一种智能纺纱粗纱故障检测系统的制作方法



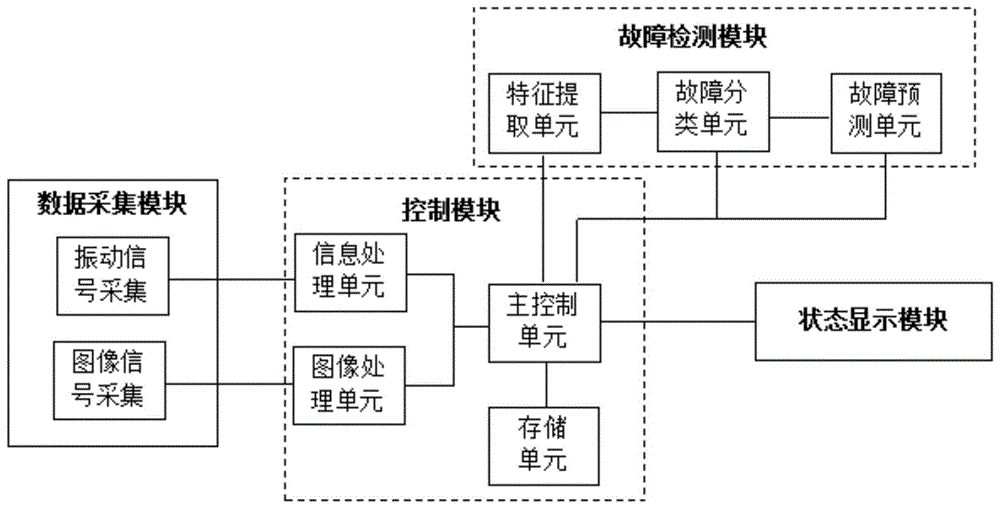
本实用新型涉及纺纱故障检测技术领域,特别是涉及一种智能纺纱粗纱故障检测系统。
背景技术:
随着工业化进程的加快,纺纱工业也得到了快速发展,并形成了较为成熟的纺纱工艺及各工艺对应的自动化设备。当前,纺纱工艺主要包括开清棉、梳棉、并条、粗纱、细纱及后加工等工序,其中,粗纱作为细纱前的最后一道准备工序,若发生故障,不仅会影响粗纱工序的顺利进行,还会影响粗纱的产品质量,进而对后续细纱工序的进行和最终的成纱质量造成影响。因此,为保障粗纱及后续工序的顺利进行、提高产品质量,对粗纱工序中的故障进行及时检测与处理具有重要意义。
目前,粗纱工序一般在粗纱机中进行,其故障也主要来源于粗纱机的机械故障。粗纱机的主要任务是将并条工序提供的熟条按照一定的牵伸倍数抽长拉细,改善纤维的平行伸直度,再加上适当的捻度,卷绕成形,以便细纱工序的使用;其主要包括牵伸机构、加捻机构、卷绕机构和成形机构,分别由罗拉牵伸电机、锭翼旋转电机、筒管卷绕电机与龙筋升降电机控制,而各电机的正常运行则是粗纱机正常工作的基础,因此,当前由可编程逻辑控制器控制的粗纱机通常设有编码器对各电机的转速进行监测,以识别相应的电机故障。然而,该方式仅能对电机故障进行检测,而不能发现粗纱机中其他机械部件的故障,故障检出率较低,隐患较大。
在粗纱机的各机械部件中,罗拉作为牵伸机构的主要部件,不仅对熟条的牵伸过程起到重要作用,且在牵伸过程中由罗拉振动产生的机械波对纱线的均匀性有较大影响,因此,当前罗拉故障主要通过对成品纱线进行均匀性测试来间接检出,而由于对成品纱线的质检通常在生产完成后进行,缺乏实时性,更不能提前预测,且对故障的分析通常由人工进行,速度较慢,待故障检出时已有大量瑕疵品产生,对产品的整体质量造成很大影响。此外,随着传感器在纺织机械中的广泛应用,当前已有利用振动传感器对罗拉进行故障检测的方法,然而,仅通过传感器对罗拉进行振动采集并不能全面地反映罗拉的振动状态,检测结果不够准确,部分故障难以检测出来,具有一定局限性。因此,有必要研究一种针对粗纱机中罗拉的故障检测系统,对其进行及时有效的故障检测,以增加粗纱工序故障的检出率,降低故障造成的影响,并对可能发生的故障进行预测,提高粗纱工序的安全性和可靠性。
技术实现要素:
本实用新型的目的在于针对上述问题,提供一种智能纺纱粗纱故障检测系统,通过对罗拉的振动状态进行实时监测,及时发现相应故障并自动进行故障检测与分类,便于相关人员及时进行维修,降低故障造成的影响;并通过对正常罗拉的振动状态进行合理预测,预知潜在故障,便于提前处理,降低故障发生率,提高粗纱工序的安全性和可靠性。
为实现上述目的,本实用新型采用的技术方案是:
一种智能纺纱粗纱故障检测系统,包括数据采集模块、控制模块、故障检测模块、状态显示模块和信息传输模块,所述控制模块通过所述信息传输模块分别与所述数据采集模块、故障检测模块和状态显示模块连接;所述数据采集模块包括振动信号采集单元和图像信号采集单元,分别用于实时采集粗纱机中罗拉的振动信号和图像信号;所述故障检测模块包括特征提取单元、故障分类单元和故障预测单元,所述特征提取单元的输入端与所述控制模块连接,其输出端与所述故障分类单元的输入端连接,所述故障分类单元的输出端分别与所述控制模块和所述故障预测单元的输入端连接,所述故障预测单元的输出端与所述控制模块连接。
进一步地,所述振动信号采集单元包括多个电涡流传感器,所述电涡流传感器设置于罗拉的前侧,并使罗拉的水平直径穿过所述电涡流传感器探头的中心,用于采集罗拉的振动信号,并传输至控制模块。
进一步地,所述图像信号采集单元包括多个由工业相机和led灯组成的图像采集装置,所述图像采集装置设置于罗拉的上方,并使罗拉的竖直直径穿过所述图像采集装置中工业相机镜头的中心,用于采集罗拉振动时的图像,并传输至控制模块。
进一步地,所述控制模块包括信号处理单元、图像处理单元、主控制单元和存储单元,所述信号处理单元包括信号放大器和a/d转换器,所述信号放大器的输入端与所述振动信号采集单元连接,其输出端与所述a/d转换器的输入端连接,所述a/d转换器的输出端与所述主控制单元连接;所述图像处理单元用于对输入的图像进行灰度处理及二值化,降低图片内存,提高后续处理速度,其输入端与所述图像信号采集单元连接,输出端与所述主控制单元连接;所述主控制单元还分别与所述存储单元、故障检测模块和状态显示模块连接。
进一步地,所述特征提取单元包括小波分析层、图像分析层和特征向量提取层,所述小波分析层用于对接收到的振动信号进行小波变换和正交小波分解,并将分解后得到的各频段振动信号输入特征向量提取层;所述图像分析层用于对接收到的图像信号进行边缘检测和振幅计算,并将结果输入特征向量提取层;所述特征向量提取层用于将接收到的振动信号的能量值按尺度顺序进行排列,并与图像分析层输入的振幅值共同组成特征向量,再将其输出至故障分类单元。
进一步地,所述故障分类单元包括存储器、训练层和神经网络分类层,所述存储器用于储存罗拉的历史故障数据,所述训练层基于存储器中的历史故障数据进行神经网络训练,所述神经网络分类层基于训练好的神经网络对输入的特征向量进行故障分类,并将故障分类结果输出至故障预测单元和控制模块。
进一步地,所述故障分类结果包括正常、罗拉弯曲故障、罗拉偏心故障、罗拉齿轮缺陷和罗拉齿轮回转不平衡。
进一步地,所述故障预测单元包括数据提取层、曲线拟合层和结果预测层,所述数据提取层用于接收故障分类结果,并对故障分类结果为正常的数据按固定频率进行周期性提取,并将提取的数据输入曲线拟合层;所述曲线拟合层用于对数据进行曲线拟合,得到预测曲线,输出至结果预测层;所述结果预测层用于将预测曲线与设定的阈值进行匹配,并将预测结果输出至控制模块。
进一步地,所述状态显示模块包括显示单元和反馈单元,所述显示单元用于接收所述控制模块传输的信息,并在led显示屏上进行显示,所述led显示屏上设有红、黄、绿三色的信号灯,分别用于表示当前故障、潜在故障和正常状态;所述反馈单元用于接收对故障的反馈信息,并传输至控制模块。
进一步地,所述信息传输模块包括工业以太网和以太网交换机,所述数据采集模块、故障检测模块和状态显示模块分别利用以太网交换机与所述控制模块通过工业以太网连接。
与现有技术相比,本实用新型的有益效果是:
1、本实用新型提供的智能纺纱粗纱故障检测系统通过对罗拉的振动状态进行实时监测,及时发现相应故障并自动进行故障检测与分类,便于相关人员及时进行维修,降低故障造成的影响;同时,本实用新型还通过对当前运行正常的罗拉的振动状态进行合理预测,预知潜在故障,便于提前处理,从而降低故障发生率,提高粗纱工序的安全性和可靠性。
2、本实用新型采用传感器和图像采集装置分别对罗拉的振动信号和图像信号进行实时监测,通过对振动信号进行小波分析、对图像信号进行边缘检测,从而更加全面、准确地提取相应的故障特征,提高故障检测的准确率;本实用新型还利用神经网络对提取到的特征进行自动分类,使相关人员能够及时了解故障原因,加快维修速度,尽可能降低故障对粗纱工序及产品质量的影响。
3、本实用新型采用曲线拟合法对分类为正常的罗拉进行故障预测,通过将罗拉振动状态的特征参数进行回归拟合,得到对应的预测曲线,对其未来的运行状态进行合理预测,便于预知潜在故障,提前采取措施,有效降低故障率。
附图说明
图1是本实用新型一种智能纺纱粗纱故障检测系统的结构示意图;
图2是本实用新型一种智能纺纱粗纱故障检测系统使用时的主要流程图。
具体实施方式
下面结合附图对本实用新型的较佳实施例进行详细阐述,以使本实用新型的优点和特征能更易于被本领域技术人员理解,从而对本实用新型的保护范围做出更为清楚明确的界定。显然,所描述的实施例仅仅是本实用新型的一部分实施例,而不是全部的实施例。基于本实用新型的实施例,本领域普通技术人员在没有做出创造性劳动的前提下所得到的所有其它实施例,都属于本实用新型所保护的范围。
实施例
请参阅图1,本实用新型实施例提供了一种智能纺纱粗纱故障检测系统,包括数据采集模块、控制模块、故障检测模块、状态显示模块和信息传输模块,所述控制模块通过所述信息传输模块分别与所述数据采集模块、故障检测模块和状态显示模块连接;所述数据采集模块包括振动信号采集单元和图像信号采集单元,分别用于实时采集粗纱机中罗拉的振动数据和图像信号;所述故障检测模块包括特征提取单元、故障分类单元和故障预测单元,所述特征提取单元的输入端与所述控制模块连接,其输出端与所述故障分类单元的输入端连接,所述故障分类单元的输出端分别与所述控制模块和所述故障预测单元的输入端连接,所述故障预测单元的输出端与所述控制模块连接。
其中,所述振动信号采集单元包括多个电涡流传感器,所述电涡流传感器设置于罗拉的前侧,并使罗拉的水平直径穿过所述电涡流传感器探头的中心,用于采集罗拉的振动数据,并传输至控制模块。
所述图像信号采集单元包括多个由工业相机和led灯组成的图像采集装置,所述图像采集装置设置于罗拉的上方,并使罗拉的竖直直径穿过所述图像采集装置中工业相机镜头的中心,用于采集罗拉振动时的图像,并传输至控制模块。
所述控制模块包括信号处理单元、图像处理单元、主控制单元和存储单元,所述信号处理单元包括信号放大器和a/d转换器,所述信号放大器的输入端与所述振动信号采集单元连接,其输出端与所述a/d转换器的输入端连接,所述a/d转换器的输出端与所述主控制单元连接;所述图像处理单元用于对输入的图像进行灰度处理及二值化,降低图片内存,提高后续处理速度,其输入端与所述图像信号采集单元连接,输出端与所述主控制单元连接;所述主控制单元还分别与所述存储单元、故障检测模块和状态显示模块连接。其中,所述信号放大器用于接收并放大由数据采集模块传输的信息,所述a/d转换器用于将接收到的模拟信号转换为数字信号,所述主控制单元用于控制信号的接收与传输,所述存储单元用于接收、存储故障信息,供相关人员查看及导出。
所述特征提取单元包括小波分析层、图像分析层和特征向量提取层,所述小波分析层用于对接收到的振动信号进行小波变换和正交小波分解,并将分解后得到的各频段振动信号输入特征向量提取层;所述图像分析层用于对接收到的图像信号进行边缘检测和振幅计算,并将结果输入特征向量提取层;所述特征向量提取层用于将接收到的振动信号的能量值按尺度顺序进行排列,并与图像分析层输入的振幅值共同组成特征向量,再将其输出至故障分类单元。
所述故障分类单元包括存储器、训练层和神经网络分类层,所述存储器用于储存罗拉的历史故障数据,所述训练层基于存储器中的历史故障数据进行神经网络训练,所述神经网络分类层基于训练好的神经网络对输入的特征向量进行故障分类,并将故障分类结果输出至故障预测单元和控制模块。
所述故障分类结果包括正常、罗拉弯曲故障、罗拉偏心故障、罗拉齿轮缺陷和罗拉齿轮回转不平衡。
所述故障预测单元包括数据提取层、曲线拟合层和结果预测层,所述数据提取层用于接收故障分类结果,并对故障分类结果为正常的数据按固定频率进行周期性提取,并将提取的数据输入曲线拟合层;所述曲线拟合层用于对数据进行曲线拟合,得到预测曲线,输出至结果预测层;所述结果预测层用于将预测曲线与设定的阈值进行匹配,并将预测结果输出至控制模块。
所述状态显示模块包括显示单元和反馈单元,所述显示单元用于接收所述控制模块传输的信息,并在led显示屏上进行显示,所述led显示屏上设有红、黄、绿三色的信号灯,分别用于表示当前故障、潜在故障和正常状态;所述反馈单元用于接收对故障的反馈信息,并传输至控制模块。
所述信息传输模块包括工业以太网和以太网交换机,所述数据采集模块、故障检测模块和状态显示模块分别利用以太网交换机与所述控制模块通过工业以太网连接。
结合参阅图2,本实用新型实施例提供的智能纺纱粗纱故障检测系统在使用时,通过在粗纱机的各罗拉上分别安装电涡流传感器和图像采集装置,对罗拉的振动信号和图像信号进行实时采集,并通过工业以太网将其分别传输至控制模块中的信号处理单元和图像处理单元,由信号处理单元对采集到的振动信号进行信号放大和模数转换,由图像处理单元对采集到的图像信号进行灰度处理和二值化,从而降低图片内存,提高后续处理速度;处理后的振动信号和图像信号均通过主控制单元传输至故障检测模块中的特征提取单元,进行特征提取,主要包括如下步骤:
s11、通过小波分析层对输入的罗拉振动信号进行离散小波变换,获取低频时域信号,并对时域信号进行傅里叶变换,获取频谱信号,再对频谱信号中高频段的信号进行正交小波分解,获得九段振动信号,其小波分解系数分别表示为q1~q9,并将其输入特征向量提取层;
s12、通过图像分析层对输入的图像信号进行滤波处理,并求出图像f(x,y)中各像素点(x,y)的梯度幅度|g|,其计算公式如下:
其中,
再采用非极大值抑制法,排除局部梯度幅度非极大值的像素点,从而提取出图像边缘,并根据图像边缘间的距离得出罗拉的振幅值a;
s13、在特征向量提取层内对步骤s11输入的九段振动信号的振动能量进行计算,计算公式如下:
式中,ej表示第j段振动信号的振动能量,qj表示第j段小波分解系数,m表示qj中分量的个数;
s14、将计算得的九段振动信号的振动能量进行归一化,并按尺度顺序排列,再将步骤s12输入的振幅值a排在最后,共同形成特征向量t=(e1,e2,…,e9,a),并将其输出至故障分类单元。
所述故障分类单元包括存储器、训练层和神经网络分类层,在开始检测前,即在所述存储器中预存有大量历史故障数据,所述历史故障数据来源于同一粗纱机过去累计的故障情况,所述历史故障数据中包括故障特征向量和对应的输出向量;所述训练层基于所述历史故障数据进行神经网络训练,并保存训练后的阈值。
当所述故障分类单元接收到特征向量后,将其输入神经网络分类层中,通过训练好的神经网络对输入的特征向量进行故障分类,根据输出向量判定故障分类结果,输出向量为(1,0,0,0,0)、(0,1,0,0,0)、(0,0,1,0,0)、(0,0,0,1,0)、(0,0,0,0,1)分别对应正常、罗拉弯曲故障、罗拉偏心故障、罗拉齿轮缺陷和罗拉齿轮回转不平衡。
当故障分类结果为罗拉弯曲故障、罗拉偏心故障、罗拉齿轮缺陷或罗拉齿轮回转不平衡时,对应故障信息输出至控制模块,由控制模块读取后将信号传输至状态显示模块,控制led显示屏上红色信号灯亮起,并在led显示屏显示故障来源与故障分类,便于相关人员及时处理;同时,输入控制模块的故障信息在存储单元中进行存档,供相关人员查看及导出,便于总结分析。
当故障分类结果为正常时,对应故障信息则输出至故障预测单元,用于对故障信息进行预测,主要包括如下步骤:
s21、通过数据提取层对故障信息进行接收,识别其中的输出向量,并按照每小时一组的频率对输出向量进行提取,待提取了24组输出向量后,将其输入曲线拟合层,所述24组输出向量分别由x1~x24表示,其中:
xi=(ai,bi,ci,di,ei);
s22、在曲线拟合层内,分别作出ai,bi,ci,di,ei相对于时间的函数曲线,并通过最小二乘法将其分别拟合成五条预测曲线,对各向量参数往后24小时的数值进行预测,并输出至结果预测层;
s23、在结果预测层中,设定ai的阈值范围为0.98~1.02,bi,ci,di,ei的阈值范围为0~0.02,分别对五条预测曲线进行匹配,当五条预测曲线内的数值均在阈值范围内时,则预测结果为正常,当bi,ci,di,ei对应的预测曲线超出阈值范围时,则预测结果分别对应罗拉弯曲故障、罗拉偏心故障、罗拉齿轮缺陷和罗拉齿轮回转不平衡。
所述预测结果经结果预测层输出至控制模块,由控制模块读取后将信号传输至状态显示模块,当预测结果为正常时,控制模块控制led显示屏上绿色信号灯亮起,并在led显示屏上显示正常;当预测结果为罗拉弯曲故障、罗拉偏心故障、罗拉齿轮缺陷或罗拉齿轮回转不平衡时,控制模块则控制led显示屏上黄色信号灯亮起,并在led显示屏上显示潜在故障与相应故障的种类及预测发生时间,便于相关人员及时处理。
当故障分类结果和故障检测结果通过状态显示模块进行显示后,相关工作人员可以进行查看,并对相应故障进行处理;同时,相关工作人员还可以通过显示屏上的反馈界面进行故障反馈,所述故障反馈包括故障已处理、故障报错和故障漏检,所述反馈信息通过反馈单元进行接收,并通过控制模块传输至存储单元,用于统计分析。
通过上述方式,本实用新型提供的一种智能纺纱粗纱故障检测系统能够实现对粗纱工序中罗拉故障的检测、分类与预测,降低了故障造成的影响和罗拉故障率,提高了粗纱工序的安全性和可靠性。
以上所述仅用以说明本实用新型的技术方案,而非对其进行限制;尽管参照前述实施例对本实用新型进行了详细的说明,本领域的普通技术人员应当理解:其依然可以对前述实施例所记载的技术方案进行修改,或者对其中部分或者全部技术特征进行等同替换;凡是利用本实用新型说明书及附图内容所作的等效结构或等效流程变换,或直接或间接运用在其他相关的技术领域,均同理包括在本实用新型的专利保护范围内。
起点商标作为专业知识产权交易平台,可以帮助大家解决很多问题,如果大家想要了解更多知产交易信息请点击 【在线咨询】或添加微信 【19522093243】与客服一对一沟通,为大家解决相关问题。
此文章来源于网络,如有侵权,请联系删除


