用于门窗管材双锯头全自动下料机的制作方法



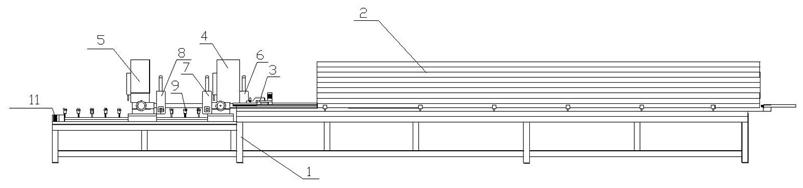
[0001]
本发明涉及双锯头下料机技术领域,特别涉及一种用于门窗管材双锯头全自动下料机。
背景技术:
[0002]
现有双锯头自动下料机,采用的是双锯头数控定位,数控往返送料,该机器的不足之处就是往返送料的夹料部分有一段距离切不到,存在一定的材料浪费。同时需要人工去拿起切好的管材,只是半自动化,且现有技术每使用完一根管材时,就需要人工再放置一根管材上去,碰上管材较长时,机架上一次只可放一根,需要人工监工,操作起来费时费力。
技术实现要素:
[0003]
本发明的目的是针对背景技术中存在的缺点和问题加以改进和创新,提供一种全自动化式的用于门窗管材双锯头全自动下料机。
[0004]
一种用于门窗管材双锯头全自动下料机,包括机架、控制模块、从右至左依次设置在机架上的自动推管机构、数控后拉机构、前驱管锯头、后驱管锯头,前驱管锯头的右端设有前驱数控滚动输送架,前驱管锯头的左端设有中驱数控滚动输送架,后驱管锯头上靠近中驱数控滚动输送架的那端设有后驱数控滚动输送架,若干个导向托滚轮设置在机架上对应前驱管锯头和后驱管锯头的下方。所述前驱管锯头固定在机架上,第一丝杆的一端连接后锯台电机,所述后驱管锯头由第一丝杆带动可在机架上移动,所述前驱管锯头的底部设有原点感光头,控制模块分别与自动推管机构、数控后拉机构、前驱数控滚动输送架、原点感光头、前驱管锯头、中驱数控滚动输送架、后驱数控滚动输送架、后驱管锯头、导向托滚轮、后锯台电机相连。
[0005]
所述自动推管机构包括管子排列机构、二个自动横向推管机构、自动轴向推管机构,自动轴向推管机构设置在机架上远离后驱管锯头的端部,二个自动横向推管机构设置在机架的侧面,且每个自动横向推管机构都与自动轴向推管机构垂直设置,管子排列机构设置在机架的顶面对应靠近自动横向推管机构的那侧,若干根管材对齐排列在管子排列机构内,管子排列机构的下部设有二个报警感光头,管子排列机构的对侧设有若干个第一侧压滚轮。
[0006]
每个所述自动横向推管机构都包括横向推进气缸、第一直线滑轨、第一滑块、活动舌、第一弹簧、第一孔,机架上对应自动横向推管机构处设有第一孔,第一滑块的下部套设在第一直线滑轨上,且第一滑块可在第一直线滑轨上滑动,第一直线滑轨固定在机架上对应管子排列机构的下方,第一滑块上部的一端固定有横向推进气缸,第一滑块的顶面设有定位套筒,定位套筒的顶面不高于管子排列机构内最底部的管材底面,第一滑块的上部对应定位套筒处开设有定位杆孔,定位杆的一端穿过定位杆孔与限位块固定,另一端固定有活动舌,且活动舌可沿定位套筒上下滑动,第一弹簧套设于定位杆上,且第一弹簧处于第一滑块顶面与活动舌底面之间。
[0007]
活动舌的上部为竖直面和倾斜面形成的夹角,且倾斜面朝向管子排列机构。
[0008]
所述自动轴向推管机构包括轴向推进气缸。
[0009]
在其中一个实施例中,所述前驱数控滚动输送架包括压紧气缸、上压紧轮、侧面定位轮、侧压气缸、第二侧压滚轮、驱动轮、前驱电机、第一感光头,管材的上方设有由压紧气缸控制的上压紧轮,管材的两侧分别设有侧面定位轮和由侧压气缸控制的第二侧压滚轮,管材的底部设有由前驱电机控制的驱动轮,所述驱动轮的右方设有第一感光头。
[0010]
所述中驱数控滚动输送架和后驱数控滚动输送架的结构都与前驱数控滚动输送架的结构一致,其中,中驱数控输送架的驱动轮由中驱电机控制,后驱数控输送架的驱动轮由后驱电机控制,中驱数控输送架的驱动轮的右方设置的是第二感光头,后驱数控输送架的驱动轮的右方设置的是第三感光头。
[0011]
在其中一个实施例中,每个所述导向托滚轮包括导向架、喇叭导向机构、托辊轮、升降气缸、左感光头、右感光头、托辊轮电机,升降气缸的顶部设有导向架,导向架上设有托辊轮和托辊轮电机,托辊轮电机驱动托辊轮,导向架上对应托辊轮的上部设有喇叭导向机构,机架上对应托辊轮一端的左、右二侧分别设有左感光头和右感光头。
[0012]
所述喇叭导向机构包括二个平行设置的第一固定块,且二个第一固定块的内侧形成两端大、中间小的通道。
[0013]
在其中一个实施例中,所述数控后拉机构包括自动左右夹紧平衡机构、第二丝杆和数控后拉电机,数控后拉电机设置在机架上。
[0014]
自动左右夹紧平衡机构包括第二滑块、第二直线滑轨、滑板、归位弹簧、固定座、夹紧气缸,第二丝杆与第二滑块配合,一端连接数控后拉电机,并由数控后拉电机驱动第二滑块移动,第二滑块上设有与第二丝杆垂直的第二直线滑轨,第二直线滑轨的顶部设有滑板且滑板可在第二直线滑轨上滑动,滑板的顶面两端分别设有固定座和夹紧气缸,滑板远离夹紧气缸的侧面设有第二固定块,第二固定块与第二直线滑轨之间设有归位弹簧。
[0015]
在其中一个实施例中,自动左右夹紧平衡机构未夹紧管材时,所述固定座与管材之间的距离为5~10mm。
[0016]
在其中一个实施例中,本发明还包括手动控制电路,手动控制电路分别与前驱管锯头、后驱管锯头、后锯台电机相连,手动控制、自动控制通过手动切换开关进行切换。
[0017]
本发明的优点和有益效果:
[0018]
本发明采用的是全自动化,节省材料、时间、人力,本发明下料机的结构配合其使用方法避免了现有技术夹料部分的浪费。
[0019]
1、本发明自动推管机构的设计,无论长管材还是短管材的切割都无需人工时刻监工,只需将管材一次堆积排列放在管子排列机构内即可,后续依靠自动横向推管机构和自动轴向推管机构自动推送,省时省力,节约人工监工成本。
[0020]
2、本发明报警感光头的设计,当报警感光头感应不到管材时,会自动报警,提醒工作人员缺管需要增补管材。
[0021]
3、本发明为了保证切管长度的准确,采用了前驱管锯头固定,后驱管锯头可在机架上移动数控调节距离。
[0022]
4、本发明导向托辊轮的设计,主要作用是托住管材。
[0023]
5、本发明自动左右夹紧平衡机构的设计,可以保证数控后拉机构在拉动管材的过
程中,自动左右夹紧平衡机构与管材的轴线保持在同一轴线上,当未夹紧管材时,固定座与管材之间的距离为5~10mm,主要避免管材送管时碰固定座。
[0024]
6、本发明还可以手动控制、自动控制进行切换。
附图说明
[0025]
图1是本发明的主视图。
[0026]
图2是本发明的俯视图。
[0027]
图3是本发明自动横向推管机构的结构示意图。
[0028]
图4为本发明前驱数控滚动输送架的侧视图。
[0029]
图5为本发明前驱数控滚动输送架的俯视图。
[0030]
图6为本发明前驱数控滚动输送架的仰视图。
[0031]
图7为本发明导向托滚轮的结构示意图。
[0032]
图8为本发明导向托滚轮的俯视图。
[0033]
图9为本发明数控后拉机构的侧视图。
[0034]
图10为本发明数控后拉机构的俯视图。
[0035]
图11为图10的a-a剖视图。
具体实施方式
[0036]
为了便于理解本发明,下面将参照相关附图对本发明进行更全面的描述。附图中给出了本发明的首选实施例。但是,本发明可以以许多不同的形式来实现,并不限于本文所描述的实施例。相反地,提供这些实施例的目的是使对本发明的公开内容更加透彻全面。
[0037]
需要说明的是,当元件被认为是“设置”在另一个元件上,它可以是直接设置或连接在另一个元件上或者可能同时存在居中元件。术语“中心”、“纵向”、“横向”、“长度”、“宽度”、“厚度”、“上”、“下”、“前”、“后”、“左”、“右”、“竖直”、“水平”、“顶”、“底”、“内”、“外”、“顺时针”、“逆时针”等指示的方位或位置关系为基于附图所示的方位或位置关系,仅是为了便于描述本发明和简化描述,而不是指示或暗示所指的设备或元件必须具有特定的方位、以特定的方位构造和操作。
[0038]
除非另有定义,本文中所使用的所有的技术和科学术语与本发明的技术领域的技术人员通常理解的含义相同。说明书中所使用的术语只是为了描述具体的实施目的,不是旨在限制本发明。
[0039]
实施例1
[0040]
请参阅图1至图11,一种用于门窗管材双锯头全自动下料机,包括机架1、控制模块、从右至左依次设置在机架1上的自动推管机构2、数控后拉机构3、前驱管锯头4、后驱管锯头5。前驱管锯头4的右端设有前驱数控滚动输送架6,前驱管锯头4的左端设有中驱数控滚动输送架7,后驱管锯头5上靠近中驱数控滚动输送架7的那端设有后驱数控滚动输送架8。若干个导向托滚轮9设置在机架1上对应前驱管锯头4和后驱管锯头5的下方。所述前驱管锯头4固定在机架1上。第一丝杆10的一端连接后锯台电机11,所述后驱管锯头5由第一丝杆10带动可在机架1上移动。所述前驱管锯头4的底部设有原点感光头41。控制模块分别与自动推管机构2、数控后拉机构3、前驱数控滚动输送架6、原点感光头41、前驱管锯头4、中驱数
控滚动输送架7、后驱数控滚动输送架8、后驱管锯头5、导向托滚轮9、后锯台电机11相连。
[0041]
如图1至图3,自动推管机构2包括管子排列机构21、二个自动横向推管机构22、自动轴向推管机构23。自动轴向推管机构23设置在机架1上远离后驱管锯头5的端部。二个自动横向推管机构22设置在机架1的侧面,且每个自动横向推管机构22都与自动轴向推管机构23垂直设置。管子排列机构21设置在机架1的顶面对应靠近自动横向推管机构22的那侧。若干根管材12对齐排列在管子排列机构21内。管子排列机构21的下部设有二个报警感光头24,管子排列机构21的对侧设有若干个第一侧压滚轮25。
[0042]
如图3,每个所述自动横向推管机构22都包括横向推进气缸221、第一直线滑轨222、第一滑块223、活动舌220、第一弹簧225、第一孔226。机架1上对应自动横向推管机构22处设有第一孔226。第一滑块223的下部套设在第一直线滑轨222上,且第一滑块223可在第一直线滑轨222上滑动。第一直线滑轨222固定在机架1上对应管子排列机构21的下方。第一滑块223上部的一端固定有横向推进气缸221。第一滑块223的顶面设有定位套筒227,定位套筒227的顶面不高于管子排列机构21内最底部的管材12底面。第一滑块223的上部对应定位套筒227处开设有定位杆孔224,定位杆228的一端穿过定位杆孔224与限位块229固定,另一端固定有活动舌220,且活动舌220可沿定位套筒227上下滑动。第一弹簧225套设于定位杆228上,且第一弹簧225处于第一滑块223顶面与活动舌220底面之间。
[0043]
其中,活动舌220的上部为竖直面201和倾斜面202形成的夹角,且倾斜面202朝向管子排列机构21。
[0044]
所述自动轴向推管机构23包括轴向推进气缸如图2。
[0045]
如图4至图6,所述前驱数控滚动输送架6包括压紧气缸61、上压紧轮62、侧面定位轮63、侧压气缸64、第二侧压滚轮65、驱动轮66、前驱电机67、第一感光头68。管材12的上方设有由压紧气缸61控制的上压紧轮62。管材12的两侧分别设有侧面定位轮63和由侧压气缸64控制的第二侧压滚轮65。管材12的底部设有由前驱电机67控制的驱动轮66。所述驱动轮66的右方设有第一感光头68。
[0046]
如图1、图2、图4、图5和图6,所述中驱数控滚动输送架7和后驱数控滚动输送架8的结构都与前驱数控滚动输送架6的结构一致。其中,如图2,中驱数控输送架7的驱动轮由中驱电机71控制,后驱数控输送架8的驱动轮由后驱电机81控制,中驱数控输送架71的驱动轮的右方设置的是第二感光头72,后驱数控输送架8的驱动轮的右方设置的是第三感光头82。
[0047]
如图1、图2、图7和图8,每个所述导向托滚轮9包括导向架91、喇叭导向机构92、托辊轮93、升降气缸94、左感光头95、右感光头96、托辊轮电机97。升降气缸94的顶部设有导向架91。导向架91上设有托辊轮93和托辊轮电机97。托辊轮电机97驱动托辊轮93。导向架91上对应托辊轮93的上部设有喇叭导向机构92。机架1上对应托辊轮93一端的左、右二侧分别设有左感光头95和右感光头96。
[0048]
如图8,喇叭导向机构92包括二个平行设置的第一固定块921,且二个第一固定块921的内侧形成两端大、中间小的通道。
[0049]
如图9至图11,所述数控后拉机构3包括自动左右夹紧平衡机构、第二丝杆32和数控后拉电机33,数控后拉电机33设置在机架1上。
[0050]
自动左右夹紧平衡机构包括第二滑块311、第二直线滑轨312、滑板313、归位弹簧314、固定座315、夹紧气缸316。第二丝杆32与第二滑块311配合,一端连接数控后拉电机33,
并由数控后拉电机33驱动第二滑块311移动。第二滑块311上设有与第二丝杆32垂直的第二直线滑轨312。第二直线滑轨312的顶部设有滑板313且滑板313可在第二直线滑轨312上滑动。滑板313的顶面两端分别设有固定座315和夹紧气缸316。滑板313远离夹紧气缸316的侧面设有第二固定块317,第二固定块317与第二直线滑轨312之间设有归位弹簧314。
[0051]
其中,自动左右夹紧平衡机构未夹紧管材时,所述固定座315与管材12之间的距离为5~10mm。
[0052]
本发明还包括手动控制电路,手动控制电路分别与前驱管锯头4、后驱管锯头5、后锯台电机11相连,手动控制、自动控制通过手动切换开关进行切换。
[0053]
请参阅图1至图11,上述用于门窗管材双锯头全自动下料机的使用方法:当进行长管材切割时,包括以下步骤:
[0054]
1)放管材:将管材12对齐排列放置在管子排列机构21内。
[0055]
2)横向推动管材:利用自动横向推管机构22将管子排列机构12内最底层
[0056]
的一根管材12推到自动送料位置上;推走最底层的一根后,倒数第二底层的管材12会掉下来替代被推走的管材成为管子排列机构12内的最底层的管材,依次循环
……
。
[0057]
3)轴向推动管材:利用自动轴向推管机构23的轴向推进气缸将自动送料位
[0058]
置上的管材向数控后拉机构3方向推进。
[0059]
4)第一位置定位找正:当管材12移动到前驱数控滚动输送架6上时,第一
[0060]
感光头68感应到管材后,控制模块控制压紧气缸61带动上压紧轮62下压,侧压气缸64带动第二侧压滚轮65压紧管材12侧面,管材12在前驱数控滚动输送架6上完成第一位置找正;同时启动前驱电机67和托辊轮电机97,管材进入数控滚动送料阶段,此时,自动轴向推管机构23的轴向推进气缸恢复至原始位置。
[0061]
5)第二位置定位找正:当原点感光头41感应到管材12时,前驱数控滚动
[0062]
输送架6开始进入程序定量定尺输送。
[0063]
当管材12移动到中驱数控滚动输送架7上时,第二感光头72感应到管材
[0064]
12后,控制模块控制压紧气缸61带动上压紧轮62下压,侧压气缸64带动第二侧压滚轮65压紧管材12侧面,管材12在中驱数控滚动输送架7上完成第二位置找正;同时启动中驱电机71。
[0065]
6)移动后驱管锯头5:控制模块控制后锯台电机11驱动第一丝杆10带动
[0066]
后驱管锯头5在机架1上向左或向右移动到一定位置。
[0067]
7)第三位置找正:当管材12移动到后驱数控滚动输送架8上时,第三感光
[0068]
头82感应到管材12后,控制模块控制压紧气缸61带动上压紧轮62下压,侧压气缸64带动第二侧压滚轮65压紧管材12侧面,管材12在后驱数控滚动输送架8上完成第三位置找正;同时启动后驱电机81。
[0069]
8)切割:当数控定尺定量送到位后,关闭前驱电机67、中驱电机71、后
[0070]
驱电机81和托辊轮电机97;然后前驱管锯头4和后驱管锯头5同时切割。
[0071]
当进行短管材切割时,包括以下步骤:
[0072]
1)放管材:将管材12对齐排列放置在管子排列机构21内。
[0073]
2)横向推动管材:利用自动横向推管机构2将管子排列机构21内的最底层
[0074]
的一根管材12推到自动送料位置上;推走最底层的一根后,倒数第二底层的管材
12会掉下来替代被推走的管材成为管子排列机构21内的最底层的管材,依次循环
……
。
[0075]
3)轴向推动管材:利用自动轴向推管机构23的轴向推进气缸将自动送料位置上的管材12向数控后拉机构3方向推进。
[0076]
4)第一位置定位找正:当管材移动到前驱数控滚动输送架6上时,第一感
[0077]
光头68感应到管材12后,控制模块控制压紧气缸61带动上压紧轮62下压,侧压气缸64带动第二侧压滚轮65压紧管材12侧面,管材12在前驱数控滚动输送架6上完成第一位置找正;同时启动前驱电机67和托辊轮电机97,管材进入数控滚动送料阶段,此时,自动轴向推管机构23的轴向推进气缸恢复至原始位置。
[0078]
5)第二位置定位找正:当原点感光头41感应到管材12时,前驱数控滚动
[0079]
输送架6开始进入程序定量定尺输送。
[0080]
当管材12移动到中驱数控滚动输送架7上时,第二感光头72感应到管材
[0081]
12后,控制模块控制压紧气缸61带动上压紧轮62下压,侧压气缸64带动第二侧压滚轮65压紧管材12侧面,管材12在中驱数控滚动输送架7上完成第二位置找正;同时启动中驱电机71。
[0082]
6)移动后驱管锯头:控制模块控制后锯台电机11驱动第一丝杆10带动后
[0083]
驱管锯头5在机架上向左或向右移动到一定位置。
[0084]
7)第三位置找正:当管材12移动到后驱数控滚动输送架8上时,第三感光
[0085]
头82感应到管材12后,控制模块控制压紧气缸61带动上压紧轮62下压,侧压气缸64带动第二侧压滚轮65压紧管材12侧面,管材12在后驱数控滚动输送架8上完成第三位置找正;同时启动后驱电机81。
[0086] 8)第一次切割:当数控定尺定量送到位后,关闭前驱电机67、中驱电机71、后驱电机81和托辊轮电机97,然后数控后拉机构3的自动左右夹紧平衡机构将管材12夹紧,再用后驱管锯头5切割,前驱管锯头4不切割。
[0087]
9)第二次切割:第一次切割完成后,解除第一位置找正、第二位置找正和第三位置找正;
[0088]
然后数控后拉机构3的数控后拉电机33通过第二丝杆32将管材12定尺拉到短管材所需尺寸后,再完成第一位置找正、第二位置找正和第三位置找正,最后前驱管锯头4开始切割,完成了短管材的自动下料。
[0089]
需要说明的是:当本发明手动进行管材12切割时,包括以下步骤:先将程序打到手动位,通过数控调前驱管锯头4和后驱管锯头5位置,其位置距离为定尺下料长度,然后开始下料。
[0090]
本发明的工作原理及其工作过程:
[0091]
当报警感光头24感应不到管材时,会自动报警,提醒工作人员缺管需要增
[0092]
补管材12。
[0093]
自动横向推管机构22的工作过程如图3:当横向推进气缸221沿着第一直线滑轨222向前推进时,第一滑块223上的活动舌220的竖直面201将管材12推到自动送料位置(自动送料位置指的是管子排列机构21与第一侧压滚轮25的中间)上如图3。当横向推进气缸221沿着第一直线滑轨222向后垃回时,第一滑块223上的活动舌220的倾斜面202从管材12底部滑过去,滑过管材12底部后,活动舌220在第一弹簧225的作用下升起,等待第2次循环
推管材。
[0094]
导向托滚轮9的工作如图7、图8、图1和图2:当后驱管锯头5向左或右移动时,当左感光头95或右感光头96感应到后驱管锯头5的工作台面时,与该感光头对应的导向架91在升降气缸94作用力下,导向架91下降,沉在后驱管锯头5的工作台面下面,这样导向架91不会影响后驱管锯头5的工作台面的左右移动。当下料完成后,控制模块控制升降气缸94使得导向架91升至原来的位置。
[0095]
自动左右夹紧平衡机构的工作如图9至图11:当自动左右夹紧平衡机构未夹紧管材时,固定座315与管材12侧面有5~10mm距离,主要避免管材12送管时碰固定座315,同时由于管材12与固定座315位于二个平面,很难将二个不同的面调到平行,如果管材12与固定座315调不到平行,就会造成管材12在后拉过程中,管材12易卡死从而影响短管切割精度。当不夹紧管材12时,归位弹簧314将滑板313上的固定座315推离管材(12)5~10mm,防止送管时管头顶到固定座315上。当夹紧气缸316夹紧管材12时,此时归位弹簧314被压缩,固定座315向管材12方向移动,完成自动后拉左右夹紧平衡找正功能。
[0096]
本发明所述的实施例仅仅是对本发明的优选实施方式进行的描述,并非对本发明构思和范围进行限定,在不脱离本发明设计思想的前提下,本领域中工程技术人员对本发明的技术方案做出的各种变型和改进,均应落入本发明的保护范围, 本发明请求保护的技术内容,已经全部记载在权利要求书中。
起点商标作为专业知识产权交易平台,可以帮助大家解决很多问题,如果大家想要了解更多知产交易信息请点击 【在线咨询】或添加微信 【19522093243】与客服一对一沟通,为大家解决相关问题。
此文章来源于网络,如有侵权,请联系删除



tips