一种用于镁合金锻造轮毂形变热处理强化的预变形装置的制作方法



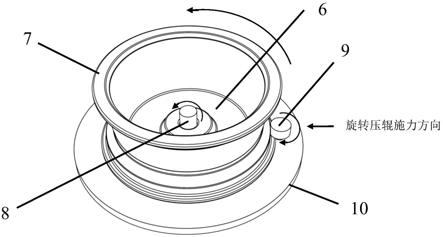
[0001]
本实用新型属于金属材料强韧化技术领域,特别涉及一种用于镁合金锻造轮毂形变热处理强化的预变形装置。
背景技术:
[0002]
轮毂是一种关键性汽车零件,直接影响行驶的舒适性和安全性。随着技术进步,主流汽车轮毂为整体件,用于承载车重、传递动力和轮胎散热,同时,轮毂作为一个旋转运动部件,必须符合轻质、高强度、高弹性模量、耐疲劳等性能要求。轮毂通常由轮辐1、安装盘2、定位孔3、轮辋4、胎圈座5五个主要部分组成,如图1所示。镁合金是目前最轻的金属结构材料,能大幅减重,提高加速和减速性能,降低启动和行驶惯性,有利于提高运行速度,改善操作稳定性,同时降低能耗,另外,镁合金结构件受到冲击载荷时能够吸收较大的冲击功,减震性能良好。镁合金轮毂比目前通用的低压铸造铝合金减重30%~45%左右,一只19寸的镁合金轮毂重8.2公斤,而同型号的铝合金轮毂重13.5公斤。因此,镁合金轮毂的应用对于新能源汽车减重增程意义非凡,对于中国镁工业开启规模化应用大门具有重要的意义,开发高品质镁合金轮毂己成为汽车制造业的全球化课题。从2017年起,中国多家企业投资镁合金轮毂并建成了生产线,典型企业为德威股份、中钰镁业、鼎鑫镁业和闻喜银光。2018年12月26日,中华人民共和国工业和信息化部于发布了《重点新材料首批次应用示范指导目录(2018年版)》(工信部原〔2018〕262号),镁合金轮毂被列入名录。要求性能满足汽车行业标准(gb/t 5334-2005《乘用车车轮性能要求和试验方法》、gb/t 15704-2012《道理车辆轻合金车轮冲击试验方法》、美国saej2530和德国tuv标准),这预示中国镁合金轮毂向大规模应用又向前迈进一步。
[0003]
传统的镁合金轮毂成形方法多采用压铸法,但压铸法容易产生冷隔、气孔等缺陷,组织粗大,其强度、韧性和抗疲劳的性能不及塑性成形轮毂。轮毂的常用的塑性成形方法包括锻造、旋压等,塑性成形法生产的镁合金轮毂具有更高的强度、更好的延展性和更多样化的机械性能,因此开展镁合金轮毂的塑性成形技术和强韧化技术研发意义重大。图2显示了锻造镁合金轮毂的常规生产流程:图2的(a)所示的饼形坯料在锻压机首先被锻压成图2的(b)所示的轮毂坯料,轮毂坯料经机加工和涂装后,成为图2的(c)所示的轮毂成品。轮毂在服役过程中,受力最大的点(危险点)位于轮辐1处,因此,轮辐1处材料需要有较高的力学性能。然而,对于图2所示的锻造工艺,由图2的(a)到图2的(b)的塑性变形过程中,轮辋4处金属发生了巨大的塑性变形量,因此轮辋4处材料的组织细化程度和第二相颗粒破碎程度最大,力学性能最高;然而,轮辐1及安装盘2处金属的变形程度有限,组织细化程度和第二相破碎程度不足,因而力学性能相对较差,这与该位置处的高应力服役条件不匹配。而现有技术尚无针对轮辐和安装盘处材料进行强化处理的研究。
技术实现要素:
[0004]
本实用新型的目的在于,针对现有技术的不足,提供一种用于镁合金锻造轮毂形
变热处理强化的预变形装置,具体技术方案如下:
[0005]
一种用于镁合金锻造轮毂形变热处理强化的预变形装置,包括设置在预变形工作平台10上的旋转芯轴8和旋转压辊9,所述旋转芯轴8位于预变形工作平台10的中心位置,旋转压辊9能自转且能沿预变形工作平台10的径向移动;
[0006]
所述旋转芯轴8穿过轮毂坯料7的定位孔,旋转压辊9与轮毂坯料7的胎圈座贴合,且旋转压辊9轮廓与轮毂坯料7的胎圈座外形匹配。
[0007]
所述旋转压辊9自转带动轮毂坯料7和旋转芯轴8同步旋转。
[0008]
所述轮毂坯料7的定位孔为通孔,优选地,所述轮毂坯料7的定位孔为中心定位孔。
[0009]
所述预变形工作平台10为圆形。
[0010]
所述镁合金包括mg-al系镁合金、mg-zn系镁合金、mg-mn系镁合金、mg-li系镁合金或mg-稀土系镁合金;优选为az80变形镁合金。
[0011]
本实用新型的有益效果为:本实用新型提供的预变形装置能使镁合金锻造轮毂的轮辐处材料发生均匀、连续、缓慢的塑性形变,在大多数晶粒中产生高体积分数的拉伸孪晶,促进时效处理后的连续析出,提高轮辐处材料包括轮辐和安装盘处的力学性能。
附图说明
[0012]
图1为常规一体式轮毂结构示意图;
[0013]
图2为镁合金锻造轮毂常规生产流程;
[0014]
图3为轮毂锻造坯料上的锻造压力方向和轮辐平面;
[0015]
图4为本实用新型预变形装置结构示意图;
[0016]
标号说明:1-轮辐;2-安装盘;3-定位孔;4-轮辋;5-胎圈座;6-轮辐平面;7-轮毂坯料;8-旋转芯轴;9-旋转压辊;10-预变形工作平台。
[0017]
图5为对比例1时效处理后轮毂的显微组织;
[0018]
图6为实施例1时效处理后轮毂的的显微组织。
具体实施方式
[0019]
本实用新型提供了一种用于镁合金锻造轮毂形变热处理强化的预变形装置,下面结合实施例和附图对本实用新型做进一步的说明。
[0020]
如图4所示的用于镁合金锻造轮毂形变热处理强化的预变形装置,包括旋转芯轴8、旋转压辊9和预变形工作平台10,轮毂坯料7在预变形工作平台10上进行预变形。
[0021]
其中,旋转芯轴8和旋转压辊9设置在预变形工作平台10上,所述旋转芯轴8位于预变形工作平台10的中心位置,旋转压辊9能自转且能沿预变形工作平台10的径向移动。
[0022]
其中,所述旋转芯轴8穿过轮毂坯料7的定位孔,能与轮毂坯料7同步旋转。
[0023]
其中,旋转压辊9与轮毂坯料7的胎圈座贴合,且旋转压辊9轮廓与轮毂坯料7的胎圈座外形相匹配,以保证与轮毂坯料7胎圈座的紧密贴合,但要留出足够的间隙满足轮缘在受到压缩载荷时高向的增长。
[0024]
具体地,本发明中的驱动旋转压辊9做径向运动的部件为领域内常规部件,如液压系统。
[0025]
其中,旋转压辊9自转带动轮毂坯料7和旋转芯轴8同步旋转。旋转压辊9沿预变形
工作平台10的径向移动实现对轮毂坯料7的加载和卸载,两种运动同时进行,实现对轮辐1和安装盘2材料的均匀压缩变形。
[0026]
其中,轮毂坯料7的定位孔为通孔。进一步地,轮毂坯料7的定位孔为中心定位孔。
[0027]
其中,预变形工作平台10形状不限,能支撑并固定轮毂坯料7、旋转芯轴8、旋转压辊9即可;预变形工作平台10优选为圆形平台,旋转芯轴8位于预变形工作平台10圆心。
[0028]
本实用新型中所述镁合金包括mg-al系镁合金、mg-zn系镁合金、mg-mn系镁合金、mg-li系镁合金或mg-稀土系镁合金。
[0029]
图4中环形箭头显示了轮毂坯料7、旋转芯轴8和旋转压辊9的旋转运动,还显示了旋转压辊9的施力方向。
[0030]
利用本实用新型预变形装置对镁合金轮毂坯料进行预变形的方法为:
[0031]
将按照常规生产流程(如图2所示生产流程)锻造镁合金坯料得到镁合金轮毂坯料后,将轮毂坯料快速降至室温,将中心定位孔机加工成通孔,给定位孔留出加工余量,然后将定位孔为通孔的轮毂坯料7置于预变形工作平台10上,旋转芯轴8穿过定位孔,移动旋转压辊9直至接触轮毂坯料7的胎圈座,然后旋转压辊9开始自转,带动轮毂坯料7和旋转芯轴8做同步旋转;同时旋转压辊9缓慢向旋转芯轴8移动,从而使得旋转压辊9沿旋转压辊施力方向即轮辐平面径向对镁合金轮毂坯料施压,使轮辐处材料发生均匀、连续、缓慢的压缩变形,塑性应变量0.5~6%。
[0032]
附图中图3是轮毂锻造坯料上的锻造压力方向、轮辐平面径向和轮辋纵向。其中,轮辐平面6优选为圆形,锻造压力方向垂直于轮辐平面6,轮辐平面径向为轮辐平面6的半径方向,轮辋纵向为轮辋4的轴向,如轮辋4垂直于轮辐平面6,则轮辋纵向为垂直于轮辐平面6的方向。图3用以定义轮辐平面及其径向,同时说明锻造压力方向,有助于理解轮辐和安装盘处的织构情况以及引入拉伸孪晶的方法。
[0033]
在高温锻造过程中,轮辐1和安装盘2处镁合金形成织构,即大多数晶粒的[0001]晶向(c轴)平行于锻造压力方向,即大多数晶粒的c轴垂直于轮辐平面6,锻造压力方向和轮辐平面6如图3所示。利用本实用新型预变形装置对镁合金轮毂坯料进行预变形,对镁合金轮毂坯料垂直于大多数晶粒的[0001]晶向(c轴)压缩,优选为在室温至常规镁合金拉伸孪晶形成最高临界温度即300℃之间沿圆形轮辐平面6上经过圆心的方向(即轮辐平面径向,见图3)进行压缩,使得轮辐处材料(轮辐1和安装盘2)发生塑性形变,在大多数晶粒中产生高体积分数的拉伸孪晶,以保证时效处理(时效制度90~250℃、0.5~1000h)后,产生的拉伸孪晶能有效抑制不连续析出相,同时促进均匀弥散分布的连续析出相,从而有效提升轮辐和安装盘处的力学性能。
[0034]
对比例1
[0035]
锻造得到az80变形镁合金轮毂坯料,不进行预变形处理,直接进行时效处理:按照如图2所示的镁合金锻造轮毂常规生产流程制备了镁合金锻造轮毂,其轮辐平面的直径留出机加工余量即可,脱模后对锻造轮毂坯料做空冷和时效处理,时效制度为160℃/12h。发现,发现,显微组织以粗大的不连续析出为主,见图5;轮辐平面6沿轮辐平面径向(图3所示)的室温力学性能为:屈服强度r
p0.2
=150mpa,抗拉强度r
m
=250mpa,延伸率a=6%;轮辋4的轮辋纵向(图3所示)的力学性能为:r
p0.2
=260mpa,r
m
=320mpa,a=5%。可以发现轮辐1处镁合金材料强度显著低于轮辋4处。
[0036]
实施例1
[0037]
锻造得到az80变形镁合金轮毂坯料,先进行预变形处理,再进行时效处理:
[0038]
(1)在利用如图2所示的镁合金锻造轮毂常规生产流程锻造镁合金轮毂过程中,模具设计时给轮毂坯料7的轮辐平面6直径留出足够的预变形量和加工余量,轮辐平面6直径增大30mm。采用如图4所示的预变形装置进行预变形:将轮毂坯料7快速降至室温,将定位孔机加工成通孔,给定位孔留出20mm加工余量,然后将定位孔为通孔的轮毂坯料7置于预变形工作平台10上,旋转芯轴8穿过定位孔,移动旋转压辊9直至接触轮毂坯料7的胎圈座5,然后旋转压辊9开始自转,带动轮毂坯料7做同步旋转;同时旋转压辊9缓慢向旋转芯轴8移动,移动速率0.5mm/min,从而使得旋转压辊9沿旋转压辊施力方向即轮辐平面径向对镁合金轮毂坯料7施压,使轮辐处材料发生均匀、连续、缓慢的压缩变形,塑性应变量5.5%,在大多数晶粒中产生约60%体积分数的拉伸孪晶。
[0039]
(2)对预变形后的镁合金轮毂坯料7进行时效处理,时效制度150℃
×
24h。
[0040]
时效处理后,拉伸孪晶内存在高密度位错,能改变mg
17
al
12
强化相的析出机制,有效抑制粗大层片状mg
17
al
12
不连续析出相,同时促进均匀弥散分布的mg
17
al
12
连续析出相,显微组织见图6。并发现,沿轮辐平面径向的室温力学性能为:屈服强度r
p0.2
=280mpa,抗拉强度r
m
=350mpa,延伸率a=4%,强度性能高于轮辋4,强化效果显著,有助于提升轮毂的服役性能。
起点商标作为专业知识产权交易平台,可以帮助大家解决很多问题,如果大家想要了解更多知产交易信息请点击 【在线咨询】或添加微信 【19522093243】与客服一对一沟通,为大家解决相关问题。
此文章来源于网络,如有侵权,请联系删除



tips