全自动防抓棉打手夹死圆盘抓棉机的制作方法



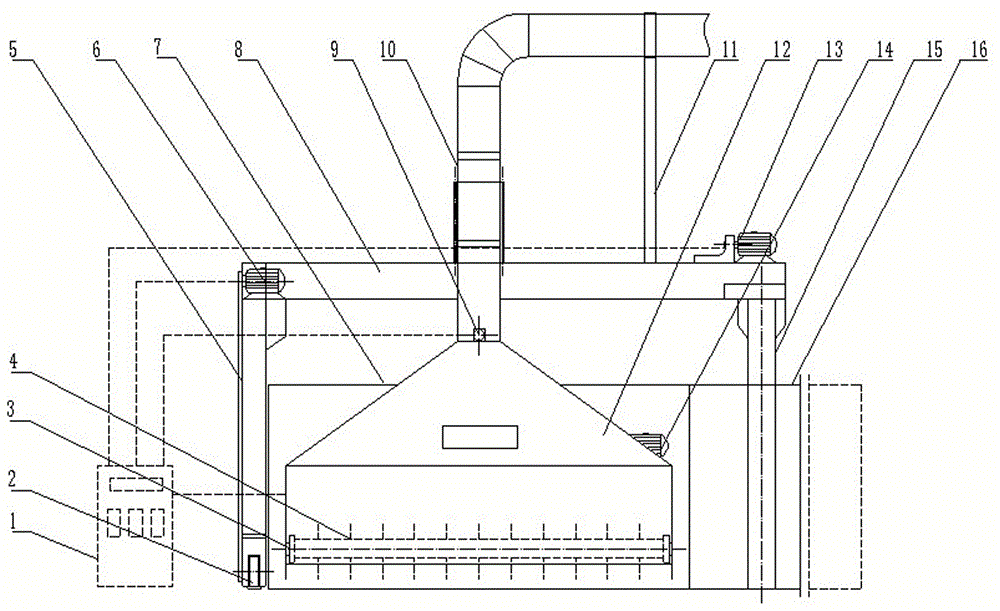
本发明涉及纺织设备,具体涉及一种全自动防抓棉打手夹死圆盘抓棉机。
背景技术:
fa002圆盘抓棉机在生产过程中由于前级吸风或者抓棉打手缠绕返花等原因造成出棉斗堵塞,会造成抓棉打手夹死以及产生大量的束丝,严重的会产生火警,造成安全隐患。针对该难题,企业组织技术人员技术攻关,以期短时间内解决。
技术实现要素:
本发明所要解决的技术问题是提供一种结构简单,作业稳定、高效、安全的全自动防抓棉打手夹死圆盘抓棉机。
为解决上述技术问题,本发明一种全自动防抓棉打手夹死圆盘抓棉机,包外圆盘、内圆盘,导轨;所述内圆盘内设置有主轴,所述主轴设置有横臂,所述横臂设置有行走支架;所述外圆盘、内圆盘之间设置有出棉斗,所述出棉斗上部设置有出料管,所述出料管固定于横臂上,所述出棉斗下方内置抓棉打手,所述抓棉打手两端分别设置有法兰盘;所述出棉斗设置有第一传动电机,所述横臂左端设置有第二传动电机,所述横臂右端设置有第三传动电机;
所述外圆盘一侧设置有主控机箱;所述第一传动电机、第二传动电机、第三传动电机分别与主控机箱连接;所述出料管设置有压力控制器,所述压力控制器与主控机箱连接。
本发明第三传动电机控制横臂升降,进而带动抓棉打手完成升降抓棉动作;第二传动电机控制行走支架沿导轨行走;第一传动电机为抓棉打手作业提供动力支持。本发明设置的压力控制器对作业过程中出料管内负压精确测值,当出料管内压力在设定值区间,设备正常运行;如出料管内压力超出设定值,则压力控制器给设备停机信号,待工作人员按工序处理故障后再运行设备。大直径的法兰盘作业过程中不易缠绕束花,可有效避免抓棉打手夹死现象产生。
优选的,所述压力控制器设置于出料管进口端。经大量生产实践,压力控制器设置在出料管进口端时,压力测值及敏感度处于最佳状态,可高效维持设备运行。
优选的,所述抓棉打手两端分别贯穿法兰盘,所述法兰盘通过螺钉固定于抓棉打手上;所述横臂与出料管折弯处设置有定位杆。采用该技术方案时,法兰盘易于拆装,维护,操作方便;定位杆支撑出料管,强化结构强度。
优选的,所述压力控制器量程设置为-500~500pa。在该压力值区间内,可确保设备运行稳定,作业高效。
综上,本发明公开的技术方案具以下有益效果:
1、结构简单,成本低廉,易于推广应用;
2、出棉斗内压力值控制精准,维持高效稳定作业;
3、有效避免抓棉打手夹死,杜绝安全隐患。
附图说明
图1是本发明的局部结构示意图。
具体实施方式
下面结合附图对本发明作进一步的说明:
如图1所示,本发明一种全自动防抓棉打手夹死圆盘抓棉机,包外圆盘7、内圆盘16,导轨2;所述内圆盘16内设置有主轴15,所述主轴15设置有横臂8,所述横臂8设置有行走支架5;所述外圆盘7、内圆盘16之间设置有出棉斗12,所述出棉斗12上部设置有出料管10,所述出料管10固定于横臂8上,所述出棉斗12下方内置抓棉打手4,所述抓棉打手4两端分别设置有法兰盘3;所述出棉斗12设置有第一传动电机14,所述横臂8左端设置有第二传动电机6,所述横臂8右端设置有第三传动电机13;
所述外圆盘7一侧设置有主控机箱1;所述第一传动电机14、第二传动电机6、第三传动电机13分别与主控机箱1连接;所述出料管10设置有压力控制器9,所述压力控制器9与主控机箱1连接。
所述压力控制器9设置于出料管10进口端。
所述抓棉打手4两端分别贯穿法兰盘3,所述法兰盘3通过螺钉固定于抓棉打手4上;所述横臂8与出料管10折弯处设置有定位杆11。
所述压力控制器9量程设置为-500~500pa。
工作人员在长期的生产实践中发现,fa002圆盘抓棉机作业过程中易出现抓棉打手夹死现象,影响生产进度的同时留下极大的安全隐患。
企业技术人员针对这一技术难题,在设备上加设压力控制器9,压力控制器9在设备运行时可实时监测出料管10内压力值并控制设备运行,确保出料管10内的压力值始终保持在合理范围内,当出料管10内压力一旦不在设定范围内,设备立即停车,工作人员排除故障后,再运行设备。
本发明的抓棉打手4两端设置的法兰盘3可有效的避免抓棉打手4缠绕返花,减少故障,提高生产功效。
本发明的压力控制器9量程为-500~500pa,可确保设备在最优状态下运行。
由上看出,本发明结构简单,依托现有设备稍加改造即可完成,其成本低廉,运行高效、稳定,适于大范围的推广应用。
以上显示和描述了本发明的基本原理和主要特征及本发明的优点。本行业的技术人员应该了解,本发明不受上述实施例的限制,上述实施例和说明书中描述的只是说明本发明的原理,在不脱离本发明精神和范围的前提下,本发明还会有各种变化和改进,这些变化和改进都落入要求保护的本发明范围内。
起点商标作为专业知识产权交易平台,可以帮助大家解决很多问题,如果大家想要了解更多知产交易信息请点击 【在线咨询】或添加微信 【19522093243】与客服一对一沟通,为大家解决相关问题。
此文章来源于网络,如有侵权,请联系删除


