放入氢炉流水线上进行高温焊接。
[0092]
如图4、图5所示,所述钎焊底座1包括底座本体101,所述底座本体101 的上端部设有第一凸台103,所述第一凸台103的上端面设有向下凹陷的第二凹槽104,用于容置所述钎焊顶杆3。所述底座本体101可以是圆柱状、长块状、棱柱状等任意形状。优选的,所述底座本体101、第一凸台103为圆柱状,二者为一体成型;第二凹槽104为向下延伸且部分位于底座本体101内的圆形孔,所述第二凹槽104与所述底座本体101、第一凸台103均为同轴设置。作为本发明的一个示例,所述底座本体101的直径为45mm,高21.7mm,第一凸台103的高度为3.1mm,直径为36.9mm;所述第二凹槽104的孔径为 16.6mm,深度为19.8mm。作为本发明的一个示例,所述底座本体101 的侧壁面上设有环形的第一凹槽102。该设置既确保底座本体101与托盘等物体的接触面大,减少原料消耗,外形美观;同时使高温焊接时受热均匀,使用寿命长,良品率高。作为本发明的另一个示例,所述第一凸台103上设有多个沿第一凸台103的周侧等间距分布的第一通孔105,其圆心所在圆距离第一凸台103的外壁面、第二凹槽104的内壁面的距离相等。所述第一通孔105有4-12个。该设置可进一步减少原料消耗,节省成本,同时有利于焊接时温度均匀上升,提高焊接质量。优选的,所述第一通孔105有8个,其直径为第二凹槽104的直径的12/25~1/2,例如所述第一通孔105的直径为 8mm。该设置可兼顾钎焊底座1的机械强度及阴极组件的良品率。优选的,所述第二凹槽104的底面上偏离底面圆心位置设有第二通孔106,例如,其直径为3mm,其圆心与底面圆心的距离为4.5mm。该设
置可进一步方便传热,提高焊接的良品率。
[0093]
如图6所示,所述引线固定块2包括设在其上端部的第二凸台22,所述第二凸台22上设有贯穿的引线孔21;优选的,所述引线固定块2、第二凸台 22为柱状,所述引线孔21为圆形,三者同轴设置。装配时,所述长引线14 背离所述支撑本体8的一端伸入至所述引线孔21内,所述下端帽13组件背离所述支撑本体8的一端套设在所述第二凸台22外。作为本发明的另一个示例,所述引线固定块2的下端设有导向部23。该设置可使引线固定块2 快速滑入钎焊顶杆3内,提高二者的装配效率。优选的,所述导向部23设在所述引线固定块2的底面与侧壁面之间,例如沿所述底面周侧设置且向轴线倾斜靠拢靠拢的导向斜面。
[0094]
如图7、图8所示,所述钎焊顶杆3为圆柱状,其顶面设有同轴的第三凹槽32,用于容置、固定所述反射板定位块4,所述第三凹槽32的底面设有同轴的第三通孔31,用于容置所述引线固定块2。所述钎焊顶杆3的直径与第二凹槽104的孔径相同,可确保二者之间为同轴装配,避免模具之间相对移位,提高焊接的良品率。优选的,所述第三通孔31包括由上自下依次设置的第一容腔311、第二容腔312。所述第二容腔312的内孔径与引线固定块2的外径相同,所述第一容腔311的孔径大于第二容腔312的孔径。例如,所述第一容腔311、第二容腔312的孔径分别为7.4mm、7.28mm。作为本发明的另一个示例,所述钎焊顶杆3上还设有第一导向结构33。所述第一导向结构33包括第一倒角331和/或第二倒角332,所述第一倒角331位于第三凹槽32的上部并沿其周侧设置,便于后续反射板定位块4的快速装配;所述第二倒角332位于钎焊顶杆3的下端部并沿其周侧设置,便于钎焊顶杆3快速装配到钎焊底座1内。当装配下模具时,将钎焊顶杆3通过第二倒角332快速装配至钎焊底座1的第二凹槽104内;之后将引线固定块2从钎焊顶杆3 的上部滑入第三通孔31并快速通过孔径较大的第一容腔311,通过通过导向部23进入第二容腔312内并与钎焊底座1接触完成装配,装配效率高、确保钎焊底座1、引线固定块2、钎焊顶杆3之间为同轴装配,避免发生相对移位而影响良品率。
[0095]
如图9、图10所示,所述反射板定位块4包括通槽43以及同轴相连的定位块本体41、凸柱42,所述凸柱42位于所述定位块本体41的下部,用于与钎焊顶杆3的限位装配。所述通槽43贯穿所述定位块本体41、凸柱42设置。优选的,所述定位块本体41的上端设有第三倒角44,所述第三倒角44沿所述定位块本体41的周侧设置。所述凸柱42的下端部还设有第二导向结构45,,便于引线组件10穿过所述通槽43。作为本发明的一个示例,所述第二导向结构45还包括穿过设在所述通槽43上的第一凹陷部451、第二凹陷部452,其结构可相同或不同,如圆形、方形、椭圆形等。作为本发明的一个示例,所述第一凹陷部451、第二凹陷部452均为弧形,并以凸柱42的纵轴线呈中心对称。该设置结构简单,便于装配;更优选的,所述第一凹陷部451、第二凹陷部452在靠近通槽43的一端逐渐收缩,方便安装时引线组件10快速穿过所述通槽43。装配时,将引线组件10的下端帽13装配到引线固定块 2的第二凸台22上,再将长引线14的一端穿过下端帽13限位到引线孔21内;之后将反射板定位块4往下放,将引线组件10的上端先限位到第二导向结构 45内,转动反射板定位块4使引线组件10顺利穿过通槽43,从而将反射板定位块4限位装配到钎焊顶杆3的第三凹槽32内,套设上所述k侧管9,所述k侧管9的形状类似于草帽,帽檐位置与钎焊底座1接触,所述k侧管9 的顶部开口且装配后略高于所述反射板定位块4,依次将反射板12、焊料板 11穿过所述引线组件10的上端后放在所述反射板定位块4上。
[0096]
具体的,如图11所示,所述上模具5为分体式结构,所述上模具5包括分体设置的第
一装配部51、第二装配部52,所述第一装配部51内设有串通的第一腔体511、第二腔体512,分别用于容置所述支撑本体8、k侧管9,所述第一腔体511、第二腔体512为同轴非等直径设置,优选的,第一腔体 511的内径大于第二腔体512的内径,所述第一腔体511的内径等于所示支撑本体8的外径,所述第二腔体512的内径等于所述k侧管9的外径。优选的,所述第一腔体511、第二腔体512之间设有收缩部513,该设置使第一装配部 51在生产时便于退刀,有利于简化生产工艺。装配时,将支撑本体8叠放在所述焊料板11上,此时引线组件10中的长引线14部分插入到所述支撑本体 8内;套上第一装配部51,其中第一腔体511位于所述k侧管9的外周侧,所述第二腔体512位于支撑本体8的外周侧。
[0097]
如图11、12所示,为了固定位于支撑本体8的上方的端子组件7,所述第一装配部51的上方设置第二装配部52,所述第二装配部52的下端面设有限位结构521,所述限位结构521包括相连串通的导向槽5211、限位槽5212,所述导向槽5211包括一个倾斜的侧壁面,所述导向槽5211从限位槽5212的一端向外逐渐扩大,所述限位槽5212沿所述支撑本体8的轴线呈左右对称设置。该设置可确保端子组件7处于同一平面上,确保装配的一致性。位于所述支撑本体8的上方的端子组件7通过导向槽5211进入所述限位槽5212内并被限位固定,完成模具组件的装配。
[0098]
作为本发明的另一个实施例,如图13、图14所示,所述上模具5包括一体成型设置的第一装配部51、第二装配部52,所述第一装配部51上设有同轴相连的第一腔体511、第二腔体512,所述第二腔体512的上端设有第二装配部52,所述第二装配部52的上端设有限位结构521,用于对所述端子组件 7进行限位。该设置可通过一个模具完成对阴极组件的多个部件进行限位,装配效率高;所述第一腔体511的内孔径大于第二腔体512的内孔径,所述第一腔体511在靠近第二腔体512的一端设有收缩部513。优选的,所述第一腔体511的内径等于所示支撑本体8的外径,所述第二腔体512的内径等于所述k侧管9的外径。该设置可同时对不同直径的阴极组件配件进行限位装配,确保装配后的支撑本体8及k侧管9相互同心。优选的,所述第一腔体511 在远离收缩部513的一端设有第三导向结构5111,所述第三导向结构5111为沿第一腔体511周侧设置的导向斜面。该设置可便于支撑本体8快速进行第一腔体511内,装配效率高。作为本发明的一个示例,所述限位结构521 为限位槽5212,所述限位槽5212向下延伸并与所述第二腔体512贯通。该设置可减少原料消耗,同时方便端子组件7进入限位结构521内,确保两个端子处于同一平面内,方便后续组装。优选的,所述限位结构521还包括与所述限位槽5212相连通的导向槽5211,所述导向槽5211从所述限位槽5212的一端向靠近第二腔体512的一端逐渐向外扩大。该设置方便操作人员从侧面观察配件情况,便于端子组件7的上端部快速进入限位结构521内;作为本发明的另一个示例,第二装配部52上还设有至少一个第四通孔522。装配时通过第四通孔522观察上模具5内配件的位置,提高装配效率。优选的,所述第四通孔522有两个,对称的设在所述导向槽5211的两侧。该设置结构简单,外形美观,既能减少原料消耗,便于观察上模具5内阴极组件的装配情况。
[0099]
作为本发明实施例的一部分,本发明还提供了一种磁控管阴极组件组装工艺,包括如下步骤:
[0100]
s1:预装部件与模具之间的预组装;
[0101]
s2:焊接、拆模;
[0102]
s3:检漏;
[0103]
s4:安装灯丝15、上端帽16,并将所述灯丝15、上端帽16焊接固定;
[0104]
s5:灯丝15碳化;
[0105]
s6:电阻检测、涂钛粉;
[0106]
其中,预装部件包括下端帽13、长引线14、反射板12、k侧管9、焊料板11、支撑本体8、端子组件7;所述模具包括上模具5和下模具。
[0107]
采用上下模具配合的方式首先将预装部件与上下模具预组装,通过上模具5和下模具内部结构的设置,使得阴极组件各个零部件保持同心,避免出现错位的情况,提高焊接后成品的良品率,并且焊接后拆模时,通过逐级拆模的形式,避免拆模时损坏阴极组件。
[0108]
为了保证阴极组件的有效组装,在步骤s1之前,需要对预装部件以及灯丝15、上端帽16进行全检工作,首先,操作人员做好准备工作,带好手套及手指套,避免直接接触模具和待组装部件;其次,检查下端帽13、长引线14、反射板12、k侧管9、端子组件7、灯丝15,剔除有变形、氧化、刮伤及黑痕脏污的情况,检查上端帽16,剔除有变形变色、毛剌、缺损、破裂以及没有焊料环的情况,检查支撑本体8,剔除有污迹、裂纹、变色、变形的情况;检查焊料板11,保持其表面清洁,剔除有油迹、氧化的情况。
[0109]
进一步的,步骤s1包括:
[0110]
s11:装配下模具,放入下端帽13和长引线14;
[0111]
s12:放上下模具及反射板12、k侧管9、焊料板11、支撑本体8、端子组件7;
[0112]
其中,所述下模具包括钎焊底座1、引线固定块2、钎焊顶杆3和反射板定位块4。
[0113]
通过可拆卸的上模具5和下模具设置,使得所述阴极组件在焊接时不会发生变形,从而确保所述阴极组件的焊接质量及结构精度,良品率更高。
[0114]
在本实施例中,步骤s11包括:
[0115]
s111:将所述钎焊顶杆3限位装配至所述钎焊底座1的第二凹槽104内;
[0116]
s112:将引线固定块2放入所述钎焊顶杆3内,使所述引线固定块2的下表面与钎焊底座1相连,所述引线固定块2的侧壁面与所述钎焊顶杆3的内壁面相连;
[0117]
s113:将下端帽13的一端限位装配至所述引线固定块2的第二凸台22 上;
[0118]
s114:将长引线14的一端穿过所述下端帽13限位至所述引线固定块2 上的引线孔21内将所述长引线14插入所述引线固定块2;
[0119]
s115:将反射板定位块4的凸柱42置于钎焊顶杆3的第三凹槽32内;
[0120]
其中,s113和s114的顺序可以互换。
[0121]
该设置使得所有的预装部件处于同轴心状态,同时各个模具对其进行限位,有效地预防了焊接变形,提高了所述阴极组件的组装精度。具体的,所述钎焊顶杆3插入所述钎焊底座1的第二凹槽104中,所述钎焊顶杆3的外径与所述第二凹槽104内径配合设置,使得所述钎焊顶杆3被迅速定位,然后将所述引线固定块2放入所述钎焊顶杆3的第三通孔31中,所述引线固定块2的外径与所述第三通孔31的内径配合设置,使得所述引线固定块2被迅速定位,此时所述钎焊底座1、引线固定块2、钎焊顶杆3处于同心状态,然后放入下端帽13和长引线14,下端帽13端帽一侧向下放入所述第三通孔31 中,与所述引线固定块2的顶部抵接或者套设在第二凸台22上,当所述下端帽13与所述引线固定块2的顶部抵接时,所述第三通孔31的内径与所述下端帽13的外径配合设置,以便完成所述下端帽13的同心定位,当所述下端帽13套设在所述第二凸台22上时,所述下端帽13的通孔内径与所述第二凸台22的外径
配合设置,可以将所述下端帽13快速同心定位;所述长引线14 远离弯折部的一端插入所述引线固定块2的引线孔21中被固定,从而完成所述下端帽13和长引线14的同心固定设置,所述反射板定位块4的凸柱42卡设在所述钎焊顶杆3的第三凹槽32内,从而完成同心固定。
[0122]
具体的,步骤s12包括:
[0123]
s121:将所述k侧管9套设在所述钎焊顶杆3上,其敞口的一端与所述钎焊底座1抵接;
[0124]
s122:将所述反射板12设置在所述反射板定位块4上;
[0125]
s123:将所述焊料板11覆盖在所述k侧管9上;
[0126]
s124:将所述支撑本体8和端子组件7设置在所述反射板定位块4上,其中,端子组件7的一端依次穿过支撑本体8、焊料板11后固定在反射板12 上;
[0127]
s125:将所述上模具5套设在所述k侧管9外侧。
[0128]
具体的,所述k侧管9套设在所述钎焊顶杆3外侧时,其内壁与所述钎焊顶杆3的外侧壁贴合,从而使得所有已组装部件处于同心状态,所述k侧管9敞口的一端与所述钎焊底座1抵接也进一步地对所述k侧管9的高度进行了限位,在本实施例中,所述焊料板11上设置有至少两条突起,其中一条突起为方角边或其他定位标志,所述方角边或其他定位标志用于所述焊料板 11的快速定位定向,便于快速确定其余长引线14连接或是与所述下端帽13 上的引线连接,优选的,所述反射板12有两块,其中一块上设置有缺角或其他定位标志,所述缺角或其他定位标志用于快速确定所述反射板12是与所述长引线14连接或是与所述下端帽13上的引线连接,所述上模具5套设在所述k侧管9外侧,其一端抵接在所述k侧管9的敞口板上,限定所述k侧管 9与支撑本体8和端子组件7的同心组装,从而保证其在焊接时不会发生变形,可选择的,s126也可以设置在s125之前进行,但组装效率相对较低。
[0129]
具体的,步骤s2包括:
[0130]
s21:检查预装部件已组装到位,且所述上模具5已盖设到位;
[0131]
s22:将所述预装部件放入氢炉链条中间,所述氢炉链条将所述预装部件送入氢炉中焊接;
[0132]
s23:拆除所述上模具5;
[0133]
s24:拆除其余模具。
[0134]
检查所述上模具5已盖到位,可确保所述预装部件之间紧密结合,在焊接时不会发生变形。
[0135]
优选的,氢炉内温度设定为800~965℃,其中氢炉两端的温度低于中间温度。更优选的,氢炉内温度设定为850~880℃。
[0136]
优选的,氢炉入口处和出口处氮气流量均设置为:1~5.6m
3
/h,更优选的的,氢炉入口和出口处氮气流量均设为4m
3
/h,具体的,氢炉入口处设置气障和气帘。
[0137]
优选的,氢炉内部设置有预热区、加热区和冷却区,加热区氢气流量大于预热区和冷却区,预热区氢气流量设置为0.2~1.25m
3
/h,优选的,预热区氢气流量设置为0.5~0.75m
3
/h。加热区氢气流量设置为0.6~4m
3
/h,优选的,加热区氢气流量1.6~2m
3
/h,冷却区氢气流量随着距离加热区的距离增加,氢气流量逐渐减小。
[0138]
优选的,所述模具整套装配和拆卸,可以确保模具配合的稳定性,从而确保所述阴极组件的组装精度。
[0139]
进一步的,步骤s3包括:
[0140]
s31:启动检漏设备,在检漏仪18自启完成、运行稳定的条件下启动检漏仪18的检测状态;
[0141]
s32:执行检漏操作,筛选出不合格工件。
[0142]
所述检漏操作依次包括大漏检测工序、小漏检测工序和氦漏检测工序;
[0143]
执行检漏操作时,阴极组件倒扣在下夹具182上,上夹具181包裹在阴极组件的k侧管9、支撑本体8和端子组件7的外部,具体的,所诉k侧管9倒扣在所述下夹具182的上表面,所述阴极组件的引线伸入所述下夹具182 的内部,所述引线包括长引线14和下端帽13上的短引线。
[0144]
具体的,如图15所示,所述检漏设备包括:控制装置、检漏仪18、操作装置、真空泵、气源,其中真空泵、气源、和操作装置均与检漏仪18和控制装置连接,且控制装置与检漏仪18连接,所述检漏仪18包括上夹具181和下夹具182,阴极组件倒扣安装在下夹具182上,控制装置控制上夹具181升降或下夹具182升降,实现上夹具181与下夹具182之间的对接或断开。
[0145]
对接时对阴极组件进行检漏,阴极组件与上夹具181之间形成容纳腔,真空泵与下夹具182连通,通过真空泵对阴极组件内部进行抽真空操作,通过真空度判断阴极组件是否有裂缝或焊接不严密等问题。
[0146]
进一步的,步骤s32包括:
[0147]
s321、执行大漏检测工序,在预设时间内阴极组件内部真空度达到第一预设值p1,继续执行小漏检测工序;
[0148]
s322、执行小漏检测工序时,在预设时间内阴极组件和内部真空度达到第二预设值p2时,继续执行氦漏检测工序;
[0149]
s323、执行氦漏检测工序时,若氦气检测仪检测到阴极组件内部有氦气,说明对应的阴极组件有氦漏现象。
[0150]
其中,p1>p2,且在进行大漏检测工序时,利用机械泵对阴极组件内部内部抽真空;在进行小漏检测工序时,利用分子泵对阴极组件内部抽真空,优选的,第一预设值设置p1为10-2
pa~10-3
pa,第二预设值p2设置为10-6
pa~ 10-8
pa,优选的,p2设置为10-7
pa。
[0151]
具体的,在s321中,在预设时间内真空度未达到第一预设值p1的阴极组件存在大漏现象,s321的检测使得存在大漏现象的阴极组件首先被筛选出来,节省工作效率,避免存在大漏现象的阴极组件继续进行小漏检测时增加真空泵负载,造成资源浪费,在s322中,在预设时间内真空度未达到第二预设值p1的阴极组件存在小漏现象,s322的检测使得存在小漏现象的阴极组件首先被筛选出来,节省工作效率,避免存在小漏现象的阴极组件继续进行氦漏检测,浪费氦气气源,若同时检测的所有阴极组件内部真空度均不能达到第二预设值p2,说明本轮检测的无大漏现象的阴极组件均有小漏现象,控制装置结束检漏操作,上夹具181和下夹具182打开,取出所有大漏和小漏的阴极组件,避免继续进行无效检测浪费时间。若同时检测的所有阴极组件中有部分内部真空度不能达到第二预设值p2,说明本轮检测的多个阴极组件有部分存在小漏现象,需关闭与对应上夹具181连通的氦气管道;另一部分无小漏,对应的氦气管道保持连通状态,继续执行进一步的检漏工序。
[0152]
具体的,步骤s323包括:
[0153]
控制装置控制对无小漏现象的阴极组件对应的上夹具181内部进行喷氦气,判断阴极组件内部氦气浓度是否达到预设浓度或阴极组件内部真空度是否超过第二预设值,若是,说明对应的阴极组件有氦漏现象,若否,说明对应的阴极组件无氦漏现象,阴极组件气密性良好,符合标准,结束检漏操作,可以进行下一步操作,在本实施例中,预设浓度根据氦气检测仪的灵敏度和阴极组件气密性理想状态设置。
[0154]
进一步的,如图15所示,步骤s4包括:
[0155]
s41:将灯丝15套设在所述长引线14上,灯丝15的一端抵接所述下端帽13;
[0156]
s42:将所述上端帽16套设在所述长引线14上,所述上端帽16与所述灯丝15的另一端抵接;
[0157]
s43:将所述上端帽16与所述长引线14焊接固定;
[0158]
s44:投影,根据投影情况调整上端帽16、下端帽13上的引线和灯丝15;
[0159]
s45:将所述灯丝15的两端分别于与所述上端帽16、下端帽13焊接固定。
[0160]
在该设置中,通过上下端帽将所述灯丝15初步固定,再通过投影调整所述上端帽16、下端帽13和灯丝15使其满足要求,然后通过焊接将所述上端帽16固定,对所述灯丝15起到了良好的限位效果,为后续的焊接提供便利。
[0161]
优选的,步骤s44的焊接采用氩弧焊,氩气流量为0.2~0.8m
3
/h,焊接电流:150~250a,焊接时间:0.3~1s,焊接完成后,需对所述阴极组件进行全检,确保焊接后的工件表面良好,无氧化、起泡、焊烂,且投影无上端帽16、灯丝15偏,间距不合格等现象。
[0162]
具体的,s44中根据投影调试上端帽16和下端帽13的同心度,具体的,根据投影工装上的规定范围进行比对,上端帽16的高低不能超过规定范围高度的0.1mm,倾斜度不能超过0.1mm;下端帽13的高低不能超过规定范围高度的0.25mm,倾斜度不能超过0.15mm。
[0163]
在本实施例中,步骤s45的焊接设备为高频焊机,保护气体为氢气,气体流量为2~6m
3
/h,加热时间为2~6s,确保灯丝15与上端帽16、下端帽13 焊接良好,以便满足碳化前的电阻要求。
[0164]
进一步的,步骤s5包括:
[0165]
s51:将阴极组件放入炭化炉中,进行灯丝15碳化;
[0166]
s52:将碳化后的阴极组件取出冷却;
[0167]
s53:对冷却后的阴极组件检测电阻,符合预设值的阴极组件执行s6。
[0168]
具体的,在本实施例中所述的碳化工艺包括恒压碳化或恒流碳化,所述恒压碳化的工艺参数为:除气电压3.8~5.8v,除气时间15~25s,碳化电压 4.1~6.1v,碳化压强25~45pa,在本实施例中,碳化前的端子组件7之间的电阻一般在31.5~34mω之间,碳化后端子组件7之间的电阻预设值为35~38mω,优选的,恒压碳化时,除气电压为4.8v,除气时间为20s,碳化电压5.1v;所述恒流碳化的工艺参数为:除气电流13~14a,除气时间20~30s,碳化电流 14.2~15.2a,碳化压强25~45pa,在本实施例中,碳化前的端子组件7之间的电阻一般在31.5~34mω之间,碳化后端子组件7之间的电阻预设值为 35~38mω,优选的,恒流碳化时,除气电流为13.5a,除气时间为25s,碳化电流为14.7a,在本实施例中,电阻值不符合预设值的阴极组件为不合格品,需挑选出后标识并分类放置,具体的,所述端子组件7之间的电阻值是指第一端子71与第二端子72之间的电阻值,应当注意的是,在将阴极组件放入炭化炉时,需抓取k侧管9部位,避免触碰阴极组件的引线和端子,以确保阴极组件的组
装良品率。
[0169]
进一步的,步骤s6包括:
[0170]
s61:检测第一端子71和第二端子72之间的电阻值,符合预设值的阴极组件执行s63;
[0171]
s62:将钛粉和粘合剂按照一定比例混合,将混合后的钛粉涂在所述上端帽16上。
[0172]
在本实施例中,步骤s62中钛粉与粘合剂的比例为体积比4:6,预设值为碳化后端子组件7之间的电阻预设值在35~38mω之间。
[0173]
在涂钛粉时需要注意,钛粉需要填满所述上端帽16,且不能从所述上端帽16中溅出,具体的,焊接后检查时,需注意合格的阴极组件无变形、氧化、断灯丝、缺损和破裂现象。
[0174]
需要说明,本发明中所有进行方向性和位置性指示的术语,诸如:“上”、“下”、“左”、“右”、“前”、“后”、“竖直”、“水平”、“内”、“外”、“顶”、“低”、“尾端”、“首端”、“中心”等,仅用于解释在某一特定状态下各部件之间的相对位置关系、连接情况等,仅为了便于描述本发明,而不是要求本发明必须以特定的方位构造和操作,因此不能理解为对本发明的限制。另外,在本发明中涉及“第一”、“第二”等的描述仅用于描述目的,而不能理解为指示或暗示其相对重要性或者隐含指明所指示的技术特征的数量。
[0175]
虽然本发明披露如上,但本发明并非限定于此。任何本领域技术人员,在不脱离本发明的精神和范围内,均可作各种更动与修改,因此本发明的保护范围应当以权利要求所限定的范围为准。
起点商标作为专业知识产权交易平台,可以帮助大家解决很多问题,如果大家想要了解更多知产交易信息请点击 【在线咨询】或添加微信 【19522093243】与客服一对一沟通,为大家解决相关问题。
此文章来源于网络,如有侵权,请联系删除



tips