一种涡流纺纱线及其用途的制作方法



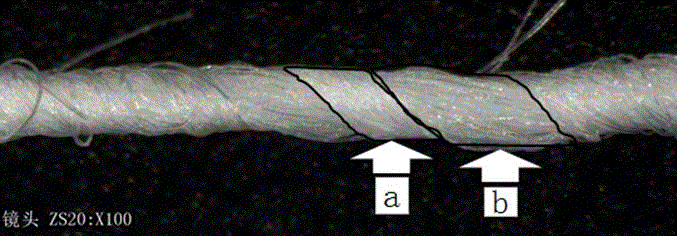
本发明涉及一种涡流纺纱线及其用途。
背景技术:
随着生活水平不断的提高,消费者越来越关注运动过程中服装对健康及生活品质的影响,特别是对贴身穿着的运动衫、内衣、袜、裤等的舒适性、速干性、抗起球性提出了更高的要求。在活动量较大的运动中,一方面会产生大量的汗液,而这些汗液如果无法及时蒸发的话,会让人感到非常不舒服,造成闷热感,特别是面料受潮黏附在皮肤上时,还会妨碍到运动;另一方面,持续运动时,服装与身体摩擦,会发生起球等影响外观的问题。因此,开发一种既能将水分迅速排出,又具有耐磨、抗起球的面料显得尤为迫切。
目前,市面上用来生产上述面料的纱线也比较多,如专利文献cn108130643a中公开了一种涡流纺纱线,利用涡流纺纱线中间无捻、外部缠绕的结构,所制得成品的抗起毛起球性可以达到3级以上,并且该结构有利于水分传递,可赋予产品良好的速干性,但是由于常规涡流纺纱线在长度方向上的直径基本一致,容易造成已经被吸入内部结构的水分与身体接触,造成汗液黏附在皮肤上,影响穿着体验。
另外,专利文献cn201459317u中公开了一种混色纺高收缩纱线,利用高收缩纤维与低收缩纤维混纺,在沸水收缩后,由于两种纤维不同的收缩率形成了丝长差,这样的纱线具有触感膨松、柔软等特性,同时吸湿性好,可解决黏附皮肤的苦恼,但是,由于外层纤维膨松,速干性不良,而且抗起球性能只能达到2-3级。
技术实现要素:
本发明的目的在于提供一种速干优良(残留水分率低)且抗起毛起球性优越的涡流纺纱线及其用途。
本发明的解决方案是:
本发明的涡流纺纱线经过热水处理后具有粗部和细部,其中粗部与细部的直径比为1.1~3:1、长度比为0.5~4:1。
本发明的涡流纺纱线具有内松外紧的结构,由其制得的纺织品抗起毛起球性极为优越。热水处理后形成粗部和细部,细部结构相对比较紧密且不与身体接触,粗部结构相对比较疏松且与身体形成点接触,与身体接触的粗部可以迅速将汗液等吸收,被吸收的水分一部分由粗部向细部扩散,利用细部与身体之间的流动空气进行蒸发;还有一部分则利用粗部的疏松结构向外蒸发,速干性得到了有效提高。
附图说明
图1为本发明涡流纺纱线的热水处理前的纱体结构图,a为缠绕部(热水处理后的细部),b为平行部(热水处理后的粗部)。
图2为本发明涡流纺纱线的热水处理后的纱体结构图,a为细部,b为粗部。
具体实施方式
本发明的涡流纺纱线经过热水处理后具有粗部和细部。当粗部和细部的直径比低于1.1:1时,纱体表面比较平整,与身体之间不能形成空气流动空间,汗液等的蒸发速度慢;当粗部和细部的直径比大于3:1的话,虽然存在了空气流动空间,但由于粗部过度蓬松,容易形成毛羽,抗起毛起球性差,因此,本发明中粗部和细部的直径比为1.1~3:1。考虑到手感、速干性等,直径比更优选为1.1~2:1。
这里的热水处理是指用60~130℃的热水对纱线进行20分钟处理,可根据纤维原料的不同进行合理选择。此外,这里处理的纱线,也可以是从纺织品中分解出来的纱线。
再者,粗部和细部的长度比小于0.5:1的话,即粗部短、细部长,这样一来,作为水分储存传导的粗部不能及时将肌面的汗液全部吸收,速干性差。而长度比大于4:1的话,即粗部长、细部短,由于粗部的内部结构松弛,会导致纱线强力降低,在纺纱、编织过程中断头率增加,而且所得产品容易出现起毛起球的问题。因此,本发明中粗部和细部的长度比为0.5~4:1。更优选长度比为1~3:1。
作为优选,本发明中,粗部和细部的直径均在200~700微米(μm)之间,粗部和细部的长度均在50~650微米(μm)之间。
作为优选,本发明的涡流纺纱线经过热水处理后的伸长率为10%~50%。当伸长率大于50%时,单纤维卷曲大,单纤维之间的三维空间大,即汗液储存空间大,吸汗速度得到提高,但是汗液储存空间大到一定程度时,毛细管效应变弱,汗液传递扩散的速度有下降的趋势;当伸长率小于5%时,单纤维卷曲小,单纤维之间的三维空间小,即汗液储存空间小,吸汗速度有下降的趋势。本发明中,更优选伸长率为10%~40%。
作为优选,本发明的涡流纺纱线由高收缩纤维和低收缩纤维所组成,其中,高收缩纤维的沸水收缩率为15%~50%,低收缩纤维的沸水收缩率小于10%。在热水处理前无张力状态下,纱线上包括有平行于纱线轴向的平行部以及缠绕部。平行部为无捻状态,而且由于表面没有缠绕纤维,热水处理后,其中的高收缩纤维不受限制产生了较大的卷曲,带动低收缩纤维形成了粗部;而热水处理后缠绕部中的部分纤维虽然也有卷曲,但受到表面缠绕纤维的阻力,向纱线内部集中、挤压,反而呈现了收紧现象,形成了细部。更优选,高收缩纤维的沸水收缩率为15%~40%,低收缩纤维的沸水收缩率为5%以下。
本发明中,高收缩纤维和低收缩纤维之间的沸水收缩率差小于10%的话,粗部与细部之间的直径比有下降的趋势,有可能会影响到速干性;而沸水收缩率差大于45%的话,粗部排列过于紧密,吸水性有下降的趋势。因此,本发明中优选两者的沸水收缩率差为10%~45%。更优选为20%~30%。
考虑到高收缩纤维与低收缩纤维的混率会影响到粗部的形成以及手感等,因此优选混率比为1:0.4~4,更优选为1:1~4。
本发明中,所用纤维原料没有特别要求,可以是如棉等天然纤维、聚酯等合成纤维和粘胶等再生纤维素纤维中的任意一种或几种。
在本发明纱线制备过程中,当喷嘴压力一定时,加工速度越快,粗部所占比率越多(细部所占比率越少);加工速度越慢,粗部所占比率越少(细部所占比率越多)。当加工速度高于600m/min时,沸水处理后粗部和细部的长度比变大,轴向无捻部分增加,有可能出现纱线强力变差、抗起毛起球性下降的问题。当加工速度低于300m/min时,粗部和细部的长度比变小,轴向无捻部分减少,汗液通过粗部传递扩散的效果下降,速干性有变差的趋势。本发明中优选加工速度为300~600m/min。
加工速度一定时,喷嘴压力由小变大时,细部也随之变得越来越紧。当压力低于0.5mpa时,热水处理后粗部和细部的直径比变小,纱线结构松弛,有利于水份传递到纱线内部,但抗起毛起球性有下降的趋势。当压力大于0.6mpa时,热水处理后粗部和细部的直径比变大,汗液通过粗部纤维层传递扩散的效果有可能下降,速干性有变差的趋势。本发明中优选压力为0.5~0.6mpa。
由使用本发明的涡流纺纱线制得的纺织品,根据jisl1076aici标准测得其抗起毛起球性在3.5级以上;根据科肯法测得其残留水分率为30%以下。经过热水处理等条件,所得纺织品中涡流纺纱线具有粗部和细部,其特征为:粗部与细部的直径比为1.1~3:1、长度比为0.5~4:1。
本发明的涡流纺纱可用于制作运动衫、内衣、袜子、裤子等。
本发明中所涉及的各性能参数的测试方法如下:
(1)纤维沸水收缩率
参照jisl1095-2010标准。
(2)纱线伸长率
参照jisl1095-2010标准。
(3)抗起毛起球性
参照jisl1076a-2006ici标准。
(4)直径、长度
选取长度约5cm且经过热水处理的纱线10根,使用电子数码显微镜(keyence),在100倍率条件下对无张力状态的上述纱线分别进行观察。在相机模式下,任意选择纱线上3处粗部以及3处细部进行测量,量出各自的直径和长度(如图2所示,直径指的是与纱体长度方向垂直的部分;长度指的是与纱体长度方向平行的部分),得到直径30组数据、长度30组数据,分别取平均值,作为本发明的粗部和细部的直径、长度(单位:微米μm)。其中,经过热水处理的纱线也可以是从纺织品中分解出来的纱线。这里的热水处理是指用60~130℃的热水进行20分钟处理,可根据纤维原料的不同进行合理选择。
下面结合实施例及比较例对本发明作进一步说明。
实施例1
选用长度38mm、沸水收缩率为24%的高收缩腈纶短纤维作为高收缩纤维原料,长度38mm、沸水收缩率为5%的普通腈纶短纤维以及沸水收缩率为4%沸水收缩率的普梳棉作为低收缩纤维原料,高收缩纤维原料与低收缩纤维原料按照1:1.5的比例进行混合,经清花打卷、梳棉、并条工序后,进入涡流纺工序,加工速度350m/min,喷嘴压力0.5mpa,得到20支的涡流纺纱线,各项参数见表1。
实施例2
加工速度调整为400m/min,其余同实施例1,得到20支的涡流纺纱线,各项参数见表1。
实施例3
加工速度调整为300m/min,其余同实施例1,得到20支的涡流纺纱线,各项参数见表1。
实施例4
选用长度38mm、沸水收缩率为14%的高收缩涤纶短纤维作为高收缩纤维原料,其余同实施例1,得到20支的涡流纺纱线,各项参数见表1。
实施例5
选用长度38mm、沸水收缩率为49%的高收缩涤纶短纤维作为高收缩纤维原料,其余同实施例1,得到20支的涡流纺纱线,各项参数见表1。
实施例6
高收缩纤维原料与低收缩纤维原料的比例调整为1:0.4,其余同实施例1,得到20支的涡流纺纱线,各项参数见表1。
实施例7
高收缩纤维原料与低收缩纤维原料的比例调整为1:4,其余同实施例1,得到20支的涡流纺纱线,各项参数见表1。
实施例8
高收缩纤维原料与低收缩纤维原料的比例调整为1:2.3,其余同实施例1,得到20支的涡流纺纱线,各项参数见表1。
实施例9
加工速度调整为500m/min,其余同实施例1,得到20支的涡流纺纱线,各项参数见表1。
实施例10
加工速度调整为550m/min,其余同实施例1,得到20支的涡流纺纱线,各项参数见表1。
实施例11
加工速度调整为600m/min,其余同实施例1,得到20支的涡流纺纱线,各项参数见表1。
实施例12
选用长度38mm、沸水收缩率为54%的高收缩涤纶短纤维作为高收缩纤维原料,其余同实施例1,得到20支的涡流纺纱线,各项参数见表1。
比较例1
加工速度调整为250m/min,其余同实施例1,得到20支的涡流纺纱线,各项参数见表1。
比较例2
选用沸水收缩率为60%的高收缩涤纶纤维作为高收缩纤维原料,其余同实施例1,得到20支的涡流纺纱线,各项参数见表1。
采用实施例1-12、比较例1-2的涡流纺纱线分别进行织造,得到纺织品。各项参数见表1。
表1
根据表1,
(1)由实施例1和实施例4可知,同等条件下,采用沸水收缩率为24%的高收缩纤维制得的涡流纺纱线与采用沸水收缩率14%的高收缩纤维制得的涡流纺纱线相比,两者制得的纺织品的抗起毛起球性相当,前者制得的纺织品的速干性(残留水分率低)优于后者。
(2)由实施例1和实施例6可知,同等条件下,高收缩与低收缩纤维的混率为1:1.5的涡流纺纱线与高收缩与低收缩纤维的混率为1:0.4的涡流纺纱线相比,前者制得的纺织品的抗起毛起球性略优于后者,但速干性(残留水分率略高)稍不及后者。
(3)由实施例1和实施例11可知,同等条件下,伸长率为30%的涡流纺纱线与55%的涡流纺纱线相比,前者制得的纺织品的抗起毛起球性及速干性均优于后者。
(4)由实施例1和实施例12可知,同等条件下,纤维原料收缩率差为20%的涡流纺纱线和纤维原料收缩率差为50%的涡流纺纱线相比,两者制得的纺织品的速干性相当,前者制得的纺织品的抗起毛起球性略优于后者。
(5)由比较例1和实施例1可知,同等条件下,粗部与细部的直径比为1:1、长度比为0.2:1的涡流纺纱线与粗部与细部的直径比为2:1、长度比为2.3:1的涡流纺纱线相比,虽然两者制得的纺织品的抗起毛起球性相当,但前者制得的纺织品的速干性很差(残留水分率高)。
(6)由比较例2和实施例5可知,同等条件下,粗部与细部的直径比为3.5:1、长度比为4.5:1的涡流纺纱线与粗部与细部的直径比为2.5:1、长度长度比为1.5:1的涡流纺纱线相比,虽然两者制得的纺织品的速干性相当,但前者制得的纺织品的抗起毛起球性很差。
起点商标作为专业知识产权交易平台,可以帮助大家解决很多问题,如果大家想要了解更多知产交易信息请点击 【在线咨询】或添加微信 【19522093243】与客服一对一沟通,为大家解决相关问题。
此文章来源于网络,如有侵权,请联系删除


