一种分段式高速钢扁丝热轧生产线及其走丝速度控制方法与流程



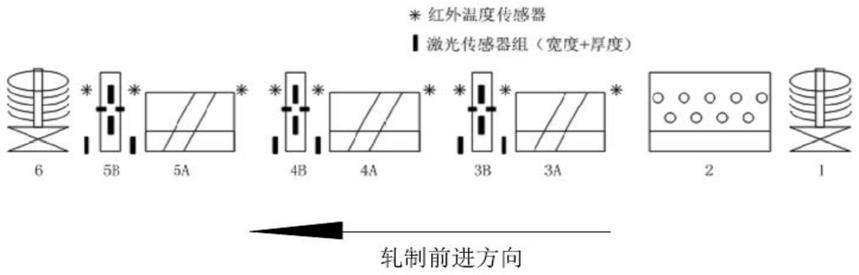
一种分段式高速钢扁丝热轧生产线及其走丝速度控制方法
【技术领域】
[0001]
本发明涉及一种高速钢扁丝热轧生产线,具体涉及一种分段式高速钢扁丝 热轧生产线及其走丝速度控制方法。
背景技术:
[0002]
高速钢扁丝(又称高速钢扁丝带、高速钢扁钢带等)的宽度通常在5~25 毫米之间,厚度通常在1~5毫米之间。高速钢扁丝可进一步被切割成长度在 10~50毫米之间的颗粒状,该颗粒可被用作为多个行业多个领域关键零部件的 原材料,例如用作油压泵、液压泵、助力泵等泵体内的转向叶片,用作木工行 业、缝纫行业的刀具与刃具材料,用作集中式空调、新风系统、风机盘管的导 风叶片,等等。
[0003]
高速钢扁丝的传统加工方法为通过纵剪高速钢宽钢带得到,即通过剪切机 施加巨大的冲击力,对高速钢宽钢带进行从上而下的纵切。该方法的优点是加 工难度小,曾是行业内的常用方法,但该方法的缺点是裁切走刀过程中的横向 张力容易造成弯曲和扭折现象,导致材料浪费。
[0004]
针对上述现象,国外逐渐采用直接轧制这种新型高速钢扁丝加工方法,即 通过放卷收卷、热装热送、立棍轧机等多类机器之间的配合轧制,直接将高速 钢圆丝加工成高速钢扁丝,这种方法属于免切削加工方法,具有效率高、节省 材料等优点,在钢铁行业节能减排的大背景下,直接轧制法越来越受到行业的 认可。
[0005]
然而,由于高速钢材料的特殊性,尤其是高速钢材料抗拉性能的欠缺,上 述直接轧制方法只被国外少数几家公司掌握,国内很多公司虽然照搬了国外生 产线的机器设备,但仍无法掌握其生产工艺,尤其是未掌握热轧时走丝速度的 控制方法:走丝速度过慢时,虽可提高扁丝质量,但却使其产品成本远超国外 同类产品;走丝速度过快时往往出现“一拉即断”的现象。综上所述,高速钢 扁丝的轧制,不仅需要成套机器设备,更需要掌握其工艺和控制方法。
技术实现要素:
[0006]
为了解决背景技术中的问题,本发明提出了一种分段式高速钢扁丝热轧生 产线及其走丝速度控制方法,实现高速钢扁丝连续、稳定、经济的热轧。
[0007]
本发明采用的技术方案如下:
[0008]
一种分段式高速钢扁丝热轧生产线,包括放卷用的放卷装置、预校直用的 预校直装置,高速钢经预校直后分别经过粗轧装置、精轧装置、细轧装置,所 述热轧生产线还包括检测系统,所述检测系统用于检测所述粗轧装置、精轧装 置、细轧装置三个轧制装置,各自在入口处和出口处设有用于检测高速钢扁丝 温度值的温度传感器,以及用于检测高速钢扁丝宽度值和厚度的激光传感器。
[0009]
采用本发明的有益效果:
[0010]
本发明中,对高速钢扁丝进行分段式轧制,具体分为粗轧装置、精轧装置、 细轧装
置,这样可以实现逐步阶段轧制,逐步渐进地完成高速钢圆料向高速钢 扁丝的轧制,所生产的高速钢扁丝具有抗拉强度高、截面尺寸一致、尺寸公差 范围小等优点。
[0011]
同时较为关键的是,本发明中还设置一个检测系统,该检测系统主要针对 于检测粗轧装置、精轧装置、细轧装置三个轧制装置,各自在入口处和出口处 的温度值,同时还要检测在入口处和出口处的高速钢扁丝宽度值和厚度,利用 这些检测到的数值,可以用来合理调整整个生产线的走丝速度,有了合理的走 丝速度,可以避免走丝速度过慢提升成本,又避免速度过快影响质量甚至拉断 扁丝,减少高速钢扁丝在轧制过程中被拉断的几率。
[0012]
作为优选,所述的粗轧装置、精轧装置、细轧装置,每个装置均包括感应 加热炉和多辊轧机机组。
[0013]
作为优选,所述检测系统包括九个温度传感器,其中第一与第二红外温度 传感器分别布置在粗轧装置的感应加热炉入口处与出口处,第四与第五红外温 度传感器分别布置在精轧装置的感应加热炉入口处与出口处,第七与第八红外 温度传感器分别布置在细轧装置的感应加热炉入口处与出口处,第三、第六、 第九红外温度传感器分别布置在粗轧、精轧、细轧装置多辊轧机机组出口处。
[0014]
作为优选,所述检测系统包括六个激光传感器,其中第一与第二激光传感 器组分别布置在粗轧装置的多辊轧机机组入口处与出口处,第三与第四激光传 感器组分别布置在精轧装置的多辊轧机机组入口处与出口处,第五与第六激光 传感器组分别布置在细轧装置的多辊轧机机组入口处与出口处。
[0015]
作为优选,所述粗轧装置、精轧装置、细轧装置中的多辊轧机机组为四辊 轧机机组;和/或,所述的预校直装置为多辊轧机,且辊轴数量为6到9个。
[0016]
另外,本发明还公开了一种分段式高速钢扁丝热轧生产线的走丝速度控制 方法,采用了上述任意一种方案中的分段式高速钢扁丝热轧生产线,走丝速度 控制方法包括:初始参数设定、热轧状态监控、走丝速度计算三个步骤。
[0017]
作为优选,所述的初始参数设定,根据高速钢牌号,通过查表确定整条流 水线的初始走丝速度,并分配粗轧装置、精轧装置、细轧装置的初始延展率设 定值。
[0018]
作为优选,所述的热轧状态监控,通过检测粗轧装置、精轧装置、细轧装 置的感应加热炉入口处和出口处的六个温度值,粗轧装置、精轧装置、细轧装 置多辊轧机机组出口处的三个温度值,粗轧装置、精轧装置、细轧装置多辊轧 机机组入口处和出口处的六个宽度值与厚度值。
[0019]
作为优选,所述的走丝速度计算,首先分别计算粗轧装置最高允许走丝速 度、精轧装置最高允许走丝速度、细轧装置最高允许走丝速度,选取上述三个 最高允许走丝速度中的最小值,作为初步计算的走丝速度,
[0020]
粗轧装置最高允许速度的计算:
[0021][0022]
上式中,v1表示粗轧装置最高允许走丝速度,minf(x)表示满足h(x)、 t(x)条件的
x的最小值,x
d
表示理论上最大允许的走丝速度,
[0023]
h(x)表示走丝速度、加热功率、加热总量之间的关系,计算公式如下:
[0024][0025]
上式中,a表示加热系数,d表示高速钢扁丝的厚度,b为感应加热炉的厚 度,h表示感应加热炉的最大加热功率;
[0026]
t(x)表示走丝速度与高速钢扁丝温升之间的关系,计算公式如下;
[0027][0028]
上式中,c为比热容,t0为加热前温度,l,d分别为高速钢扁丝横截面宽 度、横截面厚度,p表示高速钢扁丝的密度,t为可热轧的最低温度值;
[0029]
精轧装置最高允许速度的计算:
[0030][0031]
上式中,v2表示精轧装置最高允许走丝速度;δh1表示粗轧阶段的热耗 散量;t1和t2表示热轧性能最好的温度下限和上限;
[0032]
细轧装置最高允许速度的计算:
[0033][0034]
上式中,v3表示细轧装置最高允许走丝速度;δh2表示精轧阶段的热耗 散量;t1和t2表示热轧性能最好的温度下限和上限;
[0035]
流水线走丝速度的计算:v=min(v1,v2,v3);上式中,v表示整条流水 线的走丝速度。
[0036]
作为优选,还包括走丝速度优化步骤,所述的走丝速度优化步骤为,分别 计算粗轧工序、精轧工序、细轧工序的实际延展率与设定延展率之间的差值, 对延展率差值最小的工序,按照预先设定的值,步进式降低其设定延展率,以 提高其实际延展率和设定延展率之间的差,对延展率差值最大的工序,按照预 先设定的值,步进式提高其设定延展率,以降低其实际延展率和设定延展率之 间的差值,重复该步骤,以使粗轧工序、精轧工序、细轧工序的实际延展率与 设定延展率之间的差值趋于一致,实际延展率的计算公式如下:
[0037][0038]
上式中,l1,d1分别表示轧制后的高速钢扁丝横截面宽度、横截面厚度,l2, d2分别表示轧制前的高速钢扁丝横截面宽度、横截面厚度、高速钢扁丝长度。
[0039]
本发明的其他技术效果,在下文的具体实施方式进行具体展开说明。
【附图说明】
[0040]
图1是本发明流水线内各传感器的布置位置示意图。
[0041]
图2是本发明流水线的走丝速度控制方法流程图。
[0042]
图中:1、放卷装置,2、预校直装置,3、粗轧装置,3a、粗轧装置的感 应加热炉,3b、粗轧装置的四辊轧机组,4、精轧装置,4a、精轧装置的感应 加热炉,4b、精轧装置的四辊轧机组,5、细轧装置,5a、细轧装置的感应加 热炉,5b、细轧装置的四辊轧机组,6、收卷装置。
【具体实施方式】
[0043]
以下结合附图和实施例对本发明做进一步的说明。
[0044]
如图1所示,本发明提出的分段式高速钢扁丝连轧生产线,依次包括放卷 装置1、预校直装置2、粗轧装置3、精轧装置4、细轧装置5、收卷装置6, 另外再辅以检测系统和主控系统。本发明将高速钢扁丝的热轧过程分为粗轧、 精轧、细轧三段。其中粗轧在其功率范围内尽可能加热高速钢扁丝,进而在高 速钢扁丝可承受的抗拉范围内尽可能提高其延展率;精轧通过精确控温,对高 速钢扁丝实现深度加热,使其内部温度与表面温度一致,进而使高速钢扁丝的 延展率趋于目标值;最后的细轧则通过精确控温,实现高速钢扁丝的宽度、厚 度等尺寸完全达到精度要求。
[0045]
在图1中,放卷装置1和收卷装置6可采用立式或卧式放卷机/收卷机;预 校直装置2可采用市面上常见的多辊轧机(如九辊轧机),预校直过程属于未 经加热的冷轧,主要目的为将卷状的高速钢圆丝拉直并初步轧制为扁状。粗轧 装置3、精轧装置4、细轧装置5分别有感应加热机和多辊轧机机组成,其中 感应加热机为非接触式感应加热,而多辊轧机机组优选是四辊轧机,数量可在 1到3台之间,可根据高速钢材料的抗拉性能和延展性能灵活决定。
[0046]
检测系统包括九个红外温度传感器和六个激光传感器,其中红外温度传感 器可在非接触的情况下实现高速钢扁丝的温度测量,激光传感器组包括激光式 宽度传感器与激光式厚度传感器两类,以实现对高速钢扁丝的宽度、厚度参数 的非接触测量。
[0047]
需要说明的是,高速钢圆料在上本系统之前,优选要做好剥皮、抛光、烘 干等准备工作,当然实现上述工艺的机器也可以与本发明组成成套设备使用。 另外,本发明也可以与高频退火装置、自然冷却装置等联合使用,以实现高速 钢扁丝的热轧、冷轧等多种工艺。
[0048]
图1中也展示了九个红外温度传感器、六个激光传感器在本发明流水线的 布置位置示意图。如图1所示,第一与第二红外温度传感器分别布置在粗轧装 置3的感应加热炉3a入口处与出口处,第四与第五红外温度传感器分别布置 在精轧装置4的感应加热炉4a入口处与出口处,第七与第八红外温度传感器 分别布置在细轧装置5感应加热炉5a入口处与出口处。上述传感器的布置方 法,可使本系统计算得到不同牌号不同材料的高速钢扁丝走丝
速度、感应加热 炉加热功率、环境温度、加热前后温升这四类参数之间的函数关系,即得到函 数h(x)的关系表达式。同时,粗轧工序h(x)的计算,也可以为精轧工序和细轧 工序的精确加热控温t(x)的计算提供数学基础。
[0049]
如图1所示,第一与第二激光传感器分别布置在粗轧装置3的四辊轧机机 组3b入口处与出口处,第三与第四激光传感器组分别布置在精轧装置4的四 辊轧机机组4b入口处与出口处,第五与第六激光传感器组分别布置在细轧装 置5的四辊轧机机组5b入口处与出口处。上述传感器布置方法,可计算得到 各段轧制前后的高速钢扁丝延展率(延展率指轧制后扁丝截面矩形参数除以轧 制前扁丝截面矩形参数)。
[0050]
如图1所示,第三、第六、第九红外温度传感器分别布置在粗轧装置3、 精轧装置4、细轧装置5的四辊轧机机组出口处,结合各感应加热炉出口处的 第二、第五、第八红外温度传感器,同时结合上述各激光传感器组的检测参数, 可计算得到高速钢扁丝走丝速度、轧制前后延展率、环境温度、轧制过程热耗 散量之间的关系,为下一段感应加热炉的精确控温量δh提供数学基础。
[0051]
图2是本发明对轧制过程中走丝速度的控制方法流程图。本发明重点解决 走丝速度的计算和优化选择,因为不同牌号高速钢(其材料参数差异性巨大)、 不同预处理工艺(其轧制性能差异较大)、不同轧制环境(对温控要求不同) 等,都将影响高速钢扁丝的最优走丝速度。本发明通过自适应自动化的走丝速 度调整方法,既避免走丝速度过慢导致的成本过高,又避免走丝速度过快引起 的质量下降甚至拉断现象。
[0052]
如图2所示,本发明提出的走丝速度控制方法包括步骤如下:初始参数设 定、热轧状态监控、走丝速度计算。
[0053]
所述的初始参数设定,根据高速钢牌号,通过查表格确定整条流水线的初 始走丝速度,并分配粗轧、精轧、细轧的初始最低延展率设定值。该表格为历 史经验数据,由以往人工调控过程中数据积累而成。需要说明的是,即使相同 的高速钢牌号,所设定的初始走丝速度,往往会比历史经验走丝速度低,例如 取值为历史经验走丝速度的80%,以此避免不同预处理工艺、不同环境参数等 带来的影响,防止一开机即拉断高速钢扁丝。后续通过走丝速度自适应调整方 法,逐步将走丝速度提升至正常水平。
[0054]
所述的热轧状态监控,通过检测粗轧、精轧、细轧感应加热前后的六个温 度参数,粗轧、精轧、细轧四辊轧机前后的六个宽度与厚度参数,粗轧、精轧、 细轧四辊轧机之后的三个温度参数,用于后续计算使用。
[0055]
所述的走丝速度计算,首先分别计算粗轧装置3最高允许走丝速度、精轧 装置4最高允许走丝速度、细轧装置5最高允许走丝速度,然后计算流水线走 丝速度,即在上述三个速度中取其最小值。
[0056]
粗轧装置3最高允许速度的计算:
[0057][0058]
上式中,v1表示粗轧装置3最高允许走丝速度,minf(x)表示满足h (x)、t(x)条件
的x的最小值,x
d
表示理论上最大允许的走丝速度,
[0059]
h(x)表示走丝速度、加热功率、加热总量之间的关系,计算公式如下:
[0060][0061]
上式中,a表示加热系数,d表示高速钢扁丝的厚度,b为感应加热炉的厚 度,h表示感应加热炉的最大加热功率;
[0062]
t(x)表示走丝速度与高速钢扁丝温升之间的关系,计算公式如下;
[0063][0064]
上式中,c为比热容,t0为加热前温度,l,d分别为高速钢扁丝横截面宽 度、横截面厚度,p表示高速钢扁丝的密度,t为可热轧的最低温度值;
[0065]
另外,需要说明的是,在粗轧装置3的走丝速度计算时,优选也要考虑高 速钢扁丝的实际延展率,优选是实际延展率要大于粗轧工序所需要完成的最低 延展率c1,实际的延展率计算为:
[0066][0067]
上式中,l1,d1分别表示轧制后的高速钢扁丝横截面宽度、横截面厚度,l2, d2分别表示轧制前的高速钢扁丝横截面宽度、横截面厚度、高速钢扁丝长度。 由于不同的走丝速度会影响到l1,d1,l2,d2的数值变化,所以在最终计算出走 丝速度时,也需要考虑是否满足c(x)≥c1,如不满足,则适当调整走丝速度 的最终值,这一步为辅助选择。
[0068]
精轧装置4最高允许速度的计算:
[0069][0070]
上式中,v2表示精轧装置4最高允许走丝速度;δh1表示粗轧阶段的热 耗散量;t1和t2表示热轧性能最好的温度下限和上限;同理,在精轧工序中, v2的选择也优选要满足c(x)≥c2,其中c2是精轧工序中所需要完成的最 低延展率。
[0071]
细轧装置5最高允许速度的计算:
[0072][0073]
上式中,v3表示细轧装置5最高允许走丝速度;δh2表示精轧阶段的热 耗散量;t1
和t2表示热轧性能最好的温度下限和上限;同理,在细轧工序中, v3的选择也优选要满足c(x)≥c3,其中c3是精轧工序中所需要完成的最 低延展率。
[0074]
依据上面计算和辅助选择后,得出粗轧、精轧、细轧中的走丝速度v1、 v2、v3,而最终的整个生产线的流水线走丝速度的计算为v= min(v1,v2,v3)。
[0075]
为了进一步优化走丝速度,本方法中还加入了走丝速度优化步骤为,具体 为:首先根据上文c(x)的函数,分别计算粗轧、精轧、细轧的当前实际延展 率与设定最低延展率之间的差值δc,即δc1、δc2、δc3。对延展率差值最 小的工序,按照预先设定的值,步进式降低其设定延展率,以提高其实际延展 率和设定延展率之间的差,对延展率差值最大的工序,按照预先设定的值,步 进式提高其设定延展率,以降低其实际延展率和设定延展率之间的差值,重复 该步骤,以使粗轧工序、精轧工序、细轧工序的实际延展率与设定延展率之间 的差值,即δc1、δc2、δc3趋于一致。
[0076]
综上所述,本发明适用于高速钢扁丝的生产厂家,其生产的m2、m3、m4、 m42等高速钢扁丝,可用以替代目前被国外产品垄断的、售价高昂的高速钢扁 丝产品。本发明硬件简单,均为可直接采购的现成机器设备,因此具有较好的 推广性。上述具体实施方式用来解释说明本发明,而不是对本发明进行限制, 在本发明的精神和权利要求的保护范围内,对本发明作出的任何修改和改变, 都落入本发明的保护范围。
起点商标作为专业知识产权交易平台,可以帮助大家解决很多问题,如果大家想要了解更多知产交易信息请点击 【在线咨询】或添加微信 【19522093243】与客服一对一沟通,为大家解决相关问题。
此文章来源于网络,如有侵权,请联系删除



tips