一种生物基聚酰胺短纤维聚纺牵定一体化成型制备方法及设备与流程



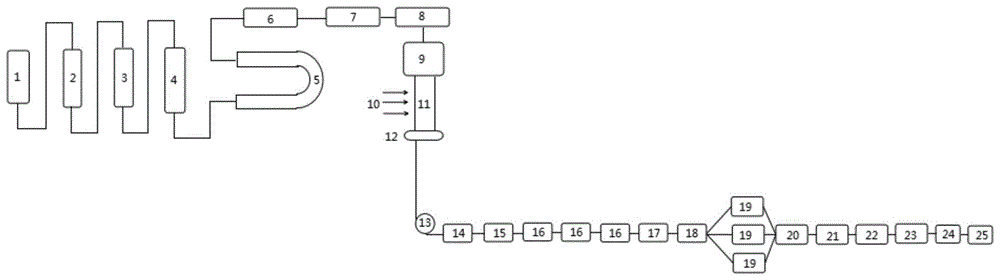
本发明涉及一种生物基聚酰胺短纤维聚纺牵定一体成型制备方法及设备,属于纤维材料制备领域。
背景技术:
聚酰胺纤维又称尼龙、锦纶是世界上最早发展并实现工业化生产的一大类合成纤维。迄今已有80多年的发展历史,是现代工业重要的聚合物材料之一。聚酰胺(pa)的重复单元(单体)具有酰胺基团作为特征性特征,由于其断裂强度高、耐磨、耐疲劳、轻质柔软、透气吸湿、弹性好等特点,在军工产品、橡胶骨架材料、绳、网、索类、篷布、工业滤布以及在高档缝纫线用丝、t恤衫用丝、雨伞面料、运动纺织品等领域拥有良好的市场前景。
目前市场占有量最大的聚酰胺6和聚酰胺66的生产原料主要来源于石油化工产品,面对世界化石资源的日益匮乏、全球环境的不断恶化,寻找清洁能源以替代石油化工产品,已是各国工业发展的重点关注方向。生物基聚酰胺是利用微生物发酵淀粉制备出戊二胺,进而与己二酸聚合纺丝制备了生物基聚酰胺纤维,具有绿色、环境友好、原料可再生以及可生物降解的特性,有助于解决当前全球经济社会发展所面临的严重的资源和能源短缺,以及环境污染等问题,是当今世界各国纺织纤维发展竞争的热点。
传统直接纺丝法是将聚合后的聚合物熔体直接送至纺丝机进行纺丝,然后经过集束、牵伸、定型等工序制备纤维,虽然工序短,成本低,但是直到现在,聚酰类纤维直接纺丝技术尚未成熟,产品性能不稳定,而随着生物基材料的兴起,生物基聚酰胺纤维逐渐成为焦点,我国急需开发产品质量好、生产成本低的适用于生物基类聚酰胺纤维的直接纺丝方法。
技术实现要素:
本发明的目的是提供一种生物基聚酰胺短纤维聚纺牵定一体化成型的制备方法及设备。
本发明提供的一种生物基聚酰胺短纤维聚纺牵定一体化成型的设备,包括依次连接的盐液调配装置系统、聚合反应装置系统、纺丝牵定装置系统和集束切断装置系统;
所述盐液调配装置系统包括依次连接的精盐储罐、盐液调配罐、盐液中间罐;
所述聚合反应装置系统包括依次连接的浓缩槽、u型反应器、闪蒸器、前聚合器和后聚合器;所述盐液中间罐与所述浓缩槽的入口相连接;
所述纺丝牵定装置系统包括依次连接的纺丝箱、上油装置、卷绕装置、牵伸装置、紧张热定型装置、冷却上油装置;其中,所述纺丝箱的纺丝甬道旁设有对其内流经的所述纺丝箱产出的熔体细流进行冷却的吹风装置;所述牵伸装置包括依次连接的第一牵伸机、第二牵伸机和第三牵伸机,所述第一牵伸机、所述第二牵伸机和所述第三牵伸机上均设有控温装置,所述第三牵伸机后连接紧张热定型装置、冷却上油装置;
所述集束切断装置系统包括依次连接的集束装置、叠丝装置、卷曲装置、松弛热定型装置、烘干装置、切断装置和打包装置。
本发明中,所述牵伸装置具体根据制备产品性能要求不同拆分组合,所述第一牵伸机进行常温牵伸、所述第二牵伸机进行低温牵伸、所述第三牵伸机进行热牵伸;如根据牵伸为一级牵伸、二级牵伸或多级牵伸,具体如第一牵伸机、第二牵伸机和第三牵伸机可均为至少1台牵伸机依次连接;更具体如第三牵伸机数量为3台牵伸机连接,以进行三级牵伸;
所述控温装置的控温方式具体可为水浴控温、热板控温和蒸汽控温中的至少一种。
本发明中,采用上述的设备进行纤维成型加工过程如下:所述纺丝箱产出熔体细流;所述熔体细流流经所述纺丝甬道;所述吹风装置对流经所述纺丝甬道的熔体细流进行冷却吹风,使其冷却凝固成为丝条;丝条经过上油装置上油,卷绕装置卷绕后,经过牵伸装置牵伸、紧张热定型装置定型;然后依次经所述冷却上油装置、集束装置、叠丝装置、卷曲装置、松弛热定型装置、烘干装置、切断装置、打包装置进行冷却上油、集束、叠丝、卷曲、松弛热定型、烘干、切断、打包步骤完成生物基聚酰胺短纤的制备。
本发明还提供了一种利用上述设备一体化成型制备生物基聚酰胺短纤维的方法,包括如下步骤:
1)盐液配制过程:将所述精盐储罐中的聚酰胺干盐注入所述盐液调配罐配制成聚酰胺盐水溶液,并将其存储于所述盐液中间罐;
2)聚合过程:所述盐液中间罐中聚酰胺盐水溶液经所述浓缩槽浓缩后进入所述u型反应器中进行预聚反应,预聚反应后在所述闪蒸器中进行快速解压,再依次进入所述前聚合器和所述后聚合器中,分别进行前聚合反应和后聚合反应,得到聚酰胺聚合物;
3)纺丝牵定过程:将所述聚酰胺聚合物熔体经所述纺丝箱的喷丝板喷出熔体细流,熔体细流流经所述纺丝甬道,经所述吹风装置冷却凝固成为丝条,所述丝条经所述上油装置上油、卷绕装置卷绕、牵伸装置牵伸,紧张热定型装置定型,冷却上油装置冷却上油后得到牵伸丝束;
4)集束切断过程:所述牵伸丝束依次经所述集束装置集束、所述叠丝装置叠丝、所述卷曲装置卷曲、所述松弛热定型装置松弛热定型、所述烘干装置烘干,最后经所述切断装置和打包装置依次切断、打包,即得到所述生物基聚酰胺短纤维。
上述的方法中,步骤1)所述聚酰胺盐水溶液的质量百分含量可为20%~80%,ph值7.25~7.95。
上述的方法中,步骤1)中还包括通过所述盐液调配罐添加助剂对所述聚酰胺进行改性的步骤。
上述的方法中,所述助剂包括分子量调节剂、阻燃剂、抗静电剂、抗菌整理剂、抗紫外线整理剂、消光剂中的至少一种;
所述助剂加入量为所述聚酰胺56干盐质量的0.10%~5.50%。
上述的方法中,步骤2)所述浓缩槽控制压力:25~35kpa;物料出口温度105~130℃。
上述的方法中,步骤2)所述u型反应器采用三段加热中进行预聚反应的条件如下:r1段入口物料温度:150~220℃,r2段出口物料温度:170~260℃,r3段出口物料温度:170~260℃,控制反应器压力稳定在1.70~1.80mpa。
上述的方法中,步骤2)所述闪蒸器中释放反应器内的压力,所述闪蒸器出口物料温度升至180~290℃。
上述的方法中,步骤2)所述前聚合反应的条件如下:液位稳定在30~50%,物料出口温度为220℃~285℃,时间为20~120min。
上述的方法中,步骤2)所述后聚合反应的条件如下:液位稳定在30~50%,真空度:50~80kpa,物料出口温度为220℃~290℃,时间为10~60min,增压泵压力:10~15mpa。
上述的方法中,步骤3)中所述聚酰胺聚合物熔体经喷丝板喷出得到熔体细流的过程如下:所述纺丝箱温度为:纺丝箱体一区温度270~290℃,二区温度270~290℃,三区温度270~290℃,计量泵温度270~290℃,纺丝组件温度为270~290℃;计量泵转速12~18rpm/min在纺丝箱体内,所述聚酰胺聚合物熔体通过管路分配,以相等的停留时间和压力降输送到每一个喷丝口,喷丝头孔数500~5000根;纺丝速率可为1000~3000m/min,具体可为2000m/min、1000~2000m/min、2000~3000m/min或1500~2500m/min。
上述的方法中,所述熔体细流经吹风装置冷却成型,所述吹风装置可为侧吹风装置或环吹风装置,其条件如下:风速可为0.30~0.50m/min;风温可为20~25℃;风压可为400~500pa;风速具体可为0.50m/min、0.30~0.50m/min、0.50~0.80m/min或0.40~0.70m/min;风温具体可为25℃、21~25℃、25~26℃或23~26℃;风压具体可为440pa、420~440pa、440~480pa或430~470pa;
所述上油的油剂浓度可为1~10%。
上述的方法中,所述牵伸过程包括依次经所述第一牵伸机进行常温牵伸、所述第二牵伸机进行低温牵伸、所述第三牵伸机进行热牵伸;其中所述牵伸可为一级牵伸、二级牵伸或多级牵伸,牵伸后纤维经过紧张热定型装置、冷却上油装置后集束;
所述常温牵伸中牵伸温度可为15~30℃,牵伸的倍率可为1.01~1.85倍;
所述低温牵伸中牵伸温度可为5~20℃,牵伸的倍率可为1.01~1.15倍;
所述热牵伸中牵伸温度可为60~210℃,牵伸的倍率可为1.01~6.0倍;
所述紧张热定型温度根据常温、低温、热牵伸温度的不同,范围可为98~230℃,具体可为150℃、170℃、190℃、210℃、230℃、150~170℃、150~190℃或150~230℃;
所述冷却上油装置,油剂浓度可为2%~6%;
所述紧张热定型根据制备纤维性能要求选择不同定型工艺,所述紧张热定型加热方式包括干热空气定型、接触加热定型、水蒸气湿热定型和浴液定型中的至少一种。所述浴液定型采用的液体为水或甘油。
上述的方法中,步骤4)中所述卷曲装置参数:主压气缸减压阀压力1~3bar、背压气缸减压阀压力1bar,卷曲温度可为60~90℃,速率可为900~1000m/min,具体可300m/min、300~320m/min或300~340m/min,卷曲数可为10~30个,具体可为15个、10~15个、15~30个或12~25个。
上述的方法中,步骤4)中所述松弛热定型加热方式包括干热空气定型和/或接触加热定型,所述松弛热定型的温度可为95~190℃,停留时间为3~15min。
本发明进一步提供了上述的方法制备得到的生物基聚酰胺短纤维。
本发明所述生物基聚酰胺短纤维的性能参数如下:断裂强度4.0~8.0cn/dtex,极限氧指数28.0~36.0%。
本发明具有以下优点:
本发明工艺流程改变,(1)由于生物基聚酰胺纤维冷却速率较慢,先集束后牵伸容易导致融丝,使产品性能下降;(2)在牵伸过程加入常温牵伸、低温牵伸步骤,纤维快速冷却,使聚合物分子链没有充足的时间排布与堆砌,导致结晶困难、不完善,一方面避免了由于纤维冷却速率慢,集束后直接牵伸纤维芯皮层差异大,成品纤维性能不稳定等情况,另一方面有助于改善纤维性能,常温牵伸和低温牵伸有助于后续高倍牵伸,从而得到性能优异的短纤维;(3)改变生物基聚酰胺纤维的牵伸工艺和热定型温度条件,针对生物基聚酰胺调整工艺设备可以改善纤维的结晶度、取向度、力学性能、阻燃性等。
本发明的设备装置是连续生产装置,从盐水溶液配置开始一直到切断纤维是连续一体化生产过程,摒弃了传统的间歇式生产,有效的节约了生产成本,提高了工作效率。
附图说明
图1为本发明生物基聚酰胺56短纤维聚纺牵定一体化成型设备的连接示意图。
图2为本发明生物基聚酰胺56短纤维聚纺牵定一体化成型制备工艺流程图。
图3为现有生产聚酰胺66纤维的工艺流程图
图1、图3中各个标记如下:
1精盐储罐;2盐液调配罐;3盐液中间罐;4浓缩槽;5u型反应器;6闪蒸器;7前聚合器;8后聚合器;9纺丝箱;10吹风装置;11纺丝甬道;12上油装置;13卷绕装置;14第一牵伸机;15第二牵伸机;16第三牵伸机;17紧张热定型装置;18冷却上油装置19集束装置;20叠丝装置;21卷曲装置;22松弛热定型装置;23烘干装置;24切断装置;25打包装置。
具体实施方式
下述实施例中所使用的实验方法如无特殊说明,均为常规方法。
下述实施例中所用的材料、试剂等,如无特殊说明,均可从商业途径得到。
下述实施例中,1、线密度根据gb/t14335-2008测试;
2、断裂强度和断裂伸长率(%)根据gb/t14337-2008测试;
3、极限氧指数根据gb/t5454-1997测试;
4、差示扫描量热仪(dsc)测试纤维的熔点、结晶度;
5、回潮率:根据gb/t6503-2008测试。
如图1所示,为本发明生物基聚酰胺短纤维设备。它包括依次连接的盐液调配装置系统、聚合反应装置系统、纺丝牵定装置系统和集束切断装置系统;
盐液调配装置系统包括依次连接的精盐储罐1、盐液调配罐2、盐液中间罐3;
聚合反应装置系统包括依次连接的浓缩槽4、u型反应器5、闪蒸器6、前聚合器7和后聚合器8;盐液中间罐3与浓缩槽4的入口相连接;
纺丝牵定装置系统包括依次连接的纺丝箱9、上油装置12、卷绕装置13、牵伸装置(由依次连接的第一牵伸机14、第二牵伸机15、第三牵伸机16组成,第一牵伸机14、第二牵伸机15和第三牵伸机16上均设有控温装置,牵伸装置可以根据制备产品性能要求不同拆分组合(如根据牵伸为一级牵伸、二级牵伸或多级牵伸,具体如第一牵伸机14、第二牵伸机15和第三牵伸机16可均为1~3台依次连接;本例具体如第三牵伸机16数量为3台连接,以进行二级牵伸,如图3所示。),控温装置的控温方式为水浴控温、热板控温和蒸汽控温中的至少一种)、紧张热定型装置17;冷却上油装置18;其中,纺丝箱9中纺丝甬道11旁设有对其内流经的纺丝箱9产出的熔体细流进行冷却的吹风装置10;
集束切断装置系统包括依次连接的集束装置19、叠丝装置20、卷曲装置21、松弛热定型装置22、烘干装置23、切断装置24和打包装置25。
实施例1、生物基聚酰胺56短纤维的一体化成型制备
采用如图1中所示装置,并按照如图2所示的工艺流程进行一体化成型制备生物基聚酰胺56短纤维,具体步骤如:
配制质量百分浓度为60%的聚酰胺56盐水溶液。将已制备好的聚酰胺56盐水溶液注入盐液中间罐2,调节ph值为7.85,然后进入浓缩槽4,浓缩槽4压力30kpa,物料出口温度:120℃;u型反应器5的r1段入口物料温度控制入口温度:217℃,r2段出口温度:224℃,r3段出口温度:245℃,u型反应器5压力1.75mpa,反应后得到预聚体;
预聚体进入闪蒸器6,控制出口物料温度升至277℃,预聚体进入前聚合器7中进行前聚合反应,控制液位45%,物料出口温度278℃,时间为20min;进入后聚合器8中进行后聚合反应,控制液位45%,真空度:65kpa,物料出口温度为280℃,时间10min,增压泵压力:12mpa,反应后得到聚酰胺56聚合物;聚酰胺56聚合物进入纺丝箱9进行纺丝,纺丝箱9温度:一区285℃,二区285℃,三区285℃,计量泵温度285℃,计量泵转速13rpm/min,纺丝组件温度为285℃,喷丝头孔数2300根,纺丝速率2000m/min,侧吹风速为0.50m/min;风温为25℃,侧吹风压为440pa;油剂浓度5%(卷绕油剂为f5103,商购于日本竹本),卷绕上油后纤维依次进行一级常温牵伸温度20℃,牵伸倍率1.55倍;一级低温牵伸温度5℃,牵伸倍率1.03倍;二级热牵伸的一牵倍率3.57,二牵倍率1.12、一辊温度80℃,二辊温度150℃,三辊温度170℃,控制热板温度170℃进行干热空气紧张定型。定型后纤维冷却上油,油剂浓度3%,再集束,集束后将纤维三片丝叠成一片后进行卷曲,卷曲主压气缸减压阀压力2bar,背压气缸减压阀压力1bar,卷曲温度可为60℃,速率可为1000m/min、卷曲数15个,然后在热板温度150℃条件下10min接触加热松弛热定型,最后经烘干、切断、打包,即得到聚酰胺56短纤维。
聚酰胺56短纤记为1#,其性能测试结果如表1所示。
实施例2、
配制质量百分浓度为60%的聚酰胺56盐水溶液。将已制备好的聚酰胺56盐水溶液注入盐液中间罐3,同时加入聚酰胺56干盐质量的0.50%消光剂二氧化钛,调节ph值为7.85,将聚酰胺56改性。其余工艺与本发明实施例1完全相同。得到聚酰胺56短纤,记为2#,其性能测试结果如表1所示。
实施例3
采用如图1中所示装置,并按照如图2所示的工艺流程进行一体化成型制备聚酰胺56/66短纤维,具体步骤如:
按照聚酰胺56干盐与聚酰胺66干盐质量比为9:1,配制质量百分浓度为65%的聚酰胺56/66盐水溶液,其中。将已制备好的聚酰胺56/66盐水溶液注入盐液中间罐,调节ph值为7.82,然后进入浓缩槽,浓缩槽压力30kpa,物料出口温度:120℃;u型反应器的r1段入口物料温度控制入口温度:217℃,r2段出口温度:224℃,r3段出口温度:245℃,u型反应器压力1.8mpa,反应后得到预聚体;
预聚体进入闪蒸器6,控制出口物料温度升至277℃,预聚体进入前聚合器7中进行前聚合反应,控制液位45%,物料出口温度278℃,时间为20min;进入后聚合器8中进行后聚合反应,控制液位45%,真空度:65kpa,物料出口温度为280℃,时间10min,增压泵压力:12mpa,反应后得到聚酰胺56/66聚合物;聚酰胺56/66聚合物进入纺丝箱9进行纺丝,纺丝箱9温度:一区286℃,二区288℃,三区287℃,计量泵温度287℃,计量泵转速12.4rpm/min,纺丝组件温度为287℃,喷丝头孔数2300根,纺丝速率2400m/min,侧吹风速为0.40m/min;风温为20℃,侧吹风压为480pa;油剂浓度6%(卷绕油剂为f5103,商购于日本竹本),卷绕上油后纤维依次进行一级常温牵伸温度20℃,牵伸倍率1.32倍;一级低温牵伸温度5℃,牵伸倍率1.02倍;二级热牵伸的一牵倍率3.34,二牵倍率1.12、一辊温度90℃,二辊温度160℃,三辊温度175℃,控制热板温度175℃进行干热空气紧张定型。定型后纤维冷却上油,油剂浓度3%,再集束,集束后将纤维三片丝叠成一片后进行卷曲,卷曲主压气缸减压阀压力2bar,背压气缸减压阀压力1bar,卷曲温度可为60℃,速率可为1000m/min、卷曲数15个,然后在热板温度160℃条件下10min接触加热松弛热定型,最后经烘干、切断、打包,即得到聚酰胺56/66短纤维。
聚酰胺56/66短纤记为3#,其性能测试结果如表1所示。
实施例4、生物基聚酰胺510短纤维的一体化成型制备
采用如图1中所示装置,并按照如图2所示的工艺流程进行一体化成型制备聚酰胺510短纤维,具体步骤如:
按照配制质量百分浓度为55%的聚酰胺510盐水溶液。将已制备好的聚酰胺510盐水溶液注入盐液中间罐2,调节ph值为7.45,然后进入浓缩槽4,浓缩槽4压力25kpa,物料出口温度:100℃;u型反应器5的r1段入口物料温度控制入口温度:170℃,r2段出口温度:180℃,r3段出口温度:185℃,u型反应器5压力1.78mpa,反应后得到预聚体;预聚体进入闪蒸器6,控制出口物料温度升至185℃,预聚体进入前聚合器7中进行前聚合反应,控制液位45%,物料出口温度215℃,时间为60min;进入后聚合器8中进行后聚合反应,控制液位45%,真空度:60kpa,物料出口温度为215℃,时间20min,增压泵压力:14mpa,反应后得到聚酰胺510聚合物;聚酰胺510聚合物进入纺丝箱9进行纺丝,纺丝箱9温度:一区245℃,二区245℃,三区245℃,计量泵温度245℃,计量泵转速15rpm/min,纺丝组件温度为245℃,喷丝头孔数2000根,纺丝速率900m/min,侧吹风速为0.50m/min;风温为22℃,侧吹风压为430pa;油剂浓度3%(卷绕油剂为f5103,商购于日本竹本),卷绕上油后纤维依次进行一级常温牵伸温度18℃,牵伸倍率1.15倍;一级低温牵伸温度8℃,牵伸倍率1.04倍;二级热牵伸一牵倍率2.83,二牵倍率1.07、一辊温度60℃,二辊温度120℃,三辊温度150℃,控制热板温度150℃进行干热空气紧张定型。定型后纤维冷却上油,油剂浓度3%,再集束,集束后将纤维三片丝叠成一片后进行卷曲,卷曲主压气缸减压阀压力2bar,背压气缸减压阀压力1bar,卷曲温度可为50℃,速率可为900m/min、卷曲数15个,然后在热板温度130℃条件下12min接触加热松弛热定型,最后经烘干、切断、打包,即得到聚酰胺510短纤维。
聚酰胺510短纤记为4#,其性能测试结果如表1所示。
表1聚酰胺短纤维测试数据
实施例5、
聚酰胺56盐水溶液配置、聚合反应以及熔融纺丝过程均与本发明实施例1完全相同,改变后纺工艺中热牵伸温度,研究纤维性能变化。未牵伸纤维记为3#。
后纺工艺中热牵伸定型工艺:二级热牵伸,一牵倍率(分别牵伸2.0、2.5、3.0、3.4);二牵倍率1.05;牵伸箱一辊温度80℃;二辊温度150℃;三辊温度170℃;牵伸后在热板温度170℃的条件下进行干热空气紧张定型。本对比例制备的聚酰胺56短纤记为5#~9#。
纤维熔点、熔融焓、结晶度、取向、力学性能测试结果如表2所示。
未牵伸丝的熔点在252.2℃,纤维拉伸后,熔点有微弱的升高。当牵伸倍数增加到3.0时,tm升到230.1℃。牵伸后,纤维的结晶度迅速增加,牵伸倍数大于2.5后,结晶度增加缓慢。未牵伸丝无取向,牵伸后,结晶和声速取向都随着牵伸倍数的增加而增加,断裂强度随着牵伸倍数的增加缓慢增加。
表2pa56纤维熔点、熔融焓、结晶度、取向、力学性能测试结果
测试牵伸工艺前后纤维物理性能,随着牵伸倍数增加,纤维的结晶和声速取向都增加,机械性能中,断裂强度缓慢增加。
实施例6、
聚酰胺56盐水溶液配置、聚合反应以及熔融纺丝过程均与本发明实施例1完全相同,改变后纺热牵伸定型工艺中定型温度,研究纤维性能变化。未定型纤维记为10#。
后纺热牵伸定型工艺:二级热牵伸的一牵倍率3.0;二牵倍率1.05;牵伸箱一辊温度80℃;二辊温度150℃;三辊温度170℃;牵伸后控制热板温度(150~230℃,间隔20℃)的条件下进行干热空气紧张定型。本实施例制备的聚酰胺56短纤记为11#~15#。
在150~230℃范围内不同温度的热定型过程中,不同温度定型聚酰胺56纤维的晶体取向从76.04增加到82.09,如表3所示。
表3热定型温度对纤维结构的影响
升高温度有利于聚合物分子链排列的更加规整,形成更加完整的结晶结构,因此热定型后纤维结晶度总体呈增长趋势,但是在热定型温度在150~170℃条件下,结晶度最高;在150~210℃范围内不同温度的热定型过程中,锦纶56纤维的晶体取向有所增加,断裂强度成增长趋势,当温度继续升高至230℃,晶区取向减小,断裂强度降低,这可能是由于高温处理纤维强力损伤。
对比例1、
聚酰胺56盐水溶液配置、聚合反应以及熔融纺丝过程均与本发明实施例1的参数设定完全相同,当纤维冷却成丝条上油后,按照传统纺丝加工进行,直接进行集束、牵伸工艺,同样工艺参照本发明实施例1设定参数,试验中发现丝束汇聚后在卷绕桶上偶尔出现熔丝现象,并且产出的纤维外观出现毛丝、测试性能强度低仅为0.84cn/dtex,无法达到应用标准。
这可能是因为聚酰胺56的冷却结晶温度低,结晶速率慢。在纺丝时,纤维没有完全冷却就开始卷绕,多层纤维叠加,纤维内部热量无法散失,不仅出现熔丝现象,而且影响产品性能,但是如果直接将初生纤维温度冷却到10℃以下,则纤维可能发生脆损,因此,聚酰胺56初生纤维需要依次进行常温牵伸、低温牵伸、热牵伸后再进行后续工艺流程。本发明增加常温牵伸、低温牵伸工艺一方面使纤维快速降温,保证后续工序顺利进行;另一方面由于聚合物分子链折叠进入晶格的速度跟不上温度的下降速度,分子链没有充足的时间排布与堆砌,因而结晶困难、不完善,有助于后续高倍牵伸,得到性能优异的短纤维。
对比例2、
常规工艺制备生物基聚酰胺56:
采用现有聚酰胺66生产流程,制备聚酰胺56短纤维,具体步骤如:
聚酰胺56盐液配制、聚合按照实施例1内容制备;
聚酰胺56聚合物进入纺丝箱纺丝,纺丝箱温度:一区285℃,二区285℃,三区285℃,计量泵温度285℃,计量泵转速13rpm/min,喷丝头孔数2300根,纺丝组件温度为285℃,纺丝速率2000m/min,侧吹风速为0.50m/min;风温为25℃,侧吹风压为440pa;油剂浓度5%(卷绕油剂为f5103,商购于日本竹本),集束,卷绕上油后纤维进行二级牵伸,一牵倍率3.57,二牵倍率1.12、一辊温度80℃,二辊温度150℃,三辊温度170℃,控制热板温度170℃进行干热空气紧张定型。再将纤维三片丝叠成一片后进行卷曲,卷曲主压气缸减压阀压力2bar,背压气缸减压阀压力1bar,卷曲温度可为60℃,速率可为900m/min、卷曲数15个,然后在热板温度150℃条件下10min接触加热松弛热定型,最后经烘干、切断、打包,即得到聚酰胺56短纤维。
本对比例制备的纤维断裂强度3.23cn/dtex,断裂伸长率54.3%,极限氧指数23%。
由上述数据可知,通过与对比例2相比,本发明制备的聚酰胺56短纤维断裂强度和极限氧指数更高,说明本发明工艺可以改善聚酰胺类纤维的力学性能及阻燃性能。
起点商标作为专业知识产权交易平台,可以帮助大家解决很多问题,如果大家想要了解更多知产交易信息请点击 【在线咨询】或添加微信 【19522093243】与客服一对一沟通,为大家解决相关问题。
此文章来源于网络,如有侵权,请联系删除


