一种柴油机电机螺栓孔修复方法与流程



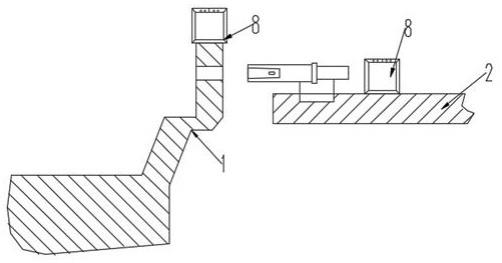
[0001]
本发明涉及螺栓孔修复技术领域,尤其是一种柴油机电机螺栓孔修复方法。
背景技术:
[0002]
机体是柴油机的安装基础,其毛坯为整铸球墨铸铁。在机体后端面有2只1-3/8unf螺栓孔,用于柴油机与电机的连接,由于柴油机与电机位置精度要求较高,位置度要求0.05mm,该2只1-3/8unf的螺栓孔位置精度要求较高,在机体加工时,该螺栓孔与主轴孔等关键部位一次装夹下加工完成。
[0003]
由于电机和柴油机安装连接部位1-3/8unf的螺栓孔螺纹为细牙螺纹,精度较高,旋深较长,组装要求较高,稍有不慎在柴油机与电机安装时会出现螺栓卡死现象,螺纹被破坏,导致无法正常安装,由于螺栓孔精度高、空间有限,柴油机重达20多吨,组装后无法利用大型设备进行返工。如果单独机体利用大型设备进行返工,需要将柴油机进行拆解,面临巨大的损失,且影响产品节点。如果采用手工修磨扩孔后单配螺栓的方案,修复效率低、螺孔位置度极易偏,影响柴油机与电机的正常组装,并且螺栓不能互换,影响后续修理。
技术实现要素:
[0004]
为了克服现有的电机螺栓孔使用大型机床进行修复或者单配该螺栓的的加工方法的不足,弥补在加工时柴油机大解体和需要大型设备周转的局限性,本发明提供了一种柴油机电机螺栓孔修复方法。
[0005]
本发明解决其技术问题所采用的技术方案是:一种柴油机电机螺栓孔修复方法,包括以下步骤:步骤s1:柴油机与万向钻床位置校调;步骤s2:设计制作非标钻铰刀扩孔并攻丝、测量和检验;步骤s3:车床加工内外螺套;步骤s4:镶套;步骤s5:回攻螺纹孔;步骤s6:螺栓组装。
[0006]
根据本发明的另一个实施例,进一步包括步骤s1中采用万向钻床将原螺栓孔进行扩孔,扩孔前,将万向钻床主轴与螺孔中心对齐。
[0007]
根据本发明的另一个实施例,进一步包括万向钻床主轴与螺孔中心对齐的检测方法为:先将柴油机放平,将水平仪放置在柴油机顶面进行检测,保证柴油机顶面前后方向水平,将万向钻床前端主轴伸出部分同样使用水平仪在水平方向校水平,水平方向的校调通过直角尺进行检测,使得钻床主轴与柴油机螺孔垂直。
[0008]
根据本发明的另一个实施例,进一步包括步骤s2中设计并制作带导向的非标钻铰刀进行扩孔,扩孔分为三个工步:工步1:使用非标钻铰刀扩孔,利用刀具前端导向柱进行定位,将原螺纹孔扩孔;
工步2:使用非标钻铰刀扩孔,利用刀具前端导向柱进行定位,将工步1中加工孔进行扩孔;工步3:使用非标钻铰刀扩孔,利用刀具前端导向柱进行定位,将工步2中加工孔进行扩孔。
[0009]
根据本发明的另一个实施例,进一步包括步骤s3中加工内外螺套时,按照原扩孔攻丝的螺纹孔深度高出0.5mm,内孔车螺纹孔,内外加工时,同一次装夹,保证内外螺孔同轴度控制在0.015mm以内。
[0010]
根据本发明的另一个实施例,进一步包括步骤s5中回攻螺纹孔:将螺套外螺纹表面均匀涂抹高强度的螺纹胶,将螺套旋入螺孔后,等待40分钟后,使用丝攻回攻,并使用止通规检查,平面打磨平整。
[0011]
根据本发明的另一个实施例,进一步包括螺纹孔和内外螺套用煤油或者清洗剂清洗。
[0012]
本发明的有益效果是:这种机体电机螺栓孔的修复方法不需要组装后的柴油机大解体,不需要大型设备,操作比较简单,避免螺栓的单配,增强产品在今后检修时零部件的互换性,减少了柴油机组装后电机螺栓孔的返修费用,易于使用推广。
附图说明
[0013]
下面结合附图和实施例对本发明进一步说明。
[0014]
图1是本发明的主视加工示意图;图2是本发明的俯视加工示意图;图3是本发明刀具前端φ32.45非标钻铰刀的结构示意图;图4是本发明刀具前端φ37非标钻铰刀的结构示意图;图5是本发明刀具前端φ42非标钻铰刀的结构示意图;图6是本发明扩孔、攻丝的加工示意图;图7是本发明内外螺套的结构示意图。
[0015]
图中1、柴油机,2、万向钻床,3、刀具前端φ32.45的非标钻铰刀,4、刀具前端φ37的非标钻铰刀,5、刀具前端φ42的非标钻铰刀,6、螺纹孔,7、内外螺套,8、水平仪,9、直角尺。
具体实施方式
[0016]
如图1是本发明的主视加工示意图,一种柴油机电机螺栓孔修复方法,其特征是,包括以下步骤:步骤s1:柴油机1与万向钻床2位置校调;步骤s2:设计制作非标钻铰刀扩孔并攻丝、测量和检验;步骤s3:车床加工内外螺套7;步骤s4:镶套,镶套修复法:对磨损的孔或外圆表面进行机械加工,把内衬套或外衬套以一定的过盈装在孔内或轴承上,在进行机械加工,从而恢复到原来尺寸的修复方法;步骤s5:回攻螺纹孔6;步骤s6:螺栓组装。
[0017]
这种机体电机螺栓孔的修复方法不需要组装后的柴油机大解体,不需要大型设备,操作比较简单,避免螺栓的单配,增强产品在今后检修时零部件的互换性,减少了柴油机组装后电机螺栓孔的返修费用,易于使用推广。
[0018]
本发明所涉及的方法尤其是在柴油机组装完成后,由于异常情况引起的1-3/8unf螺栓孔被破坏,不能正常组装的情况,在不需要柴油机解体、正常摆放的情况下,利用现有的空间和角度,发明的一种对较大螺栓孔进行镶套修复的方法,使其恢复到原有的尺寸,恢复螺栓孔原有的位置和功能,满足柴油机与电机组装要求。
[0019]
该修理方案可运用于其他各类型不便拆解且无法使用大型设备的较大连接螺栓孔的修复,修复效率快、位置精度高,不影响后续使用与修理。
[0020]
所述步骤s1中采用万向钻床2将原螺栓孔进行扩孔,扩孔前,将万向钻床2主轴与螺孔中心对齐。
[0021]
所述万向钻床2主轴与螺孔中心对齐的检测方法为:先将柴油机1放平,将水平仪放置在柴油机顶面进行检测,保证柴油机顶面前后方向水平,将万向钻床(2)前端主轴伸出部分同样使用水平仪在水平方向校水平,水平方向的校调通过直角尺(9)进行检测,使得钻床主轴与柴油机螺孔垂直。
[0022]
如图3、图4、图5所示的非标钻铰刀,所述步骤s2中设计并制作带导向的非标钻铰刀进行扩孔,扩孔分为三个工步:工步1:使用非标钻铰刀3扩孔,利用刀具前端导向柱进行定位,将原螺纹孔6扩孔;工步2:使用非标钻铰刀4扩孔,利用刀具前端导向柱进行定位,将工步1中加工孔进行扩孔;工步3:使用非标钻铰刀5扩孔,利用刀具前端导向柱进行定位,将工步2中加工孔进行扩孔所述步骤s3中加工内外螺套7时,按照原扩孔攻丝的螺纹孔6深度高出0.5mm,内孔车螺纹孔6,内外加工时,同一次装夹,保证内外螺孔同轴度控制在0.015mm以内。
[0023]
所述步骤s5中回攻螺纹孔6:将螺套外螺纹表面均匀涂抹高强度的螺纹胶,将螺套旋入螺孔后,等待40分钟后,使用丝攻回攻,并使用止通规检查,平面打磨平整。
[0024]
所述螺纹孔6和内外螺套7用煤油或者清洗剂清洗。
[0025]
实施例:一种柴油机机体电机螺栓孔修复方案,其方法包括以下步骤:万向钻与柴油机校调
→
利用钻铰刀扩孔并攻丝、测量和检验
→
车内外螺套
→
清洗螺纹孔6并镶套
→
回攻螺纹孔6。
[0026]
如图6所示,采用万向钻床将原螺栓孔进行扩孔,扩孔前,将万向钻床主轴与螺孔中心对齐,其检测方法为:先将柴油机放平,将水平仪放置在柴油机顶面进行检测,保证柴油机顶面前后方向水平,将万向钻床(2)前端主轴伸出部分同样使用水平仪在水平方向校水平,水平方向的校调通过直角尺(9)进行检测,使得钻床主轴与柴油机螺孔垂直。
[0027]
扩孔刀具:使用前端带导向的非标钻铰刀,非标钻铰刀3,导向部位前端导向柱φ32.45
±
0.02mm,刀具直径φ37(0~+0.02)mm;非标钻铰刀4,导向部位前端导向柱φ37
±
0.02mm,刀具直径φ42(0~+0.02)mm;非标钻铰刀5,导向部位前端导向柱φ42
±
0.02mm,刀具直径φ43
±
0.02mm。
[0028]
扩孔分为三个工步:工步1,使用非标钻铰刀3扩孔,利用刀具前端φ32.45
±
0.02mm导向柱进行定位,将原螺纹孔扩孔到φ37(0~+0.02)mm;工步2,使用非标钻铰刀4扩孔,利用刀具前端φ37
±
0.02mm导向柱进行定位,将原螺纹孔扩孔到φ42(0~+0.02)mm;工步3,使用非标钻铰刀5扩孔,利用刀具前端φ42
±
0.02mm导向柱进行定位,将原螺纹孔扩孔到φ43
±
0.02mm。
[0029]
采用万向钻床将原螺栓孔进行钻铰孔,扩大至φ43mm。
[0030]
对扩大的孔进行攻丝,攻成m45
×
2mm螺纹孔6,使用止通规检查,并测量其深度。
[0031]
根据m45
×
2mm的螺纹孔6深度,加工内外均为螺纹的螺套,螺套外螺纹为m45
×
2mm,内螺纹为1-3/8 unf,加工螺套时,内外螺纹应在同一次装夹下完成,加工螺纹前内孔和外径同轴度0.015mm,螺套长度比m45
×
2mm螺纹孔6深度高出0.5mm。
[0032]
使用煤油或者清洗剂清洗干净m45
×
2mm螺纹孔6和螺套,确保无翻边毛刺和杂物。
[0033]
如图7所示,将螺套外螺纹表面均匀涂抹高强度的螺纹胶,将螺套旋入螺孔后,等待40分钟后,使用1-3/8 unf丝攻回攻,并使用止通规检查,平面打磨平整。
[0034]
以上说明对本发明而言只是说明性的,而非限制性的,本领域普通技术人员理解,在不脱离所附权利要求所限定的精神和范围的情况下,可做出许多修改、变化或等效,但都将落入本发明的保护范围内。
起点商标作为专业知识产权交易平台,可以帮助大家解决很多问题,如果大家想要了解更多知产交易信息请点击 【在线咨询】或添加微信 【19522093243】与客服一对一沟通,为大家解决相关问题。
此文章来源于网络,如有侵权,请联系删除



tips