直伞锥齿轮温锻精密成形模具的制作方法



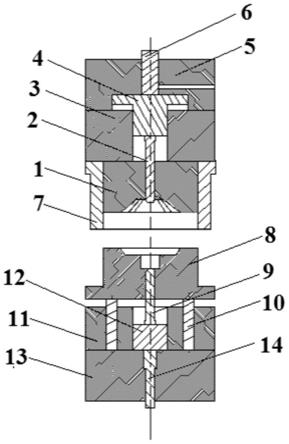
[0001]
本实用新型涉及机械制造技术领域,具体涉及一种直伞锥齿轮温锻精密成形模具。
背景技术:
[0002]
电动螺旋压力机自动线上直伞锥齿轮温锻成形时,一方面由于变形材料的各向异性及用于模具安装的模架必须方便机械手对物料的摆放和抓取,因此通常采用无导柱结构,仅靠设备的导轨精度及刚性实现上、下模合模时错模量不超过0.3mm是无法实现的;另一方面现有技术中粗锻齿模作为下模时,粗锻齿模内定位面由于其直径通常大于待变形坯料的直径,待变形坯料在粗锻齿模内无法准确定位;这两种原因的存在造成待变形坯料成形齿坯时分配不均匀,齿轮残余应力消除后变形大,精度等级低。同时,粗锻齿模作为下模时,与高温齿坯接触时间较长,极易造成粗锻齿模高温回火软化,大幅降低粗锻齿模的寿命,一般使用寿命不超过3000只。
[0003]
一些工艺中,也有将粗锻齿模与粗锻型腔模位置对调,粗锻齿模作为上模、粗锻型腔模作为下模,采用粗锻型腔模的轴颈准确定位待变形坯料,并采用液压装置进行打料,但是由于液压装置具有“迟滞性”,存在当设备滑块回程到下死点以上一定距离时挤压成形后的齿坯才脱离粗锻齿模的模腔,机械手无法正常抓取到齿坯导致电动螺旋压力机自动线的非正常停机。
技术实现要素:
[0004]
本实用新型目的在于提供一种直伞锥齿轮温锻精密成形模具,通过对成形模具进行精密结构设计,包括调整模具上下模组成、锻造时上模自动打料、坯料精准定位和设置预应力及导向机构等方式显著提高粗、精锻模具的使用寿命,提高齿形精度和坯料利用率,有效解决上述技术问题。
[0005]
为达成上述目的,本实用新型提出如下技术方案:一种直伞锥齿轮温锻精密成形模具,包括由电动螺旋压力机自动线构成的粗锻模具和精锻模具,其中,定义以粗锻模具中模腔分型面为界分成第一上模和第一下模、以精锻模具中模腔分型面为界分成第二上模和第二下模;
[0006]
所述第一上模包括上齿模、第一上打料顶杆、上齿模承压垫块、第一上过渡垫块、第一上承压垫块、第一上打料弹性元件和第一导向筒;所述上齿模的下端面设置有敞口朝下的上齿模型腔,第一导向筒套设在上齿模外圆周,且第一导向筒下端面向下凸出于上齿模下端面;所述第一上打料顶杆竖直设置在上齿模和上齿模承压垫块的内孔中,并且支承于活动设置在上齿模承压垫块、第一上承压垫块内孔中的第一上过渡垫块;所述第一上过渡垫块为台阶轴,第一上过渡垫块的台阶面支设在上齿模承压垫块的上端面;所述第一上打料弹性元件竖直设置在第一上承压垫块内孔中,第一上打料弹性元件的下端面抵触于第一上过渡垫块的上端面,且所述第一上打料弹性元件、第一上过渡垫块和第一上打料顶杆
构成同轴相顶结构;
[0007]
所述第一上打料弹性元件在第一上承压垫块内孔中至少具有第一状态和第二状态;所述第一状态为第一上打料弹性元件支撑第一上过渡垫块的台阶面抵触于上齿模承压垫块的上端面,第一上打料顶杆部分伸入上齿模型腔内;所述第二状态为第一上打料弹性元件处于压缩状态,第一上过渡垫块的台阶面间隔于上齿模承压垫块的上端面。
[0008]
所述第一下模包括下型腔模、第一下顶出杆、浮动举模弹性元件、下型腔模承压垫块、第一下过渡垫块、第一下承压垫块和第一下顶料杆;所述下型腔模的上端面设置有敞口朝上的下凹模型腔,下型腔模与上齿模适配,且下型腔模外圆周与第一导向筒内孔适配;所述下型腔模承压垫块居中设置有内孔,所述第一下顶出杆竖直设置在下型腔模和下型腔模承压垫块内孔中,第一下顶出杆并由活动设置在下型腔模承压垫块内孔中的第一下过渡垫块支承;所述第一下过渡垫块设置为竖直的圆柱轴,圆柱轴的下端面支设在第一下承压垫块上端面;所述第一下顶料杆竖直设置在第一下承压垫块内孔中,第一下顶料杆上端面抵触于第一下过渡垫块下端面,所述第一下顶料杆、第一下过渡垫块和第一下顶出杆构成同轴相顶结构;
[0009]
所述浮动举模弹性元件设置在下型腔模和第一下承压垫块之间,浮动举模弹性元件的上端面抵接于下型腔模的下端面,浮动举模弹性元件的下端面抵接于第一下承压垫块的上端面;所述浮动举模弹性元件在下型腔模和第一下承压垫块之间至少具有第一压缩状态和第二压缩状态,所述第一压缩状态为浮动举模弹性元件支撑下型腔模下端面间隔于下型腔模承压垫块上端面,所述第二压缩状态为浮动举模弹性元件被压缩至下型腔模下端面抵触于下型腔模承压垫块上端面,且第一下顶出杆部分伸入下凹模型腔内。
[0010]
所述第二上模包括上型腔模、第二上打料顶杆、上型腔模承压垫块、第二上过渡垫块、第二上承压垫块和第二上打料弹性元件;所述上型腔模的下端面居中设置有敞口朝下的上凹模型腔,所述上凹模型腔部分向下突出于上型腔模的下端面构成上型腔模外圆导向部;所述第二上打料顶杆竖直设置在上型腔模和上型腔模承压垫块的内孔中,并且支承于活动设置在上型腔模承压垫块、第二上承压垫块内孔中的第二上过渡垫块;所述第二上过渡垫块为台阶轴,第二上过渡垫块的台阶面支设在上型腔模承压垫块的上端面;所述第二上打料弹性元件竖直设置在第二上承压垫块内孔中,第二上打料弹性元件的下端面抵触于第二上过渡垫块的上端面,且所述第二上打料弹性元件、第二上过渡垫块和第二上打料顶杆构成同轴相顶结构;
[0011]
所述第二上打料弹性元件在第二上承压垫块内孔中至少具有第三状态和第四状态;所述第三状态为第二上打料弹性元件支撑第二上过渡垫块的台阶面抵触于上型腔模承压垫块的上端面,且第二上打料顶杆部分伸入上凹模型腔内;所述第四状态为第二上打料弹性元件处于压缩状态,第二上过渡垫块的台阶面间隔于上型腔模承压垫块的上端面。
[0012]
所述第二下模包括下齿模、第二下顶出杆、下齿模承压垫块、第二下过渡垫块、第二下承压垫块和第二下顶料杆,下齿模与上型腔模适配;所述下齿模的上端面设置有敞口朝上的下齿模型腔,且下齿模的外圆周套设有第二导向筒;所述第二导向筒上端面向上凸出于下齿模上端面,且第二导向筒内孔与上型腔模外圆导向部外圆周适配;所述第二下顶出杆竖直设置在下齿模和下齿模承压垫块内孔中,第二下顶出杆并由活动设置在下齿模承压垫块内孔中的第二下过渡垫块支承,且第二下顶出杆部分伸入下齿模型腔内;所述第二
下过渡垫块设置为竖直的圆柱轴,圆柱轴的下端面支设在第二下承压垫块上端面;所述第二下顶料杆竖直设置在第二下承压垫块内孔中,第二下顶料杆上端面抵触于第二下过渡垫块下端面,所述第二下顶料杆、第二下过渡垫块和第二下顶出杆构成同轴相顶结构。
[0013]
进一步的,定义第一导向筒下端面和上齿模下端面在竖直方向上的高度差为h1,第二导向筒上端面和下齿模上端面在竖直方向上的高度差为h2,上型腔模外圆导向部突出上型腔模的下端面的高度为h3,则h3=h2,h2≥23mm,h1≥40mm。
[0014]
进一步的,所述上型腔模外圆导向部上设置有排气孔。
[0015]
进一步的,所述第一导向筒的上端面抵接于上齿模承压垫块的下端面,第二导向筒的下端面抵接于下齿模承压垫块的上端面,第一导向筒与上齿模过盈配合、第二导向筒与下齿模过盈配合,过盈系数保持在4
‰-6‰
最佳,并且第一导向筒和第二导向筒的材质为h13模具钢,热处理后硬度为hrc44—48。
[0016]
进一步的,所述下型腔模承压垫块上还设置有若干贯穿下型腔模承压垫块上、下端面的贯穿孔,所述贯穿孔沿下型腔模承压垫块内孔周圈均匀布置;所述浮动举模弹性元件设置在贯穿孔内,设置为弹簧。
[0017]
进一步的,所述第一上打料弹性元件设置为第一氮气弹簧,所述第二上打料弹性元件设置为第二氮气弹簧;所述第一上承压垫块内设置有第一冷却机构,所述第二上承压垫块内设置有第二冷却机构;冷却机构用于调整氮气弹簧至正常工作温度。
[0018]
由以上技术方案可知,本实用新型的技术方案提供的直伞锥齿轮温锻精密成形模具,获得了有益效果:
[0019]
本实用新型公开的直伞锥齿轮温锻精密成形模具,结构简单,操作方便,包括由上齿模、下型腔模配合的粗锻模具和由上型腔模、下齿模配合的精锻模具;粗锻时,齿模在上,高温坯料与齿模接触时间最短,基本消除齿模高温回火软化的风险,上齿模的失效形式仅表现为正常磨损,齿模寿命显著提升。其中,本实用新型分别在粗锻模具和精锻模具的上模中设置由弹性元件构成的打料结构,避免成形的齿坯和齿轮粘连上模,即弹性元件在合模时蓄能,脱模时直接应用蓄能将坯料从上模脱离,解决采用液压装置打料时的“迟滞性”;分别在粗锻模具的上齿模和精锻模具的下齿模外圆周设置导向筒,一方面用于导向型腔模与齿模合模,确保上、下模的错模量不超过0.3mm,另一方面对型腔模提供在导向筒包覆范围内的预应力,避免齿模齿廓变形,防止坯料在合模镦挤时产生飞边。
[0020]
本实用新型在粗锻模具的下模设置由弹性结构构成的浮动举模结构,将下型腔模从下型腔模承压垫块上浮起,配合型腔模轴颈准确定位坯料,确保粗锻时待变形坯料在齿模型腔齿形内的分配均匀,提升齿形精度,减小齿轮残余应力消除后的变形;同时,也能便于粗锻时合模时压缩浮动举模结构,使得第一下顶出杆部分伸入下凹模型腔,与第一上打料顶杆配合在齿坯的齿形端面和轴颈端面锻出向齿坯内部的凹陷结构,提高坯料的3%的利用率。
[0021]
此外,采用在精锻齿模用导向筒提供预应力的结构除保证上、下模错模量不超过0.3mm外,还避免了精锻齿模在三向压应力状态下的齿廓变形,进而避免模具变形引起的齿形精度下降问题;同时在精锻上型腔模外圆导向部布置排气孔,能保证润滑剂在精锻齿轮齿面分布均匀,保证精锻齿形精度的一致性,提升模具寿命,增幅达68.75%以上。
[0022]
应当理解,前述构思以及在下面更加详细地描述的额外构思的所有组合只要在这
样的构思不相互矛盾的情况下都可以被视为本公开的实用新型主题的一部分。
[0023]
结合附图从下面的描述中可以更加全面地理解本实用新型教导的前述和其他方面、实施例和特征。本实用新型的其他附加方面例如示例性实施方式的特征和/或有益效果将在下面的描述中显见,或通过根据本实用新型教导的具体实施方式的实践中得知。
附图说明
[0024]
附图不意在按比例绘制。在附图中,在各个图中示出的每个相同或近似相同的组成部分可以用相同的标号表示。为了清晰起见,在每个图中,并非每个组成部分均被标记。现在,将通过例子并参考附图来描述本实用新型的各个方面的实施例,其中:
[0025]
图1为直伞锥齿轮粗锻成形模具的结构示意图;
[0026]
图2为直伞锥齿轮精锻成形模具的结构示意图;
[0027]
图3为图1中带第一导向筒的上齿模剖面图;
[0028]
图4为图1中第一上承压垫块的剖面图;
[0029]
图5为图1中下型腔模的剖面图;
[0030]
图6为图1中下型腔模承压垫块的剖面图;
[0031]
图7位图1中第一下承压垫块的剖面图;
[0032]
图8为图2中上型腔模的剖面图;
[0033]
图9为图2中第二上承压垫块的剖面图;
[0034]
图10为图2中下齿模的剖面图。
[0035]
图中,各标记的具体意义为:
[0036]
1-上齿模,2-第一上打料顶杆,3-上齿模承压垫块,4-第一上过渡垫块,5-第一上承压垫块,6-第一上打料弹性元件,7-第一导向筒,8-下型腔模,9-第一下顶出杆,10-浮动举模弹性元件,11-下型腔模承压垫块,12-第一下过渡垫块,13-第一下承压垫块,14-第一下顶料杆,15-上型腔模,16-第二上打料顶杆,17-上型腔模承压垫块,18-第二上过渡垫块,19-第二上承压垫块,20-第二上打料弹性元件,21-下齿模,22-第二下顶出杆,23-下齿模承压垫块,24-第二下过渡垫块,25-第二下承压垫块,26-第二下顶料杆,27-第二导向筒。
具体实施方式
[0037]
为使本实用新型实施例的目的、技术方案和优点更加清楚,下面将结合本实用新型实施例的附图,对本实用新型实施例的技术方案进行清楚、完整地描述。显然,所描述的实施例是本实用新型的一部分实施例,而不是全部的实施例。基于所描述的本实用新型的实施例,本领域普通技术人员在无需创造性劳动的前提下所获得的所有其他实施例,都属于本实用新型保护的范围。除非另作定义,此处使用的技术术语或者科学术语应当为本实用新型所属领域内具有一般技能的人士所理解的通常意义。
[0038]
本实用新型专利申请说明书以及权利要求书中使用的“第一”、“第二”以及类似的词语并不表示任何顺序、数量或者重要性,而只是用来区分不同的组成部分。同样,除非上下文清楚地指明其它情况,否则单数形式的“一个”“一”或者“该”等类似词语也不表示数量限制,而是表示存在至少一个。“包括”或者“包含”等类似的词语意指出现在“包括”或者“包含”前面的元件或者物件涵盖出现在“包括”或者“包含”后面列举的特征、整体、步骤、操作、
元素和/或组件,并不排除一个或多个其它特征、整体、步骤、操作、元素、组件和/或其集合的存在或添加。“上”“下”等仅用于表示相对位置关系,当被描述对象的绝对位置改变后,则该相对位置关系也可能相应地改变。
[0039]
基于现有技术直齿锥齿轮锻造过程中,齿模作为粗锻下模时存在坯料定位不精准导致合模时坯料在齿形间分配不均匀和齿模回火软化寿命低的问题,齿模作为粗锻上模时又存在采用液压打料机构的“迟滞性”问题;此外,还存在锻造时仅依靠设备定位及导轨无法达到错模量不超过0.3mm的要求等一系列技术问题。本实用新型旨在提出一种直伞锥齿轮温锻精密成形模具,结构简单,有效解决上述技术问题,整体提高模具的寿命和成形齿轮的精度。
[0040]
下面结合附图所示的实施例,对本实用新型的直伞锥齿轮温锻精密成形模具作进一步具体介绍。
[0041]
结合图1和图2所示,一种直伞锥齿轮温锻精密成形模具,包括由电动螺旋压力机自动线构成的粗锻模具和精锻模具,其中,定义以粗锻模具中模腔分型面为界分成第一上模和第一下模、以精锻模具中模腔分型面为界分成第二上模和第二下模;所述第一上模包括上齿模1、第一下模包括下型腔模8,所述第二上模包括上型腔模15、第二下模包括下齿模21,即将粗锻时采用型腔模轴颈对坯料定位,高温坯料在粗锻时主要停留在下型腔模8上,也减少了其与上齿模1的接触时间,基本消除上齿模1易受高温回火软化的风险,改变上齿模1的失效形式由过去的坍塌、变形、龟裂,快速磨损的早期失效形式变成现在的正常磨损失效,上齿模1寿命由过去的成形不超过3000只变成现在的成形远超10000只,延长粗锻齿模具寿命200%以上。
[0042]
为避免上齿模1在电动螺旋压力机自动线上采用液压装置打料而具有“迟滞性”,以及现有电动螺旋压力机自动线无导柱结构、仅依靠设备导轨精度及刚性无法实现上、下模合模时错模量不超过0.3mm的技术问题,本实用新型对上齿模1结构改进如下。结合图3和图4所示,第一上模还包括第一上打料顶杆2、上齿模承压垫块3、第一上过渡垫块4、第一上承压垫块5、第一上打料弹性元件6和第一导向筒7,其中,上齿模1的下端面设置有敞口朝下的上齿模型腔,第一导向筒7套设在上齿模1外圆周,且第一导向筒7下端面向下凸出于上齿模1下端面。第一上打料顶杆2竖直设置在上齿模1和上齿模承压垫块3的内孔中,并且支承于活动设置在上齿模承压垫块3、第一上承压垫块5内孔中的第一上过渡垫块4;所述第一上过渡垫块4为台阶轴,第一上过渡垫块4的台阶面支设在上齿模承压垫块3的上端面;所述第一上打料弹性元件6竖直设置在第一上承压垫块5内孔中,第一上打料弹性元件6的下端面抵触于第一上过渡垫块4的上端面,并且第一上打料弹性元件6、第一上过渡垫块4和第一上打料顶杆2构成同轴相顶结构。
[0043]
为确保第一上打料顶杆2在脱模时能迅速将齿坯从上齿模1脱离,第一上打料弹性元件6在第一上承压垫块5内孔中至少具有第一状态和第二状态,具体为,第一状态为第一上打料弹性元件6支撑第一上过渡垫块4的台阶面抵触于上齿模承压垫块3的上端面,此时,第一上打料顶杆2在第一上打料弹性元件6的作用下靠近上齿模1的端部部分伸入上齿模型腔内;第二状态为第一上打料弹性元件6处于压缩状态,在合模压力的作用下,第一上过渡垫块4的台阶面间隔于上齿模承压垫块3的上端面。
[0044]
本实用新型的上齿模1在初始时经第一上打料弹性元件6作用处于第一状态,合模
时受上齿模型腔内坯料挤压,第一上打料顶杆2经第一上过渡垫块4向上压缩第一上打料弹性元件6,实现第一上打料弹性元件6的预紧蓄能;在脱模时,上齿模1在电动螺旋压力机的滑块到达下死点后立即向上回程,第一上打料弹性元件6无需液压启动自动恢复形变,迅速释放蓄能,第一上打料弹性元件6经第一上过渡垫块4向下推动第一上打料顶杆2直至部分伸入上齿模1的齿模型腔内,第一上打料顶杆2将成形的齿坯推出齿模型腔,使得齿坯脱离上齿模1、始终留下型腔模8内,避免发生齿坯粘连上齿模1,导致齿坯从上齿模1掉落碰伤的现象。
[0045]
结合图5至图7所示,第一下模还包括第一下顶出杆9、浮动举模弹性元件10、下型腔模承压垫块11、第一下过渡垫块12、第一下承压垫块13和第一下顶料杆14,下型腔模8的上端面设置有敞口朝上的下凹模型腔,下型腔模8与上齿模1适配,且下型腔模8外圆周与第一导向筒7内孔适配。下型腔模承压垫块11居中设置有内孔,第一下顶出杆9竖直设置在下型腔模8和下型腔模承压垫块11内孔中,第一下顶出杆9并由活动设置在下型腔模承压垫块11内孔中的第一下过渡垫块12支承。其中,第一下过渡垫块12设置为竖直的圆柱轴,圆柱轴的下端面支设在第一下承压垫块13上端面;所述第一下顶料杆14竖直设置在第一下承压垫块13内孔中,第一下顶料杆14上端面抵触于第一下过渡垫块13下端面,并且第一下顶料杆14、第一下过渡垫块12和第一下顶出杆9构成同轴相顶结构。在下型腔模8中设置浮动举模弹性元件10是为了将下型腔模8从下型腔模承压垫块11上浮起,一方面是为了配合下型腔模轴颈准确定位坯料,确保粗锻时坯料在上齿模型腔的齿形内均匀分配,减小齿轮残余应力消除后的变形,提升齿形精度;另一方面是为了提高粗锻时坯料的利用率。
[0046]
具体为,浮动举模弹性元件10设置在下型腔模8和第一下承压垫块13之间,浮动举模弹性元件10的上端面抵接于下型腔模8的下端面,浮动举模弹性元件10的下端面抵接于第一下承压垫块13的上端面。浮动举模弹性元件10在下型腔模8和第一下承压垫块13之间至少具有第一压缩状态和第二压缩状态,第一压缩状态为浮动举模弹性元件10支撑下型腔模8下端面间隔于下型腔模承压垫块11上端面,即浮起在下型腔模承压垫块11的上方;第二压缩状态为浮动举模弹性元件10被压缩至下型腔模8下端面抵触于下型腔模承压垫块11上端面,且第一下顶出杆9部分伸入下凹模型腔内。合模时,浮动举模弹性元件10在上齿模1压力下,浮动举模弹性元件10被压缩,浮动举模弹性元件10处于第二压缩状态,第一下顶出杆9靠近第一上模的端部在下凹模型腔内与坯料接触,成形时在齿坯的轴颈端面锻出向齿坯内部的凹陷结构。
[0047]
同时,在上齿模1中,合模时,第一上打料弹性元件6处于第二状态时,第一上打料顶杆2靠近第一下模的端部也部分伸入上齿模型腔内与坯料接触,在成形齿坯的齿形端面锻出向齿坯内部的凹陷结构。齿坯两端的凹陷结构能显著在现有坯料利用率的基础上,进一步提升材料利用率达3%。
[0048]
在粗锻时,由于在上齿模1外圆周设置第一导向筒7,合模时,能准确对下型腔模8导向,确保上齿模1和下型腔模8的中轴线重合,将上、下模之间的错模量控制在0.3mm以内,同时对上齿模1提供预应力,防止上齿模1在受到三向压应力引起齿模齿廓变形造成的齿形精度超差和飞边问题。
[0049]
结合图8和图9所示,第二上模还包括第二上打料顶杆16、上型腔模承压垫块17、第二上过渡垫块18、第二上承压垫块19和第二上打料弹性元件20,其中,上型腔模15的下端面
居中设置有敞口朝下的上凹模型腔,上凹模型腔部分向下突出于上型腔模15的下端面构成上型腔模外圆导向部。第二上打料顶杆16竖直设置在上型腔模15和上型腔模承压垫块17的内孔中,并且支承于活动设置在上型腔模承压垫块17、第二上承压垫块19内孔中的第二上过渡垫块18上;所述第二上过渡垫块18为台阶轴,第二上过渡垫块18的台阶面支设在上型腔模承压垫块17的上端面。所述第二上打料弹性元件20竖直设置在第二上承压垫块19内孔中,第二上打料弹性元件20的下端面抵触于第二上过渡垫块18的上端面,并且第二上打料弹性元件20、第二上过渡垫块18和第二上打料顶杆16构成同轴相顶结构。
[0050]
为确保第二上打料顶杆16在脱模时能迅速将成形的齿轮从上型腔模15脱离,第二上打料弹性元件20在第二上承压垫块19内孔中至少具有第三状态和第四状态;具体包括,第三状态为第二上打料弹性元件20支撑第二上过渡垫块18的台阶面抵触于上型腔模承压垫块17的上端面,且第二上打料顶杆16部分伸入上凹模型腔内;第四状态为第二上打料弹性元件20处于压缩状态,第二上过渡垫块18的台阶面间隔于上型腔模承压垫块17的上端面。
[0051]
与粗锻打料过程类似,初始时,第二上打料弹性元件20作用处于第三状态,合模时受上凹模型腔内坯料挤压,第二上打料顶杆16经第二上过渡垫块18向上压缩第二上打料弹性元件20,实现第二上打料弹性元件20的预紧蓄能;在脱模时,上型腔模15在电动螺旋压力机的滑块到达下死点后立即向上回程,第二上打料弹性元件20无需液压启动自动恢复形变,迅速释放蓄能,第二上打料弹性元件20经第二上过渡垫块18向下推动第二上打料顶杆16直至部分伸入上凹模型腔内,第二上打料顶杆16将精锻获得的齿轮推出,脱离上型腔模15。
[0052]
结合图10所示,第二下模还包括第二下顶出杆22、下齿模承压垫块23、第二下过渡垫块24、第二下承压垫块25和第二下顶料杆26,其中,下齿模21与上型腔模15适配,下齿模21的上端面设置有敞口朝上的下齿模型腔,且下齿模21的外圆周套设有第二导向筒27;所述第二导向筒27上端面向上凸出于下齿模21上端面,且第二导向筒27内孔与上型腔模外圆导向部的外圆周适配。第二下顶出杆22竖直设置在下齿模21和下齿模承压垫块23内孔中,第二下顶出杆22并由活动设置在下齿模承压垫块23内孔中的第二下过渡垫块24支承,并且第二下顶出杆22部分伸入下齿模型腔内;所述第二下过渡垫块24设置为竖直的圆柱轴,圆柱轴的下端面支设在第二下承压垫块25上端面。第二下顶料杆26竖直设置在第二下承压垫块25内孔中,第二下顶料杆26上端面抵触于第二下过渡垫块24下端面,并且第二下顶料杆26、第二下过渡垫块24和第二下顶出杆22构成同轴相顶结构。
[0053]
精锻中第二导向筒27实现与粗锻时相同的技术效果,导向及提供预应力,具体为,下齿模21外圆周的第二导向筒27在合模时与上型腔模外圆导向部配合,准确对上型腔模15导向,确保上型腔模15和下齿模21的中轴线重合,将精锻上、下模之间的错模量控制在0.3mm以内,同时对下齿模21提供预应力,避免下齿模在三向压应力状态下引起齿模齿廓变形造成的齿形精度下降问题,降低齿模耗损。实施例中,为提高精锻时齿形精度的一致性、提高精锻模具的寿命,上型腔模外圆导向部上布置排气孔,确保润滑剂在上齿模型腔齿面上的均匀分布,精锻模具寿命增幅达68.75%以上。
[0054]
实施例中,为确保第一导向筒7和第二导向筒27有足够的刚度对型腔模导向及提供预应力,第一导向筒7和第二导向筒27选用硬度为hrc44-hrc48的h13模具钢制造,并且第
一导向筒7的上端面抵接于上齿模承压垫块3的下端面,第二导向筒27的下端面抵接于下齿模承压垫块23的上端面,第一导向筒7与上齿模1过盈配合、第二导向筒27与下齿模21过盈配合,过盈系数保持在4
‰-6‰
为最佳。同时,为确保第一导向筒7和第二导向筒27的实施效果,定义第一导向筒7下端面和上齿模1下端面在竖直方向上的高度差为h1,第二导向筒27上端面和下齿模21上端面在竖直方向上的高度差为h2,上型腔模外圆导向部突出上型腔模15的下端面的高度为h3,则h3=h2,h2≥23mm,h1≥40mm;如当下型腔模8在上齿模1未接触坯料时整个外圆周已经有5mm以上进入第一导向筒7内部。
[0055]
进一步结合图1所示的实施例,下型腔模承压垫块11上还设置有若干贯穿下型腔模承压垫块11上、下端面的贯穿孔,贯穿孔沿下型腔模承压垫块内孔周圈均匀布置,浮动举模弹性元件10设置在贯穿孔内,设置为弹簧。附图所示的实施例中,下型腔模承压垫块内孔周圈布置有4个贯穿孔,弹簧选用矩形弹簧,型号为sg25x12.5x125,4根矩形弹簧为一组合均布在贯穿孔中,矩形弹簧预设压缩行程为10mm,即下型腔模8在下型腔模承压垫块11上端面浮起高度不超过10mm。
[0056]
为减少在上模中布置上打料弹性元件所占据的轴向空间,第一上打料弹性元件6设置为第一氮气弹簧,第二上打料弹性元件20设置为第二氮气弹簧,氮气弹簧的型号均选用u4700-16。同时,由于氮气弹簧对使用环境温度要求较高,氮气弹簧的正常使用温度在0℃-40℃范围内,否则会引起氮气弹簧密封件的早期失效,降低氮气弹簧的正常使用寿命,影响自动线生产的连续性,因此为保证氮气弹簧工作环境温度的稳定,实施例通过在第一上承压垫块5内设置有第一冷却机构、第二上承压垫块19内设置第二冷却机构,调整氮气弹簧至正常工作温度,如图4和图9所示。冷却机构具体可采用测温热电偶与冷却循环通道组合的方式实现,例如设定测温热电偶下限温度10℃,上限温度30℃,通过测温热电偶将信号传递给控制中心plc,plc指令开关向冷却循环通道通入压缩空气,保证氮气弹簧在规定的环境温度内工作。
[0057]
本实用新型的直伞锥齿轮温锻精密成形模具,采用调整模具组成、上模自动打料、坯料精准定位和设置预应力导向机构等方式改变粗、精锻模具的受损形式为正常磨损失效,显著提高粗、精锻模具的使用寿命,提高齿形精度和坯料利用率。
[0058]
虽然本实用新型已以较佳实施例揭露如上,然其并非用以限定本实用新型。本实用新型所属技术领域中具有通常知识者,在不脱离本实用新型的精神和范围内,当可作各种的更动与润饰。因此,本实用新型的保护范围当视权利要求书所界定者为准。
起点商标作为专业知识产权交易平台,可以帮助大家解决很多问题,如果大家想要了解更多知产交易信息请点击 【在线咨询】或添加微信 【19522093243】与客服一对一沟通,为大家解决相关问题。
此文章来源于网络,如有侵权,请联系删除
相关标签: 垫块



tips