发制品假发纤维复合式全自动纺丝生产设备的制作方法



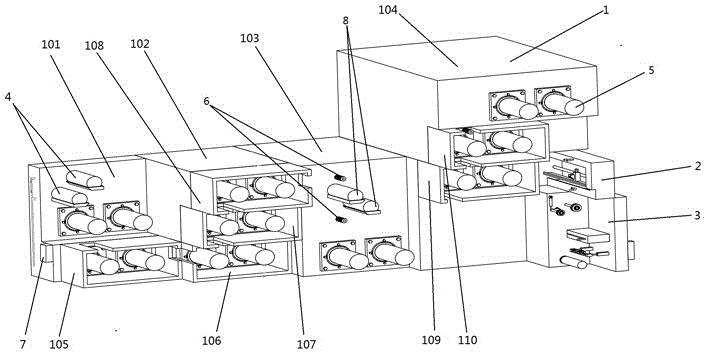
本发明属于一种发用化纤生产装置,特别涉及一种发制品假发纤维复合式全自动纺丝生产设备。
背景技术:
随着人们生活水平的提高,人们对于美的需求越来越高,目前人们脱发现象较为严重,假发需求越来越大,尤其对于非洲国家的人民,假发对于他们来说相当于生活必需品,而他们的生产能力有限,因此假发类产品越来越受人们青睐,市场缺口依然很大。
发用化纤在生产过程中需要经过大量的工艺步骤才能够满足预定的发用化纤的质量要求;但是发用化纤的生产工艺较多,各个工艺步骤又包含有大量的工序,因此制备发用化纤时需要的设备较多,占用的场地较大;在各个工序之间需要用转运车来运输上个工序的发用化纤。因此各个工艺以及转运时需要用到大量的人力物力。
发用化纤在生产过程中需要将发用化纤丝缠绕在丝辊上方便后道工序的生产以及转运,在进行发用化纤丝收卷完成后需要对其进行剪切,人工剪切存在很大的安全隐患,因为拿着剪刀去剪切易发生将发用化纤丝其它部位碰到造成断裂的现状,且人工剪切可能存在一定的风险,机器的转动可能会造成发用化纤丝缠绕在剪刀上或手上对员工造成伤害。
为了能够使产品质量更好,生产效率更快,能够节约生产成本,以及减少设备的占用场地,我们提供了一种发制品假发纤维复合式全自动纺丝生产设备。
技术实现要素:
本发明旨在解决现有技术中存在的问题而发明的一种发制品假发纤维复合式全自动纺丝生产设备。
本发明的目的是这样实现的:发制品假发纤维复合式全自动纺丝生产设备,包括箱体机构,箱体机构右下方设置有剪切机构,所述的箱体机构包括有第一箱体、第二箱体、第三箱体、第四箱体、第一辊轴框、第二辊轴框、第三辊轴框、第四辊轴框、第五辊轴框、第六辊轴框,第一箱体、第二箱体、第三箱体、第四箱体从左到右依次排列,第一箱体下部凸出,第一箱体的前表面设置有第一辊轴框,第二箱体的前表面为阶梯型结构,第二箱体的阶梯上从下到上依次设置有第二辊轴框、第三辊轴框、第四辊轴框,第四箱体上部为阶梯型结构,第四箱体的阶梯处从下到上依次设置有第五辊轴框、第六辊轴框;第一辊轴框、第二辊轴框、第三辊轴框、第四辊轴框、第五辊轴框、第六辊轴框内各设置有一对辊轴机构,第一箱体的中部、第三箱体的下部以及第四箱体的上部也各设置有一对辊轴机构;第一箱体的左侧面设置有控制器以及外供液管,第一箱体的上部设置有第一冷却机构,第三箱体的上部设置有第二冷却机构,第二冷却机构的上下方分别设置有一个导丝杆;剪切机构上方设置有引丝机构。
进一步的,所述的第一辊轴框上表面与第二辊轴框上表面位于同一平面,第一辊轴框上表面左侧开设有第一进线口,第一辊轴框右侧面上部开设有第一出线口,第二辊轴框左侧面上部开设有第二进线口,第二辊轴框上表面左侧开设有第二出线口;第三辊轴框下表面左侧开设有与第二出线口相对应的第三进线口,第三辊轴框上表面左侧开设有第三出线口,第四辊轴框下表面开设有与第三出线口相对应的第四进线口,第四进线框右侧面上部开设有第四出线口;第五辊轴框下表面左侧开设有第五进线口,第五辊轴框上表面左侧开设有第五出线口;第六辊轴框下表面开设有与第五出线口相对应的第六进线口,第六辊轴框上表面左侧开设有第六出线口;第五进线口与第六出线口处分别设置有一个导丝杆。
进一步的,所述的辊轴机构包括有辊筒、固定板、固定螺栓、紧固螺栓、调节螺栓、辊轴支架、电机、转杆、轴承、电机耳板、支架耳板,固定板通过固定螺栓固定在箱体上,固定板中部开设有辊轴孔,辊轴支架位于辊轴孔内,箱体上开设有与辊轴孔相同尺寸的电机孔,固定板后侧面开设有十字形凹槽,辊轴支架外侧面固定连接有转杆,辊轴支架通过转杆与固定板转动连接,辊轴支架外侧面均匀分布有四个支架耳板,支架耳板位于十字形凹槽内,电机通过轴承与辊轴支架连接,电机的外侧面均匀分布有四个电机耳板,电机耳板与支架耳板通过紧固螺栓连接,支架耳板前侧面中部开设有弧形凹槽,固定板上设置有四个调节螺栓,调节螺栓底部位于支架耳板的弧形凹槽内。
进一步的,所述的第一冷却机构包括有两个第一辊子机构、第一冷却电机、第一主动轮、第一皮带、辅从动轮、支撑杆,第一箱体内上部设置有固定板一,第一冷却电机固定在固定板一上,第一冷却电机输出端设置有第一主动轮,支撑杆固定在第一箱体内,辅从动轮与支撑杆之间转动连接,两个第一辊子机构上下分布,第一辊子机构包括有第一从动轮、积液槽一、辊子一、辊轴一、第一轴承、进液管一,积液槽一贯穿第一箱体,积液槽内端部分侧面连接有进液管一,进液管一与外供液管连接,辊轴一外端面固定连接有辊子一,辊轴一贯穿第一箱体,辊轴一与第一箱体之间通过第一轴承连接,辊轴一内端面固定连接有第一从动轮;第一主动轮、辅从动轮、下方的第一辊子机构的第一从动轮之间通过第一皮带连接,上方的第一辊子机构的第一从动轮与第一皮带外侧面接触。
进一步的,所述的第二冷却机构包括有两个第二辊子机构、第二冷却电机、第二主动轮、第二皮带,第三箱体内上部设置有固定板二,第二冷却电机固定在固定板二上,第二冷却电机输出端设置有第二主动轮,两个第二辊子机构上下分布,第二辊子机构包括有第二从动轮、积液槽二、辊子二、辊轴二、第二轴承、进液管二,积液槽二贯穿第三箱体,积液槽内端部分侧面连接有进液管二,进液管二连接有内供液管,辊轴二外端面固定连接有辊子二,辊轴二贯穿第三箱体,辊轴二与第三箱体之间通过第二轴承连接,辊轴二内端面固定连接有第二从动轮;第二主动轮、上方的第二辊子机构的第二从动轮之间通过第二皮带连接,下方的第二辊子机构的第二从动轮与第二皮带外侧面接触。
进一步的,所述的引丝机构包括有引丝台、供水管、引丝杆、收丝杆、导水板、供水开关、旋钮、排水头、斜板,引丝台后端面固定连接在箱体上,引丝台底部开设有水槽,引丝台内固定连接有导水板,导水板上固定连接有供水开关,供水开关上方设置有旋钮,供水开关左侧面的输出端贯穿排水头,排水头下部为斜面,排水头中部开设有凹槽,排水头斜面处连接有斜板,供水开关连接有供水管,导水板截面为l形。
本装置使用时,丝纤从第一冷却机构上方向下移动,丝纤从两个辊子一中间穿过,丝纤贴紧上方的辊子一再贴紧下方的辊子一向下移动。丝纤再从第一箱体中部左侧的辊轴机构左侧绕向右侧的辊轴机构,在两个辊子机构上饶过数圈之后再从左侧的辊轴机构穿过第一辊轴框上方的第一进线口进入,丝纤绕过第一辊轴框内的一对辊轴机构由第一出线口进入至第二辊轴框;丝纤再绕过第二辊轴框内的一对辊轴机构后由第二出线口进入至第三辊轴框;丝纤再绕过第三辊轴框内的一对辊轴机构后由第三出线口进入至第四辊轴框;丝纤再绕过第四辊轴框内的一对辊轴机构后由第四出线口穿出;丝纤绕过第三箱体上方的导丝杆再从两个辊子二中间穿过,导丝杆上均匀开设有多个弧形凹槽,丝纤均匀位于导丝杆的弧形凹槽内,避免丝纤脱离导丝杆;丝纤贴紧两个辊子二向下移动从下方的导丝杆右侧绕过;丝纤再绕过第三箱体下部的一对辊轴机构,丝纤从第四箱体上的第五辊轴框的第五进线口的导丝杆绕过,丝纤再绕过第五辊轴框内的一对辊轴机构后由第五出线口进入至第六辊轴框;丝纤再绕过第六辊轴框内的一对辊轴机构,并由第六出线口处的导丝杆绕出,再绕过第四箱体上部的一对辊轴机构。丝纤再进入至引丝机构的引丝杆处,再经过排水头处的凹槽内,再贴近斜板上开设的线槽内导出,丝纤穿过收丝杆进入剪切机构。
向引丝机构的供水管供水,向外供液管以及内供液管供给冷却液,通过控制器控制电机、第一冷却电机、第二冷却电机进行转动;通过剪切台控制器控制剪切机构,此时九对辊轴机构带动丝纤进行移动拉伸。通过进液管一向积液槽一供给冷却液,通过进液管二向积液槽二供给冷却液,第一冷却电机带动两个辊子一进行转动,两个辊子一转向相反,辊子一转动时带动积液槽一内的冷却液沾湿丝纤,实现对丝纤的冷却降温,并具有保湿润滑的作用,使丝纤再后续工艺上更加顺滑;丝纤经过第二冷却机构时原理相同。供水管向供水开关供水,通过旋转旋钮可以控制供水量的大小,供水开关将丝纤进行湿润降温,多余的水通过斜板进行刮出,多余的水通过斜板的下端流向导水板,水再通过导水板流向水槽,水槽内的水可以通过设置排水管排出,技术方案较为简单,只要能将水排出即可,不在赘述。
通过转动调节螺栓可对辊筒相对于箱体的角度进行微调,以避免丝纤在成对的辊轴机构上进行缠绕拉伸时丝纤相互干扰,造成丝纤拉伸不均匀或者丝纤断裂,影响生产。调整时可以调整四个调节螺栓,调节螺栓末端对支架耳板进行压紧,以使得辊筒绕转杆进行转动调整;进而实现对辊筒角度的微调。
本装置的有益效果,将发用纤维生产过程中的各个工艺步骤进行集中安装放置,减少生产线占地面积,使得各个工艺之间的距离变得更加紧凑,提高生产效率,避免了各个工艺之间的人工搬运操作,使用该设备进行生产减少了人员的使用量,进而实现节约生产成本。
附图说明
图1为发明的结构示意图。
图2为发明的后侧面剖视图。
图3为发明的局部结构示意图。
图4为发明的左侧面结构剖视图。
图5为发明的左部后侧箱体局部结构剖视图。
图6为发明的辊轴机构结构示意图。
图7为发明的辊轴机构后视结构示意图。
图8为发明的辊轴机构后侧局部结构剖视图。
图9为发明的辊轴机构辊筒剖视图。
图10为发明的引丝机构结构示意图。
图11为发明的引丝机构局部结构示意图。
图12为发明的剪切装置结构示意图。
图13为发明的剪切装置局部结构剖视图。
图14为发明的剪切装置引丝机构示意图。
图15为发明的剪切装置牵丝张紧机构结构示意图。
图16为发明的剪切装置剪切机构结构示意图。
图17为发明的剪切装置剪切机构局部结构剖视图。
附图标记的零件列表
1.箱体机构、101.第一箱体、102.第二箱体、103.第三箱体、104.第四箱体、105.第一辊轴框、106.第二辊轴框、107.第三辊轴框、108.第四辊轴框、109.第五辊轴框、110.第六辊轴框、2.引丝机构、201.引丝台、202.引丝杆、203.供水管、204.旋钮、205.供水开关、206.收丝杆、207.导水板、208.排水头、209.斜板、3.剪切装置、4.第一冷却机构、401.第一冷却电机、402.第一从动轮、403.辊轴一、404.进液管一、405.第一皮带、406.辅从动轮、407.支撑杆、408.辊子一、409.积液槽一、410.第一主动轮、411.第一轴承、5.辊轴机构、501.辊筒、502.固定板、503.固定螺栓、504.调节螺栓、505.紧固螺栓、506.电机、507.转杆、508.电机耳板、509.支架耳板、510.辊轴支架、511.轴承、6.导丝杆、7.控制器、8.第二冷却机构、801.第二冷却电机、802.第二从动轮、803.辊轴二、804.进液管二、805.第二皮带、806.第二主动轮、807.第二轴承、808.辊子二、809.积液槽二、9.内供液管、10.固定板二、11.固定板一、12.外供液管、13.剪切台、1301.底板、1302.右侧板、1303.左侧板、1304.前板、1305.顶板、1306.后板;14.卷辊机构、1401.电机座、1402.卷辊电机、1403.轴承一、1404.卷辊;15.牵丝张紧机构、1501.支撑杆、1502.大导轮、1503.轴承四、1504.气弹簧座、1505.气弹簧、1506.轴承二、1507.转轴二、1508.z形杆、1509.小导轮、1510.轴承三、1511.转轴一;16.引丝机构、1601.引丝电机、1602.转盘、1603.转杆、1604.连接杆、1605.导杆、1606.引丝板、1607.导槽、1608.引丝环;17.剪切机构、1701.纵向电缸、1702.横向电缸、1703.小电缸、1704.滑动块、1705.上刀片、1706.凸形导槽、1707.连接块、1708.凸形导轨、1709.滑动杆、1710.转动杆一、1711.下刀片、1712、转动杆二、1713.转动杆三;18.剪切台控制器。
具体实施方式
实施例1,如图1-11所示,发制品假发纤维复合式全自动纺丝生产设备,包括箱体机构1,箱体机构1右下方设置有剪切机构,所述的箱体机构1包括有第一箱体101、第二箱体102、第三箱体103、第四箱体104、第一辊轴框105、第二辊轴框106、第三辊轴框107、第四辊轴框108、第五辊轴框109、第六辊轴框110,第一箱体101、第二箱体102、第三箱体103、第四箱体104从左到右依次排列,第一箱体101下部凸出,第一箱体101的前表面设置有第一辊轴框105,第二箱体102的前表面为阶梯型结构,第二箱体102的阶梯上从下到上依次设置有第二辊轴框106、第三辊轴框107、第四辊轴框108,第四箱体104上部为阶梯型结构,第四箱体104的阶梯处从下到上依次设置有第五辊轴框109、第六辊轴框110;第一辊轴框105、第二辊轴框106、第三辊轴框107、第四辊轴框108、第五辊轴框109、第六辊轴框110内各设置有一对辊轴机构5,第一箱体101的中部、第三箱体103的下部以及第四箱体104的上部也各设置有一对辊轴机构5;第一箱体101的左侧面设置有控制器7以及外供液管12,第一箱体101的上部设置有第一冷却机构4,第三箱体103的上部设置有第二冷却机构8,第二冷却机构8的上下方分别设置有一个导丝杆6;剪切机构上方设置有引丝机构。
第一辊轴框105上表面与第二辊轴框106上表面位于同一平面,第一辊轴框105上表面左侧开设有第一进线口,第一辊轴框105右侧面上部开设有第一出线口,第二辊轴框106左侧面上部开设有第二进线口,第二辊轴框106上表面左侧开设有第二出线口;第三辊轴框107下表面左侧开设有与第二出线口相对应的第三进线口,第三辊轴框107上表面左侧开设有第三出线口,第四辊轴框108下表面开设有与第三出线口相对应的第四进线口,第四进线框右侧面上部开设有第四出线口;第五辊轴框109下表面左侧开设有第五进线口,第五辊轴框109上表面左侧开设有第五出线口;第六辊轴框110下表面开设有与第五出线口相对应的第六进线口,第六辊轴框110上表面左侧开设有第六出线口;第五进线口与第六出线口处分别设置有一个导丝杆6。
辊轴机构5包括有辊筒501、固定板502、固定螺栓503、紧固螺栓505、调节螺栓504、辊轴支架510、电机506、转杆507、轴承511、电机耳板508、支架耳板509,固定板502通过固定螺栓503固定在箱体101上,固定板502中部开设有辊轴811孔,辊轴支架510位于辊轴811孔内,箱体101上开设有与辊轴811孔相同尺寸的电机506孔,固定板502后侧面开设有十字形凹槽,辊轴支架510外侧面固定连接有转杆507,辊轴支架510通过转杆507与固定板502转动连接,辊轴支架510外侧面均匀分布有四个支架耳板509,支架耳板509位于十字形凹槽内,电机506通过轴承511与辊轴支架510连接,电机506的外侧面均匀分布有四个电机耳板508,电机耳板508与支架耳板509通过紧固螺栓505连接,支架耳板509前侧面中部开设有弧形凹槽,固定板502上设置有四个调节螺栓504,调节螺栓504底部位于支架耳板509的弧形凹槽内。
第一冷却机构4包括有两个第一辊子机构、第一冷却电机401、第一主动轮410、第一皮带405、辅从动轮406、支撑杆407,第一箱体101内上部设置有固定板一11,第一冷却电机401固定在固定板一11上,第一冷却电机401输出端设置有第一主动轮410,支撑杆407固定在第一箱体101内,辅从动轮406与支撑杆407之间转动连接,两个第一辊子机构上下分布,第一辊子机构包括有第一从动轮402、积液槽一409、辊子一408、辊轴一403、第一轴承411、进液管一404,积液槽一409贯穿第一箱体101,积液槽内端部分侧面连接有进液管一404,进液管一404与外供液管12连接,辊轴一403外端面固定连接有辊子一408,辊轴一403贯穿第一箱体101,辊轴一403与第一箱体101之间通过第一轴承411连接,辊轴一403内端面固定连接有第一从动轮402;第一主动轮410、辅从动轮406、下方的第一辊子机构的第一从动轮402之间通过第一皮带405连接,上方的第一辊子机构的第一从动轮402与第一皮带405外侧面接触。
第二冷却机构8包括有两个第二辊子机构、第二冷却电机801、第二主动轮806、第二皮带805,第三箱体103内上部设置有固定板二10,第二冷却电机801固定在固定板二10上,第二冷却电机801输出端设置有第二主动轮806,两个第二辊子机构上下分布,第二辊子机构包括有第二从动轮802、积液槽二809、辊子二808、辊轴二803、第二轴承807、进液管二804,积液槽二809贯穿第三箱体103,积液槽内端部分侧面连接有进液管二804,进液管二804连接有内供液管9,辊轴二803外端面固定连接有辊子二808,辊轴二803贯穿第三箱体103,辊轴二803与第三箱体103之间通过第二轴承807连接,辊轴二803内端面固定连接有第二从动轮802;第二主动轮806、上方的第二辊子机构的第二从动轮802之间通过第二皮带805连接,下方的第二辊子机构的第二从动轮802与第二皮带805外侧面接触。
引丝机构2包括有引丝台201、供水管203、引丝杆202、收丝杆206、导水板207、供水开关205、旋钮204、排水头208、斜板209,引丝台201后端面固定连接在箱体101上,引丝台201底部开设有水槽,引丝台201内固定连接有导水板207,导水板207上固定连接有供水开关205,供水开关205上方设置有旋钮204,供水开关205左侧面的输出端贯穿排水头208,排水头208下部为斜面,排水头208中部开设有凹槽,排水头208斜面处连接有斜板209,供水开关205连接有供水管203,导水板207截面为l形。
在使用时,丝纤从第一冷却机构4上方向下移动,丝纤从两个辊子一408中间穿过,丝纤贴紧上方的辊子一408再贴紧下方的辊子一408向下移动。丝纤再从第一箱体101中部左侧的辊轴机构5左侧绕向右侧的辊轴机构5,在两个辊子机构上饶过数圈之后再从左侧的辊轴机构5穿过第一辊轴框105上方的第一进线口进入,丝纤绕过第一辊轴框105内的一对辊轴机构5由第一出线口进入至第二辊轴框106;丝纤再绕过第二辊轴框106内的一对辊轴机构5后由第二出线口进入至第三辊轴框107;丝纤再绕过第三辊轴框107内的一对辊轴机构5后由第三出线口进入至第四辊轴框108;丝纤再绕过第四辊轴框108内的一对辊轴机构5后由第四出线口穿出;丝纤绕过第三箱体103上方的导丝杆6再从两个辊子二中间穿过,导丝杆6上均匀开设有多个弧形凹槽,丝纤均匀位于导丝杆6的弧形凹槽内,避免丝纤脱离导丝杆6;丝纤贴紧两个辊子二向下移动从下方的导丝杆6右侧绕过;丝纤再绕过第三箱体103下部的一对辊轴机构5,丝纤从第四箱体104上的第五辊轴框109的第五进线口的导丝杆6绕过,丝纤再绕过第五辊轴框109内的一对辊轴机构5后由第五出线口进入至第六辊轴框110;丝纤再绕过第六辊轴框110内的一对辊轴机构5,并由第六出线口处的导丝杆6绕出,再绕过第四箱体104上部的一对辊轴机构5。丝纤再进入至引丝机构2的引丝杆202处,再经过排水头208处的凹槽内,再贴近斜板209上开设的线槽内导出,丝纤穿过收丝杆206进入剪切机构。
向引丝机构2的供水管203供水,向外供液管12以及内供液管9供给冷却液,通过控制器7控制电机、第一冷却电机401、第二冷却电机进行转动;通过剪切台13控制器18控制剪切机构,此时九对辊轴机构5带动丝纤进行移动拉伸。通过进液管一404向积液槽一409供给冷却液,通过进液管二向积液槽二供给冷却液,第一冷却电机401带动两个辊子一408进行转动,两个辊子一408转向相反,辊子一408转动时带动积液槽一409内的冷却液沾湿丝纤,实现对丝纤的冷却降温,并具有保湿润滑的作用,使丝纤再后续工艺上更加顺滑;丝纤经过第二冷却机构8时原理相同。供水管203向供水开关205供水,通过旋转旋钮204可以控制供水量的大小,供水开关205将丝纤进行湿润降温,多余的水通过斜板209进行刮出,多余的水通过斜板209的下端流向导水板207,水再通过导水板207流向水槽,水槽内的水可以通过设置排水管排出,技术方案较为简单,只要能将水排出即可,不在赘述。
通过转动调节螺栓504可对辊筒501相对于箱体的角度进行微调,以避免丝纤在成对的辊轴机构5上进行缠绕拉伸时丝纤相互干扰,造成丝纤拉伸不均匀或者丝纤断裂,影响生产。调整时可以调整四个调节螺栓504,调节螺栓504末端对支架耳板509进行压紧,以使得辊筒501绕转杆507进行转动调整;进而实现对辊筒501角度的微调。
剪切装置可以根据需要自行定制,在此特提供一种用于剪切丝纤的一种剪切装置,如图12-17所示,一种剪切装置,包括剪切台13,剪切台13包括有底板1301、左侧板1303、右侧板1302、顶板1305、前板1304、后板1306,底板1301、左侧板1303、右侧板1302、顶板1305、前板1304、后板1306相互连接成一个矩形剪切台,后板1306右侧延长至剪切台13外;剪切台13的右侧下部设置有卷辊机构14,剪切台13的右侧上部设置有牵丝张紧机构15,剪切台13的右侧面中部设置有引丝机构16,后板1306右部前侧面中部设置有剪切机构17,后板1306右部后侧面中部设置有剪切台控制器18,剪切台控制器18优选为三菱fx2n-64mt-001剪切台控制器18,剪切台控制器18用来控制卷辊电机1402、引丝电机1601的启停,卷辊电机1402以及引丝电机1601优选为塞雷42hs08步进电机以满足剪切台控制器18的设定功能,通过剪切台控制器18设定当卷辊电机1402、引丝电机1601停止时引丝环1608始终位于导槽1607的右端,通过剪切台控制器18设定当启动剪切功能时剪切机构1701先向前移动,带动滑动杆1709向前移动,使发用化纤丝位于与下刀片1711与上刀片1705夹角水平的位置,横向电缸1702带动滑动块1704向右移动,凸形导轨1708沿凸形导槽1706向右移动,直至滑动块1704移动到最右端,此时发用化纤丝位于下刀片1711与上刀片1705的夹角内,上刀片1705与小电缸1703输出端通过转动杆三1713转动连接,以及小电缸1703与滑动块1704之间通过转动杆二1712转动连接,实现小电缸1703收缩带动上刀片1705左端绕滑动杆1710向后移动,上刀片1705右端绕滑动杆1710向下刀片1711方向移动,下刀片1711与上刀片1705完成对发用化纤的剪切;剪切完成后小电缸1703、横向电缸1702以及剪切机构1701复位。
卷辊机构14包括有卷辊电机1402、电机座1401、轴承一1403、卷辊1404,电机座1401固定连接在底板1301上表面,电机座1401上设置有卷辊电机1402,卷辊电机1402输出端固定连接有卷辊1404,卷辊电机1402输出端贯穿右侧板1302,卷辊电机1402输出端通过轴承一1403与右侧板1302连接。
牵丝张紧机构15包括有气弹簧1505、气弹簧座1504、转轴一1511、转轴二1507、轴承二1506、z形杆1508、轴承三1510、小导轮1509、支撑杆1501、大导轮1502、轴承四1503,大导轮1502与小导轮1509外侧面中部开设有环形凹槽,且大导轮1502与小导轮1509的外侧面中间位置位于同一平面;z形杆1508位于支撑杆1501前下方。气弹簧座1504通过转轴一1511与右侧板1302上部转动连接,气弹簧座1504上设置有气弹簧1505,气弹簧1505输出端通过转轴二1507与z形杆1508中部前端连接,z形杆1508左端通过轴承二1506与右侧板1302转动连接,z形杆1508右端通过轴承三1510连接有小导轮1509;支撑杆1501固定连接在右侧板1302上部中间位置,支撑杆1501右端通过轴承四1503与大导轮1502转动连接。
引丝机构16包括有引丝电机1601、转盘1602、转杆1603、连接杆1604、导杆1605、引丝板1606、导槽1607、引丝环1608,引丝电机1601固定连接在后板1306前表面右侧中部,引丝电机1601输出端固定连接有转盘1602,转盘1602外侧边缘通过转杆1603转动连接有连接杆1604,连接杆1604与导杆1605之间为转动连接,导杆1605前侧面右端固定连接有引丝环1608,引丝板1606固定连接在后板1306前侧面右部中间位置,且引丝板1606贯穿右侧板1302,引丝板1606前侧面开设有导槽1607,引丝环1608分为杆与环两部分,杆固定在环的外侧面,杆末端与导杆1605连接,杆部可滑动的位于导槽1607内;导杆1605可滑动的位于引丝板1606内,引丝环1608贯穿导槽1607且可在导槽1607内左右移动。
剪切机构17包括有剪切机构1701、横向电缸1702、小电缸1703、滑动杆1709、滑动块1704、凸形导轨1708、连接块1707、上刀片1705、下刀片1711,剪切机构1701、横向电缸1702优选为上海昱多自动化科技有限公司迈普罗p045电缸,小电缸1703优选为kss品牌的dda微型电缸;上刀片1705与小电缸1703输出端通过转动杆三1713转动连接,以及小电缸1703与滑动块1704之间通过转动杆二1712转动连接,实现小电缸1703收缩带动上刀片1705左端绕滑动杆1710向后移动,滑动杆1709两端固定连接有连接块1707,连接块1707后端固定连接有剪切机构1701,剪切机构1701垂直固定连接在后板1306前侧面右部中间位置,滑动杆1709左部上表面固定连接有横向电缸1702,横向电缸1702输出端固定连接有滑动块1704,滑动块1704下表面中部固定连接有凸形导轨1708,滑动杆1709上表面中部开设有凸形导槽1706,凸形导轨1708滑动位于凸形导槽1706中,凸形导轨1708与凸形导槽1706为间隙配合且可相对滑动。小电缸1703转动连接在滑动块1704上表面左部,小电缸1703输出端与上刀片1705左端转动连接,下刀片1711固定连接滑动块1704上表面右部,上刀片1705与下刀片1711中部转动连接。
在使用时,将丝辊套装在卷辊机构14上的卷辊1404上,再将发用化纤从牵丝张紧机构15的小导轮1509下方绕过,再从大导轮1502上方绕过,当发用化纤丝较紧时,小导轮1509受向上的力,气弹簧1505受压收缩,小导轮1509上移,小导轮1509与大导轮1502之间的距离变短,缓解发用化纤丝的张紧力,避免发用化纤丝拉断;再将发用化纤穿过引丝机构16的引丝环1608,再将发用化纤绕在卷辊机构14上的丝辊上;通过剪切台控制器18控制卷辊电机1402以及引丝电机1601进行转动,卷辊电机1402带动丝辊进行转动,丝辊将发用化纤进行收卷,引丝电机1601带动转盘1602进行转动,转盘1602转动时连接杆1604右端带动导杆1605左右移动,导杆1605在引丝板1606内进行移动,导杆1605带动引丝环1608沿着导槽1607进行左右移动;此时发用化纤丝在引丝环1608的带动下绕丝辊左右移动缠绕,避免发用化纤丝只缠绕在丝辊的某一处位置,使发用化纤丝在丝辊上均匀分布,当发用化纤丝缠绕完成,通过剪切台控制器18控制卷辊电机1402以及引丝电机1601停止转动,通过剪切台控制器18设定当引丝电机1601以及卷辊电机1402停止时引丝环1608停在导槽1607内最右端。
再通过剪切台控制器18控制剪切机构17对化纤丝进行剪切,此时剪切机构1701先向前移动,带动滑动杆1709向前移动,使发用化纤丝位于与下刀片1711与上刀片1705夹角水平的位置,横向电缸1702带动滑动块1704向右移动,凸形导轨1708沿凸形导槽1706向右移动,直至滑动块1704移动到最右端,此时发用化纤丝位于下刀片1711与上刀片1705的夹角内,上刀片1705与小电缸1703输出端通过转动杆三1713转动连接,以及小电缸1703与滑动块1704之间通过转动杆二1712转动连接,实现小电缸1703收缩带动上刀片1705左端绕滑动杆1710向后移动,上刀片1705右端绕滑动杆1710向下刀片1711方向移动,下刀片1711与上刀片1705完成对发用化纤的剪切;剪切完成后小电缸1703、横向电缸1702以及剪切机构1701复位。
在本发明的描述中,需要理解的是,术语“中心”、“纵向”、“横向”、“长度”、“宽度”、“厚度”、“上”、“下”、“前”、“后”、“左”、“右”、“竖直”、“水平”、“顶”、“底”、“内”、“外”、“顺时针”、“逆时针”等指示的方位或位置关系为基于附图所示的方位或位置关系,仅是为了便于描述本发明和简化描述,而不是指示或暗示所指的设备或元件必须具有特定的方位、以特定的方位构造和操作,因此不能理解为对本发明的限制。
以上所述仅为本发明的优选实施例而已,并不用以限制本发明,对于本领域的技术人员来说,本发明可以有各种更改和变化,凡在本发明的精神和原则之内,所作的任何修改、等同替换、改进等,均应包含在本发明的保护范围之内。
起点商标作为专业知识产权交易平台,可以帮助大家解决很多问题,如果大家想要了解更多知产交易信息请点击 【在线咨询】或添加微信 【19522093243】与客服一对一沟通,为大家解决相关问题。
此文章来源于网络,如有侵权,请联系删除


